Imagine crafting intricate, high-performance metal parts with near-net shapes and exceptional mechanical properties. That’s the magic of Metal Injection Molding (MIM), and Poudre d'inconel 718 takes this technology to a whole new level. Buckle up, because we’re diving deep into the world of Inconel 718 powder for MIM, exploring its potential, applications, and the nitty-gritty details you need to know.
Understanding the Inconel 718 Powder
Inconel 718, a nickel-chromium superalloy, reigns supreme in demanding environments. Picture this: scorching jet engines, pressure-laden oil rigs, or the heart of a nuclear power plant. Inconel 718 stands up to extreme heat, corrosion, and stress like a champ. Its secret lies in its unique blend of elements:
- Nickel (Ni) : The foundation, providing strength and ductility.
- Chrome (Cr) : The shield, forming a protective oxide layer that resists corrosion.
- Molybdène (Mo) : The muscle, enhancing high-temperature strength.
- Niobium (Nb): The refiner, promoting grain refinement and strengthening the microstructure.
These elements, along with others like iron and titanium, work together to create a material that’s truly exceptional.
Metal Injection Molding (MIM): The Art of Shaping Metal Powder
MIM, a near-net shaping technology, takes metal powder and transforms it into complex, intricate parts. Think of it like baking a cake – you start with a powder (flour), mix it with a binder (wet ingredients), shape it (molding), and then remove the binder (baking) to reveal the final product. In MIM, the metal powder is mixed with a binder to create a feedstock that can be injected into a mold. After shaping, the binder is removed through a thermal debinding process, leaving behind a near-net shape metal part. Finally, sintering – a high-temperature treatment – densifies the part, enhancing its strength and properties.
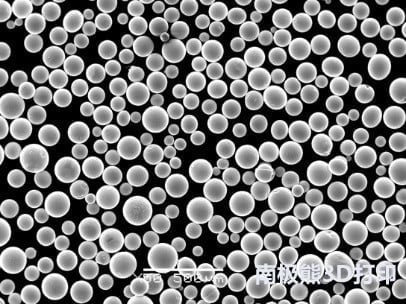
Poudre d'Inconel 718 and MIM
So, why is Inconel 718 powder a perfect match for MIM? Here’s the beauty:
- Formes complexes : Inconel 718 powder, with its fine particle size, allows for intricate and near-net shape parts, eliminating the need for complex machining. Imagine crafting tiny turbine blades or intricate aerospace components – MIM with Inconel 718 powder makes it possible!
- Propriétés exceptionnelles : MIM preserves the outstanding mechanical properties of Inconel 718, including high strength, corrosion resistance, and excellent performance at elevated temperatures.
- Production de masse : MIM enables efficient mass production of complex Inconel 718 parts, making it a cost-effective alternative to traditional manufacturing methods like machining or forging.
Specific Inconel 718 Powder Models
Now, let’s delve into the world of specific Inconel 718 powder models. Here are 10 popular options, each with its own unique characteristics:
Modèle | Description | Caractéristiques principales |
---|---|---|
AMCP AM 718 | A gas-atomized Inconel 718 powder with excellent flowability and packing density, ideal for complex geometries. | – High sphericity for smooth flow – Consistent particle size distribution – Good sintering response |
Höganäs AM 267 | A nitrogen-atomized Inconel 718 powder known for its high purity and cleanliness, leading to superior mechanical properties. | – Low oxygen and nitrogen content – Tight particle size distribution – Excellent for demanding applications |
Carpenter Inj718 | A gas-atomized Inconel 718 powder specifically designed for MIM, offering good flowability and a well-defined microstructure. | – Optimized for MIM process – Consistent flow characteristics – Predictable sintering behavior |
Materion MEtalMIM 718 | A gas-atomized Inconel 718 powder with a focus on achieving high density and strength after sintering. | – Promotes densification during sintering – Delivers excellent mechanical properties – Suitable for high-performance applications |
Special Metals AM718 | A nitrogen-atomized Inconel 718 powder known for its exceptional wear resistance and high fatigue strength. | – Enhanced wear properties – Superior fatigue performance – Ideal for components under heavy wear and tear |
Admatec MIM 718 | A gas-atomized Inconel 718 powder formulated for excellent mold filling capability, crucial for intricate parts. | – Optimized flow for complex geometries – Reduces molding defects – Enables near-net shape production |
Sandvik Osprey AM 718 | A nitrogen-atomized Inconel 718 powder recognized for its superior surface finish and good corrosion resistance. | – Produces parts with smooth surfaces – Enhances resistance to corrosive environments – Ideal for applications requiring a polished look and corrosion protection |
AP&C AP MIM 718 | A gas-atomized Inconel 718 powder with a focus on cost-effectiveness while maintaining good mechanical properties. | – Balanced cost and performance – Suitable for mid-range applications – Offers a cost-competitive option |
Praxair AM 718 | A gas-atomized Inconel 718 powder known for its tight chemistry control, ensuring consistent material properties. | – Precise control over element composition – Predictable material behavior – Ideal for applications requiring consistent performance |
Factors to Consider When Selecting Poudre d'Inconel 718
With an arsenal of Inconel 718 powder models at your disposal, how do you pick the right one for your project? Here are some crucial factors to weigh:
- Complexité des pièces : Highly intricate geometries might require powders with exceptional flowability like Admatec MIM 718 or AMCP AM 718.
- Performance Requirements: For applications demanding the highest strength and wear resistance, consider powders like Special Metals AM718 or Höganäs AM 267.
- Finition de la surface : If a smooth, polished surface is critical, Sandvik Osprey AM 718 or powders with a focus on surface finish might be ideal.
- Considérations relatives aux coûts : AP&C AP MIM 718 offers a balance between cost and performance, while Carpenter Inj718 is specifically designed for cost-effective MIM processing.
- Supplier Capabilities: Research the reputation and expertise of potential powder suppliers. Look for companies with experience in Inconel 718 powder production and a commitment to quality control.
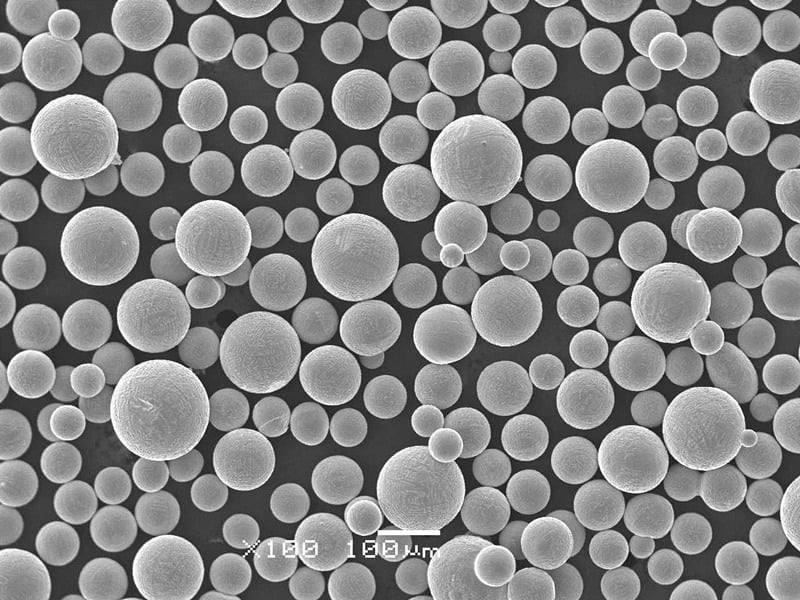
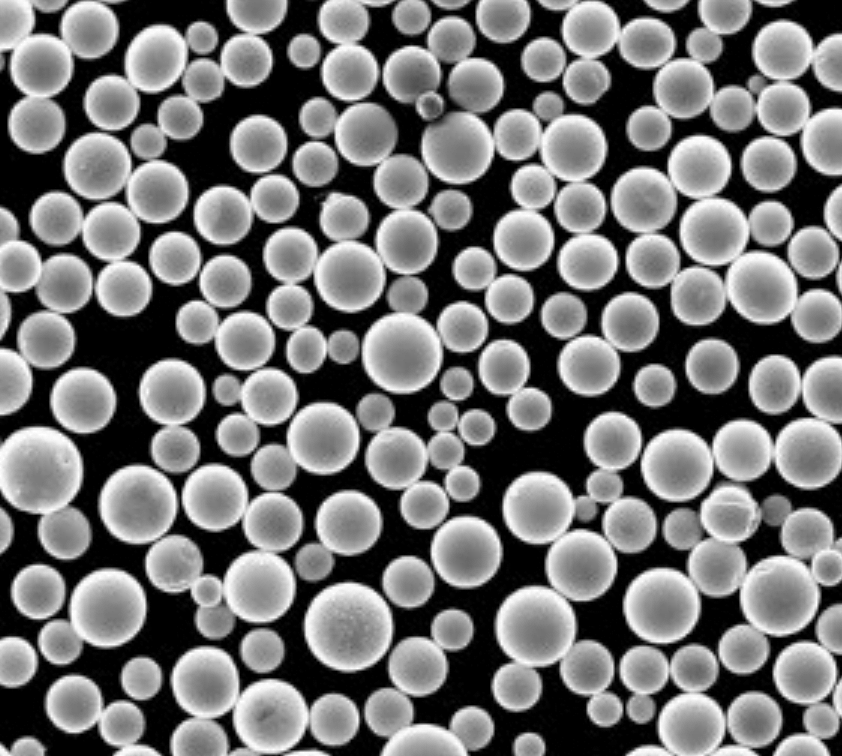
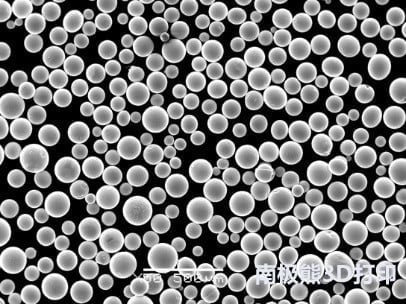
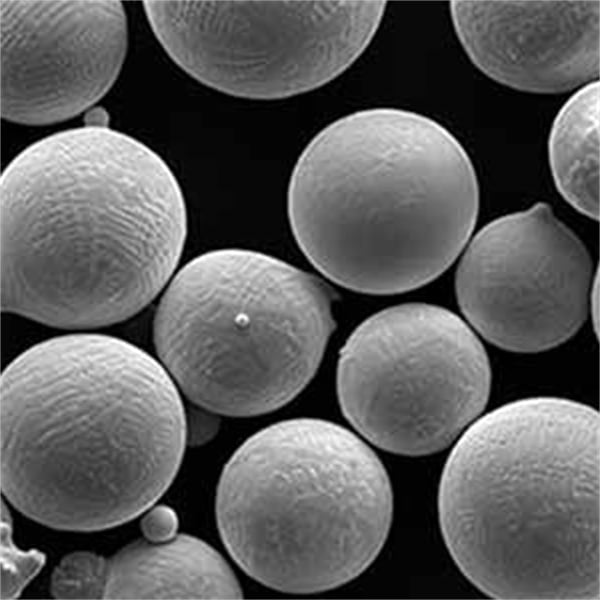
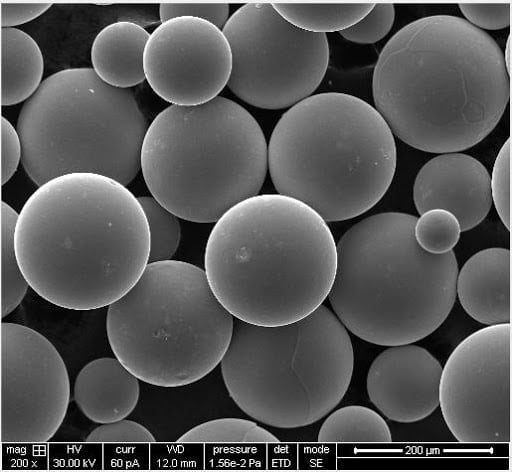
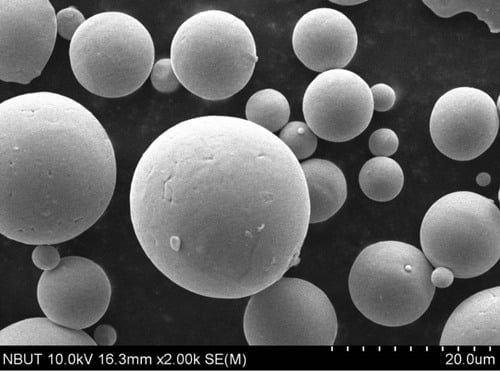
Applications of Inconel 718 Powder via MIM
Inconel 718 powder, when harnessed through MIM, unlocks a treasure trove of potential applications across various industries:
- Aérospatial : Turbine blades, valves, and other high-temperature, high-stress components in jet engines and spacecraft benefit from Inconel 718’s exceptional performance.
- Pétrole et gaz : Downhole tools, wellhead components, and valves used in harsh downhole environments require the strength and corrosion resistance of Inconel 718.
- Dispositifs médicaux : Surgical instruments, implants, and other medical devices demanding biocompatibility and durability can be crafted from Inconel 718 powder.
- Traitement chimique : Pumps, valves, and other components exposed to aggressive chemicals can leverage Inconel 718’s superior corrosion resistance.
- Électronique : Heat sinks and other components operating at high temperatures can be manufactured using MIM with Inconel 718 powder.
Advantages of Using Poudre d'Inconel 718 for MIM
Here’s a breakdown of the compelling advantages that make Inconel 718 powder a champion in the MIM arena:
- Géométries complexes : MIM with Inconel 718 powder allows for the creation of intricate near-net shape parts, reducing the need for complex and expensive machining.
- Exceptional Mechanical Properties: Parts produced through MIM retain the outstanding mechanical properties of Inconel 718, including high strength, excellent high-temperature performance, and superior corrosion resistance.
- Production de masse : MIM facilitates the cost-effective mass production of complex Inconel 718 parts, making it a viable alternative to traditional manufacturing methods.
- Flexibilité de la conception : MIM with Inconel 718 powder offers greater design freedom compared to conventional techniques, enabling the creation of intricate features and internal channels.
- Efficacité matérielle : MIM minimizes material waste compared to traditional methods like machining, leading to a more sustainable manufacturing process.
Disadvantages and Considerations
While Inconel 718 powder for MIM boasts a plethora of advantages, it’s essential to acknowledge some limitations and considerations:
- Higher upfront costs: Setting up MIM infrastructure can be more expensive compared to traditional techniques. However, these costs can be offset by the efficiency and reduced waste associated with MIM for high-volume production.
- Part size limitations: Current MIM technology might not be suitable for very large or very small parts. The ideal size range for MIM with Inconel 718 powder typically falls within a few millimeters to several centimeters.
- Finition de la surface : While some Inconel 718 powder models offer good surface finishes, MIM parts might require additional post-processing steps like polishing or machining to achieve a desired aesthetic or tighter tolerances.
- Propriétés du matériau : Although MIM preserves many of Inconel 718’s properties, there might be slight variations in grain structure and mechanical properties compared to wrought forms of Inconel 718. This is a crucial factor to consider for applications demanding the absolute peak performance.
- Complexité du processus : MIM is a multi-step process requiring careful control over each stage, from feedstock preparation to debinding and sintering. Partnering with an experienced MIM manufacturer is vital to ensure consistent quality and successful outcomes.
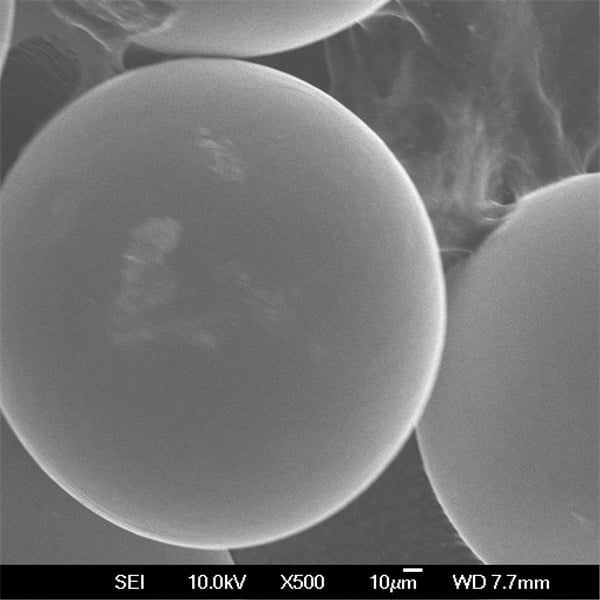
FAQ
Q: Is Inconel 718 powder for MIM stronger than machined Inconel 718?
A: In most cases, the mechanical properties of MIM-produced Inconel 718 are comparable to machined Inconel 718. However, slight variations in grain structure due to the MIM process might exist. For applications requiring the absolute highest strength, wrought Inconel 718 might be a better choice.
Q: Can Inconel 718 powder be used for 3D printing?
A: Yes, Inconel 718 powder can be used in some 3D printing techniques like laser beam melting (LBM). However, 3D printing of Inconel 718 can be more challenging compared to MIM due to factors like higher laser power requirements and potential for cracking during the process. MIM offers a more established and potentially more cost-effective solution for complex Inconel 718 parts.
Q: How does the cost of Inconel 718 powder for MIM compare to other manufacturing methods?
A: For high-volume production of complex parts, MIM with Inconel 718 powder can be more cost-effective than traditional methods like machining or forging. The upfront costs of MIM setup might be higher, but these are balanced by the efficiency and reduced waste associated with MIM.
Q: What are some of the future advancements expected in MIM with Inconel 718 powder?
A: Research and development are ongoing to improve the capabilities of MIM with Inconel 718 powder. This includes advancements in powder technology for even better flowability and packing density, leading to more intricate geometries. Additionally, there’s a focus on optimizing the MIM process to achieve even closer mechanical properties to wrought Inconel 718.
À propos de 3DP mETAL
Catégorie de produits
CONTACTEZ-NOUS
Des questions ? Envoyez-nous un message maintenant ! Après avoir reçu votre message, nous traiterons votre demande avec toute une équipe.