Overview of Binder Jetting Additive Manufacturing
Binder jetting is a revolutionary additive manufacturing (AM) process that’s turning heads in the manufacturing industry. Imagine a printer, but instead of ink, it spits out a liquid binder onto a bed of powder. This binder acts like glue, sticking the powder particles together to form the shape of your desired object, layer by layer. It’s like building a sandcastle, but with metal, ceramic, or even sand!
Unlike other AM techniques that melt or fuse materials, binder jetting is more like traditional printing. This makes it incredibly fast and efficient, capable of producing complex parts in volumes that were once unimaginable. It’s like the turbocharged version of 3D printing.
Metal Powders Used in Binder Jetting
Binder jetting is particularly well-suited for metal parts. The type of metal powder used significantly impacts the final product’s properties. Let’s explore some common metal powders used in this process:
Metal Powder | Description |
---|---|
Stainless Steel Powder | Known for its corrosion resistance and durability, stainless steel is a popular choice for various applications. |
Aluminum Powder | Lightweight and strong, aluminum powder is ideal for aerospace and automotive components. |
Titanium Powder | Renowned for its high strength-to-weight ratio, titanium powder is used in medical implants and aerospace parts. |
Inconel Powder | Offering excellent resistance to high temperatures and corrosion, Inconel is used in demanding environments. |
Nickel Alloy Powder | Known for its strength and resistance to extreme conditions, nickel alloys are used in various industries. |
Cobalt Chrome Powder | Often used in dental and medical implants due to its biocompatibility and strength. |
Copper Powder | Highly conductive, copper powder is used in electronics and heat exchange applications. |
Iron Powder | A versatile metal powder used in various applications, from tooling to automotive parts. |
Maraging Steel Powder | Offering exceptional strength and toughness, maraging steel is used in high-performance applications. |
Tool Steel Powder | Known for its hardness and wear resistance, tool steel is used in cutting tools and molds. |
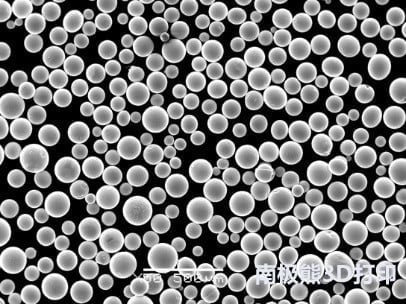
Applications of Binder Jetting
Binder jetting’s versatility shines through in its wide range of applications. From prototyping to large-scale production, this technology is making waves across industries:
Industry | Applications |
---|---|
Automotive | Engine components, tooling, jigs and fixtures |
Aerospace | Structural components, turbine blades, tooling |
Medical | Implants, dental prosthetics, surgical instruments |
Oil and Gas | Downhole tools, pump components, tooling |
Consumer Goods | Jewelry, fashion accessories, home decor |
Specifications and Considerations
Binder jetting offers flexibility in terms of part size, resolution, and material properties. However, there are essential factors to consider:
Specification | Details |
---|---|
Build Volume | Varies depending on the machine, but can range from small desktop models to large industrial systems. |
Layer Thickness | Typically ranges from 20 to 100 microns, affecting part resolution and build time. |
Surface Finish | Generally requires post-processing to achieve desired surface quality. |
Mechanical Properties | Dependent on the metal powder and sintering process. |
Cost | Varies based on machine, material, and part complexity. |
Suppliers and Pricing
The binder jetting market is growing rapidly, with several key players offering equipment, materials, and services. Pricing can vary significantly based on factors such as machine size, material type, and production volume.
Supplier | Focus |
---|---|
ExOne | Pioneers in binder jetting technology, offering a range of machines and materials. |
Desktop Metal | Focuses on accessible binder jetting solutions for various industries. |
HP | Enters the market with its Metal Jet technology, aiming for high-volume production. |
Note: Pricing information can fluctuate and is best obtained directly from suppliers.
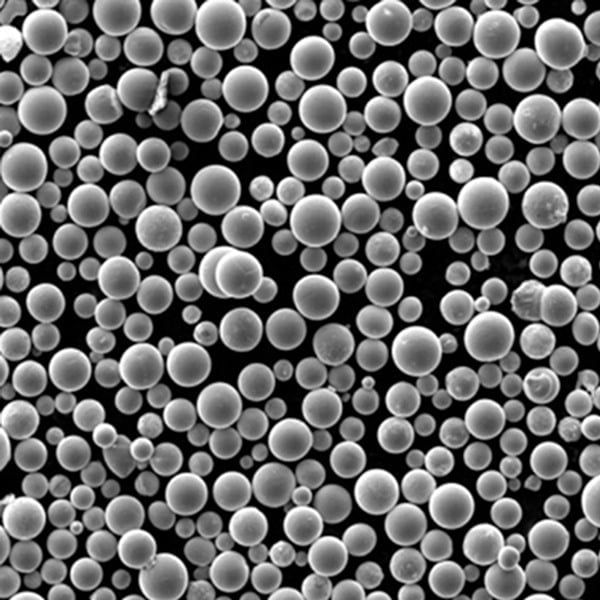
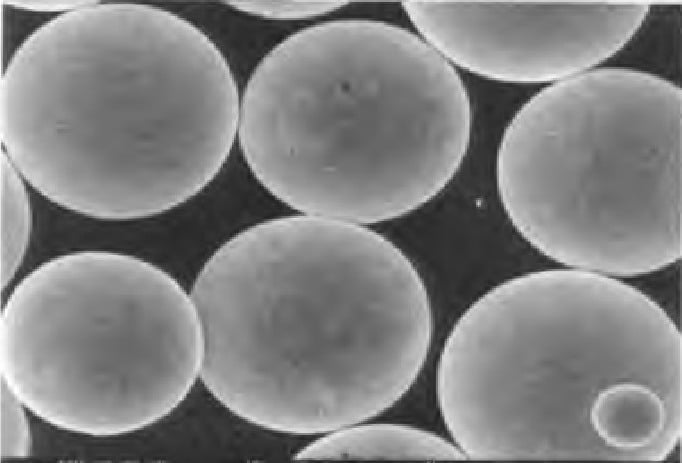
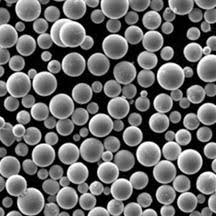
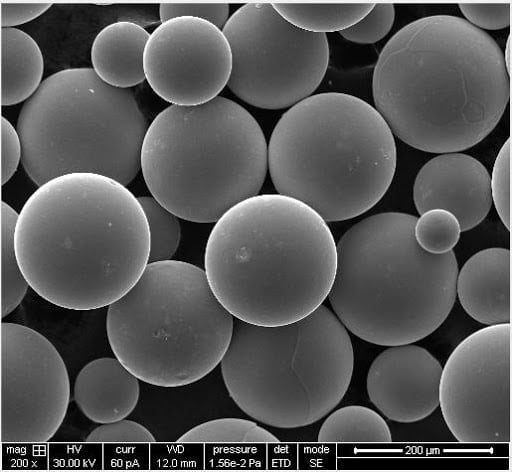
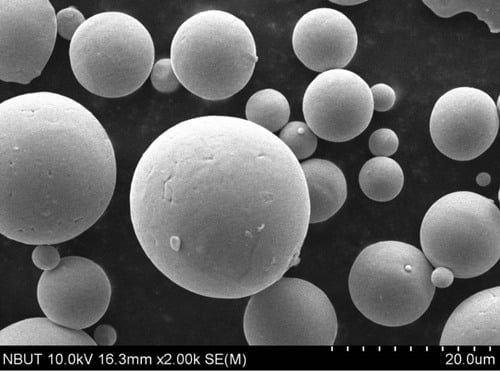
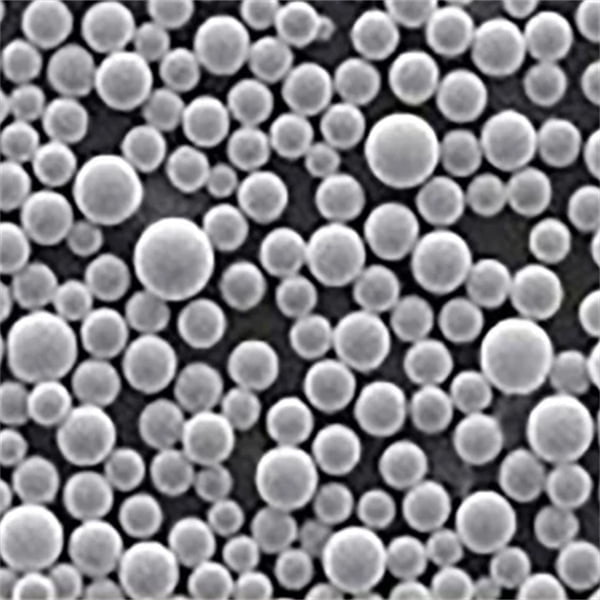
Binder Jetting: Pros and Cons
Binder jetting is a powerful technology, but like any process, it has its strengths and limitations:
Advantages | Disadvantages |
---|---|
Fast build times | Requires post-processing for final properties |
High production volume | Potential for part distortion |
Cost-effective for large parts | Material waste due to powder bed |
Complex geometries possible | Limited material options compared to other AM processes |
Conclusion
Binder jetting is undeniably transforming the manufacturing landscape. Its speed, efficiency, and versatility make it a compelling choice for a wide range of applications. As the technology continues to evolve, we can expect even more exciting developments in the world of additive manufacturing.
About 3DP mETAL
Product Category
CONTACT US
Any questions? Send us a message now! After receiving your message, we will process your request with a whole team.