Inconel 625-Pulver –– the name might sound like something out of a superhero movie, but this wonder material is no fictional creation. It’s a real-life champion in the world of metal powders, boasting an impressive combination of strength, heat resistance, and corrosion defiance.
This article delves into the fascinating world of Inconel 625 powder, unraveling its characteristics, production process, applications, and even addressing some frequently asked questions. So, buckle up and get ready to discover the potential of this metallic marvel!
Characteristics of Inconel 625 Powder
Imagine a metal dust so tough, it can shrug off scorching temperatures, relentless wear and tear, and even the corrosive bite of harsh chemicals. That’s the essence of Inconel 625 powder. Here’s a closer look at its key characteristics:
- Super Alloy Strength: At its core, Inconel 625 powder is a nickel-based superalloy. This translates to exceptional tensile strength, meaning it can withstand immense pulling forces without breaking. Think of it like a tiny metal rope that can hold a staggering amount of weight.
- High-Temperature Hero: Unlike most metals that go soft and weak in the face of extreme heat, Inconel 625 powder thrives in such environments. It maintains its strength and structural integrity even at scorching temperatures exceeding 1500°F (815°C). Imagine using this powder to create parts for jet engines or industrial furnaces –– the intense heat wouldn’t stand a chance!
- Corrosion Conqueror: Imagine tossing a regular metal component into a vat of acid –– it wouldn’t last long. But Inconel 625 powder possesses phenomenal resistance to a wide range of corrosive environments, including harsh acids, alkalis, and even seawater. This makes it ideal for applications where constant exposure to corrosive elements is a concern, like in chemical processing plants or marine equipment.
- Tailor-Made for 3D Printing: The magic of Inconel 625 powder lies in its perfect marriage of exceptional properties and 3D printing compatibility. Its fine, spherical particles are ideal for additive manufacturing processes like Selective Laser Melting (SLM) or Electron Beam Melting (EBM).
These characteristics, combined, make Inconel 625-Pulver a highly sought-after material for creating high-performance components in various demanding industries.
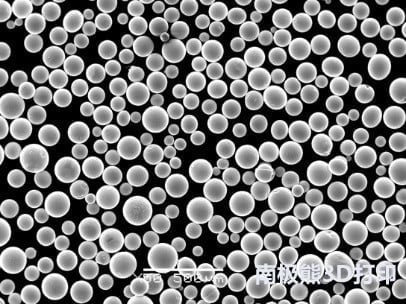
The Production Process of Inconel 625 Powder
So, how exactly does this superhero powder come to life? The production process of Inconel 625 powder involves several meticulous steps:
- Raw Material Selection: The journey begins with carefully chosen raw materials like nickel, chromium, molybdenum, and niobium. Just like baking a delicious cake, using the right ingredients is crucial for achieving the desired properties in the final product.
- Melting and Alloying: The chosen raw materials are precisely weighed and melted together in a controlled environment. This molten metal mixture is then carefully alloyed to achieve the specific composition of Inconel 625. Imagine this step like mixing all the cake ingredients together to create a uniform batter.
- Zerstäubung: Here’s where things get interesting. The molten Inconel 625 is subjected to a high-pressure stream, typically water or gas. This rapid atomization process breaks down the molten metal into a fine mist of tiny droplets, which solidify rapidly into spherical Inconel 625 powder particles. Think of it like using a high-powered whisk to create tiny, perfectly round cake batter balls!
- Classification and Sieving: Not all the powder particles are created equal. After atomization, the Inconel 625 powder undergoes a classification and sieving process. This ensures that the final product consists of particles with a specific size range, critical for optimal performance in 3D printing processes. Just like sorting different sized sprinkles for your cake, this step ensures consistency in the final powder.
- Qualitätskontrolle: Finally, the produced Inconel 625 powder undergoes rigorous quality control checks. These checks analyze factors like particle size distribution, chemical composition, and flowability to ensure the powder meets the desired specifications. It’s like the final quality check before your cake goes into the oven!
Through this meticulous process, raw materials are transformed into the microscopic marvels that are Inconel 625 powder, ready to be utilized in additive manufacturing to create high-performance components.
Anwendungen von Inconel 625-Pulver
The exceptional properties of Inconel 625 powder translate into a diverse range of applications across various demanding industries. Here are some prime examples:
- Luft- und Raumfahrt: Imagine the scorching heat and immense stress a jet engine endures during flight. Inconel 625 powder comes to the rescue here. Its ability to withstand high temperatures and maintain strength makes it ideal for creating critical components in jet engines, such as turbine blades, combustor liners, and afterburner parts. These components can handle the intense heat and pressure within the engine, ensuring safe and efficient operation.
- Chemische Verarbeitung: Chemical processing plants often deal with harsh and corrosive environments. Regular metals simply wouldn’t survive long-term exposure to these elements. Inconel 625 powder steps up to the challenge. Thanks to its exceptional resistance to a wide range of chemicals, it’s used to create components like pumps, valves, and heat exchangers. These components can withstand the corrosive attacks of chemicals, ensuring the smooth functioning of the processing plant.
- Marine Applications: The unforgiving saltwater environment poses a constant threat to traditional metals, causing them to rust and deteriorate rapidly. Inconel 625 powder offers a solution. Its impressive resistance to saltwater corrosion makes it perfect for creating marine components like impellers, propellers, and rudders. These components can endure the harsh ocean environment, ensuring the longevity and reliability of marine vessels.
- Öl- und Gasindustrie: The oil and gas industry operates in extreme environments, with high temperatures and pressures being commonplace. Inconel 625 powder proves its mettle (pun intended) here as well. It’s used to create components like downhole drilling tools, wellhead equipment, and valves. These components can handle the demanding conditions within oil and gas wells, ensuring safe and efficient extraction of resources.
- Stromerzeugung: The world relies heavily on power generation for its daily needs. Inconel 625 powder plays a role here too. Its high-temperature resistance and strength make it ideal for creating components in power plants, such as turbine blades, heat exchangers, and combustor liners. These components can withstand the intense heat and pressure within the power generation process, ensuring the reliable production of electricity.
- Medizinische Geräte: When it comes to medical devices implanted in the human body, biocompatibility and corrosion resistance are paramount. Inconel 625 powder, with its exceptional properties, is used to create some medical implants, like bone screws and joint replacements. These implants offer a durable and biocompatible option for patients, improving their quality of life.
Beyond these core applications, Inconel 625 powder finds use in various other demanding fields, including:
- Kernenergie
- Desalination Plants
- Rocket Engine Components
- Vorrichtungen für die Wärmebehandlung
As 3D printing technology continues to evolve, we can expect even more innovative applications for Inconel 625 powder to emerge in the future.
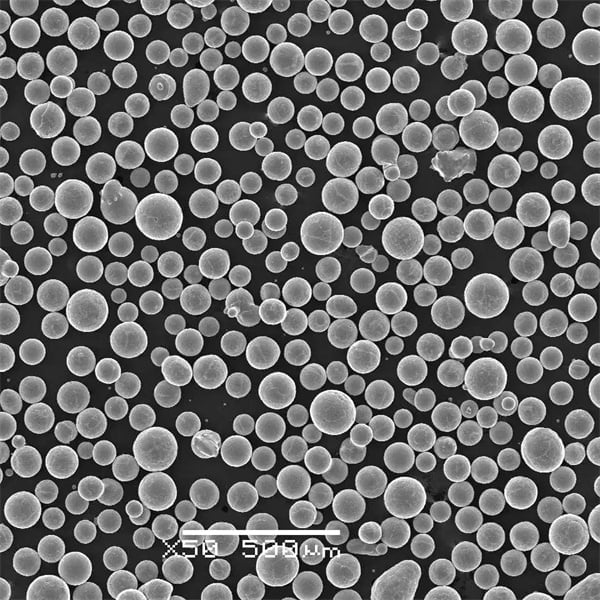
Vorteile und Beschränkungen von Inconel 625-Pulver
While Inconel 625 powder boasts impressive characteristics, it’s important to consider both its advantages and limitations before incorporating it into your project.
Vorteile:
- Exceptional Strength and High-Temperature Resistance: As discussed earlier, Inconel 625 powder excels in these areas, making it ideal for demanding applications.
- Hervorragende Korrosionsbeständigkeit: Its ability to withstand harsh chemicals and saltwater environments opens doors for various applications in harsh conditions.
- 3D Printing Compatibility: The spherical morphology of the powder makes it perfect for additive manufacturing processes, allowing for the creation of complex and intricate components.
- Biokompatibilität: For specific medical applications, Inconel 625 powder offers a biocompatible option for certain implants.
Beschränkungen:
- Kosten: Inconel 625 powder is a premium material, and its production process reflects that. Compared to some conventional metals, it can be a more expensive option.
- 3D Printing Challenges: While compatible with 3D printing, Inconel 625 powder requires specialized printers and expertise to handle its high melting point and flow characteristics.
- Nachbereitung: Depending on the application, some Inconel 625 powder components might require post-processing techniques like heat treatment for optimal performance.
Eine informierte Entscheidung treffen:
The decision to use Inconel 625 powder should be based on a careful evaluation of your specific needs. If your project demands exceptional strength, high-temperature resistance, and corrosion defiance, and the budget allows for it, then Inconel 625 powder might be the perfect choice. Consulting with a 3D printing expert can be beneficial to determine if your design is compatible with the specific challenges of Inconel 625 powder printing and to explore potential alternatives.
Das Richtige finden Inconel 625-Pulver Anbieter
Having identified Inconel 625 powder as the ideal material for your project, the next step is finding a reliable supplier. Here are some key factors to consider:
- Reputation und Erfahrung: Look for a supplier with a proven track record in providing high-quality Inconel 625 powder. Experience in the additive manufacturing industry is a plus.
- Powder Quality and Certification: Ensure the supplier offers Inconel 625 powder that meets industry standards and certifications. Inquire about the powder’s chemical composition, particle size distribution, and flowability to guarantee optimal printing results.
- Technische Unterstützung: A reputable supplier will offer technical support to assist you with any questions or challenges you might encounter while working with Inconel 625 powder.
- Preise und Vorlaufzeiten: Compare pricing and lead times from different suppliers to find the best fit for your project’s budget and timeline.
By carefully considering these factors, you can select a reliable Inconel 625 powder supplier who can provide the high-quality materials and support you need for your project’s success.
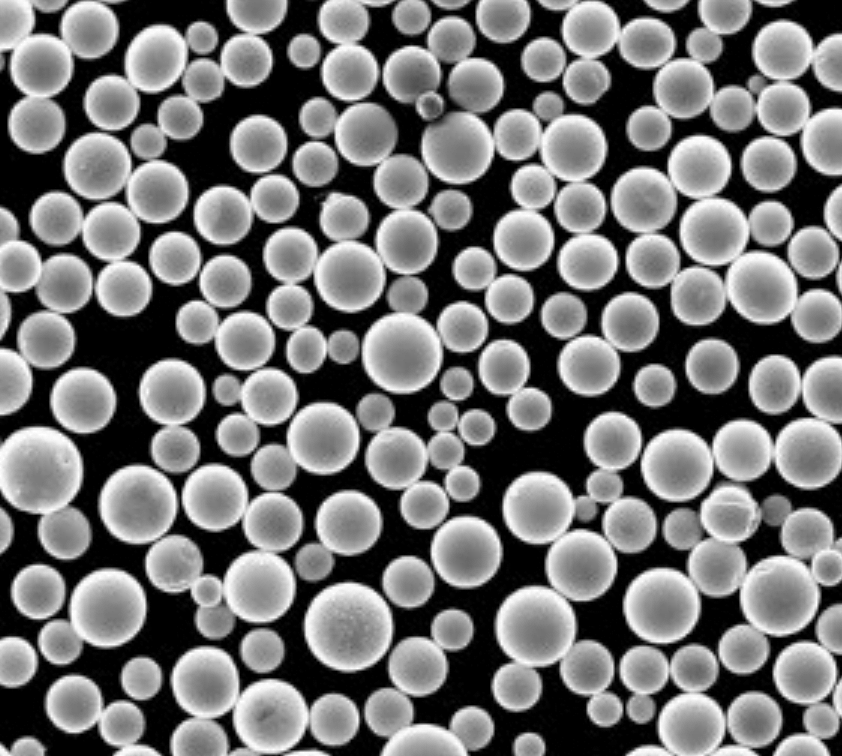
FAQ
Q: What are the typical particle sizes of Inconel 625 powder?
A: Inconel 625 powder is typically available in a range of particle sizes, from 15-45 microns to 45-100 microns. The specific size chosen will depend on the desired application and the 3D printing process being used.
Q: Does Inconel 625 powder require special storage conditions?
A: Yes, proper storage is crucial for maintaining the quality of Inconel 625 powder. It should be stored in a dry, inert atmosphere to prevent moisture absorption and oxidation. Many suppliers offer packaging specifically designed for safe and long-term storage of Inconel 625 powder.
Q: Can Inconel 625 powder components be recycled?
A: Yes, Inconel 625 powder, like most metal powders, is recyclable. This makes it an attractive option for projects with sustainability considerations. Check with your supplier about their recycling programs for metal powders.
Q: What are some safety precautions to take when handling Inconel 625 powder?
A: Inconel 625 powder can be slightly irritating to the skin and respiratory system. When handling the powder, it’s advisable to wear gloves, safety glasses, and a dust mask to minimize inhalation.
Fazit
Inconel 625 powder stands as a testament to cutting-edge material science. Its exceptional combination of strength, high-temperature resistance, and corrosion defiance makes it a valuable asset in various demanding industries. By understanding its characteristics, production process, applications, advantages, and limitations, you can make an informed decision about whether Inconel 625 powder is the right choice for your project. With careful selection of a reliable supplier and proper handling practices, you can harness the power of Inconel 625 powder to create high-performance components that push the boundaries of design and engineering.
Über 3DP mETAL
Produktkategorie
KONTAKT
Hast du Fragen? Schick uns jetzt eine Nachricht! Nach Eingang deiner Nachricht bearbeiten wir deine Anfrage im Team.