Binder jet 3D printing has emerged as a revolutionary technology, transforming the way we design and manufacture complex objects. At the heart of this process lies a critical component: Bindemittel Strahlpulver. These finely-grained materials act as the building blocks, meticulously layered and bonded together to create intricate 3D structures. But what exactly are binder jet powders, and what makes them so special? Delve into this comprehensive guide to explore the fascinating world of binder jet powders and unlock the potential for limitless 3D printing possibilities.
die Zusammensetzung und Eigenschaften von Bindemittel Jet-Pulver
Binder jet powders come in a diverse range, each offering unique properties tailored for specific applications. Here’s a breakdown of the key aspects to consider:
Immobilie | Beschreibung |
---|---|
Material Typ | The primary material that constitutes the powder particles. Common materials include metals, ceramics, sand, and even plastics. |
Partikelgröße und -verteilung | The size and uniformity of the powder particles significantly impact the resolution, surface finish, and overall quality of the printed object. Typically, finer particles achieve smoother finishes but may require specialized printing equipment. |
Dichte | The density of the powder influences the final weight and mechanical properties of the printed part. Denser powders generally result in sturdier objects. |
Fließfähigkeit | The powder’s ability to flow freely and spread evenly across the printing bed is crucial for consistent layer formation. Good flowability ensures smooth operation and minimizes printing defects. |
Sinterfähigkeit | For some materials, like metal powders, sinterability determines how well the particles bond together during a post-printing heat treatment process, impacting the final strength of the object. |
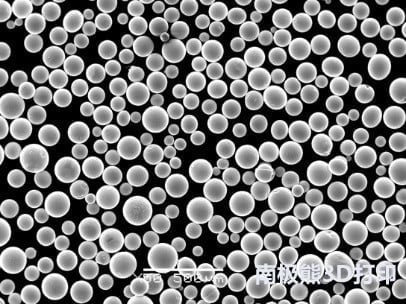
Popular Metal Binder Jet Powders
The realm of metal binder jet powders boasts a vast array of options, each catering to specific needs. Here’s a glimpse into ten prominent players in this arena:
- Rostfreier Stahl 316L: Renowned for its excellent corrosion resistance, this versatile powder is ideal for parts exposed to harsh environments, such as medical implants and marine components.
- Martensitaushärtender Stahl: Imagine a metal that combines exceptional strength with high ductility – that’s maraging steel. This powder is perfect for applications demanding both toughness and the ability to withstand deformation, like aerospace components and tooling.
- Inconel 625: For ventures into high-temperature territories, Inconel 625 reigns supreme. This nickel-chromium superalloy powder boasts superior heat resistance, making it a prime choice for jet engine parts and components exposed to extreme thermal conditions.
- Titan 6Al-4V: Lightweight yet remarkably strong, titanium 6Al-4V powder is a favorite in the aerospace and biomedical industries. Its biocompatibility makes it suitable for prosthetics and other medical implants.
- Kupfer: Imagine crafting intricate electrical components with the power of 3D printing. Copper powder offers exceptional thermal and electrical conductivity, ideal for heat sinks, electrical connectors, and even waveguides.
- Aluminium: For applications prioritizing weight savings and good machinability, aluminum powder shines. Think lightweight automotive parts, aerospace components, and even intricate heat exchangers.
- Tool Steel: Durability is the name of the game for tool steel powder. This option excels in creating robust tools and dies that can withstand high wear and tear, perfect for manufacturing applications.
- Kovar: Imagine a metal that seamlessly integrates with glass and ceramics – that’s Kovar. This iron-nickel-cobalt alloy powder boasts a thermal expansion coefficient that closely matches glass, making it ideal for electronic packaging applications.
- Nickel: For applications requiring high magnetic permeability, pure nickel powder takes center stage. Its magnetic properties make it suitable for electrical components like transformers and inductors.
- Biokompatible Legierungen: The medical field is embracing 3D printing in a big way, and biocompatible alloys are leading the charge. Powders like Ti-6Al-4V ELI (extra low interstitial) offer excellent biocompatibility for creating implants and prosthetics that seamlessly integrate with the human body.
Applications of Binder Jet Powders
Binder jet powders empower the creation of a diverse range of objects, transforming industries and igniting innovation. Let’s delve into some of the captivating applications that leverage the power of these versatile materials:
Metal Binder Jet Applications:
- Prototyping: Imagine crafting intricate prototypes rapidly and iteratively. Binder jetting excels at creating functional prototypes made from real metal, allowing designers and engineers to validate designs and functionalities before committing to full-scale production. The ability to use the same material as the final part in the prototype offers valuable insights into performance characteristics.
- End-use Parts: Beyond prototyping, binder jetting is increasingly used to manufacture production-ready metal parts. This technology is particularly well-suited for creating complex geometries that might be challenging or expensive to produce using traditional subtractive techniques like machining. Applications span across industries, including:
- Luft- und Raumfahrt: Lightweight and high-strength metal parts like brackets, housings, and even heat exchangers can be fabricated for aircraft and spacecraft.
- Automotive: Customizable components, intricate engine parts, and even lightweight structural components can be produced for automobiles.
- Medizin: Biocompatible metal powders like titanium pave the way for the creation of customized prosthetics, implants, and even surgical instruments.
- Werkzeuge: Binder jetting offers a cost-effective way to manufacture complex jigs, fixtures, and even molds. The ability to create intricate geometries with good surface finishes makes this technology a valuable tool for production processes.
The applications of binder jet powders extend far beyond the realm of metals. Here are some captivating examples:
- Keramiken: Binder jetting unlocks a new chapter in ceramic manufacturing. This technology enables the creation of intricate ceramic parts with complex geometries, previously difficult or impossible to achieve with traditional techniques. Applications include:
- Art and Design: Imagine crafting intricate sculptures, decorative elements, and even architectural components with the freedom of 3D printing.
- Functional Ceramics: Binder jetting paves the way for the creation of wear-resistant components like bushings, cutting tools, and even thermal insulators made from high-performance ceramic materials.
- Sand Casting Molds: Binder jetting finds its application beyond final parts. Sand, a cost-effective and readily available material, can be jetted to create intricate casting molds for metal parts. These 3D-printed sand molds offer several advantages over traditional methods, including:
- Geometric Complexity: Binder jetting allows for the creation of intricate mold geometries that might be challenging or expensive to produce using traditional techniques.
- Rapid Prototyping: Sand casting molds can be rapidly created using binder jetting, enabling faster design iterations and reduced lead times.
- Nachhaltigkeit: Binder jetting sand molds can be recycled and reused in some cases, minimizing waste compared to traditional sand casting methods.
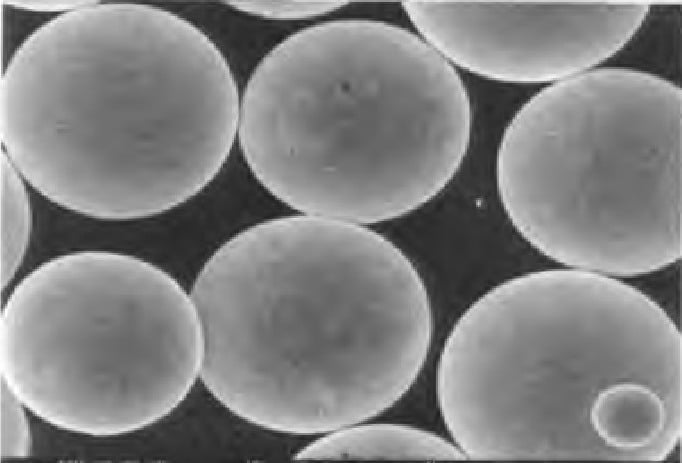
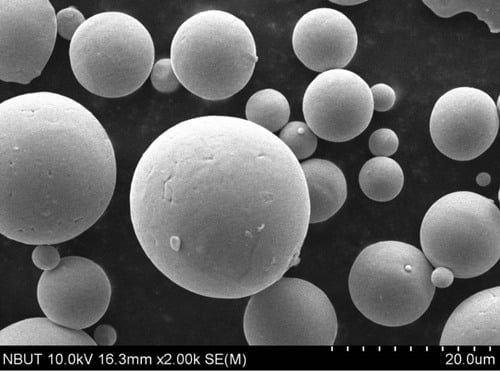
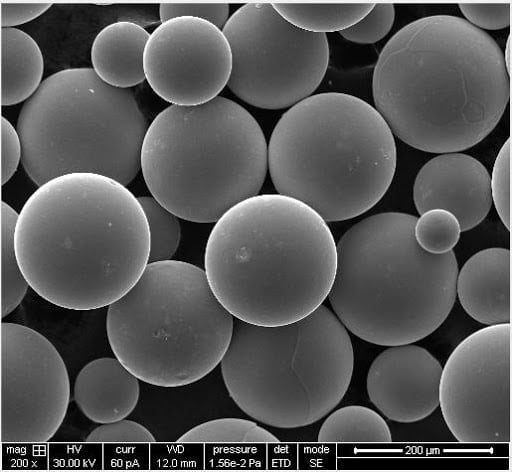
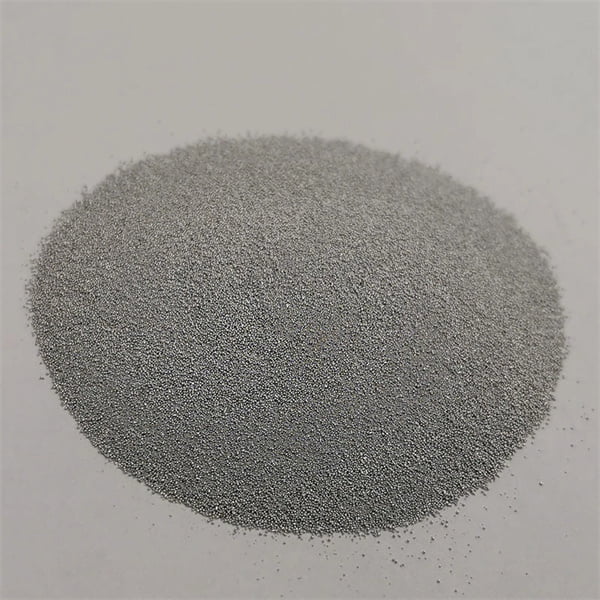
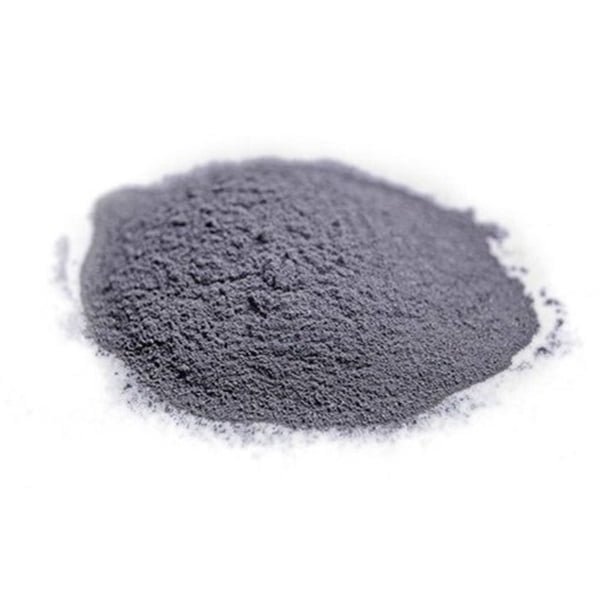
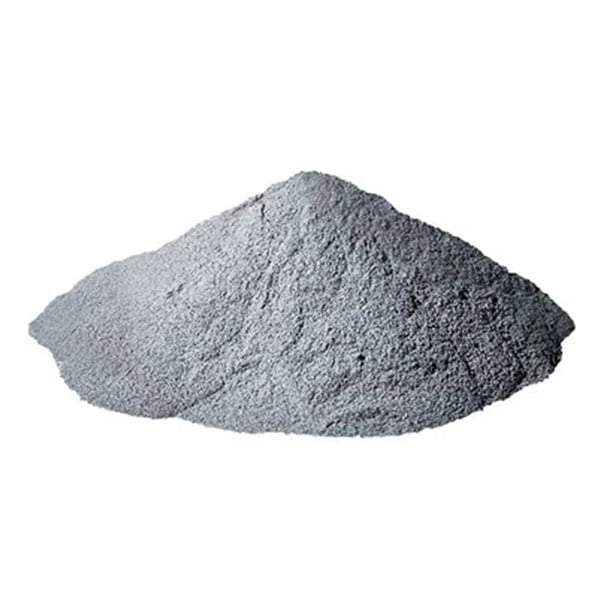
Vorteile und Beschränkungen von Bindemittel Jet-Pulver
Binder jet powders offer a compelling set of advantages that make them a valuable tool in the 3D printing landscape. However, it’s essential to consider the limitations as well to make informed decisions:
Vorteile:
- Gestaltungsfreiheit: Binder jetting allows for the creation of complex geometries that might be challenging or even impossible with traditional subtractive manufacturing techniques. This opens doors for innovative designs and functionalities.
- Vielseitigkeit der Materialien: A wide range of binder jet powders are available, catering to diverse applications. From metals and ceramics to sand, this technology offers the flexibility to work with various materials.
- Rapid Prototyping: Binder jetting excels at creating functional prototypes quickly and iteratively. This allows for faster design cycles and efficient product development.
- Kosten-Nutzen-Verhältnis: For certain applications, binder jetting can be a cost-effective way to manufacture complex parts compared to traditional techniques, especially when considering factors like reduced waste and design flexibility.
- Skalierbarkeit: Binder jet printing systems can accommodate a range of production volumes, from small-batch prototyping to larger-scale manufacturing.
Beschränkungen:
- Nachbereitung: Binder jet parts often require post-processing steps like infiltration (for metals) or sintering (for ceramics) to achieve their final properties. This can add time and complexity to the overall process.
- Materialeigenschaften: While material options are expanding, the mechanical properties of binder jet parts may not always match those of parts produced using traditional techniques like forging or machining.
- Oberfläche: Binder jet parts can exhibit a slightly rougher surface finish compared to some other 3D printing technologies like selective laser melting (SLM). However, post-processing techniques can improve the surface finish to some extent.
Selecting the Right Binder Jet Powder
Choosing the optimal binder jet powder hinges on several critical factors. Here’s a roadmap to navigate the selection process:
Auswahl der Materialien:
- Bewerbungsvoraussetzungen: The primary consideration is the intended use of the printed object. Mechanical properties, thermal performance, and weight are all crucial aspects to consider.
- Materialeigenschaften: Delve into the specific properties offered by different binder jet powders. For metals, factors like strength, ductility, and corrosion resistance come into play. For ceramics, thermal conductivity, wear resistance, and biocompatibility might be key considerations.
Eigenschaften des Pulvers:
- Partikelgröße und -verteilung: Particle size significantly impacts the resolution and surface finish of the printed object. Finer particles generally achieve smoother finishes but may require specialized printing equipment. A consistent particle size distribution ensures even flow and minimizes printing defects.
- Fließfähigkeit: The powder’s ability to flow freely and spread evenly across the printing bed is essential. Good flowability facilitates smooth operation and minimizes printing inconsistencies.
- Sinterability (for metals): This property determines how well the metal particles bond together during the post-printing heat treatment process. Higher sinterability generally leads to stronger final parts.
Zusätzliche Überlegungen:
- Nachbearbeitungsanforderungen: Different powders may necessitate varying post-processing steps, such as infiltration for metals or sintering for ceramics. Factor in the time and resources required for these additional steps.
- Availability and Cost: The availability and cost of different binder jet powders can vary depending on the material and supplier. While cost is a factor, prioritize material properties and suitability for your application.
- Auswirkungen auf die Umwelt: Consider the environmental impact of different powder materials and their associated post-processing needs.
Here’s a table summarizing some key specifications to consider when selecting binder jet powders:
Spezifikation | Beschreibung |
---|---|
Material Typ | Metal, Ceramic, Sand, etc. |
Teilchengrösse | Typically ranges from 10 to 150 microns |
Korngrößenverteilung | Measured by a statistical range (e.g., D10, D50) |
Dichte | Varies depending on the material |
Fließfähigkeit | Measured by a standardized test method |
Sinterability (for metals) | Measured by the degree of bonding achieved after heat treatment |
Nachbearbeitungsanforderungen | Infiltration (metals), Sintering (ceramics), etc. |
Verfügbarkeit | May vary depending on the material |
Kosten | Varies depending on the material and supplier |
Examples of Binder Jet Powder Specifications:
Material | Particle Size (microns) | Dichte (g/cm³) |
---|---|---|
Rostfreier Stahl 316L | 50-100 | 7.8 |
Martensitaushärtender Stahl | 45-90 | 8.0 |
Inconel 625 | 20-50 | 8.4 |
Titan 6Al-4V | 45-100 | 4.4 |
Alumina Ceramic | 15-30 | 3.7 |
Zirconia Ceramic | 30-60 | 6.0 |
Remember, these are just examples, and the specific specifications will vary depending on the powder material and supplier.
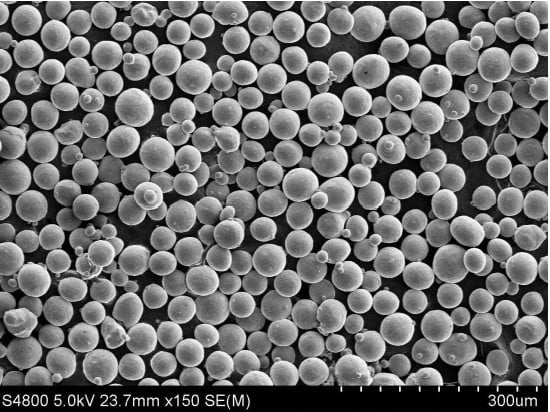
Supplier Landscape: Finding the Perfect Match
The landscape of binder jet powder suppliers is constantly evolving. Here are some key considerations when searching for a reliable source:
- Sachkenntnis: Look for suppliers with a strong understanding of the specific Bindemittel Strahlpulver you require. They should be able to provide technical guidance and support.
- Qualitätskontrolle: Ensure the supplier adheres to strict quality control procedures to guarantee consistent powder properties and minimize printing defects.
- Preisgestaltung und Verfügbarkeit: Compare pricing and lead times from different suppliers to find the best fit for your needs.
- Technische Unterstützung: Seek a supplier that offers technical support to assist you with any challenges you encounter during the selection or printing process.
Here’s a table listing some prominent binder jet powder suppliers:
Anbieter | Website | Angebotene Materialien |
---|---|---|
ExOne | https://www.exone.com/ | Metals, Ceramics |
Höganäs | https://www.hoganas.com/en/ | Metalle |
Schreibtisch Metall | https://www.desktopmetal.com/ | Metalle |
AMProto | https://www.amprogo.com/shop-tour | Metals, Ceramics |
The Materialise Group | https://www.materialise.com/en | Metalle |
FAQ
Binder jet powders open a world of possibilities in 3D printing. To shed light on some common questions, here’s a helpful FAQ section:
Q: What are the advantages of using binder jet powders compared to other 3D printing technologies?
A: Binder jetting offers several advantages, including:
- Gestaltungsfreiheit: It allows for the creation of complex geometries that might be challenging or impossible with traditional techniques.
- Vielseitigkeit der Materialien: A wide range of powders are available, catering to diverse applications.
- Rapid Prototyping: Binder jetting excels at creating functional prototypes quickly.
- Kosten-Nutzen-Verhältnis: In some cases, it can be a cost-effective way to manufacture complex parts.
- Skalierbarkeit: Binder jetting systems can accommodate various production volumes.
Q: What are the limitations of binder jet powders?
A: Some limitations to consider include:
- Nachbereitung: Binder jet parts often require additional steps like infiltration or sintering.
- Materialeigenschaften: Mechanical properties may not always match those of traditionally produced parts.
- Oberfläche: The surface finish might be slightly rougher compared to some other 3D printing methods.
Q: How safe is it to handle binder jet powders?
A: Safety precautions are crucial when working with binder jet powders. Some metal and ceramic powders can be hazardous if inhaled or ingested. Always follow the manufacturer’s safety data sheets (SDS) and wear appropriate personal protective equipment (PPE) when handling powders.
Q: What is the future outlook for binder jet powder technology?
A: The future of binder jet powders is bright. Here are some exciting trends to watch:
- Development of new materials: Researchers are continuously exploring new materials for binder jetting, expanding its application possibilities.
- Improved post-processing techniques: Advancements in post-processing methods could lead to enhanced mechanical properties and surface finishes for binder jet parts.
- Increased affordability: As the technology matures, binder jetting systems and materials are expected to become more cost-effective, making it even more accessible.
Q: Where can I find more information about binder jet powders?
A: Several resources offer valuable information:
- 3D Printing Industry Websites: Many websites dedicated to 3D printing provide in-depth articles and resources on binder jetting.
- Hersteller-Websites: Reputable binder jet powder suppliers often provide detailed information about their products and applications on their websites.
- Academic Research Papers: Research papers and studies delve deeper into the technical aspects of binder jet powders and their properties.
By understanding the intricacies of binder jet powders, you can unlock the potential of this transformative 3D printing technology. With its versatility, design freedom, and ever-evolving capabilities, binder jetting is poised to revolutionize the way we design and manufacture objects across diverse industries.
Über 3DP mETAL
Produktkategorie
KONTAKT
Hast du Fragen? Schick uns jetzt eine Nachricht! Nach Eingang deiner Nachricht bearbeiten wir deine Anfrage im Team.