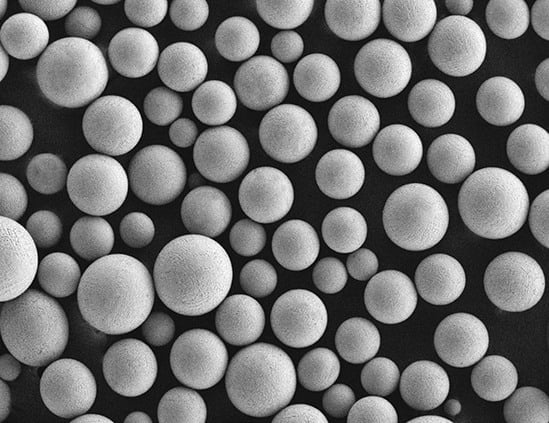
Ti3Al Powder
Ti3Al Powder: Composition, Properties, Applications, and More Some of the key properties and characteristics of Ti3Al powder include: High strength at elevated temperatures up to 750¡«C Density about half that of nickel superalloys Outstanding corrosion resistance Low density compared to other titanium alloys Oxidation resistance up to about 700¡«C Wear resistance Biocompatibility However, Ti3Al also…
Small MOQ
Flexible sourcing for hundreds of products
Customization support
Customized powder according to industry
Rapid shipment
By DHL Express, safe and fast direct to your hands
Ti3Al Powder: Composition, Properties, Applications, and More
Some of the key properties and characteristics of Ti3Al powder include:
- High strength at elevated temperatures up to 750¡«C
- Density about half that of nickel superalloys
- Outstanding corrosion resistance
- Low density compared to other titanium alloys
- Oxidation resistance up to about 700¡«C
- Wear resistance
- Biocompatibility
However, Ti3Al also has limitations like poor room temperature ductility, low fracture toughness, and poor weldability. Proper processing and alloying additions are required to optimize the balance of properties for different applications.
This article provides a detailed overview of the composition, properties, applications, suppliers, costs, testing methods, and other technical details related to Ti3Al powder.
Ti3Al Powder Composition
Ti3Al powder has a nominal composition of 75% titanium and 25% aluminum by weight. The titanium aluminide intermetallic compound forms between 50-75% aluminum, with Ti3Al being the most common version.
The exact composition can vary depending on the production method. Other elements like Nb, Mo, Si, B, Ta, W, C, and O are often added in small quantities to enhance certain properties. The table below shows the typical composition range:
Element | Weight % |
---|---|
Titanium (Ti) | 69 – 76% |
Aluminum (Al) | 24 – 31% |
Niobium (Nb) | 0 – 6% |
Molybdenum (Mo) | 0 – 4% |
Silicon (Si) | 0 – 2% |
Boron (B) | 0 – 0.5% |
Tantalum (Ta) | 0 – 5% |
Tungsten (W) | 0 – 5% |
Carbon (C) | 0 – 0.1% |
Oxygen (O) | 0 – 0.2% |
Controlling the oxygen and carbon content is critical to avoid embrittlement and maintain ductility. Other trace elements may also be present depending on the raw materials and process.
Ti3Al Powder Properties
The unique properties of Ti3Al powder stem from its ordered intermetallic crystal structure consisting of both titanium and aluminum atoms. Some of the notable properties include:
High Temperature Strength
Ti3Al retains relatively high strength up to 750¡«C, significantly better than titanium or aluminum alone. This makes it suitable for elevated temperature applications in engines, turbines, valves, etc. The table below compares Ti3Al’s strength to other titanium alloys at different temperatures:
Alloy | Room Temp Strength (MPa) | Strength at 500¡«C (MPa) | Density (g/cm3) |
---|---|---|---|
Ti3Al | 400 | 260 | 3.9 |
Ti6Al4V | 900 | 500 | 4.5 |
Ti64 | 900 | 400 | 4.5 |
Low Density
With a density around 3.7 – 4.1 g/cm3, Ti3Al is much lighter than nickel superalloys and most other titanium alloys. This helps reduce component weight critical in aerospace applications.
Oxidation Resistance
Ti3Al offers good oxidation resistance up to 700¡«C in air, better than unalloyed titanium. This allows it to operate at high temperatures without excessive material loss.
Corrosion Resistance
The titanium content gives Ti3Al excellent corrosion resistance to a wide range of acids, alkalis, and saline environments. This makes it useful in chemical processing equipment.
Wear Resistance
Ti3Al has good abrasion and erosions resistance comparable to steels, making it suitable for high wear applications like valves, pumps, and extrusion dies.
However, Ti3Al also suffers from disadvantages like:
- Poor room temperature ductility and fracture toughness
- Difficult to fabricate and machine
- Poor weldability due to susceptibility to cracking
Proper processing and alloying additions are required to optimize the balance of properties for the intended application.
Ti3Al Powder Applications
The unique properties of Ti3Al powder make it suitable for the following applications:
Aerospace
The aerospace industry is the largest consumer of Ti3Al products due to the need for weight savings, high temperature strength, and oxidation resistance. Typical applications include:
- Turbine blades, vanes, disks
- Combustion chambers, afterburners
- Airframes, structural components
- Hydraulic tubing, valves
Automotive
The automotive industry utilizes Ti3Al for turbocharger components, valves, springs, fasteners, and exhaust system parts that require high temperature strength and lower weight.
Chemical Processing
Ti3Al is used for components like valves, pumps, pipe fittings, reaction vessels that require corrosion resistance combined with high temperature mechanical properties.
Biomedical
The biocompatibility, corrosion resistance, and strength of Ti3Al make it suitable for orthopedic implants like artificial hip joints.
Other applications include high performance valves, extrusion dies, heating elements, and sporting goods. Ti3Al is also used as an additive manufacturing powder.
Ti3Al Powder Specifications
Ti3Al powder is available in different size ranges, morphologies, and purity levels depending on the production process. The key specifications are given below:
Specification | Details |
---|---|
Particle sizes | 15 – 150 microns |
Morphology | Spherical, angular, mixed |
Apparent density | 2 – 3.5 g/cm3 |
Tap density | 3 – 4.5 g/cm3 |
Purity | ¡Ô99%, ¡Ô99.9% |
Oxygen content | ¨P 0.2 wt% |
Nitrogen content | ¨P 0.05 wt% |
Carbon content | ¨P 0.08 wt% |
Iron content | ¨P 0.30 wt% |
Nickel content | ¨P 0.10 wt% |
Standard packs | 5kg, 10kg, 25kg |
Finer particle sizes generally provide better flowability, packing density, and reactivity. Spherical morphologies also improve powder flow. Higher purity reduces contaminants and improves properties.
Ti3Al Powder Production
There are several methods used to produce Ti3Al powder including:
- Gas Atomization?- Molten Ti-Al alloy is atomized with inert gas into fine droplets that solidify into powder. This produces spherical particles with good flowability.
- Mechanical Alloying?- Elemental Ti and Al powders are ball milled to synthesize the intermetallic compound mechanically. The powder particles have irregular shapes.
- Plasma Spheroidization?- Irregular Ti3Al powder from mechanical alloying is re-melted in a plasma to generate spherical powder.
- Electrode Induction Melting Gas Atomization (EIGA)?- Directly melts and atomizes an electrode of Ti3Al to produce powder.
Gas atomization and plasma processing allow better control over particle size distribution, morphology, oxygen pickup, and microstructure. The powder must usually be sieved into specific size fractions after production based on application requirements.
Ti3Al Powder Cost
Ti3Al powder is significantly more expensive than titanium or aluminum powders alone. Costs vary between:
- $100 – $500 per kg for 99% purity gas atomized powder
- $50 – $250 per kg for 99% mechanical alloyed powder
- $300 – $1000 per kg for 99.9% plasma spheroidized powder
Prices depend on particle size, morphology, purity level, order quantity, and manufacturer. Custom alloys with special compositions can cost even higher. Costs have been decreasing due to increased production volumes and process improvements.
Ti3Al Powder Suppliers
Some of the major global suppliers of Ti3Al powder include:
Company | Location |
---|---|
AP&C | Canada |
TLS Technik GmbH | Germany |
Metal Technology | UK |
ATI Powder Metals | USA |
Carpenter Additive | USA |
Met3DP | China |
Tekna | Canada |
There are a few producers in China as well. It is recommended to source powder from established manufacturers using qualified production processes to ensure reliable quality and properties.
Ti3Al versus Alternatives
Ti3Al competes against several alternatives for high temperature structural applications:
Table: Comparison of Ti3Al versus other high-temperature alloys
Alloy | Density | Max Temp | Strength | Ductility | Oxidation Resistance | Cost |
---|---|---|---|---|---|---|
Ti3Al | Low | Very high | High | Low | Good | High |
Inconel 718 | High | High | Medium | Medium | Good | Medium |
Haynes 230 | High | Very high | High | Low | Excellent | Very high |
Ti6Al4V | Medium | Medium | Medium | Medium | Excellent | Medium |
Ferritic stainless steels | Medium | Medium | Low | High | Poor | Low |
For maximum service temperatures, Ti3Al and nickel-based superalloys like Haynes 230 are superior. However, the lower density and cost of Ti3Al are advantageous for weight-critical applications like aerospace.
The poor room temperature ductility of Ti3Al remains a key limitation versus steels and Ti6Al4V. Alloy and process development continue to improve machinability and fabricability.
Advantages of Ti3Al Powder
Key benefits of using Ti3Al powder include:
- High strength maintained to 800¡«C
- Density 40% lower than nickel superalloys
- Excellent creep resistance
- Good oxidation and corrosion resistance
- Refractory metal substitution without strategic material risks
- Near-net shape manufacturing with powder metallurgy
- Components can operate at higher temperatures
- Weight savings in rotating parts like turbine blades
- Improved efficiency through higher operating parameters
The unique balance of mechanical properties, low density and thermal stability make Ti3Al an enabling material for next-generation aerospace, automotive and power generation systems.
Limitations of Ti3Al Powder
Despite its advantages, Ti3Al also has certain drawbacks:
- Brittle at room temperature, ductility improves above 500¡«C
- Fabrication and machining is challenging
- Rapid property loss below 400¡«C
- Raw material and processing costs are very high
- Supply chain is limited with few producers
- Component design requires specialized engineering expertise
- Not easily welded or joined with conventional techniques
- Difficult to recycle and reuse
Manufacturing and cost hurdles have slowed broad commercial adoption of Ti3Al to date. But its capabilities continue to drive development efforts to overcome these limitations through improved alloy chemistries, powder quality and component design.
Outlook for Ti3Al Powder
Ti3Al is forecast to see expanded usage in aerospace, automotive, industrial gas turbine and power generation sectors due to:
- Increasing demand for jet engine fuel efficiency and lower emissions
- High temperature materials required for electrical turbochargers
- Growing market for additive manufacturing technologies
- Focus on strategic material substitution for rare earths and refractory metals
- Cost reduction through improved manufacturing productivity
Automotive and industrial markets are more price-sensitive and require demonstrated cost-performance advantage versus existing alloys. Aerospace sector is more willing to pay a premium for maximum performance.
Government initiatives in US, EU and Japan are accelerating R&D on Ti3Al powder production, component fabrication, joining methods and alloy development. This will expand application space and drive higher adoption rates.
Frequently Asked Questions
Q: What is Ti3Al powder used for?
A: Ti3Al powder is used to manufacture high temperature components like turbine blades, turbocharger wheels, heat exchangers and other parts that operate from 500-800¡«C. It provides an excellent balance of high strength, low density and good oxidation resistance.
Q: How is Ti3Al powder made?
A: Common production methods include gas atomization, plasma atomization, electrode induction melting gas atomization (EIGA) and mechanical alloying. Each process results in different powder characteristics suited for specific applications.
Q: Is Ti3Al powder better than Inconel 718?
A: Ti3Al has lower density, so provides weight savings over Inconel 718. It has higher strength at temperatures above 700¡«C. However, room temperature ductility of Ti3Al is quite low while Inconel 718 can be fabricated and machined easily.
Q: What is the cost of Ti3Al powder?
A: Ti3Al powder costs around $450-750 per kg, which is nearly 5 times more expensive than nickel superalloys and 10 times more than titanium or aluminum powders. The high cost is due to complex processing and limited market demand.
Q: How is Ti3Al powder handled and stored?
A: Like other reactive alloy powders, Ti3Al requires inert gas blanketing and moisture-free storage. Only ceramic, glass or stainless containers should be used. Safety precautions include grounding, ventilation and respiratory PPE.
Q: What are the challenges with using Ti3Al powder?
A: Key limitations are poor room temperature ductility, high material cost, limited number of suppliers, difficulty in machining/fabrication, and lack of joining technologies. Alloy improvements, process developments and component design optimization are required to expand commercial usage.
Q: What is the future outlook for Ti3Al powder?
A: Ti3Al powder usage is forecast to grow significantly in aerospace engines, automotive turbochargers, and high temperature industrial applications. Initiatives to lower costs, improve properties, and mature manufacturing will enable broader adoption.
Contact us now
Please contact us for recent product quotes and stock availability.