Inconel powder, a superhero material in the realm of 3D printing, stands out for its exceptional strength, heat resistance, and corrosion defiance. Imagine crafting intricate components that can withstand scorching temperatures, relentless wear, and harsh environments – that’s the magic of Inconel powder. But delve deeper, and you’ll discover a universe of complexities and variations within this wonder material. This comprehensive guide unravels the secrets of Inconel powder, empowering you to make informed decisions for your next 3D printing project.
the Essence of Inconel Polvo
At its core, Inconel powder is a meticulously crafted metal dust composed of nickel-based superalloys. These alloys are a potent blend of nickel, chromium, and other strengthening elements, resulting in a material that laughs in the face of extreme conditions. The magic lies in the intricate dance between its composition and the creation process. Through various techniques like gas atomization, the molten metal is transformed into a fine powder, each particle boasting a near-perfect spherical shape. This meticulous design ensures smooth flow during the 3D printing process, enabling the creation of intricate and robust structures.
Common Alloy Compositions of Inconel Powder:
Aleación | Composición | Características principales |
---|---|---|
Inconel 625 | Nickel (Ni) – Base, Chromium (Cr) – 20-25%, Molybdenum (Mo) – 5%, Iron (Fe) – 5% | Exceptional resistance to various corrosive environments, particularly acidic media. |
Inconel 718 | Nickel (Ni) – Base, Chromium (Cr) – 17-21%, Molybdenum (Mo) – 2.8-3.3%, Niobium (Nb) + Tantalum (Ta) – 5.1%, Aluminum (Al) – 0.7-1.2% | Unbeatable combination of high strength, excellent weldability, and good resistance to high temperatures and various corrosive media. |
Inconel 600 | Nickel (Ni) – Base, Chromium (Cr) – 15-20%, Iron (Fe) – 7-12% | Renowned for its outstanding resistance to oxidation and high-temperature environments. |
Inconel 93K | Nickel (Ni) – Base, Cobalt (Co) – 13-17%, Chromium (Cr) – 19-23%, Tungsten (W) – 1.5-2.5% | Unbeaten champion in strength and resistance to high temperatures, making it ideal for aerospace applications. |
Inconel X-750 | Nickel (Ni) – Base, Chromium (Cr) – 17-20%, Iron (Fe) – 6.5-8.5%, Titanium (Ti) – 2.5-3.5% | Offers a compelling balance between strength, oxidation resistance, and fabricability. |
Additional Elements: Manganese (Mn), Silicon (Si), Sulfur (S), Carbon (C), Copper (Cu) are often included in small quantities to refine specific properties.
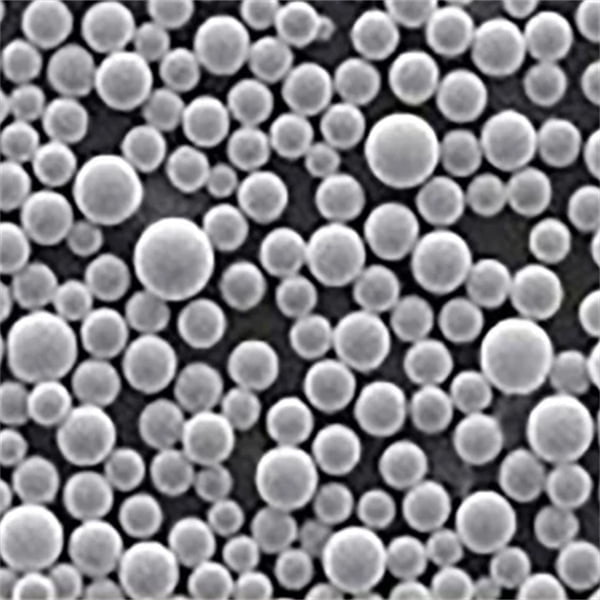
the Applications of Inconel Polvo
Inconel powder’s exceptional properties unlock a treasure trove of applications across various industries. Let’s explore some of the most prominent:
Industria aeroespacial: Soaring to new heights, Inconel powder crafts components that can withstand the searing heat of jet engines and the harsh environment of space. Think turbine blades, rocket nozzles, and heat exchangers – all benefiting from Inconel powder’s resilience.
Procesamiento químico: In the face of aggressive chemicals, Inconel powder stands strong. Reaction vessels, valves, and pipes crafted from this material can endure the relentless assault of corrosive fluids.
Oil and Gas Industry: Drilling deep into the earth’s core demands exceptional materials. Inconel powder delivers, used in components like downhole tools and wellhead equipment that can handle the extreme pressures and temperatures encountered.
Generación de Energía: From the heart of power plants to the intricate components of gas turbines, Inconel powder plays a vital role. Its ability to withstand high temperatures and resist corrosion ensures smooth and efficient power generation.
Productos sanitarios: When biocompatibility meets exceptional strength, the result is groundbreaking medical implants. Inconel powder can be used to create prosthetics, surgical instruments, and other medical devices that can endure the rigors of the human body.
These are just a few examples, and the potential applications of Inconel powder continue to expand as 3D printing technology evolves.
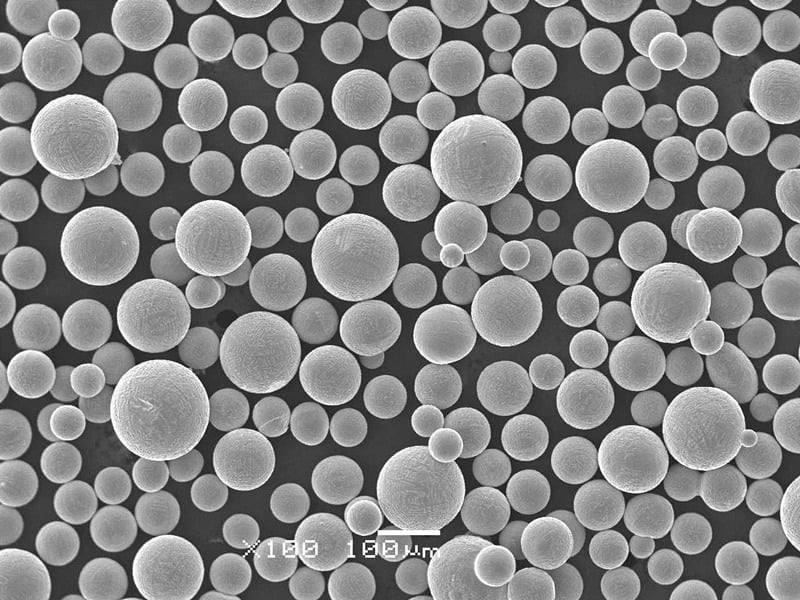
the Specifications of Inconel Polvo
The properties of Inconel powder vary depending on the specific alloy composition, particle size, and manufacturing process. Here’s a deeper dive into the nitty-gritty details:
Tamaño y distribución de partículas:
The size and distribution of Inconel powder particles significantly impact the quality and properties of the final 3D printed part. Generally, finer powders (in the range of 15-45 microns) produce smoother surfaces and intricate details, but they can also be more challenging to flow freely during the printing process. Conversely, coarser powders (45-100 microns) offer better flow characteristics but might result in a slightly rougher surface finish. The ideal particle size depends on the specific 3D printing technology and the desired outcome.
Forma esférica:
As mentioned earlier, the near-perfect spherical shape of Inconel powder particles is crucial for optimal performance. This shape ensures consistent flow during printing, minimizes voids within the finished product, and contributes to its overall strength.
Fluidez:
Flowability refers to the ease with which powder particles move and pack together. Good flowability is essential for achieving a uniform and dense layer during the 3D printing process. Factors like particle size distribution, surface texture, and moisture content can all influence flowability.
Densidad aparente:
Apparent density refers to the weight of powder per unit volume, taking into account the spaces between particles. It’s a crucial parameter for determining the amount of powder needed for a specific 3D printing job. The apparent density of Inconel powder can vary depending on the alloy composition and particle size.
Composición química:
As discussed previously, the specific alloy composition of Inconel powder dictates its mechanical properties, corrosion resistance, and other characteristics. Strict adherence to industry standards like ASTM International (ASTM) specifications ensures consistent material performance.
Normas y certificaciones:
Inconel powder manufacturers adhere to various industry standards to ensure consistent quality and performance. Some of the most common standards include:
- ASTM B163 – Standard Specification for Nickel Alloy Strip, Sheet, and Plate
- ASTM B939 – Standard Test Method for Powder Flowability of Metal Powders Using a Hall Flowmeter
- AMS (Aerospace Material Specifications) standards set by SAE International
Precios:
The cost of Inconel powder can vary depending on several factors, including:
- Composición de la aleación: More complex alloys with higher performance characteristics typically command a higher price.
- Tamaño de las partículas: Finer powders often involve a more intricate manufacturing process, leading to a slightly higher cost.
- Cantidad: Bulk purchases typically benefit from economies of scale, resulting in a lower price per unit weight.
- Proveedor: Market competition and individual supplier pricing strategies can influence the final cost.
Here’s a table summarizing some key specifications of commonly used Inconel powders:
Especificación | Descripción |
---|---|
Distribución de granulometría | Typically ranges from 15-100 microns, with specific choices impacting surface finish and flowability. |
Forma esférica | Ideally close to perfect spheres for optimal flow and minimal voids. |
Fluidez | Crucial for achieving uniform layers during printing; influenced by particle size, shape, and moisture content. |
Densidad aparente | Weight of powder per unit volume, considering spaces between particles; affects the amount of powder needed for printing. |
Composición química | Specific alloy composition dictates mechanical properties, corrosion resistance, etc.; adheres to standards like ASTM. |
Standards and Certifications | Conforms to industry standards like ASTM B163 and AMS for consistent quality. |
Precios | Varies based on alloy, particle size, quantity, and supplier; generally higher for complex alloys and finer powders. |
Remember, this table provides a general overview. Consulting with a reputable Inconel powder supplier is vital to obtain the most up-to-date specifications and pricing information for your specific needs.
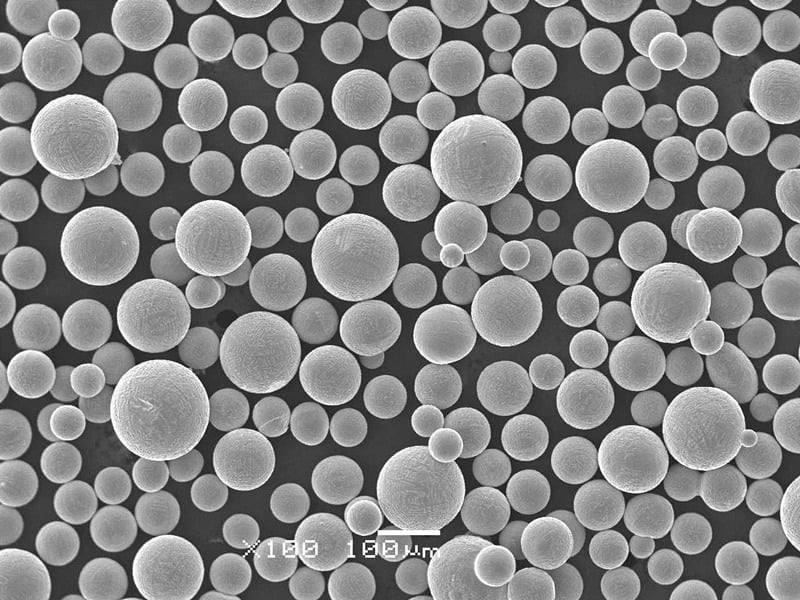
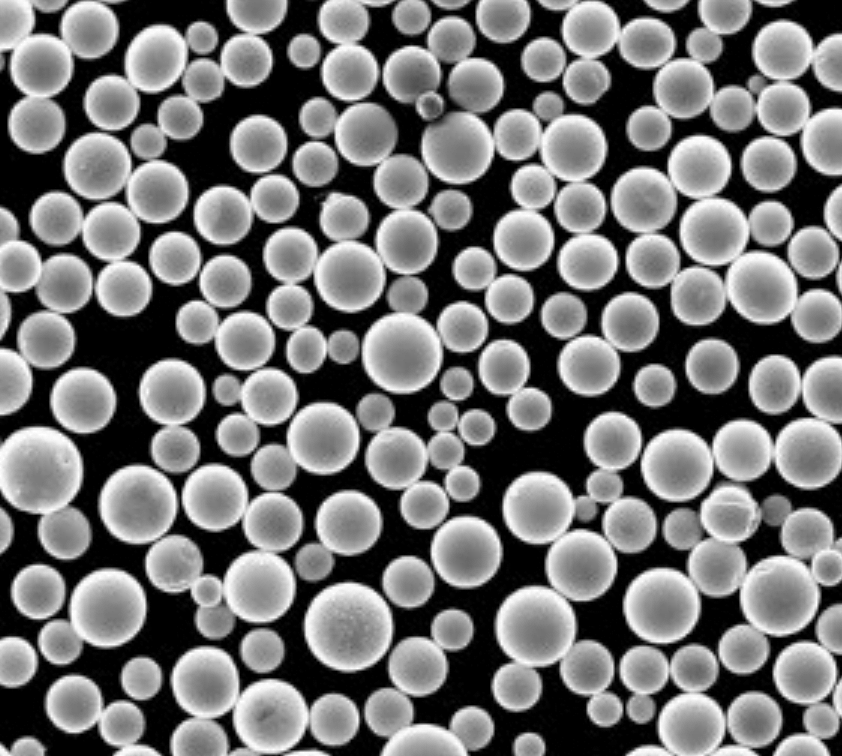
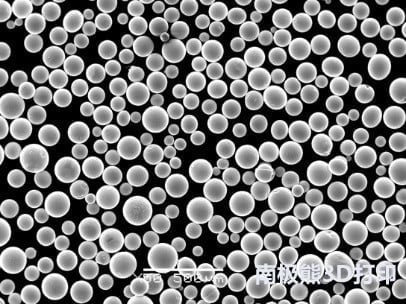
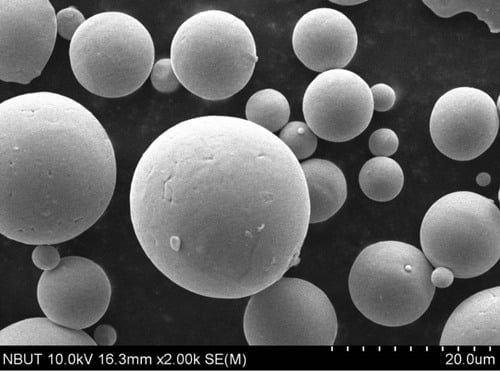
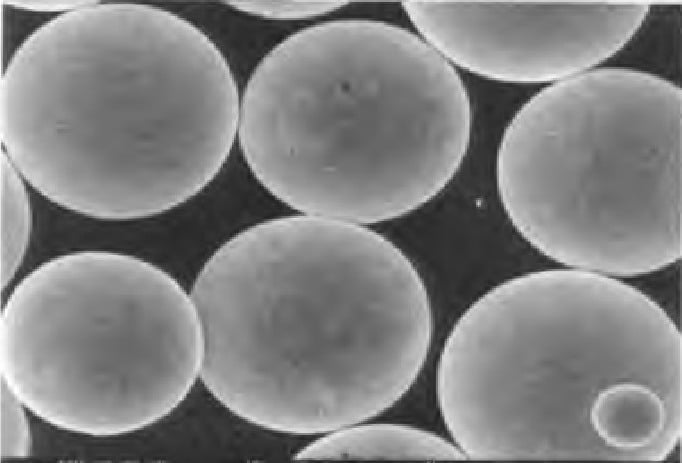
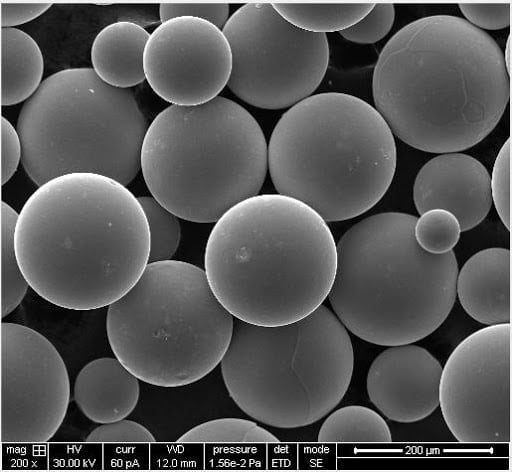
Advantages and Limitations of Inconel Powder
Like any material, Inconel powder boasts a unique set of advantages and limitations. Understanding these aspects is crucial for making informed decisions about its suitability for your project.
Advantages of Inconel Powder:
- Fuerza excepcional: Inconel powder delivers outstanding strength at elevated temperatures, making it ideal for demanding applications.
- Resistencia superior a la corrosión: Many Inconel powder variants boast exceptional resistance to a wide range of corrosive environments, ensuring long-lasting performance.
- Rendimiento a altas temperaturas: Inconel powder retains its strength and structural integrity even at scorching temperatures, making it perfect for applications like jet engines and power generation.
- Flexibilidad de diseño: 3D printing technology unlocks a world of design possibilities with Inconel powder. Complex geometries and intricate components become achievable.
- Potencial ligero: Compared to traditional manufacturing methods, 3D printing with Inconel powder can result in lighter components. This translates to weight savings in applications like aerospace and automotive, where every gram counts.
- Reducción de residuos: 3D printing with Inconel powder minimizes material waste compared to subtractive manufacturing techniques. This translates to cost savings and environmental benefits.
- Creación rápida de prototipos: The ability to create complex prototypes quickly with Inconel powder expedites the product development process.
Limitations of Inconel Powder:
- Coste elevado: Inconel powder itself is a relatively expensive material, and the 3D printing process can also add to the overall cost.
- Disponibilidad limitada: While availability is improving, Inconel powder might not be as readily available as some other 3D printing materials.
- Specialised Equipment: 3D printing with Inconel powder requires specialized equipment that can handle the high temperatures and abrasive nature of the material. This limits accessibility for some users.
- Requisitos de postprocesamiento: Inconel powder parts might require post-processing steps like heat treatment or hot isostatic pressing (HIP) to achieve optimal properties.
- Acabado superficial: While achievable with proper technique, achieving an exceptionally smooth surface finish with Inconel powder can be more challenging compared to some other 3D printing materials.
By carefully considering these advantages and limitations, you can make an informed decision about whether Inconel powder is the right material for your specific 3D printing project.
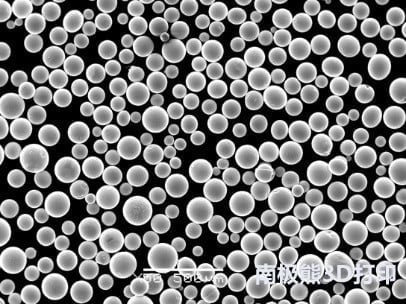
Preguntas frecuentes (FAQ)
Here are some of the most frequently asked questions regarding Inconel powder:
Q: What are the different types of Inconel powder available?
A: There are various Inconel powder variants, each with a unique blend of properties. Some of the most common include Inconel 625, Inconel 718, Inconel 600, Inconel 93K, and Inconel X-750. The ideal choice depends on the specific application requirements.
Q: Is Inconel powder safe to handle?
A: Inconel powder, like most metal powders, can pose health risks if inhaled. Proper safety precautions like using a fume hood and wearing appropriate personal protective equipment (PPE) are crucial during handling.
Q: Can Inconel powder be recycled?
A: Yes, Inconel powder can be recycled to a certain extent. The specific recycling process depends on the type of powder and the recycling facility’s capabilities.
Q: What are some alternative materials to Inconel powder?
A: Depending on the specific application requirements, alternative materials like stainless steel powder, titanium powder, or nickel alloy powders with different compositions might be considered.
Q: Where can I buy Inconel powder?
A: Several reputable suppliers offer Inconel powder. It’s essential to research and choose a supplier with a proven track record of quality and customer service.
Acerca de 3DP mETAL
Categoría de productos
CONTÁCTANOS
¿Tienes alguna pregunta? ¡Envíanos un mensaje ahora! Después de recibir tu mensaje, procesaremos tu solicitud con todo un equipo.