Imagine crafting intricate, high-strength metal parts straight from a digital design. That’s the magic of 3D printing with aluminum powder, a revolutionary technology rapidly transforming the manufacturing landscape. Unlike traditional methods like casting or machining, 3D printing offers unparalleled design freedom, complex part geometries, and on-demand production – all with minimal waste.
But what exactly is 3d printer aluminum powder, and how does it work? Buckle up, because we’re diving deep into this fascinating realm, exploring different metal powder options, their properties, applications, and everything you need to know to leverage this cutting-edge technology.
the Powerhouse of 3d Printer Aluminum Powder
3d printer aluminum powder isn’t your average picnic table sprinkle. These meticulously engineered metallic grains are specially designed for specific 3D printing techniques, like Laser Powder Bed Fusion (LPBF) and Electron Beam Melting (EBM).
Here’s a breakdown of the key characteristics:
- Particle Size & Distribution: Measured in microns (µm), the size and distribution of the powder particles significantly impact printability, surface finish, and mechanical properties of the final part. Typically, particles range from 15 to 90 microns, with a tight distribution ensuring smooth layer-by-layer deposition during printing.
- Material Composition: Pure aluminum offers excellent weight savings but might lack strength for certain applications. To address this, aluminum alloys are commonly used. These alloys combine aluminum with other elements like silicon (Si), magnesium (Mg), copper (Cu), or manganese (Mn) to enhance specific properties like strength, corrosion resistance, or weldability.
- Flowability: Imagine pouring sand versus flour. Flowability refers to the powder’s ability to move freely and pack densely, crucial for even layer formation during printing. Manufacturers optimize powder flow characteristics to ensure smooth operation within the 3D printer.
- Sphericity: Ideally, powder particles should be spherical for optimal packing density and minimal inter-particle friction. This reduces voids within the printed part and leads to better mechanical performance.
Now, let’s delve into the world of specific metal powder models!
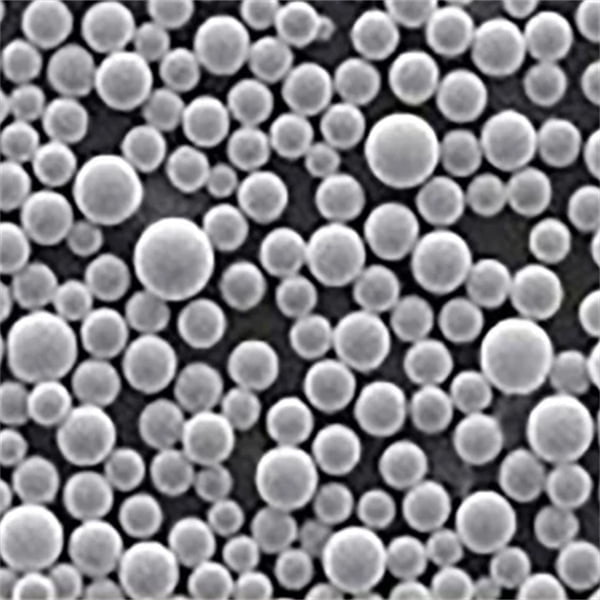
Exploring a Range of Aluminum Powder Options
The world of 3D printing aluminum powder boasts a diverse range of options, each catering to specific needs. Here’s a closer look at ten popular metal powder models:
- AlSi10Mg: This workhorse alloy is renowned for its excellent printability, good weldability, and a balance of strength and ductility. It’s widely used for aerospace components, automotive parts, and general-purpose applications.
- AlSi7Mg: A close cousin to AlSi10Mg, this alloy offers similar printability but with slightly lower silicon content, translating to a bit higher strength and improved corrosion resistance. It’s suitable for applications demanding a good balance of mechanical properties and environmental resilience.
- Scalmalloy: This family of aluminum-scandium alloys boasts exceptional strength-to-weight ratios, exceeding even some titanium grades. Developed by Exone, Scalmalloy is ideal for high-performance applications in aerospace and motorsports, where weight reduction and strength are paramount.
- A357: Known for its outstanding castability, A357 translates well to the 3D printing realm. This silicon-magnesium alloy offers good strength, wear resistance, and decent corrosion resistance, making it suitable for pistons, cylinder heads, and other wear-prone parts.
- AM3004: This pure aluminum powder offers the ultimate in lightweight design. However, its strength is lower compared to alloys. AM3004 shines in applications where weight reduction is the primary concern, such as heat exchangers or aircraft components requiring minimal weight.
- AA2024: A popular choice for aerospace applications, AA2024 offers high strength and good fatigue resistance. However, it requires specific post-processing techniques to manage its susceptibility to stress corrosion cracking.
- Maraging Steel 316L: While not strictly aluminum, this steel powder deserves a mention for its unique properties. Maraging steel offers exceptional strength-to-weight ratios, exceeding even some aluminum alloys. It’s ideal for demanding applications like aerospace components and high-performance tools.
- Nickel Alloy IN625: Another non-aluminum option, IN625 is a nickel-chromium alloy known for its outstanding high-temperature performance and corrosion resistance. It’s perfect for parts operating in harsh environments like jet engines or chemical processing equipment.
- Copper (Cu): Pure copper powder offers excellent thermal and electrical conductivity.
Applications of 3D Printer Aluminum Powder
The versatility of 3d printer aluminum powder extends far beyond mere prototyping. Here’s a glimpse into the diverse applications driving this technology forward:
Aerospace & Defense:
- Lightweight components: Aluminum’s excellent strength-to-weight ratio makes it ideal for aircraft parts, reducing overall weight and improving fuel efficiency. Complex internal structures can be printed for increased performance and part consolidation.
- High-performance parts: alloys like Scalmalloy offer exceptional strength for demanding applications like engine mounts, landing gear components, and even spacecraft structures.
- Rapid prototyping & customization: The ability to fabricate complex geometries quickly allows for faster design iterations and creation of customized parts for specific needs.
Automotive & Transportation:
- Lightweight parts: Similar to aerospace, 3D printing aluminum powder can create lightweight car components like brackets, levers, and even engine parts, contributing to improved fuel economy and performance.
- Custom components: The technology facilitates the creation of personalized car parts like customized wheels or ergonomic knobs, catering to individual preferences.
- Motorsports: High-performance alloys like Scalmalloy are ideal for fabricating lightweight yet strong parts for race cars, motorcycles, and other high-performance vehicles.
Medical & Healthcare:
- Prosthetics & Implants: 3D printing aluminum powder allows for the creation of lightweight, customized prosthetics and implants, improving patient comfort and functionality.
- Surgical instruments: Complex surgical tools with intricate geometries can be printed, enabling minimally invasive procedures and potentially improving surgical outcomes.
- Medical devices: Aluminum parts can be incorporated into various medical devices, such as X-ray equipment or MRI scanner components.
Consumer Goods & Electronics:
- Customized electronics casings: The ability to create complex shapes allows for the production of personalized electronic device housings, catering to individual styles.
- Lightweight consumer goods: Aluminum parts can be incorporated into various consumer products like bicycles, cameras, or even high-end sports equipment, offering weight reduction and improved performance.
- Rapid prototyping & design freedom: 3D printing empowers designers to create and iterate on product designs quickly, accelerating the development process and bringing innovative products to market faster.
Other Emerging Applications:
- Construction: 3D printing with aluminum powder holds potential for creating lightweight building components or even on-site construction of customized architectural elements.
- Robotics: Aluminum parts can be used in robot arms or other robotic components, offering a balance of strength and weight for optimal performance.
- Art & Design: The freedom of 3D printing allows artists and designers to create intricate and unique aluminum sculptures and art pieces, pushing the boundaries of artistic expression.
This is just a glimpse into the vast potential of 3D printing aluminum powder. As the technology matures and new materials emerge, we can expect even more innovative applications to reshape various industries in the years to come.
Key Considerations: Specifications & Standards
Selecting the right aluminum powder for your 3D printing project requires careful consideration of various specifications:
Feature | Description |
---|---|
Particle Size & Distribution | Typically ranges from 15 to 90 microns, with a tight distribution for optimal printability. |
Chemical Composition | Pure aluminum (AM3004) offers low weight but lower strength. Alloys like AlSi10Mg or AA2024 provide a balance of properties. |
Flowability | The powder’s ability to move freely for smooth layer formation during printing. |
Sphericity | Ideally spherical particles offer better packing density and minimal inter-particle friction. |
Standards | ASTM International and other organizations set standards for aluminum powder composition and properties for 3D printing applications (e.g., ASTM B299). |
Matching these specifications with your project requirements and chosen 3D printing technology is crucial for achieving optimal results. Additionally, factors like surface finish requirements and post-processing needs may influence your choice of aluminum powder. Consulting with a qualified 3D printing materials supplier can help you select the most suitable powder for your project.
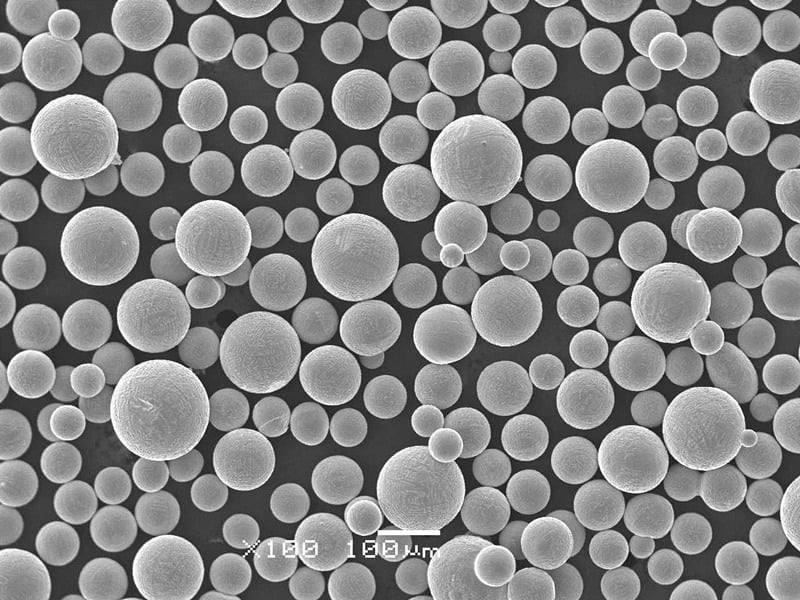
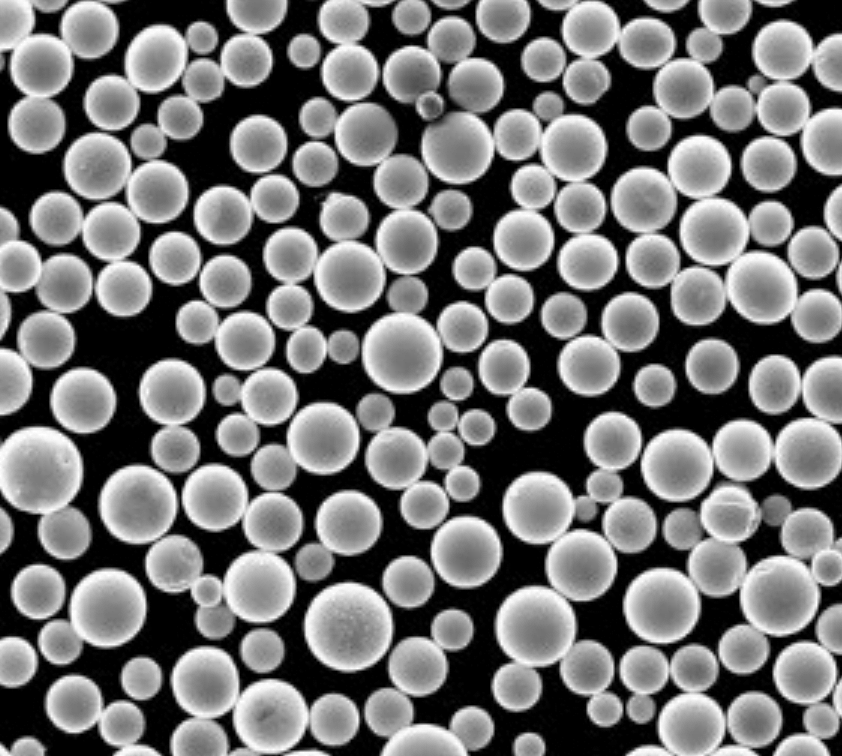
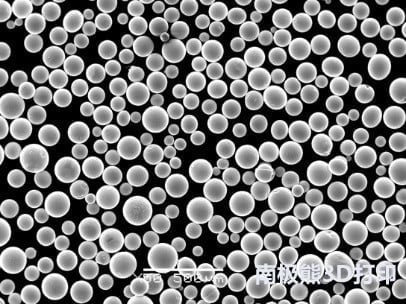
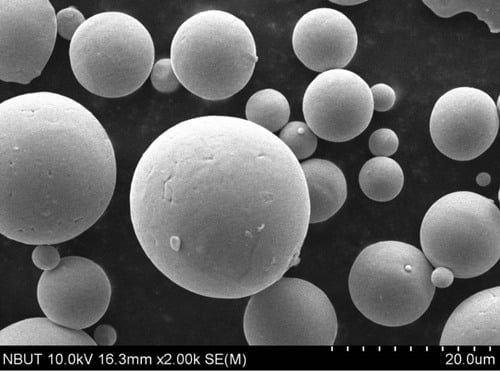
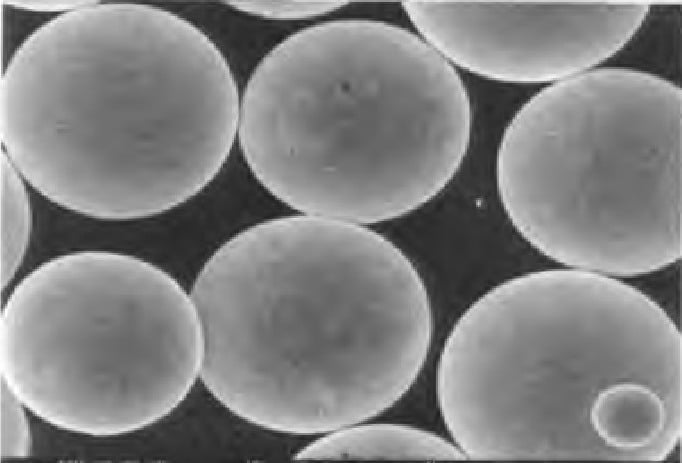
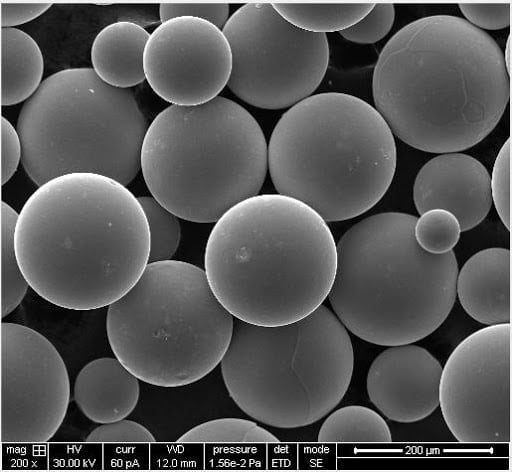
Pros & Cons of 3d printer aluminum powder
As with any technology, 3D printing aluminum powder has its own set of advantages and limitations:
Advantages:
- Design Freedom: Unleash complex geometries and intricate internal structures impossible with traditional methods.
- Lightweight Parts: Aluminum’s inherent lightness translates to lighter printed parts, crucial for applications like aerospace or automotive.
- On-demand Production: Print parts as needed, reducing waste and minimizing inventory requirements.
- Rapid Prototyping: Fabricate prototypes quickly, accelerating the design iteration process.
- Customization: Create personalized parts or components tailored to specific needs.
- Material Efficiency: 3D printing minimizes material waste compared to traditional subtractive manufacturing techniques.
- High Strength-to-Weight Ratio: Certain aluminum alloys offer exceptional strength while maintaining a lightweight profile.
Disadvantages:
- Limited Material Selection: While a variety of aluminum powders exist, the selection is not as vast as with traditional manufacturing methods.
- Cost: The technology can be expensive compared to some conventional techniques, especially for high-volume production.
- Post-Processing: Some aluminum alloys may require additional post-processing steps like heat treatment for achieving optimal mechanical properties.
- Surface Finish: 3D printed parts may require additional surface finishing depending on the desired aesthetics and functional requirements.
- Support Structures: Complex geometries might necessitate the use of support structures during printing, which can add time and material consumption.
Making an informed decision about whether 3D printing aluminum powder is the right choice for your project requires careful consideration of both its advantages and limitations.
Suppliers & Pricing of Aluminum Powder Match
The landscape of 3d printer aluminum powder suppliers is constantly evolving. Here’s a glimpse into some key players, but it’s vital to conduct your own research to find the best fit for your needs:
- APWorks: A leading manufacturer of metal powders for additive manufacturing, offering various aluminum alloys like AlSi10Mg and Scalmalloy.
- Höganäs: A global provider of metal powders, including aluminum options for 3D printing with diverse chemistries and particle size distributions.
- AMEX Additive GmbH: Specializes in high-performance metal powders for additive manufacturing, including aluminum alloys for demanding applications.
- SLM Solutions: A renowned manufacturer of 3D printing machines, also offers a range of metal powders, including aluminum options for their LPBF systems.
- Exone: The developer of Scalmalloy, Exone provides this exceptional aluminum-scandium alloy powder for high-strength applications.
Pricing for aluminum powder can vary depending on the specific alloy, particle size, quantity, and supplier. Generally, expect premium prices compared to standard aluminum materials due to the specialized nature of the powder for 3D printing.
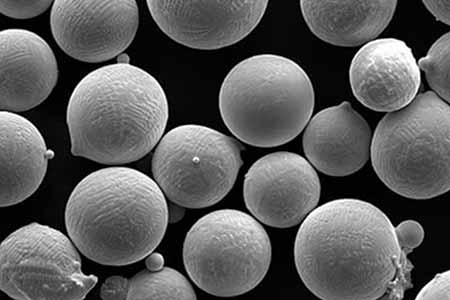
FAQ
Q: What are the different types of aluminum powder for 3D printing?
A: There’s a range of aluminum powders available, with common options including AlSi10Mg, AlSi7Mg, Scalmalloy, A357, and AM3004. Each offers unique properties in terms of strength, ductility, corrosion resistance, and printability.
Q: What are the advantages of using aluminum powder for 3D printing?
A: The key advantages include design freedom, lightweight parts, on-demand production, rapid prototyping, customization, and material efficiency. Aluminum’s high strength-to-weight ratio is another significant benefit.
Q: What are the limitations of 3D printing aluminum powder?
A: Limitations include a limited selection of materials compared to traditional methods, higher costs, potential post-processing needs, surface finish considerations, and the use of support structures for complex geometries.
Q: Where can I buy aluminum powder for 3D printing?
A: Several reputable suppliers offer aluminum powder specifically designed for 3D printing. Leading names include APWorks, Höganäs, AMEX Additive GmbH, SLM Solutions, and Exone. It’s recommended to research and compare pricing and offerings from various vendors.
Q: Is 3D printing aluminum powder right for my project?
A: The suitability depends on your specific needs. Consider the advantages and limitations, along with factors like project complexity, budget, and desired material properties. Consulting with a qualified 3D printing specialist can help you make an informed decision.
About 3DP mETAL
Product Category
CONTACT US
Any questions? Send us a message now! After receiving your message, we will process your request with a whole team.