The world of metal additive manufacturing, also known as 3D printing, is revolutionizing how we design and produce mechanical parts. Gone are the days of clunky, time-consuming subtractive manufacturing techniques. With 3D printing, complex geometries and intricate designs are just a button press away. But choosing the right metal powder for the job is crucial. Enter 8620 Stahlmehl – a versatile workhorse powering the creation of a vast array of mechanical components.
Understanding 8620 Steel Powders
8620 steel belongs to the low-alloy steel family, known for its excellent balance of strength, toughness, and machinability. This desirable combination stems from its specific chemical composition:
Element | Gew.-% | Funktion |
---|---|---|
Chrom (Cr) | 0.15 – 0.25 | Enhances hardenability and corrosion resistance |
Nickel (Ni) | 0.40 – 0.70 | Improves strength and toughness |
Molybdän (Mo) | 0.15 – 0.25 | Further enhances hardenability and high-temperature strength |
Mangan (Mn) | 0.70 – 1.00 | Improves hardenability and grain refinement |
Kohlenstoff (C) | 0.18 – 0.23 | Primary contributor to strength and hardness |
Silizium (Si) | 0.15 – 0.35 | Improves deoxidization and castability |
Eisen (Fe) | Balanse | The base metal that binds all elements together |
By carefully controlling these elements, manufacturers create a metal powder specifically designed for additive manufacturing processes like Selective Laser Melting (SLM) and Electron Beam Melting (EBM).
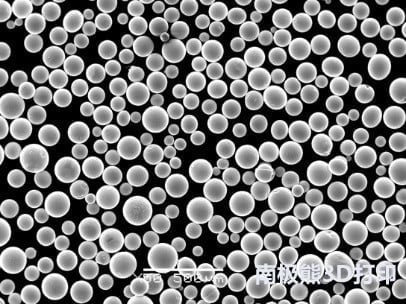
Anwendungen von 8620 Stahlmehl
The versatility of 8620 steel translates into a wide range of applications across various industries.
Industrie | ANWENDUNGEN |
---|---|
Automotive | Gears, shafts, brackets, suspension components |
Luft- und Raumfahrt | Engine components, lightweight structural parts, landing gear components |
Öl- und Gasindustrie | Downhole tools, valves, casings |
Medizinisch | Surgical instruments, prosthetics, dental implants |
Konsumgüter | Sporting goods components, firearm parts, tools |
Imagine needing a custom gear for a high-performance race car. Traditional manufacturing might require extensive machining, leading to material waste and longer production times. With 8620 steel powder, 3D printing allows for the creation of a strong, lightweight gear with intricate internal features – all in one go! This translates to faster development cycles, lighter vehicles, and potentially, a podium finish.
Beyond the Applications: Unveiling the Hidden Gems of 8620 Steel
But the power of 8620 goes beyond its diverse applications. Here are some key characteristics that make it a popular choice:
- Excellent Strength and Toughness: The combination of chromium, nickel, and molybdenum creates a material that can withstand significant loads and impacts without compromising integrity. Think of it as the “Goldilocks” zone of strength – not too brittle, not too soft.
- Gute Bearbeitbarkeit: Even after 3D printing, 8620 parts can be further machined to achieve precise tolerances and surface finishes. This allows for the creation of even more complex and high-precision components.
- Schweißeignung: Need to join multiple 3D printed parts together? No problem! 8620 exhibits good weldability, making it ideal for creating larger assemblies. Think of it as Legos for grown-ups – but way stronger!
- Kostengünstig: Compared to other high-performance metal powders, 8620 offers a balance of desirable properties at a competitive price point. This makes it a budget-friendly option for a range of applications.
However, no material is perfect. Here are some limitations to consider:
- Moderate Corrosion Resistance: While offering some protection from the elements, 8620 is not ideal for highly corrosive environments. Think of it like a raincoat in a light drizzle – good for everyday use, but not for a tropical storm. For those situations, manufacturers might opt for stainless steel powders.
- Heat Treatment Required: To achieve its full strength potential, 8620 parts often require post-processing heat treatment. This adds an extra step to the manufacturing process.
Exploring the World of 8620 Steel Powders
Not all 8620 steel powders are created equal. Different manufacturers offer variations with slight tweaks in composition or processing methods, leading to subtle differences in performance. Here, we delve into the world of some popular 8620 steel powder options:
1. Höganäs AM 265 (Höganäs AB, Sweden) This gas-atomized powder boasts excellent flowability and packing density, leading to good printability and minimal waste during the 3D printing process. Höganäs AM 265 offers a good balance of strength, toughness, and ductility, making it suitable for a wide range of applications.
2. LPW® 8620 (LPW Technology Ltd., UK) LPW® 8620 is another gas-atomized powder known for its high sphericity and tight particle size distribution. This translates to smooth surface finishes and consistent mechanical properties in the final printed parts. LPW® 8620 is a popular choice for applications requiring high precision and dimensional accuracy.
3. EOS StainlessSteel 17-4 PH (EOS GmbH, Germany) While technically not a pure 8620 steel, EOS StainlessSteel 17-4 PH offers a close composition with similar properties. This gas-atomized powder is known for its excellent weldability and good corrosion resistance, making it a versatile option for parts exposed to harsh environments.
4. AMSL 316L (Additive Manufacturing Sciences Ltd., UK) This nitrogen-atomized powder offers a slightly higher Nickel content compared to traditional 8620. This translates to improved strength and high-temperature performance. AMSL 316L is a good choice for applications requiring additional strength under demanding operating conditions.
5. Element 174 (Element 17, LLC, USA) This gas-atomized powder is known for its high level of purity and tight chemical composition control. This translates to consistent performance and predictable mechanical properties in the final printed parts. Element 174 is a good option for applications where repeatability and high-quality standards are paramount.
6. Carpenter Incusa 316L (Carpenter Technology Corporation, USA) Another variation on the 8620 theme, Carpenter Incusa 316L boasts a slightly higher Molybdenum content. This enhances its high-temperature strength and creep resistance, making it suitable for applications involving heat and sustained loads.
7. SLM Solutions SX 17-4 PH (SLM Solutions GmbH, Germany) This gas-atomized powder is specifically optimized for use with SLM 3D printing machines from SLM Solutions. It offers excellent flowability and packing density, leading to efficient printing processes and minimal material waste.
8. Proto Labs 316L (Proto Labs, Inc., USA) Proto Labs offers a gas-atomized 316L powder suitable for a wide range of applications. They prioritize fast turnaround times and high-quality standards, making it a good option for rapid prototyping and low-volume production runs.
9. ExOne M2 Metal (ExOne GmbH, Germany) This binder jetting-specific powder boasts a slightly coarser particle size compared to traditional 8620 powders used in laser-based 3D printing. This allows for efficient powder spreading and good packing density in the binder jetting process.
10. BASF AM StainlessSteel 17-4 PH (BASF SE, Germany) BASF offers a gas-atomized 17-4 PH powder known for its good printability and consistent mechanical properties. They have a strong focus on quality control and material consistency, making it a reliable option for demanding applications.
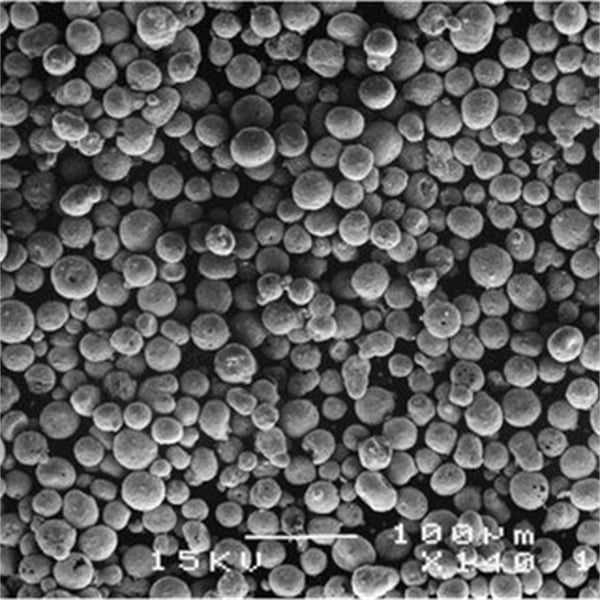
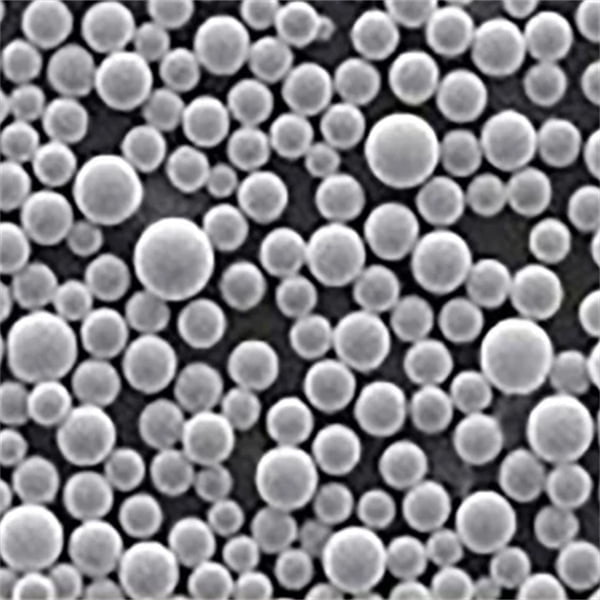
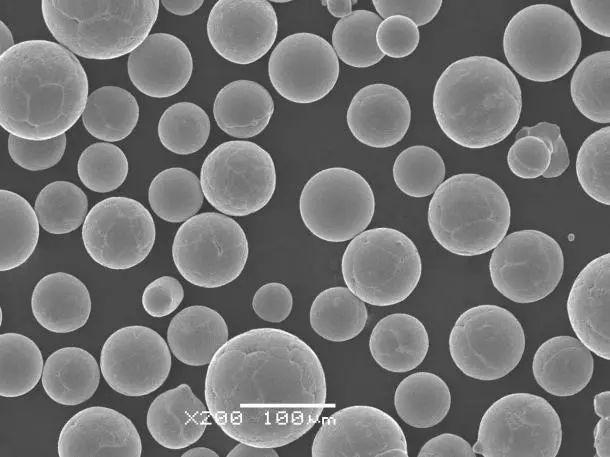
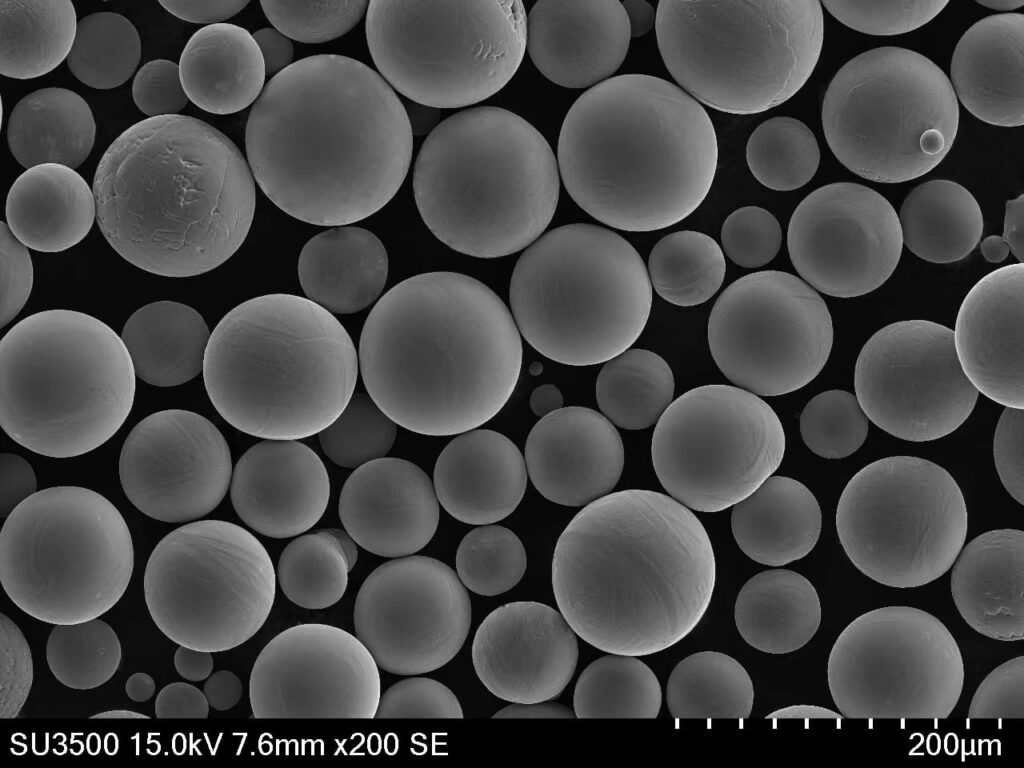
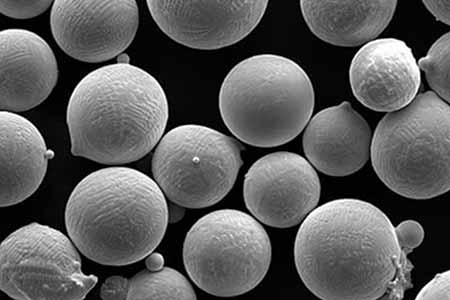
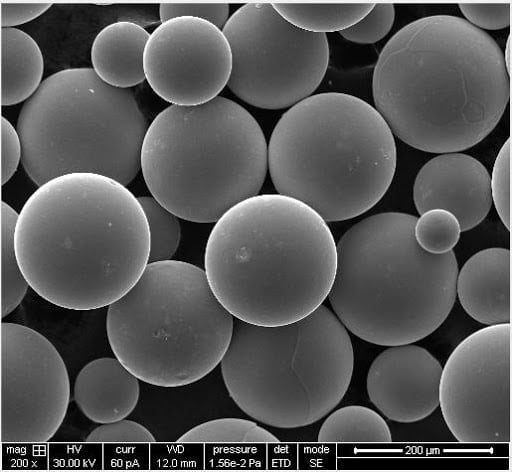
Choosing Your Weapon: A Comparative Analysis
While all these powders fall under the 8620 umbrella, subtle differences exist. Here’s a breakdown to help you choose the right one for your project:
Merkmal | Überlegungen | Powders to Consider |
---|---|---|
Bewerbung | Strength, Corrosion Resistance, High-Temperature Performance | Varies depending on the specific needs. |
3D Printing Process | Laser Melting (SLM) vs. Electron Beam Melting (EBM) vs. Binder Jetting | Powders are often optimized for specific processes. |
Flowability & Packing Density | Impacts printability and material waste | Höganäs AM 265, LPW® 8620 |
Sphericity & Particle Size Distribution | Impacts surface finish and mechanical properties | LPW® 8620, Element 174 |
Korrosionsbeständigkeit | For parts exposed to harsh environments | EOS StainlessSteel 17-4 PH (consider stainless steel powders for extreme cases) |
Schweißbarkeit | Important for joining multiple printed parts | EOS StainlessSteel 17-4 PH |
Leistung bei hohen Temperaturen | For applications involving heat and sustained loads | AMSL 316L, Carpenter Incusa 316L |
Purity & Chemical Composition Control | Impacts consistency and repeatability | Element 174 |
Price | Consider budget constraints | Varies depending on the manufacturer and powder characteristics |
Beyond the Table: Expert Insights and Real-World Examples
Remember, the best powder choice hinges on a deeper understanding of your specific project needs. Consider consulting with experienced 3D printing professionals who can analyze your application and recommend the most suitable option. Here are some additional factors to consider:
- Build complexity: Highly intricate designs might benefit from powders with exceptional flowability and packing density, like Höganäs AM 265.
- Nachbearbeitungsanforderungen: If your application demands a high-quality surface finish, powders known for tight particle size distribution like LPW® 8620 might be ideal.
- Lead time and turnaround times: Proto Labs 316L could be a good option if fast turnaround times are crucial for rapid prototyping.
Seeing 8620 Steel in Action
The versatility of 8620 steel powders translates into a wide range of successful applications across industries. Here are a few inspiring examples:
- Lightweighting Efforts in Motorsports: Formula One racing teams are constantly pushing the boundaries of weight reduction. 8620 steel components, like suspension arms and gear housings, offer a combination of strength and weight savings, allowing for faster lap times and improved performance.
- Aerospace Takes Flight: The aerospace industry utilizes 8620 steel for lightweight structural parts and engine components. These components benefit from the material’s good strength-to-weight ratio and ability to withstand demanding operating conditions.
- Medizinische Wundermittel: The intricate world of medical implants requires materials that are biocompatible and strong. Custom surgical instruments and prosthetics can be created using 8620 steel powder, offering patients a durable and reliable solution.
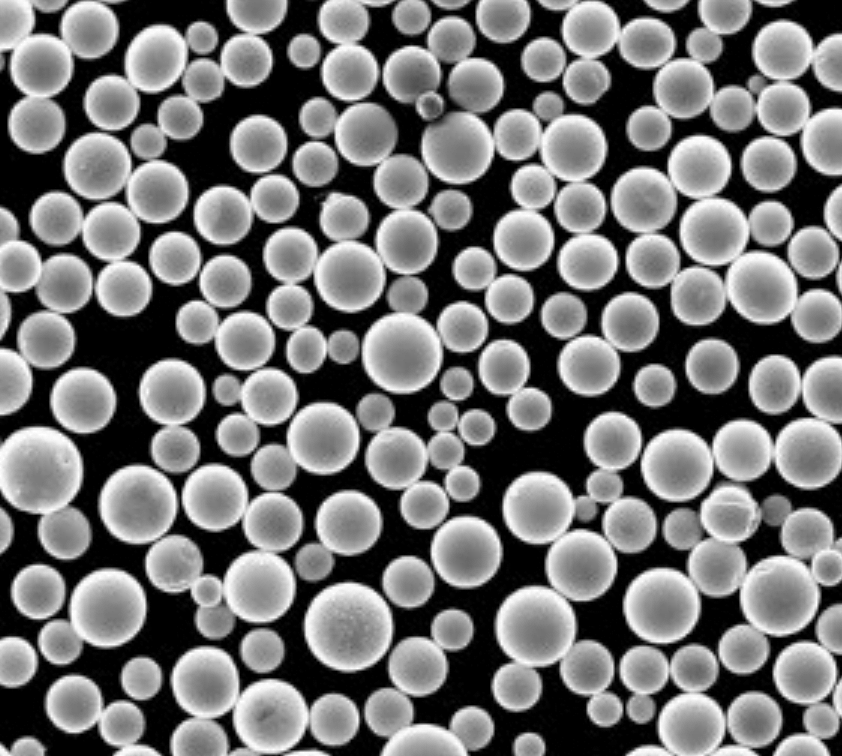
FAQ
Q: Is 8620 steel powder the same as stainless steel powder?
A: While very similar, there are slight differences. 8620 steel contains lower Chromium content compared to stainless steel, impacting its corrosion resistance. For highly corrosive environments, stainless steel powders might be a better choice.
Q: What are the advantages of using 8620 steel powder for 3D printing?
A: The key advantages include excellent strength, good toughness, good machinability, weldability, and a cost-effective price point.
Q: What are the limitations of using 8620 steel powder for 3D printing?
A: Moderate corrosion resistance and the need for post-processing heat treatment are the main drawbacks.
Q: How safe is 8620 steel powder for human contact?
A: The material itself is generally safe. However, proper handling protocols are crucial during the 3D printing process to minimize exposure to dust particles.
Q: What is the future of 8620 steel powder in additive manufacturing?
A: As 3D printing technology continues to evolve, ongoing research and development efforts might lead to improved powder characteristics, including higher corrosion resistance and even better mechanical properties.
Über 3DP mETAL
Produktkategorie
KONTAKT
Hast du Fragen? Schick uns jetzt eine Nachricht! Nach Eingang deiner Nachricht bearbeiten wir deine Anfrage im Team.