Imagine a world where manufacturing creates less waste and precious resources are used more efficiently. In the realm of 3D printing, this vision is becoming a reality thanks to advancements in recycling and utilizing metal powder. This revolutionary approach isn’t just about saving money; it’s about minimizing environmental impact and pushing the boundaries of sustainable production.
The Recycling and Utilization Method of 3D Printed Metal Powder
The magic of metal powder recycling lies in its ability to recapture unutilized material from the 3D printing process. Here’s a breakdown of the hero’s journey (so to speak) of used metal powder:
- Sammlung: After a print job is complete, leftover powder resides within the printer’s build chamber. Sophisticated systems are employed to meticulously collect this powder, ensuring minimal contamination.
- Sifting and Separation: The collected powder isn’t a uniform bunch. Think of it like a trail mix with various sized particles. Specialized sieves or sifters come into play, meticulously separating the usable powder from oversized particles or debris formed during the printing process. These oversized bits, often called “spatter,” can negatively affect future prints if not removed.
- Cleaning and Degasification: Even the “good” powder might harbor unwanted hitchhikers – moisture or trapped gases. Advanced cleaning techniques, like inert gas purging or thermal treatments, meticulously remove these contaminants. Imagine it as giving the powder a refreshing spa day to ensure optimal performance.
- Analysis and Reintegration: The revitalized powder isn’t sent back into action blindly. Rigorous testing analyzes its chemical composition, flowability (how easily it moves), and other critical properties. If it meets the stringent quality standards, it’s then strategically blended with virgin powder to create a fresh batch, ready to breathe life into a new generation of 3D printed parts.
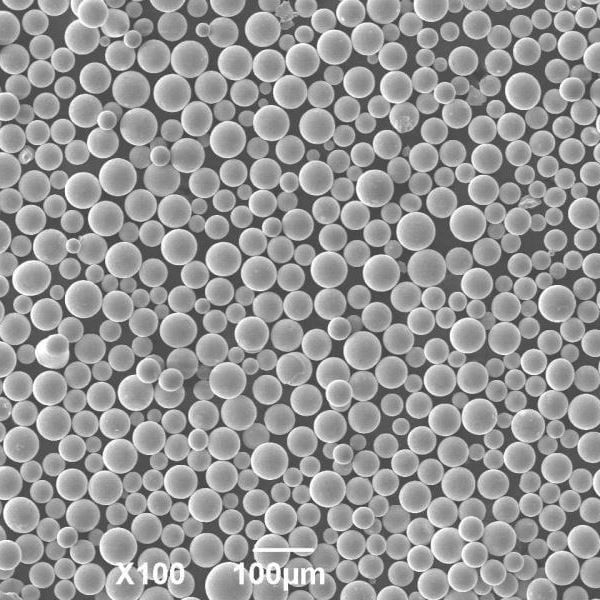
The Technology of 3D printed metal powder Recycling and Utilization
While the core principles remain the same, the technology behind metal powder recycling has several variations. Here are a couple of prominent approaches:
- Closed-Loop Systems: These self-contained heroes keep the party going within the same printer. They boast integrated collection units that seamlessly capture and process leftover powder for immediate reuse in subsequent print jobs. Think of it as an in-house recycling plant for your 3D printer, minimizing waste and maximizing efficiency.
- Off-Site Recycling Facilities: For larger operations or dealing with a wider variety of metal powders, off-site recycling facilities offer a centralized solution. These specialized centers possess the expertise and equipment to handle diverse metal types and ensure a meticulous recycling process. Imagine sending your used toner cartridges to a dedicated recycling center – but for metal powder from multiple printers.
The Advantages and Considerations of Metal Powder Recycling
The benefits of recycling metal powder are numerous:
- Reduced Environmental Impact: Virgin metal production is an energy-intensive process. Recycling significantly reduces the need for new material extraction, lowering the overall environmental footprint of 3D printing. It’s like giving the planet a high five for sustainability!
- Kosteneinsparungen: Metal powders can be quite expensive, especially for high-performance alloys. Recycling allows for significant cost savings by maximizing the utilization of existing materials. Think of it as stretching your metal powder budget further.
- Material Consistency: Recycled powder, when properly processed, can maintain the exceptional properties of virgin material. This consistency ensures the high quality and performance expected from 3D printed metal parts. Imagine a well-maintained car – recycled powder keeps your 3D printing running smoothly.
However, there are also some considerations to keep in mind:
- Qualitätskontrolle: Maintaining consistent powder quality is paramount. Any contamination or degradation during the recycling process can compromise the final printed parts. Strict quality control measures are essential to ensure recycled powder meets the necessary specifications.
- Powder Degradation: Some metal powders, particularly those prone to oxidation, might experience a slight decline in their properties after multiple recycling cycles. Understanding the specific limitations of each material is crucial.
- Separation Challenges: Differentiating between usable powder and splatter can be tricky for certain metals. Advanced separation techniques are required to ensure optimal performance of the recycled material.
The Impact of 3D printed metal powder Recycling
The implications of metal powder recycling extend far beyond cost savings and environmental benefits. Here are some exciting ways it’s shaping the future of manufacturing:
- Reduced Dependence on Virgin Materials: As recycling becomes more efficient and cost-effective, the reliance on virgin metal extraction will decrease. This translates to a more sustainable and resource-conscious manufacturing landscape.
- Unlocking New Applications: The economic viability of 3D printing metal parts often hinges on material costs. Metal powder recycling can make previously cost-prohibitive applications, such as complex aerospace components or medical implants, more accessible. Imagine being able to 3D print a lighter, stronger rocket engine at a fraction of the cost – recycled metal powder makes such dreams a possibility.
- Embracing Circular Economy Principles: The concept of a circular economy revolves around minimizing waste and maximizing resource utilization. Metal powder recycling perfectly embodies this principle by creating a closed-loop system within the 3D printing process. Imagine a world where materials are constantly reused and reinvented, minimizing environmental impact.
Examples of Metal Powder Recycling in Action
The potential of metal powder recycling isn’t just theoretical. Here are some real-world examples showcasing its transformative power:
- Luft- und Raumfahrtindustrie: Weight reduction is a constant pursuit in airplane design. 3D printing with recycled titanium allows aerospace manufacturers to create lightweight, high-strength components, improving fuel efficiency and overall aircraft performance. Imagine airplanes soaring through the sky with a lighter footprint, thanks to recycled metal parts.
- Medizinische Implantate: Metal powder recycling is making waves in the medical field. The ability to create custom-made implants using recycled materials like titanium or cobalt-chrome offers numerous advantages. Reduced cost, improved biocompatibility, and the possibility of personalized designs are just a few benefits this technology offers. Imagine a future where patients receive life-changing implants made with sustainable practices.
- Automobilindustrie: The automotive industry is constantly seeking ways to reduce weight and improve fuel efficiency. Metal powder recycling allows car manufacturers to explore 3D printing for lightweight components, potentially leading to a new generation of eco-friendly vehicles. Imagine a car with a lighter body and a smaller environmental footprint, made possible by recycled metal parts.
Challenges and Opportunities for Metal Powder Recycling
While the future of metal powder recycling is bright, there are still challenges to overcome:
- Standardization: Currently, there’s a lack of standardized guidelines for recycled metal powder qualification. Developing robust standards will ensure consistent quality and wider adoption of this technology.
- Public Perception: Some hesitation exists regarding the quality and reliability of recycled metal parts. Increased education and successful real-world applications are crucial to addressing these concerns.
- Economies of Scale: As recycling technology matures and production volumes increase, the overall cost of recycled metal powder is expected to decrease. This will further enhance the economic viability of 3D printing with recycled materials.
Despite these challenges, the opportunities presented by metal powder recycling are undeniable. With continued research, development, and industry collaboration, this technology has the potential to revolutionize 3D printing and usher in a new era of sustainable manufacturing.
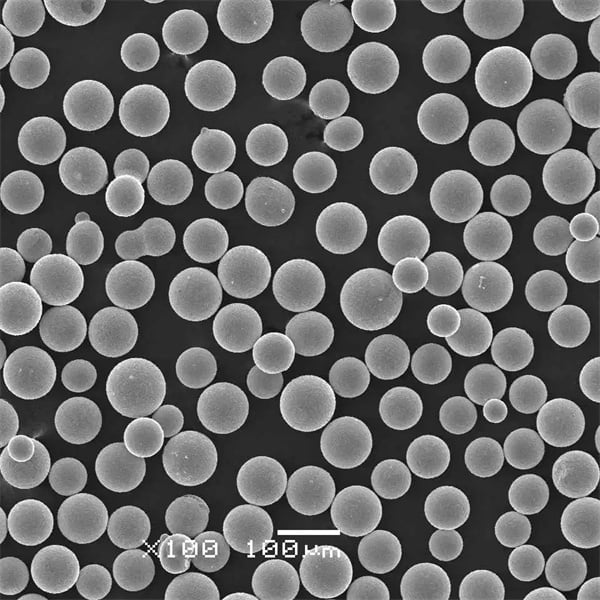
FAQ
Q: Is recycled metal powder less effective than virgin powder?
A: Not necessarily. When properly processed, recycled metal powder can maintain the exceptional properties of virgin material. Rigorous quality control measures ensure that the recycled powder meets the necessary specifications for optimal performance in 3D printed parts.
Q: What are the different methods for recycling metal powder?
A: The two main approaches are closed-loop systems and off-site recycling facilities. Closed-loop systems are self-contained units within a 3D printer, allowing for immediate reuse of leftover powder. Off-site facilities handle diverse metal types and offer centralized recycling solutions for larger operations.
Q: What are the environmental benefits of metal powder recycling?
A: Virgin metal production is an energy-intensive process. Metal powder recycling significantly reduces the need for new material extraction, resulting in a lower environmental footprint for 3D printing. It translates to less energy consumption and a smaller impact on the planet’s resources.
Q: Does the type of metal affect the recycling process?
A: Yes. Different metals have varying properties and sensitivities to oxidation or contamination. The recycling process needs to be tailored to the specific type of metal powder to ensure optimal results.
Q: What is the future of metal powder recycling in 3D printing?
A: The future is bright! As technology advances and costs decrease, metal powder recycling is poised to become a mainstream practice. This will lead to a more sustainable manufacturing landscape, reduced dependence on virgin materials, and exciting new applications for 3D printing across various ind
Über 3DP mETAL
Produktkategorie
KONTAKT
Hast du Fragen? Schick uns jetzt eine Nachricht! Nach Eingang deiner Nachricht bearbeiten wir deine Anfrage im Team.