Additive manufacturing, often referred to as 3D printing, has revolutionized the manufacturing landscape, enabling complex designs and reducing waste. A crucial element in this process is the powder used in additive manufacturing. This article delves into the intricacies of additive manufacturing powders, focusing on metal powders, their types, applications, and more.
Overview of Additive Manufacturing Powder
Additive manufacturing powders are finely divided materials used in various 3D printing technologies such as Selective Laser Melting (SLM), Electron Beam Melting (EBM), and Direct Metal Laser Sintering (DMLS). These powders can be made from metals, ceramics, polymers, or composites. Metal powders are particularly significant due to their extensive use in high-performance applications.
Points clés :
- Composition : Pure metals or metal alloys.
- Propriétés : High purity, spherical shape, narrow particle size distribution.
- Applications : Aerospace, automotive, healthcare, and industrial sectors.
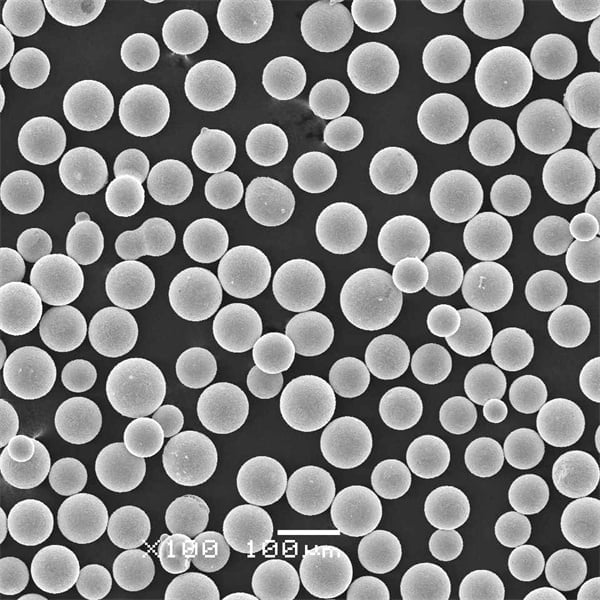
Types of Metal Powders in Additive Manufacturing
Metal powders are selected based on the specific requirements of the application, including mechanical properties, thermal properties, and corrosion resistance. Here are some common types of metal powders used in additive manufacturing:
Poudre métallique | Composition | Caractéristiques | APPLICATIONS |
---|---|---|---|
Titane (Ti-6Al-4V) | Titanium alloy with 6% aluminum and 4% vanadium | Rapport résistance/poids élevé, résistance à la corrosion | Aérospatiale, implants médicaux |
Aluminium (AlSi10Mg) | Aluminum alloy with silicon and magnesium | Léger, bonnes propriétés thermiques | Automobile, aérospatiale, biens de consommation |
Acier inoxydable (316L) | Iron alloy with chromium, nickel, and molybdenum | Résistance élevée à la corrosion, bonnes propriétés mécaniques | Dispositifs médicaux, transformation des aliments |
Inconel (IN718) | Alliage nickel-chrome | Résistance aux températures élevées, résistance à la corrosion | Aérospatiale, turbines à gaz |
Cuivre (Cu) | Pure copper | Excellente conductivité électrotechnique et thermique | Composants électriques, échangeurs de chaleur |
Cobalt-Chrome (CoCr) | Alliage cobalt-chrome | Résistance élevée à l'usure et à la corrosion, biocompatibilité | Dental implants, aerospace |
Acier à outils (H13) | Alloy steel with chromium, molybdenum, and vanadium | Dureté élevée, résistance à l'usure | Moules, matrices, outils de coupe |
Acier maraging (MS1) | Low-carbon steel with nickel, cobalt, and molybdenum | Ultra-high strength, excellent toughness | Aérospatiale, outillage |
Nickel Alloy (IN625) | Alliage nickel-chrome-molybdène | Excellent mechanical properties, high corrosion resistance | Traitement chimique, marin |
Tungstène (W) | Pure tungsten | Very high melting point, high density | Aérospatiale, défense |
Applications de la Poudre pour la fabrication additive
Additive manufacturing powders are pivotal in various sectors, offering unique advantages like lightweight structures, complex geometries, and customization. Here’s a closer look at where these powders are making an impact:
Secteur | Application | Avantages |
---|---|---|
Aérospatial | Composants du moteur, pièces structurelles | Weight reduction, fuel efficiency, complex geometries |
Automobile | Prototyping, custom parts | Rapid prototyping, reduced production time, improved performance |
Healthcare | Implants, prothèses, instrumentation chirurgicale | Customization, biocompatibility, reduced recovery time |
Industriel | Tooling, molds, production aids | Durability, wear resistance, cost-effectiveness |
Biens de consommation | Electronics, jewelry, fashion accessories | Customization, design flexibility, rapid manufacturing |
L'énergie | Aubes de turbines, échangeurs de chaleur | High-temperature performance, efficiency improvement |
Spécifications, tailles, qualités et normes
Selecting the right powder involves understanding various specifications, including particle size distribution, purity, and packing density. Here’s a table summarizing key specifications:
Poudre métallique | Taille des particules (µm) | Pureté (%) | Packing Density (g/cm³) | Grade/Standard |
---|---|---|---|---|
Titane (Ti-6Al-4V) | 15-45 | 99.5 | 2.6 | ASTM F2924-14 |
Aluminium (AlSi10Mg) | 20-63 | 99.9 | 1.2 | ISO 23510 |
Acier inoxydable (316L) | 15-45 | 99.5 | 4.0 | ASTM A276 |
Inconel (IN718) | 15-53 | 99.0 | 4.5 | AMS 5662 |
Cuivre (Cu) | 10-45 | 99.95 | 8.9 | ASTM B216 |
Cobalt-Chrome (CoCr) | 15-45 | 99.0 | 4.4 | ISO 5832-4 |
Acier à outils (H13) | 15-53 | 99.5 | 7.7 | ASTM A681 |
Acier maraging (MS1) | 20-53 | 99.0 | 7.9 | AMS 6514 |
Nickel Alloy (IN625) | 15-45 | 99.0 | 4.4 | AMS 5666 |
Tungstène (W) | 5-45 | 99.95 | 19.3 | ASTM B777 |
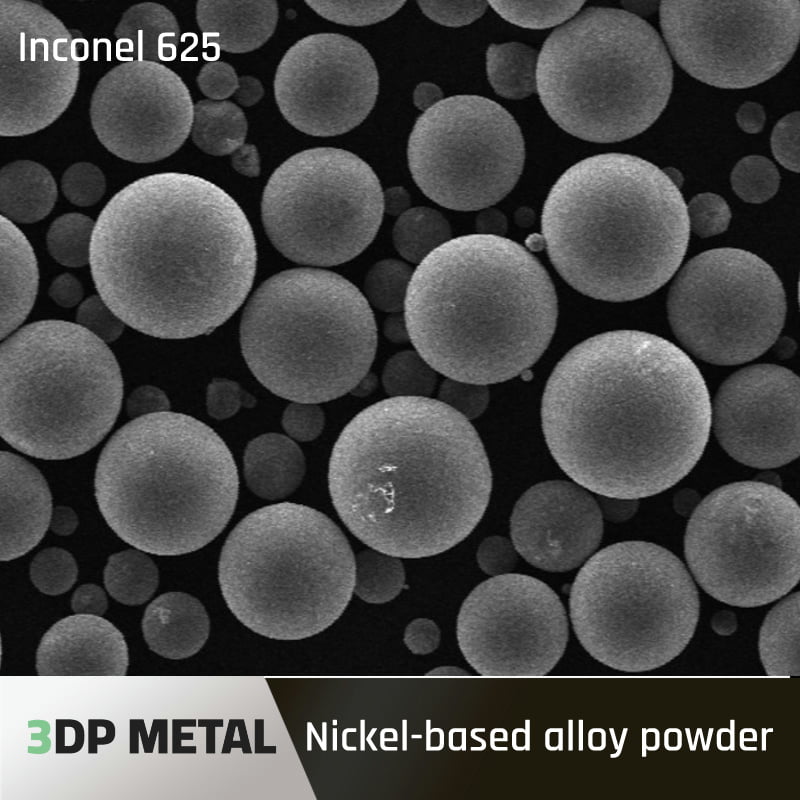
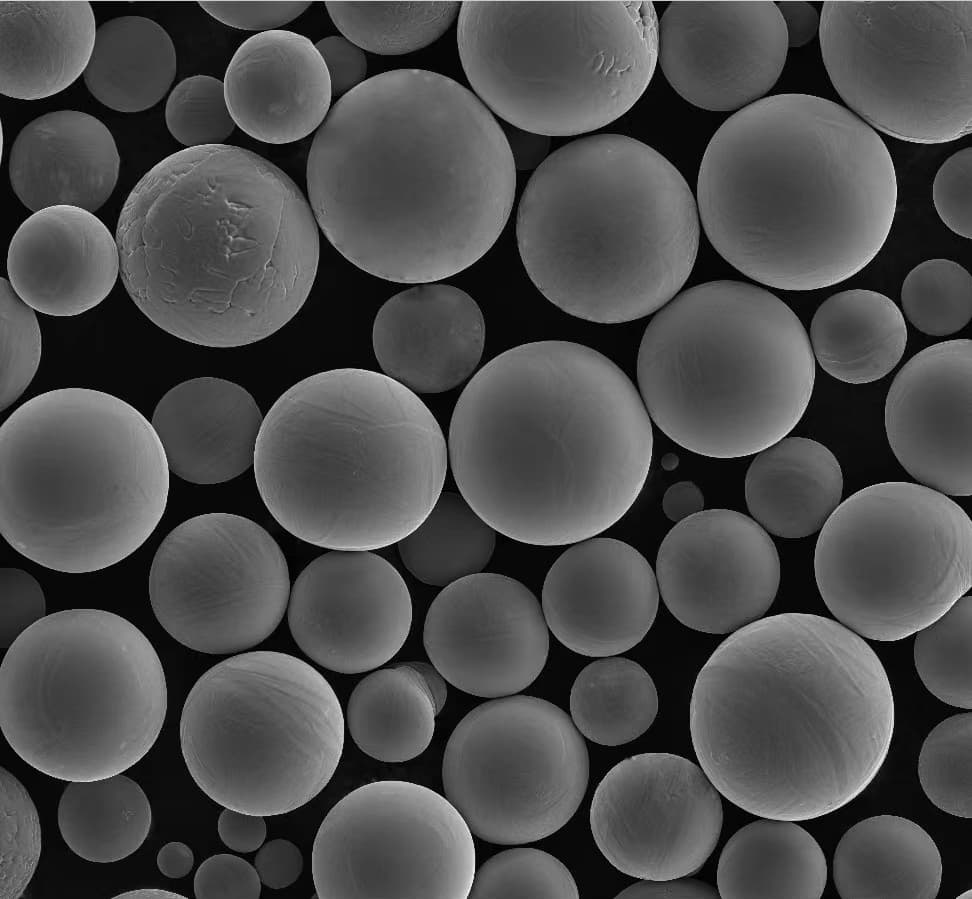
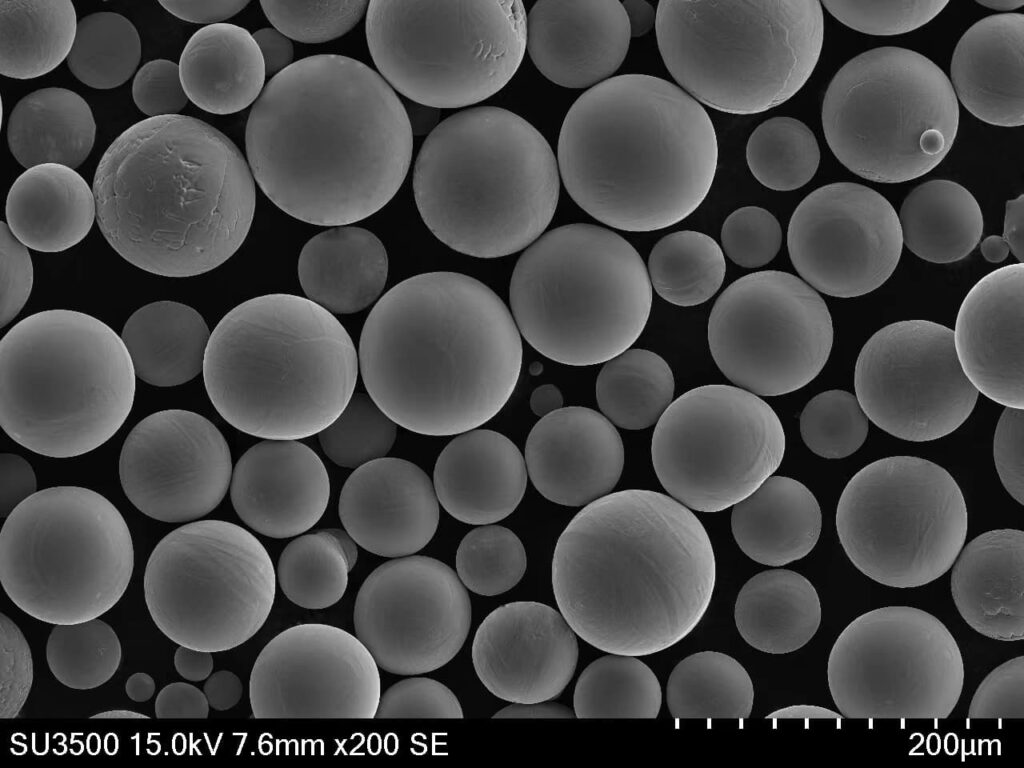
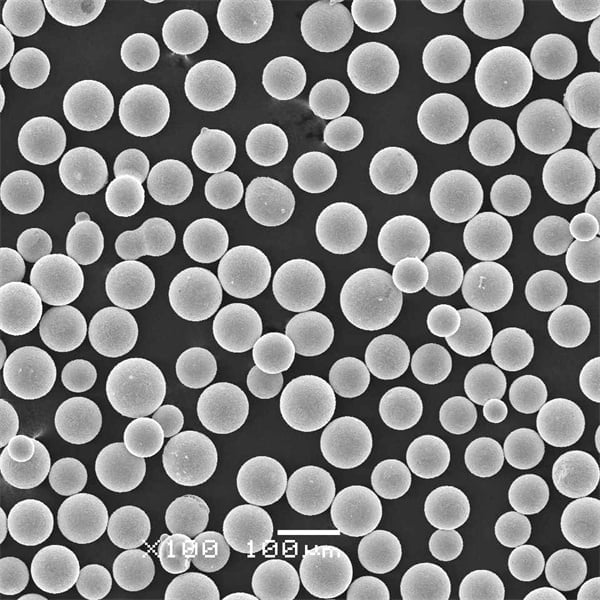
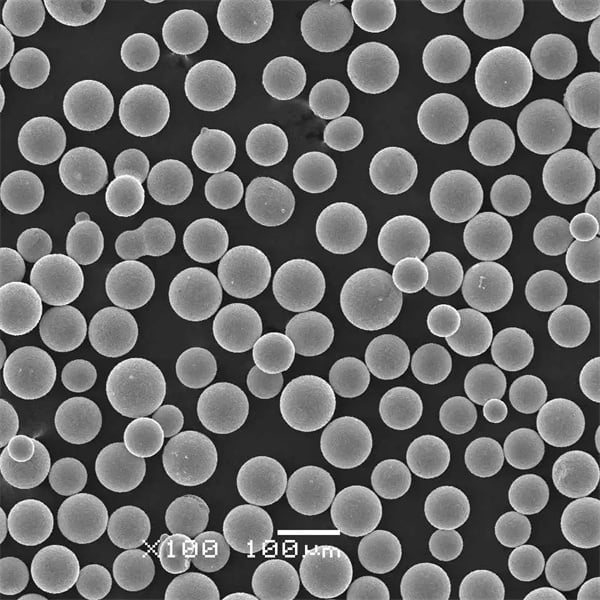
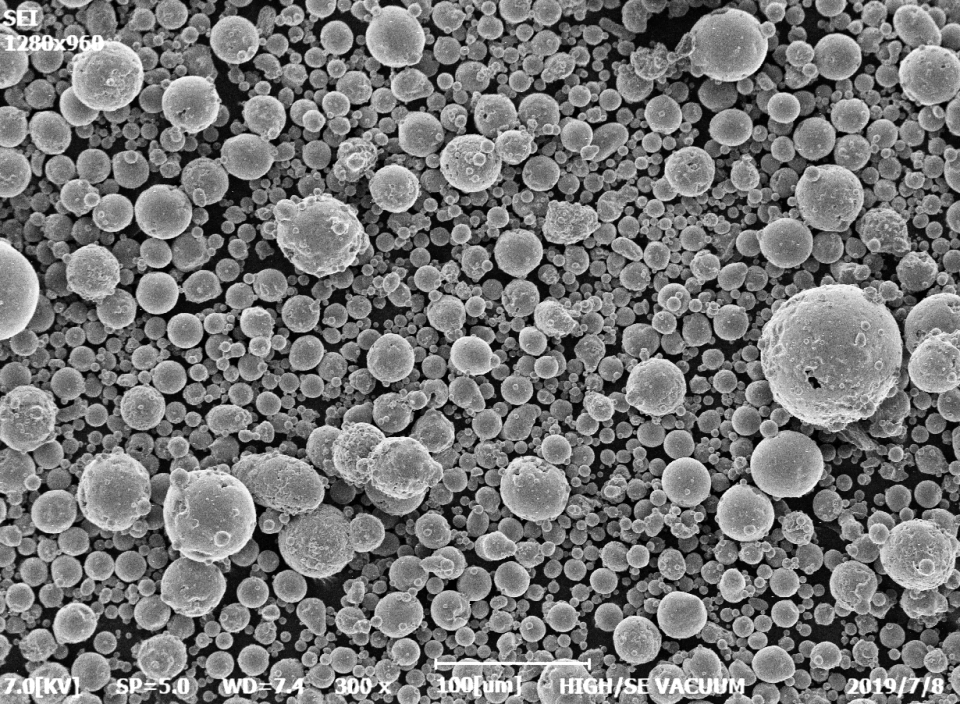
Fournisseurs et détails des prix
Choosing a reliable supplier is essential for ensuring consistent quality and performance of metal powders. Here’s a table listing some prominent suppliers along with estimated pricing:
Fournisseur | Poudre métallique | Fourchette de prix (par kg) | Région |
---|---|---|---|
Sandvik | Titane (Ti-6Al-4V) | $300 – $400 | Mondial |
Höganäs | Aluminium (AlSi10Mg) | $50 – $100 | Mondial |
Technologie des charpentiers | Acier inoxydable (316L) | $70 – $150 | Mondial |
Praxair | Inconel (IN718) | $150 – $250 | Amérique du Nord, Europe |
AMETEK | Cuivre (Cu) | $20 – $50 | Amérique du Nord, Europe |
Kennametal | Cobalt-Chrome (CoCr) | $200 – $300 | Mondial |
GKN Additive | Acier à outils (H13) | $80 – $120 | Mondial |
Technologie LPW | Acier maraging (MS1) | $100 – $200 | Europe, Amérique du Nord |
VDM Metals | Nickel Alloy (IN625) | $200 – $350 | Mondial |
Tungstène et poudres à l'échelle mondiale | Tungstène (W) | $400 – $600 | Mondial |
Avantages de la Poudre pour la fabrication additive
1. Design Flexibility
Additive manufacturing allows for intricate designs that are impossible to achieve with traditional methods. Complex geometries, internal structures, and lightweight designs become feasible, enhancing product performance.
2. Material Efficiency
Using metal powders minimizes waste, as the material is added layer by layer, unlike subtractive manufacturing where excess material is often discarded. This efficiency translates to cost savings and environmental benefits.
3. Rapid Prototyping and Production
The speed of producing prototypes and final parts is significantly increased. This rapid turnaround is crucial for industries like aerospace and automotive, where time-to-market is critical.
4. Customization and Personalization
Additive manufacturing excels in producing customized parts tailored to specific needs, such as medical implants designed for individual patients. This level of customization improves functionality and user satisfaction.
Disadvantages of Additive Manufacturing Powder
1. Initial Costs
The initial investment in additive manufacturing equipment and high-quality metal powders can be substantial. This barrier can be significant for small to medium-sized enterprises.
2. Limited Material Choices
While the range of available metal powders is expanding, it is still limited compared to traditional manufacturing materials. Not all metals and alloys are currently suitable for additive manufacturing.
3. Surface Finish and Post-Processing
Parts produced with metal powders often require post-processing to achieve the desired surface finish and mechanical properties. This additional step can increase production time and costs.
4. Technical Expertise
Operating additive manufacturing equipment and optimizing processes require a high level of technical expertise. Companies must invest in training or hire skilled personnel to maximize the technology’s potential.
Optimizing the Use of Poudre pour la fabrication additive
To fully harness the potential of additive manufacturing powders, consider the following strategies:
1. Powder Quality Control
Ensuring consistent powder quality is critical. This involves regular testing for particle size distribution, morphology, and purity to maintain high performance and avoid defects.
2. Process Parameter Optimization
Fine-tuning parameters such as laser power, scanning speed, and layer thickness can significantly impact the quality of the final product. Continuous monitoring and adjustments are necessary for optimal results.
3. Post-Processing Techniques
Effective post-processing can enhance the properties of 3D-printed parts. Techniques such as heat treatment, machining, and surface finishing are often required to meet final specifications.
4. Material Recycling
Implementing recycling strategies for unused powder can reduce costs and waste. However, careful management is required to avoid contamination and maintain powder quality.
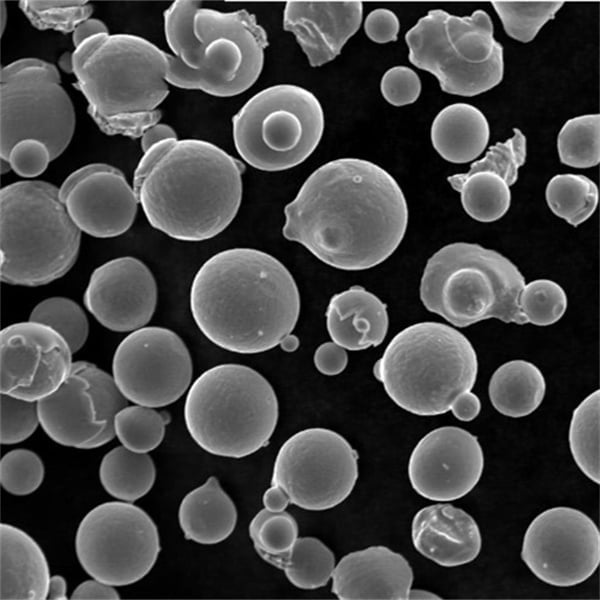
FAQ
Question | Réponse |
---|---|
What is additive manufacturing powder? | Fine metal powders used in 3D printing to create parts layer by layer through various technologies. |
How is powder quality controlled? | Through regular testing for particle size distribution, morphology, and purity. |
Quelles sont les applications courantes ? | Aerospace, automotive, healthcare, industrial, consumer goods, and energy sectors. |
What are the main advantages? | Design flexibility, material efficiency, rapid prototyping, customization. |
Quelles sont les limites ? | High initial costs, limited material choices, need for post-processing, technical expertise required. |
How do you optimize the use of these powders? | By ensuring powder quality, optimizing process parameters, effective post-processing, and recycling. |
Why is titanium powder used in medical implants? | Due to its biocompatibility, high strength-to-weight ratio, and corrosion resistance. |
What post-processing techniques are commonly used? | Heat treatment, machining, and surface finishing. |
How does powder recycling work? | Unused powder is collected, tested for quality, and reused to reduce costs and waste. |
Which industries benefit most from additive manufacturing? | Aerospace, automotive, and healthcare industries benefit significantly from the technology. |
Conclusion
Additive manufacturing powders, particularly metal powders, are central to the advancements in 3D printing technology. Their unique properties and capabilities enable the creation of complex, high-performance parts across various industries. By understanding the types, applications, and optimization techniques, businesses can fully leverage the benefits of additive manufacturing powders. Whether it’s the aerospace sector looking for lightweight, strong components or the medical field requiring customized implants, additive manufacturing powders provide the versatility and efficiency needed to meet these demands.
À propos de 3DP mETAL
Catégorie de produits
CONTACTEZ-NOUS
Des questions ? Envoyez-nous un message maintenant ! Après avoir reçu votre message, nous traiterons votre demande avec toute une équipe.