Overview of Ceramic-Lined Induction Crucibles
When it comes to melting and refining metals, the quality of the crucible you use can make a world of difference. Whether you’re an industrial manufacturer or a researcher in a lab, a ceramic-lined induction crucible offers a level of precision, efficiency, and durability that’s hard to beat. But what exactly is a ceramic-lined induction crucible? How does it work, and why might it be the best choice for your specific needs?
A ceramic-lined induction crucible is a type of crucible specifically designed for induction furnaces. These crucibles are made from high-quality ceramic materials that are capable of withstanding extreme temperatures while providing excellent thermal insulation. The ceramic lining inside the crucible acts as a protective barrier, shielding the metal being melted from impurities and ensuring consistent results. This technology is particularly useful when working with reactive metals, high-purity alloys, and metal powders.
In this guide, we’ll delve into everything you need to know about ceramic-lined induction crucibles—from their composition and characteristics to their advantages and applications. We’ll also explore different metal powder models suitable for use with these crucibles and provide a detailed comparison to help you make an informed decision.
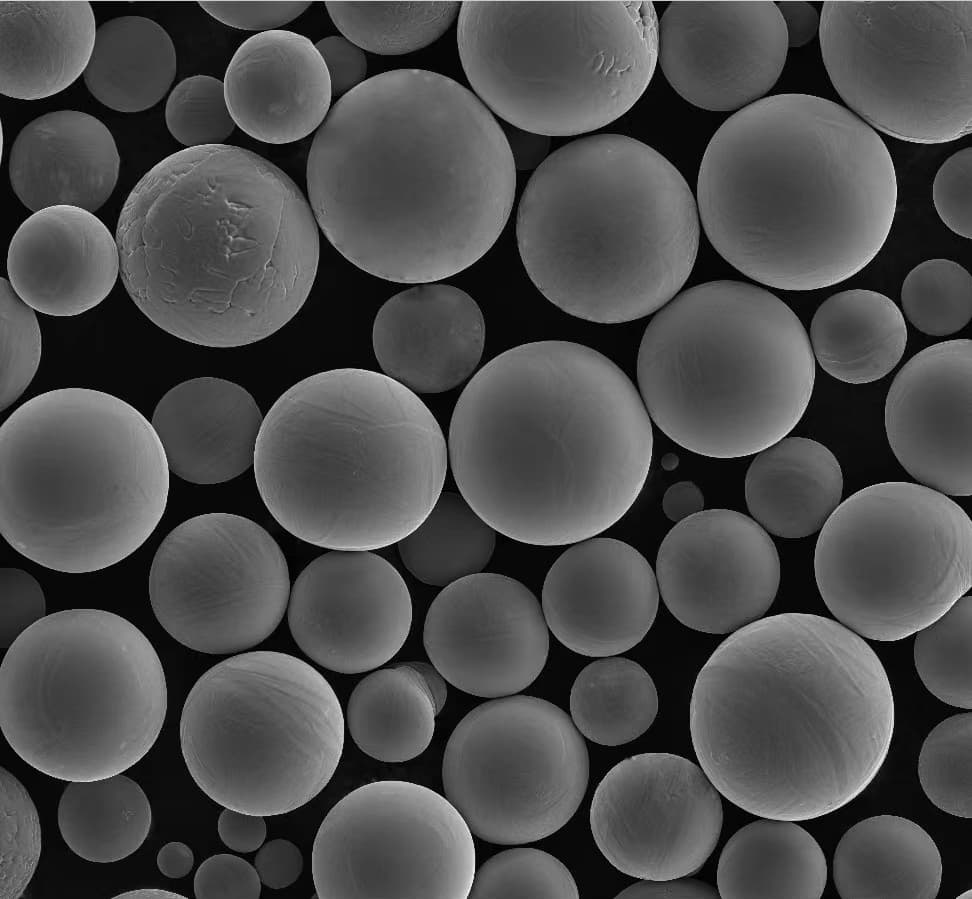
Composition of Ceramic-Lined Induction Crucibles
The composition of ceramic-lined induction crucibles is a critical factor that influences their performance. These crucibles are typically made from high-purity alumina, zirconia, or silicon carbide, which are chosen for their ability to withstand high temperatures and resist chemical reactions with the molten metal. The lining is applied to the inner surface of the crucible to create a barrier that protects the metal from contamination.
Here’s a table summarizing the typical composition of ceramic-lined induction crucibles:
Material | Description | Properties |
---|---|---|
Alumina (Al₂O₃) | High-purity alumina is known for its excellent thermal stability and resistance to corrosion. | High melting point (2040°C), low thermal expansion, high dielectric strength. |
Zirconia (ZrO₂) | Zirconia offers high fracture toughness and resistance to thermal shock, making it suitable for repeated heating and cooling cycles. | High melting point (2700°C), excellent thermal shock resistance, low thermal conductivity. |
Silicon Carbide | Silicon carbide is used for its superior thermal conductivity and strength at high temperatures. | High melting point (2700°C), excellent thermal conductivity, good chemical resistance. |
These materials are chosen based on the specific needs of the application, such as the type of metal being melted, the required temperature range, and the desired lifespan of the crucible.
Characteristics of Ceramic-Lined Induction Crucibles
Ceramic-lined induction crucibles possess several characteristics that make them ideal for high-temperature metalworking applications. Let’s explore these features in detail:
1. High Thermal Resistance
Ceramic materials like alumina and zirconia can withstand extremely high temperatures, often exceeding 2000°C. This makes them perfect for melting metals with high melting points, such as steel, nickel alloys, and precious metals.
2. Chemical Inertness
The ceramic lining in these crucibles is chemically inert, meaning it does not react with the molten metal. This prevents contamination of the metal and ensures high-purity results, which is especially important when working with reactive or precious metals.
3. Thermal Shock Resistance
Ceramic materials are known for their ability to resist thermal shock, which is the rapid change in temperature that can cause cracking or failure in other materials. This property allows ceramic-lined crucibles to withstand the rapid heating and cooling cycles common in induction furnaces.
4. Durability and Longevity
Due to their resistance to thermal shock and chemical attack, ceramic-lined induction crucibles have a long lifespan, reducing the need for frequent replacements and lowering the overall cost of operation.
5. Energy Efficiency
The excellent thermal insulation provided by the ceramic lining helps to reduce heat loss, making the melting process more energy-efficient. This not only saves energy but also reduces the time required to reach the desired temperature.
Applications of Ceramic-Lined Induction Crucibles
Ceramic-lined induction crucibles are used in a wide range of applications, from small-scale laboratory experiments to large industrial metal production processes. Here’s a look at some of the most common uses:
Application | Description |
---|---|
Precious Metal Refining | Ideal for refining gold, silver, platinum, and other precious metals where purity and consistency are crucial. |
Metal Alloy Production | Used in the production of high-purity alloys, particularly those involving reactive metals like titanium and zirconium. |
Powder Metallurgy | Suitable for melting and sintering metal powders used in additive manufacturing and other advanced processes. |
Aerospace and Defense | Utilized in the production of superalloys and other advanced materials required for aerospace and defense applications. |
Automotive Industry | Employed in the manufacture of components made from high-strength steels and nickel-based alloys. |
Electronics and Semiconductors | Used in the production of high-purity materials for electronic components and semiconductor devices. |
Research and Development | Commonly used in laboratories and research institutions for experimental and prototype work. |
Energy and Power Generation | Used in the production of materials for power generation, including gas turbine blades and nuclear fuel rods. |
Chemical Processing | Ideal for processes involving corrosive materials or high-purity chemicals. |
Jewelry Making | Widely used in the jewelry industry for melting and casting precious metals. |
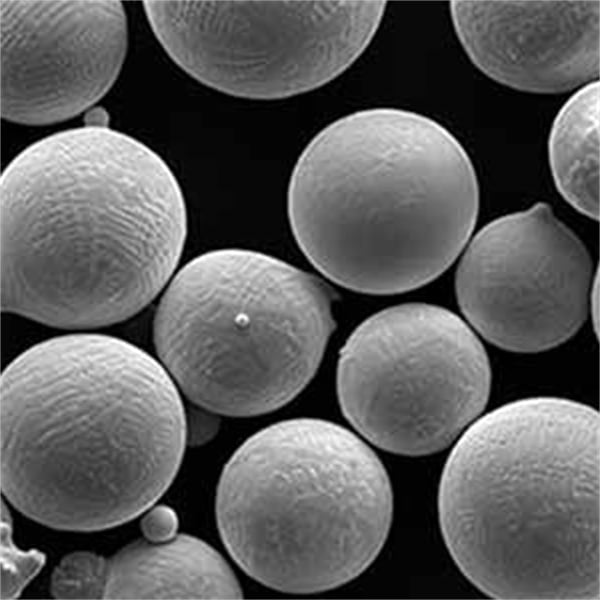
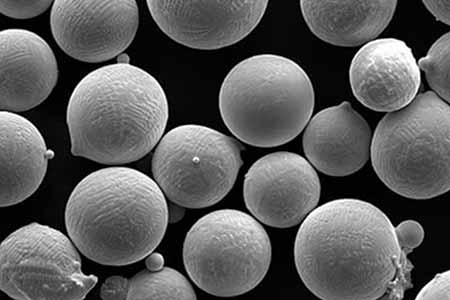
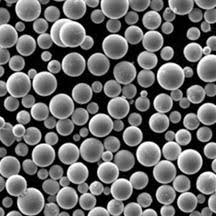
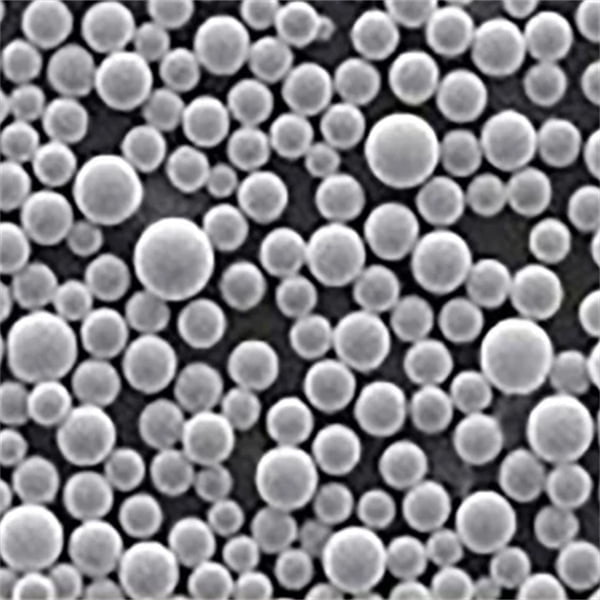
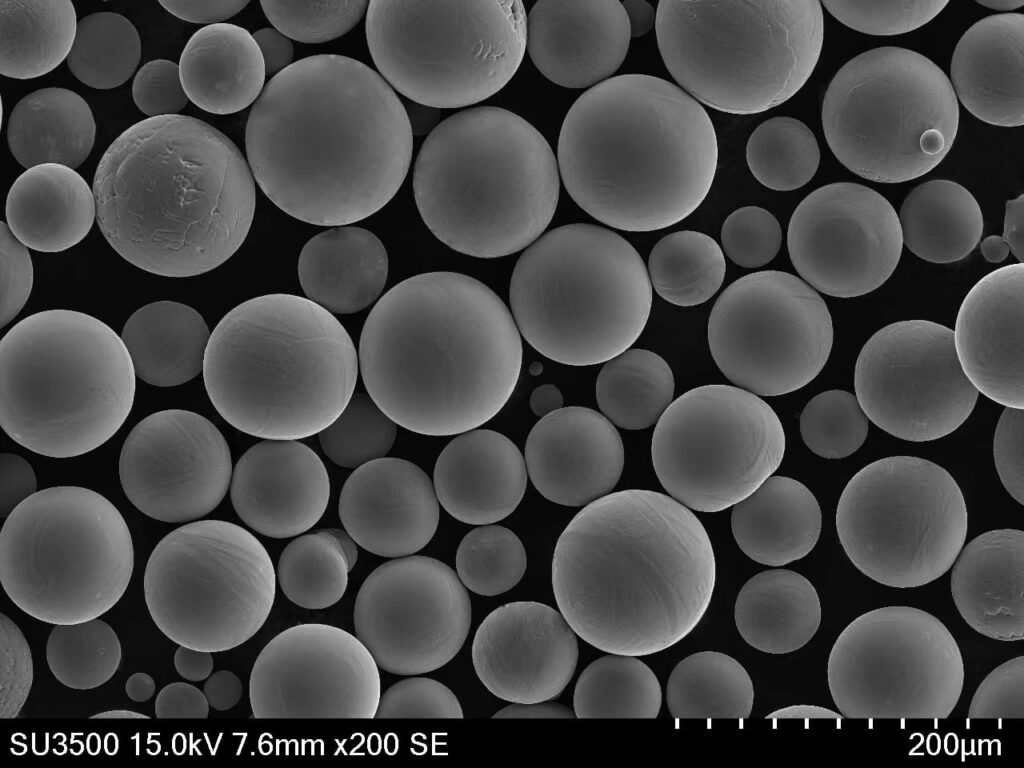
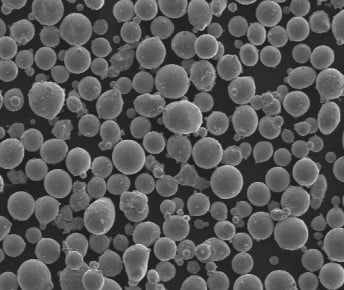
Specific Metal Powder Models for Ceramic-Lined Induction Crucibles
When it comes to selecting metal powders for use with ceramic-lined induction crucibles, there are several models to consider, each with unique properties and applications. Here are ten specific metal powder models that are commonly used:
- Höganäs Astaloy A
- Description: A high-purity iron powder with low carbon content, suitable for producing high-density, high-strength parts.
- Applications: Used in powder metallurgy for automotive components, gears, and structural parts.
- Höganäs Distaloy AE
- Description: An iron-based powder alloyed with nickel and molybdenum, offering excellent mechanical properties and wear resistance.
- Applications: Ideal for producing components that require high strength and toughness.
- Sandvik Osprey Alloy 625
- Description: A nickel-based superalloy powder known for its excellent corrosion resistance and high-temperature strength.
- Applications: Used in aerospace, chemical processing, and marine environments.
- Carpenter Micro-Melt 440C
- Description: A martensitic stainless steel powder with high carbon content, offering superior hardness and wear resistance.
- Applications: Suitable for making cutting tools, bearings, and other wear-resistant components.
- Carpenter Custom 465
- Description: A precipitation-hardening stainless steel powder with high strength and toughness.
- Applications: Used in aerospace components, medical devices, and high-performance applications.
- LPW Technology Ti-6Al-4V
- Description: A titanium alloy powder with excellent strength-to-weight ratio and corrosion resistance.
- Applications: Commonly used in aerospace, medical implants, and automotive applications.
- EOS NickelAlloy IN718
- Description: A nickel-based superalloy powder with high tensile strength and excellent fatigue resistance.
- Applications: Ideal for turbine blades, rocket engines, and other high-temperature applications.
- GKN Hoeganaes Ancorsteel 1000
- Description: A high-purity iron powder used in a variety of powder metallurgy applications.
- Applications: Suitable for producing sintered components for the automotive and industrial sectors.
- Erasteel 316L
- Description: Austenitic stainless steel powder with low carbon content, offering excellent corrosion resistance.
- Applications: Used in the production of medical devices, food processing equipment, and chemical containers.
- Carpenter Micro-Melt 420
- Description: A martensitic stainless steel powder with high hardness and good corrosion resistance.
- Applications: Suitable for cutting tools, surgical instruments, and other wear-resistant applications.
These metal powders are selected based on their compatibility with ceramic-lined induction crucibles and the specific requirements of the application, such as temperature range, mechanical properties, and corrosion resistance.
Specifications and Standards for Ceramic-Lined Induction Crucibles
When choosing a ceramic-lined induction crucible, it’s essential to consider the specifications, sizes, and standards that apply. Here’s a breakdown of some of the key specifications:
Specification | Description |
---|---|
Temperature Range | Typically ranges from 1000°C to 2000°C, depending on the material and application. |
Crucible Sizes | Available in various sizes, from small laboratory crucibles (50-100 ml) to large industrial sizes (>10 liters). |
Standards | Crucibles must meet industry standards such as ASTM C1171 for high-temperature applications. |
Grades | Available in different grades based on purity and thermal properties, such as Grade A (High-purity alumina) and Grade B (Zirconia). |
Thermal Conductivity | Varies depending on the material; typically ranges from 20-100 W/m·K for silicon carbide and lower for alumina. |
These specifications help ensure that the crucible is suitable for the intended application and provides reliable performance under the required operating conditions.
Suppliers and Pricing for Ceramic-Lined Induction Crucibles
Finding the right supplier is crucial for obtaining high-quality ceramic-lined induction crucibles at a reasonable price. Here’s a table summarizing some of the top suppliers and their pricing details:
Supplier | Location | Product Range | Pricing |
---|---|---|---|
Morgan Advanced Materials | Global | Offers a wide range of ceramic-lined crucibles for industrial and laboratory use. | Prices range from $100 to $2000, depending on size and material. |
Saint-Gobain | Global | Specializes in high-performance ceramic materials, including induction crucibles. | Custom pricing based on specifications. |
CoorsTek | USA | Provides advanced ceramics, including crucibles made from alumina, zirconia, and silicon carbide. | Prices start at $150 for small crucibles. |
Rauschert | Germany | Offers a variety of ceramic-lined crucibles for different applications, with a focus on high-temperature performance. | Pricing available upon request. |
ZIRCAR Ceramics | USA | Produces ceramic-lined crucibles for high-temperature and corrosive environments. | Prices vary based on material and size. |
It’s important to compare suppliers based on their product range, quality, and pricing to find the best option for your specific needs.
Advantages and Limitations of Ceramic-Lined Induction Crucibles
While ceramic-lined induction crucibles offer numerous benefits, they also have certain limitations. Here’s a comparison of the pros and cons:
Advantages | Limitations |
---|---|
High Thermal Resistance | Fragility: Ceramic materials can be brittle and may crack if mishandled. |
Chemical Inertness | Cost: Ceramic-lined crucibles are often more expensive than other types of crucibles. |
Durability and Longevity | Thermal Conductivity: Lower thermal conductivity compared to some metal crucibles, which can affect heating efficiency. |
Energy Efficiency | Limited Sizes: Larger sizes may be more difficult to manufacture, leading to availability issues. |
Resistance to Thermal Shock | Special Handling: Requires careful handling to avoid damage during use. |
Understanding these advantages and limitations can help you determine whether a ceramic-lined induction crucible is the right choice for your application.
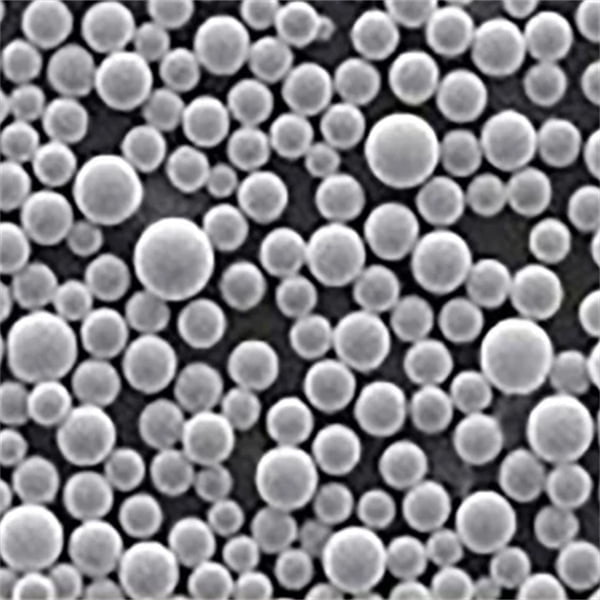
FAQ
Question | Answer |
---|---|
What metals can be melted in ceramic-lined induction crucibles? | These crucibles are suitable for melting a wide range of metals, including steel, nickel alloys, titanium, and precious metals. |
How long do ceramic-lined induction crucibles last? | The lifespan depends on the material and usage conditions, but they generally last longer than metal crucibles due to their resistance to thermal shock and corrosion. |
Can ceramic-lined induction crucibles be used in other types of furnaces? | While they are designed for induction furnaces, they can sometimes be used in other high-temperature environments, but it’s essential to check compatibility first. |
What is the maximum temperature for ceramic-lined induction crucibles? | The maximum temperature typically ranges from 1000°C to 2000°C, depending on the material used in the lining. |
How do you maintain and clean ceramic-lined induction crucibles? | Regular cleaning with appropriate tools and avoiding thermal shock are key to maintaining the crucible’s longevity. |
Are there alternatives to ceramic-lined induction crucibles? | Yes, other options include graphite crucibles, silicon carbide crucibles, and metal crucibles, each with its pros and cons. |
How do I choose the right size of ceramic-lined induction crucible? | Consider the volume of metal to be melted, the furnace’s capacity, and the crucible’s dimensions to ensure a proper fit. |
Conclusion
Ceramic-lined induction crucibles offer a powerful solution for high-temperature metalworking applications, providing excellent thermal resistance, durability, and energy efficiency. Whether you’re refining precious metals or producing high-purity alloys, these crucibles can help you achieve the precision and consistency you need. By understanding the composition, characteristics, and applications of ceramic-lined induction crucibles, as well as comparing different metal powder models and suppliers, you can make an informed decision that will enhance your production process.
If you’re ready to invest in a ceramic-lined induction crucible, consider the factors we’ve discussed here, and don’t hesitate to reach out to suppliers for specific pricing and product details. With the right crucible, you’ll be well-equipped to tackle even the most challenging melting and refining tasks with confidence.
About 3DP mETAL
Product Category
CONTACT US
Any questions? Send us a message now! After receiving your message, we will process your request with a whole team.