Deposición de metales por láser (LMD) es una tecnología de vanguardia que está revolucionando las industrias de fabricación y reparación. Imagine poder construir o reparar piezas metálicas con una precisión milimétrica, capa por capa, utilizando un láser. Suena futurista, ¿verdad? Pues no es sólo el futuro, sino que está sucediendo ahora mismo. Profundicemos en esta fascinante tecnología.
Descripción general del depósito de metales por láser (LMD)
La deposición metálica por láser (LMD), también conocida como deposición metálica directa (DMD), es un proceso de fabricación aditiva que utiliza un láser de alta potencia para fundir polvo o alambre metálico y depositarlo sobre un sustrato. Esta tecnología es fundamental para crear geometrías complejas, reparar componentes de gran valor y añadir características a piezas existentes.
Detalles clave:
- Proceso: Un rayo láser crea un baño de fusión en el sustrato por el que se introduce polvo o alambre metálico, formando una capa a medida que se solidifica.
- SOLICITUDES: Industrias aeroespacial, de automoción, de implantes médicos y de herramientas y matrices.
- Materiales: Diversos metales, incluidos titanio, acero inoxidable, cromo-cobalto e Inconel.
- Ventajas: Alta precisión, mínimo desperdicio y posibilidad de reparar componentes caros.
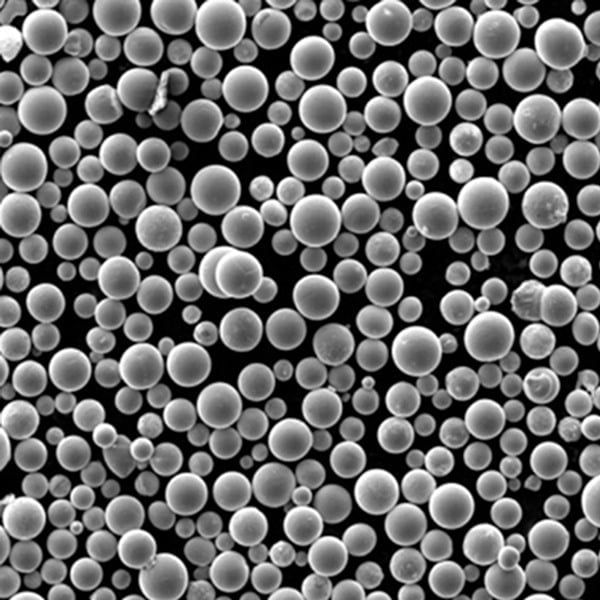
Tipos de polvos metálicos para el depósito de metales por láser
Polvos metálicos comunes utilizados en LMD
Polvo metálico | Composición | Propiedades | Características |
---|---|---|---|
Inconel 625 | Níquel-cromo | Alta resistencia a la corrosión y a la oxidación | Excelente soldabilidad, utilizado en entornos difíciles |
Titanio 6Al-4V | Titanio-Aluminio-Vanadio | Elevada relación resistencia/peso, resistencia a la corrosión | Ligero, biocompatible, utilizado en la industria aeroespacial |
Acero inoxidable 316L | Hierro-Cromo-Níquel | Alta resistencia a la corrosión, buena conformabilidad | Se utiliza en implantes médicos y aplicaciones marinas |
Cromo-cobalto | Cobalto-Cromo-Molibdeno | Gran resistencia al desgaste y a la corrosión | Se utiliza en implantes dentales y ortopédicos |
Aluminio AlSi10Mg | Aluminio-Silicio-Magnesio | Ligero, buenas propiedades térmicas | Utilizado en automoción, aeroespacial |
Cobre | Cobre puro | Excelente conductividad térmica y eléctrica | Utilizado en componentes eléctricos, intercambiadores de calor |
Níquel 718 | Níquel-Cromo-Hierro | Alta resistencia, excelente resistencia a la fatiga y a la fluencia | Se utiliza en turbinas de gas y en la industria aeroespacial |
Acero para herramientas H13 | Hierro-Carbono-Cromo | Gran tenacidad, resistencia al desgaste | Utilizado en la fabricación de herramientas y matrices |
Acero martensítico envejecido | Hierro-níquel-cobalto-molibdeno | Alta resistencia, buena tenacidad | Utilizado en la industria aeroespacial, utillaje |
Bronce CuSn10 | Cobre-Estaño | Buena resistencia al desgaste y a la corrosión | Se utiliza en aplicaciones artísticas, rodamientos de maquinaria |
Descripciones detalladas
- Inconel 625: Esta superaleación a base de níquel-cromo es conocida por sus excelentes propiedades frente a la fatiga y la fatiga térmica, así como por su resistencia a la oxidación y la corrosión. Se suele utilizar en aplicaciones aeroespaciales y marinas por su robustez en entornos extremos.
- Titanio 6Al-4V: Con una composición de titanio, aluminio y vanadio, esta aleación ofrece una relación fuerza-peso y una resistencia a la corrosión superiores, lo que la convierte en un elemento básico en la industria aeroespacial y los implantes médicos.
- Acero inoxidable 316L: Esta aleación de hierro, cromo y níquel es muy apreciada por su resistencia a la corrosión y su buena conformabilidad, lo que la hace ideal para aplicaciones marinas y médicas en las que la durabilidad es crucial.
- Cromo-cobalto: Conocido por su gran resistencia al desgaste y la corrosión, el cobalto-cromo se utiliza mucho en implantes dentales y ortopédicos por su biocompatibilidad y resistencia.
- Aluminio AlSi10Mg: Esta aleación ligera ofrece buenas propiedades térmicas y se utiliza en los sectores automovilístico y aeroespacial, donde es esencial reducir el peso sin comprometer la resistencia.
- Cobre: El cobre puro se utiliza en aplicaciones que requieren una excelente conductividad térmica y eléctrica, como componentes eléctricos e intercambiadores de calor.
- Níquel 718: Esta aleación de níquel, cromo y hierro, de excepcional solidez y resistencia a la fatiga y la fluencia, se utiliza habitualmente en turbinas de gas y aplicaciones aeroespaciales.
- Acero para herramientas H13: Conocido por su gran tenacidad y resistencia al desgaste, el acero para herramientas H13 es un material de referencia para la fabricación de herramientas y matrices.
- Acero martensítico envejecido: Esta aleación de alta resistencia y tenacidad se utiliza en la industria aeroespacial y de utillaje. Su composición incluye hierro, níquel, cobalto y molibdeno.
- Bronce CuSn10: Conocida por su resistencia al desgaste y la corrosión, esta aleación de cobre y estaño se utiliza en aplicaciones artísticas y cojinetes de maquinaria.
Composición de Deposición de metales por láser (LMD)
La composición de los materiales utilizados en LMD es crucial para conseguir las propiedades deseadas en el producto acabado. He aquí un análisis detallado:
Composición de los polvos metálicos LMD más comunes
Polvo metálico | Elementos primarios | Elementos adicionales | Usos típicos |
---|---|---|---|
Inconel 625 | Níquel, Cromo | Molibdeno, niobio | Industria aeroespacial, naval y química |
Titanio 6Al-4V | Titanio, aluminio | Vanadio | Aeroespacial, implantes médicos |
Acero inoxidable 316L | Hierro, Cromo | Níquel, molibdeno | Dispositivos médicos, aplicaciones marinas |
Cromo-cobalto | Cobalto, cromo | Molibdeno | Implantes dentales y ortopédicos |
Aluminio AlSi10Mg | Aluminio, Silicio | Magnesio | Automoción, aeroespacial |
Cobre | Cobre | Oxígeno | Componentes eléctricos, intercambiadores de calor |
Níquel 718 | Níquel, Cromo | Hierro, molibdeno, niobio | Turbinas de gas, aeroespacial |
Acero para herramientas H13 | Hierro, carbono | Cromo, molibdeno | Utillaje, matricería |
Acero martensítico envejecido | Hierro, níquel | Cobalto, molibdeno | Aeroespacial, utillaje |
Bronce CuSn10 | Cobre, estaño | Zinc | Aplicaciones artísticas, rodamientos de maquinaria |
Propiedades y características del depósito de metales por láser (LMD)
Propiedades clave
- Precisión: El LMD permite controlar con precisión el proceso de deposición, lo que se traduce en una gran exactitud a la hora de construir o reparar piezas.
- Eficiencia material: Los residuos generados son mínimos, ya que el proceso utiliza únicamente la cantidad de material necesaria.
- Versatilidad: Puede utilizarse una amplia gama de metales, incluidas las superaleaciones y los materiales biocompatibles.
- Resistencia mecánica: Los componentes fabricados con LMD suelen tener propiedades mecánicas que igualan o superan las de las piezas fabricadas tradicionalmente.
Características detalladas
Propiedad | Descripción |
---|---|
Precisión dimensional | Alta precisión en la creación de geometrías complejas |
Acabado superficial | Puede variar de suave a áspero en función de los parámetros y el postprocesado |
Microestructura | Típicamente de grano fino debido a la rápida solidificación |
Densidad | Se puede alcanzar una densidad casi total con parámetros óptimos |
Porosidad | Se puede conseguir una baja porosidad, crítica para las propiedades mecánicas |
Fuerza de adhesión | Fuertes uniones metalúrgicas entre las capas y el sustrato |
Resistencia a la corrosión | Depende del material; alto para aleaciones como acero inoxidable e Inconel |
Propiedades térmicas | Buena conductividad térmica para metales como el cobre; esencial para intercambiadores de calor |
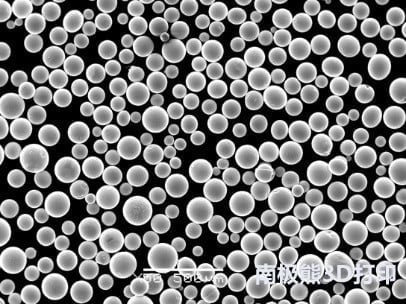
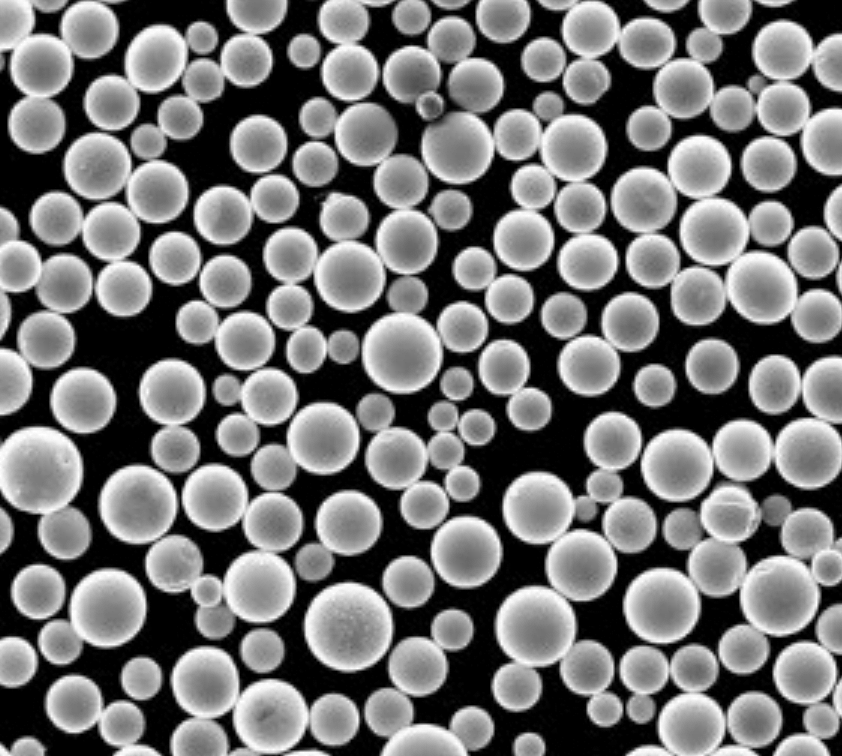
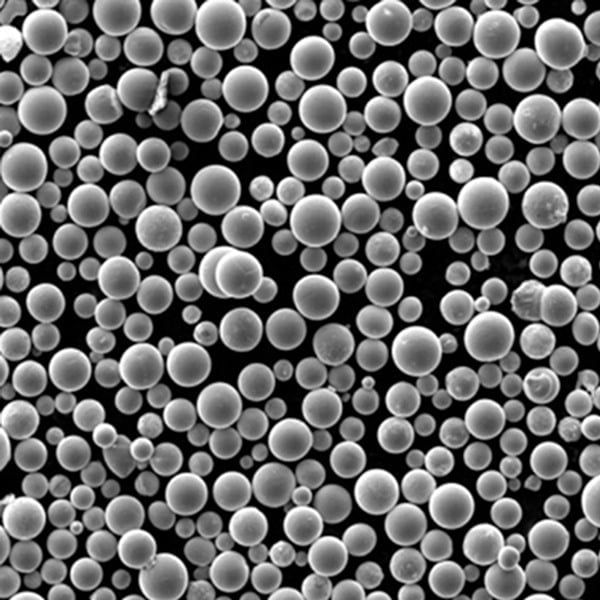
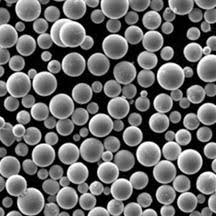
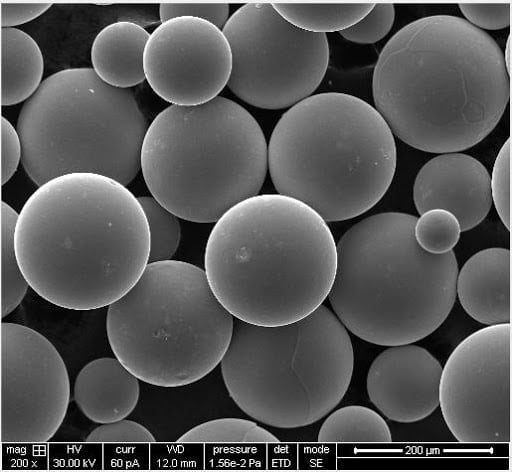
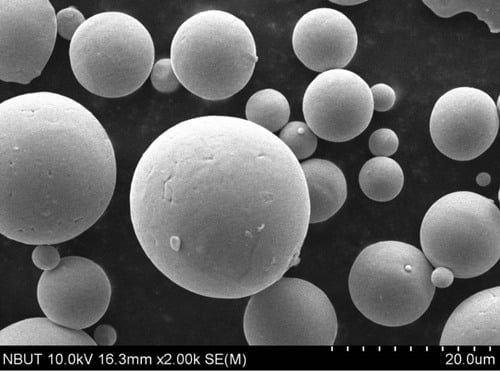
Aplicaciones de Deposición de metales por láser (LMD)
La tecnología LMD es versátil y encuentra aplicaciones en diversos sectores gracias a su capacidad para producir piezas complejas de alta calidad y reparar componentes caros.
Aplicaciones industriales
Industria | SOLICITUDES |
---|---|
Aeroespacial | Componentes de motor, piezas estructurales, reparación de álabes de turbina |
Automovilístico | Componentes ligeros, prototipos, reparación de herramientas |
Médico | Implantes a medida, restauraciones dentales, dispositivos ortopédicos |
Herramientas y troqueles | Reparación de moldes y matrices, fabricación de herramientas de corte |
Energía | Reparación de turbinas, intercambiadores de calor, componentes de reactores nucleares |
Defensa | Componentes de armas, reparación y mantenimiento de piezas críticas |
Casos prácticos
- Aeroespacial: La capacidad de reparar y fabricar componentes complejos de motores hace que LMD tenga un valor incalculable. Por ejemplo, los álabes de turbina, que funcionan en condiciones extremas, pueden repararse con un tiempo de inactividad mínimo.
- Automovilístico: El LMD se utiliza para fabricar componentes ligeros y de alta resistencia que mejoran la eficiencia del combustible y el rendimiento. También es excelente para crear prototipos y reparar herramientas.
- Médico: Los implantes y las restauraciones dentales a medida se elaboran con precisión, garantizando la biocompatibilidad y soluciones específicas para cada paciente.
- Herramientas y troqueles: La reparación de moldes y matrices mediante LMD prolonga su vida útil y reduce los costes de fabricación. También se fabrican herramientas de corte de alta precisión con esta tecnología.
Especificaciones, tamaños, calidades y normas
Especificaciones y normas para polvos metálicos LMD
Polvo metálico | Especificaciones | Tamaños (µm) | Grados | Normas |
---|---|---|---|---|
Inconel 625 | ASTM B443, AMS 5599 | 15-45, 45-106 | UNS N06625 | ASTM, AMS, ISO |
Titanio 6Al-4V | ASTM F1472, AMS 4928 | 15-45, 45-106 | 5.º grado | ASTM, AMS, ISO |
Acero inoxidable 316L | ASTM A240, AMS 5507 | 15-45, 45-106 | UNS S31603 | ASTM, AMS, ISO |
Cromo-cobalto | ASTM F75, ISO 5832-4 | 15-45, 45-106 | Aleación de CoCrMo | ASTM, ISO |
Aluminio AlSi10Mg | ASTM B209 | 15-45, 45-106 | AlSi10Mg | ASTM, ISO |
Cobre | ASTM B152 | 15-45, 45-106 | C11000 | ASTM, ISO |
Níquel 718 | ASTM B637, AMS 5663 | 15-45, 45-106 | UNS N07718 | ASTM, AMS, ISO |
Acero para herramientas H13 | ASTM A681, DIN 1.2344 | 15-45, 45-106 | H13 | ASTM, DIN |
Acero martensítico envejecido | ASTM A538 | 15-45, 45-106 | 18Ni(300) | ASTM, ISO |
Bronce CuSn10 | ASTM B505 | 15-45, 45-106 | UNS C90500 | ASTM, ISO |
Proveedores y precios
Proveedor | Polvos metálicos | Precio (por kg) | Ubicación | Póngase en contacto con |
---|---|---|---|---|
Höganäs | Inconel 625, Titanio 6Al-4V, Acero inoxidable 316L | $200 – $400 | Suecia | www.hoganas.com |
Tecnología LPW | Inconel 625, Níquel 718, Acero martensítico envejecido | $250 – $450 | Reino Unido | www.lpwtechnology.com |
Tecnología Carpenter | Acero para herramientas H13, acero inoxidable 316L | $220 – $380 | EE. UU. | www.carpentertechnology.com |
EOS GmbH | Cromo-cobalto, aluminio AlSi10Mg | $300 – $500 | Alemania | www.eos.info |
AP&C | Titanio 6Al-4V, Inconel 625 | $270 – $460 | Canadá | www.advancedpowders.com |
Oerlikon Metco | Cromo-cobalto, níquel 718 | $280 – $470 | Suiza | www.oerlikon.com/metco |
Sandvik | Acero inoxidable 316L, acero para herramientas H13 | $240 – $420 | Suecia | www.materials.sandvik |
Renishaw | Acero martensítico envejecido, aluminio AlSi10Mg | $260 – $440 | Reino Unido | www.renishaw.com |
Arcam AB | Titanio 6Al-4V, Cromo-cobalto | $280 – $460 | Suecia | www.arcam.com |
GKN Hoeganaes | Inconel 625, Acero inoxidable 316L | $230 – $410 | EE. UU. | www.gknpm.com |
Comparación de ventajas y limitaciones
Ventajas y limitaciones de los polvos metálicos LMD
Polvo metálico | Ventajas | Limitaciones |
---|---|---|
Inconel 625 | Excelente resistencia a la corrosión y a la oxidación, alta resistencia | Caro, difícil de mecanizar |
Titanio 6Al-4V | Elevada relación resistencia/peso, biocompatible | Coste elevado, dificultad para trabajar |
Acero inoxidable 316L | Alta resistencia a la corrosión, buena conformabilidad | Menor resistencia en comparación con otras aleaciones |
Cromo-cobalto | Gran resistencia al desgaste y a la corrosión, biocompatible | Quebradizo, caro |
Aluminio AlSi10Mg | Ligero, buenas propiedades térmicas | Menor resistencia que las aleaciones de acero |
Cobre | Excelente conductividad térmica y eléctrica | Coste elevado, propenso a la oxidación |
Níquel 718 | Alta resistencia, excelente resistencia a la fatiga y a la fluencia | Caro, difícil de mecanizar |
Acero para herramientas H13 | Gran tenacidad y resistencia al desgaste | Requiere tratamiento térmico, caro |
Acero martensítico envejecido | Alta resistencia, buena tenacidad | Caro, requiere tratamiento de envejecimiento |
Bronce CuSn10 | Buena resistencia al desgaste y a la corrosión | Menor resistencia que el acero, propenso a la deszincificación |
Parámetros y umbrales
Parámetro | Umbral/Rango | Descripción |
---|---|---|
Potencia del láser | 200 - 1000 W | Determina el aporte de energía para fundir el polvo |
Velocidad de escaneo | 200 - 1000 mm/s | Afecta a la velocidad de deposición y a la calidad de la capa |
Velocidad de alimentación de polvo | 1 - 10 g/min | Controla la cantidad de polvo suministrado al baño de fusión |
Grosor de la capa | 20 - 100 µm | Afecta a la resolución y al acabado superficial de la pieza |
Gas de protección | Argón, nitrógeno | Protege el baño de fusión de la oxidación |
Temperatura del sustrato | Temperatura ambiente a 200°C | Puede influir en la calidad de la unión y en las tensiones residuales |
Espaciado de la eclosión | 0,1 - 0,5 mm | Distancia entre pistas láser adyacentes |
Porcentaje de solapamiento | 50 – 90% | Garantiza una cobertura completa y la unión entre capas |
Tasa de enfriamiento | 10^2 - 10^6 °C/s | Afecta a la microestructura y a las propiedades mecánicas |
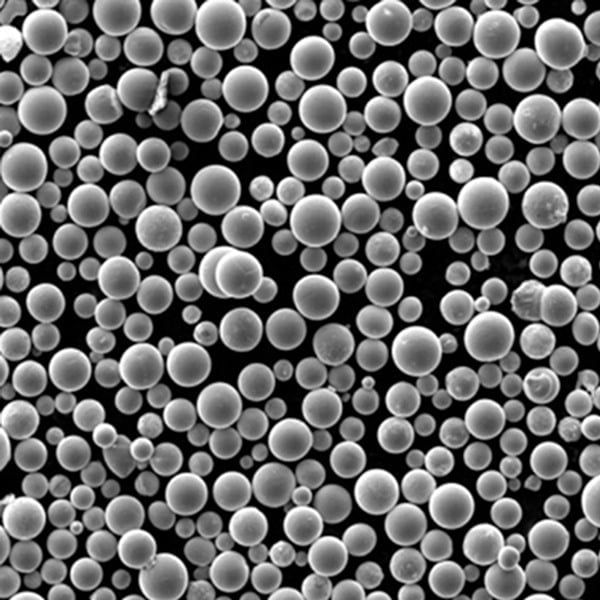
Preguntas frecuentes (FAQ)
Pregunta | Respuesta |
---|---|
¿Qué es el depósito de metales por láser (LMD)? | El LMD es un proceso de fabricación aditiva que utiliza un láser para fundir polvo o alambre metálico y depositarlo sobre un sustrato. |
¿Qué materiales pueden utilizarse en LMD? | Diversos metales, como Inconel, aleaciones de titanio, acero inoxidable, cromo-cobalto, aluminio, cobre, etc. |
¿Qué industrias utilizan LMD? | Industrias aeroespacial, automovilística, médica, de herramientas y matrices, energética y de defensa. |
¿Cuáles son las ventajas del LMD? | Alta precisión, mínimo desperdicio, capacidad para reparar componentes caros y versatilidad de materiales. |
¿En qué se diferencia el LMD de la fabricación tradicional? | El LMD ofrece mayor precisión, menos residuos y la posibilidad de crear geometrías complejas en comparación con los métodos tradicionales. |
¿Cuáles son las limitaciones de la LMD? | Coste inicial elevado, ritmos de construcción más lentos en comparación con algunos métodos tradicionales y limitación por el tamaño del área de construcción. |
¿Cuál es el grosor de capa típico en LMD? | El grosor típico de la capa oscila entre 20 y 100 micrómetros. |
¿Se puede utilizar LMD para reparar piezas? | Sí, el LMD es muy eficaz para reparar componentes de gran valor, prolongar su vida útil y reducir costes. |
¿Cuáles son los parámetros clave del proceso LMD? | Los parámetros clave son la potencia del láser, la velocidad de escaneado, la velocidad de avance del polvo, el grosor de la capa y el gas de protección. |
¿Cómo se garantiza la calidad de las piezas LMD? | La calidad se garantiza mediante un control preciso de los parámetros del proceso, una selección adecuada del material y técnicas de postprocesado. |
Acerca de 3DP mETAL
Categoría de productos
CONTÁCTANOS
¿Tienes alguna pregunta? ¡Envíanos un mensaje ahora! Después de recibir tu mensaje, procesaremos tu solicitud con todo un equipo.