Overview of Brake Disc Coatings Powder
When it comes to the performance and longevity of brake discs, the type of coating applied can make a world of difference. Brake disc coatings powder is a vital component in the automotive industry, providing essential protection against corrosion, wear, and high temperatures. This guide will dive deep into the world of brake disc coatings powder, exploring the various types, compositions, properties, applications, and much more. Whether you’re a professional in the automotive industry or just someone curious about the science behind brake discs, this article is tailored to give you all the information you need.
Composition of Brake Disc Coatings Powder
Brake disc coatings are typically composed of a variety of metallic powders, each with its unique properties that contribute to the overall performance of the coating. These powders are carefully selected and mixed to achieve the desired balance of hardness, heat resistance, and anti-corrosion capabilities.
Detailed Breakdown of Common Metal Powders Used
Metal Powder | Composition | Key Properties | Uses |
---|---|---|---|
Zinc Powder | Pure Zinc or Zinc Alloys | Corrosion resistance, easy application | Base coatings, rust prevention |
Aluminum Powder | Pure Aluminum or Aluminum Alloys | Lightweight, high thermal conductivity | High-temp environments, lightweight components |
Iron Powder | Pure Iron or Iron-Carbon Mixtures | High durability, excellent wear resistance | Heavy-duty brake systems, high-wear environments |
Nickel Powder | Pure Nickel or Nickel Alloys | High resistance to oxidation and corrosion | High-performance coatings, aerospace applications |
Chromium Powder | Pure Chromium | Extreme hardness, high melting point | Ultra-durable coatings, extreme environments |
Molybdenum Powder | Pure Molybdenum | High thermal stability, excellent strength | High-temp applications, racing vehicles |
Titanium Powder | Pure Titanium or Titanium Alloys | Lightweight, high strength-to-weight ratio | Specialized coatings, lightweight components |
Copper Powder | Pure Copper or Copper Alloys | Excellent electrical and thermal conductivity | Electrical components, high-temp environments |
Tungsten Powder | Pure Tungsten | Extremely high melting point, very dense | Extreme heat applications, aerospace industry |
Cobalt Powder | Pure Cobalt or Cobalt Alloys | High wear resistance, good corrosion resistance | Specialized applications, high-wear environments |
Why Composition Matters
Imagine your brake disc coatings as the armor of a knight; it needs to be strong enough to withstand constant battle but light enough not to weigh the knight down. The composition of brake disc coatings powder is crucial because it determines how well the coating will perform under various conditions. For example, a zinc-based coating might be ideal for standard vehicles where corrosion resistance is key, but for high-performance racing cars, a coating with molybdenum or titanium might be better due to the need for superior heat resistance.
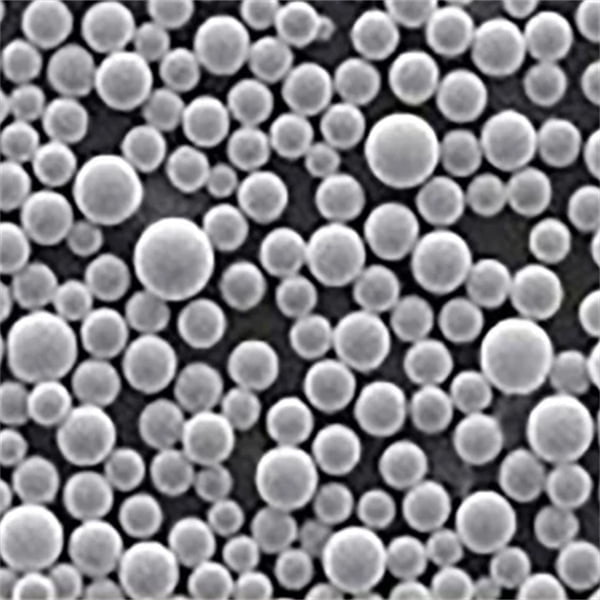
Characteristics of Different Brake Disc Coatings Powder
Different coatings serve different purposes, and understanding the unique characteristics of each type of powder helps in selecting the right one for specific applications. Let’s explore the key characteristics of the most commonly used brake disc coatings powders.
Key Characteristics Explained
Characteristic | Description | Example Powders |
---|---|---|
Corrosion Resistance | The ability of the coating to withstand rust and other forms of corrosion. | Zinc, Nickel |
Heat Resistance | How well the coating can perform under high temperatures. | Molybdenum, Tungsten |
Durability | The overall lifespan of the coating in terms of wear and tear. | Iron, Chromium |
Weight | The weight of the coating, which affects the overall weight of the brake disc. | Aluminum, Titanium |
Application Method | How the coating is applied, which can influence the quality and thickness of the coating. | Powder Coating (Electrostatic Application) |
Thermal Conductivity | The ability to transfer heat, which is crucial in brake systems to avoid overheating. | Copper, Aluminum |
Oxidation Resistance | The ability to resist the formation of oxides, which can degrade performance over time. | Nickel, Chromium |
Cost | The expense involved in using the coating, including both material cost and application cost. | Zinc (affordable), Titanium (expensive) |
Environmental Impact | The ecological footprint of producing and applying the coating. | Zinc (Low Impact), Chromium (Higher Impact) |
Adhesion Strength | How well the coating adheres to the brake disc material, which affects its durability and effectiveness. | Cobalt, Iron |
Real-World Examples
- Zinc Coatings: Often used in standard vehicles due to their excellent corrosion resistance and affordability. Zinc coatings are like a good, reliable raincoat—great for everyday use in various weather conditions.
- Molybdenum Coatings: Think of these as the fireproof suit of the brake disc world. They’re designed to withstand extremely high temperatures, making them perfect for high-performance vehicles that push the limits.
Applications of Brake Disc Coatings Powder
The applications of brake disc coatings powder vary depending on the type of vehicle, the environment in which the vehicle operates, and the specific demands placed on the brake system. Understanding where and how these coatings are used can help in selecting the right powder for the job.
Diverse Applications Across Industries
Application Area | Description | Ideal Coating Type |
---|---|---|
Automotive Industry | Coatings for standard passenger vehicles, providing corrosion resistance and durability. | Zinc, Iron |
Racing Vehicles | High-performance vehicles that require coatings with exceptional heat resistance and wear properties. | Molybdenum, Titanium |
Aerospace Industry | Coatings used in aircraft brakes, where extreme conditions demand the highest levels of performance. | Tungsten, Nickel |
Heavy Machinery | Brake systems in industrial machinery that need to withstand heavy loads and harsh environments. | Chromium, Iron |
Military Vehicles | Coatings for armored vehicles and other military applications where durability and reliability are crucial. | Cobalt, Nickel |
Marine Industry | Brake systems in boats and ships, where corrosion resistance is particularly important. | Zinc, Aluminum |
Electric Vehicles (EVs) | Specialized coatings designed to optimize the performance of regenerative braking systems. | Copper, Aluminum |
Motorcycles | Coatings that offer a balance of durability and lightweight properties for optimal performance. | Titanium, Aluminum |
Public Transportation | Coatings for buses and trains, where longevity and reliability are key factors. | Iron, Zinc |
Luxury Vehicles | Coatings that offer not only performance but also a high level of aesthetic appeal. | Nickel, Titanium |
Real-Life Examples of Applications
- Racing Vehicles: Picture a Formula 1 car hurtling down the track at 200 mph. The brake discs need to handle immense heat, so a molybdenum-based coating is applied to ensure the brakes can keep up with the intense demands of racing.
- Marine Industry: Imagine the saltwater constantly attacking the brake system of a boat. Here, a zinc coating is ideal because of its superior corrosion resistance, acting like a suit of armor against rust.
Specifications, Sizes, and Standards
When it comes to brake disc coatings powder, there are specific standards and specifications that manufacturers must adhere to. These standards ensure that the coatings meet the required performance criteria for various applications.
Key Specifications and Standards
Specification | Description | Example Standards |
---|---|---|
Coating Thickness | The thickness of the coating, typically measured in microns (µm). | ISO 2178, ASTM B499 |
Adhesion Strength | The strength of the bond between the coating and the substrate, ensuring it doesn’t peel or flake. | ASTM D3359, ISO 2409 |
Hardness | The hardness of the coating, which affects its wear resistance and durability. | ASTM E18, ISO 6508 |
Corrosion Resistance | The ability of the coating to resist corrosion, usually tested in salt spray environments. | ASTM B117, ISO 9227 |
Thermal Conductivity | How well the coating can conduct heat, crucial for high-performance brake systems. | ASTM E1461, ISO 22007-2 |
Electrical Conductivity | Important for coatings used in electric vehicles and other applications where electrical conductivity is required. | ASTM B193, IEC 60093 |
Coating Weight | The total weight of the applied coating, which can impact the overall weight of the brake disc. | ASTM B659, ISO 2064 |
Environmental Standards | Guidelines and regulations to ensure the coatings are environmentally friendly. | RoHS, REACH, ISO 14001 |
Application Method | The method used to apply the coating, which can affect the quality and consistency of the coating. | ASTM D4138, ISO 2360 |
Surface Preparation | The preparation of the brake disc surface before coating, ensuring proper adhesion and performance. | ASTM D6386, ISO 8501-1 |
Understanding Standards in Practice
- ASTM B117 (Salt Spray Test): This standard is like the ultimate endurance test for coatings, subjecting them to a simulated salty environment to see how long they can withstand corrosion. For marine applications, this test is particularly crucial.
- ISO 6508 (Rockwell Hardness Test): Imagine testing how tough a superhero’s armor is. This standard measures the hardness of the coating, ensuring it’s up to the challenge of heavy use.
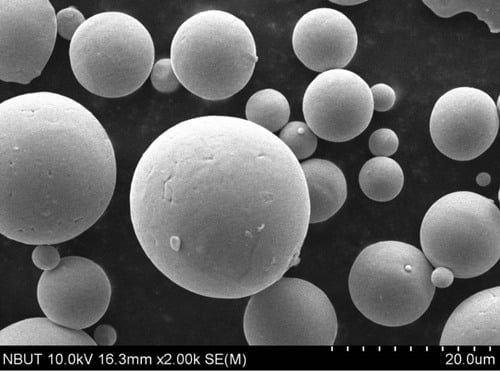
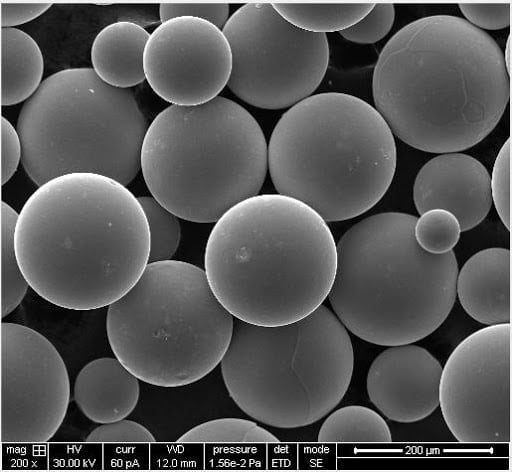
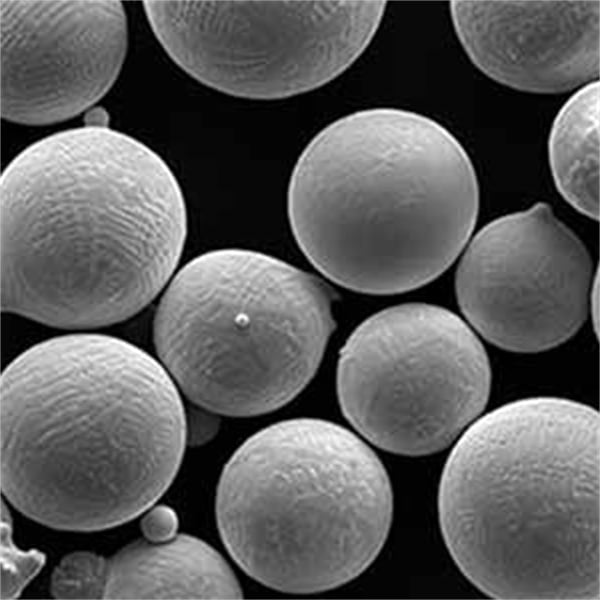
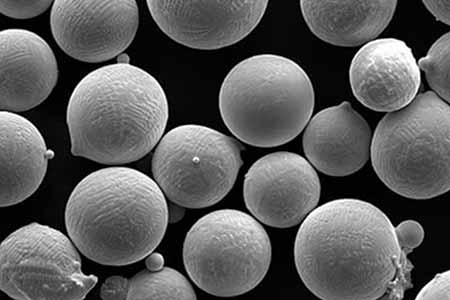
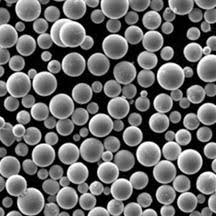
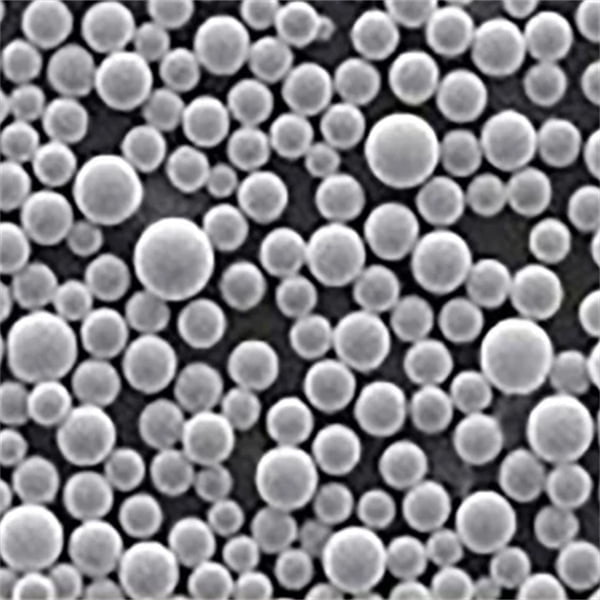
Suppliers and Pricing
Selecting the right supplier for brake disc coatings powder is essential, especially when considering factors such as cost, quality, and reliability. Here’s a look at some of the leading suppliers and a general idea of what you can expect to pay.
Top Suppliers of Brake Disc Coatings Powder
Supplier | Location | Available Powders | Price Range | Special Notes |
---|---|---|---|---|
Höganäs AB | Sweden | Iron, Copper, Nickel, Aluminum | $50 – $300 per kg | Leading in high-performance powders |
Global Tungsten & Powders (GTP) | USA | Tungsten, Molybdenum, Nickel | $100 – $500 per kg | Specializes in high-temp applications |
HC Starck | Germany | Titanium, Molybdenum, Chromium | $150 – $600 per kg | Known for premium quality |
Sandvik Materials Technology | Sweden | Stainless Steel, Chromium, Nickel | $60 – $400 per kg | Focus on industrial applications |
Makin Metal Powders | UK | Zinc, Aluminum, Copper | $40 – $200 per kg | Affordable options, wide range |
Praxair Surface Technologies | USA | Cobalt, Nickel, Tungsten | $120 – $700 per kg | Expertise in aerospace applications |
Carpenter Powder Products | USA | Titanium, Nickel, Stainless Steel | $130 – $600 per kg | High-quality powders for various uses |
Sumitomo Electric Industries | Japan | Copper, Aluminum, Titanium | $90 – $450 per kg | Strong focus on EV applications |
Kymera International | USA | Aluminum, Zinc, Copper | $50 – $250 per kg | Broad range, reliable supply |
AMETEK Specialty Metal Products | USA | Nickel, Chromium, Iron | $110 – $550 per kg | Industrial and high-performance powders |
Factors Influencing Pricing
Pricing for brake disc coatings powder can vary significantly depending on the type of powder, the quantity purchased, and the supplier’s location. For instance, tungsten and molybdenum powders tend to be more expensive due to their specialized applications in high-temperature environments. On the other hand, zinc and aluminum powders are generally more affordable, making them popular for standard automotive applications.
Comparison of Different Brake Disc Coatings Powder
Choosing the right brake disc coatings powder can be a complex decision, especially when considering the various options available. Here’s a side-by-side comparison to help you make an informed choice.
Detailed Comparison of Key Powders
Metal Powder | Advantages | Disadvantages | Best Used For |
---|---|---|---|
Zinc | Excellent corrosion resistance, affordable | Lower heat resistance, less durable under heavy use | Standard vehicles, marine applications |
Aluminum | Lightweight, good thermal conductivity | Lower hardness, can be expensive for some applications | Electric vehicles, lightweight components |
Iron | High durability, excellent wear resistance | Heavier, lower corrosion resistance compared to other options | Heavy-duty vehicles, industrial machinery |
Nickel | High resistance to oxidation and corrosion | Higher cost, can be challenging to apply uniformly | Aerospace, high-performance vehicles |
Chromium | Extremely hard, high melting point | Expensive, higher environmental impact | Extreme environments, ultra-durable applications |
Molybdenum | High thermal stability, excellent strength | Very expensive, typically used in specialized applications | Racing vehicles, high-temp applications |
Titanium | Lightweight, high strength-to-weight ratio | High cost, can be challenging to apply correctly | Specialized coatings, luxury vehicles |
Copper | Excellent electrical and thermal conductivity | Not as durable under high mechanical stress | Electric vehicles, high-temp environments |
Tungsten | Extremely high melting point, very dense | Extremely expensive, limited availability | Extreme heat applications, aerospace industry |
Cobalt | High wear resistance, good corrosion resistance | High cost, less common in standard automotive applications | Specialized applications, military vehicles |
Making the Right Choice
- Standard Automotive Use: If you’re looking for a reliable, cost-effective option, zinc or iron powders are excellent choices. They offer good performance for everyday driving conditions without breaking the bank.
- High-Performance Vehicles: For those in need of something more robust, like in racing or aerospace, molybdenum or tungsten powders are ideal, offering superior heat resistance and durability, though they come at a higher cost.
Advantages and Disadvantages of Brake Disc Coatings Powder
Every type of brake disc coating powder has its strengths and weaknesses. Here’s a closer look at the pros and cons of using these coatings in various applications.
Pros and Cons Table
Metal Powder | Advantages | Disadvantages |
---|---|---|
Zinc | Affordable, excellent corrosion resistance | Limited heat resistance, lower durability in high-performance applications |
Aluminum | Lightweight, good thermal and electrical conductivity | Lower hardness, can be more expensive |
Iron | Highly durable, excellent wear resistance | Heavier, prone to corrosion without additional treatment |
Nickel | High resistance to corrosion and oxidation | Higher cost, application process can be more complex |
Chromium | Extremely hard, resistant to high temperatures | Expensive, environmentally impactful |
Molybdenum | Superior thermal stability, very strong under high stress | Very expensive, typically used in niche applications |
Titanium | Exceptional strength-to-weight ratio, corrosion-resistant | High cost, can be difficult to apply |
Copper | Excellent thermal and electrical conductivity, relatively affordable | Less durable under mechanical stress, can corrode if not properly sealed |
Tungsten | Extremely high melting point, unmatched durability | Extremely expensive, limited to specific high-performance applications |
Cobalt | High wear resistance, good corrosion resistance | High cost, less commonly used in automotive applications |
Balancing Pros and Cons
Selecting the right brake disc coating powder often involves balancing the advantages and disadvantages. For example, while chromium coatings offer unparalleled durability, their environmental impact and cost may make them less attractive for some applications. On the other hand, zinc coatings, while more affordable, may not be suitable for high-performance vehicles due to their lower heat resistance.
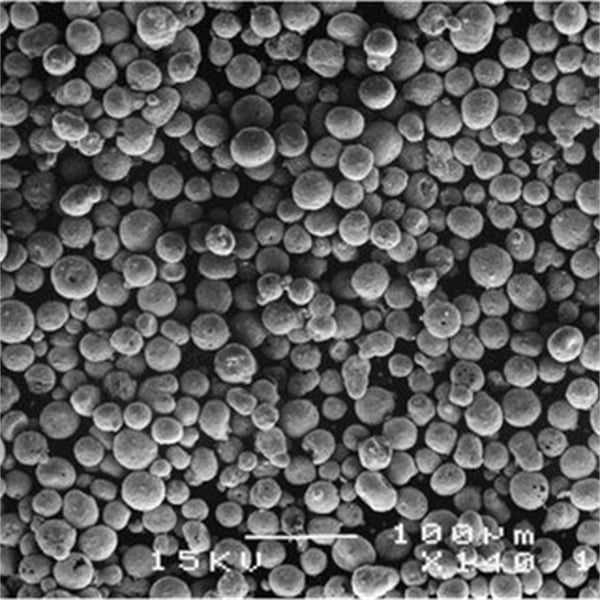
FAQ
Here are some frequently asked questions about brake disc coatings powder to help clarify any remaining doubts.
Question | Answer |
---|---|
What is the purpose of brake disc coatings powder? | Brake disc coatings powder is used to protect brake discs from corrosion, wear, and heat, extending their lifespan. |
How is brake disc coatings powder applied? | It is typically applied through a process called powder coating, where the powder is electrostatically charged and sprayed onto the disc. |
What factors should I consider when choosing a brake disc coating powder? | Consider the type of vehicle, the environment it will be used in, the required performance, and the cost. |
Are there environmentally friendly options for brake disc coatings powder? | Yes, powders like zinc and aluminum are considered more environmentally friendly compared to chromium or nickel. |
How does the thickness of the coating affect performance? | Thicker coatings generally offer better protection but can also add weight and affect heat dissipation. |
Can brake disc coatings powder improve braking performance? | While the coating itself doesn’t improve braking power, it does protect the brake disc, ensuring consistent performance over time. |
Is it possible to reapply brake disc coatings powder after wear? | Yes, brake discs can be recoated, though it requires proper surface preparation to ensure the new coating adheres well. |
What are the most cost-effective brake disc coatings powders? | Zinc and iron powders are generally the most cost-effective options. |
Which brake disc coatings powders are best for high-performance vehicles? | Molybdenum, tungsten, and titanium powders are ideal for high-performance vehicles due to their superior heat resistance. |
How do brake disc coatings powder impact the overall weight of the vehicle? | Powders like aluminum and titanium are lightweight, while iron and tungsten are heavier, impacting the vehicle’s total weight. |
Conclusion
Brake disc coatings powder is a critical element in ensuring the durability and performance of brake systems across various industries. From the everyday commuter car to high-performance racing vehicles, the right choice of coating can significantly impact the longevity and reliability of the brakes. By understanding the composition, characteristics, and applications of different powders, you can make an informed decision that best suits your needs.
Whether you’re looking to protect your vehicle from corrosion, improve heat resistance, or simply extend the lifespan of your brake discs, there’s a brake disc coating powder out there that’s perfect for you. So, next time you’re considering brake maintenance, remember—the right coating powder can be the difference between a smooth stop and a screeching halt.
About 3DP mETAL
Product Category
CONTACT US
Any questions? Send us a message now! After receiving your message, we will process your request with a whole team.