Imagine building complex metal parts layer-by-layer with a focused beam of electrons, melting metal powder into intricate shapes with unmatched precision. This isn’t science fiction; it’s the reality of Electron Beam Additive Manufacturing (EBAM), a revolutionary technology transforming the way we design and manufacture metal components.
What is Electron Beam Additive Manufacturing (EBAM)?
EBAM, also known as Electron Beam Melting (EBM), is a metal 3D printing process that utilizes a high-powered electron beam to selectively melt metal powder into a 3D object. Unlike traditional manufacturing methods like machining or casting, EBAM builds parts from the ground up, adding material one layer at a time based on a digital 3D model. This allows for the creation of complex geometries, intricate internal features, and near-net-shape components that minimize post-processing.
Here’s how the magic happens:
- Preparation: Metal powder, meticulously chosen for its properties and particle size, is spread across a build platform within a vacuum chamber.
- Electron Beam Action: An electron gun fires a highly focused beam of electrons, guided by magnets, onto the powder bed. The intense heat melts the powder particles, fusing them together to form the first layer of the object.
- Layer by Layer: The build platform lowers slightly, and a fresh layer of powder is deposited. The electron beam then selectively melts the new powder, adhering it to the previous layer and building the object one slice at a time.
- Completion and Cooling: Once all layers are completed, the chamber cools down, and the finished part is extracted.
EBAM offers a compelling alternative to conventional metalworking techniques. It enables the creation of previously impossible geometries, reduces waste material, and streamlines production for complex parts.
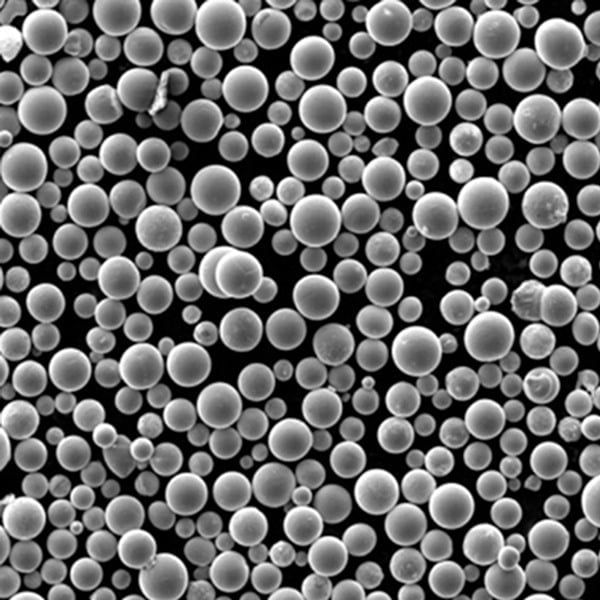
Metal Powders for EBAM
The success of EBAM hinges on the specific metal powder used. Different powders offer unique properties, catering to diverse applications. Let’s delve into some of the most common metal powders employed in EBAM:
Material | Description | Properties | Applications |
---|---|---|---|
Titanium Ti6Al4V (Grade 23) | The most widely used EBAM powder, known for its excellent strength-to-weight ratio, biocompatibility, and corrosion resistance. | High strength, low density, good fatigue strength, biocompatible | Aerospace components, biomedical implants, automotive parts |
Stainless Steel 316L | A versatile stainless steel powder offering superior corrosion resistance and good mechanical properties. | Excellent corrosion resistance, formability, good strength and ductility | Chemical processing equipment, marine components, medical devices |
Inconel 625 | A high-performance nickel-chromium superalloy renowned for its exceptional strength and resistance to high temperatures and oxidation. | Exceptional high-temperature strength, oxidation resistance, good weldability | Turbine blades, rocket engine components, heat exchangers |
Cobalt Chrome (CoCr) | A biocompatible cobalt-chromium alloy commonly used for its wear resistance and biocompatibility. | High wear resistance, biocompatible, good strength | Joint replacements, dental implants, wear-resistant components |
Aluminum AlSi10Mg | An aluminum alloy with good castability and machinability, offering a lightweight and cost-effective alternative. | Lightweight, good strength, machinability | Automotive parts, aerospace components, heat sinks |
Copper | Pure copper powder provides excellent thermal and electrical conductivity, making it ideal for heat exchangers and electrical components. | High thermal conductivity, high electrical conductivity, good ductility | Heat exchangers, electrical conductors, busbars |
Titanium Grade 5 | Offers superior strength compared to Ti6Al4V, ideal for high-stress applications. | High strength, good fatigue strength, biocompatible | Aerospace components, orthopedic implants, sporting goods |
Inconel 718 | Another high-performance superalloy boasting exceptional strength and creep resistance at elevated temperatures. | High strength, creep resistance, good oxidation resistance | Turbine disks, nuclear reactor components, oil and gas equipment |
Hastelloy C-276 | A nickel-chromium-molybdenum alloy renowned for its outstanding corrosion resistance to a wide range of chemicals. | Exceptional corrosion resistance, high strength, good weldability | Chemical processing equipment, pollution control systems, marine components |
Nickel 62 | A pure nickel powder offering good strength, ductility, and excellent electrical and thermal conductivity. | High strength, good ductility, high electrical conductivity, high thermal conductivity | Electrical components, electrodes, heat exchangers |
These are just a few examples, and the selection of metal powders for EBAM is constantly expanding. Material scientists are developing new alloys specifically designed for optimal performance in the EBAM environment, further pushing the boundaries
Characteristics of Electron Beam Additive Manufacturing
EBAM boasts a unique set of characteristics that differentiate it from other metal additive manufacturing processes:
- High Precision and Resolution: The focused electron beam allows for incredibly precise melting of metal powder, resulting in near-net-shape parts with exceptional dimensional accuracy and surface finish. Compared to techniques like laser powder bed fusion (LPBF), EBAM can achieve finer features and smoother surfaces due to the deeper melt pool it creates.
- Vacuum Environment: The entire EBAM process takes place within a high-vacuum chamber. This eliminates the risk of oxidation and contamination, ensuring the purity and quality of the final part. This is particularly advantageous for materials like reactive metals such as titanium and tantalum.
- High Melting Power: The electron beam generates immense heat, enabling the melting of a wider range of metal powders, including refractory metals with high melting points like tungsten and molybdenum. This versatility expands the design possibilities for engineers.
- Minimal Thermal Distortion: EBAM offers superior control over thermal gradients during the build process. The high-powered electron beam creates a deep melt pool, minimizing heat transfer to surrounding areas. This reduces warping and distortion, leading to parts with exceptional dimensional stability.
- Material Efficiency: Unlike subtractive manufacturing techniques that generate significant scrap material, EBAM utilizes a powder-bed approach. Unused powder can be recycled and reused for subsequent builds, minimizing material waste and promoting sustainability.
However, EBAM also comes with some limitations to consider:
- Higher Cost: EBAM systems are generally more expensive compared to other metal additive manufacturing technologies. The high vacuum environment, complex machinery, and specialized metal powders contribute to the initial investment cost.
- Surface Roughness: While EBAM offers good surface finish, it might not be as smooth as parts produced by LPBF. This is due to the nature of the electron beam melting process, which can leave a slightly rougher surface texture.
- Limited Build Size: Current EBAM systems typically have smaller build volumes compared to some other additive manufacturing technologies. This can restrict the size of parts that can be manufactured using EBAM.
- Post-Processing: While EBAM minimizes the need for post-processing compared to traditional methods, some parts might still require support structure removal and additional finishing depending on the application.
Choosing the right metal additive manufacturing technology depends on your specific needs and priorities. EBAM excels in applications where high precision, material compatibility, and exceptional mechanical properties are paramount.
Advantages of Electron Beam Additive Manufacturing
EBAM offers a compelling array of advantages that are revolutionizing metal manufacturing:
- Design Freedom: EBAM transcends the limitations of conventional techniques, allowing for the creation of complex geometries with internal channels, lattices, and intricate features that would be impossible or highly challenging to achieve through traditional methods. This opens doors for innovative and lightweight designs.
- Material Versatility: The ability to handle a wide range of metal powders, including reactive metals and high-melting-point alloys, broadens the material options for designers. This allows for the selection of materials with the ideal properties for specific applications.
- Near-Net-Shape Manufacturing: EBAM builds parts close to their final dimensions, minimizing the need for extensive post-processing steps such as machining. This translates to reduced lead times, lower production costs, and less material waste.
- Superior Mechanical Properties: The high melting temperatures and vacuum environment in EBAM lead to parts with exceptional mechanical properties, including high strength, good fatigue resistance, and excellent corrosion resistance. These properties are particularly crucial for demanding applications in aerospace, energy, and medical sectors.
- Lightweighting Potential: The ability to create complex internal structures allows for the design of lightweight components without compromising strength. This is a significant advantage for applications in aerospace, automotive, and other weight-sensitive industries.
- Reduced Waste: EBAM utilizes a powder-bed approach, and unused powder can be recycled and reused for subsequent builds. This minimizes material waste and promotes a more sustainable manufacturing process.
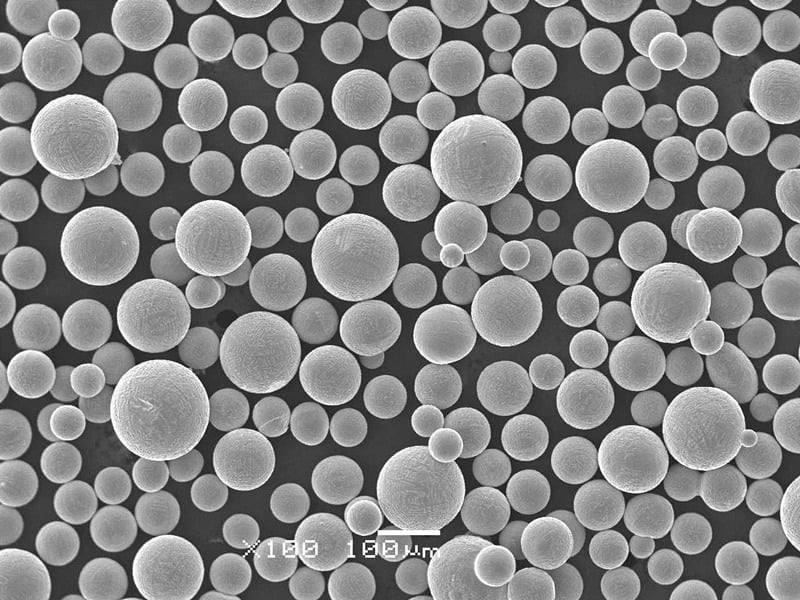
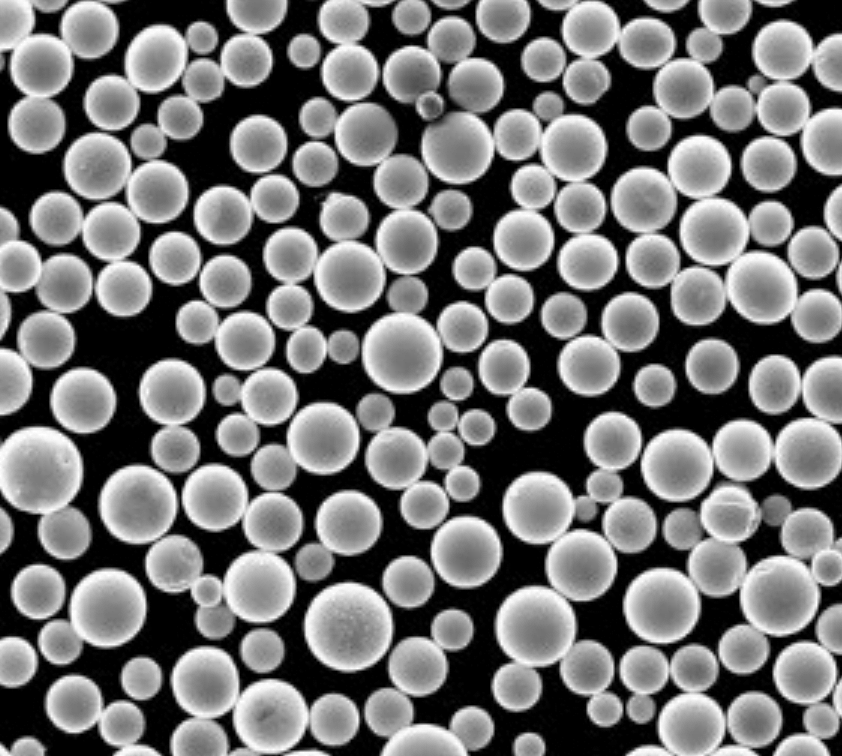
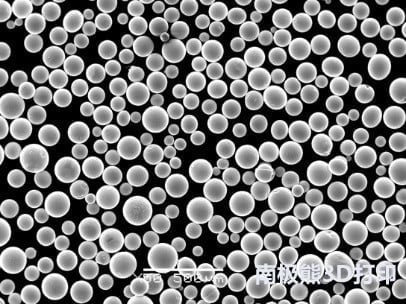
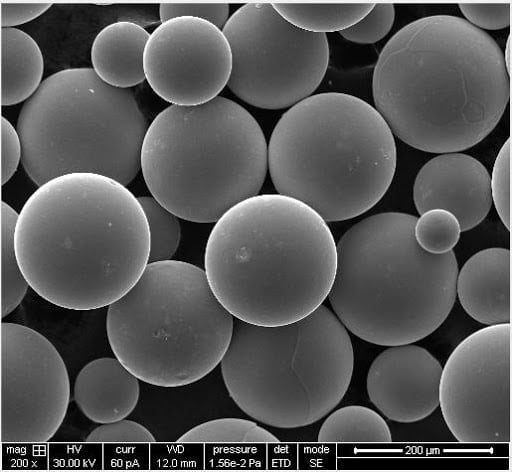
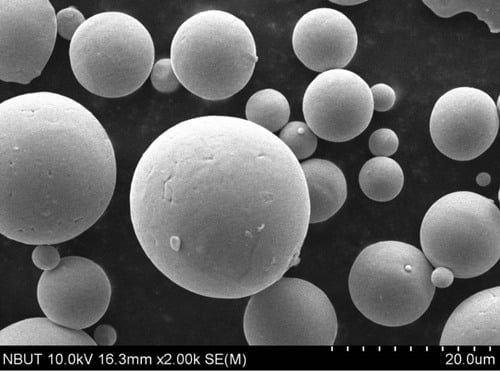
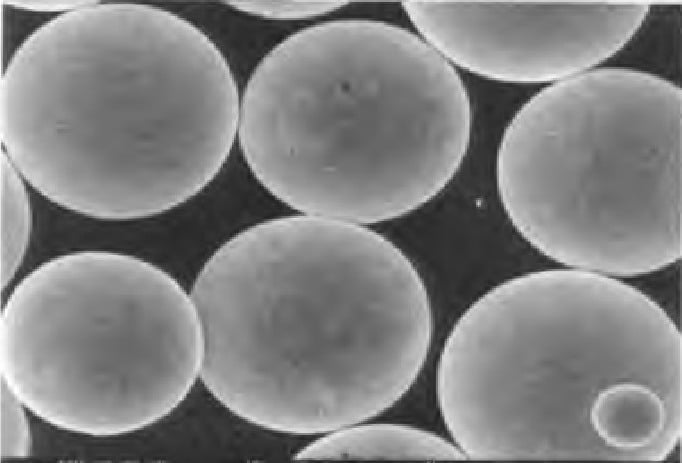
Disadvantages of Electron Beam Additive Manufacturing
While EBAM offers numerous benefits, it’s essential to acknowledge its limitations:
- Higher Initial Investment: EBAM systems are generally more expensive than other metal additive manufacturing technologies. The high upfront cost can be a barrier for entry for some companies.
- Limited Build Size: Current EBAM systems typically have smaller build volumes compared to some other additive manufacturing technologies. This restricts the size of parts that can be manufactured using EBAM.
- Surface Roughness: While EBAM offers good surface finish, it might not be as smooth as parts produced by LPBF. This can be a factor to consider depending on the application’s specific requirements.
- Support Structures: Some EBAM builds may require intricate support structures to prevent warping and distortion. Removing these supports can be a time-consuming process and can add to the overall production time and cost. Additionally, support removal can leave marks on the surface, requiring additional finishing steps.
- Process Control: EBAM requires careful process control to ensure consistent part quality. Factors like beam power, scan speed, and powder layer thickness need to be precisely monitored and controlled to achieve optimal results. This necessitates skilled operators and robust quality control procedures.
- Limited Color Options: Unlike some polymer additive manufacturing technologies, EBAM is currently limited in terms of producing parts with a wide range of colors. This might be a consideration for certain aesthetic or functional applications.
Despite these limitations, EBAM’s advantages often outweigh the drawbacks for many applications. As the technology matures and becomes more cost-effective, its adoption is expected to continue to grow across various industries.
Applications of Electron Beam Additive Manufacturing
EBAM’s unique capabilities make it a powerful tool for a diverse range of applications:
- Aerospace: The ability to create lightweight, high-strength components with complex geometries makes EBAM ideal for aerospace applications. Parts like turbine blades, rocket engine components, and aircraft structural components can benefit from EBAM’s precision and material properties.
- Medical Implants: The biocompatible nature of certain metal powders, coupled with EBAM’s ability to create intricate structures, make it suitable for manufacturing customized medical implants like joint replacements, dental prosthetics, and cranial implants.
- Automotive: EBAM is increasingly being explored in the automotive industry for producing lightweight components with high strength-to-weight ratios. This can contribute to improved fuel efficiency and performance.
- Energy Sector: EBAM is used to manufacture components for power generation equipment, such as turbine blades and heat exchangers. The technology’s ability to handle high-performance alloys makes it valuable for demanding energy applications.
- Tooling and Molds: EBAM is used to create complex molds and tooling inserts with intricate cooling channels, enabling efficient and high-quality production of plastic parts.
- Defense and Security: EBAM is utilized to manufacture components for defense applications where high strength, lightweight design, and material performance are critical.
The potential applications of EBAM are constantly expanding as the technology evolves and new materials are developed.
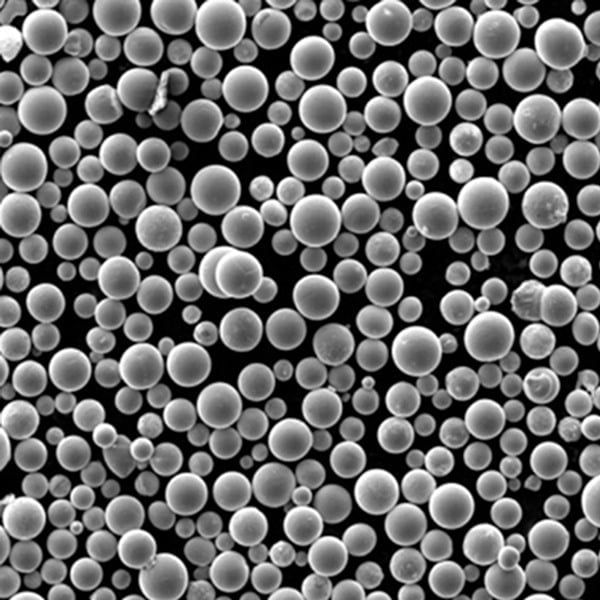
Specifications, Sizes, Grades, and Standards for EBAM
Metal Powder Specifications:
EBAM metal powders need to meet specific requirements for particle size distribution, flowability, and chemical composition to ensure optimal performance during the build process. Standard powder particle sizes for EBAM typically range from 20 to 150 microns.
Build Sizes:
Current EBAM systems offer varying build volumes depending on the manufacturer and model. Build volumes can range from a few cubic centimeters to several cubic meters. The selection of an EBAM system with an adequate build volume is crucial for the parts you intend to manufacture.
Material Grades:
A wide range of metal powder grades are available for EBAM, catering to diverse application needs. Common grades include commercially pure (CP), wrought grades, and special purpose alloys. The specific grade chosen will depend on the desired mechanical properties, corrosion resistance, and other performance requirements.
Standards:
Several industry standards govern the use of EBAM for specific applications. These standards define requirements for materials, processes, and quality control procedures to ensure the safety and reliability of additively manufactured parts. Some relevant standards include ASTM F4224 for Additive Manufacturing of Aerospace and Defense Parts and ASTM F2980 for Additive Manufacturing with Metal Powder.
Suppliers and Pricing of EBAM Systems and Metal Powders
Several companies manufacture EBAM systems and metal powders. Here’s a glimpse into some of the key players:
- EBAM System Suppliers: Arcam EBM (GE Additive), Renishaw, SLM Solutions, EOS GmbH, Trumpf
- Metal Powder Suppliers: Höganäs AB, Carpenter Additive, AP Powder Company, LPW Powder Products, Aubert & Duval
Pricing:
The cost of EBAM systems varies depending on the build volume, capabilities, and brand. Generally, EBAM systems are more expensive compared to other metal additive manufacturing technologies. Metal powder prices also fluctuate based on the material type, grade, and market conditions.
For the latest pricing information, it’s recommended to contact EBAM system and metal powder suppliers directly.
EBAM vs. Other Metal Additive Manufacturing Technologies
When considering metal additive manufacturing, it’s crucial to compare EBAM with other prominent technologies like Laser Powder Bed Fusion (LPBF) to determine the most suitable option for your needs. Here’s a breakdown of some key differences:
Feature | EBAM | LPBF |
---|---|---|
Energy Source | Electron Beam | Laser Beam |
Vacuum Environment | Yes | Yes (Inert Gas) |
Melting Depth | Deeper Melt Pool | Shallower Melt Pool |
Surface Finish | Slightly Rougher | Smoother |
Build Speed | Generally Faster | Can be Faster for Some Applications |
Material Compatibility | Wider Range, Including Reactive Metals | Limited to Laser-Absorptive Materials |
Cost | Generally Higher Initial Investment | Lower Initial Investment |
Build Size | Currently Limited Build Volumes | Larger Build Volumes Available |
Choosing between EBAM and LPBF depends on your specific needs.
- If high precision, surface finish, and intricate details are paramount, LPBF might be a better choice.
- If you require the ability to work with a wider range of materials, including reactive metals, or need exceptional mechanical properties, EBAM is a strong contender.
- For applications demanding high-strength, lightweight components and where build speed is a factor, EBAM could be a better fit.
Ultimately, the optimal technology selection hinges on a careful evaluation of your project requirements, budget constraints, and desired part characteristics.
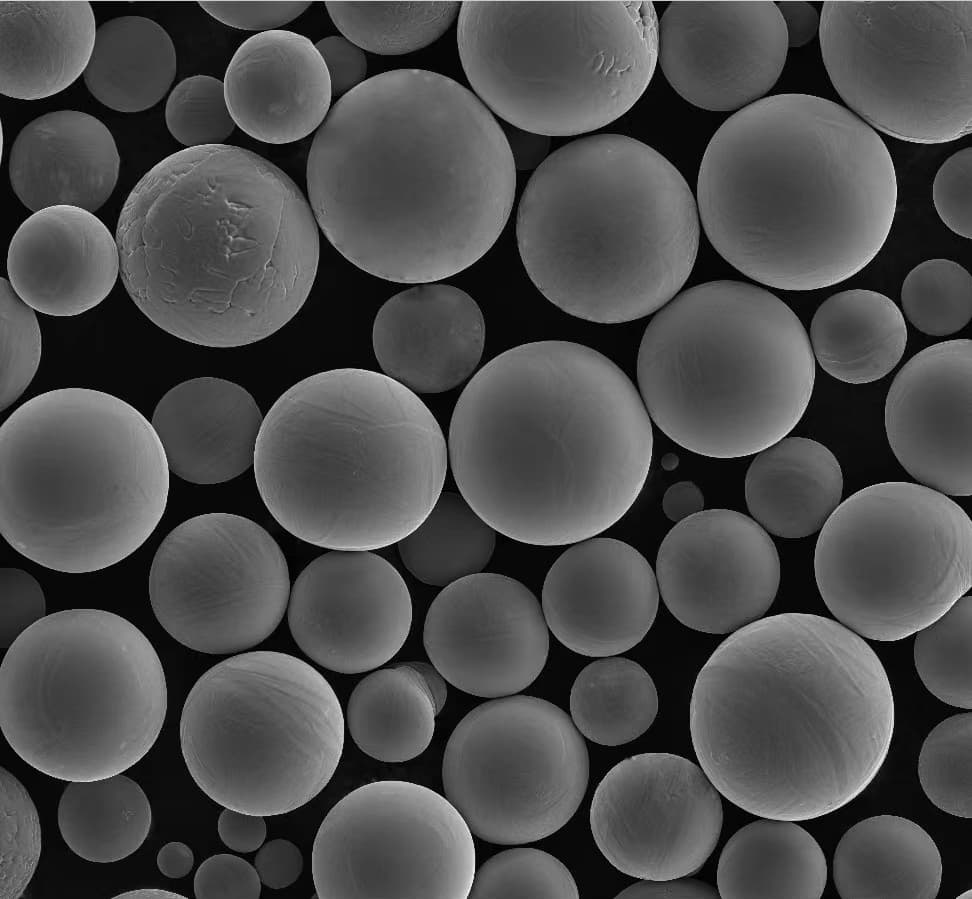
FAQ
1. What are the advantages of EBAM over traditional manufacturing methods?
EBAM offers several advantages over traditional methods like machining and casting. These include:
- Design freedom for complex geometries
- Minimal material waste
- Near-net-shape manufacturing
- Superior mechanical properties
- Lightweighting potential
2. What are some limitations of EBAM?
- Higher initial investment
- Limited build size (currently)
- Slightly rougher surface finish compared to LPBF
- Need for support structures, which can add to cost and complexity
3. What types of metal powders can be used in EBAM?
A wide range of metal powders can be used in EBAM, including:
- Titanium alloys (Ti6Al4V, Grade 5)
- Stainless steels (316L)
- Nickel-based superalloys (Inconel 625, 718)
- Cobalt Chrome (CoCr)
- Aluminum alloys (AlSi10Mg)
- Copper
- Refractory metals (tungsten, molybdenum)
4. What are some applications of EBAM?
EBAM finds applications in various industries, including:
- Aerospace (turbine blades, engine components)
- Medical implants (joint replacements, dental prosthetics)
- Automotive (lightweight components)
- Energy sector (turbine blades, heat exchangers)
- Tooling and molds
- Defense and security
5. How does EBAM compare to Laser Powder Bed Fusion (LPBF)?
Both EBAM and LPBF are metal additive manufacturing technologies. Here’s a quick comparison:
- EBAM: Utilizes electron beam, wider range of materials, deeper melt pool, generally faster build speed, higher initial cost.
- LPBF: Uses laser beam, smoother surface finish, larger build volumes available, lower initial cost.
The best choice depends on your specific project requirements.
6. Is EBAM a sustainable manufacturing process?
EBAM offers some sustainability benefits compared to traditional methods. It minimizes material waste through its powder-bed approach and allows for near-net-shape manufacturing, reducing the need for extensive post-processing. However, the energy consumption during the EBAM process needs to be considered for a complete sustainability assessment.
7. What is the future of EBAM?
EBAM is a rapidly evolving technology. Advancements in machine technology, powder development, and process control are expected to improve build speeds, part quality, and affordability. This will likely lead to wider adoption of EBAM across various industries.
About 3DP mETAL
Product Category
CONTACT US
Any questions? Send us a message now! After receiving your message, we will process your request with a whole team.