Imagine a world where creating physical objects is as simple as downloading a file and hitting print. Well, that’s the magic of 3D-Druck, a revolutionary technology that’s transforming countless industries. But with so many different 3D printing processes out there, it can feel overwhelming for beginners. Fear not, curious minds! This guide will be your compass, navigating the most common types of 3D printing and demystifying their unique capabilities.
Fused Deposition Modeling (FDM)
Think of FDM as the trusty inkjet printer of the 3D world. It’s the most widely used technology due to its affordability, versatility, and ease of use. Here’s how it works: a spool of filament (think of it as a thin plastic wire) is fed through a heated nozzle. This molten plastic is meticulously deposited layer by layer, building your 3D creation from the bottom up.
What can you print with FDM? The answer is a vast array of objects, from phone cases and toys to prototypes and architectural models. FDM shines in creating durable, functional parts with a wide range of filament options like PLA (plant-based plastic), ABS (strong and heat-resistant), and even exotic materials like woodfill or metalfill.
Pros of FDM:
- Affordable: FDM printers are generally the most budget-friendly option, making them perfect for hobbyists and schools.
- Easy to use: FDM printing is relatively straightforward, with a simple setup and readily available filament.
- Wide material selection: Experiment with different filament types to achieve desired properties like strength, flexibility, or aesthetics.
Cons of FDM:
- Print quality: Compared to other technologies, FDM prints may have visible layer lines, resulting in a slightly rougher surface finish.
- Limited color options: While you can find filaments in various colors, FDM printing typically offers a single color per print.
- Printing time: Depending on the object’s complexity and size, FDM prints can take a significant amount of time.
Who should consider FDM? FDM is a fantastic choice for beginners, educators, and hobbyists who want to explore the world of 3D printing without breaking the bank. It’s also well-suited for rapid prototyping and creating functional parts that prioritize durability over aesthetics.
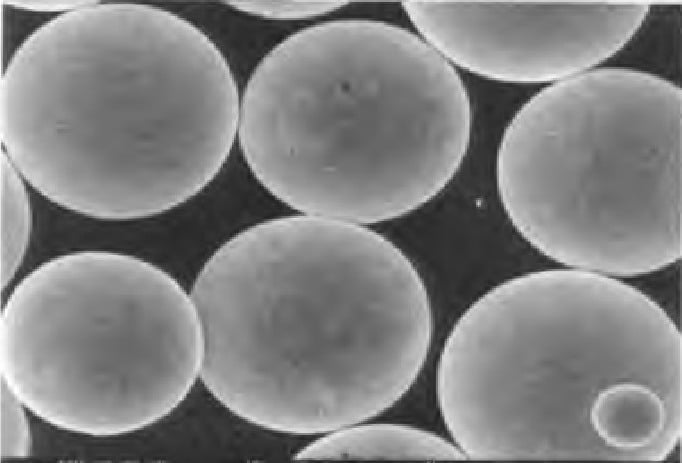
Stereolithographie (SLA)
If you crave high-resolution prints with exceptional detail, then SLA is your knight in shining armor. This technology utilizes a laser beam to selectively cure liquid resin layer by layer, solidifying it into your desired 3D object. Think of it like sculpting with light!
What can you print with SLA? SLA excels in creating intricately detailed models, jewelry prototypes, and even medical devices. The smooth surface finish and fine details make SLA prints stand out, particularly for applications where appearance is paramount.
Pros of SLA:
- Exceptional detail: SLA produces some of the most detailed and smooth-surfaced prints in the 3D-Druck world.
- Wide range of materials: Explore a variety of resins with unique properties, from clear and transparent to tough and durable.
- Accuracy: SLA prints boast high dimensional accuracy, making them ideal for applications requiring precise measurements.
Cons of SLA:
- Kosten: SLA printers tend to be more expensive than FDM printers, both in terms of machine cost and resin materials.
- Nachbearbeitung: SLA prints often require additional post-processing steps like cleaning and curing, adding time to the overall workflow.
- Limited material properties: While resin options are expanding, SLA materials generally offer less flexibility and strength compared to FDM filaments.
Who should consider SLA? SLA is perfect for designers, jewelers, and professionals who require high-fidelity prints with exceptional detail. It’s also a valuable tool for creating prototypes and models for applications where visual accuracy is crucial.
Here’s a quick comparison between FDM and SLA to help you decide:
Merkmal | FDM | SLA |
---|---|---|
Kosten | Affordable | Teurer |
Ease of use | Easier to use | Requires more setup and post-processing |
Print quality | Good, visible layer lines | Excellent, smooth surface finish |
Material selection | Wide range of filaments | Wide range of resins |
Ideal for | Functional parts, prototypes | Detailed models, jewelry, prototypes |
3D-Druck: Selective Laser Sintering (SLS)
SLS takes a different approach to 3D printing, utilizing a high-powered laser to selectively sinter (fuse) tiny particles of powder together, layer by layer, building your 3D model. Imagine a magical 3D sandbox where the laser acts like your sculpting tool!
What can you print with SLS? SLS excels in creating strong, functional parts with a fine level of detail. Common applications include prototypes, automotive parts, and even medical implants. The materials used in SLS, like nylon and metal powders, offer exceptional strength and durability, making them ideal for applications requiring high performance.
Pros of SLS:
- Strength and durability: SLS-printed parts boast exceptional strength and heat resistance, making them suitable for demanding applications.
- High accuracy: SLS delivers high dimensional accuracy, perfect for creating precise and functional parts.
- Wide material selection: Explore a variety of powders, including nylon, glass-filled nylon, and even metals like aluminum and titanium.
Cons of SLS:
- Kosten: SLS printers are on the higher end of the 3D printing spectrum, both in terms of machine cost and material prices.
- Support structures: SLS prints often require intricate support structures, which can add time and waste material during post-processing.
- Limited color options: Similar to FDM, SLS printing typically offers a single color per print, though some machines offer multi-material capabilities.
Who should consider SLS? SLS is a valuable tool for engineers, product designers, and professionals who require strong, functional prototypes or end-use parts. It’s particularly well-suited for applications in the automotive, aerospace, and medical industries.
Here’s a table summarizing the key differences between FDM, SLA, and SLS to help you choose the right technology for your needs:
Merkmal | FDM | SLA | SLS |
---|---|---|---|
Technologie | Material extrusion (filament) | Vat photopolymerization (resin) | Powder bed fusion (powder) |
Kosten | Affordable | Teurer | Most expensive |
Ease of use | Easy to use | Requires more setup and post-processing | Requires more expertise |
Print quality | Good, visible layer lines | Excellent, smooth surface finish | Excellent, high detail |
Material selection | Wide range of filaments | Wide range of resins | Wide range of powders (including metals) |
Ideal for | Functional parts, prototypes | Detailed models, jewelry, prototypes | Strong, functional parts, prototypes, end-use parts |
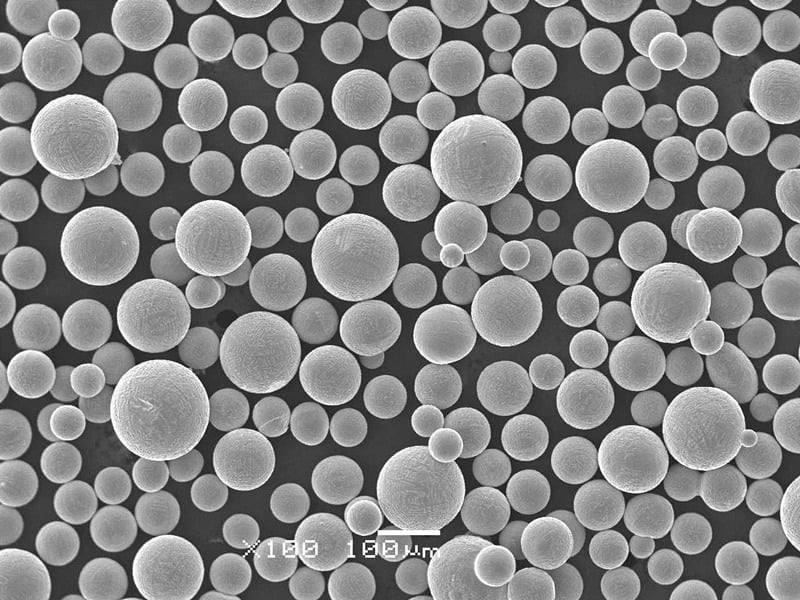
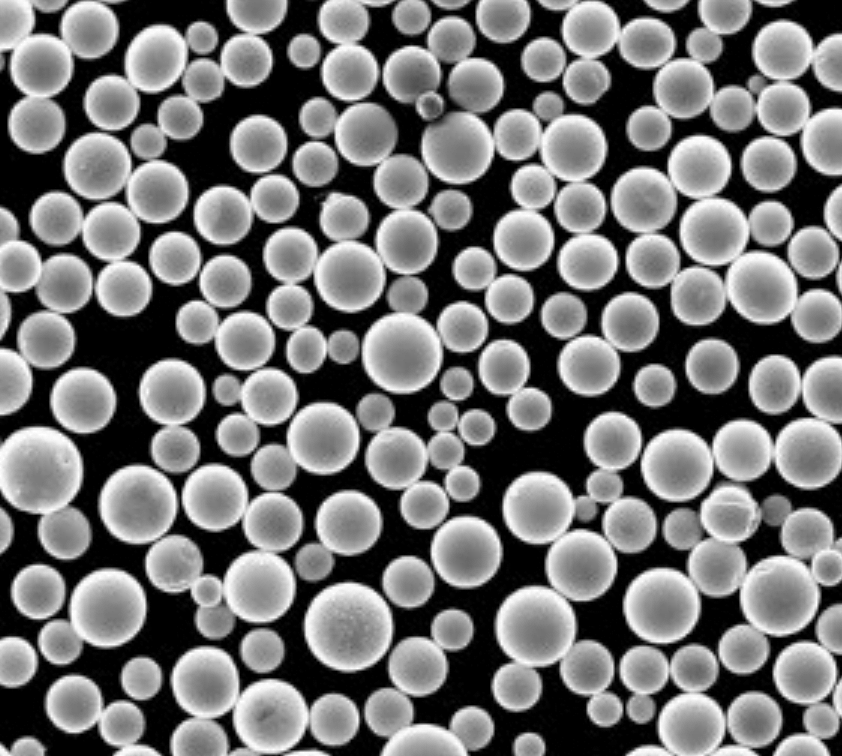
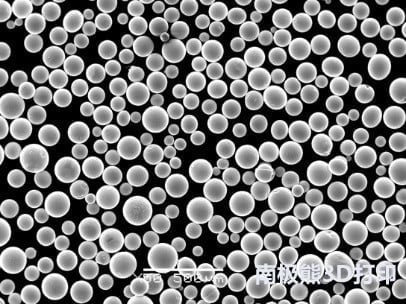
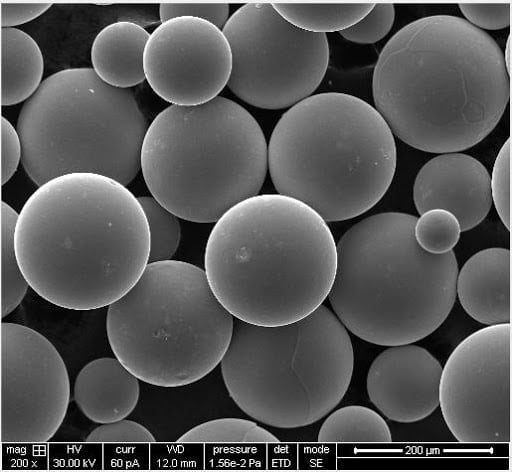
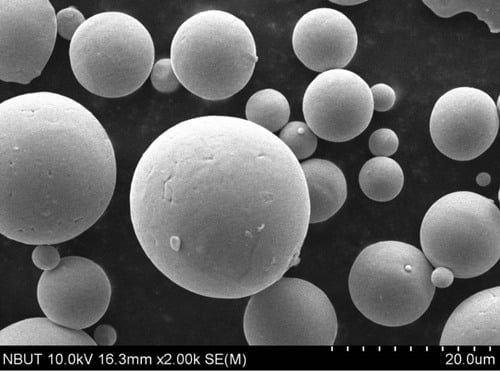
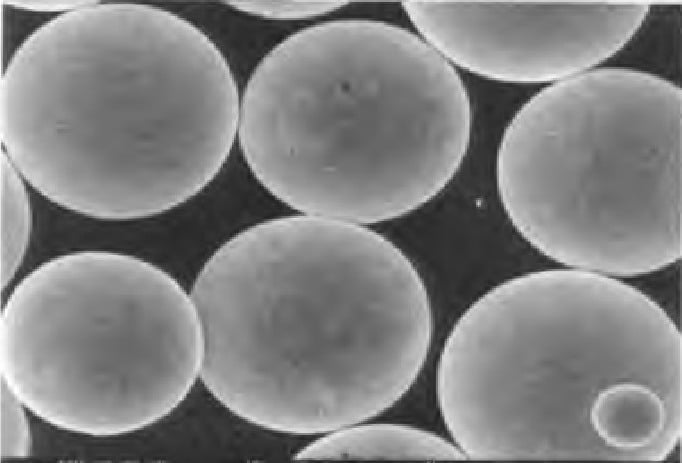
Multi Jet Fusion (MJF)
MJF is a relatively new and exciting 3D printing technology developed by HP. Similar to SLS, it utilizes a powder bed, but instead of a laser, MJF employs a printhead that jets droplets of binding agent and detailing agents across the powder layers. This inkjet-like approach allows for incredible detail and full-color capabilities.
What can you print with MJF? MJF shines in creating functional prototypes with high detail and vibrant colors. Imagine printing a realistic prototype of a new product with all its intricate details and branding colors! This makes MJF ideal for product designers, engineers, and marketing professionals who need prototypes that closely resemble the final product.
Pros of MJF:
- Full-color printing: Unlike most other 3D printing technologies, MJF allows for printing objects in full color, adding a new dimension to prototypes and models.
- High detail: MJF delivers excellent detail and resolution, making it ideal for creating complex prototypes.
- Fast printing: Compared to some other 3D printing processes, MJF offers faster printing speeds.
Cons of MJF:
- Kosten: MJF printers are still a relatively new technology and can be expensive compared to FDM or SLA.
- Begrenzte Materialauswahl: While materials are expanding, MJF currently offers a narrower range compared to FDM or SLS.
- Support structures: Similar to SLS, MJF prints may require support structures, adding to post-processing time.
Who should consider MJF? MJF is a valuable tool for product designers, engineers, and marketing professionals who require high-fidelity, full-color prototypes for product development and marketing purposes.
Digital Light Processing (DLP)
Think of DLP as SLA’s energetic little cousin. It utilizes a projector instead of a laser beam to cure an entire layer of resin at once. This significantly reduces printing time compared to SLA, making DLP a great option for high-volume printing.
Think of DLP as SLA’s energetic little cousin. It utilizes a projector instead of a laser beam to cure an entire layer of resin at once. This significantly reduces printing time compared to SLA, making DLP a great option for high-volume printing.
What can you print with DLP? DLP excels in creating detailed models, jewelry prototypes, and dental applications. Similar to SLA, DLP shines in applications where exceptional detail and smooth surface finish are crucial.
Pros of DLP:
- Faster printing: DLP boasts significantly faster printing speeds compared to SLA, making it ideal for larger print jobs or production environments.
- High detail: Just like SLA, DLP delivers exceptional detail and resolution, perfect for intricate models.
- Wide range of materials: Explore a variety of resins with unique properties, similar to the selection available in SLA printing.
Cons of DLP:
- Kosten: While generally less expensive than SLA, DLP printers still carry a higher price tag compared to FDM.
- Limited color options: Similar to most other 3D printing processes, DLP typically offers single-color printing per build.
- Resolution limitations: Compared to the high-resolution lasers used in SLA, DLP projectors may have limitations in achieving the absolute finest details.
Who should consider DLP? DLP is a valuable tool for businesses and professionals who require high-volume production of detailed parts, such as jewelry makers, dental labs, and manufacturers of miniature models. It’s a good compromise between SLA’s exceptional detail and the faster printing speeds needed for production environments.
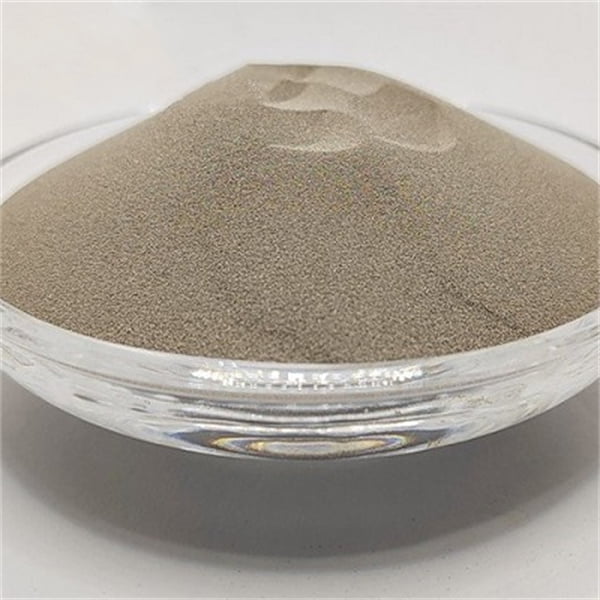
Binder Jetting
Binder jetting takes a unique approach, utilizing a printhead that jets a binding agent onto layers of powder, inkjet style. Unlike SLS and MJF that use high temperatures to fuse the powder particles, binder jetting relies on the adhesive properties of the binding agent. This allows for a wider range of powder materials, including sand!
What can you print with Binder Jetting? Binder jetting is commonly used for creating large-scale prototypes, architectural models, and even molds for metal casting. The ability to use sand as a printing material makes binder jetting a cost-effective option for large projects.
Pros of Binder Jetting:
- Large-scale printing: Binder jetting excels at creating large objects due to the flexibility in build volume.
- Wide material selection: Explore a variety of powder materials beyond just plastics, including sand, metal powders, and even ceramics.
- Kostengünstig: For large prints, binder jetting can be a more economical option compared to other 3D printing technologies.
Cons of Binder Jetting:
- Strength and durability: Binder-jetted parts generally have lower strength and durability compared to SLS or MJF printed parts.
- Nachbearbeitung: Binder jetted parts require extensive post-processing steps, including infiltration with strengthening agents and additional curing.
- Oberflächengüte: The surface finish of binder-jetted parts may be rougher compared to other technologies.
Who should consider Binder Jetting? Binder jetting is a valuable tool for architects, designers, and professionals who need to create large-scale models or prototypes. It’s also used in applications like creating sand molds for metal casting.
Elektronenstrahlschmelzen (EBM)
EBM takes 3D printing to a whole new level by utilizing an electron beam to melt metal powder layer by layer, building a solid metal object. Imagine a miniature electron forge in your workshop, meticulously crafting metal parts!
What can you print with EBM? EBM excels in creating high-strength, complex metal parts for demanding applications. Common uses include aerospace components, medical implants, and tools and molds for extreme environments.
Pros of EBM:
- Exceptional strength: EBM-printed parts boast exceptional strength and heat resistance, making them ideal for functional metal parts.
- High accuracy: EBM delivers high dimensional accuracy and intricate details, perfect for complex metal components.
- Biocompatible materials: Certain metal powders used in EBM are biocompatible, making this technology valuable for medical implants.
Cons of EBM:
- Kosten: EBM printers are the most expensive 3D printing technology on this list, with both high machine costs and expensive metal powders.
- Sicherheitserwägungen: EBM printing involves high temperatures and electron beams, requiring proper safety protocols and trained personnel.
- Limited build volume: Compared to some other 3D printing technologies, EBM printers typically have smaller build volumes.
Who should consider EBM? EBM is a powerful tool for aerospace, automotive, and medical industries that require high-performance, metal parts.
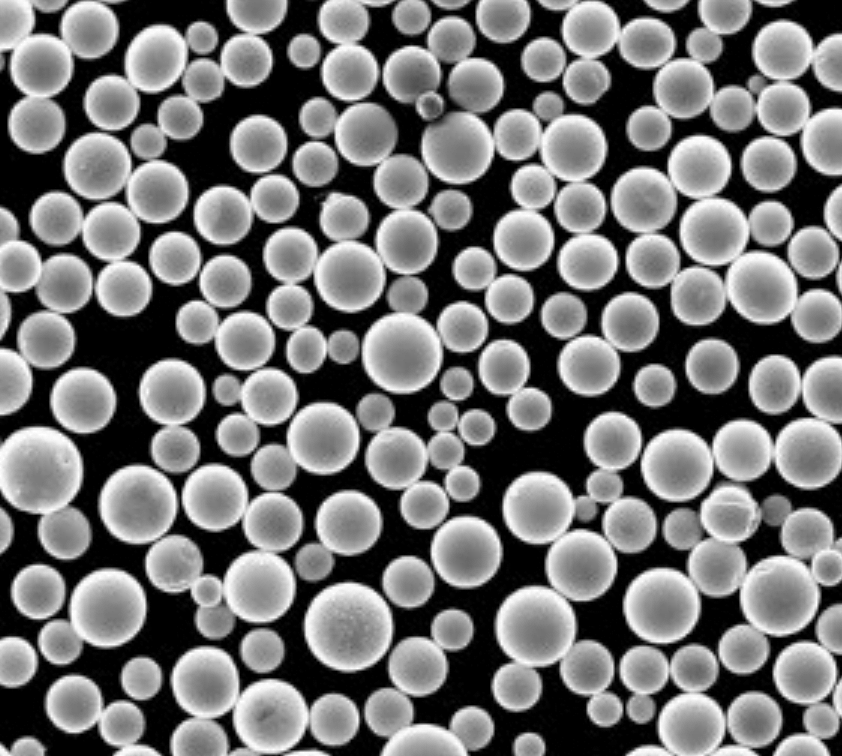
FAQ
This FAQ section provides a quick reference guide to the 3D printing technologies covered in this article, answering common questions in an easy-to-understand format.
Frage | FDM | SLA | SLS | MJF | DLP | Binder Jetting | EBM |
---|---|---|---|---|---|---|---|
What is it? | Fused Deposition Modeling | Stereolithography | Selective Laser Sintering | Multi Jet Fusion | Digital Light Processing | Binder Jetting | Elektronenstrahlschmelzen |
How does it work? | Extrudes molten filament layer by layer | Uses a laser to cure liquid resin layer by layer | Uses a laser to sinter powder particles layer by layer | Uses inkjet technology to jet binding agent and detailing agents onto powder layers | Uses a projector to cure an entire layer of resin at once | Uses inkjet technology to jet binding agent onto powder layers | Uses an electron beam to melt metal powder layer by layer |
What materials can it print with? | Wide range of filaments (PLA, ABS, etc.) | Wide range of resins | Wide range of powders (nylon, metal powders) | Wide range of powders (including nylon and some metals) | Wide range of resins | Wide range of powders (including sand) | Metal powders (titanium, Inconel) |
What are the pros? | Affordable, easy to use, wide material selection | Exceptional detail, high accuracy, wide material selection | Strong and durable parts, high accuracy, wide material selection | Full-color printing, high detail, fast printing | Faster printing than SLA, high detail, wide range of resins | Large-scale printing, wide material selection, cost-effective | High-strength metal parts, high accuracy, biocompatible materials |
What are the cons? | Lower print quality (visible layer lines), limited color options, longer printing times | More expensive, requires post-processing, limited material properties | Expensive, requires support structures, limited color options | Expensive, limited material selection, requires support structures | Limited color options, resolution limitations | Lower strength, extensive post-processing, rougher surface finish | Most expensive, safety considerations, limited build volume |
Who should consider it? | Hobbyists, educators, beginners, prototyping | Designers, jewelers, professionals requiring high detail | Engineers, product designers, professionals requiring strong functional parts | Product designers, engineers, marketing professionals needing full-color prototypes | Businesses, professionals needing high-volume detailed parts | Architects, designers, professionals needing large-scale models or prototypes | Aerospace, automotive, medical industries needing high-performance metal parts |
Über 3DP mETAL
Produktkategorie
KONTAKT
Hast du Fragen? Schick uns jetzt eine Nachricht! Nach Eingang deiner Nachricht bearbeiten wir deine Anfrage im Team.