Visión general de Moldeo por inyección de metales (MIM)
El moldeo por inyección de metal (MIM) es un proceso de fabricación que combina la versatilidad del moldeo por inyección de plástico con la resistencia e integridad del metal. Este proceso permite la producción en serie de componentes metálicos intrincados que serían difíciles, costosos o incluso imposibles de producir mediante métodos tradicionales. El MIM es especialmente ventajoso para crear piezas pequeñas y complejas con gran precisión y excelentes propiedades mecánicas.
El proceso MIM comienza con la mezcla de polvos metálicos con un material aglutinante para crear una materia prima que se inyecta en un molde para darle la forma deseada. La pieza moldeada, conocida como "pieza verde", se somete a un proceso de desaglomerado para eliminar el aglutinante y, a continuación, a un proceso de sinterización para densificar el polvo metálico.
Este proceso es muy valorado en industrias como la automovilística, aeroespacial, de dispositivos médicos, electrónica y de bienes de consumo por su capacidad de producir piezas metálicas complejas de alta resistencia a un coste inferior al del mecanizado o la fundición tradicionales.
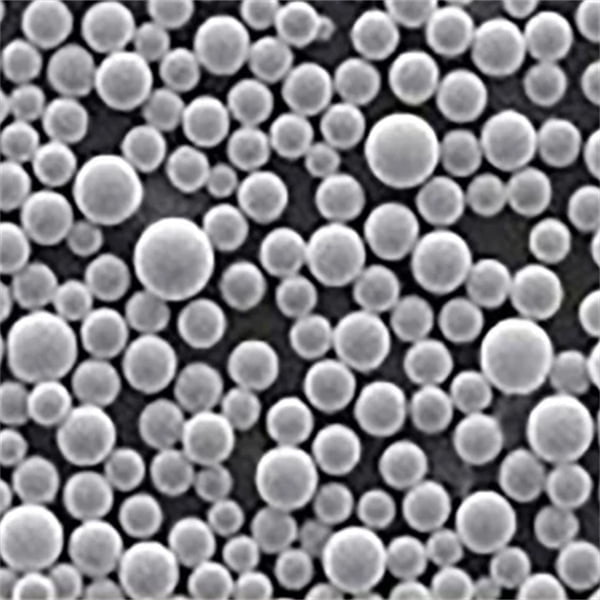
Tipos de polvos metálicos utilizados en MIM y sus propiedades
Polvo metálico | Composición | Propiedades | Características |
---|---|---|---|
Acero inoxidable 316L | Fe-Cr-Ni-Mo | Resistencia a la corrosión, buena ductilidad | Ideal para dispositivos médicos, herramientas quirúrgicas y equipos de procesamiento de alimentos |
Acero inoxidable 17-4 PH | Fe-Cr-Ni-Cu | Alta resistencia, buena resistencia a la corrosión | De uso común en aplicaciones aeroespaciales y de automoción |
Polvo de hierro carbonilado | Hierro de gran pureza | Alta densidad, propiedades magnéticas | Utilizados en aplicaciones magnéticas, materiales magnéticos blandos |
Aleaciones a base de níquel | Ni-Cr-Mo-Fe | Resistencia a altas temperaturas y a la corrosión | Adecuado para aplicaciones aeroespaciales, de procesamiento químico y marinas |
Aleación de titanio (Ti-6Al-4V) | Ti-Al-V | Elevada relación resistencia/peso, biocompatibilidad | Se utiliza en implantes médicos, la industria aeroespacial y la ingeniería de alto rendimiento |
Aleaciones de cobalto-cromo | Co-Cr-Mo | Resistencia al desgaste, biocompatibilidad | A menudo se utiliza en implantes dentales y ortopédicos |
Carburo de wolframio (WC-Co) | WC con aglutinante de Co | Dureza extrema, resistencia al desgaste | Común en herramientas de corte y componentes resistentes al desgaste |
Aleaciones de cobre | Cu con Zn o Sn | Excelente conductividad eléctrica y térmica | Se utiliza en conectores eléctricos, intercambiadores de calor y fontanería |
Aleaciones de aluminio | Al con Mg, Si, Cu | Ligero, buena resistencia a la corrosión | Ideal para componentes estructurales ligeros |
Acero para herramientas (M2, D2) | Fe-Cr-V-W-Mo | Gran dureza, resistencia al desgaste | Se utiliza en herramientas de corte, troqueles y moldes |
Composición del moldeo por inyección de metales (MIM)
La composición de la materia prima utilizada en el moldeo por inyección de metales es un factor crítico que influye en las propiedades del producto final. La materia prima suele consistir en una mezcla de polvos metálicos finos y un aglutinante termoplástico. La elección del polvo metálico y del aglutinante influye significativamente en las propiedades del material, en las características de flujo durante el moldeo y en los procesos de desaglomerado y sinterización.
- Polvos metálicos: Los polvos metálicos utilizados en el MIM son partículas finamente divididas, normalmente de un tamaño inferior a 20 micras. Estos polvos pueden estar hechos de una gran variedad de metales, como acero inoxidable, titanio, carburo de tungsteno y otros. El tipo de polvo metálico elegido depende de las propiedades requeridas del producto final, como la solidez, la resistencia a la corrosión o la biocompatibilidad.
- Carpetas: El sistema aglutinante suele ser una mezcla de polímeros y ceras que unen las partículas de polvo metálico y proporcionan las características de fluidez necesarias para el moldeo por inyección. Tras el moldeo, el aglutinante se elimina mediante un proceso de desligado, que puede incluir métodos térmicos, con disolventes o catalíticos.
Características principales de los materiales MIM
Material | Características principales | Aplicaciones típicas |
---|---|---|
Acero inoxidable 316L | Excelente resistencia a la corrosión, buenas propiedades mecánicas | Dispositivos médicos, equipos de procesamiento de alimentos, piezas marinas |
Aleación de titanio (Ti-6Al-4V) | Elevada relación resistencia/peso, biocompatibilidad | Componentes aeroespaciales, implantes médicos |
Carburo de wolframio (WC-Co) | Extremadamente duro, excelente resistencia al desgaste | Herramientas de corte, componentes resistentes al desgaste |
Aleaciones a base de níquel | Resistencia a altas temperaturas, resistencia a la corrosión | Álabes de turbina, equipos de procesamiento químico |
Acero para herramientas (M2, D2) | Gran dureza, excelente resistencia al desgaste | Herramientas de corte, troqueles, moldes. |
El proceso MIM: Desglose paso a paso
Comprender el proceso de moldeo por inyección de metales implica una serie de pasos, cada uno de ellos crucial para garantizar que el producto final cumpla las especificaciones deseadas.
- Preparación de la materia prima: El primer paso del MIM es crear la materia prima, lo que implica mezclar polvos metálicos con un aglutinante. El aglutinante permite que el polvo metálico fluya como un plástico durante el proceso de moldeo por inyección.
- Moldeo por inyección: La materia prima se calienta y se inyecta en la cavidad de un molde, formando la "parte verde". Esta parte es una forma aproximada del producto final, unida por el aglutinante.
- Debinding: En este paso, se elimina el aglutinante de la parte verde, dejando una estructura porosa conocida como "parte marrón". El desencolado puede realizarse mediante diversos métodos, como procesos térmicos, con disolventes o catalíticos.
- Sinterización: La pieza marrón se calienta en una atmósfera controlada hasta justo por debajo del punto de fusión del polvo metálico. Durante la sinterización, las partículas metálicas se fusionan, lo que provoca la densificación y contracción de la pieza hasta sus dimensiones finales.
- Posprocesamiento: Dependiendo de la aplicación, la pieza sinterizada puede someterse a procesos adicionales, como mecanizado, tratamiento térmico o acabado superficial, para conseguir las propiedades y tolerancias deseadas.
Visión general del proceso MIM y pasos clave
Etapa del proceso | Descripción | Resultado |
---|---|---|
Preparación de la materia prima | Mezcla de polvos metálicos con aglutinante para crear material moldeable | Materia prima lista para el moldeo por inyección |
Moldeo por inyección | Inyección de materia prima en un molde para crear la pieza verde | Parte verde formada, mantiene la forma pero es frágil |
Desbobinado | Eliminación del aglutinante de la parte verde para formar la parte marrón | Estructura porosa sin aglutinantes (parte marrón) |
Sinterización | Calentamiento de la pieza marrón para fundir partículas metálicas | Pieza final densa y resistente con porosidad reducida |
Tratamiento posterior | Tratamientos adicionales como mecanizado, tratamiento térmico, acabado | Propiedades mejoradas, dimensiones finales y acabado superficial |
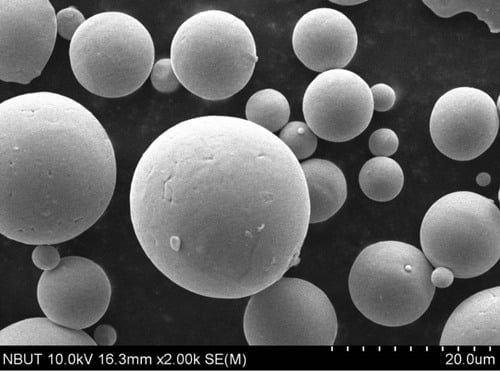
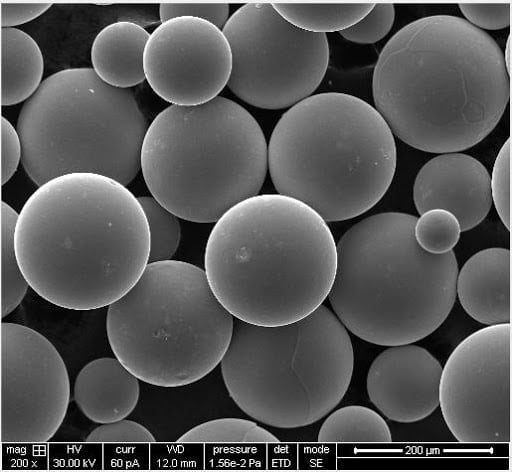
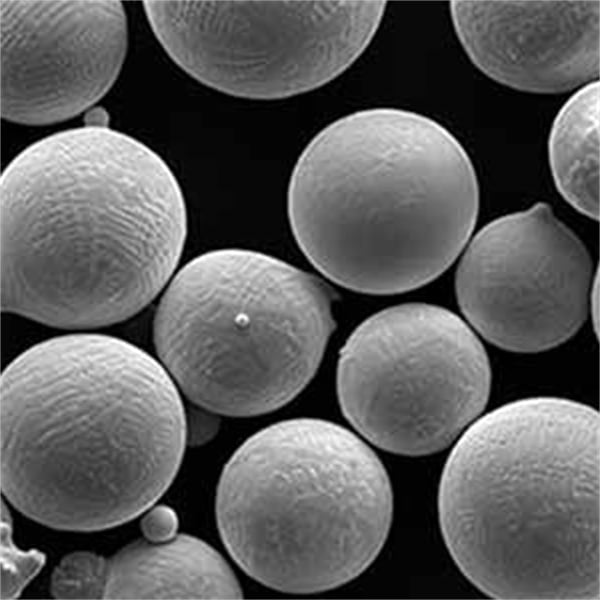
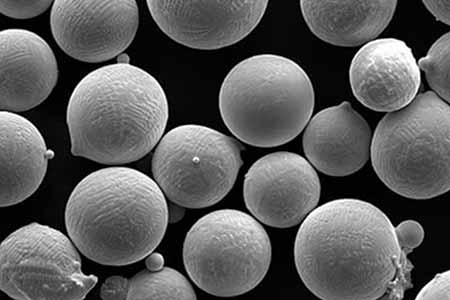
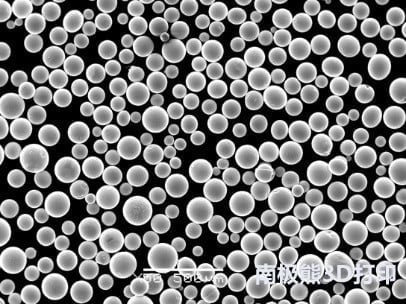
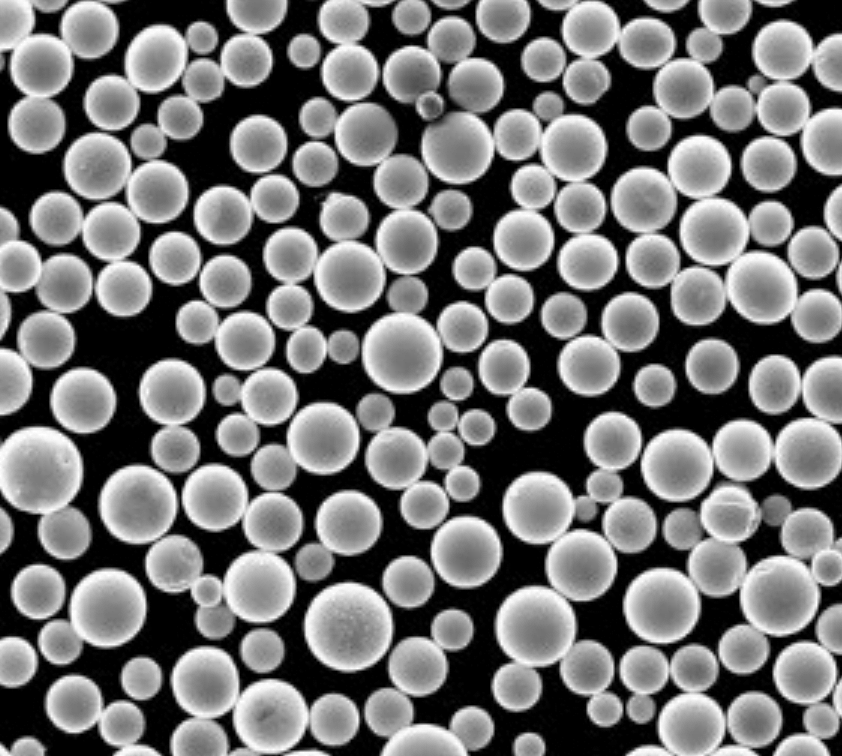
Ventajas de Moldeo por inyección de metales (MIM)
¿Por qué elegir el MIM frente a los métodos tradicionales de trabajo del metal? Hay varias ventajas convincentes:
- Geometría compleja: El MIM permite producir formas complejas que serían difíciles o imposibles con otras técnicas de fabricación. Esta capacidad reduce la necesidad de operaciones secundarias, como el mecanizado, que pueden ser largas y costosas.
- Eficiencia del material: Dado que el MIM utiliza metales finamente pulverizados, permite fabricar formas casi netas, lo que minimiza el desperdicio de material en comparación con el mecanizado tradicional, que suele implicar una importante eliminación de material.
- Alta precisión y consistencia: El MIM produce piezas con tolerancias estrechas y calidad constante, por lo que es ideal para aplicaciones en las que la precisión es fundamental.
- Escalabilidad: El proceso es altamente escalable, lo que permite la producción masiva de piezas a un coste por unidad relativamente bajo, especialmente cuando se trata de grandes volúmenes.
- Variedad de materiales: El MIM puede trabajar con una amplia gama de metales, como acero inoxidable, titanio y aleaciones de alto rendimiento, lo que proporciona flexibilidad en la selección de materiales en función de las necesidades de la aplicación.
- Propiedades mecánicas: Las piezas MIM pueden presentar propiedades mecánicas comparables a las fabricadas por métodos tradicionales, como la fundición o la forja, lo que las hace aptas para aplicaciones exigentes.
Ventajas del moldeo por inyección de metales
Ventaja | Descripción | Comparación |
---|---|---|
Geometría compleja | Capaz de producir piezas complejas y detalladas | Mejor que la fundición y el mecanizado para formas complejas |
Eficiencia material | La fabricación con forma casi de red minimiza los residuos | Más eficaz que los métodos sustractivos |
Alta precisión | Tolerancias estrictas y calidad constante | Comparable al mecanizado CNC |
Escalabilidad | Adecuada para grandes volúmenes de producción | Más rentable que los métodos tradicionales para grandes tiradas |
Variedad de materiales | Compatible con una amplia gama de metales | Más flexible que la fundición a presión |
Propiedades Mecánicas | Alta resistencia, resistencia al desgaste y otras propiedades deseables | Comparable a las piezas forjadas o fundidas |
Aplicaciones del moldeo por inyección de metales (MIM)
El MIM se utiliza en diversos sectores gracias a su capacidad para producir piezas pequeñas y complejas de forma eficaz y rentable. Estas son algunas de sus principales aplicaciones:
- Industria del automóvil: Los componentes MIM se utilizan en sistemas de combustible, turbocompresores, sensores y diversas piezas del motor. El proceso permite crear componentes ligeros y de alta resistencia que contribuyen a la eficiencia del combustible y al rendimiento.
- Industria aeroespacial: El MIM se emplea para fabricar piezas complejas y ligeras para motores de aviones, sistemas de control y componentes estructurales. La capacidad de fabricar piezas con gran precisión y excelentes propiedades mecánicas hace que el MIM sea una tecnología muy rentable.
IM ideal para aplicaciones aeroespaciales.
- Productos sanitarios: La industria médica se beneficia de la capacidad del MIM para fabricar componentes biocompatibles con geometrías complejas. El MIM se utiliza para fabricar instrumentos quirúrgicos, implantes ortopédicos y dispositivos dentales.
- Electrónica: El MIM se utiliza para crear piezas pequeñas y complejas para dispositivos electrónicos, como conectores, carcasas y componentes para teléfonos móviles y ordenadores portátiles. El proceso es idóneo para la producción de grandes volúmenes de piezas con tolerancias estrictas.
- Bienes de consumo: En el sector de bienes de consumo, el MIM se utiliza para fabricar componentes duraderos y de alta calidad para productos como relojes, gafas y equipamiento deportivo.
- Defensa: La industria de defensa utiliza el MIM para fabricar componentes ligeros, resistentes y duraderos para armas de fuego, munición y otros equipos militares.
Aplicaciones del moldeo por inyección de metales en la industria
Industria | Aplicaciones clave | Ejemplos de componentes MIM |
---|---|---|
Automovilístico | Piezas de motor, sensores, turbocompresores | Inyectores de combustible, asientos de válvulas, componentes del árbol de levas |
Aeroespacial | Componentes del motor, piezas estructurales | Álabes de turbina, componentes de actuadores, elementos de fijación |
Productos sanitarios | Instrumental quirúrgico, implantes ortopédicos | Hojas de bisturí, tornillos óseos, brackets dentales |
Electrónica | Conectores, carcasas, pequeños componentes intrincados | Conectores USB, carcasas de cámaras, bisagras de portátiles |
Bienes de consumo | Productos de consumo duraderos y de alta calidad | Estuches de relojes, monturas de gafas, cabezas de palos de golf |
Defensa | Equipamiento militar, componentes de armas de fuego | Componentes del gatillo, piezas del cargador, casquillos de munición |
Especificaciones, tamaños, calidades y normas del MIM
Las especificaciones, tamaños, calidades y normas del moldeo por inyección de metales varían en función del material utilizado, la complejidad de la pieza y los requisitos de la aplicación. He aquí un resumen de las especificaciones más comunes:
- Acero inoxidable (316L, 17-4 PH): Los tamaños de grano típicos oscilan entre 5 y 20 micras, con densidades finales de pieza superiores a 95% de la densidad teórica. Las normas incluyen ASTM F2885 para piezas de acero inoxidable de grado médico.
- Aleaciones de titanio (Ti-6Al-4V): El tamaño de las partículas de polvo suele ser inferior a 25 micras. Las piezas MIM de este material cumplen normas como ASTM F2885 e ISO 5832-3 para implantes médicos.
- Carburo de tungsteno: El tamaño de las partículas de polvo oscila entre 0,5 y 10 micras. Las piezas finales pueden alcanzar una densidad de hasta 99% de la densidad teórica. Entre las normas se incluye la ISO 513 para herramientas de corte.
- Acero para herramientas (M2, D2): Los tamaños de grano suelen oscilar entre 10 y 40 micras, con densidades sinterizadas en torno a 98% de la densidad teórica. Las normas incluyen ASTM A681 para piezas de acero para herramientas.
Especificaciones, tamaños y normas de los materiales MIM más comunes
Material | Tamaño típico de las partículas | Densidad final | Normas pertinentes |
---|---|---|---|
Acero inoxidable 316L | 5-20 micras | >95% | ASTM F2885 para aplicaciones médicas |
Aleación de titanio (Ti-6Al-4V) | <25 micras | >95% | ASTM F2885, ISO 5832-3 para implantes médicos |
Carburo de wolframio (WC-Co) | 0,5-10 micras | ~99% | ISO 513 para herramientas de corte |
Acero para herramientas (M2, D2) | 10-40 micras | ~98% | ASTM A681 para piezas de acero para herramientas |
Proveedores y precios
Encontrar el proveedor adecuado de componentes MIM es crucial para garantizar la calidad, la rentabilidad y la puntualidad de la entrega. Los precios de los componentes MIM pueden variar considerablemente en función del material, la complejidad, el volumen y los requisitos de procesamiento adicionales.
- Pulvimetalurgia GKN: GKN, proveedor líder de polvos metálicos y componentes MIM, ofrece una amplia gama de materiales y soluciones personalizadas. Los precios suelen oscilar entre $0,10 y $10 por pieza, en función de la complejidad y el volumen.
- Moldeo por inyección de metales Parmaco: Se especializa en componentes MIM de alta precisión destinados a los sectores médico, automovilístico y electrónico. Los precios oscilan entre $0,50 y $20 por pieza.
- Productos avanzados en polvo (APP): Conocida por producir piezas MIM complejas con tolerancias estrictas, APP presta servicio a sectores como el aeroespacial y el de defensa. Los precios varían, pero suelen rondar los $1 por pieza.
Principales proveedores y precios de los componentes MIM
Proveedor | Especialidad | Precios típicos (por pieza) | Industrias atendidas |
---|---|---|---|
Pulvimetalurgia GKN | Amplia gama de materiales y componentes MIM | $0.10 – $10 | Automoción, aeroespacial, industrial |
Moldeo por inyección de metales Parmaco | Componentes de alta precisión | $0.50 – $20 | Medicina, automoción, electrónica |
Productos avanzados en polvo (APP) | Piezas MIM complejas y de tolerancia ajustada | A partir de $1 | Aeroespacial, defensa, medicina |
Comparación de ventajas e inconvenientes del moldeo por inyección de metal
Como cualquier proceso de fabricación, el moldeo por inyección de metales tiene sus propias ventajas e inconvenientes. Comprenderlas puede ayudarle a determinar si el MIM es el proceso adecuado para su aplicación específica.
Ventajas e inconvenientes del moldeo por inyección de metales
Aspecto | Puntos a favor | Contras |
---|---|---|
Complejidad | Puede producir geometrías intrincadas y complejas | Limitado a piezas de tamaño relativamente pequeño |
Residuos materiales | Mínimo desperdicio gracias a un procesado casi en forma de red | Costes elevados de determinados metales |
Volumen de producción | Económico para grandes volúmenes de producción | Menos rentable para la producción de bajo volumen |
Propiedades Mecánicas | Alta resistencia y buenas propiedades mecánicas | Potencial de contracción durante la sinterización |
Variedad de materiales | Amplia gama de metales compatibles | Algunos materiales pueden requerir procesos de descortezado especializados |
Tratamiento posterior | Permite un mayor mecanizado y acabado | Costes adicionales del tratamiento posterior |
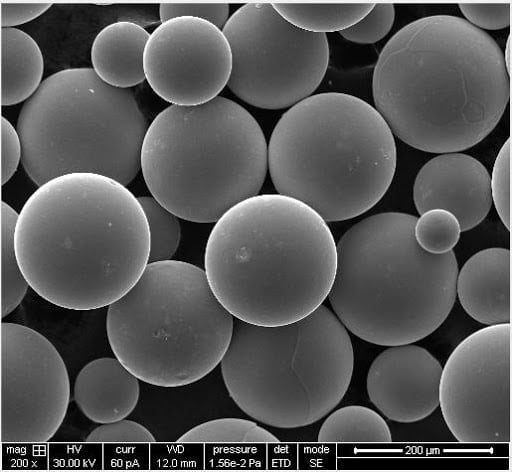
Preguntas frecuentes (FAQ)
Pregunta | Respuesta |
---|---|
¿Qué es el moldeo por inyección de metales (MIM)? | El MIM es un proceso de fabricación que combina polvos metálicos con un aglutinante para producir piezas metálicas complejas. |
¿Qué industrias utilizan más el MIM? | Industrias como la automoción, la aeroespacial, los dispositivos médicos, la electrónica y la defensa utilizan mucho el MIM. |
¿Qué metales pueden utilizarse en MIM? | Se suelen utilizar metales como el acero inoxidable, el titanio, el carburo de tungsteno y aleaciones a base de níquel. |
¿En qué se diferencia el MIM del mecanizado tradicional? | El MIM es más rentable para piezas complejas y de gran volumen, mientras que el mecanizado es más adecuado para piezas más sencillas y de bajo volumen. |
¿Cuáles son las limitaciones del MIM? | El MIM es menos rentable para la producción de bajo volumen y tiene limitaciones para producir piezas muy grandes. |
¿Es el MIM respetuoso con el medio ambiente? | El MIM produce menos residuos que el mecanizado tradicional, lo que lo convierte en una opción más respetuosa con el medio ambiente. |
¿Qué grado de precisión tienen las piezas MIM? | Las piezas MIM pueden alcanzar una gran precisión con tolerancias comparables a las de las piezas mecanizadas por CNC. |
¿Cuál es el plazo de entrega habitual de los componentes MIM? | Los plazos de entrega pueden oscilar entre unas semanas y varios meses, en función de la complejidad y el volumen del pedido. |
¿Se pueden personalizar las piezas MIM? | Sí, el MIM permite una gran personalización en cuanto a forma, material y acabado superficial. |
¿Cómo afecta el sinterizado a la pieza MIM final? | La sinterización densifica la pieza, reduciendo la porosidad y mejorando las propiedades mecánicas, pero también puede provocar contracción. |
Conclusiones
Moldeo por inyección de metales (MIM) es un potente proceso de fabricación que tiende un puente entre el moldeo por inyección de plástico y las técnicas tradicionales de trabajo del metal. Gracias a su capacidad para producir piezas metálicas complejas y de alta resistencia a gran escala, el MIM es la solución a la que recurren los sectores que requieren precisión, durabilidad y eficiencia. El MIM es una solución versátil y rentable para los sectores de automoción, aeroespacial, médico o cualquier otro en el que sean esenciales los componentes metálicos de alto rendimiento. Conocer los materiales, los pasos del proceso y las ventajas y limitaciones del MIM le ayudará a tomar decisiones informadas para su próximo proyecto.
Acerca de 3DP mETAL
Categoría de productos
CONTÁCTANOS
¿Tienes alguna pregunta? ¡Envíanos un mensaje ahora! Después de recibir tu mensaje, procesaremos tu solicitud con todo un equipo.