Haben Sie jemals davon geträumt, etwas Schicht für Schicht aufzubauen, mit geschmolzenem Metall als Farbe und einem Roboterarm als Pinsel? Nun, Gerichtete Energieabscheidung (DED) macht diese Science-Fiction zur Realität. DED ist ein revolutionäres 3D-Druckverfahren, das die Fertigung verändert und es uns ermöglicht, komplexe Metallstrukturen mit unübertroffener Präzision und Flexibilität herzustellen.
Dieser Artikel taucht in die faszinierende Welt des DED ein und untersucht seine Grundprinzipien, die Vorteile, die es gegenüber herkömmlichen Methoden bietet, und die vielfältigen Anwendungen, die es in verschiedenen Branchen findet.
Das Grundprinzip der gerichteten Energieabscheidung (DED)
Stellen Sie sich einen leistungsstarken Laserstrahl vor, wie eine aufgeladene Version eines Laserpointers, der auf einen bestimmten Punkt fokussiert ist. Nun stellen Sie sich einen Metalldraht oder ein Metallpulver vor, das kontinuierlich durch eine Düse direkt neben dem Laserstrahl geführt wird. Wenn der Laserstrahl auf das Metall trifft, schmilzt er es sofort. Das geschmolzene Metall wird dann nach einem digitalen Plan Schicht für Schicht auf eine Plattform aufgetragen. Während jede Schicht schnell erstarrt, nimmt die gewünschte 3D-Struktur Gestalt an.
Im Folgenden finden Sie eine Aufschlüsselung der wichtigsten Komponenten des DED:
- Energiequelle: Laser, Elektronenstrahlen und Plasmabögen sind die am häufigsten verwendeten Energiequellen bei der DED. Jede von ihnen bietet einzigartige Vorteile und Überlegungen, je nach dem gewünschten Material und der Anwendung.
- Ausgangsstoff Material: DED kann eine Vielzahl von Metalllegierungen verarbeiten, darunter Titan, Stahl, Aluminium und Nickelsuperlegierungen. Die Wahl des Materials hängt von den gewünschten Eigenschaften des Endprodukts ab, wie Festigkeit, Gewicht und Korrosionsbeständigkeit.
- Lieferungssystem: Die Düse spielt eine entscheidende Rolle, da sie das Ausgangsmaterial in den Weg der Energiequelle führt und eine präzise Abscheidung gewährleistet.
- Computersteuerung: Der gesamte DED-Prozess wird von einer Computersoftware genauestens gesteuert. Diese Software übersetzt die 3D-Konstruktionsdatei in eine Reihe von Anweisungen, die die Bewegung des Roboterarms, die Leistung der Energiequelle und die Durchflussmenge des Rohmaterials vorgeben.
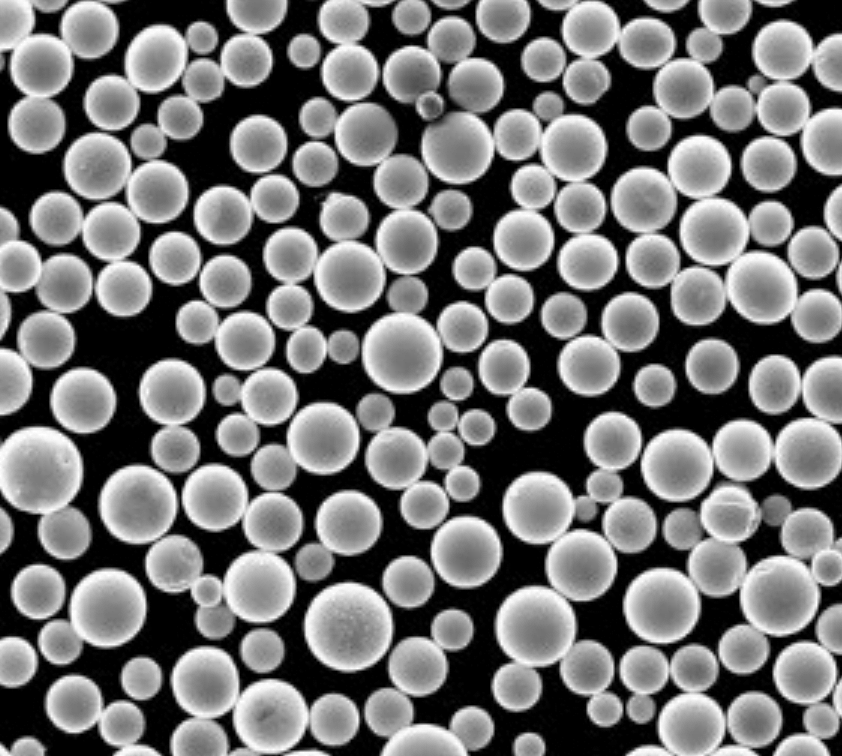
Vorteile der gerichteten Energieabscheidung (DED)
DED bietet eine Reihe überzeugender Vorteile im Vergleich zu herkömmlichen Fertigungsverfahren wie Zerspanung und Gießen. Lassen Sie uns einige der wichtigsten Vorteile erkunden:
- Gestaltungsfreiheit: Im Gegensatz zu subtraktiven Verfahren wie der zerspanenden Bearbeitung ist das DED ein additives Verfahren. Das bedeutet, dass Sie nicht durch die ursprüngliche Form eines Rohmaterialblocks eingeschränkt sind. Mit DED lassen sich komplexe Geometrien mit inneren Merkmalen und komplizierten Details herstellen, die mit herkömmlichen Verfahren unmöglich oder sehr teuer wären.
- Materialeffizienz: DED zeichnet sich durch eine außergewöhnliche Materialeffizienz aus. Dank der präzisen Abscheidung gibt es nur minimalen Abfall im Vergleich zu subtraktiven Verfahren, bei denen viel Metallschrott anfällt. Dies führt zu Kosteneinsparungen und einem umweltfreundlicheren Verfahren.
- Leichte Strukturen: DED zeichnet sich durch die Herstellung leichter und dennoch stabiler Strukturen aus. Durch die strategische Gestaltung hohler innerer Merkmale können DED-Teile ein außergewöhnliches Verhältnis von Festigkeit zu Gewicht erreichen, was sie ideal für Anwendungen wie Luft- und Raumfahrt und Transport macht.
- Rapid Prototyping: DED ermöglicht die schnelle Erstellung von Funktionsprototypen direkt aus digitalen Modellen. Dies macht langwierige Werkzeugprozesse überflüssig und beschleunigt den Design- und Entwicklungszyklus.
- Near-Net-Shape Manufacturing: Mit dem DED-Verfahren können Teile sehr nahe an ihren endgültigen Abmessungen hergestellt werden, so dass sich umfangreiche Nachbearbeitungsschritte wie die spanende Bearbeitung erübrigen. Dies führt zu kürzeren Produktionszeiten und niedrigeren Gesamtkosten.
- Reparatur und Restaurierung: Die Fähigkeit des DED, Material präzise abzuscheiden, macht es ideal für die Reparatur beschädigter Metallkomponenten. Dadurch wird die Lebensdauer bestehender Anlagen verlängert und die Notwendigkeit eines kompletten Austauschs verringert.
Anwendungen der gerichteten Energieabscheidung (DED)
Die Vielseitigkeit von DED ist wirklich bemerkenswert. Hier ein kleiner Einblick in einige der spannenden Anwendungen in verschiedenen Branchen:
- Luft- und Raumfahrt: DED wird eingesetzt, um leichte und hochfeste Komponenten für Flugzeuge herzustellen, z. B. Halterungen, Flügelrippen und Triebwerksteile. Diese Technologie trägt zur Optimierung der Treibstoffeffizienz und Leistung in der Luft- und Raumfahrtindustrie bei.
- Automotive: DED findet Anwendung bei der Herstellung maßgeschneiderter Teile für Rennfahrzeuge und bei der Reparatur beschädigter Komponenten in Hochleistungsfahrzeugen.
- Medizin: DED revolutioniert den medizinischen Bereich, indem es die Herstellung von maßgeschneiderten Prothesen und Implantaten ermöglicht, die perfekt auf den einzelnen Patienten zugeschnitten sind.
- Öl und Gas: DED wird für die Reparatur und Verkleidung kritischer Komponenten in der Öl- und Gasindustrie eingesetzt, um deren Lebensdauer zu verlängern und ihre Widerstandsfähigkeit gegenüber rauen Umgebungsbedingungen zu erhöhen.
- Werkzeuge: DED kann zur Herstellung komplexer Formen und Gesenke mit konformen Kühlkanälen verwendet werden, was die Effizienz und Produktionsgeschwindigkeit in verschiedenen Fertigungsprozessen verbessert.
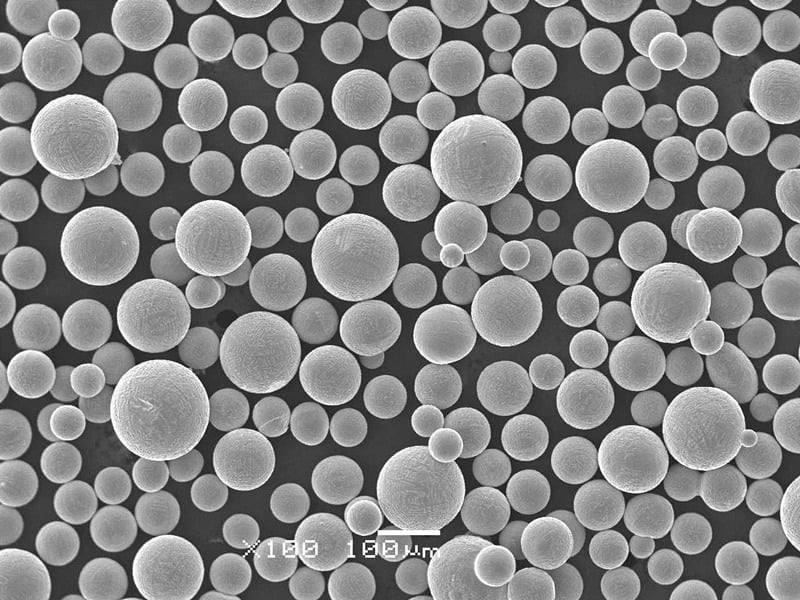
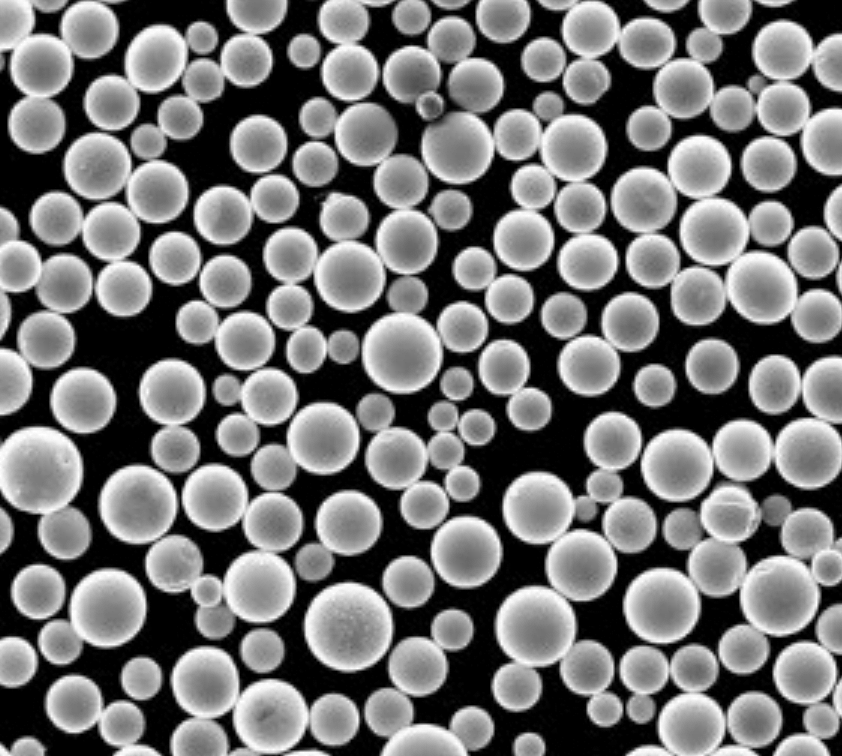
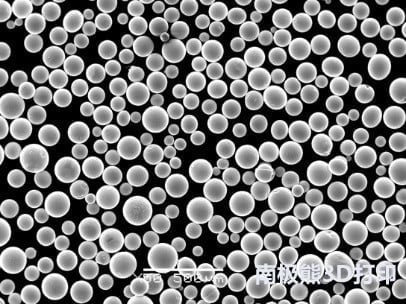
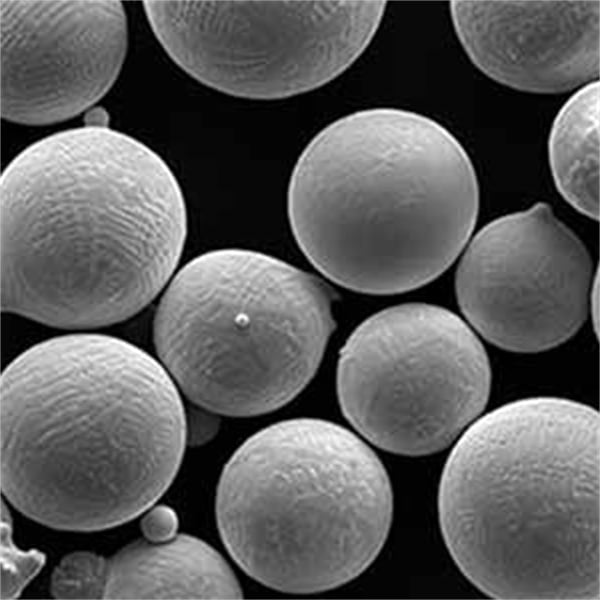
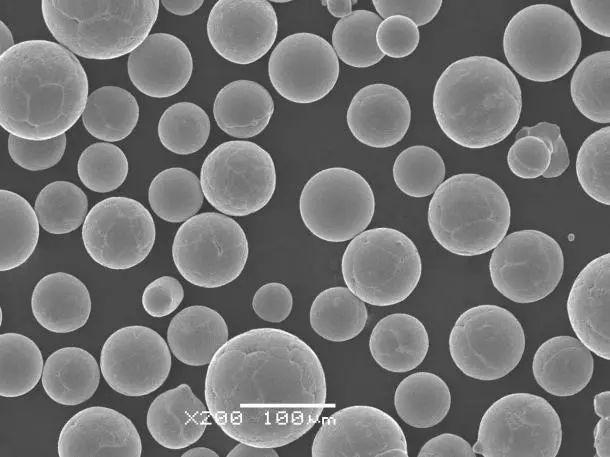
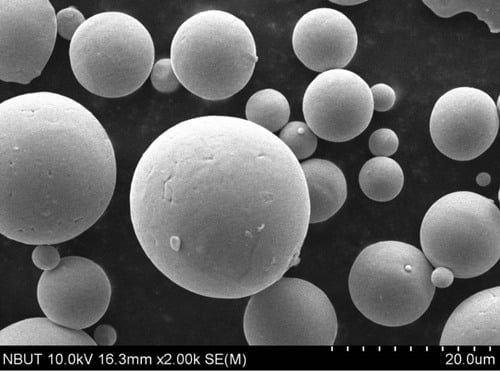
Überlegungen zum DED
DED bietet zwar zahlreiche Vorteile, aber es ist wichtig, einige Schlüsselfaktoren zu berücksichtigen, bevor man sich mit dieser Technologie beschäftigt.
Kosten: DED-Maschinen können im Vergleich zu herkömmlichen Fertigungsanlagen teuer sein. Die Kosteneinsparungen bei der Materialeffizienz, der Designfreiheit und der reduzierten Nachbearbeitung können jedoch dazu führen, dass DED langfristig eine überzeugende Wahl ist, insbesondere für hochwertige, komplexe Teile.
Materialeigenschaften und Überlegungen zum DED
Die Fähigkeit des DED, eine breite Palette von Metallen zu bearbeiten, ist ein wesentlicher Vorteil. Es ist jedoch wichtig zu verstehen, wie das DED-Verfahren die Materialeigenschaften des Endprodukts im Vergleich zu herkömmlichen Verfahren beeinflussen kann. Hier sind einige wichtige Überlegungen:
- Struktur der Körner: Das schnelle Schmelzen und Erstarren des Metalls beim DED kann im Vergleich zu gegossenen oder gekneteten Metallen zu einer feineren Kornstruktur führen. Dieses feinere Korngefüge kann die mechanischen Eigenschaften wie Festigkeit und Duktilität des DED-Teils verbessern. Es kann jedoch auch dazu führen, dass das Material bei bestimmten Anwendungen anfälliger für Spannungsrisse ist.
- Eigenspannung: Das DED-Verfahren beinhaltet eine örtliche Erwärmung und Abkühlung, die zu Eigenspannungen im Bauteil führen kann. Unkontrollierte Eigenspannungen können zu Verzug und Verformung führen. Bei DED-Verfahren werden häufig Wärmebehandlungen nach der Abscheidung durchgeführt, um Eigenspannungen zu kontrollieren und die endgültigen Eigenschaften des Teils zu optimieren.
- Oberfläche: Die Oberflächengüte eines DED-Teils hängt von mehreren Faktoren ab, u. a. von der Energiequelle, dem Ausgangsmaterial und den Abscheidungsparametern. DED-Teile können im Vergleich zu maschinell bearbeiteten Teilen eine etwas rauere Oberfläche aufweisen. Durch Nachbearbeitungstechniken wie Zerspanen oder Polieren kann jedoch eine glattere Oberfläche erzielt werden, wenn dies für die Anwendung erforderlich ist.
Verschiedene DED-Techniken und ihre Anwendungen
Während das Grundprinzip des DED gleich bleibt, gibt es je nach verwendeter Energiequelle verschiedene Varianten der Technologie. Hier eine Übersicht über die drei wichtigsten DED-Techniken:
- Laser-DED (L-DED):
- Verwendet einen leistungsstarken Laserstrahl als Energiequelle.
- Bietet hervorragende Kontrolle und Präzision und eignet sich daher für die Erstellung komplizierter Geometrien und Merkmale.
- Gut geeignet für Anwendungen, die eine hohe Oberflächengüte erfordern, wie z. B. medizinische Implantate und Komponenten für die Luft- und Raumfahrt.
- Im Vergleich zu anderen DED-Verfahren kann die Abscheiderate bei L-DED begrenzt sein, so dass es sich nicht unbedingt für großflächige Anwendungen eignet.
- Elektronenstrahl-DED (EB-DED):
- Setzt einen fokussierten Elektronenstrahl in einer Vakuumkammer zum Schmelzen des Ausgangsmaterials ein.
- Bietet im Vergleich zu L-DED eine tiefere Penetration und höhere Ablagerungsraten.
- Damit ist EB-DED eine gute Wahl für die Herstellung von dickwandigen Strukturen und die Reparatur von großen Bauteilen.
- Die erforderliche Vakuumkammer erhöht jedoch die Komplexität und die Kosten des EB-DED-Verfahrens.
- Plasma Arc DED (PA-DED):
- Verwendet einen Hochtemperatur-Plasmalichtbogen als Energiequelle.
- Bietet die schnellsten Abscheidungsraten unter den DED-Verfahren und eignet sich daher für Anwendungen im großen Maßstab und mit hohem Durchsatz.
- PA-DED kann im Vergleich zu L-DED und EB-DED auch ein breiteres Spektrum an metallischen Rohstoffen verarbeiten.
- Allerdings kann PA-DED im Vergleich zu anderen DED-Verfahren eine breitere Wärmezone aufweisen, was zu einer raueren Oberfläche und einer potenziell größeren Korngröße im abgeschiedenen Material führt.
Die Zukunft der gerichteten Energieabscheidung
DED ist eine noch relativ junge Technologie mit einem immensen Potenzial für Wachstum und Innovation. Hier sind einige spannende Trends, die die Zukunft des DED prägen:
- Multi-Material DED: Die Forscher erforschen Möglichkeiten, verschiedene DED-Verfahren zu kombinieren oder sogar DED mit anderen additiven Fertigungsverfahren zu integrieren, um Multimaterialteile mit maßgeschneiderten Eigenschaften in verschiedenen Bereichen herzustellen. Man stelle sich ein leichtes Bauteil für die Luft- und Raumfahrt mit einem hochfesten Kern und einer korrosionsbeständigen Außenschicht vor - alles in einem einzigen DED-Verfahren hergestellt.
- Hybride DED-Verfahren: Die Integration von DED mit In-situ-Bearbeitungs- oder Überwachungstechnologien ist sehr vielversprechend. Prozesssteuerung in Echtzeit und adaptive Fertigungsmöglichkeiten würden es dem DED ermöglichen, qualitativ hochwertige Teile mit noch größerer Präzision und Effizienz herzustellen.
- Standardisierung und Qualifizierung: Mit der zunehmenden Verbreitung von DED wird die Einführung standardisierter Prozesse und Qualifizierungsverfahren entscheidend sein. Dies wird die Zuverlässigkeit und Wiederholbarkeit von DED-Teilen für kritische Anwendungen in Branchen wie der Luft- und Raumfahrt und der Medizintechnik gewährleisten.
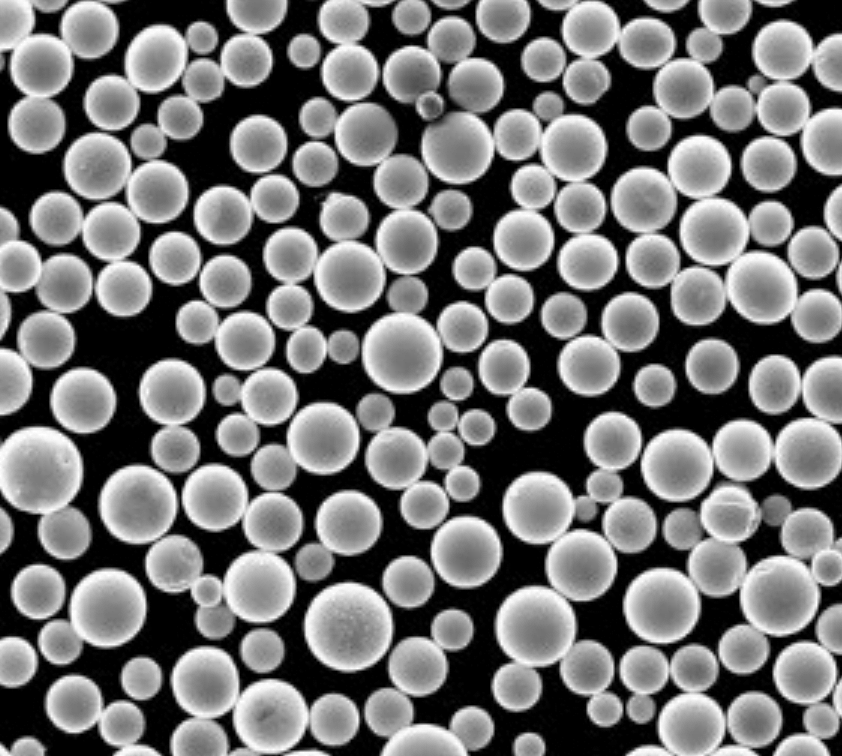
FAQ
Frage | Antwort |
---|---|
Was sind die Vorteile von DED gegenüber herkömmlichen Fertigungsmethoden? | DED bietet Designfreiheit, Materialeffizienz, die Möglichkeit, leichte Strukturen zu schaffen, schnelles Prototyping, endkonturnahe Fertigung und Reparaturmöglichkeiten. |
Was sind einige der Anwendungen des DED? | DED wird in der Luft- und Raumfahrt, im Automobilbau, in der Medizintechnik, in der Öl- und Gasindustrie sowie im Werkzeugbau eingesetzt. |
Welche Faktoren sind bei der Anwendung des DED zu beachten? | Kosten, Materialeigenschaften (Kornstruktur, Eigenspannungen, Oberflächengüte) und die Wahl der DED-Technik (Laser, Elektronenstrahl, Plasmabogen) sind wichtige Faktoren. |
Über 3DP mETAL
Produktkategorie
KONTAKT
Hast du Fragen? Schick uns jetzt eine Nachricht! Nach Eingang deiner Nachricht bearbeiten wir deine Anfrage im Team.