Imagine a machine that can take a scorching hot stream of molten metal and, in a split second, turn it into a cloud of ultra-fine powder. That’s the magic of gas atomization equipment, a marvel of industrial engineering that plays a crucial role in various cutting-edge applications.
In this comprehensive guide, we’ll delve deep into the world of gas atomization equipment. We’ll explore its inner workings, understand its advantages and limitations, and uncover the exciting possibilities it unlocks in various industries. So, buckle up and get ready to dive into the fascinating world of metal miniaturization!
The Basic Principle of Gas Atomization Equipment
At its core, gas atomization equipment operates on a deceptively simple principle. Here’s a breakdown of the process:
- Das Schmelzen des Metalls: The first step involves melting the target metal using a high-powered furnace. This furnace can be an induction furnace, a plasma torch, or an electron beam melter, depending on the specific metal and the desired properties of the final powder.
- Zerstäubung: The molten metal is then forced through a tiny nozzle at high pressure. Imagine squeezing toothpaste out of a tube, but with a molten metal that’s thousands of degrees hot!
- Gas Meets Metal: As the molten metal exits the nozzle, a high-velocity stream of inert gas (usually argon or nitrogen) collides with the metal stream. This forceful impact breaks the molten metal into tiny droplets, which rapidly solidify into fine metal powder particles.
- Powder Collection: The newly formed metal powder is carried away by the gas stream and separated using a cyclone separator or a filter system.
The size and morphology (shape) of the final powder particles can be controlled by various factors, including the pressure of the gas stream, the size of the nozzle, and the properties of the molten metal itself.
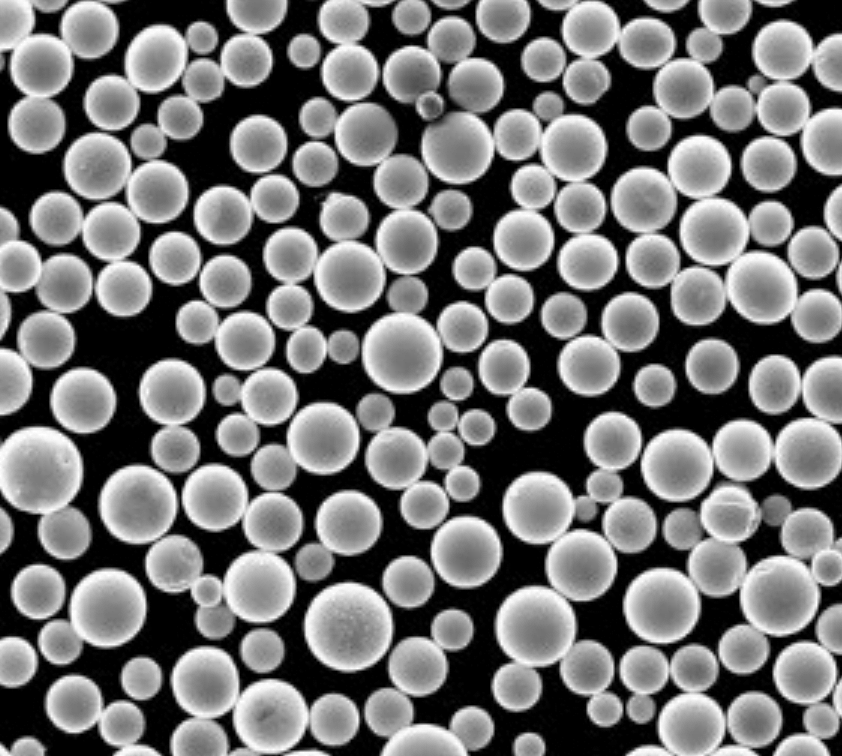
Advantages of Gas Atomization Equipment
Gas atomization equipment offers several distinct advantages over other metal powder production methods like water atomization:
- Highly Spherical Powders: Gas atomization produces near-perfectly spherical metal powders. This is crucial for many applications, such as additive manufacturing (3D printing) where uniform powder flow is essential.
- Feinere Pulver: Compared to water atomization, gas atomization can generate much finer metal powders. This allows for the creation of new materials with unique properties and opens doors for applications in areas like electronics and aerospace.
- Reduced Oxygen Content: The use of inert gas during atomization minimizes the amount of oxygen trapped within the powder particles. This is essential for metals that are susceptible to oxidation, as even small amounts of oxygen can significantly alter their properties.
- Greater Control: Gas atomization offers a high degree of control over the powder’s characteristics, such as size, shape, and even internal microstructure. This allows manufacturers to tailor the powder to meet the specific needs of their application.
The Power of Spherical Powders in 3D Printing
Imagine building a complex metal object layer by layer using a 3D printer. Here, the consistency and flow of the metal powder become paramount. Spherical powders produced by gas atomization flow freely within the 3D printer, ensuring smooth layer formation and ultimately leading to a strong and structurally sound final product.
Disadvantages of Gas Atomization Equipment
While gas atomization offers numerous advantages, it also comes with some limitations:
- Höhere Kosten: Gas atomization equipment is generally more expensive than water atomization equipment. The high-pressure systems, the need for inert gas, and the precise control mechanisms all contribute to the higher cost.
- Lower Production Rates: Compared to water atomization, gas atomization typically produces powder at a slower rate. This can be a disadvantage for applications that require large volumes of metal powder.
- Materielle Beschränkungen: Not all metals are suitable for gas atomization. Highly reactive metals can pose challenges due to their tendency to oxidize rapidly.
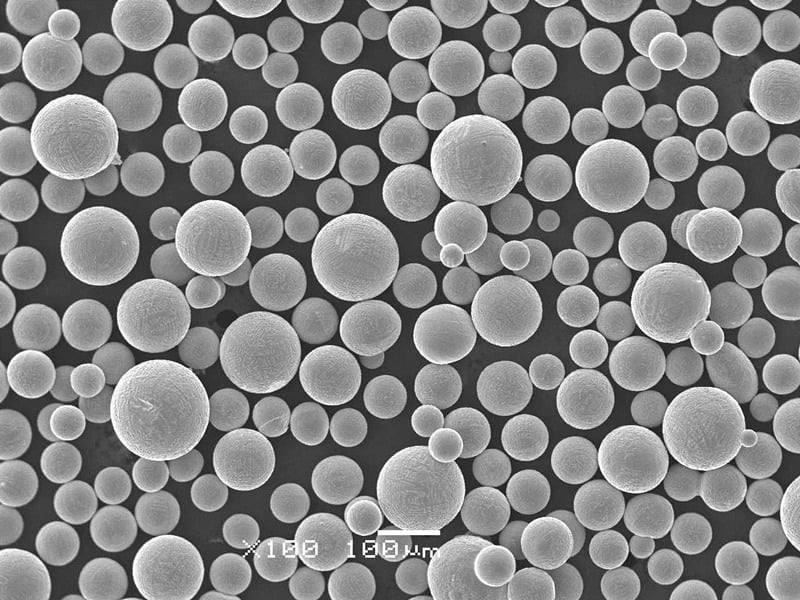
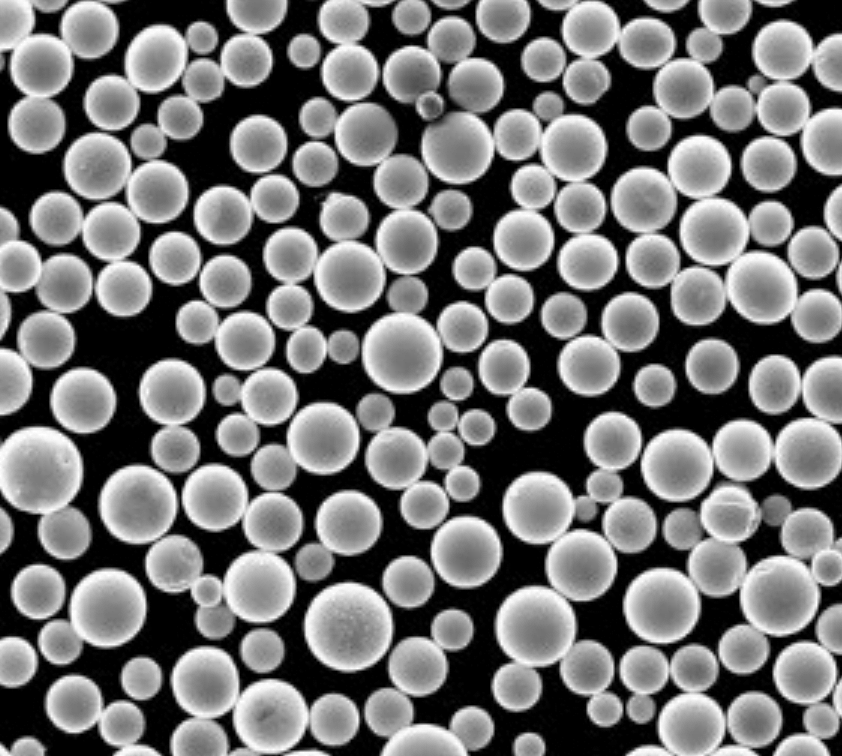
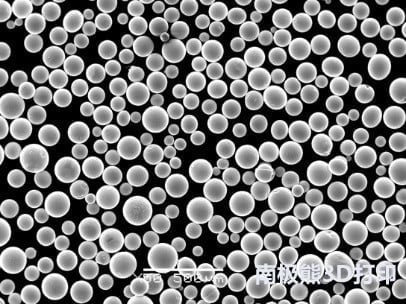
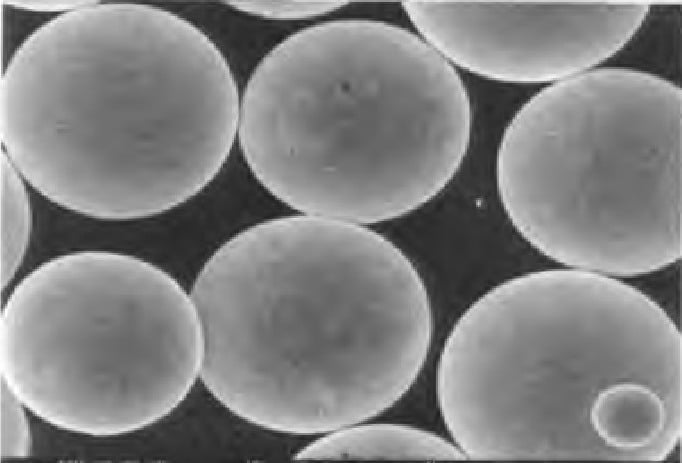
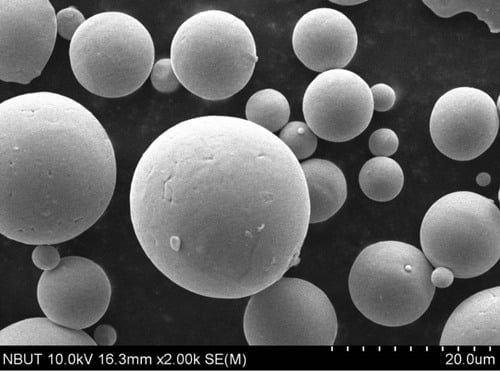
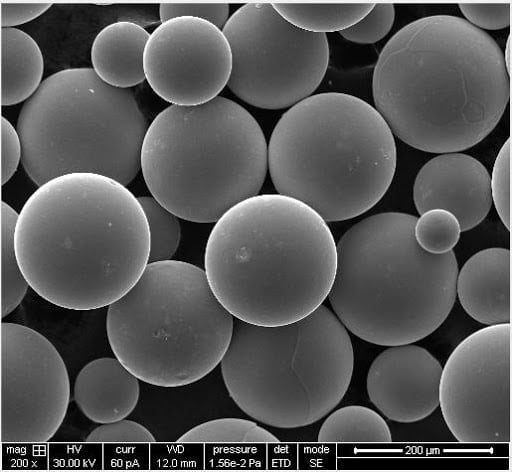
Key Considerations When Choosing Gas Atomization Equipment
Selecting the right gas atomization equipment requires careful consideration of several factors:
- Desired Powder Characteristics: The size, shape, and other properties of the final powder will dictate the specific equipment configuration needed.
- Metall-Typ: The type of metal being processed will influence factors like furnace selection and the choice of inert gas.
- Produktionsvolumen: The anticipated production volume will determine the size and capacity of the gas atomization system required.
- Haushalt: Gas atomization equipment can be a significant investment. It’s crucial to evaluate your budget and choose a system that offers the desired capabilities while remaining cost-effective.
Applications of Gas Atomization Equipment: From Jet Engines to Artificial Limbs
Gas atomized metal powders find their way into a surprisingly wide range of applications across various industries. Let’s explore some of the most prominent examples:
1. Additive Manufacturing (3D Printing):
As mentioned earlier, gas-atomized powders are a game-changer in the world of 3D printing. Their near-perfect spherical shapes and consistent flow characteristics make them ideal for building complex metal objects layer by layer. From intricate aerospace components to customized medical implants, gas-atomized powders are pushing the boundaries of what’s possible with 3D printing.
2. Metal Injection Molding (MIM):
Metal injection molding (MIM) is a versatile manufacturing process that utilizes metal powders to create complex near-net-shape parts. Gas-atomized powders, with their excellent flowability and packing density, are particularly well-suited for MIM. They enable the creation of intricate metal components with high precision and dimensional accuracy, making them ideal for applications in electronics, automotive, and medical industries.
3. Advanced Alloys and Composites:
Gas atomization allows for the production of unique metal powders that can be used to create novel alloys and composites. By precisely controlling the size, shape, and composition of the powder particles, engineers can tailor the properties of the final material to meet specific requirements. This opens doors for the development of lighter, stronger, and more heat-resistant materials for applications in aerospace, defense, and transportation.
4. Thermal Spray Coatings:
Thermal spraying is a technique used to coat surfaces with a layer of metal for improved properties like wear resistance, corrosion protection, or thermal insulation. Gas-atomized powders are often the preferred choice for thermal spraying due to their excellent flow characteristics and ability to form dense, well-bonded coatings. This technology is used to protect everything from jet engine turbine blades to oil drilling equipment.
5. Biomedical Applications:
The medical field is increasingly utilizing gas-atomized powders for various applications. For instance, these powders are used to create biocompatible materials for orthopedic implants like artificial knees and hips. The controlled porosity of gas-atomized powders allows for bone ingrowth, promoting better osseointegration (bonding with bone) of the implant.
Beyond these prominent applications, gas-atomized powders are also making their mark in areas like:
- Electronic components: Used to create miniaturized electronic components with high conductivity.
- Catalytic converters: Employed to create catalysts with high surface area for improved emission control.
- Friction materials: Used to manufacture brake pads and clutches with enhanced wear resistance.
The possibilities with gas-atomized powders are constantly expanding, making them a vital tool for innovation across diverse industries.
Challenges and Future Outlook of Gas Atomization Equipment
Despite its numerous advantages, gas atomization equipment faces some ongoing challenges:
- Energieverbrauch: The process requires significant energy to melt the metal and maintain the high-pressure gas stream. Optimizing energy efficiency remains an ongoing area of research.
- Auswirkungen auf die Umwelt: Inert gas production and the potential for metal dust emissions necessitate careful environmental considerations. Sustainable practices and closed-loop systems are being explored to minimize the environmental footprint.
- Kostenreduzierung: Bringing down the cost of gas atomization equipment and processes would make this technology more accessible to a wider range of manufacturers. Advancements in automation and material selection hold promise for future cost reductions.
The Future is Bright for Gas Atomization
Looking ahead, the future of gas atomization equipment appears bright. With continuous advancements in technology, materials science, and process optimization, we can expect to see:
- Development of more energy-efficient systems: Minimizing energy consumption will not only reduce operational costs but also contribute to a more sustainable future.
- Exploration of alternative gas sources: Research into utilizing recycled or renewable inert gases could further enhance the environmental sustainability of the process.
- Production of even finer and more complex powders: This will open doors for even more advanced applications, particularly in areas like nanotechnology and bioprinting.
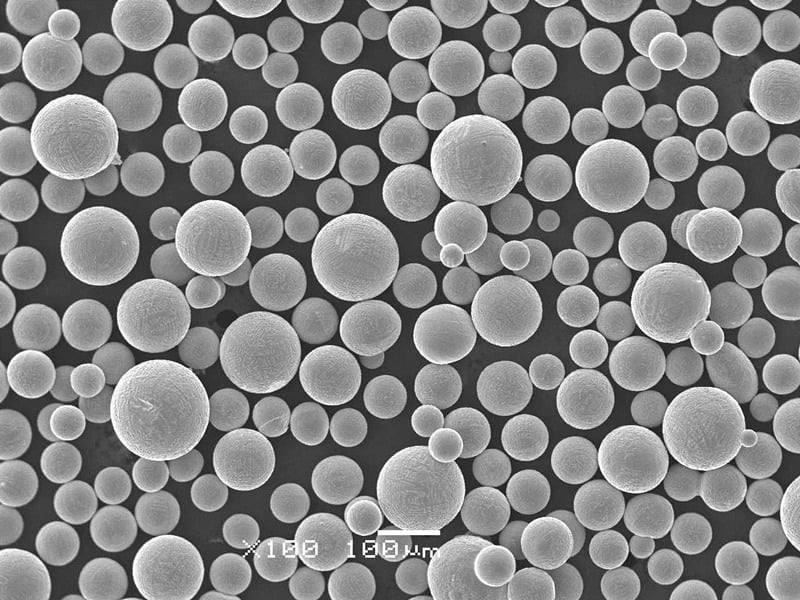
FAQ
Table 1: Frequently Asked Questions on Gas Atomization Equipment
Frage | Antwort |
---|---|
What are some alternatives to gas atomization? | Water atomization is a more cost-effective option, but it produces less spherical and coarser powders. Other methods include centrifugal atomization and electrode induction atomization. |
Can gas atomization be used for all metals? | No, highly reactive metals like lithium or sodium can be challenging due to their rapid oxidation. |
How safe is gas atomization equipment? | Modern gas atomization systems prioritize safety through features like explosion-proof enclosures and proper ventilation systems. |
What are the maintenance requirements for gas atomization equipment? | Regular maintenance is crucial to ensure optimal performance and safety. This includes cleaning the system, inspecting critical components |
Über 3DP mETAL
Produktkategorie
KONTAKT
Hast du Fragen? Schick uns jetzt eine Nachricht! Nach Eingang deiner Nachricht bearbeiten wir deine Anfrage im Team.