Visión general del moldeo por inyección de metales (MIM)
Moldeo por inyección de metales (MIM) es un proceso de fabricación que combina la versatilidad del moldeo por inyección de plástico con la resistencia e integridad de la metalurgia de polvos. Es un método ideal para producir piezas metálicas complejas de gran volumen con una precisión excepcional. El MIM es especialmente ventajoso para crear geometrías intrincadas que serían difíciles o imposibles de conseguir con los procesos metalúrgicos tradicionales.
El proceso consiste en mezclar metal en polvo fino con un material aglutinante para crear una materia prima, a la que se da la forma deseada mediante moldeo por inyección. Tras el moldeo, la pieza se somete a un proceso de desligado para eliminar el aglutinante, seguido de la sinterización, en la que las partículas metálicas se fusionan a altas temperaturas para formar una pieza densa y sólida.
¿Por qué es importante el MIM?
El MIM ofrece varias ventajas sobre las técnicas convencionales de metalurgia, como la reducción del desperdicio de material, menores costes de producción para grandes volúmenes y la capacidad de crear formas complejas con tolerancias ajustadas. Este proceso es especialmente valioso en sectores como la automoción, la industria aeroespacial, los dispositivos médicos y la electrónica de consumo, donde la precisión y el rendimiento son primordiales.
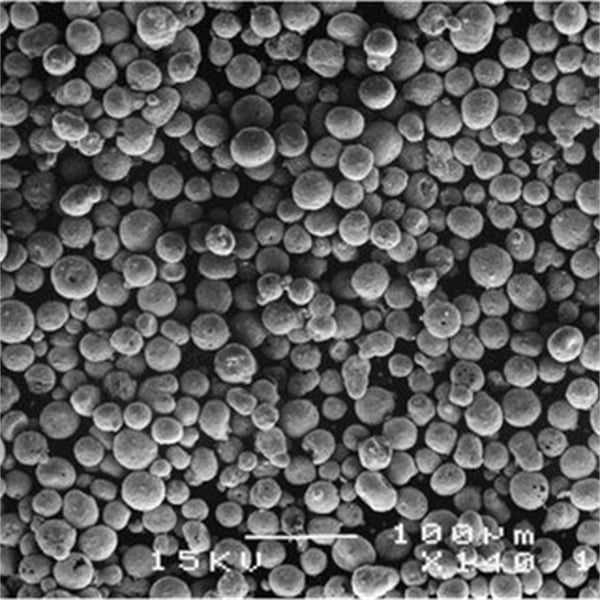
Composición de la materia prima para el moldeo por inyección de metales
La materia prima utilizada en el moldeo por inyección de metales consiste en una mezcla de polvos metálicos y aglutinantes. La elección del polvo metálico depende de los requisitos específicos de la pieza final, incluidas sus propiedades mecánicas, su resistencia a la corrosión y su coste.
Tipos de polvos metálicos utilizados en MIM
Polvo metálico | Composición | Propiedades | Aplicaciones habituales |
---|---|---|---|
Acero inoxidable 316L | Hierro (Fe), Cromo (Cr), Níquel (Ni), Molibdeno (Mo) | Alta resistencia a la corrosión, excelentes propiedades mecánicas | Dispositivos médicos, componentes aeroespaciales, piezas de automóvil |
Acero inoxidable 17-4 PH | Hierro (Fe), Cromo (Cr), Níquel (Ni), Cobre (Cu) | Alta resistencia, buena resistencia a la corrosión | Instrumentos aeroespaciales, militares y quirúrgicos |
Cromo-cobalto | Cobalto (Co), Cromo (Cr), Molibdeno (Mo) | Excepcional resistencia al desgaste y a la corrosión, biocompatibilidad | Implantes médicos, prótesis dentales |
Titanio (Ti-6Al-4V) | Titanio (Ti), Aluminio (Al), Vanadio (V) | Elevada relación resistencia/peso, excelente resistencia a la corrosión | Aeroespacial, implantes médicos, piezas de automoción de alto rendimiento |
Inconel 718 | Níquel (Ni), Cromo (Cr), Hierro (Fe), Molibdeno (Mo) | Alta resistencia a la temperatura y a la corrosión | Palas de turbina, equipos aeroespaciales y de procesamiento químico |
Acero para herramientas M2 | Hierro (Fe), Wolframio (W), Molibdeno (Mo), Vanadio (V) | Gran dureza, resistencia al desgaste | Herramientas de corte, troqueles y moldes |
Aleaciones magnéticas blandas Fe-Ni | Hierro (Fe), Níquel (Ni) | Alta permeabilidad magnética, baja coercitividad | Núcleos magnéticos, sensores y actuadores |
Aleaciones pesadas de wolframio | Tungsteno (W), Níquel (Ni), Hierro (Fe), Cobre (Cu) | Alta densidad, blindaje contra las radiaciones | Contrapesos, blindaje contra radiaciones, dispositivos de amortiguación de vibraciones |
Aleaciones de cobre | Cobre (Cu), Zinc (Zn), Estaño (Sn), Níquel (Ni) | Alta conductividad térmica y eléctrica | Conectores eléctricos, disipadores térmicos, accesorios de fontanería |
Aleaciones de aluminio | Aluminio (Al), Silicio (Si), Magnesio (Mg) | Ligero, buena resistencia a la corrosión | Componentes de automoción, electrónica de consumo, piezas aeroespaciales |
Características principales de los polvos metálicos en el MIM
La selección de los polvos metálicos es fundamental para determinar las propiedades finales del componente MIM. Los polvos metálicos deben poseer las siguientes características:
- Tamaño y distribución de partículas: Los polvos utilizados en el MIM suelen tener tamaños de partícula que oscilan entre 2 y 20 micras. Se prefiere una distribución granulométrica estrecha para garantizar un empaquetado uniforme y reducir los defectos.
- Forma: En general, se prefieren los polvos esféricos para el MIM porque ofrecen mejores propiedades de fluidez y densidad de empaquetamiento, que son cruciales para el proceso de moldeo por inyección.
- Pureza: Los polvos metálicos de gran pureza son esenciales para evitar la contaminación, que puede provocar defectos y reducir las propiedades mecánicas de la pieza final.
- Compatibilidad con encuadernadoras: El polvo metálico debe ser compatible con el aglutinante utilizado en la materia prima para garantizar una mezcla homogénea y un procesamiento óptimo.
Características de Moldeo por inyección de metales
El moldeo por inyección de metales ofrece un conjunto único de características que lo convierten en un proceso de fabricación atractivo para diversas industrias. Estas características se derivan de la combinación de la metalurgia de polvos y las técnicas de moldeo por inyección de plásticos.
Alta complejidad y precisión
El MIM es capaz de producir piezas con geometrías complejas y detalles finos que serían difíciles de conseguir con otros métodos de fabricación. Esta precisión es especialmente beneficiosa para sectores en los que son esenciales los diseños intrincados y las tolerancias estrechas, como los dispositivos médicos y los componentes aeroespaciales.
Eficiencia material
Una de las principales ventajas del MIM es la eficiencia de sus materiales. El proceso genera unos residuos mínimos en comparación con los métodos metalúrgicos tradicionales, ya que el material sobrante a menudo puede reciclarse de nuevo en el proceso. Esta eficiencia no solo reduce costes, sino que también contribuye a los esfuerzos de sostenibilidad.
Propiedades Mecánicas
Las piezas fabricadas mediante MIM presentan propiedades mecánicas comparables a las de los materiales forjados. El proceso de sinterización garantiza que las partículas metálicas se fusionen para formar una estructura densa y sólida, lo que da lugar a piezas de gran resistencia, dureza y resistencia al desgaste.
Versatilidad en la elección de materiales
El MIM es compatible con una amplia gama de polvos metálicos, lo que permite a los fabricantes seleccionar el material que mejor se adapte a la aplicación. Esta versatilidad se extiende a la capacidad de crear piezas con propiedades a medida, como relaciones específicas entre resistencia y peso, resistencia a la corrosión o propiedades magnéticas.
Rentabilidad para grandes volúmenes
Aunque los costes iniciales de utillaje y preparación del MIM pueden ser elevados, el proceso resulta muy rentable para grandes series de producción. La capacidad de producir grandes volúmenes de piezas complejas con el mínimo desperdicio se traduce en un importante ahorro de costes.
Aplicaciones del moldeo por inyección de metales
El moldeo por inyección de metales se utiliza en una amplia gama de sectores gracias a su capacidad para producir piezas complejas de alto rendimiento a gran escala. A continuación, exploramos algunas de las principales aplicaciones del MIM, destacando cómo este proceso está impulsando la innovación en diversos sectores.
Industria automotriz
En el sector de la automoción, el MIM se utiliza para fabricar componentes que requieren gran precisión y resistencia, como sistemas de engranajes, piezas de turbocompresores y boquillas de inyectores de combustible. El proceso permite fabricar piezas ligeras y duraderas que contribuyen a mejorar la eficiencia y el rendimiento del combustible.
Industria Aeroespacial
La industria aeroespacial se beneficia de la capacidad del MIM para producir componentes ligeros y de alta resistencia que pueden soportar temperaturas y presiones extremas. Las aplicaciones más comunes son álabes de turbina, componentes estructurales y elementos de fijación.
Productos sanitarios
El MIM es especialmente adecuado para la industria médica, donde la biocompatibilidad y la precisión son fundamentales. El proceso se utiliza para fabricar instrumentos quirúrgicos, brackets de ortodoncia y dispositivos implantables. Materiales como el titanio y el cromo-cobalto se utilizan habitualmente por sus excelentes propiedades mecánicas y biocompatibilidad.
Electrónica de consumo
En el sector de la electrónica de consumo, el MIM se emplea para crear componentes pequeños y complejos, como conectores, bisagras y carcasas. La capacidad de producir piezas con detalles finos y tolerancias ajustadas es esencial para la miniaturización de los dispositivos electrónicos.
Armas de fuego y defensa
La industria de las armas de fuego utiliza el MIM para fabricar componentes como conjuntos de gatillos, soportes de miras y mecanismos de seguridad. La precisión del proceso y su capacidad para producir piezas de alta resistencia lo hacen ideal para fabricar componentes de armas de fuego que deben cumplir estrictas normas de seguridad y rendimiento.
Aplicaciones industriales
El MIM también se utiliza en diversas aplicaciones industriales, como la fabricación de herramientas de corte, engranajes y elementos de fijación. La capacidad del proceso para crear piezas resistentes al desgaste y de alta resistencia lo hace valioso en entornos industriales donde la durabilidad y el rendimiento son fundamentales.
Prótesis dentales
En la industria dental, el MIM se utiliza para fabricar componentes protésicos como coronas, puentes y pilares. El proceso permite crear piezas biocompatibles a medida que ofrecen una resistencia y longevidad superiores a las de los materiales tradicionales.
Sector de Energía
El sector energético utiliza el MIM para fabricar componentes para la generación de energía y la prospección de petróleo y gas. Piezas como álabes de turbina, componentes de válvulas y herramientas de perforación se benefician de la capacidad del proceso para producir piezas de alta resistencia a la corrosión que pueden soportar entornos difíciles.
Joyería y artículos de lujo
El MIM también está ganando terreno en el mercado de la joyería y los artículos de lujo, donde se utiliza para producir diseños intrincados con metales preciosos. El proceso permite crear piezas detalladas y personalizadas, duraderas y estéticamente agradables.
Artículos deportivos
En la industria de artículos deportivos, el MIM se utiliza para fabricar componentes para palos de golf, armas de fuego y bicicletas de alto rendimiento. El proceso permite crear piezas ligeras y de alta resistencia que mejoran el rendimiento y la durabilidad del equipamiento deportivo.
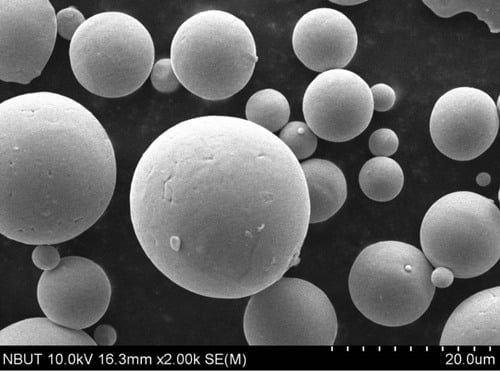
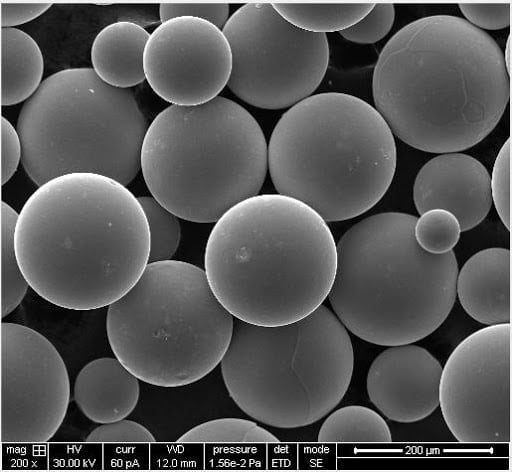
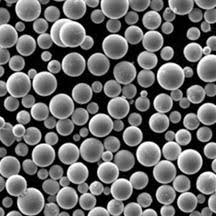
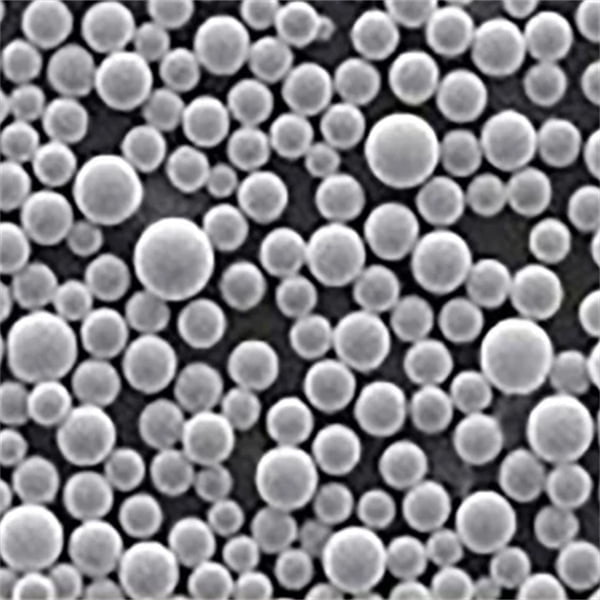
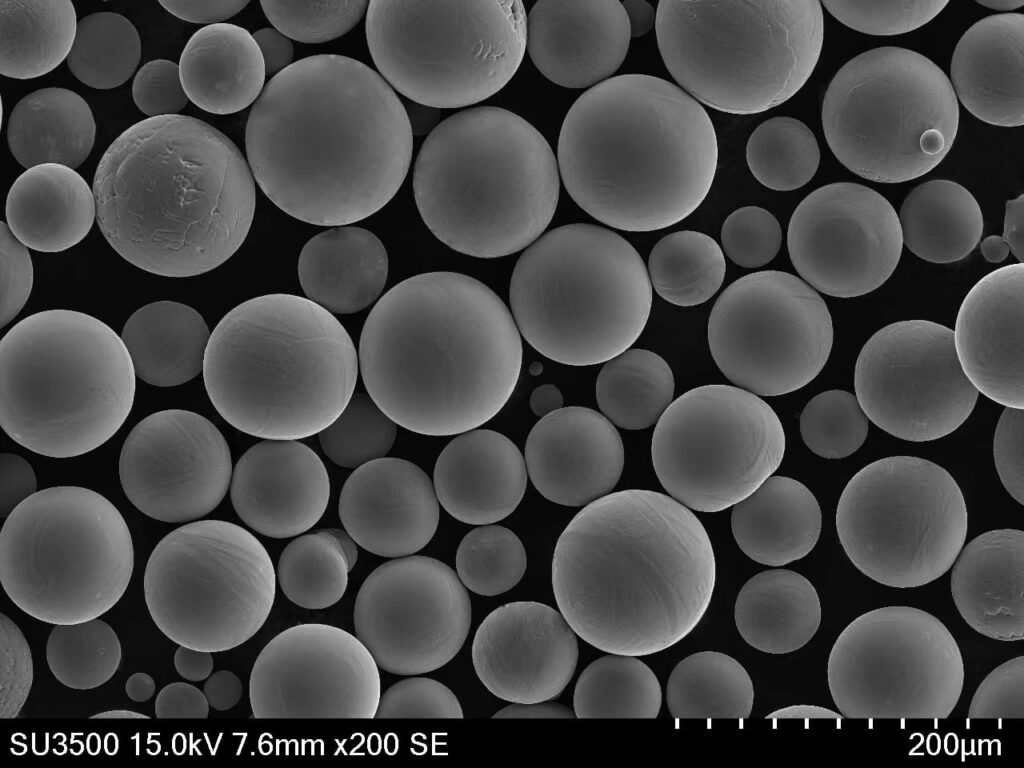
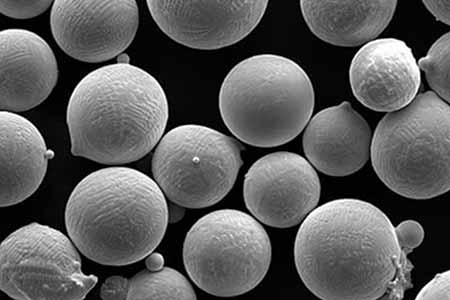
Especificaciones, tamaños y normas en Moldeo por inyección de metales
Cuando se trata del moldeo por inyección de metales, comprender las especificaciones, tamaños y normas es crucial para garantizar la calidad y el rendimiento del producto final. Estos parámetros suelen venir dictados por la aplicación y los requisitos del sector.
Especificaciones y normas comunes
Especificaciones | Descripción | SOLICITUDES |
---|---|---|
ASTM F2885 | Especificación normalizada para el MIM de aleaciones de acero inoxidable | Se utiliza en la fabricación de dispositivos médicos, instrumentos quirúrgicos y componentes aeroespaciales. |
ISO 22068 | Norma internacional para el control del proceso MIM y la garantía de calidad | Se aplica en todos los sectores para garantizar la calidad y el rendimiento uniformes de las piezas producidas por MIM. |
Norma MPIF 35 | Normas de materiales para polvos metálicos y piezas metálicas sinterizadas | Ampliamente utilizado en aplicaciones de automoción, aeroespaciales e industriales para normalizar las propiedades de los materiales. |
ISO 5755 | Norma para componentes metálicos sinterizados, incluidas tolerancias y dimensiones | Garantiza la precisión dimensional y la uniformidad de las piezas MIM |
AMS 7715 | Especificación de materiales aeroespaciales para el MIM de aleaciones a base de níquel | Esencial para componentes aeroespaciales que requieren resistencia a altas temperaturas y a la corrosión |
DIN 30910 | Norma alemana para piezas metálicas moldeadas por inyección | Utilizado habitualmente en las industrias manufactureras europeas para garantizar la calidad de las piezas MIM. |
JIS Z2550 | Norma japonesa sobre pulvimetalurgia, incluidos los procesos MIM | Garantiza una calidad constante en las piezas MIM utilizadas en automoción y electrónica de consumo en Japón. |
MIL-STD-883 | Norma militar para componentes microelectrónicos, incluidas las piezas MIM | Se aplica en la producción de equipos militares y de defensa para garantizar la fiabilidad y el rendimiento. |
Tamaños y tolerancias
El MIM permite fabricar piezas con una amplia gama de tamaños y tolerancias. El tamaño de la pieza suele estar limitado por la capacidad de la máquina de moldeo por inyección y el proceso de sinterización.
- Tamaño de la pieza: Las piezas MIM suelen oscilar entre 0,1 y 100 gramos, con algunos procesos especializados capaces de producir piezas de hasta 250 gramos.
- Tolerancias: Las tolerancias estándar de las piezas MIM suelen ser de ±0,5% de la dimensión, pero pueden conseguirse tolerancias más ajustadas de ±0,3% con operaciones secundarias.
Grados de material
El grado de material utilizado en el MIM se selecciona en función de las propiedades mecánicas requeridas, la resistencia a la corrosión y consideraciones de coste. A continuación se indican algunos grados de material habituales en el MIM:
Calidad del material | Descripción | SOLICITUDES |
---|---|---|
316L (UNS S31603) | Acero inoxidable austenítico con bajo contenido en carbono y excelente resistencia a la corrosión | Implantes médicos, componentes aeroespaciales |
17-4 PH (UNS S17400) | Acero inoxidable endurecido por precipitación de alta resistencia | Instrumentos aeroespaciales, militares y quirúrgicos |
Ti-6Al-4V (Grado 5) | Aleación de titanio con una elevada relación resistencia-peso | Aeroespacial, implantes médicos, piezas de alto rendimiento |
Inconel 718 (UNS N07718) | Aleación de níquel-cromo resistente a altas temperaturas y a la corrosión | Álabes de turbina, industria aeroespacial y procesamiento químico |
Cromo-cobalto (ASTM F75) | Aleación con una excepcional resistencia al desgaste y a la corrosión | Implantes médicos, prótesis dentales |
Proveedores y precios del moldeo por inyección de metales
La cadena de suministro de materiales y servicios MIM es global, con numerosos proveedores que ofrecen una amplia gama de polvos metálicos, aglutinantes y equipos de procesamiento MIM. Los precios varían en función del material, la complejidad de la pieza y el volumen de producción.
Principales proveedores de la industria MIM
Proveedor | Productos ofrecidos | Ubicación | Rango de precios |
---|---|---|---|
Metalurgia avanzada | Polvos metálicos, aglutinantes, equipos MIM | EE. UU. | $50 - $200/kg (polvos) |
Materiales Sandvik | Polvos metálicos de alto rendimiento | Suecia | $80 - $250/kg (según la aleación) |
GKN Hoeganaes | Polvos metálicos, soluciones MIM a medida | EE. UU. | $60 - $180/kg |
Hitachi Metales | Polvos metálicos especiales, piezas MIM | Japón | $90 - $300/kg |
Materiales Molyworks | Polvos metálicos reciclados, soluciones MIM sostenibles | EE. UU. | $70 - $220/kg |
Tecnología Carpenter | Polvos metálicos de primera calidad, materiales de calidad aeroespacial | EE. UU. | $100 - $350/kg |
Polvo de CNPC | Amplia gama de polvos metálicos para MIM | China | $40 - $150/kg |
Epson Atmix | Polvos metálicos ultrafinos, aglutinantes MIM | Japón | $100 - $300/kg |
Soluciones HC Starck | Metales refractarios, polvos MIM | Alemania | $120 - $400/kg (para aleaciones de wolframio) |
Mimete Srl | Polvos y servicios MIM a medida | Italia | $80 - $250/kg |
Consideraciones sobre precios
El coste de las piezas MIM depende de varios factores:
- Tipo de material: Los materiales de alto rendimiento, como el titanio y el Inconel, son más caros que los aceros inoxidables estándar.
- Parte Complejidad: Las piezas más complejas con geometrías intrincadas pueden requerir herramientas más avanzadas y tiempos de producción más largos, lo que aumenta los costes.
- Volumen de producción: Los mayores volúmenes de producción suelen reducir los costes por pieza gracias a las economías de escala.
- Operaciones secundarias: Los procesos adicionales, como el mecanizado, el tratamiento térmico o el acabado superficial, pueden aumentar el coste total de las piezas MIM.
Ventajas y desventajas de Moldeo por inyección de metales
Aunque el moldeo por inyección de metales ofrece numerosas ventajas, también tiene ciertas limitaciones. Comprender estos pros y contras es esencial para determinar si el MIM es el proceso de fabricación adecuado para una aplicación concreta.
Ventajas del moldeo por inyección de metales
Ventaja | Descripción |
---|---|
Geometría compleja | El MIM puede producir piezas con diseños intrincados y detalles finos difíciles de conseguir con otros métodos. |
Alta precisión | El proceso permite obtener tolerancias estrechas y dimensiones precisas, esenciales para aplicaciones críticas. |
Eficiencia material | El MIM genera un mínimo de residuos, lo que lo convierte en un proceso rentable y respetuoso con el medio ambiente. |
Versatilidad | El MIM es compatible con una amplia gama de materiales, lo que permite personalizar las propiedades de las piezas. |
Escalabilidad | El proceso es altamente escalable, por lo que resulta ideal para grandes series de producción. |
Desventajas del moldeo por inyección de metales
Desventaja | Descripción |
---|---|
Costes iniciales elevados | Los costes iniciales de utillaje y preparación del MIM pueden ser elevados, por lo que resulta menos económico para pequeñas series de producción. |
Limitaciones materiales | No todos los metales son aptos para el MIM, y el proceso puede no ser ideal para piezas muy grandes o muy pequeñas. |
Complejidad del desbobinado y la sinterización | Las fases de descortezado y sinterización requieren un control preciso para evitar defectos y garantizar una calidad constante. |
Requisitos de postprocesamiento | Algunas piezas pueden requerir mecanizado adicional, tratamiento térmico o acabado superficial, lo que aumenta el coste total. |
Duración del ciclo | El MIM suele tener ciclos más largos que el moldeo por inyección de plástico, debido al proceso adicional de sinterización. |
Flujo del proceso de moldeo por inyección de metales
Comprender el flujo del proceso de moldeo por inyección de metales es crucial para optimizar la producción y garantizar piezas de alta calidad. El proceso puede dividirse en varios pasos clave, cada uno de los cuales desempeña un papel fundamental en la calidad y el rendimiento del producto final.
1. Preparación de la materia prima
El primer paso del proceso MIM es preparar la materia prima, una mezcla de polvos metálicos y un sistema aglutinante. El aglutinante ayuda a unir las partículas metálicas, lo que permite moldearlas con la forma deseada. La materia prima suele prepararse mezclando el polvo metálico con el aglutinante a temperaturas elevadas para garantizar la homogeneidad.
2. Moldeo por inyección
Una vez preparada la materia prima, se introduce en una máquina de moldeo por inyección. La máquina calienta la materia prima a una temperatura en la que el aglutinante se vuelve fluido, lo que permite inyectar el material en la cavidad de un molde. El molde está diseñado para dar a la materia prima la geometría deseada, con características complejas y detalles finos. Tras la inyección, la pieza moldeada, conocida como "pieza verde", se enfría y se expulsa del molde.
3. Desencuadernación
La parte verde aún contiene una cantidad significativa de aglutinante, que debe eliminarse antes de la sinterización. El proceso de desaglomerado suele consistir en una combinación de extracción con disolvente y descomposición térmica. Durante la extracción con disolventes, la pieza se sumerge en un disolvente que disuelve el componente aglutinante primario. A continuación se procede a la descomposición térmica, en la que el aglutinante restante se elimina calentando la pieza en una atmósfera controlada.
4. Sinterización
Tras el desbobinado, la pieza se sinteriza a altas temperaturas, normalmente entre 1.200°C y 1.450°C, según el material. Durante la sinterización, las partículas metálicas se fusionan, dando lugar a una pieza densa y sólida con propiedades similares a las de los materiales forjados. El proceso de sinterización también hace que la pieza se encoja, normalmente entre 15 y 20%, lo que debe tenerse en cuenta durante el proceso de sinterización.
fase de diseño.
5. Tratamiento posterior
En algunos casos, las piezas MIM pueden requerir etapas adicionales de posprocesamiento para lograr las propiedades o el acabado deseados. Entre las operaciones de postprocesado más comunes se encuentran el mecanizado, el tratamiento térmico, el acabado superficial y el revestimiento. Estos pasos pueden ayudar a mejorar la precisión dimensional, las propiedades mecánicas y la estética de la pieza final.
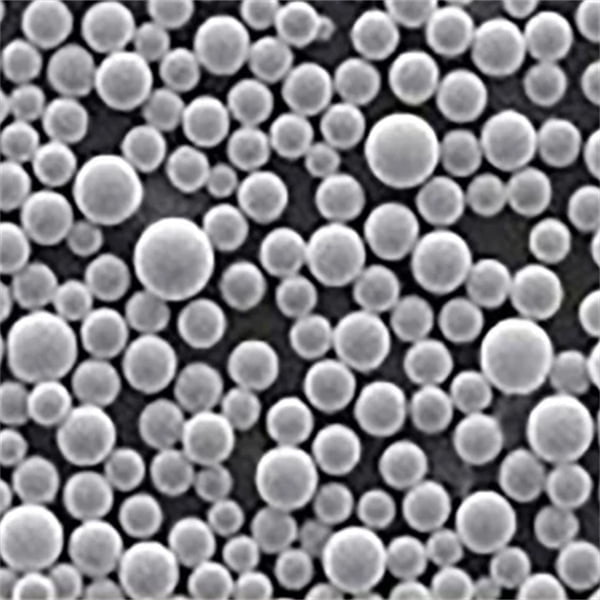
Preguntas frecuentes (FAQ)
Pregunta | Respuesta |
---|---|
¿Qué es el MIM? | El moldeo por inyección de metales (MIM) es un proceso de fabricación que combina las técnicas del moldeo por inyección de plásticos y la pulvimetalurgia para producir piezas metálicas complejas de gran precisión. |
¿Qué materiales pueden utilizarse en MIM? | En el MIM se puede utilizar una amplia gama de materiales, como acero inoxidable, titanio, cromo-cobalto y diversas aleaciones con base de níquel. |
¿Cuáles son las ventajas del MIM? | El MIM ofrece varias ventajas, como la capacidad de producir geometrías complejas, la alta eficiencia de los materiales y la escalabilidad para grandes series de producción. |
¿Cuáles son las limitaciones del MIM? | Algunas limitaciones del MIM son los elevados costes iniciales, las limitaciones de material y la necesidad de un control preciso durante los procesos de desbobinado y sinterización. |
¿En qué se diferencia el MIM de los métodos de fabricación tradicionales? | En comparación con los métodos tradicionales, como el mecanizado o la fundición, el MIM es más adecuado para la producción de grandes volúmenes de piezas complejas con tolerancias estrictas y desperdicios mínimos. |
¿Qué sectores utilizan el MIM? | El MIM se utiliza en diversas industrias, como la automovilística, aeroespacial, de dispositivos médicos, electrónica de consumo y armas de fuego. |
¿Cuáles son los tamaños típicos de las piezas MIM? | El tamaño de las piezas MIM suele oscilar entre 0,1 y 100 gramos, y algunos procesos pueden producir piezas de hasta 250 gramos. |
¿Se pueden postprocesar las piezas MIM? | Sí, las piezas MIM pueden someterse a etapas de postprocesado como mecanizado, tratamiento térmico y acabado superficial para mejorar sus propiedades y acabado. |
¿Cuál es el coste de las piezas MIM? | El coste de las piezas MIM varía en función del material, la complejidad y el volumen de producción. Sin embargo, el MIM suele ser rentable para grandes series de producción. |
¿Cuáles son las aplicaciones típicas del MIM? | Las aplicaciones típicas del MIM incluyen componentes de automoción, piezas aeroespaciales, dispositivos médicos y electrónica de consumo. |
Conclusiones
Moldeo por inyección de metales es un proceso de fabricación transformador que sigue ganando adeptos en una amplia gama de industrias. Su capacidad para producir piezas complejas de alto rendimiento con una precisión y una eficiencia de materiales excepcionales lo convierten en una valiosa herramienta para la fabricación moderna. A medida que avance la tecnología y se desarrollen nuevos materiales, las aplicaciones potenciales del MIM seguirán ampliándose.
Tanto si pertenece al sector de la automoción como al aeroespacial, médico o electrónico, conocer las capacidades y ventajas del MIM puede ayudarle a tomar decisiones informadas sobre sus procesos de fabricación. Gracias a su combinación única de versatilidad, escalabilidad y precisión, el moldeo por inyección de metales está llamado a desempeñar un papel fundamental en el futuro de la fabricación.
Acerca de 3DP mETAL
Categoría de productos
CONTÁCTANOS
¿Tienes alguna pregunta? ¡Envíanos un mensaje ahora! Después de recibir tu mensaje, procesaremos tu solicitud con todo un equipo.