Overview of Additive Manufacturing Copper
Additive Manufacturing (AM), commonly known as 3D printing, has revolutionized the manufacturing industry. Among the myriad of materials used in AM, copper stands out due to its exceptional electrical and thermal conductivity. Additive Manufacturing Copper‘s inclusion in AM processes has unlocked new potentials in industries such as aerospace, electronics, and automotive, where complex geometries and efficient performance are paramount.
In this comprehensive guide, we delve into the specifics of additive manufacturing with copper, exploring various copper powder models, their properties, applications, specifications, and more. Our aim is to provide a detailed, engaging, and SEO-optimized resource for enthusiasts and professionals alike.
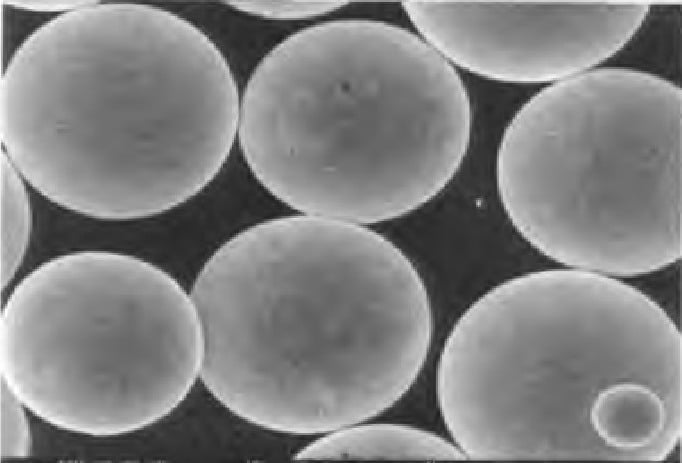
Types and Properties of Copper Powders in Additive Manufacturing
Understanding the different copper powder models is crucial for selecting the right material for your application. Below is a detailed table showcasing specific copper powder models, their composition, properties, and characteristics.
Copper Powder Model | Composition | Properties | Characteristics |
---|---|---|---|
CuCr1Zr | Copper, Chromium, Zirconium | High strength, good thermal conductivity, excellent wear resistance | Ideal for high-temperature applications and components requiring high strength and conductivity |
CuNi2SiCr | Copper, Nickel, Silicon, Chromium | Enhanced mechanical properties, good corrosion resistance | Used in applications demanding high strength and excellent corrosion resistance |
CuSn10 | Copper, Tin | Good thermal and electrical conductivity, moderate strength | Widely used in electrical connectors and bearings due to its balanced properties |
CuCrZr | Copper, Chromium, Zirconium | Superior thermal conductivity, high strength | Suitable for applications in welding and electrical contacts |
CuAl8Fe3 | Copper, Aluminum, Iron | High tensile strength, good corrosion resistance | Often used in marine and aerospace industries for its strength and durability |
CuBe2 | Copper, Beryllium | Excellent electrical and thermal conductivity, high fatigue strength | Preferred for electronic connectors and components requiring high precision and fatigue resistance |
CuSn5Zn5Pb5 | Copper, Tin, Zinc, Lead | Good machinability, moderate strength | Utilized in bearings and bushings where good machinability is essential |
CuNi3Si | Copper, Nickel, Silicon | High strength, excellent wear resistance | Suitable for components under high stress and wear conditions |
CuAg0.1 | Copper, Silver | Enhanced electrical conductivity, high thermal stability | Used in electrical applications where superior conductivity is required |
Cu-OF | Oxygen-free Copper | Excellent electrical and thermal conductivity | Ideal for high-purity applications such as semiconductor manufacturing and high-frequency electronic devices |
Applications of Additive Manufacturing Copper
The versatility of copper makes it an invaluable material in numerous industries. The following table outlines various applications of copper in additive manufacturing, highlighting the benefits in each sector.
Application Area | Description | Benefits |
---|---|---|
Electronics | Production of heat sinks, connectors, and complex circuitry | Improved electrical conductivity, reduced weight |
Aerospace | Manufacturing of engine components, heat exchangers, and lightweight structures | High thermal management, reduced manufacturing costs |
Automotive | Creation of intricate engine parts, cooling systems, and electrical components | Enhanced performance, lighter components |
Medical Devices | Fabrication of MRI components, surgical instruments, and prosthetics | High biocompatibility, precision in complex designs |
Energy | Production of components for solar panels, wind turbines, and battery systems | Superior electrical and thermal properties |
Telecommunications | Manufacture of waveguides, antennas, and connectors | Improved signal strength and quality |
Industrial Machinery | Development of wear-resistant parts, custom tooling, and cooling systems | Increased durability, efficiency in manufacturing |
Consumer Goods | Custom-made jewelry, household appliances, and decorative items | Unique designs, high aesthetic value |
Defense | Production of components for communication devices, weapon systems, and defense infrastructure | Enhanced performance, reliability in critical applications |
Specifications, Sizes, Grades, and Standards of Copper Powders
Selecting the right copper powder involves considering various specifications and standards. The table below provides a detailed overview of the specifications, sizes, grades, and standards of different copper powders used in additive manufacturing.
Copper Powder Model | Particle Size | Grade | Standard |
---|---|---|---|
CuCr1Zr | 15-45 µm | Grade A | ASTM B506 |
CuNi2SiCr | 10-50 µm | Grade B | AMS 4596 |
CuSn10 | 20-60 µm | Grade C | ASTM B271 |
CuCrZr | 15-50 µm | Grade A | EN 12163 |
CuAl8Fe3 | 20-70 µm | Grade B | ASTM B505 |
CuBe2 | 10-45 µm | Grade A | ASTM B196 |
CuSn5Zn5Pb5 | 25-75 µm | Grade C | EN 1982 |
CuNi3Si | 15-55 µm | Grade B | ASTM B422 |
CuAg0.1 | 10-50 µm | Grade A | ASTM B189 |
Cu-OF | 10-40 µm | Grade A | ASTM B170 |
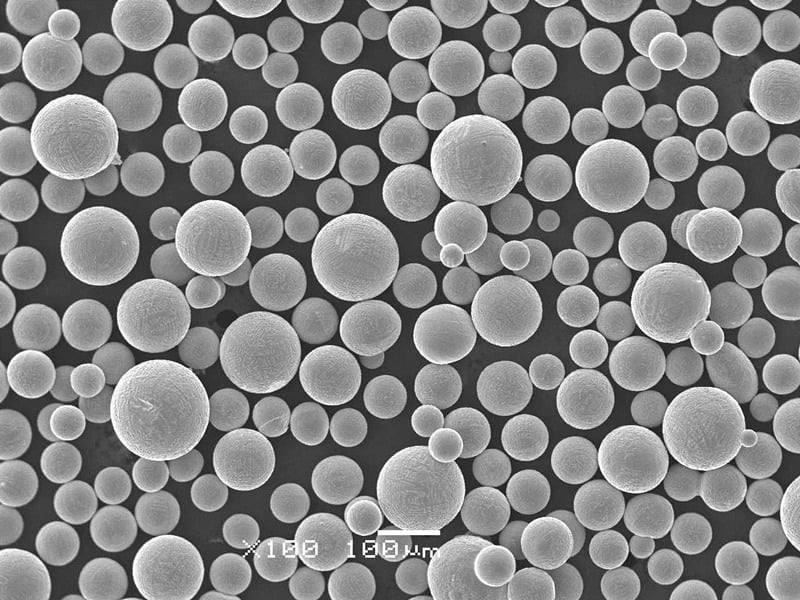
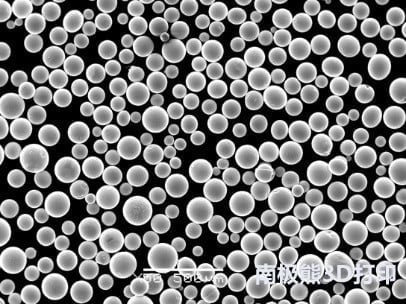
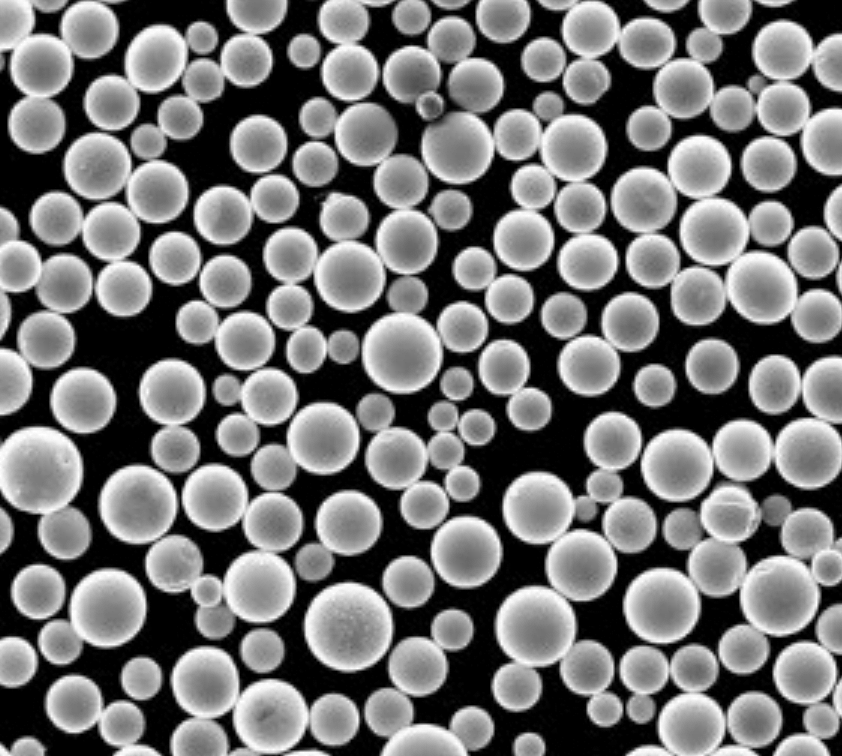
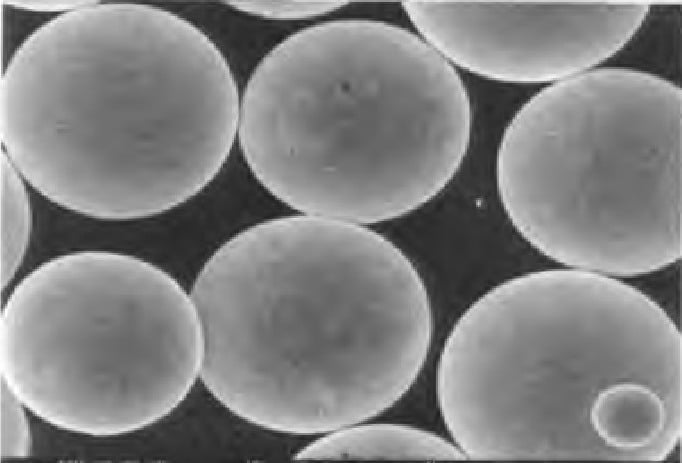
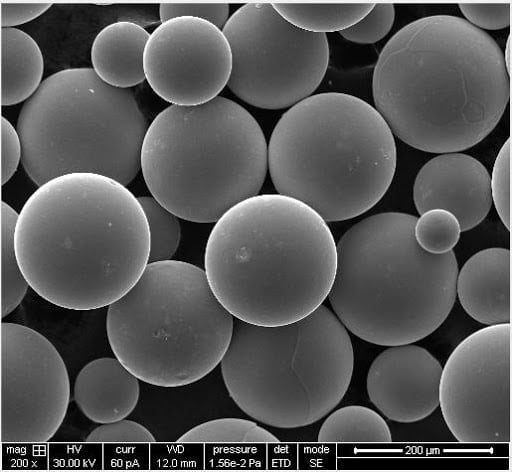
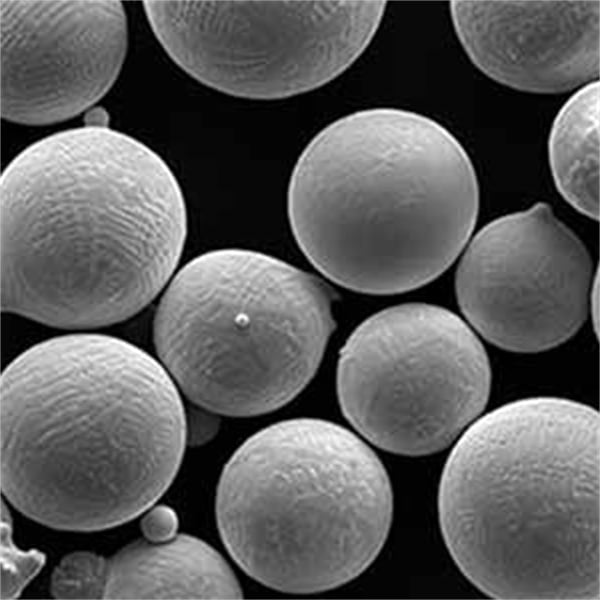
Suppliers and Pricing of Copper Powders
The availability and pricing of copper powders can vary significantly based on supplier and market conditions. Here’s a table providing insights into suppliers and pricing details for different copper powders.
Supplier | Copper Powder Model | Price (per kg) | Location |
---|---|---|---|
Höganäs | CuCr1Zr | $120 | Sweden |
GKN Powder Metallurgy | CuNi2SiCr | $130 | USA |
ECKA Granules | CuSn10 | $115 | Germany |
Kymera International | CuCrZr | $125 | USA |
Sandvik | CuAl8Fe3 | $135 | Sweden |
Advanced Powder Tech | CuBe2 | $140 | China |
Metal Powder Works | CuSn5Zn5Pb5 | $110 | India |
LPW Technology | CuNi3Si | $130 | UK |
American Elements | CuAg0.1 | $145 | USA |
Tekna | Cu-OF | $150 | Canada |
Pros and Cons of Additive Manufacturing Copper
Using copper in additive manufacturing comes with its set of advantages and limitations. The table below compares these aspects to help you make an informed decision.
Aspect | Advantages | Limitations |
---|---|---|
Thermal Conductivity | Excellent for heat dissipation in electronic and industrial applications | Managing thermal properties during printing can be challenging |
Electrical Conductivity | Ideal for producing high-efficiency electrical components | Potential oxidation if not properly handled |
Strength and Durability | High mechanical strength, especially in alloys | Can be more brittle compared to other metals when not alloyed |
Corrosion Resistance | Good resistance to corrosion in various environments | Some copper alloys may require additional coatings for enhanced corrosion resistance |
Manufacturing Flexibility | Enables the creation of complex geometries and intricate designs | Requires precise control over printing parameters to avoid defects |
Cost Efficiency | Reduces material waste and allows for on-demand production | Initial setup and material costs can be higher compared to traditional manufacturing |
Environmental Impact | Potential for recycling and reduced waste | Energy-intensive processes can have a higher environmental footprint |
Customization | High level of customization and rapid prototyping capabilities | Customization can lead to longer production times for single parts |
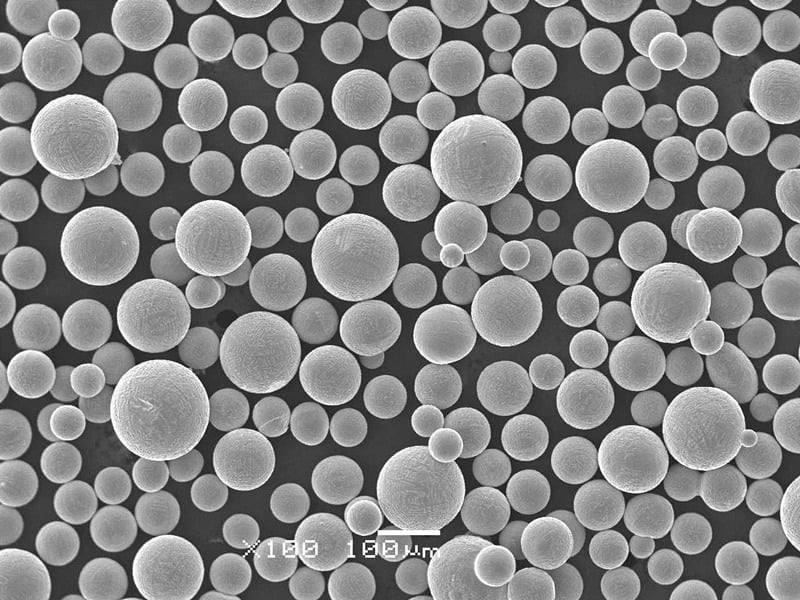
Applications of Additive Manufacturing Copper in Various Industries
Copper’s unique properties make it highly suitable for a wide range of industrial applications. This section explores in greater detail the impact of copper additive manufacturing across different sectors.
Electronics
In the electronics industry, the demand for miniaturization and improved performance has never been higher. Additive manufacturing with copper enables the production of components such as heat sinks, connectors, and complex circuitry with unparalleled precision. The excellent electrical conductivity of copper ensures efficient power distribution, while its thermal properties aid in effective heat dissipation, crucial for maintaining the performance and longevity of electronic devices.
Aerospace
The aerospace sector benefits immensely from the use of copper in additive manufacturing. Components such as engine parts and heat exchangers require materials that can withstand extreme temperatures while maintaining structural integrity. Copper’s thermal management capabilities make it an ideal choice. Additionally, the ability to create lightweight yet strong structures helps in reducing the overall weight
of aerospace components, leading to improved fuel efficiency and performance.
Automotive
In the automotive industry, the need for innovative, high-performance materials is constant. Copper additive manufacturing allows for the creation of intricate engine parts, efficient cooling systems, and reliable electrical components. The enhanced thermal and electrical properties of copper contribute to better performance and durability, making vehicles more reliable and efficient.
Medical Devices
Medical devices demand precision, biocompatibility, and reliability. Copper’s properties align perfectly with these requirements. Additive manufacturing enables the production of intricate MRI components, surgical instruments, and custom prosthetics with high precision. Copper’s excellent biocompatibility ensures that these devices are safe for use within the human body, while its conductivity properties are beneficial in imaging and diagnostic tools.
Energy
The energy sector is continually evolving, with a focus on sustainability and efficiency. Copper additive manufacturing plays a pivotal role in the production of components for solar panels, wind turbines, and battery systems. Copper’s superior electrical and thermal properties enhance the efficiency and longevity of these components, contributing to more sustainable energy solutions.
Telecommunications
Telecommunications rely heavily on the quality of signal transmission. Copper’s high conductivity makes it an excellent material for manufacturing waveguides, antennas, and connectors. Additive manufacturing allows for the creation of complex geometries and custom designs, improving signal strength and quality, which is crucial for modern communication networks.
Industrial Machinery
In industrial machinery, wear-resistant parts, custom tooling, and efficient cooling systems are essential. Copper’s durability and thermal properties make it an ideal material for these applications. Additive manufacturing facilitates the production of parts with complex designs and enhanced performance, increasing the efficiency and lifespan of industrial machinery.
Consumer Goods
The consumer goods sector benefits from copper’s aesthetic and functional properties. Custom-made jewelry, household appliances, and decorative items produced through additive manufacturing can achieve unique designs and high aesthetic value. Copper’s antimicrobial properties also make it suitable for producing items that require high hygiene standards.
Defense
The defense industry demands materials that provide reliability and performance in critical applications. Copper additive manufacturing allows for the production of communication devices, weapon systems, and defense infrastructure components that meet these stringent requirements. The high conductivity and durability of copper ensure these components perform reliably under extreme conditions.
Detailed Comparison: Additive Manufacturing Copper vs. Traditional Manufacturing
Comparing additive manufacturing with copper to traditional manufacturing methods highlights the advantages and challenges of this innovative approach.
Aspect | Additive Manufacturing Copper | Traditional Manufacturing |
---|---|---|
Design Flexibility | Allows for complex and intricate designs | Limited by tooling and machining capabilities |
Material Utilization | Efficient, reduces waste | Higher material waste due to subtractive processes |
Production Time | Faster for prototypes and small batches | Longer setup and production times for prototypes and customization |
Cost | Higher initial setup costs, cost-effective for small batches | Lower initial costs, more cost-effective for mass production |
Customization | High level of customization | Limited customization options |
Strength and Durability | Comparable, with specific alloys offering enhanced properties | Proven track record with well-understood material properties |
Environmental Impact | Potential for recycling, reduced waste | Higher waste generation, energy-intensive processes |
Precision and Accuracy | High precision and accuracy for complex geometries | High precision, but limited by tooling capabilities |
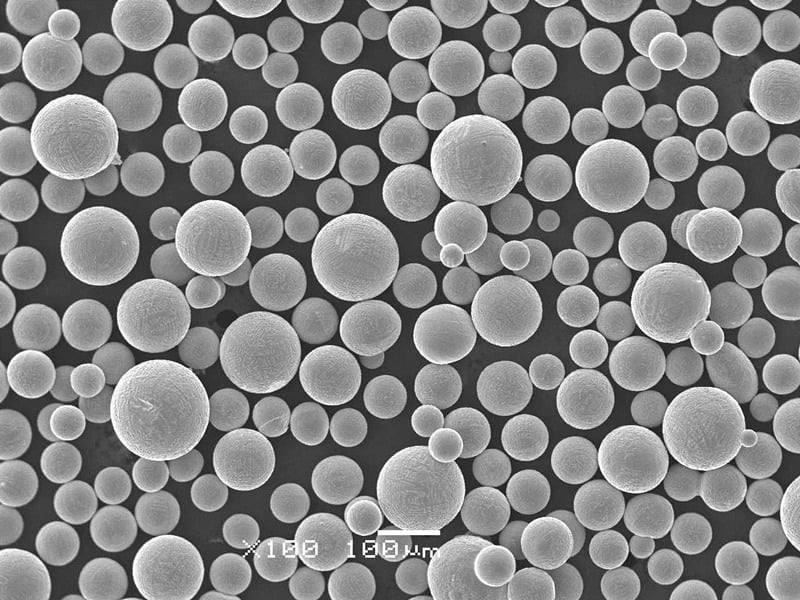
FAQ
Q: What are the primary benefits of using copper in additive manufacturing?
Copper offers excellent electrical and thermal conductivity, making it ideal for applications in electronics, aerospace, and automotive industries. Its versatility and performance enhance product efficiency and durability.
Q: Are there any challenges associated with using copper in additive manufacturing?
Yes, challenges include managing thermal properties during printing, potential oxidation, and ensuring precise control over printing parameters to avoid defects.
Q: How does additive manufacturing with copper compare to traditional manufacturing methods?
Additive manufacturing allows for greater design flexibility, reduced material waste, and faster production times for prototypes and small batches. However, it can have higher initial setup costs compared to traditional methods.
Q: What are some common applications of additive manufacturing copper?
Common applications include electronic components, aerospace parts, automotive engine parts, medical devices, energy systems, telecommunications equipment, industrial machinery, consumer goods, and defense components.
Q: What are the environmental benefits of using copper in additive manufacturing?
Additive manufacturing with copper reduces material waste and allows for recycling of unused powder. This process can contribute to more sustainable manufacturing practices.
Q: How do I choose the right copper powder for my application?
Consider factors such as the required mechanical properties, thermal and electrical conductivity, corrosion resistance, and specific application needs. Consult the specifications and standards for each copper powder model to make an informed decision.
Conclusion
Additive manufacturing with copper is transforming the way industries approach design, production, and efficiency. With its superior electrical and thermal properties, copper enables the creation of complex and high-performance components across various sectors. Despite the challenges, the advantages of using copper in additive manufacturing are substantial, offering new possibilities for innovation and sustainability.
By understanding the different copper powder models, their properties, applications, and the pros and cons of additive manufacturing, you can make informed decisions and leverage this technology to its full potential. Whether you’re in electronics, aerospace, automotive, or any other industry, additive manufacturing copper is paving the way for a more efficient and advanced future.
About 3DP mETAL
Product Category
CONTACT US
Any questions? Send us a message now! After receiving your message, we will process your request with a whole team.