Cobalt-chromium (Co-Cr) powders have become indispensable in industries requiring high-performance materials, particularly in medical implants, aerospace, and high-temperature applications. This article delves into the intricacies of cobalt-chromium powders, examining their types, compositions, properties, and applications. We will also explore specific models, suppliers, and pricing details, providing a well-rounded understanding of this critical material.
Overview of Cobalt-Chromium Powders
Cobalt-chromium powders are known for their excellent mechanical properties, corrosion resistance, and biocompatibility. These powders are essential in manufacturing components that need to withstand extreme conditions without compromising on performance or longevity.
Table: Key Details of Cobalt-Chromium Powders
Aspect | Description |
---|---|
Chemical Composition | Primarily cobalt (Co) and chromium (Cr), with possible additions of molybdenum (Mo), nickel (Ni), and others |
Properties | High strength, wear resistance, corrosion resistance, biocompatibility |
Applications | Medical implants, aerospace components, high-temperature environments |
Manufacturing Methods | Powder metallurgy, additive manufacturing (3D printing), and thermal spraying |
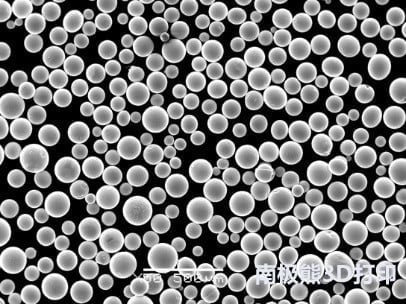
Types and Models of Cobalt-Chromium Powders
When selecting cobalt-chromium powders, it’s crucial to consider the specific model that best fits your application. Here, we’ll look at some of the most common models, detailing their unique properties and ideal uses.
1. Cobalt-Chromium-Molybdenum Alloy (CoCrMo)
Composition: 65% Co, 28% Cr, 6% Mo, 1% others
Properties: Excellent wear and corrosion resistance, high strength
Applications: Hip and knee implants, dental prosthetics
2. Cobalt-Chromium-Nickel Alloy (CoCrNi)
Composition: 60% Co, 30% Cr, 8% Ni, 2% others
Properties: High corrosion resistance, good machinability
Applications: Surgical instruments, dental implants
3. Cobalt-Chromium-Tungsten Alloy (CoCrW)
Composition: 55% Co, 30% Cr, 10% W, 5% others
Properties: Exceptional high-temperature strength, excellent wear resistance
Applications: Gas turbine blades, high-temperature engine components
4. Cobalt-Chromium-Aluminum Alloy (CoCrAl)
Composition: 60% Co, 25% Cr, 10% Al, 5% others
Properties: High oxidation resistance, good structural stability at high temperatures
Applications: Aerospace components, heat exchangers
5. Cobalt-Chromium-Iron Alloy (CoCrFe)
Composition: 50% Co, 30% Cr, 15% Fe, 5% others
Properties: Enhanced magnetic properties, good corrosion resistance
Applications: Magnetic applications, electronic components
6. Cobalt-Chromium-Tantalum Alloy (CoCrTa)
Composition: 60% Co, 30% Cr, 5% Ta, 5% others
Properties: High wear resistance, excellent biocompatibility
Applications: Medical implants, cutting tools
7. Cobalt-Chromium-Nickel-Molybdenum Alloy (CoCrNiMo)
Composition: 55% Co, 25% Cr, 10% Ni, 8% Mo, 2% others
Properties: Outstanding corrosion resistance, high strength
Applications: Marine applications, chemical processing equipment
8. Cobalt-Chromium-Silicon Alloy (CoCrSi)
Composition: 65% Co, 25% Cr, 8% Si, 2% others
Properties: High hardness, excellent wear resistance
Applications: Cutting tools, wear-resistant coatings
9. Cobalt-Chromium-Nickel-Tungsten Alloy (CoCrNiW)
Composition: 55% Co, 30% Cr, 10% Ni, 5% W
Properties: High-temperature strength, good corrosion resistance
Applications: Aerospace components, high-temperature environments
10. Cobalt-Chromium-Manganese Alloy (CoCrMn)
Composition: 60% Co, 30% Cr, 8% Mn, 2% others
Properties: High wear resistance, good corrosion resistance
Applications: Valve components, pump parts
Composition of Cobalt-Chromium Powders
Understanding the composition of cobalt-chromium powders is critical for selecting the right material for your specific needs. The primary elements, cobalt and chromium, provide a solid foundation, while additional elements tailor the powder’s properties to suit various applications.
Model | Cobalt (Co) | Chromium (Cr) | Additional Elements |
---|---|---|---|
CoCrMo | 65% | 28% | 6% Mo, 1% others |
CoCrNi | 60% | 30% | 8% Ni, 2% others |
CoCrW | 55% | 30% | 10% W, 5% others |
CoCrAl | 60% | 25% | 10% Al, 5% others |
CoCrFe | 50% | 30% | 15% Fe, 5% others |
CoCrTa | 60% | 30% | 5% Ta, 5% others |
CoCrNiMo | 55% | 25% | 10% Ni, 8% Mo, 2% others |
CoCrSi | 65% | 25% | 8% Si, 2% others |
CoCrNiW | 55% | 30% | 10% Ni, 5% W |
CoCrMn | 60% | 30% | 8% Mn, 2% others |
Characteristics of Cobalt-Chromium Powders
Cobalt-chromium powders exhibit a range of characteristics that make them suitable for demanding applications. Let’s break down these characteristics to understand what sets them apart.
Mechanical Properties
Cobalt-chromium powders are known for their exceptional mechanical properties. They offer high strength, excellent wear resistance, and the ability to retain these properties at high temperatures.
Corrosion Resistance
One of the standout features of cobalt-chromium powders is their high corrosion resistance. This makes them ideal for use in environments where they are exposed to corrosive elements, such as in marine and chemical processing applications.
Biocompatibility
In the medical field, biocompatibility is crucial. Cobalt-chromium alloys, particularly those used in implants, are highly biocompatible, ensuring they do not cause adverse reactions in the human body.
High-Temperature Stability
Cobalt-chromium powders can maintain their structural integrity at high temperatures, making them suitable for aerospace and other high-temperature applications.
Grades of Cobalt-Chromium Powders
Different grades of cobalt-chromium powders cater to various applications, each offering unique properties that make them ideal for specific uses.
Grade | Applications |
---|---|
CoCrMo | Hip and knee implants, dental prosthetics |
CoCrNi | Surgical instruments, dental implants |
CoCrW | Gas turbine blades, high-temperature engine components |
CoCrAl | Aerospace components, heat exchangers |
CoCrFe | Magnetic applications, electronic components |
CoCrTa | Medical implants, cutting tools |
CoCrNiMo | Marine applications, chemical processing equipment |
CoCrSi | Cutting tools, wear-resistant coatings |
CoCrNiW | Aerospace components, high-temperature environments |
CoCrMn | Valve components, pump parts |
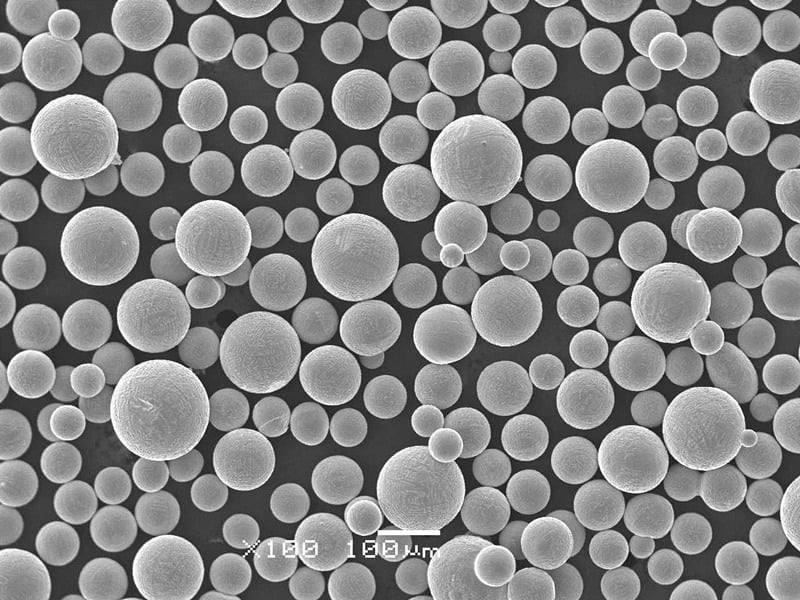
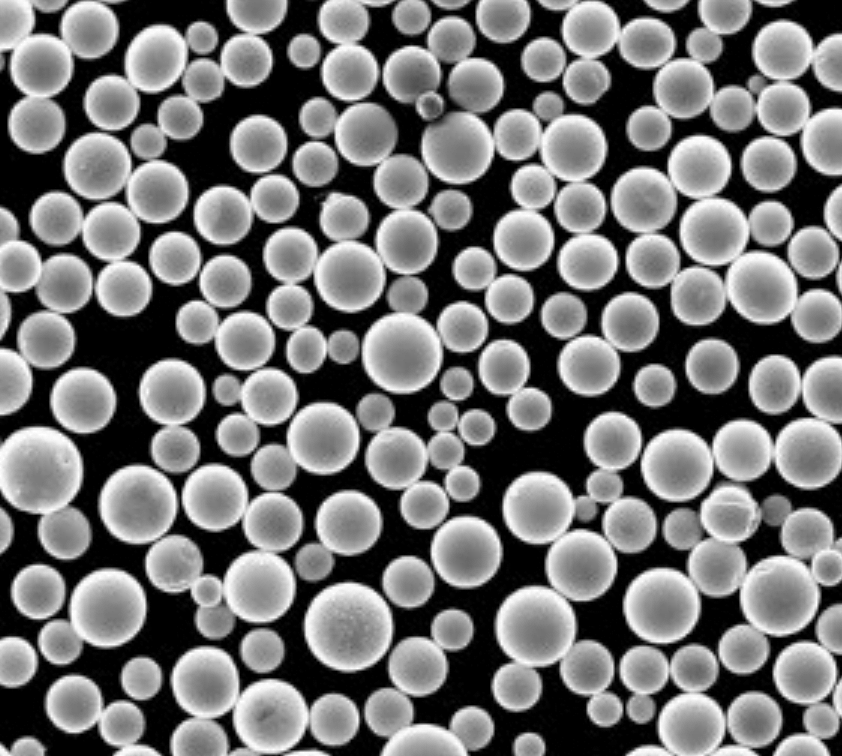
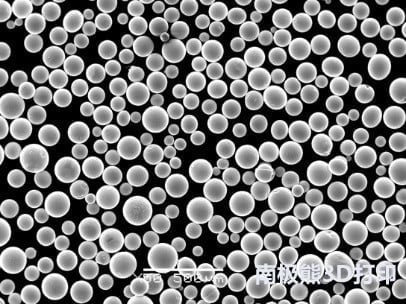
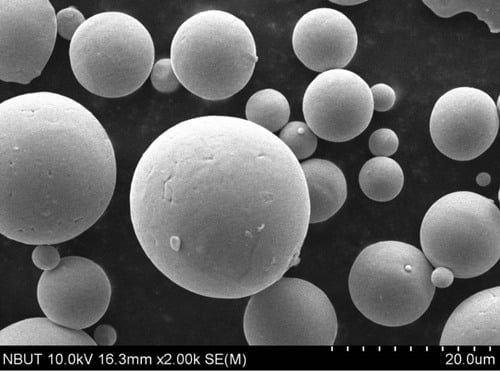
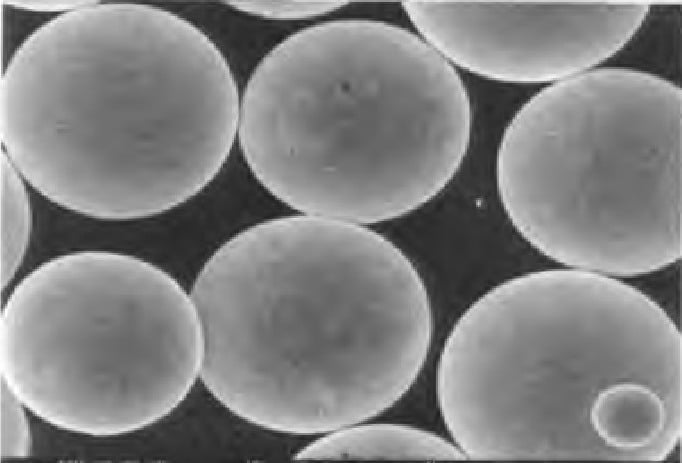
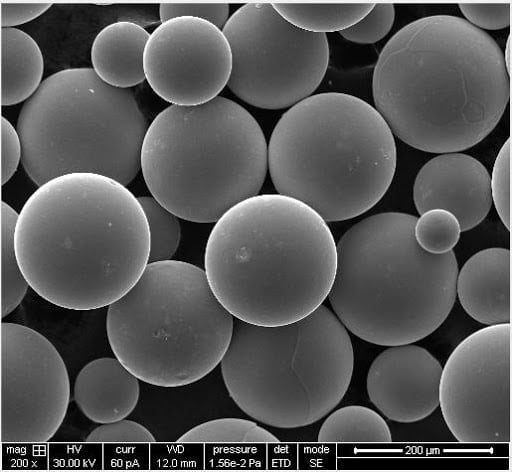
Applications of Cobalt-Chromium Powders
Cobalt-chromium powders are versatile, finding use in various industries due to their unique properties. Let’s explore some of the primary applications.
Medical Implants
Cobalt-chromium alloys, such as CoCrMo and CoCrNi, are widely used in medical implants. Their biocompatibility and corrosion resistance make them ideal for hip and knee replacements, dental prosthetics, and other surgical implants.
Aerospace Components
In the aerospace industry, materials need to withstand extreme conditions. Cobalt-chromium powders, particularly CoCrW and CoCrNiW, are used in gas turbine blades and other high-temperature components due to their exceptional strength and stability.
High-Temperature Environments
Cobalt-chromium powders are also used in environments where high temperatures are a constant challenge. Their ability to maintain structural integrity at elevated temperatures makes them suitable for applications such as heat exchangers and high-temperature engine components.
Cutting Tools
The wear resistance of cobalt-chromium powders, especially CoCrSi and CoCrTa, makes them ideal for cutting tools and wear-resistant
coatings. These materials can endure the rigors of machining and cutting without significant degradation.
Marine Applications
In marine environments, materials are constantly exposed to corrosive seawater. Cobalt-chromium alloys, such as CoCrNiMo, offer high corrosion resistance, making them suitable for marine applications, including shipbuilding and offshore structures.
Specifications, Sizes, and Standards of Cobalt-Chromium Powders
Choosing the right cobalt-chromium powder involves considering various specifications, sizes, and standards to ensure optimal performance for your application.
Specification | Details |
---|---|
Particle Size | Typically ranges from 15 µm to 150 µm |
Purity | High purity levels, often exceeding 99.5% |
Standards | ASTM F75, ISO 5832-4, ASTM F1537 |
Grades | CoCrMo, CoCrNi, CoCrW, etc. |
Table: Sizes and Grades
Size Range (µm) | Grade |
---|---|
15-45 | CoCrMo, CoCrNi, CoCrW |
45-75 | CoCrAl, CoCrFe, CoCrTa |
75-150 | CoCrNiMo, CoCrSi, CoCrNiW, CoCrMn |
Suppliers and Pricing Details of Cobalt-Chromium Powders
When sourcing cobalt-chromium powders, it’s essential to consider reliable suppliers and the associated costs. Here, we provide a snapshot of some suppliers and pricing details.
Supplier | Product | Price (per kg) |
---|---|---|
Sandvik | CoCrMo Powder | $120 – $150 |
Praxair Surface Technologies | CoCrNi Powder | $130 – $160 |
Carpenter Technology | CoCrW Powder | $140 – $170 |
HC Starck | CoCrAl Powder | $125 – $155 |
Oerlikon Metco | CoCrFe Powder | $135 – $165 |
EOS GmbH | CoCrTa Powder | $145 – $175 |
Hoganas AB | CoCrNiMo Powder | $150 – $180 |
Kennametal | CoCrSi Powder | $130 – $160 |
GE Additive | CoCrNiW Powder | $140 – $170 |
Renishaw | CoCrMn Powder | $135 – $165 |
Comparing Pros and Cons of Cobalt-Chromium Powders
Each type of cobalt-chromium powder has its own set of advantages and limitations. Here, we compare these to help you make an informed decision.
Table: Advantages and Limitations
Type | Advantages | Limitations |
---|---|---|
CoCrMo | High strength, excellent wear resistance | Expensive, difficult to machine |
CoCrNi | Good machinability, high corrosion resistance | Moderate strength compared to other alloys |
CoCrW | Exceptional high-temperature strength | High cost, limited availability |
CoCrAl | High oxidation resistance | Lower strength at room temperature |
CoCrFe | Enhanced magnetic properties | Lower corrosion resistance compared to other alloys |
CoCrTa | Excellent biocompatibility | High cost, limited application scope |
CoCrNiMo | Outstanding corrosion resistance | Expensive, difficult to process |
CoCrSi | High hardness, excellent wear resistance | Brittle, challenging to work with |
CoCrNiW | Good corrosion resistance, high-temperature strength | Expensive, limited availability |
CoCrMn | Good wear resistance, affordable | Lower overall strength |
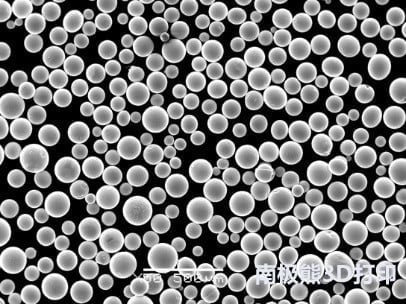
FAQ
Question | Answer |
---|---|
What are cobalt-chromium powders used for? | They are used in medical implants, aerospace components, cutting tools, and high-temperature applications. |
Why are cobalt-chromium powders biocompatible? | They have excellent corrosion resistance and do not cause adverse reactions in the human body. |
Which cobalt-chromium alloy is best for implants? | CoCrMo and CoCrNi are commonly used for their strength and biocompatibility. |
How are cobalt-chromium powders manufactured? | They are typically produced through powder metallurgy, additive manufacturing, and thermal spraying. |
What is the typical particle size of these powders? | Particle sizes usually range from 15 µm to 150 µm, depending on the application. |
Are cobalt-chromium powders expensive? | Yes, they can be relatively expensive, ranging from $120 to $180 per kg depending on the type and supplier. |
Can these powders be used in high-temperature environments? | Yes, alloys like CoCrW and CoCrNiW are designed to maintain stability at high temperatures. |
What are the standards for cobalt-chromium powders? | Common standards include ASTM F75, ISO 5832-4, and ASTM F1537. |
Which alloy is best for cutting tools? | CoCrSi and CoCrTa are ideal due to their high hardness and wear resistance. |
How do I choose the right cobalt-chromium powder? | Consider the specific application requirements, including mechanical properties, corrosion resistance, and biocompatibility. |
In conclusion, cobalt-chromium powders are a versatile and high-performance material suitable for a range of demanding applications. By understanding the different types, compositions, properties, and applications, you can select the right alloy to meet your needs. Whether for medical implants, aerospace components, or cutting tools, these powders offer unparalleled performance and reliability.
About 3DP mETAL
Product Category
CONTACT US
Any questions? Send us a message now! After receiving your message, we will process your request with a whole team.