Imagine having a box filled with tiny, magical metal spheres. These aren’t your average ball bearings; these are diffusion alloy powders, the building blocks of a revolutionary metal additive manufacturing (AM) process. By combining different metal elements on a microscopic level, diffusion alloy powders unlock a world of possibilities for creating high-performance and customized metal parts.
But before we delve into the nitty-gritty, let’s take a step back. Have you ever wondered how those sleek prosthetic limbs or intricate jet engine components are made? Traditional methods like machining or casting can be limiting. Enter AM, also known as 3D printing for metals. This technology uses a computer-controlled process to build objects layer-by-layer from a digital file. Diffusion alloy powders are the fuel that powers this innovative technique.
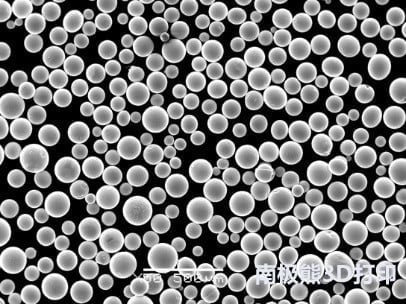
Chemical Composition of Diffusion Alloy Powder
Unlike regular metal powders, diffusion alloy powders have a secret weapon: a pre-alloyed composition. Imagine a tiny metal grain with elements like nickel and chromium subtly diffused throughout its structure. This creates a more uniform and consistent material compared to simply mixing different metal powders together.
Here’s a table to showcase the variety of diffusion alloy powder compositions available:
Diffusion Alloy Powder Type | Chemical Composition | Key Properties |
---|---|---|
Nickel-Chromium (Ni-Cr) | Nickel (Ni) as the base metal with Chromium (Cr) additions | High-temperature resistance, excellent corrosion resistance |
Cobalt-Chromium (Co-Cr) | Cobalt (Co) as the base metal with Chromium (Cr) additions | Biocompatible, wear-resistant, ideal for medical implants |
Copper-Tin (Cu-Sn) | Copper (Cu) as the base metal with Tin (Sn) additions | Enhanced electrical conductivity, good thermal conductivity |
Iron-Nickel (Fe-Ni) | Iron (Fe) as the base metal with Nickel (Ni) additions | Magnetic properties, good for electromagnetic applications |
Inconel | Nickel-chromium alloy with additions like molybdenum and iron | Exceptional high-temperature strength, oxidation resistance |
Invar | Iron-nickel alloy with a very low thermal expansion coefficient | Dimensionally stable, ideal for precision instruments |
Maraging Steel | High-nickel steel alloy with additions like molybdenum, titanium, and aluminum | High strength-to-weight ratio, excellent toughness |
Stainless Steel | Iron-chromium alloy with varying levels of chromium and molybdenum | Corrosion resistance, good for diverse applications |
Tungsten Carbide (WC) | Hard ceramic compound of Tungsten (W) and Carbon (C) | Extremely hard and wear-resistant, used for cutting tools |
Tool Steel | Various iron-based alloys with additions like chromium, vanadium, and tungsten | High hardness, wear resistance, ideal for tooling applications |
The Advantages of Diffusion Alloy Powder
Now that we’ve peeked inside the chemistry, let’s explore the superpowers of diffusion alloy powders:
- Uniform Microstructure: The pre-alloyed nature ensures a consistent distribution of elements throughout the powder particles. This translates to a more predictable and reliable final product compared to mixed metal powders.
- Enhanced Properties: By diffusing elements on a microscopic level, manufacturers can achieve superior properties like increased strength, improved corrosion resistance, and tailored electrical or magnetic characteristics.
- Superior Printability: The optimized flow characteristics of diffusion alloy powders make them ideal for AM processes. They flow smoothly during the printing process, leading to better layer adhesion and reduced porosity in the final part.
- Design Flexibility: The diverse range of available diffusion alloy powders allows for the creation of parts with a wide range of properties. This opens doors for designing and manufacturing complex, high-performance components.
Disadvantages of Diffusion Alloy Powder
While diffusion alloy powders boast impressive advantages, it’s important to acknowledge some limitations:
- Cost: Compared to basic metal powders, diffusion alloy powders can be more expensive due to the additional processing involved in pre-alloying the elements.
- Limited Availability: Not all metal combinations are readily available as diffusion alloy powders. The selection might be narrower compared to individual metal powders.
- Process Optimization: AM machines might require specific parameter adjustments to handle the unique properties of diffusion alloy powders compared to standard metal powders.
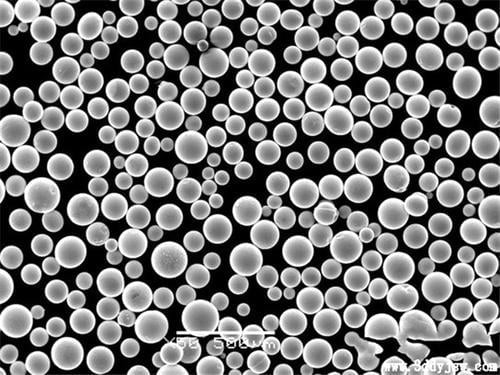
Applications of Diffusion Alloy Powder
Diffusion alloy powders are revolutionizing various industries by enabling the creation of:
Industry | Applications |
---|---|
Aerospace | High-temperature resistant turbine blades, lightweight and strong airframe components |
Medical | Biocompatible implants like hip replacements and dental crowns |
Automotive | Wear-resistant engine components, lightweight and high-strength suspension parts |
Energy | Corrosion-resistant heat exchangers, components for nuclear reactors |
Consumer Goods | Customizable jewelry, durable sporting equipment, lightweight and strong electronics components |
Tooling | Hard-wearing cutting tools, long-lasting molds and dies |
Examples of Specific Metal Diffusion Alloy Powders and their Uses:
- Cobalt-Chromium (Co-Cr): This biocompatible workhorse is a popular choice for medical implants like knee and hip replacements. Its wear resistance ensures smooth articulation for years to come.
- Inconel: An all-star for high-temperature applications, Inconel powders are used to create turbine blades for jet engines. Their exceptional heat resistance allows them to withstand the extreme temperatures within a jet engine.
- Maraging Steel: Looking for a lightweight champion? Maraging steel powders are perfect for aerospace applications where weight reduction is crucial. Despite being lightweight, they offer impressive strength for critical aircraft components.
- Stainless Steel: A versatile player in many industries, stainless steel diffusion alloy powders are used for everything from corrosion-resistant pipes in the oil and gas industry to medical instruments that need to be sterilized repeatedly.
- Tungsten Carbide (WC): The ultimate tough guy, WC powders are used to create drill bits and cutting tools that can slice through even the hardest materials.
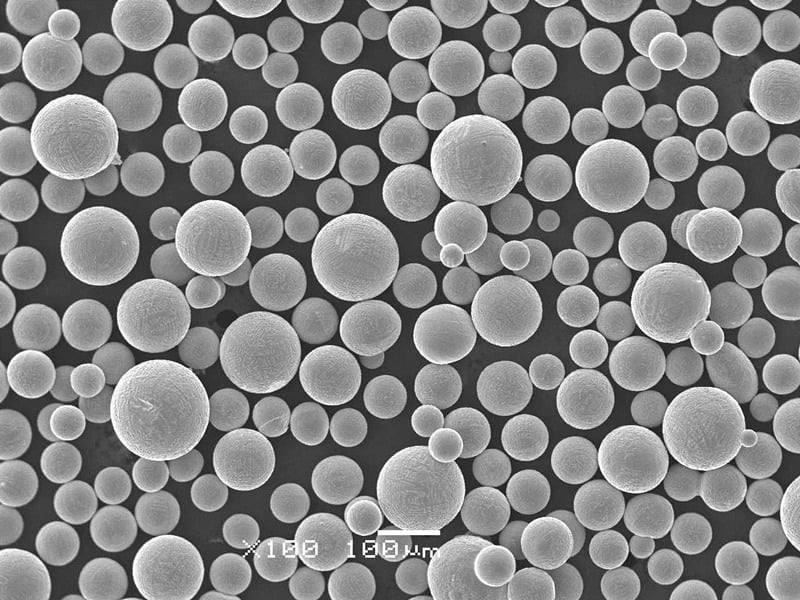
Specifications, Sizes, Grades, and Standards of Diffusion Alloy Powder
Diffusion alloy powders come in a variety of specifications to cater to different AM processes and desired final part properties. Here’s a breakdown:
- Particle Size: The size of the powder particles plays a crucial role in the printability and final surface finish of the part. Typical sizes range from 15 to 150 microns, with finer powders offering smoother finishes but potentially requiring more specialized printing techniques.
- Grades: Similar to other metal powders, diffusion alloy powders come in various grades depending on their chemical composition and intended application. For example, a medical-grade Co-Cr powder might have tighter control over impurities compared to a general-purpose grade.
- Standards: To ensure quality and consistency, diffusion alloy powders adhere to industry standards set by organizations like ASTM International and the Metal Powder Industries Federation (MPIF). These standards define parameters like chemical composition, particle size distribution, and flowability.
Suppliers and Pricing of Diffusion Alloy Powder
Several companies specialize in the production and supply of diffusion alloy powders. Here’s a table with some prominent players:
Supplier | Website | Products Offered | Price Range (Estimated) |
---|---|---|---|
Höganäs AB | https://www.hoganas.com/en/ | Nickel alloys, stainless steel, tool steel | $50-200 per kg |
AP Powder Company | https://www.allpowderpaints.com/ | Cobalt-chromium, Inconel, maraging steel | $100-300 per kg |
Carpenter Additive | https://www.carpenteradditive.com/ | Nickel alloys, stainless steel, tool steel | $80-250 per kg |
AM powders | https://www.amixon.com/en/blog/powder-processing-for-additive-manufacturing-with-plastic-ceramic-and-metallic-materials | Wide variety of diffusion alloy powders | Varied depending on material |
Pricing is a crucial factor to consider when choosing a diffusion alloy powder. Generally, the price is influenced by the material composition, powder grade, and supplier. More exotic materials like Inconel or maraging steel will typically command a higher price compared to common stainless steel powders.
Diffusion Alloy Powder: A Balancing Act
Choosing the right diffusion alloy powder requires careful consideration. Here’s a table summarizing the pros and cons to help you navigate the decision-making process:
Advantages | Disadvantages |
---|---|
Uniform microstructure | Higher cost |
Enhanced properties | Limited availability |
Superior printability | Process optimization required |
Design flexibility |
Ultimately, the ideal diffusion alloy powder depends on your specific project requirements. Factors like budget, desired final part properties, and compatibility with your AM equipment all play a role.
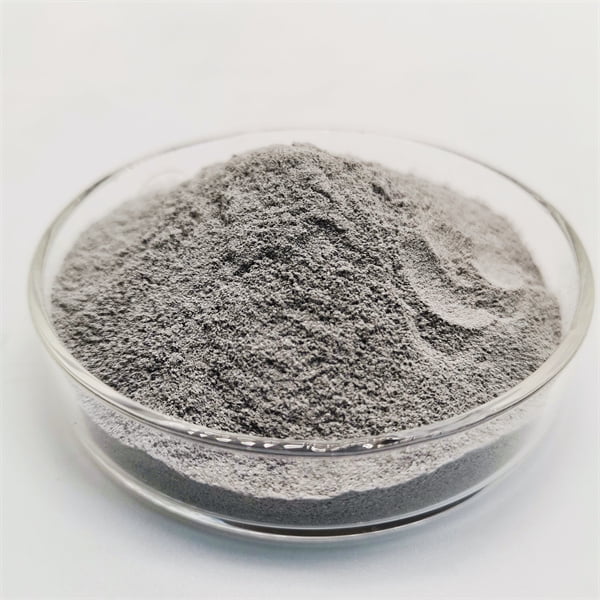
FAQ
Q: Are diffusion alloy powders the same as mixed metal powders?
A: No, diffusion alloy powders differ from mixed metal powders. In diffusion alloy powders, the elements are pre-alloyed at the particle level. Mixed metal powders simply combine individual metal powders, which can lead to inconsistencies in the final product.
Q: What are the benefits of using diffusion alloy powders for 3D printing?
A: Diffusion alloy powders offer several advantages for 3D printing, including improved material properties, better printability, and the ability to create parts with tailored functionalities.
Q: Are there any limitations to using diffusion alloy powders?
A: Yes, there are a few limitations to consider. Diffusion alloy powders can be more expensive than standard metal powders, and the selection of available compositions might be narrower. Additionally, some AM machines might require parameter adjustments to optimize printing with these powders.
Q: What are some of the safety considerations when handling diffusion alloy powders?
A: Diffusion alloy powders, like many metal powders, can pose health risks if inhaled. Proper safety protocols like using a fume hood and wearing personal protective equipment (PPE) are crucial during handling and storage.
About 3DP mETAL
Product Category
CONTACT US
Any questions? Send us a message now! After receiving your message, we will process your request with a whole team.