Laser-Based Powder Bed Fusion: An In-Depth Exploration
Laser-Based Powder Bed Fusion (LPBF) is one of the most exciting advancements in the realm of additive manufacturing. It allows for the creation of highly complex, intricate parts that are difficult or even impossible to achieve through traditional manufacturing methods. This article will delve deeply into the specifics of LPBF, providing a comprehensive overview, detailed tables, and engaging content to keep you informed and entertained.
Overview of Laser-Based Powder Bed Fusion
Laser-Based Powder Bed Fusion is an additive manufacturing process that uses a high-powered laser to fuse fine metal powders layer by layer. This technique is capable of producing parts with high precision and excellent mechanical properties, making it highly suitable for industries such as aerospace, automotive, and medical devices.
Key Points:
- Utilizes a high-powered laser to fuse metal powders.
- Produces high-precision, complex parts.
- Commonly used in aerospace, automotive, and medical industries.
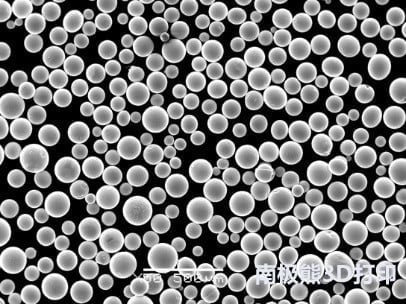
Types, Composition, and Properties of Metal Powders in LPBF
Understanding the different types of metal powders used in LPBF, along with their composition and properties, is crucial for selecting the right material for your application. Below is a detailed table summarizing these aspects.
Types, Composition, and Properties
Metal Powder | Composition | Properties | Characteristics |
---|---|---|---|
Titanium (Ti-6Al-4V) | Ti, Al, V | High strength-to-weight ratio, corrosion-resistant | Ideal for aerospace, medical implants |
Stainless Steel (316L) | Fe, Cr, Ni, Mo | High strength, corrosion-resistant, good weldability | Used in marine applications, medical devices |
Inconel (718) | Ni, Cr, Fe, Nb | High temperature resistance, good mechanical properties | Suitable for aerospace, gas turbines |
Aluminum (AlSi10Mg) | Al, Si, Mg | Lightweight, good thermal conductivity | Used in automotive, aerospace |
Cobalt-Chrome (CoCrMo) | Co, Cr, Mo | High wear resistance, biocompatible | Ideal for dental and orthopedic implants |
Tool Steel (H13) | Fe, Cr, Mo, V | High toughness, wear-resistant | Used in tooling and die-making |
Maraging Steel (1.2709) | Fe, Ni, Co, Mo | Ultra-high strength, good toughness | Suitable for aerospace, tooling |
Copper (Cu) | Cu | Excellent thermal and electrical conductivity | Used in electronics, heat exchangers |
Nickel Alloy (625) | Ni, Cr, Mo, Nb | Corrosion-resistant, high strength | Ideal for marine, chemical processing |
Bronze (CuSn10) | Cu, Sn | High strength, good wear resistance | Used in bearings, bushings |
Applications and Uses of LPBF Metal Powders
Each type of metal powder used in LPBF has unique applications and uses based on its properties and characteristics. Here’s a table detailing the specific applications for each metal powder type.
Applications and Uses
Metal Powder | Applications | Industry |
---|---|---|
Titanium (Ti-6Al-4V) | Aerospace components, medical implants | Aerospace, Medical |
Stainless Steel (316L) | Surgical instruments, marine equipment | Medical, Marine |
Inconel (718) | Jet engine components, gas turbine parts | Aerospace, Energy |
Aluminum (AlSi10Mg) | Automotive parts, aerospace structures | Automotive, Aerospace |
Cobalt-Chrome (CoCrMo) | Dental implants, orthopedic devices | Medical, Dental |
Tool Steel (H13) | Molds, dies, high-temperature tools | Manufacturing, Tooling |
Maraging Steel (1.2709) | High-strength aerospace parts, tooling | Aerospace, Tooling |
Copper (Cu) | Electrical components, heat exchangers | Electronics, Energy |
Nickel Alloy (625) | Marine parts, chemical plant components | Marine, Chemical |
Bronze (CuSn10) | Bearings, bushings | Manufacturing, Automotive |
Specifications, Sizes, Grades, and Standards
For those looking to implement LPBF in their manufacturing processes, understanding the specifications, sizes, grades, and standards of the available metal powders is essential.
Specifications, Sizes, Grades, and Standards
Metal Powder | Specification | Size (μm) | Grade | Standard |
---|---|---|---|---|
Titanium (Ti-6Al-4V) | ASTM F2924 | 15-45 | Grade 5 | ASTM, ISO |
Stainless Steel (316L) | ASTM A276 | 15-53 | 316L | ASTM, ISO |
Inconel (718) | AMS 5662 | 15-45 | 718 | ASTM, ISO |
Aluminum (AlSi10Mg) | DIN EN 1706 | 20-63 | AlSi10Mg | ASTM, ISO |
Cobalt-Chrome (CoCrMo) | ASTM F75 | 15-53 | CoCrMo | ASTM, ISO |
Tool Steel (H13) | ASTM A681 | 20-63 | H13 | ASTM, ISO |
Maraging Steel (1.2709) | AMS 6512 | 15-45 | 1.2709 | ASTM, ISO |
Copper (Cu) | ASTM B170 | 20-63 | C11000 | ASTM, ISO |
Nickel Alloy (625) | ASTM B443 | 15-45 | 625 | ASTM, ISO |
Bronze (CuSn10) | ASTM B103 | 20-63 | CuSn10 | ASTM, ISO |
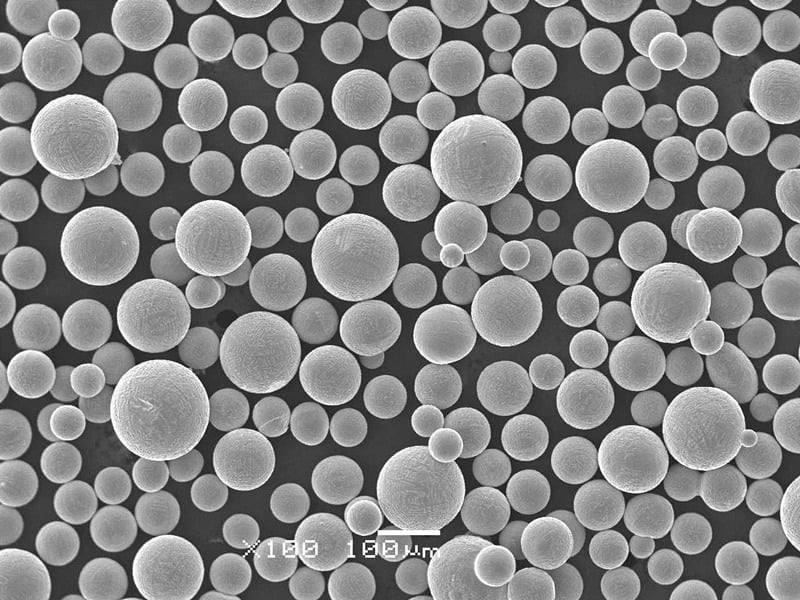
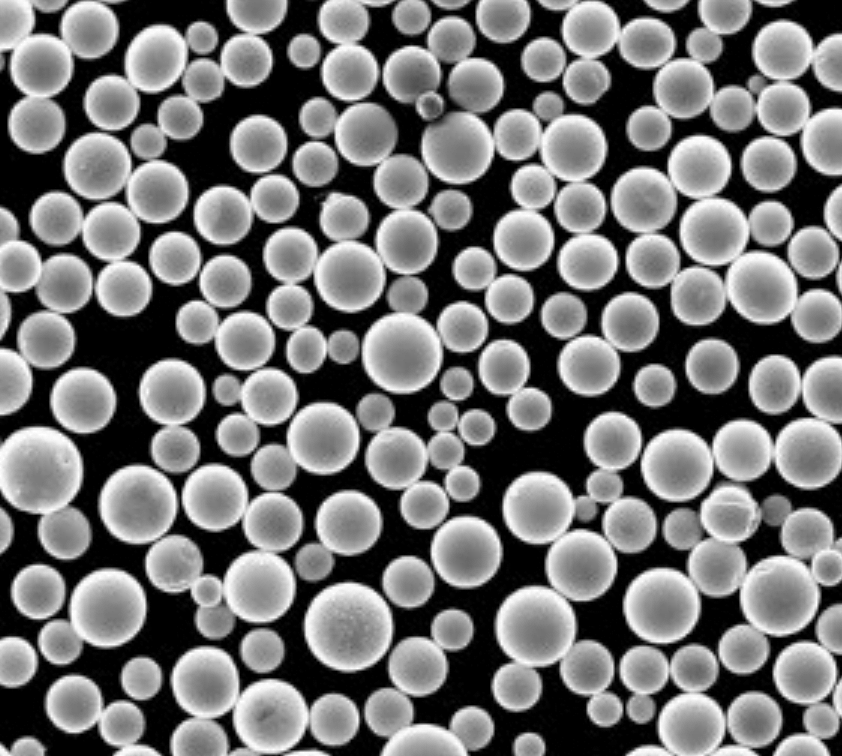
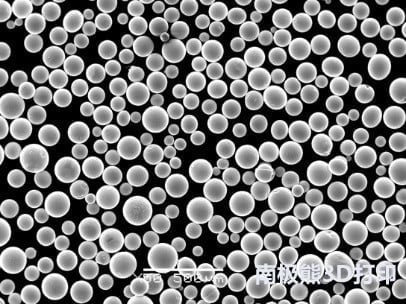
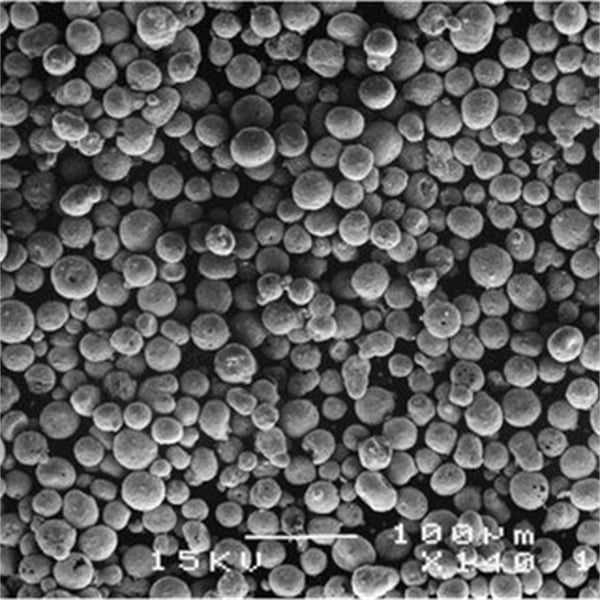
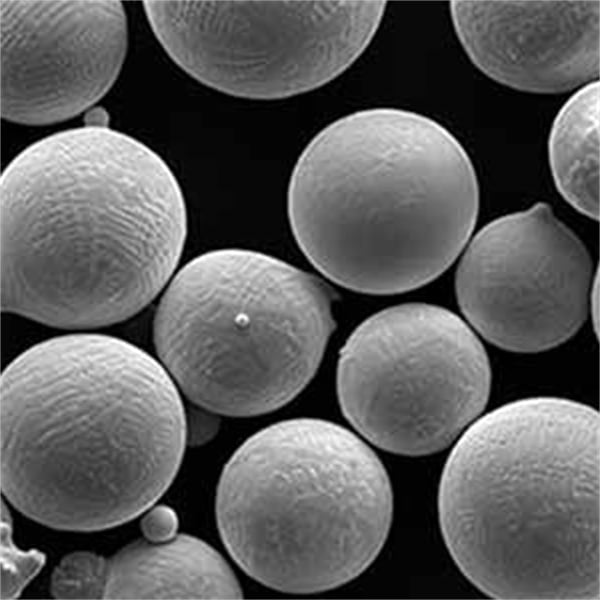
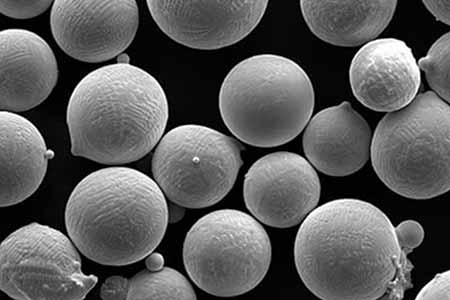
Suppliers and Pricing Details
Finding reliable suppliers and understanding the pricing for LPBF metal powders is critical for budgeting and sourcing materials. Below is a table that outlines some of the top suppliers and their pricing details.
Suppliers and Pricing
Metal Powder | Supplier | Price (per kg) | Notes |
---|---|---|---|
Titanium (Ti-6Al-4V) | AP&C | $300 | High quality, aerospace grade |
Stainless Steel (316L) | Sandvik | $80 | Medical grade, corrosion-resistant |
Inconel (718) | Carpenter Technology | $200 | High-temperature applications |
Aluminum (AlSi10Mg) | Equispheres | $60 | Lightweight, high strength |
Cobalt-Chrome (CoCrMo) | Praxair | $350 | Biocompatible, high wear resistance |
Tool Steel (H13) | Höganäs | $100 | Durable, high toughness |
Maraging Steel (1.2709) | Renishaw | $250 | Ultra-high strength |
Copper (Cu) | GKN Additive | $50 | Excellent conductivity |
Nickel Alloy (625) | EOS | $220 | Corrosion-resistant, high strength |
Bronze (CuSn10) | Höganäs | $70 | High strength, wear resistance |
Pros and Cons, Advantages and Limitations of LPBF
Like any technology, LPBF has its pros and cons. It’s important to weigh these factors to determine if this manufacturing method is right for your specific needs.
Advantages and Limitations
Metal Powder | Advantages | Limitations |
---|---|---|
Titanium (Ti-6Al-4V) | High strength-to-weight ratio, biocompatible | Expensive, difficult to process |
Stainless Steel (316L) | Corrosion-resistant, good weldability | Lower strength compared to other alloys |
Inconel (718) | High temperature resistance, strong | Expensive, difficult to machine |
Aluminum (AlSi10Mg) | Lightweight, good thermal conductivity | Lower strength compared to other metals |
Cobalt-Chrome (CoCrMo) | High wear resistance, biocompatible | Expensive, limited ductility |
Tool Steel (H13) | High toughness, wear-resistant | Prone to cracking under high stress |
Maraging Steel (1.2709) | Ultra-high strength, good toughness | Expensive, complex heat treatment |
Copper (Cu) | Excellent thermal and electrical conductivity | Prone to oxidation, relatively soft |
Nickel Alloy (625) | Corrosion-resistant, high strength | Expensive, difficult to machine |
Bronze (CuSn10) | High strength, good wear resistance | Heavier, prone to oxidation |
Comparing Metal Powders for LPBF
To make an informed decision, it’s essential to compare the different metal powders available for LPBF. Here’s a detailed comparison highlighting key parameters and performance indicators.
Comparison of Metal Powders
Parameter | Titanium (Ti-6Al-4V) | Stainless Steel (316L) | Inconel (718) | Aluminum (AlSi10Mg) | Cobalt-Chrome (CoCrMo) | Tool Steel (H13) | Maraging Steel (1.2709) | Copper (Cu) | Nickel Alloy (625) | Bronze (CuSn10) |
Strength | High | Moderate | High | Moderate | High | High | Ultra-high | Moderate | High | Moderate |
Weight | Low | Moderate | High | Low | High | High | High | Moderate | High | High |
Corrosion Resistance | High | High | High | Moderate | High | Moderate | Moderate | Low | High | Moderate |
Cost | High | Moderate | High | Low | High | Moderate | High | Low | High | Moderate |
Thermal Conductivity | Moderate | Low | Low | High | Low | Low | Low | High | Low | Low |
Electrical Conductivity | Low | Low | Low | Moderate | Low | Low | Low | High | Low | Low |
Biocompatibility | High | High | Low | Low | High | Low | Low | Low | Low | Low |
Wear Resistance | Moderate | Moderate | High | Low | High | High | High | Low | High | High |
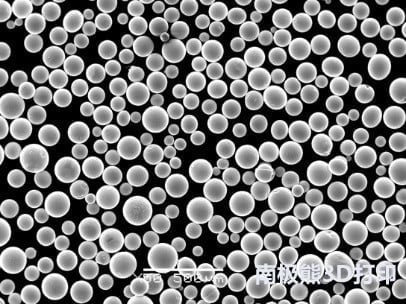
FAQ
Question | Answer |
---|---|
What is Laser-Based Powder Bed Fusion (LPBF)? | LPBF is an additive manufacturing process that uses a high-powered laser to fuse metal powders layer by layer, creating highly precise and complex parts. |
What are the advantages of using LPBF? | LPBF allows for the creation of intricate designs, reduces material waste, and can produce parts with excellent mechanical properties. |
Which industries commonly use LPBF? | LPBF is widely used in aerospace, automotive, medical, and tooling industries. |
What types of metal powders can be used in LPBF? | Common metal powders include titanium, stainless steel, Inconel, aluminum, cobalt-chrome, tool steel, maraging steel, copper, nickel alloys, and bronze. |
What are the limitations of LPBF? | LPBF can be expensive, some materials are difficult to process, and the process can be slower compared to traditional manufacturing methods. |
How does LPBF compare to traditional manufacturing methods? | LPBF allows for more complex and precise designs, reduces material waste, and can be more cost-effective for small production runs, but it can be slower and more expensive for large-scale production. |
What factors should be considered when selecting a metal powder for LPBF? | Consider the mechanical properties, weight, corrosion resistance, cost, thermal and electrical conductivity, biocompatibility, and wear resistance of the metal powder. |
Are there any health and safety concerns with LPBF? | Yes, there are concerns with metal powder handling, laser operation, and ensuring proper ventilation and protective equipment to avoid inhalation of fine particles. |
How do the properties of metal powders affect the final product in LPBF? | The properties of the metal powders, such as strength, corrosion resistance, and thermal conductivity, directly impact the performance, durability, and suitability of the final product for specific applications. |
What are some common post-processing steps for LPBF parts? | Common post-processing steps include heat treatment, surface finishing, machining, and inspection to ensure the part meets the required specifications and standards. |
Conclusion
Laser-Based Powder Bed Fusion is a revolutionary technology that has transformed the way we think about manufacturing. Its ability to create complex, high-precision parts from a wide variety of metal powders makes it an invaluable tool in industries ranging from aerospace to medical devices. By understanding the different metal powders available, their properties, and their applications, you can make informed decisions to optimize your manufacturing processes.
With this comprehensive guide, you’re now equipped with the knowledge to dive deeper into the world of LPBF, select the right materials, and leverage this technology to its fullest potential. Whether you’re a seasoned professional or a newcomer to additive manufacturing, LPBF offers endless possibilities to innovate and create.
About 3DP mETAL
Product Category
CONTACT US
Any questions? Send us a message now! After receiving your message, we will process your request with a whole team.