Imagine a manufacturing process that merges the intricate design freedom of plastic injection molding with the unparalleled strength and durability of metal. That’s the magic of Τεχνολογία MIM, a game-changer in the world of metalworking.
This article delves into the fascinating world of MIM Technology, exploring its intricacies, applications, advantages, and considerations. So, buckle up and get ready to discover a technology that’s pushing the boundaries of what’s possible in metal manufacturing.
The MIM Process
MIM operates on a deceptively simple principle. Here’s a breakdown of the steps involved:
- Powder Powerhouse: The journey begins with finely-powdered metal, akin to a metallic dust. This powder can be composed of various metals, including steel, stainless steel, titanium, and even exotic alloys.
- Binder Bonding: Imagine mixing the metal powder with a special binding agent, like a glue holding everything together. This concoction, known as feedstock, becomes the moldable material for the next step.
- Injection Intuition: The feedstock is then injected into a precisely designed mold cavity under high pressure. Think of it like squeezing Play-Doh into a cookie cutter, but with much more sophisticated machinery.
- Διαμόρφωση: Once injected, the feedstock takes the shape of the mold cavity, forming a near-net shape component. This near-net shape refers to a part that requires minimal post-processing to achieve its final dimensions.
- Binder Buh-Bye: The next stage involves removing the binder through a thermal debinding process. This can involve techniques like solvent extraction or thermal degradation, essentially vaporizing the binder and leaving behind the metal skeleton.
- Strength Surge: The final step is a high-temperature sintering process. Here, the metal particles get hot and cozy, fusing together and densifying the component. This significantly enhances the strength and structural integrity of the part.
Think of MIM as a sophisticated metallic origami, meticulously folding metal powder into intricate shapes with impressive strength.
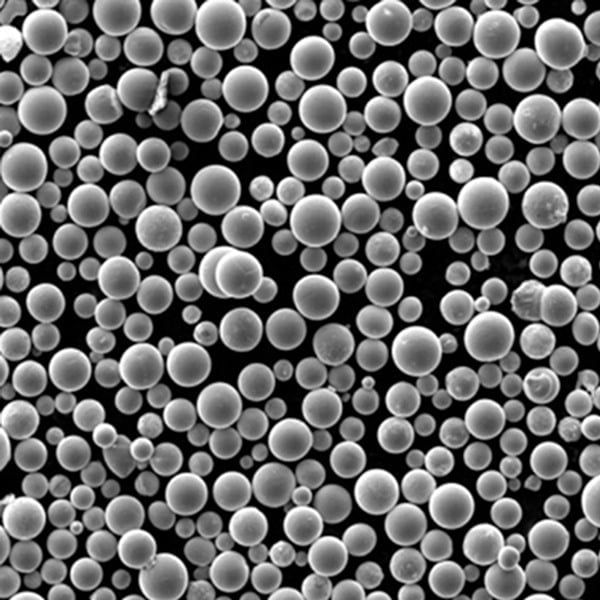
Τα πλεονεκτήματα της Τεχνολογία MIM
MIM technology boasts a compelling set of advantages that make it a preferred choice for various manufacturing applications. Let’s delve into some key benefits:
- Design Versatility: Unlike traditional metalworking methods like casting or machining, MIM offers exceptional design freedom. Complex geometries, intricate details, and thin walls – MIM handles it all with ease. Imagine crafting gears with minuscule teeth or intricate medical instruments with delicate features – MIM makes it possible.
- High-Volume, High-Precision: MIM shines in high-volume production runs. The ability to create near-net shapes minimizes the need for extensive post-processing, leading to faster production cycles and cost savings. Additionally, MIM ensures exceptional dimensional accuracy, crucial for components requiring precise tolerances.
- Υλικό Marvel: MIM offers the flexibility to work with a wide range of metal powders. This opens doors to crafting components from high-strength steels, corrosion-resistant alloys, or even lightweight materials like titanium.
- Εκτιμήσεις κόστους: While the initial setup costs for MIM can be higher, the high-volume production capabilities and minimal post-processing translate to significant cost savings in the long run. This makes MIM a compelling option for mass-producing complex metal parts.
- Waste Not, Want Not: MIM is a relatively eco-friendly process compared to traditional methods. The near-net shape approach minimizes material waste, and the controlled debinding process allows for the recovery and reuse of binders in some cases.
MIM technology is a well-rounded champion, offering design flexibility, high-precision manufacturing, material versatility, and cost-effectiveness, all while minimizing environmental impact.
Οι εφαρμογές της Τεχνολογία MIM
MIM technology finds application in a diverse range of industries, from the intricate world of medical devices to the colossal realm of automotive components. Here are some prominent examples:
- Ιατρικά θαύματα: MIM plays a crucial role in crafting intricate medical implants like joint replacements, dental prosthetics, and surgical instruments. The ability to create complex shapes with biocompatible materials makes MIM ideal for these demanding applications.
- Automotive Advantage: The automotive industry leverages MIM for manufacturing various components like gears, sprockets, and fuel system parts. MIM’s high-volume production capabilities and ability to create near-net shapes with tight tolerances make it a perfect fit for the fast-paced automotive world.
- Consumer Electronics Symphony: From tiny components in mobile phones to intricate parts in wearables, MIM contributes to the miniaturization and functionality of consumer electronics. Its ability to produce complex shapes with high precision caters perfectly to the ever-shrinking world of gadgets.
- Aerospace Ascendancy: The aerospace industry demands lightweight yet robust components. MIM steps up to the challenge by enabling the creation of complex parts from high-strength, low-weight alloys like titanium. This translates to fuel efficiency and improved performance for aircraft and spacecraft.
- Firearms Finesse: MIM plays a role in the firearms industry for crafting intricate components like triggers, hammers, and safeties. Its ability to produce near-net shapes with high precision and exceptional strength makes it suitable for these demanding applications.
Beyond these prominent examples, MIM technology has the potential to revolutionize various other industries. As the technology matures and costs become more competitive, we can expect to see MIM applications expand into fields like:
- Energy Infrastructure: Manufacturing intricate components for pumps, valves, and other critical parts in power generation and distribution systems.
- Telecommunications: Creating miniaturized and high-precision components for complex telecommunication equipment.
- Αθλητικά είδη: Crafting lightweight and durable components for bicycles, golf clubs, and other sporting equipment.
The possibilities with MIM technology are truly vast, and its impact on various industries is only expected to grow in the coming years.
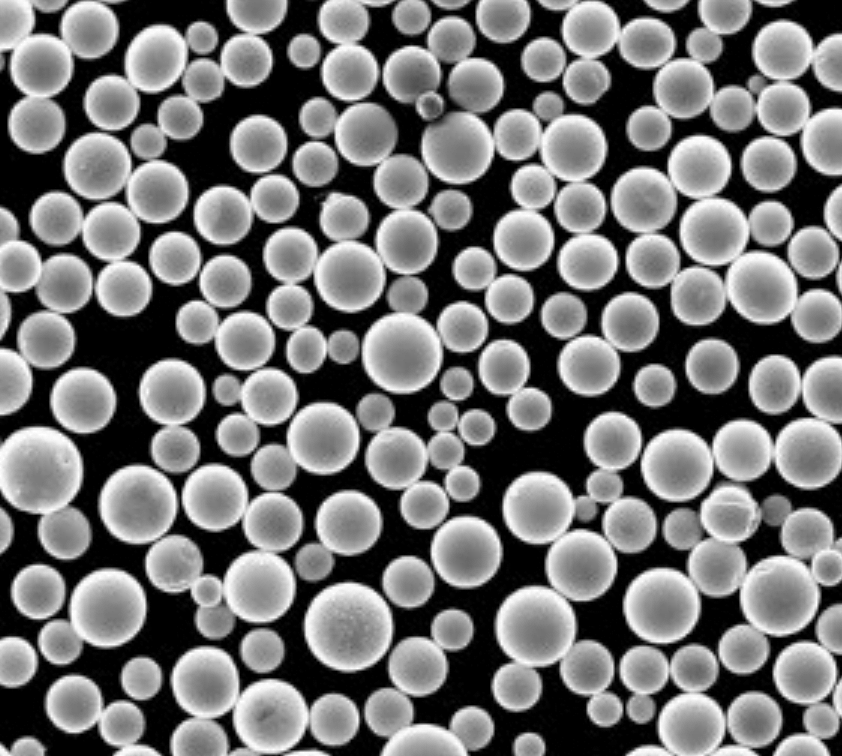
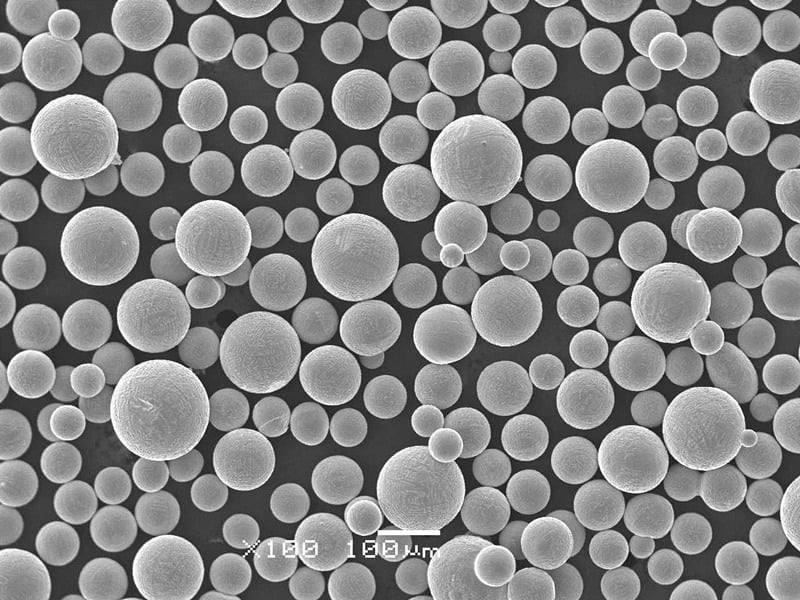
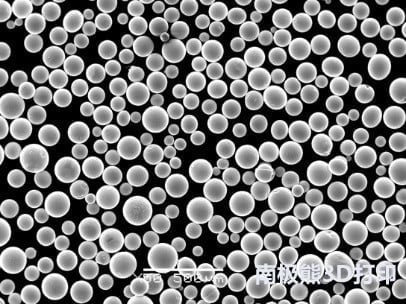
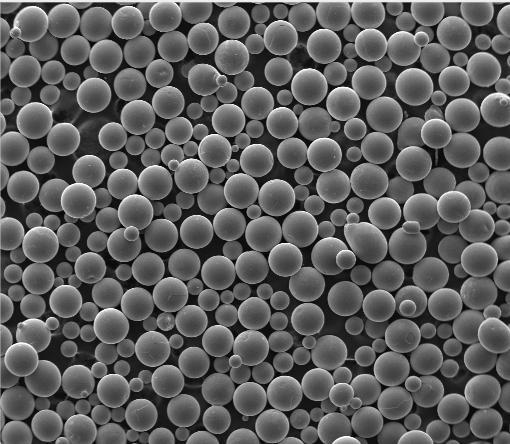
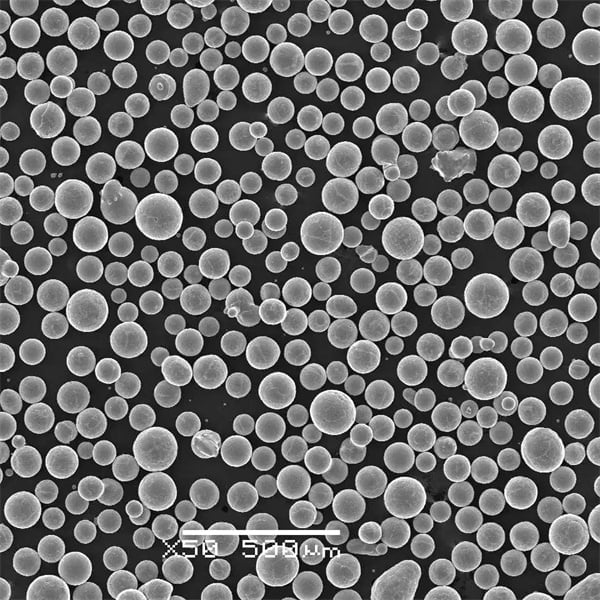
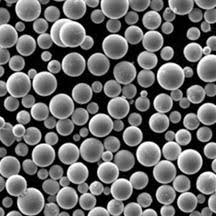
The Characteristics of Atomization Technology
Now that we’ve explored the magic of MIM, let’s delve deeper into a crucial aspect – atomization technology. This process is responsible for creating the fine metal powders that form the foundation of MIM. Here’s a breakdown of the two primary atomization techniques:
- Ατομοποίηση αερίου: Imagine molten metal being forced through a high-pressure nozzle, breaking it into tiny droplets that solidify in mid-air as fine metal powder. This is the essence of gas atomization. It’s a versatile technique suitable for a wide range of metals and alloys.
- Ψεκασμός νερού: This method utilizes a high-velocity water jet to fragment molten metal into fine particles. Water atomization is particularly well-suited for producing spherical metal powders and is often used for specific materials like stainless steel.
The choice of atomization technique depends on several factors, including the desired powder characteristics, the type of metal being processed, and the cost considerations.
Here’s a table summarizing the key characteristics of each atomization technique:
Χαρακτηριστικό γνώρισμα | Αεριοποίηση | Ατομοποίηση νερού |
---|---|---|
Διαδικασία | Molten metal forced through a high-pressure nozzle | Molten metal fragmented by a high-velocity water jet |
Μορφολογία σκόνης | Generally irregular shapes | Typically more spherical |
Metal Suitability | Wide range of metals and alloys | Primarily suited for specific materials like stainless steel |
Κόστος | Generally higher cost | Lower cost compared to gas atomization |
It’s important to note that this table provides a general comparison, and there can be some overlap in capabilities depending on the specific technology and process parameters.
Εκτιμήσεις και περιορισμοί της Τεχνολογία MIM
While MIM offers a compelling set of advantages, it’s essential to understand its limitations and considerations before diving headfirst. Here are some key points to keep in mind:
- Part Size Constraints: MIM is best suited for producing relatively small to medium-sized components. The limitations arise from factors like mold filling capabilities and the potential for internal cracking during the debinding and sintering stages.
- Φινίρισμα επιφάνειας: While MIM can produce good surface finishes, it may not be ideal for applications requiring exceptional smoothness. Additional post-processing steps like polishing or machining might be necessary in such cases.
- Επιλογή υλικού: Not all metals are readily compatible with MIM. Factors like melting point and sintering behavior play a crucial role. Refractory metals with extremely high melting points might not be suitable for MIM due to limitations in processing temperatures.
- Design for MIM: To reap the full benefits of MIM, designing components specifically for the process is crucial. This involves considering factors like wall thickness, draft angles, and potential for internal stresses during processing.
By understanding these considerations and limitations, manufacturers can make informed decisions about whether MIM is the right fit for their specific application.
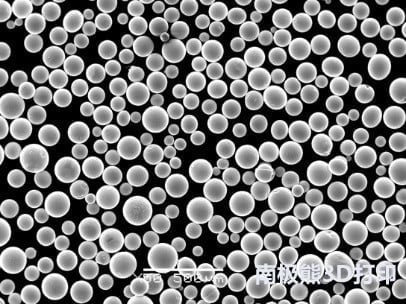
Συχνές ερωτήσεις
Here’s a section addressing some frequently asked questions about Τεχνολογία MIM, που παρουσιάζονται με σαφή και συνοπτική μορφή πίνακα:
Ερώτηση | Απάντηση |
---|---|
What are the advantages of MIM technology? | Design flexibility, high-volume production, material versatility, cost-effectiveness, and minimal waste. |
What are some applications of MIM technology? | Medical devices, automotive components, consumer electronics, aerospace parts, firearms components, and more. |
What are the different types of atomization techniques used in MIM? | Gas atomization and water atomization. |
What are the limitations of MIM technology? | Size constraints, surface finish limitations, material selection considerations, and the need for design for MIM principles. |
Is MIM an eco-friendly process? | MIM is relatively eco-friendly compared to traditional metalworking methods due to minimal material waste and potential for binder reuse. |
What are the future prospects of MIM technology? | MIM technology is expected to see continued growth and adoption across various industries due to its advantages and ongoing advancements. |
How does MIM compare to other metalworking processes like machining or casting? | MIM offers greater design freedom and near-net shapes compared to machining. While casting can produce complex shapes, MIM often boasts higher precision and better material properties. |
What are some of the challenges associated with MIM technology? | Developing cost-effective methods for processing a wider range of metals and alloys, and further advancements in debinding techniques to minimize potential for defects. |
Σχετικά με το 3DP mETAL
Κατηγορία προϊόντος
ΕΠΙΚΟΙΝΩΝΗΣΤΕ ΜΑΖΙ ΜΑΣ
Έχετε οποιεσδήποτε ερωτήσεις; Στείλτε μας τώρα ένα μήνυμα! Αφού λάβουμε το μήνυμά σας, θα επεξεργαστούμε το αίτημά σας με ολόκληρη την ομάδα.