Imagine building complex objects layer by layer, not with bricks and mortar, but with tiny particles of metal, sand, or even plastic. That’s the magic of Binder Jetting Additive Manufacturing (BJAM), a revolutionary technology that’s transforming the way we design and produce parts.
Overview of Binder Jetting Additive Manufacturing
BJAM belongs to the exciting world of 3D printing, also known as Additive Manufacturing (AM). Unlike traditional subtractive methods like machining, which start with a solid block and remove material to create a desired shape, AM builds objects layer by layer, adding material until the final design is complete. In BJAM, the “building blocks” are fine powders, and the “glue” that holds them together is a special binding agent.
Advantages of Binder Jetting Additive Manufacturing
BJAM offers a compelling set of advantages that make it a game-changer for various industries:
- Speed Demon: Compared to other AM processes, BJAM is a real speedster. By selectively jetting binder onto multiple layers simultaneously, BJAM can produce complex parts much faster, making it ideal for high-volume production runs.
- Material Marvel: BJAM boasts incredible versatility when it comes to materials. It can handle a wide range of powders, from metals like steel and stainless steel to ceramics, sand, and even some polymers. This opens doors to creating complex objects with unique properties for diverse applications.
- Cost Cutter: While the initial investment in a BJAM system might seem high, the cost per part can be significantly lower compared to traditional manufacturing methods, especially for complex geometries. Additionally, minimal material waste due to the powder-based approach contributes to overall cost savings.
- Design Freedom Unleashed: BJAM breaks free from the limitations of traditional manufacturing. With minimal restrictions on design complexity, BJAM allows for the creation of intricate internal features and lattice structures that would be impossible with subtractive methods. This opens doors for lightweight and highly functional designs.
- Customization Champion: BJAM excels at producing customized parts and small batch production runs. Need a one-of-a-kind prototype or a batch of specialized components? BJAM can handle it efficiently, eliminating the need for expensive tooling changes.
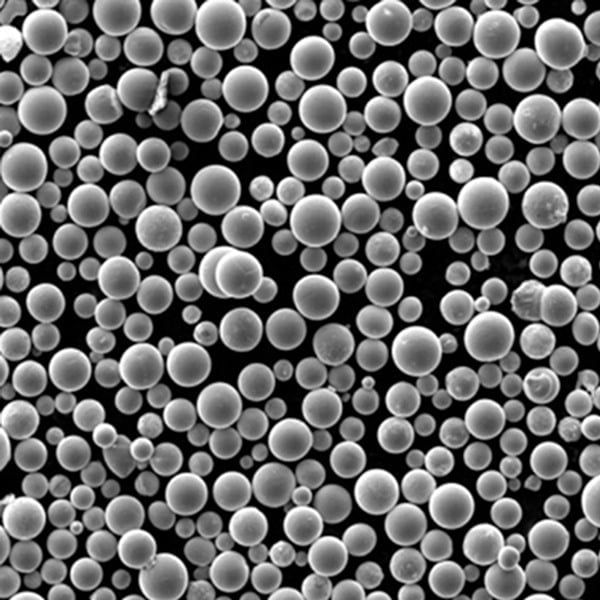
The Production Process of Binder Jetting Additive Manufacturing
So, how exactly does BJAM translate this magic of powder and binder into real objects? Let’s delve into the fascinating production process:
- Powder Preparation: The journey begins with a bed of fine powder particles spread evenly across a platform. The powder selection depends on the desired final product properties – metal powders for metallic parts, ceramic powders for heat-resistant components, and so on.
- Binder Jetting: Here’s where the real artistry comes in. An inkjet printhead similar to those in 2D printers meticulously traverses the powder bed, selectively depositing droplets of a liquid binder agent. This binder acts like glue, holding the powder particles together in the desired pattern, essentially “drawing” a single layer of the future object.
- Layer by Layer: The magic continues as the platform lowers slightly, and a fresh layer of powder is deposited on top. The printhead then jets binder again, this time creating the next layer of the object on top of the previous one. This process repeats layer by layer until the entire 3D geometry is complete.
- Post-Processing: Once the printing is finished, the unbound powder surrounding the “green part” is carefully removed. Depending on the material used, the green part might undergo additional processes like infiltration (filling pores with a secondary material) or debinding (removing the binder agent) before reaching its final form.
- Finalization: The final step involves sintering or heat treatment for metal parts, a process that strengthens the bond between the particles, resulting in a robust and functional object. For other materials, post-processing techniques might vary.
Applications of Binder Jetting Additive Manufacturing
BJAM’s diverse capabilities translate into a wide range of applications across various industries:
- Aerospace & Defense: BJAM is a valuable tool for creating lightweight, high-strength components for aircraft and spacecraft. Its ability to handle complex geometries allows for the production of parts with internal lattice structures, optimizing weight and performance.
- Automotive: The automotive industry is increasingly turning to BJAM for prototyping and production of customized parts like complex engine components, fuel injectors, and even lightweight car body parts.
- Medical & Dental: BJAM’s ability to handle biocompatible materials makes it ideal for creating custom medical implants, prosthetics, and even dental crowns and bridges.
- Consumer Goods: From customized phone cases to intricate figurines and even functional tools, BJAM is finding its way into consumer product creation, offering possibilities for mass customization and on-demand production.
Limitations of Binder Jetting Additive Manufacturing
While BJAM offers a compelling set of advantages, it’s important to acknowledge its limitations to make informed decisions about its suitability for specific applications:
- Material Properties: Compared to some other AM processes like Selective Laser Melting (SLM), BJAM parts might exhibit slightly lower mechanical strength and surface finish, especially for metals. This is because the sintering process doesn’t achieve the same level of material fusion as laser melting.
- Post-Processing Requirements: BJAM typically involves more extensive post-processing steps compared to some other AM methods. Depending on the material, debinding, infiltration, and sintering can add time and complexity to the overall production process.
- Limited Material Selection: While BJAM offers a broader material selection compared to some AM techniques, it still has limitations. For instance, some high-performance polymers or exotic materials might not be readily compatible with the binder jetting process.
- Resolution and Surface Finish: BJAM’s resolution and surface finish capabilities might not be as fine as some other AM processes like Stereolithography (SLA). This can be a factor for applications requiring extremely smooth surfaces or intricate details.
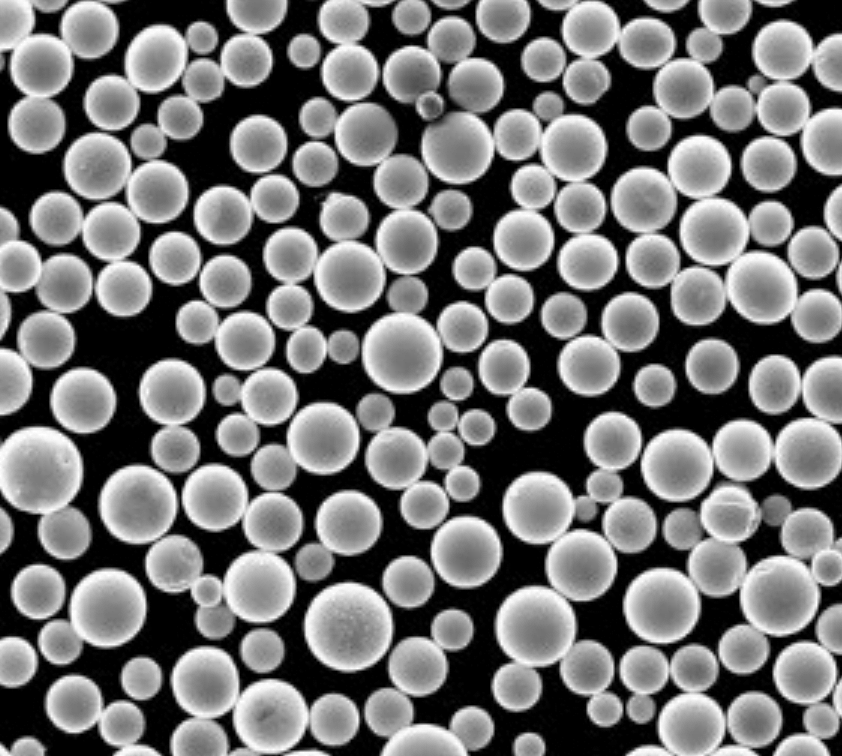
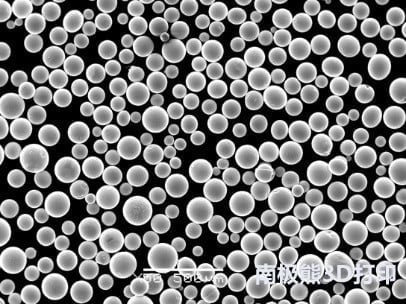
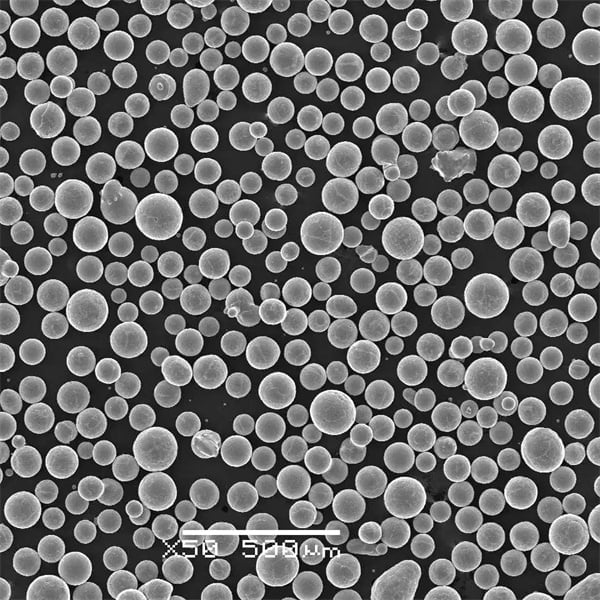
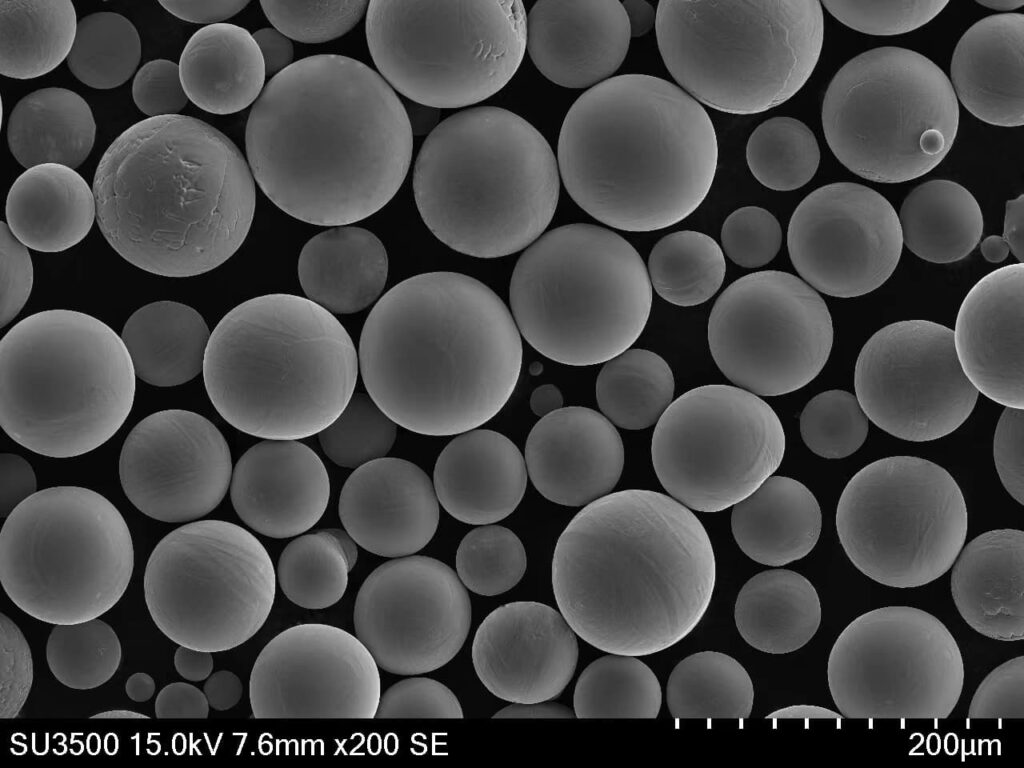
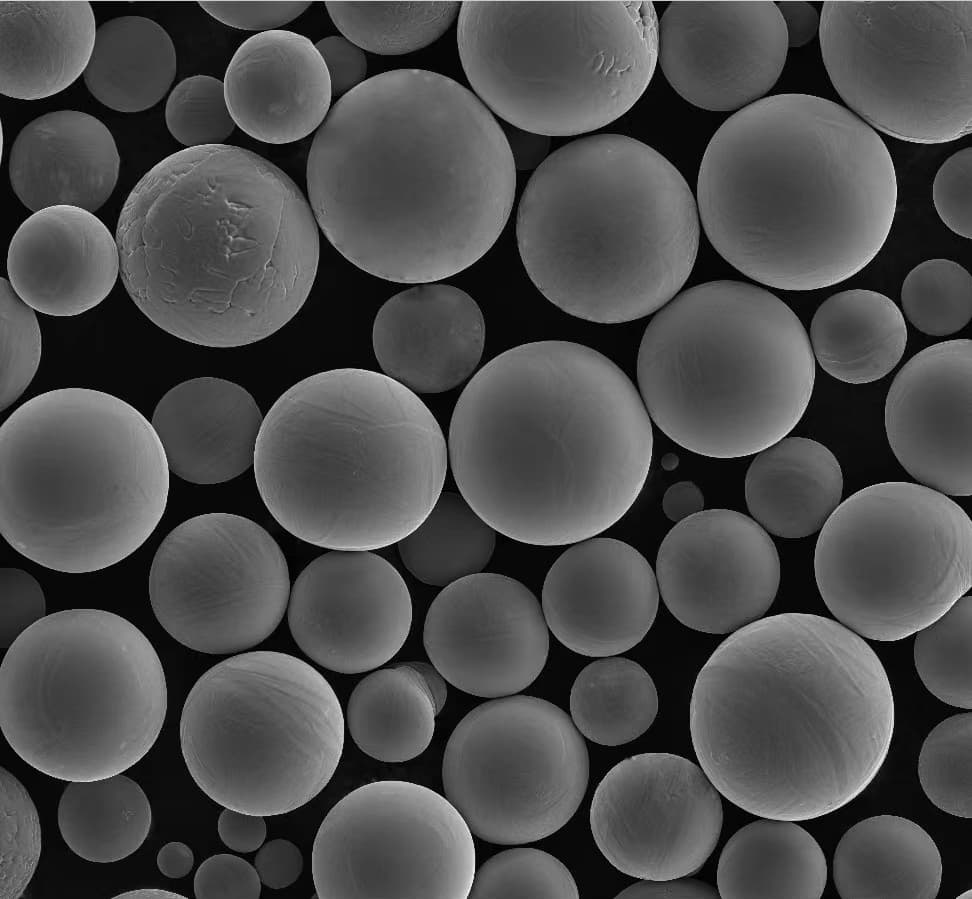
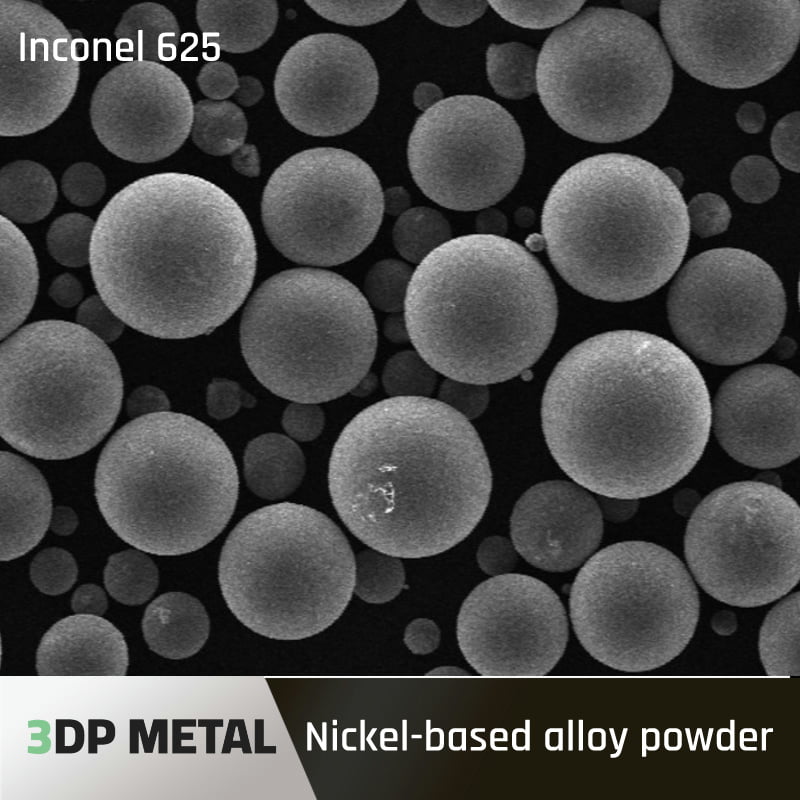
BJAM vs Other AM Processes
Choosing the right AM technology for your project depends on various factors like material needs, design complexity, production volume, and budget. Here’s a quick comparison of BJAM with some of the most common AM processes:
Feature | Binder Jetting (BJAM) | Selective Laser Melting (SLM) | Stereolithography (SLA) | Fused Deposition Modeling (FDM) |
---|---|---|---|---|
Material Compatibility | Metals, Ceramics, Sand, some Polymers | Metals | Polymers | Thermoplastics |
Speed | Fast | Moderate | Moderate | Slow |
Part Complexity | High | High | High | Moderate |
Surface Finish | Moderate | High | Very High | Moderate |
Mechanical Strength | Moderate to High (material dependent) | Very High | High | Moderate |
Cost per Part | Low to Moderate (for high volume) | High | Moderate | Low |
The Future of Binder Jetting Additive Manufacturing
BJAM is a rapidly evolving technology with immense potential. Here are some exciting trends shaping its future:
- Advanced Materials: Researchers are continuously developing new binder formulations and powder materials specifically optimized for BJAM. This will lead to improved mechanical properties, expanded material compatibility, and potentially even functional graded parts with varying properties within a single object.
- Multi-Material BJAM: Imagine creating a single object with different materials seamlessly integrated within it. This is the future that multi-material BJAM promises. By utilizing different printheads for various binder types, it will be possible to combine metal and plastic components within the same build, opening doors for innovative functional designs.
- Improved Resolution and Speed: As technology advances, BJAM systems are expected to achieve even finer resolutions and faster printing speeds. This will further enhance the viability of BJAM for a wider range of applications, including those requiring intricate details or high-volume production runs.
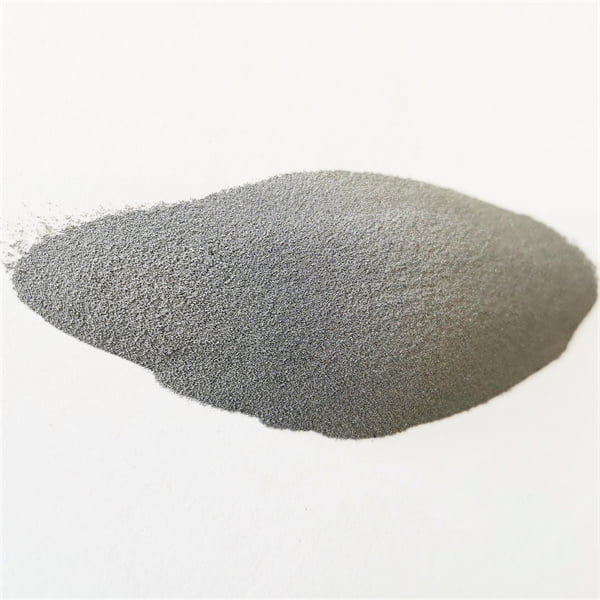
FAQ
Q: What are the benefits of using BJAM compared to traditional manufacturing methods?
A: BJAM offers several advantages, including:
- Faster production times, especially for complex geometries.
- Design freedom for creating intricate features and lattice structures.
- Reduced material waste compared to subtractive manufacturing.
- Potential for customization and small batch production.
- Broader material compatibility compared to some other AM processes.
Q: What are some limitations of BJAM to consider?
A: BJAM might not be ideal for every application due to limitations like:
- Slightly lower mechanical strength and surface finish compared to some AM processes for metals.
- More extensive post-processing requirements depending on the material.
- Limited material selection compared to some other AM technologies.
- Resolution and surface finish might not be as fine as some other AM methods.
Q: What industries are using BJAM the most?
A: BJAM is finding applications in various industries, including:
- Aerospace & Defense
- Automotive
- Medical & Dental
- Consumer Goods
Q: How does BJAM compare to other AM processes like SLM or FDM?
A: The best AM process for your project depends on your specific needs. Here’s a simplified comparison table:
Feature | Binder Jetting (BJAM) | Selective Laser Melting (SLM) | Fused Deposition Modeling (FDM) |
---|---|---|---|
Material Compatibility | Metals, Ceramics, Sand | Metals | Thermoplastics |
Typical Application | High-volume production, complex geometries | High-value components, prototypes | Functional prototypes |
About 3DP mETAL
Product Category
CONTACT US
Any questions? Send us a message now! After receiving your message, we will process your request with a whole team.