Avez-vous déjà rêvé de construire quelque chose couche par couche, avec du métal en fusion comme peinture et un bras robotisé comme pinceau ? Et bien.., Dépôt d'énergie dirigée (DED) fait de cette science-fiction une réalité. Le DED est un procédé d'impression 3D révolutionnaire qui transforme la fabrication, nous permettant de créer des structures métalliques complexes avec une précision et une flexibilité inégalées.
Cet article se penche sur le monde fascinant de la DED, en explorant ses principes fondamentaux, les avantages qu'elle offre par rapport aux méthodes traditionnelles et les diverses applications qu'elle trouve dans différents secteurs.
Le principe de base du dépôt par énergie dirigée (DED)
Imaginez un faisceau laser très puissant, comme une version suralimentée d'un pointeur laser, focalisé sur un point précis. Imaginez maintenant un fil ou une poudre métallique alimenté en continu par une buse située juste à côté du faisceau laser. Lorsque le faisceau laser frappe la matière première métallique, il la fait fondre instantanément. Ce métal en fusion est ensuite déposé méticuleusement sur une plate-forme, couche par couche, en suivant un plan numérique. Chaque couche se solidifiant rapidement, la structure 3D souhaitée prend forme.
Voici un aperçu des principaux éléments qui entrent en ligne de compte dans la détermination de l'âge de la retraite :
- Source d'énergie : Les lasers, les faisceaux d'électrons et les arcs de plasma sont les sources d'énergie les plus couramment utilisées en DED. Chacune offre des avantages et des considérations uniques, en fonction du matériau et de l'application souhaités.
- Matière première : DED peut traiter une grande variété d'alliages métalliques, notamment le titane, l'acier, l'aluminium et les superalliages de nickel. Le choix du matériau dépend des propriétés souhaitées pour le produit final, telles que la solidité, le poids et la résistance à la corrosion.
- Système de livraison : La buse joue un rôle crucial en guidant le matériau de base dans la trajectoire de la source d'énergie et en assurant un dépôt précis.
- Contrôle informatique : L'ensemble du processus DED est minutieusement contrôlé par un logiciel. Ce logiciel traduit le fichier de conception 3D en une série d'instructions, dictant le mouvement du bras robotique, la puissance de la source d'énergie et le débit de la matière première.
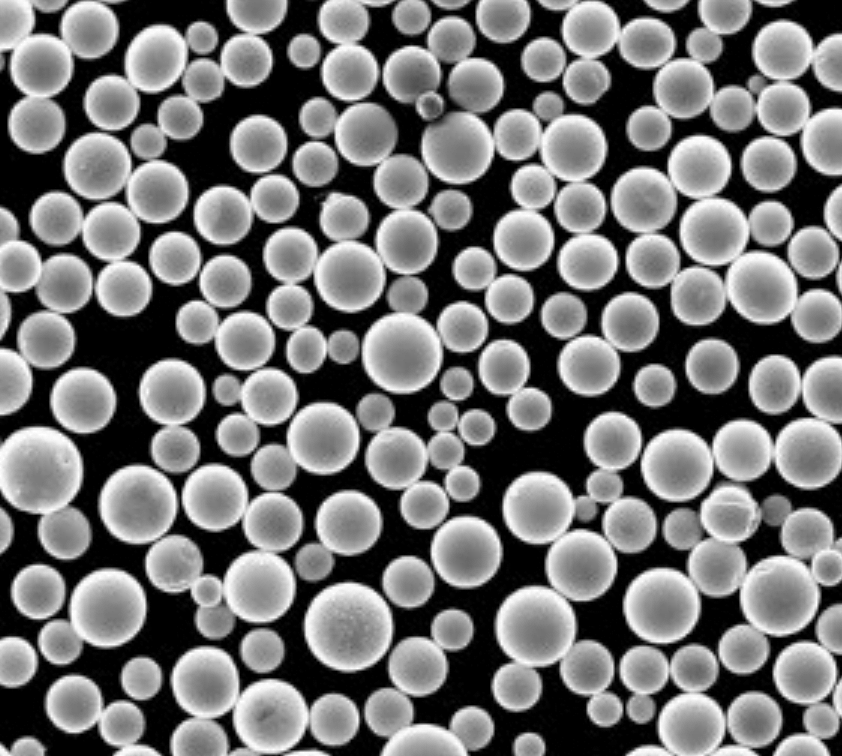
Avantages du dépôt d'énergie dirigée (DED)
Le DED offre un ensemble d'avantages convaincants par rapport aux méthodes de fabrication traditionnelles telles que l'usinage et le moulage. Examinons quelques-uns de ces avantages :
- Liberté de conception : Contrairement aux techniques soustractives telles que l'usinage, la DED est additive. Cela signifie que vous n'êtes pas limité par la forme initiale d'un bloc de matière première. La DED permet de créer des géométries complexes avec des caractéristiques internes et des détails complexes qu'il serait impossible ou très coûteux de réaliser avec les méthodes traditionnelles.
- Efficacité matérielle : La technique DED offre une efficacité exceptionnelle en matière de matériaux. Grâce à un dépôt précis, les déchets sont minimes par rapport aux techniques soustractives qui génèrent une quantité importante de ferraille. Cela se traduit par des économies et un processus plus respectueux de l'environnement.
- Structures légères : DED excelle dans la création de structures à la fois légères et solides. En concevant stratégiquement des caractéristiques internes creuses, les pièces DED peuvent atteindre des rapports poids/résistance exceptionnels, ce qui les rend idéales pour des applications telles que l'aérospatiale et les transports.
- Prototypage rapide : Le DED permet de créer rapidement des prototypes fonctionnels directement à partir de modèles numériques. Il n'est donc plus nécessaire de recourir à de longs processus d'outillage, ce qui accélère le cycle de conception et de développement.
- Fabrication en forme de filet : La technologie DED permet de produire des pièces très proches de leurs dimensions finales, ce qui minimise la nécessité de recourir à des étapes de post-traitement approfondies telles que l'usinage. Cela se traduit par des délais de production plus courts et des coûts globaux moins élevés.
- Réparation et restauration : La capacité du DED à déposer des matériaux avec précision le rend idéal pour réparer les composants métalliques endommagés. Cela permet de prolonger la durée de vie des équipements existants et de réduire la nécessité de les remplacer complètement.
Applications du dépôt d'énergie dirigée (DED)
La polyvalence de la DED est vraiment remarquable. Voici un aperçu de quelques-unes des applications passionnantes dans différents secteurs :
- Aérospatial : Le DED est utilisé pour créer des composants légers et très résistants pour les avions, tels que des supports, des nervures d'aile et des pièces de moteur. Cette technologie contribue à optimiser le rendement énergétique et les performances de l'industrie aérospatiale.
- Automobile : Le DED trouve des applications dans la création de pièces personnalisées pour les véhicules de course et dans la réparation de composants endommagés dans les voitures à hautes performances.
- Médical : La DED révolutionne le domaine médical en permettant la création de prothèses et d'implants sur mesure, parfaitement adaptés à chaque patient.
- Pétrole et gaz : Le DED est utilisé pour réparer et revêtir des composants critiques dans l'industrie du pétrole et du gaz, afin de prolonger leur durée de vie et d'améliorer leur résistance aux environnements difficiles.
- Outillage : Le DED peut être utilisé pour créer des moules et des matrices complexes avec des canaux de refroidissement conformes, améliorant ainsi l'efficacité et la vitesse de production dans divers processus de fabrication.
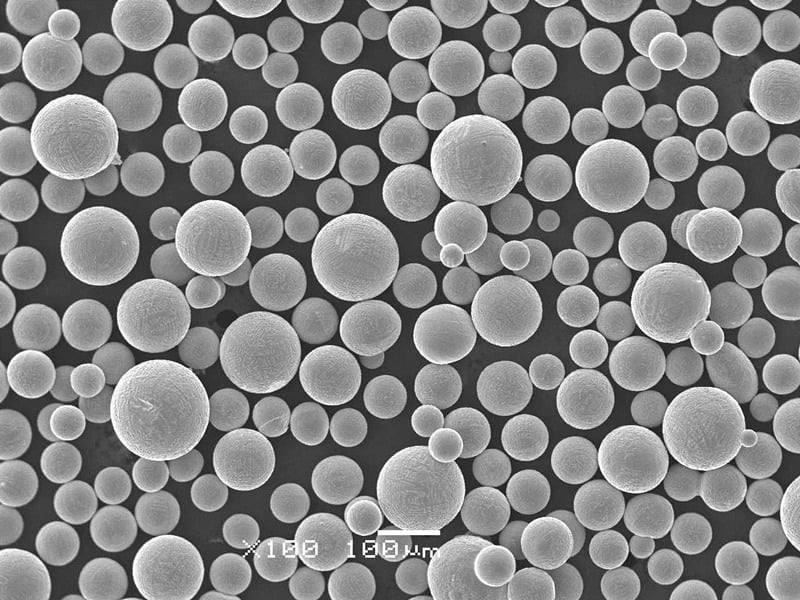
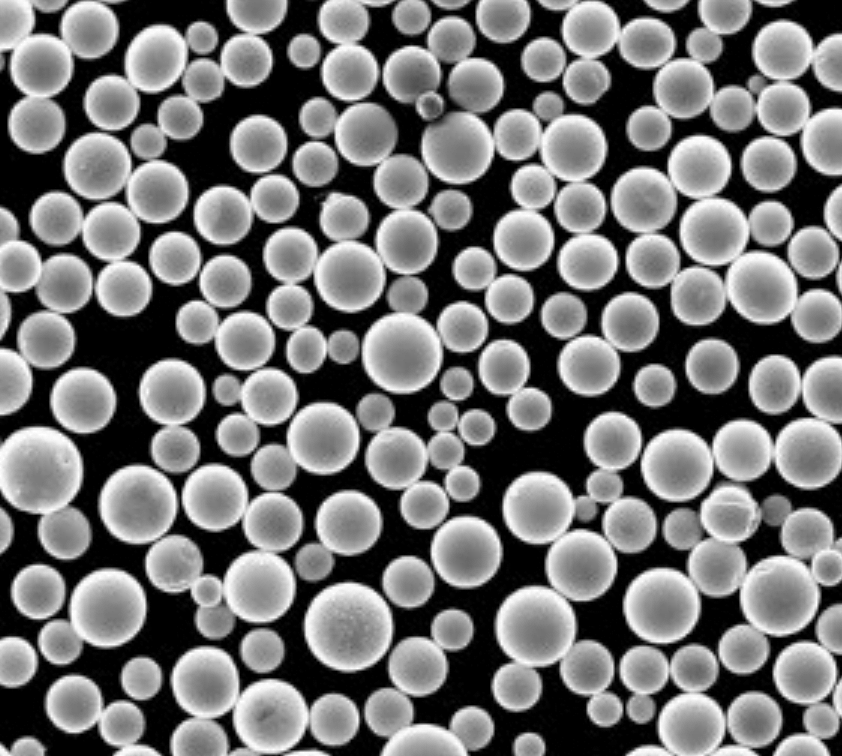
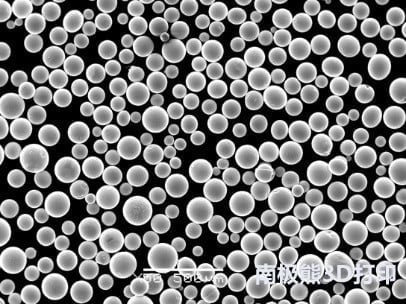
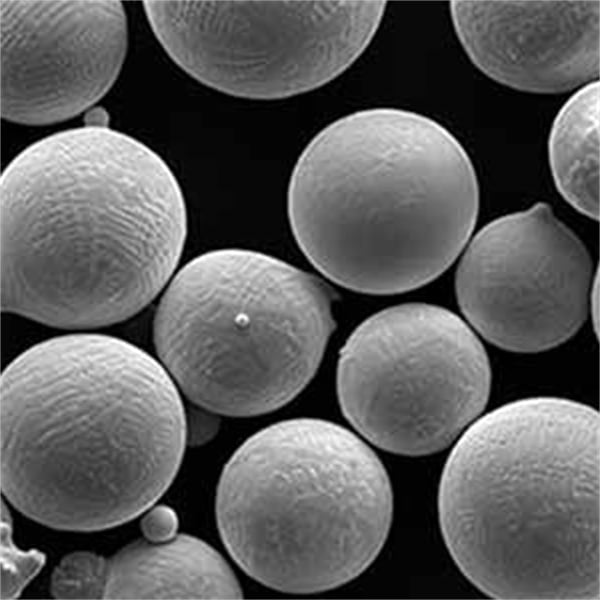
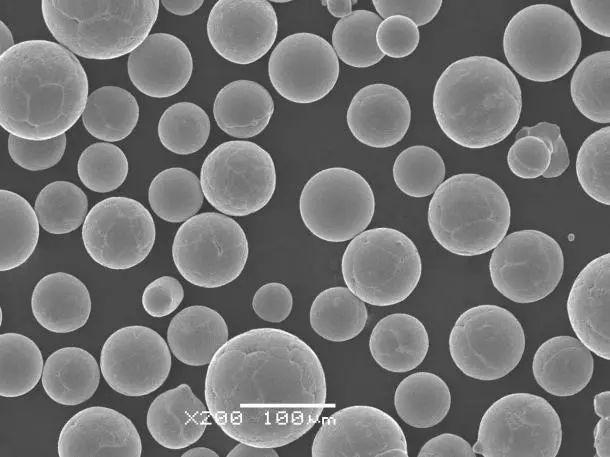
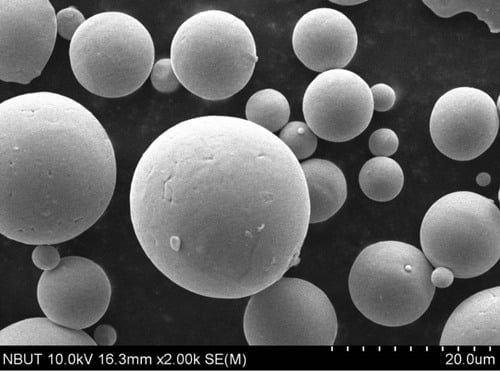
Considérations relatives au DED
Bien que le DED offre de nombreux avantages, il est essentiel de prendre en compte certains facteurs clés avant de se lancer dans cette technologie.
Coût : Les machines DED peuvent être coûteuses par rapport aux équipements de fabrication traditionnels. Toutefois, les économies réalisées sur l'efficacité des matériaux, la liberté de conception et la réduction du post-traitement peuvent faire du DED un choix convaincant à long terme, en particulier pour les pièces complexes de grande valeur.
Propriétés des matériaux et considérations relatives à la DED
La capacité du procédé DED à travailler avec une large gamme de métaux est un avantage significatif. Toutefois, il est essentiel de comprendre comment le processus DED peut affecter les propriétés matérielles du produit final par rapport aux méthodes traditionnelles. Voici quelques éléments clés à prendre en compte :
- Structure du grain : La fusion et la solidification rapides du métal dans le procédé DED peuvent donner lieu à une structure de grain plus fine que celle des métaux coulés ou corroyés. Cette structure de grain plus fine peut améliorer les propriétés mécaniques telles que la résistance et la ductilité de la pièce DED. Toutefois, elle peut également rendre le matériau plus sensible à la fissuration sous contrainte dans certaines applications.
- Contrainte résiduelle : Le processus DED implique un chauffage et un refroidissement localisés qui peuvent introduire des contraintes résiduelles dans la pièce. Des contraintes résiduelles non contrôlées peuvent entraîner des déformations et des distorsions. Les procédés DED intègrent souvent des traitements thermiques post-dépôt afin de gérer les contraintes résiduelles et d'optimiser les propriétés finales de la pièce.
- Finition de la surface : L'état de surface d'une pièce DED dépend de plusieurs facteurs, notamment de la source d'énergie, du matériau de base et des paramètres de dépôt. Les pièces DED peuvent avoir un état de surface légèrement plus rugueux que les pièces usinées. Toutefois, des techniques de post-traitement telles que l'usinage ou le polissage peuvent être utilisées pour obtenir un état de surface plus lisse si l'application l'exige.
Différentes techniques DED et leurs applications
Si le principe de base de la DED reste le même, il existe plusieurs variantes de la technologie en fonction de la source d'énergie utilisée. Voici un aperçu des trois principales techniques DED :
- DED laser (L-DED) :
- Utilise un faisceau laser de haute puissance comme source d'énergie.
- Il offre un excellent contrôle et une grande précision, ce qui le rend adapté à la création de géométries et de caractéristiques complexes.
- Bien adapté aux applications nécessitant des finitions de surface de haute qualité, telles que les implants médicaux et les composants aérospatiaux.
- Par rapport à d'autres techniques DED, la L-DED peut être limitée en termes de vitesse de dépôt et peut ne pas être idéale pour des applications à grande échelle.
- DED par faisceau d'électrons (EB-DED) :
- Utilise un faisceau d'électrons focalisé dans une chambre à vide pour faire fondre le matériau de base.
- Offre une pénétration plus profonde et des taux de dépôt plus élevés par rapport à la L-DED.
- EB-DED est donc un bon choix pour créer des structures à parois épaisses et réparer des composants de grande taille.
- Cependant, l'exigence d'une chambre à vide ajoute de la complexité et du coût au processus EB-DED.
- DED par arc plasma (PA-DED) :
- Utilise un arc plasma à haute température comme source d'énergie.
- Elle offre les taux de dépôt les plus rapides parmi les techniques DED, ce qui la rend adaptée aux applications à grande échelle et à haut débit.
- La PA-DED peut également traiter une gamme plus large de matières premières métalliques par rapport à la L-DED et à l'EB-DED.
- Cependant, la PA-DED peut avoir une zone de chaleur plus large que les autres techniques DED, ce qui conduit à une finition de surface plus rugueuse et à une taille de grain potentiellement plus importante dans le matériau déposé.
L'avenir du dépôt d'énergie dirigée
La technologie DED est encore relativement jeune et présente un immense potentiel de croissance et d'innovation. Voici quelques tendances passionnantes qui façonnent l'avenir de la DED :
- DED multi-matériaux : Les chercheurs étudient les moyens de combiner différentes techniques DED ou même d'intégrer la DED à d'autres procédés de fabrication additive pour créer des pièces multi-matériaux avec des propriétés adaptées dans différentes régions. Imaginez un composant aérospatial léger doté d'un noyau à haute résistance et d'une couche extérieure résistante à la corrosion, le tout fabriqué au cours d'un seul processus DED.
- Procédés hybrides DED : L'intégration de la DED avec des technologies d'usinage ou de surveillance in situ est très prometteuse. Le contrôle des processus en temps réel et les capacités de fabrication adaptative permettraient aux DED de produire des pièces de haute qualité avec une précision et une efficacité encore plus grandes.
- Normalisation et qualification : Au fur et à mesure de l'adoption de la technologie DED, la mise en place de processus normalisés et de procédures de qualification sera cruciale. Cela garantira la fiabilité et la répétabilité des pièces DED pour les applications critiques dans des secteurs tels que l'aérospatiale et la médecine.
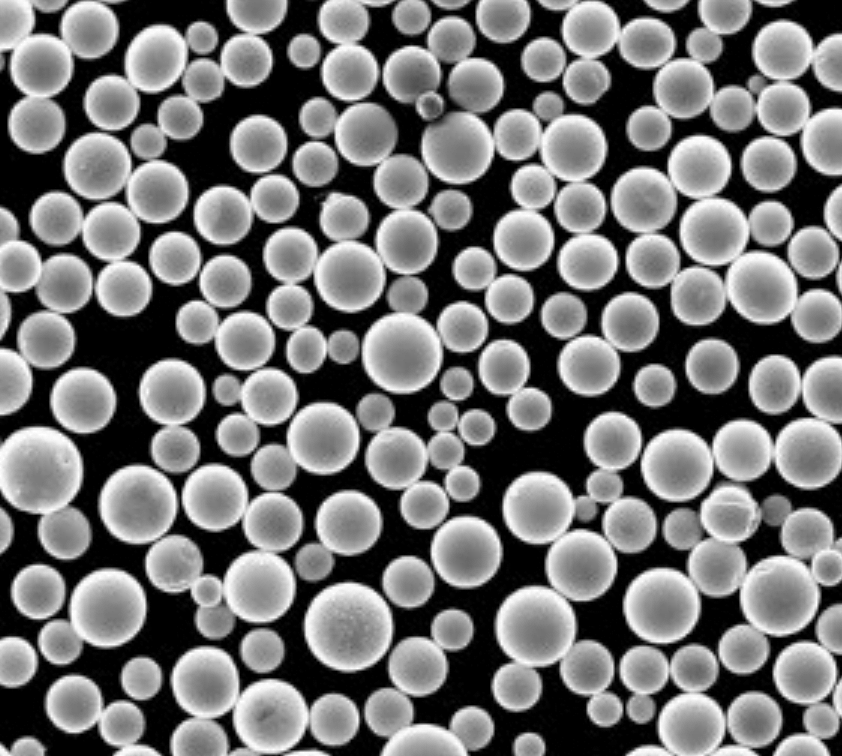
FAQ
Question | Réponse |
---|---|
Quels sont les avantages du DED par rapport aux méthodes de fabrication traditionnelles ? | Le DED offre la liberté de conception, l'efficacité des matériaux, la capacité de créer des structures légères, le prototypage rapide, la fabrication de formes presque nettes et les capacités de réparation. |
Quelles sont les applications du DED ? | Le DED est utilisé dans les secteurs de l'aérospatiale, de l'automobile, de la médecine, du pétrole et du gaz, et de l'outillage. |
Quels sont les facteurs à prendre en compte lors de l'utilisation du DED ? | Le coût, les propriétés du matériau (structure du grain, contraintes résiduelles, finition de surface) et le choix de la technique DED (laser, faisceau d'électrons, arc plasma) sont des éléments importants à prendre en compte. |
À propos de 3DP mETAL
Catégorie de produits
CONTACTEZ-NOUS
Des questions ? Envoyez-nous un message maintenant ! Après avoir reçu votre message, nous traiterons votre demande avec toute une équipe.