Overview of Atomization
Atomization is a process widely used in various industries to convert bulk liquid into a spray or powder form through the application of energy. This method is crucial in fields such as pharmaceuticals, metallurgy, and chemical engineering due to its ability to create fine, uniform particles. Understanding atomization is essential for optimizing processes that require precise particle sizes and distributions.
What is Atomization?
At its core, atomization involves breaking down a liquid into smaller droplets or particles. This can be achieved through different methods, including ultrasonic, hydraulic, pneumatic, and electrostatic atomization. Each technique has unique characteristics and applications, making atomization a versatile tool in manufacturing and processing.
Key Aspects of Atomization
- Types of Atomization: Various methods such as ultrasonic, pneumatic, and hydraulic.
- Applications: Utilized in industries like pharmaceuticals, food processing, and metallurgy.
- Benefits: Enhanced control over particle size and distribution, improved product quality.
- Challenges: Equipment cost, maintenance, and the need for precise control parameters.
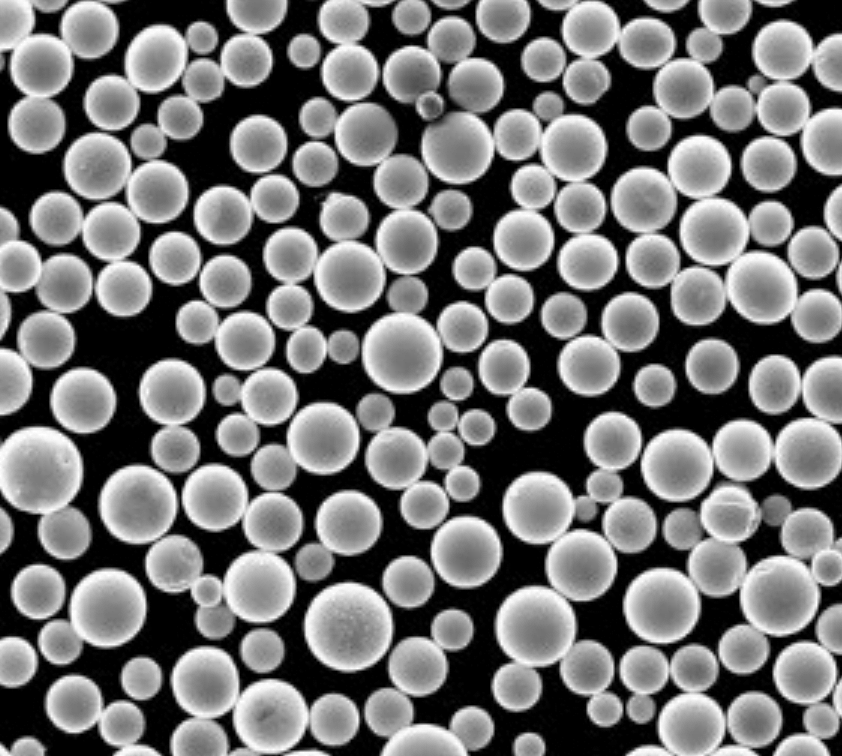
Types of Atomization Methods
Different atomization techniques cater to specific industrial needs, from creating metal powders to producing fine mists for cooling or coating. Here, we’ll dive into the most common atomization methods:
Ultrasonic Atomization
This method uses high-frequency sound waves to create vibrations in the liquid, causing it to break into fine droplets. It’s particularly useful for creating uniform particle sizes.
Properties:
- Particle Size: 1-10 microns
- Applications: Drug delivery systems, spray drying
- Advantages: High uniformity, low energy consumption
- Disadvantages: Limited to low-viscosity liquids
Pneumatic Atomization
Pneumatic atomization involves using compressed air to atomize liquids. This technique is common in spray painting and coating applications.
Properties:
- Particle Size: 10-50 microns
- Applications: Paint spraying, agricultural spraying
- Advantages: Versatile, suitable for various viscosities
- Disadvantages: Higher energy consumption compared to ultrasonic
Hydraulic Atomization
In hydraulic atomization, high-pressure liquid is forced through a small nozzle, creating fine droplets. It’s widely used in fuel injection systems and industrial spray applications.
Properties:
- Particle Size: 50-200 microns
- Applications: Fuel injection, fire suppression systems
- Advantages: Simple setup, effective for high-viscosity fluids
- Disadvantages: Nozzle wear, high pressure requirements
Electrostatic Atomization
This method uses electrostatic forces to charge liquid particles, which then disperse due to repulsion between like charges. It’s highly efficient for coating and agricultural applications.
Properties:
- Particle Size: 1-50 microns
- Applications: Coating, agricultural spraying
- Advantages: High transfer efficiency, reduced overspray
- Disadvantages: Sensitive to environmental conditions
Metal Powder Models and Their Descriptions
In metallurgy, atomization is a key process for producing metal powders with specific properties required for various applications. Here are some notable metal powder models:
1. Stainless Steel 316L Powder
Composition:
- Chromium: 16-18%
- Nickel: 10-14%
- Molybdenum: 2-3%
Properties:
- Corrosion resistance
- High tensile strength
Applications:
- Medical implants
- Aerospace components
2. Titanium Alloy Powder (Ti-6Al-4V)
Composition:
- Titanium: 90%
- Aluminum: 6%
- Vanadium: 4%
Properties:
- Lightweight
- High strength-to-weight ratio
Applications:
- Aerospace parts
- Biomedical devices
3. Copper Powder
Composition:
- Copper: 99.9%
Properties:
- Excellent electrical conductivity
- High thermal conductivity
Applications:
- Electrical components
- Heat exchangers
4. Aluminum Alloy Powder (AlSi10Mg)
Composition:
- Aluminum: 90%
- Silicon: 10%
- Magnesium: 0.4-0.6%
Properties:
- Lightweight
- Good castability
Applications:
- Automotive parts
- Structural components
5. Nickel Alloy Powder (Inconel 718)
Composition:
- Nickel: 50-55%
- Chromium: 17-21%
- Iron: 4.75-5.5%
- Niobium: 4.75-5.5%
Properties:
- High temperature resistance
- Corrosion resistance
Applications:
- Gas turbines
- Jet engines
6. Iron Powder
Composition:
- Iron: 99.5%
Properties:
- High magnetic properties
- Good compressibility
Applications:
- Powder metallurgy
- Magnetic materials
7. Cobalt-Chromium Alloy Powder (CoCrMo)
Composition:
- Cobalt: 60%
- Chromium: 27-30%
- Molybdenum: 5-7%
Properties:
- High wear resistance
- Biocompatible
Applications:
- Dental implants
- Orthopedic implants
8. Tantalum Powder
Composition:
- Tantalum: 99.9%
Properties:
- High melting point
- Corrosion resistance
Applications:
- Medical devices
- Electronics
9. Molybdenum Powder
Composition:
- Molybdenum: 99.9%
Properties:
- High temperature stability
- Good thermal conductivity
Applications:
- High-temperature furnaces
- Electronics
10. Magnesium Alloy Powder
Composition:
- Magnesium: 90%
- Aluminum: 9%
- Zinc: 1%
Properties:
- Lightweight
- High strength-to-weight ratio
Applications:
- Automotive industry
- Aerospace components
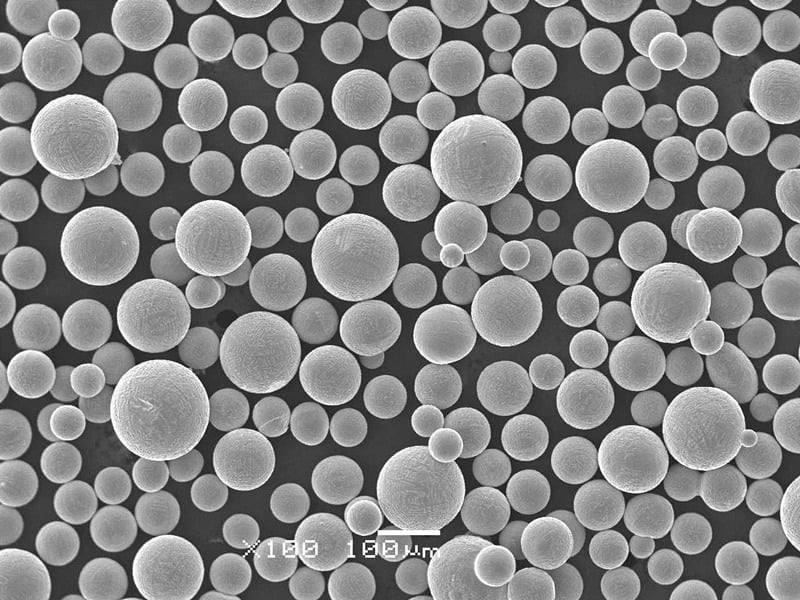
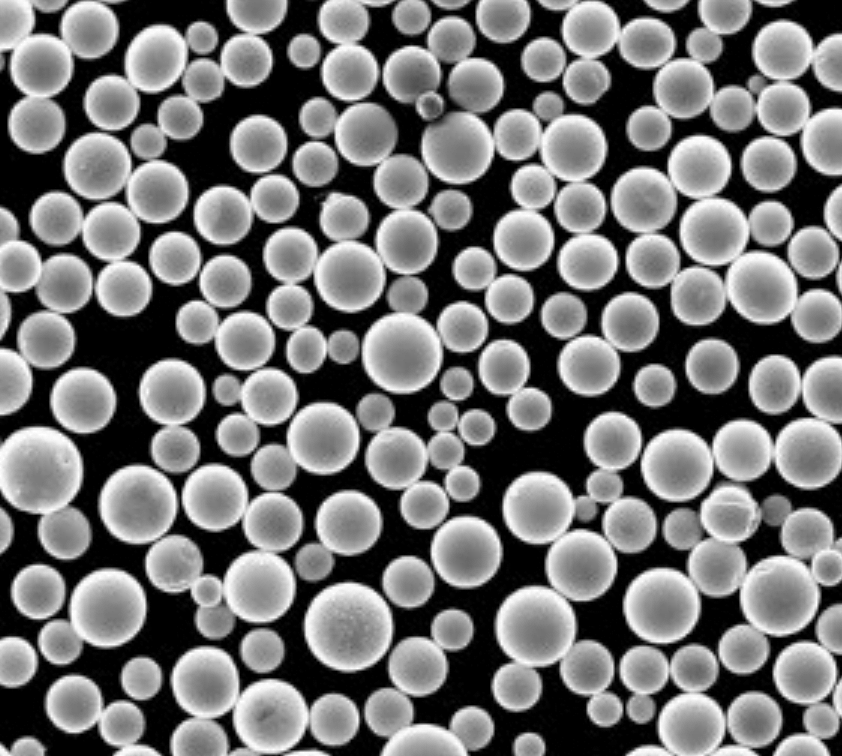
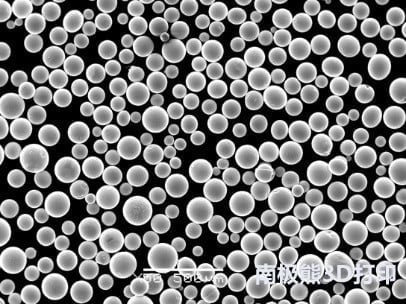
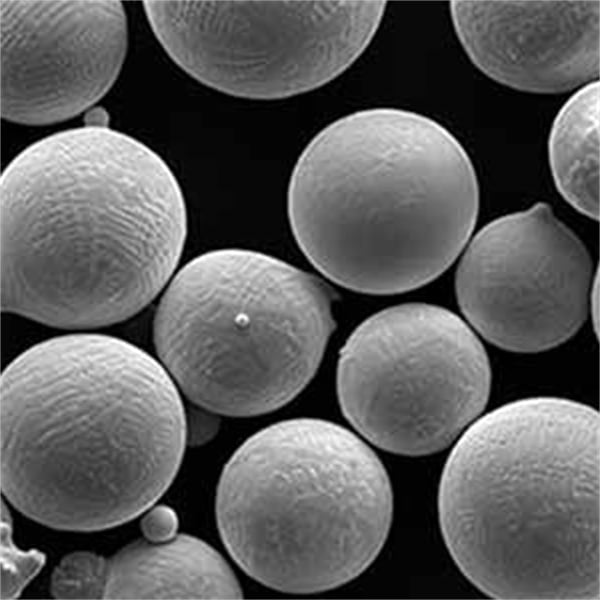
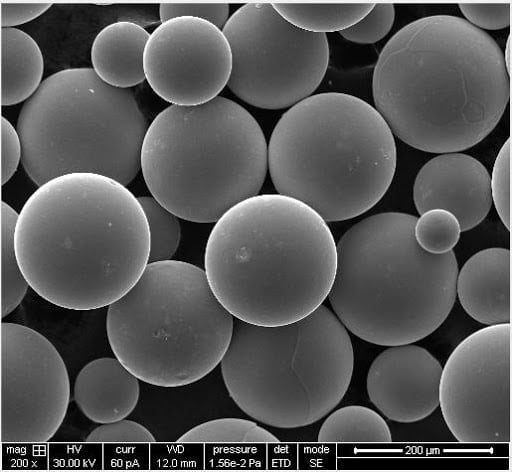
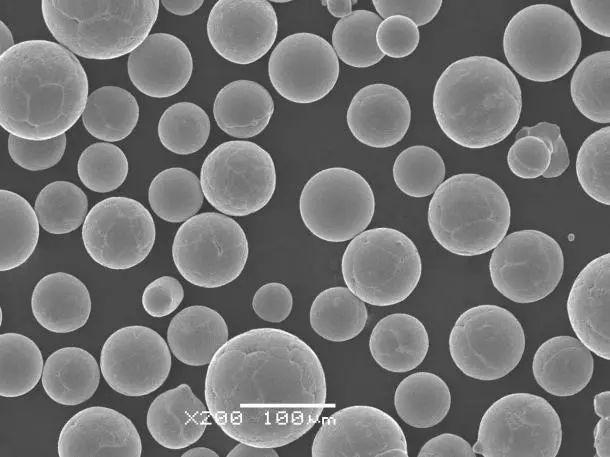
Applications of Atomization
Atomization finds applications across a diverse range of industries. Here are some key sectors where atomization plays a crucial role:
Pharmaceutical Industry
Atomization is used in the production of fine powders for inhalers, enhancing drug delivery efficiency.
Food and Beverage Industry
In this industry, atomization is used for spray drying, which helps in creating powdered forms of products like milk, coffee, and spices.
Metallurgy
Atomization is essential for producing metal powders used in additive manufacturing and powder metallurgy.
Agriculture
Pneumatic and electrostatic atomization techniques are used for pesticide and fertilizer spraying, ensuring even distribution and minimizing waste.
Coatings and Paints
Atomization techniques provide uniform coating layers, enhancing the quality and durability of the finish.
Fuel Injection Systems
Hydraulic atomization is used in fuel injectors to create fine fuel mist, improving combustion efficiency.
Specifications, Sizes, Grades, Standards
When selecting metal powders or atomization equipment, understanding specifications, sizes, grades, and standards is crucial.
Metal Powders
Metal Powder | Particle Size | Grade | Standard |
---|---|---|---|
Stainless Steel 316L | 15-45 microns | ASTM F138 | ISO 5832-1 |
Titanium Alloy (Ti-6Al-4V) | 20-53 microns | Grade 23 | ASTM B348 |
Copper | 25-45 microns | C11000 | ASTM B170 |
Aluminum Alloy (AlSi10Mg) | 10-45 microns | EN AW-6061 | ISO 3522 |
Nickel Alloy (Inconel 718) | 15-53 microns | AMS 5662 | ASTM B637 |
Iron | 20-50 microns | AISI 1008 | ASTM B241 |
Cobalt-Chromium (CoCrMo) | 15-45 microns | F75 | ASTM F1537 |
Tantalum | 10-45 microns | ASTM F560 | ISO 13782 |
Molybdenum | 15-45 microns | Mo1 | ASTM B386 |
Magnesium Alloy | 20-50 microns | AZ91D | ASTM B403 |
Atomization Equipment
Equipment Type | Specification | Standard |
---|---|---|
Ultrasonic Atomizer | Frequency: 20 kHz | ASTM E1138 |
Pneumatic Atomizer | Air Pressure: 1-5 bar | ISO 12100 |
Hydraulic Atomizer | Pressure: 50-200 bar | ISO 5167 |
Electrostatic Atomizer | Voltage: 10-30 kV | ASTM D618 |
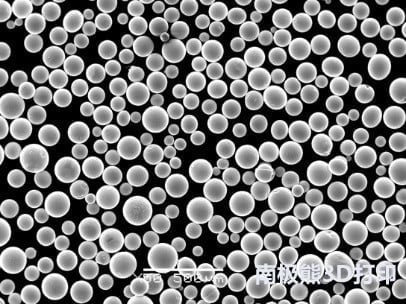
Suppliers and Pricing Details
Finding the right supplier and understanding pricing details is essential for businesses looking to implement atomization processes.
Metal Powder Suppliers
Supplier | Metal Powder | Price (per kg) | Contact Information |
---|---|---|---|
Advanced Powder & Coatings | Stainless Steel 316L | $100 | www.apc.com |
Global Titanium | Titanium Alloy (Ti-6Al-4V) | $300 | www.globaltitanium.com |
Copper Industries Inc. | Copper | $50 | www.copperindustries.com |
Alumetal Corp. | Aluminum Alloy (AlSi10Mg) | $70 | www.alumetalcorp.com |
Superalloys Inc. | Nickel Alloy (Inconel 718) | $200 | www.superalloys.com |
Atomization Equipment Suppliers
Supplier | Equipment Type | Price Range | Contact Information |
---|---|---|---|
Atomizer World | Ultrasonic Atomizer | $10,000 – $50,000 | www.atomizerworld.com |
SprayTech Solutions | Pneumatic Atomizer | $5,000 – $25,000 | www.spraytechsolutions.com |
Hydraulic Systems Inc. | Hydraulic Atomizer | $15,000 – $60,000 | www.hydraulicsystems.com |
ElectroStatic Inc. | Electrostatic Atomizer | $20,000 – $80,000 | www.electrostaticinc.com |
Comparing Pros and Cons of Atomization Methods
Ultrasonic Atomization
Pros:
- High uniformity
- Low energy consumption
- Suitable for fine particles
Cons:
- Limited to low-viscosity liquids
- Higher initial cost
Pneumatic Atomization
Pros:
- Versatile
- Suitable for various viscosities
Cons:
- Higher energy consumption
- Nozzle clogging issues
Hydraulic Atomization
Pros:
- Simple setup
- Effective for high-viscosity fluids
Cons:
- Nozzle wear
- High pressure requirements
Electrostatic Atomization
Pros:
- High transfer efficiency
- Reduced overspray
Cons:
- Sensitive to environmental conditions
- Requires precise control
Advantages of Atomization
Atomization offers several advantages across different industries:
Enhanced Particle Control
Atomization allows for precise control over particle size and distribution, which is critical in applications like pharmaceuticals and additive manufacturing.
Improved Product Quality
By creating uniform particles, atomization improves the consistency and quality of the final product, whether it’s a metal powder or a food ingredient.
Versatility
With multiple methods available, atomization can be adapted to suit various liquids and applications, from low-viscosity solutions to high-viscosity suspensions.
Energy Efficiency
Some atomization methods, like ultrasonic atomization, are energy efficient, reducing operational costs over time.
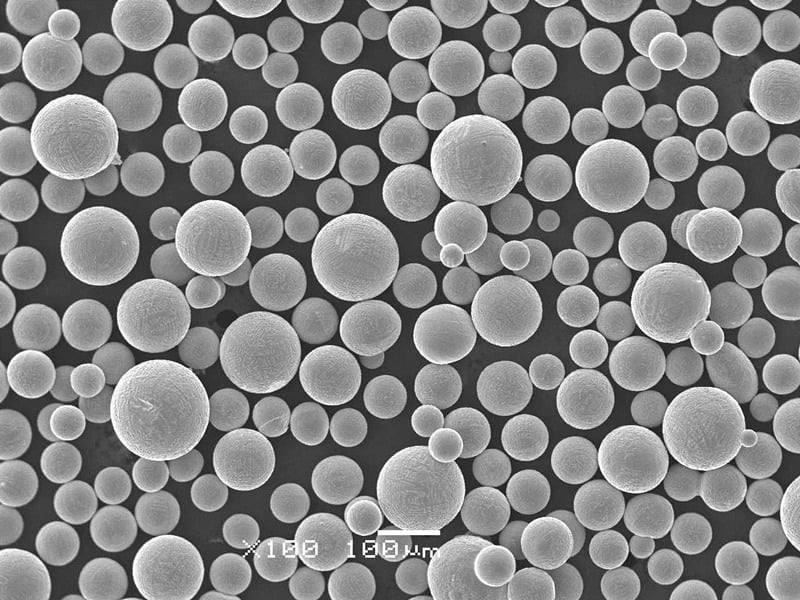
Disadvantages of Atomization
Despite its many benefits, atomization also presents some challenges:
High Initial Costs
The equipment required for atomization, especially advanced systems like ultrasonic and electrostatic atomizers, can be expensive.
Maintenance Requirements
Atomizers, particularly hydraulic and pneumatic types, require regular maintenance to prevent issues like nozzle clogging and wear.
Complex Control Systems
Methods like electrostatic atomization need precise control systems to maintain efficiency and effectiveness, which can complicate the setup and operation.
Environmental Sensitivity
Some atomization techniques are sensitive to environmental conditions like humidity and temperature, affecting their performance and reliability.
FAQ
What is atomization used for?
Atomization is used to create fine droplets or particles from a liquid. It is widely applied in industries such as pharmaceuticals, metallurgy, food processing, and agriculture to improve product quality and process efficiency.
What are the different types of atomization?
The main types of atomization include ultrasonic, pneumatic, hydraulic, and electrostatic atomization. Each method has its own advantages, disadvantages, and specific applications.
Which atomization method is the most energy-efficient?
Ultrasonic atomization is generally considered the most energy-efficient method due to its low power consumption and high particle uniformity.
Can atomization be used for high-viscosity liquids?
Yes, hydraulic atomization is particularly effective for high-viscosity liquids, making it suitable for applications like fuel injection and industrial spraying.
What are the main challenges of using atomization?
The primary challenges include high initial equipment costs, maintenance requirements, the need for precise control systems, and sensitivity to environmental conditions.
How does atomization improve product quality?
By producing uniform particles, atomization enhances the consistency and quality of products. This is crucial in industries like pharmaceuticals, where precise dosages and delivery methods are essential.
About 3DP mETAL
Product Category
CONTACT US
Any questions? Send us a message now! After receiving your message, we will process your request with a whole team.