Introduction
Corrosion resistance powders play a pivotal role in modern engineering and manufacturing, especially when it comes to protecting metals from degradation caused by environmental factors. These powders are used in a range of applications, from aerospace and automotive to industrial equipment. But what exactly makes these powders so essential, and how do you choose the right one for your needs? In this guide, we will dive deep into the world of corrosion resistance powders, exploring their types, characteristics, applications, and more.
What is Corrosion Resistance Powder?
Corrosion resistance powder is a specialized coating material designed to protect metals from corrosion. This powder is applied to metal surfaces to form a protective layer that shields the metal from moisture, chemicals, and other environmental factors that could lead to rust and degradation. By using these powders, industries can extend the lifespan of their equipment and reduce maintenance costs.
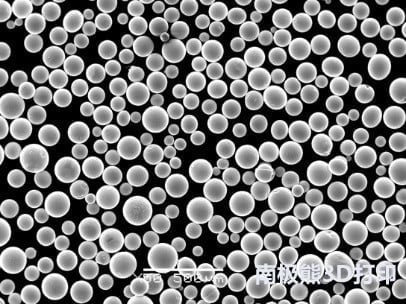
Types of Corrosion Resistance Powders
When it comes to corrosion resistance powders, there are several types available, each with unique properties and applications. Below, we outline some of the most commonly used metal powders, their compositions, and characteristics:
Powder Model | Composition | Properties | Characteristics |
---|---|---|---|
Zinc Powder | Zinc, Zinc Compounds | High galvanic protection, anti-rust | Ideal for steel protection, sacrificial coating |
Aluminum Powder | Aluminum, Aluminum Oxides | Excellent barrier properties | High corrosion resistance, light-weight |
Stainless Steel Powder | Stainless Steel (Fe-Cr-Ni alloys) | High strength, high corrosion resistance | Durable, suitable for harsh environments |
Nickel Powder | Nickel, Nickel Alloys | High resistance to acids and alkalis | Superior durability, expensive |
Chromium Powder | Chromium, Chromium Oxides | High resistance to corrosion and wear | Used in high-performance coatings |
Iron Powder | Pure Iron or Iron Alloys | Moderate corrosion resistance | Cost-effective, used in various applications |
Copper Powder | Copper, Copper Alloys | Excellent thermal and electrical conductivity | Good for conductive coatings |
Titanium Powder | Titanium, Titanium Alloys | Excellent corrosion resistance, lightweight | Used in aerospace and marine applications |
Molybdenum Powder | Molybdenum, Molybdenum Alloys | High melting point, excellent corrosion resistance | High-performance, used in high-temperature environments |
Silver Powder | Silver, Silver Alloys | Excellent conductivity, high corrosion resistance | Used in specialized electronic applications |
Composition of Corrosion Resistance Powders
Understanding the composition of these powders helps in selecting the right type for your needs. Here’s a detailed look at the components that make up various corrosion resistance powders:
Powder Model | Key Components | Purpose of Each Component |
---|---|---|
Zinc Powder | Zinc, Zinc Oxides, Zinc Compounds | Provides sacrificial protection to steel |
Aluminum Powder | Aluminum, Aluminum Oxides | Forms a protective barrier against environmental damage |
Stainless Steel Powder | Iron, Chromium, Nickel | Provides structural strength and corrosion resistance |
Nickel Powder | Nickel, Nickel Alloys | Offers high resistance to corrosive chemicals |
Chromium Powder | Chromium, Chromium Oxides | Enhances resistance to corrosion and wear |
Iron Powder | Iron, Iron Alloys | Basic corrosion resistance, cost-effective |
Copper Powder | Copper, Copper Alloys | Provides electrical and thermal conductivity |
Titanium Powder | Titanium, Titanium Alloys | High strength, excellent corrosion resistance |
Molybdenum Powder | Molybdenum, Molybdenum Alloys | Withstands high temperatures and corrosion |
Silver Powder | Silver, Silver Alloys | High conductivity and excellent corrosion resistance |
Characteristics of Corrosion Resistance Powders
Each type of powder has unique characteristics that make it suitable for specific applications:
Powder Model | Key Characteristics | Applications |
---|---|---|
Zinc Powder | Sacrificial protection, cost-effective | Steel galvanizing, automotive parts |
Aluminum Powder | Barrier protection, lightweight | Aerospace, marine coatings |
Stainless Steel Powder | High strength, durability | Industrial equipment, structural components |
Nickel Powder | Acid and alkali resistance | Chemical processing, electronics |
Chromium Powder | Wear and corrosion resistance | High-performance coatings |
Iron Powder | Basic protection, cost-effective | General industrial use |
Copper Powder | Conductivity, corrosion resistance | Electrical and thermal applications |
Titanium Powder | Lightweight, excellent corrosion resistance | Aerospace, marine applications |
Molybdenum Powder | High melting point, exceptional resistance | High-temperature applications |
Silver Powder | High conductivity, excellent durability | Electronics, specialized applications |
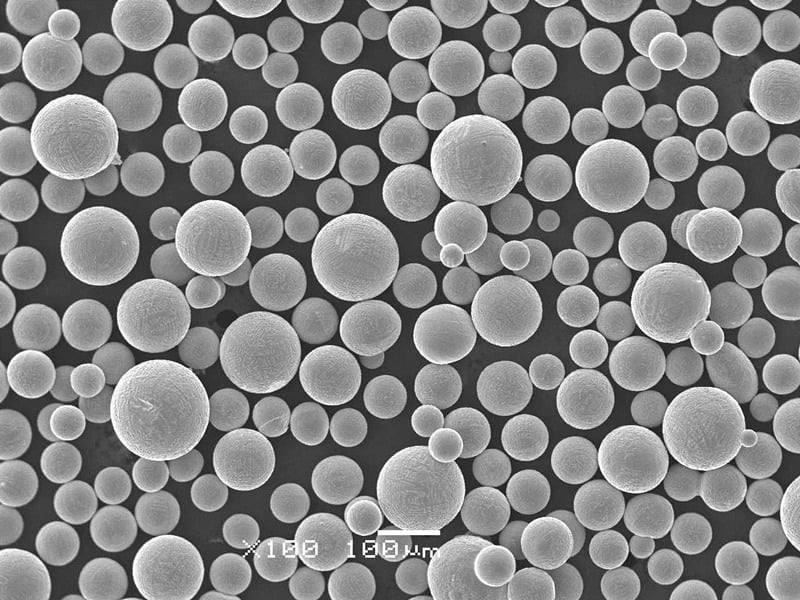
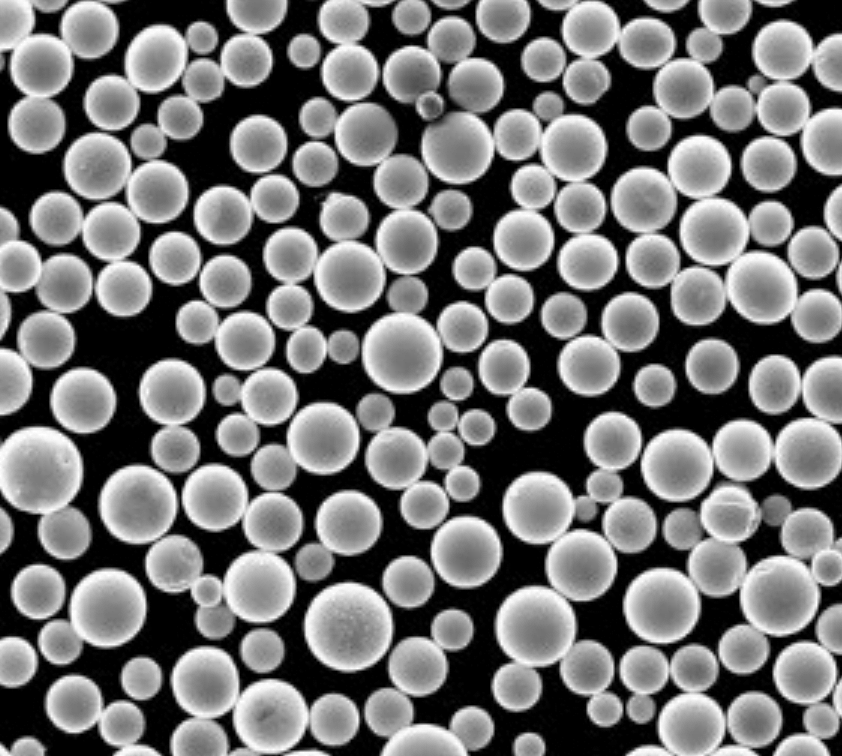
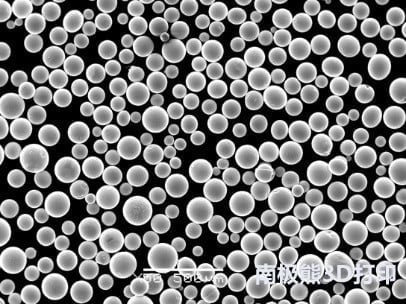
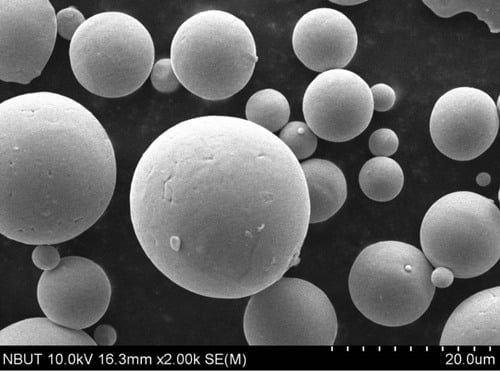
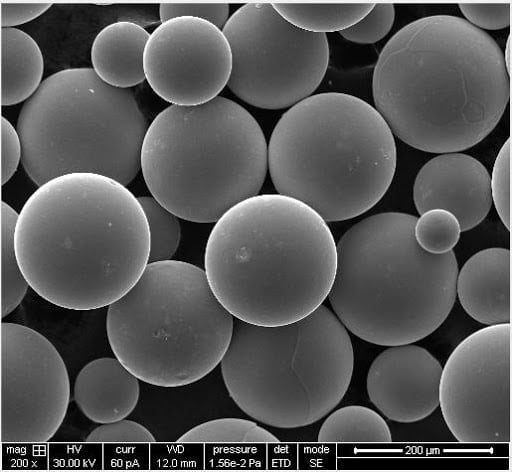
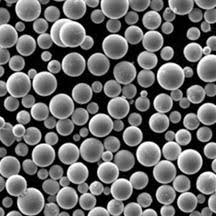
Advantages and Limitations
Every type of corrosion resistance powder comes with its own set of advantages and limitations. Here’s a comparison to help you make an informed choice:
Powder Model | Advantages | Limitations |
---|---|---|
Zinc Powder | Cost-effective, sacrificial protection | Limited to steel, may require frequent reapplication |
Aluminum Powder | Lightweight, excellent barrier properties | Can be expensive, may require specialized application techniques |
Stainless Steel Powder | High durability, resistant to harsh environments | Higher cost, requires careful handling |
Nickel Powder | Superior corrosion resistance, versatile | Expensive, may be overkill for some applications |
Chromium Powder | Exceptional wear resistance, long-lasting | Expensive, can be difficult to apply |
Iron Powder | Affordable, good for general use | Moderate resistance, less durable than other options |
Copper Powder | Excellent conductivity, good resistance | Not ideal for all environments, can be costly |
Titanium Powder | Lightweight, very high corrosion resistance | Expensive, specialized applications required |
Molybdenum Powder | High-temperature resistance, durable | Very costly, limited application areas |
Silver Powder | Outstanding conductivity, corrosion resistance | Very expensive, used in niche applications |
Applications of Corrosion Resistance Powders
Corrosion resistance powders are used in a wide variety of applications across different industries. Here’s a breakdown of where these powders are commonly utilized:
Powder Model | Primary Applications | Industry |
---|---|---|
Zinc Powder | Steel galvanizing, automotive components | Construction, Automotive |
Aluminum Powder | Aerospace coatings, marine environments | Aerospace, Marine |
Stainless Steel Powder | Industrial machinery, structural components | Manufacturing, Construction |
Nickel Powder | Chemical processing, electronics | Chemical, Electronics |
Chromium Powder | High-performance coatings, wear-resistant parts | Automotive, Aerospace |
Iron Powder | General industrial use, iron-based coatings | Manufacturing, Construction |
Copper Powder | Electrical components, thermal applications | Electronics, Electrical Engineering |
Titanium Powder | Aerospace components, marine equipment | Aerospace, Marine |
Molybdenum Powder | High-temperature equipment, industrial parts | Aerospace, Industrial |
Silver Powder | Electronics, specialized high-performance applications | Electronics, High-Tech |
Specifications and Standards
Understanding the specifications and standards for each powder type is crucial for ensuring proper application and performance. Below is a detailed look at the specifications, sizes, and grades for these powders:
Powder Model | Specifications | Sizes Available | Grades | Standards |
---|---|---|---|---|
Zinc Powder | Purity > 99%, Particle size 5-20 microns | 100 mesh, 200 mesh | Standard, High Purity | ASTM B117, ISO 12944 |
Aluminum Powder | Purity > 99%, Particle size 10-50 microns | 60 mesh, 100 mesh | Standard, Fine | ASTM B417, ISO 8501 |
Stainless Steel Powder | Purity > 99%, Particle size 10-45 microns | 80 mesh, 200 mesh | 304, 316, 430 | ASTM A240, ISO 4948 |
Nickel Powder | Purity > 99%, Particle size 10-50 microns | 100 mesh, 200 mesh | Standard, Fine | ASTM B160, ISO 9727 |
Chromium Powder | Purity > 99%, Particle size 10-40 microns | 50 mesh, 100 mesh | Standard, High Purity | ASTM B313, ISO 3685 |
Iron Powder | Purity > 98%, Particle size 10-50 microns | 100 mesh, 200 mesh | Standard, High Purity | ASTM A100, ISO 6438 |
Copper Powder | Purity > 99%, Particle size 20-80 microns | 50 mesh, 100 mesh | Standard, Fine | ASTM B115, ISO 4118 |
Titanium Powder | Purity > 99%, Particle size 20-100 microns | 60 mesh, 100 mesh | Standard, High Purity | ASTM B348, ISO 5832 |
Molybdenum Powder | Purity > 99%, Particle size 10-50 microns | 100 mesh, 200 mesh | Standard, High Purity | ASTM B387, ISO 12680 |
Silver Powder | Purity > 99%, Particle size 10-50 microns | 100 mesh, 200 mesh | Standard, Fine | ASTM B740, ISO 4427 |
Suppliers and Pricing
When it comes to purchasing corrosion resistance powders, it’s important to source from reputable suppliers and be aware of pricing. Below is a table with examples of suppliers and a general idea of pricing:
Powder Model | Supplier | Approximate Price per kg | Notes |
---|---|---|---|
Zinc Powder | Sigma-Aldrich, Makin Metal Powders | $25 – $50 | Varies by purity and quantity |
Aluminum Powder | US Powder, Atlantic Equipment Engineers | $30 – $60 | Price depends on particle size |
Stainless Steel Powder | H.C. Starck, Carpenter Technology | $100 – $200 | Higher for fine grades |
Nickel Powder | Vale, Metallurgical Industries | $150 – $300 | Price varies by alloy |
Chromium Powder | American Elements, Materion | $200 – $400 | High cost due to purity |
Iron Powder | Hoeganaes, Rio Tinto | $15 – $40 | More affordable |
Copper Powder | Fuchs Lubricants, Metal Powder Company | $50 – $100 | Cost varies with market trends |
Titanium Powder | Titanium Industries, AMETEK | $200 – $400 | High cost due to processing |
Molybdenum Powder | Plansee, Global Tungsten & Powders | $250 – $500 | Expensive due to high-tech applications |
Silver Powder | Johnson Matthey, Heraeus | $800 – $1200 | Premium pricing |
Comparing Corrosion Resistance Powders: Pros and Cons
Selecting the right corrosion resistance powder involves weighing the pros and cons of each option. Here’s a comparative look:
Powder Model | Pros | Cons |
---|---|---|
Zinc Powder | Affordable, effective sacrificial protection | Limited to steel, can require frequent maintenance |
Aluminum Powder | Lightweight, good barrier properties | Can be expensive, requires precise application |
Stainless Steel Powder | Highly durable, excellent for harsh environments | High cost, complex handling |
Nickel Powder | Superior chemical resistance | Expensive, may be over-spec for some applications |
Chromium Powder | Excellent wear and corrosion resistance | Very costly, difficult to apply |
Iron Powder | Cost-effective, versatile | Moderate corrosion resistance, less durable |
Copper Powder | Good conductivity, decent resistance | Not suitable for all environments, higher cost |
Titanium Powder | Lightweight, exceptional resistance | Very high cost, specialized use |
Molybdenum Powder | Excellent high-temperature resistance | Very expensive, limited applications |
Silver Powder | Outstanding conductivity and durability | Extremely high cost, niche applications |
Applications in Different Industries
Corrosion resistance powders are tailored to meet the specific needs of various industries. Below is an overview of how these powders are applied across different sectors:
Industry | Powder Models Used | Typical Applications |
---|---|---|
Automotive | Zinc Powder, Stainless Steel Powder | Underbody coatings, engine components |
Aerospace | Aluminum Powder, Titanium Powder | Aircraft parts, jet engine components |
Marine | Aluminum Powder, Stainless Steel Powder | Ship hulls, offshore equipment |
Chemical Processing | Nickel Powder, Chromium Powder | Reactors, pipelines |
Electronics | Copper Powder, Silver Powder | Circuit boards, connectors |
Construction | Iron Powder, Zinc Powder | Structural steel, reinforcing bars |
Industrial Equipment | Stainless Steel Powder, Molybdenum Powder | Machinery, tools |
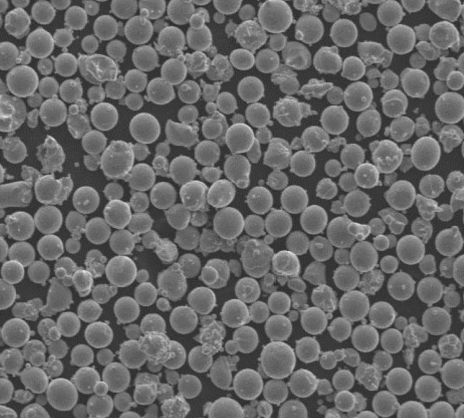
FAQ
Here’s a quick reference to some common questions about corrosion resistance powders:
Question | Answer |
---|---|
What is the main benefit of using corrosion resistance powder? | The primary benefit is to protect metal surfaces from rust and degradation, extending the lifespan of equipment and reducing maintenance costs. |
How do I choose the right corrosion resistance powder for my application? | Consider the specific environmental conditions, mechanical requirements, and budget. Different powders offer varying levels of protection and cost. |
Are there environmental considerations for using these powders? | Yes, some powders may have environmental impacts, such as the release of fine particles. Always check for environmental certifications and guidelines. |
How often does corrosion resistance powder need to be reapplied? | It depends on the type of powder and the conditions of use. Some coatings may last several years, while others might need more frequent reapplication. |
Can corrosion resistance powders be applied to any type of metal? | Most powders are designed for specific metals or alloys. Always check the manufacturer’s recommendations for compatibility. |
What are the safety considerations when handling these powders? | Wear appropriate protective equipment such as gloves and masks. Follow the manufacturer’s safety guidelines to minimize exposure. |
How do corrosion resistance powders compare to traditional coatings? | Powders generally offer better durability and protection compared to traditional liquid coatings, especially in harsh environments. |
Conclusion
Choosing the right corrosion resistance powder is essential for ensuring the longevity and performance of metal components. By understanding the various types of powders, their compositions, characteristics, and applications, you can make informed decisions that align with your specific needs. Whether you’re in aerospace, automotive, or another industry, the right powder can make a significant difference in performance and durability.
For more detailed information, consult with suppliers and consider your specific application requirements to find the best corrosion resistance solution.
About 3DP mETAL
Product Category
CONTACT US
Any questions? Send us a message now! After receiving your message, we will process your request with a whole team.