Overview
Electron Beam Additive Manufacturing (EBAM) is an advanced 3D printing technology that uses an electron beam to melt and fuse metal powder layer by layer to create complex and high-strength metal parts. This technology is particularly suited for the aerospace, defense, and automotive industries due to its ability to produce large, high-quality components with intricate geometries.
EBAM stands out because of its speed, precision, and the superior mechanical properties of the parts it produces. Unlike traditional manufacturing methods, EBAM reduces material waste and allows for the creation of parts with complex internal structures that would be impossible or very costly to produce using conventional techniques.
Key Features of EBAM:
- High Precision: EBAM can achieve extremely fine resolutions, allowing for detailed and complex designs.
- Material Efficiency: Significantly reduces waste by using only the material needed for the part.
- Strength and Durability: Produces parts with excellent mechanical properties.
- Speed: Faster production times compared to traditional manufacturing methods.
- Versatility: Capable of using a wide range of metal powders.
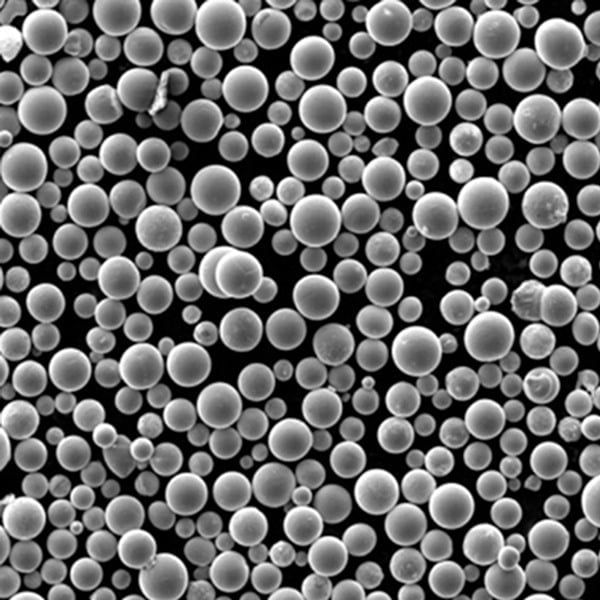
Composition of Electron Beam Additive Manufacturing (EBAM)
EBAM utilizes various metal powders, each with unique compositions that contribute to the specific properties of the final product. Below is a detailed description of some commonly used metal powders in EBAM.
Metal Powder | Composition | Properties | Applications |
---|---|---|---|
Titanium Alloy (Ti-6Al-4V) | Titanium, Aluminum, Vanadium | High strength, low weight, corrosion resistance | Aerospace, biomedical implants |
Inconel 718 | Nickel, Chromium, Iron, Molybdenum | High temperature resistance, corrosion resistance | Jet engines, gas turbines |
Stainless Steel 316L | Iron, Chromium, Nickel, Molybdenum | Corrosion resistance, good mechanical properties | Medical devices, marine applications |
Aluminum Alloy (AlSi10Mg) | Aluminum, Silicon, Magnesium | Lightweight, good thermal properties | Automotive, aerospace |
Copper Alloy (CuCr1Zr) | Copper, Chromium, Zirconium | Excellent electrical conductivity, high strength | Electrical components, heat exchangers |
Maraging Steel | Iron, Nickel, Cobalt, Molybdenum | Ultra-high strength, toughness | Tooling, aerospace components |
Tool Steel (H13) | Iron, Chromium, Molybdenum, Vanadium | High wear resistance, toughness | Molds, dies, cutting tools |
Cobalt-Chrome Alloy | Cobalt, Chromium, Molybdenum | Wear resistance, biocompatibility | Dental implants, orthopedic devices |
Nickel Alloy (Invar 36) | Nickel, Iron | Low thermal expansion, high stability | Precision instruments, aerospace |
Tantalum Alloy | Tantalum | High melting point, corrosion resistance | Chemical processing, medical implants |
Characteristics of Electron Beam Additive Manufacturing (EBAM)
The characteristics of EBAM define its suitability for various applications and industries. Below is a table summarizing these characteristics.
Characteristic | Description |
---|---|
Resolution | EBAM can achieve resolutions as fine as 100 microns, allowing for intricate designs. |
Build Volume | Capable of producing parts up to several meters in size, suitable for large components. |
Build Rate | High build rates due to the powerful electron beam, reducing production time. |
Material Variety | Supports a wide range of metal powders, providing flexibility in material choice. |
Surface Finish | Parts typically require post-processing to achieve a smooth surface finish. |
Mechanical Properties | Produces parts with excellent mechanical properties, often superior to those made by traditional methods. |
Energy Efficiency | Uses high energy from the electron beam, which is efficiently utilized in the melting process. |
Complex Geometry | Capable of creating complex internal structures and geometries. |
Minimal Waste | Reduces material waste significantly compared to subtractive manufacturing. |
Applications of Electron Beam Additive Manufacturing (EBAM)
EBAM has a wide range of applications across various industries due to its ability to produce high-quality, complex metal parts. Here are some notable applications:
Industry | Application |
---|---|
Aerospace | Jet engine components, structural parts, turbine blades |
Automotive | Lightweight components, custom parts, high-performance parts |
Medical | Implants, prosthetics, surgical tools |
Defense | Weapon components, military vehicle parts |
Energy | Turbine components, heat exchangers, power plant parts |
Industrial | Tooling, molds, and dies, custom machinery parts |
Marine | Propellers, ship components, underwater equipment |
Electronics | Heat sinks, conductive components, customized electronic parts |
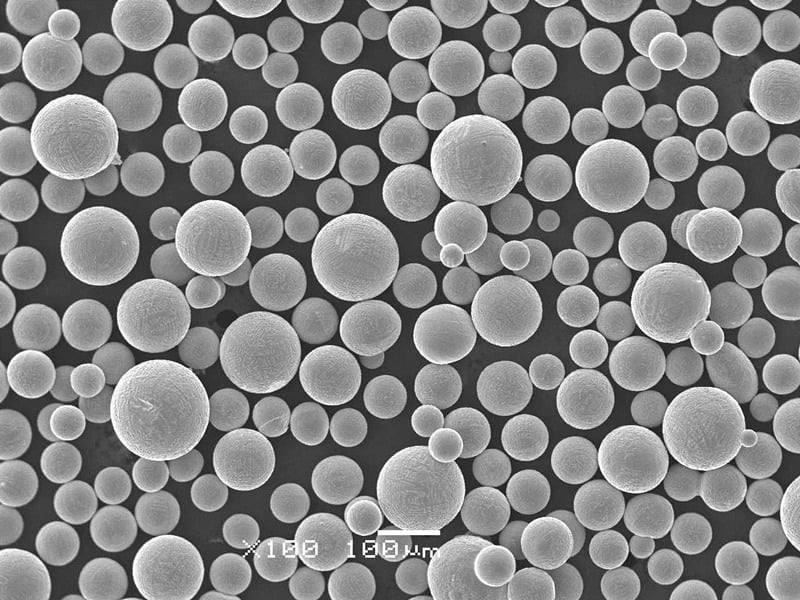
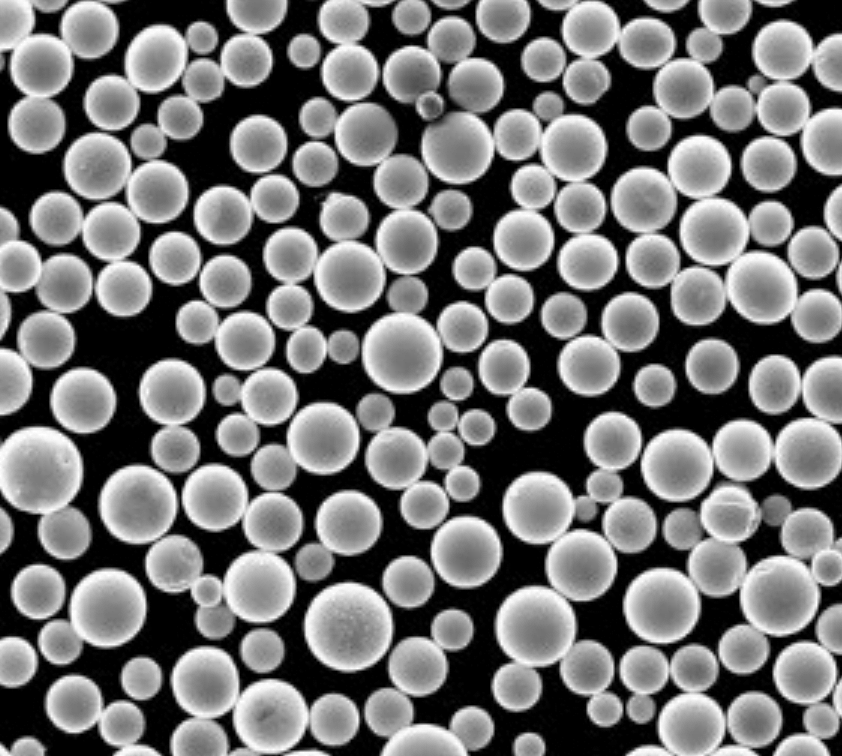
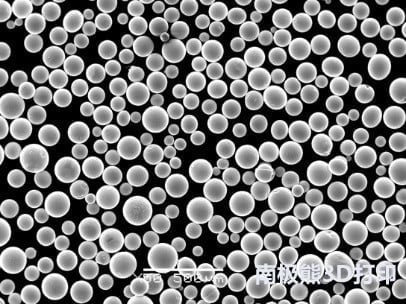
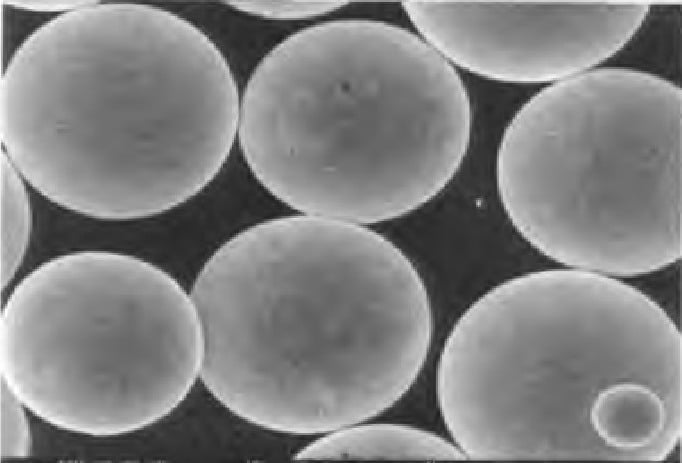
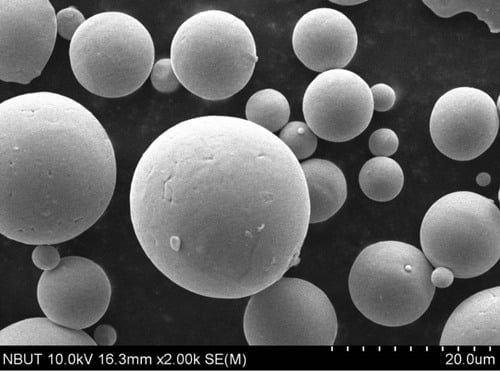
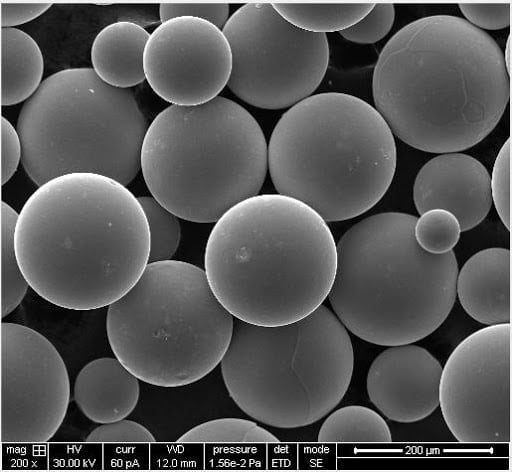
Specifications, Sizes, Grades, and Standards of EBAM
Understanding the specifications, sizes, grades, and standards of EBAM is crucial for selecting the right material and process for a specific application. Here’s a detailed overview:
Specification | Detail |
---|---|
Build Volume | Up to several meters in length and width |
Layer Thickness | Typically ranges from 50 to 200 microns |
Electron Beam Power | Up to 10 kW, depending on the machine |
Material Feedstock | Metal powders with particle sizes between 45 to 106 microns |
Grades | Various grades available based on metal type (e.g., Ti-6Al-4V Grade 5, Inconel 718, Stainless Steel 316L) |
Standards | ASTM F3001 (Titanium alloys), ASTM F3055 (Nickel alloys), ISO 10993 (Biocompatibility for medical applications) |
Suppliers and Pricing Details of EBAM
Choosing the right supplier is critical for obtaining quality materials and services. Below is a list of some prominent suppliers along with pricing details.
Supplier | Metal Powders Offered | Price Range (per kg) | Additional Services |
---|---|---|---|
Arcam AB (GE Additive) | Titanium alloys, Inconel, Stainless steel | $300 – $700 | Custom powder blends, technical support |
GKN Additive | Titanium, Aluminum, Tool steel, Nickel alloys | $200 – $600 | Design assistance, post-processing |
Höganäs AB | Stainless steel, Copper, Tool steel, Nickel alloys | $150 – $500 | Material development, application support |
LPW Technology | Cobalt-Chrome, Inconel, Maraging steel | $250 – $800 | Powder lifecycle management, quality assurance |
Sandvik Additive Manufacturing | Titanium, Stainless steel, Nickel alloys | $200 – $650 | Advanced materials, powder customization |
Carpenter Additive | Titanium, Aluminum, Stainless steel | $250 – $700 | Material certification, R&D support |
EOS GmbH | Aluminum, Nickel alloys, Tool steel | $200 – $600 | Technical consulting, training services |
Tekna Plasma Systems | Titanium, Nickel alloys, Stainless steel | $300 – $750 | Powder development, application engineering |
3D Systems | Titanium, Aluminum, Tool steel | $250 – $700 | Application development, material expertise |
Aperam | Stainless steel, Nickel alloys, Cobalt-Chrome | $200 – $650 | Custom alloy development, technical services |
Advantages and Limitations of Electron Beam Additive Manufacturing (EBAM)
Like any technology, EBAM has its pros and cons. Understanding these can help in making an informed decision about its application.
Advantages | Limitations |
---|---|
High Precision | Surface Finish: Often requires post-processing for smooth finishes. |
Material Efficiency | Equipment Cost: High initial investment for machinery. |
Strong Mechanical Properties | Material Availability: Limited to specific metal powders. |
Large Build Volume | Energy Consumption: High energy usage during operation. |
Complex Geometries | Operational Expertise: Requires skilled operators and maintenance. |
Reduced Waste | Build Speed: While faster than traditional methods, still slower than some other 3D printing technologies. |
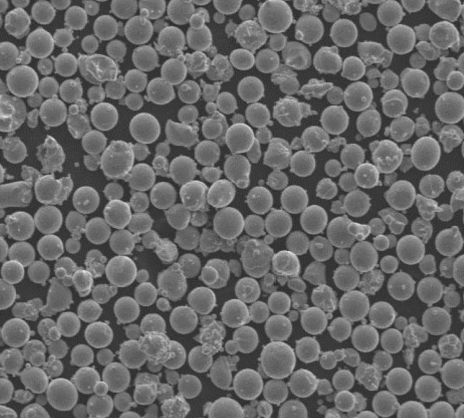
FAQ
Question | Answer |
---|---|
What is EBAM? | Electron Beam Additive Manufacturing (EBAM) is a 3D printing technology that uses an electron beam to melt and fuse metal powders layer by layer. |
What metals can be used in EBAM? | Common metals include Titanium alloys, Inconel, Stainless steel, Aluminum alloys, Copper alloys, Maraging steel, Tool steel, Cobalt-Chrome, Nickel alloys, and Tantalum alloys. |
What are the advantages of EBAM? | High precision, reduced material waste, strong mechanical properties, large build volume, and the ability to create complex geometries. |
What industries use EBAM? | Aerospace, automotive, medical, defense, energy, industrial, marine, and electronics industries. |
How does EBAM compare to other 3D printing methods? | EBAM offers superior material properties and build volumes but requires more energy and higher initial costs compared to other methods like SLM or DMLS. |
What post-processing is needed for EBAM parts? | Typically includes surface finishing, heat treatment, and machining to achieve desired tolerances and surface qualities. |
How does the electron beam work in EBAM? | The electron beam is generated by an electron gun and directed onto the metal powder bed, where it melts and fuses the powder into a solid layer. |
Conclusion
Electron Beam Additive Manufacturing (EBAM) represents a significant advancement in the field of 3D printing and metal manufacturing. With its ability to produce high-quality, complex parts with excellent mechanical properties, EBAM is revolutionizing industries from aerospace to medical. While it comes with challenges such as high costs and energy consumption, the benefits it offers in terms of precision, material efficiency, and design flexibility make it a compelling choice for advanced manufacturing needs.
Whether you’re a manufacturer looking to produce custom parts or an engineer exploring new materials and designs, EBAM opens up a world of possibilities, pushing the boundaries of what can be achieved with metal additive manufacturing.
About 3DP mETAL
Product Category
CONTACT US
Any questions? Send us a message now! After receiving your message, we will process your request with a whole team.