Vue d'ensemble Moulage par injection de métal (MIM)
Le moulage par injection de métal (MIM) est un procédé de fabrication qui combine la polyvalence du moulage par injection de plastique avec la résistance et l'intégrité du métal. Ce procédé permet la production en masse de composants métalliques complexes qui seraient difficiles, coûteux, voire impossibles à produire par des méthodes traditionnelles. Le MIM est particulièrement avantageux pour la création de petites pièces complexes d'une grande précision et dotées d'excellentes propriétés mécaniques.
Le processus MIM commence par le mélange de poudres métalliques et d'un matériau liant pour créer une matière première, qui est ensuite injectée dans un moule pour former la forme souhaitée. La pièce moulée, appelée "pièce verte", subit un déliant pour éliminer le liant, puis un frittage pour densifier la poudre métallique, ce qui permet d'obtenir un composant final qui correspond étroitement aux spécifications de la conception d'origine.
Ce processus est très apprécié dans des secteurs tels que l'automobile, l'aérospatiale, les appareils médicaux, l'électronique et les biens de consommation, en raison de sa capacité à produire des pièces métalliques complexes à haute résistance à un coût inférieur à celui de l'usinage ou du moulage traditionnels.
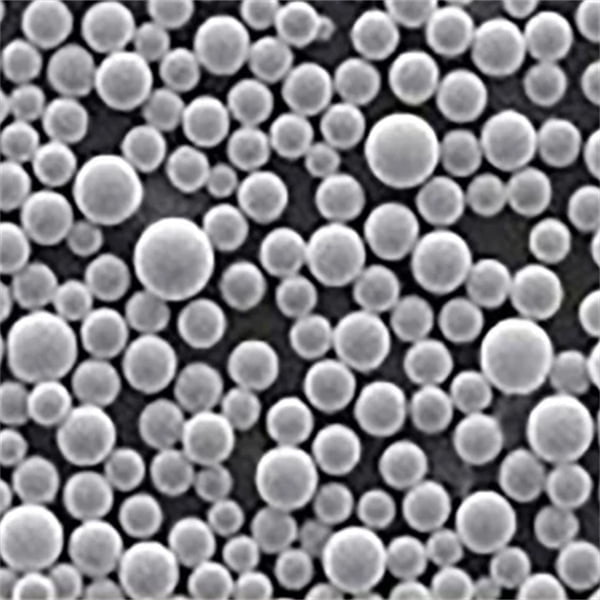
Types de poudres métalliques utilisées dans le MIM et leurs propriétés
Poudre métallique | Composition | Propriétés | Caractéristiques |
---|---|---|---|
Acier inoxydable 316L | Fe-Cr-Ni-Mo | Résistance à la corrosion, bonne ductilité | Idéal pour les dispositifs médicaux, les outils chirurgicaux et les équipements de transformation des aliments |
Acier inoxydable 17-4 PH | Fe-Cr-Ni-Cu | Haute résistance, bonne résistance à la corrosion | Couramment utilisé dans les applications aérospatiales et automobiles |
Poudre de fer carbonique | Fer de haute pureté | Haute densité, propriétés magnétiques | Utilisé dans les applications magnétiques, les matériaux magnétiques doux |
Alliages à base de nickel | Ni-Cr-Mo-Fe | Résistance aux températures élevées, résistance à la corrosion | Convient aux applications aérospatiales, chimiques et marines |
Alliage de titane (Ti-6Al-4V) | Ti-Al-V | Rapport résistance/poids élevé, biocompatibilité | Utilisé dans les implants médicaux, l'aérospatiale et l'ingénierie de haute performance |
Alliages de cobalt et de chrome | Co-Cr-Mo | Résistance à l'usure, biocompatibilité | Souvent utilisé dans les implants dentaires et orthopédiques |
Carbure de tungstène (WC-Co) | WC avec liant Co | Dureté extrême, résistance à l'usure | Courant dans les outils de coupe et les composants résistants à l'usure |
Alliages de cuivre | Cu avec Zn ou Sn | Excellente conductivité électrotechnique et thermique | Utilisé dans les connecteurs électriques, les échangeurs de chaleur et la plomberie |
Alliages d'aluminium | Al avec Mg, Si, Cu | Léger, bonne résistance à la corrosion | Idéal pour les composants structurels légers |
Acier à outils (M2, D2) | Fe-Cr-V-W-Mo | Dureté élevée, résistance à l'usure | Utilisé dans les outils de coupe, les matrices et les moules |
Composition du moulage par injection de métal (MIM)
La composition de la matière première utilisée dans le moulage par injection de métaux est un facteur critique qui influence les propriétés du produit final. La matière première est généralement constituée d'un mélange de poudres métalliques fines et d'un liant thermoplastique. Le choix de la poudre métallique et du liant a un impact significatif sur les propriétés du matériau, les caractéristiques d'écoulement pendant le moulage et les processus de déliantage et de frittage.
- Poudres métalliques : Les poudres métalliques utilisées dans le MIM sont des particules finement divisées, dont la taille est généralement inférieure à 20 microns. Ces poudres peuvent être fabriquées à partir de divers métaux, notamment l'acier inoxydable, le titane, le carbure de tungstène, etc. Le type de poudre métallique choisi dépend des propriétés requises pour le produit final, telles que la solidité, la résistance à la corrosion ou la biocompatibilité.
- Classeurs : Le système de liant est généralement un mélange de polymères et de cires qui lient les particules de poudre métallique entre elles et fournissent les caractéristiques d'écoulement nécessaires au moulage par injection. Après le moulage, le liant est éliminé par un processus de déliantage, qui peut faire appel à des méthodes thermiques, à des solvants ou à des catalyseurs.
Principales caractéristiques des matériaux MIM
Matériau | Caractéristiques principales | Applications Types |
---|---|---|
Acier inoxydable 316L | Excellente résistance à la corrosion, bonnes propriétés mécaniques | Dispositifs médicaux, équipements agroalimentaires, pièces détachées pour la marine |
Alliage de titane (Ti-6Al-4V) | Rapport résistance/poids élevé, biocompatibilité | Composants aérospatiaux, implants médicaux |
Carbure de tungstène (WC-Co) | Extrêmement dur, excellente résistance à l'usure | Outils de coupe, composants résistants à l'usure |
Alliages à base de nickel | Résistance aux températures élevées, résistance à la corrosion | Aubes de turbines, équipements de traitement chimique |
Acier à outils (M2, D2) | Dureté élevée, excellente résistance à l'usure | Outils de coupe, matrices, moules |
Le processus MIM : Décomposition étape par étape
Le processus de moulage par injection de métal comprend une série d'étapes, chacune d'entre elles étant cruciale pour garantir que le produit final réponde aux spécifications souhaitées.
- Préparation des matières premières : La première étape du MIM consiste à créer la matière première, c'est-à-dire à mélanger des poudres métalliques avec un liant. Le liant permet à la poudre métallique de s'écouler comme un plastique pendant le processus de moulage par injection.
- Moulage par injection : La matière première est chauffée et injectée dans la cavité d'un moule, formant ainsi la "pièce verte". Cette pièce est une ébauche du produit final, maintenue par le liant.
- Débouclage : Au cours de cette étape, le liant est retiré de la partie verte, laissant derrière lui une structure poreuse appelée "partie brune". Le déliantage peut être effectué par différentes méthodes, telles que des procédés thermiques, à base de solvants ou catalytiques.
- Frittage : La pièce brune est chauffée dans une atmosphère contrôlée jusqu'à un niveau juste inférieur au point de fusion de la poudre métallique. Pendant le frittage, les particules de métal fusionnent, ce qui entraîne une densification et un rétrécissement de la pièce à ses dimensions finales.
- Post-traitement : En fonction de l'application, la pièce frittée peut subir des processus supplémentaires, tels que l'usinage, le traitement thermique ou la finition de surface, afin d'obtenir les propriétés et les tolérances souhaitées.
Aperçu du processus MIM et étapes clés
Étape du processus | Description | Résultats |
---|---|---|
Préparation des matières premières | Mélange de poudres métalliques avec un liant pour créer un matériau moulable | Matières premières prêtes pour le moulage par injection |
Moulage par injection | Injection de la matière première dans un moule pour créer la pièce verte | Partie verte formée, conserve sa forme mais est fragile |
Débouclage | Élimination du liant de la partie verte pour former la partie brune | Structure poreuse sans liant (partie brune) |
Frittage | Chauffage d'une pièce brune pour fusionner des particules métalliques | Pièce finale dense et solide avec une porosité réduite |
Post-traitement | Traitements supplémentaires tels que l'usinage, le traitement thermique, la finition | Propriétés améliorées, dimensions finales et finition de surface |
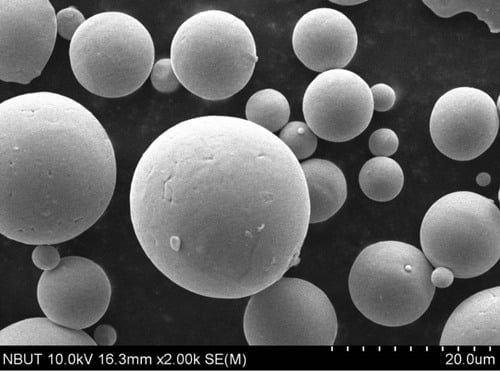
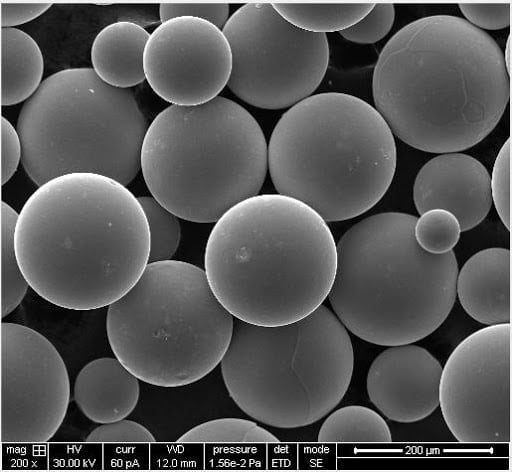
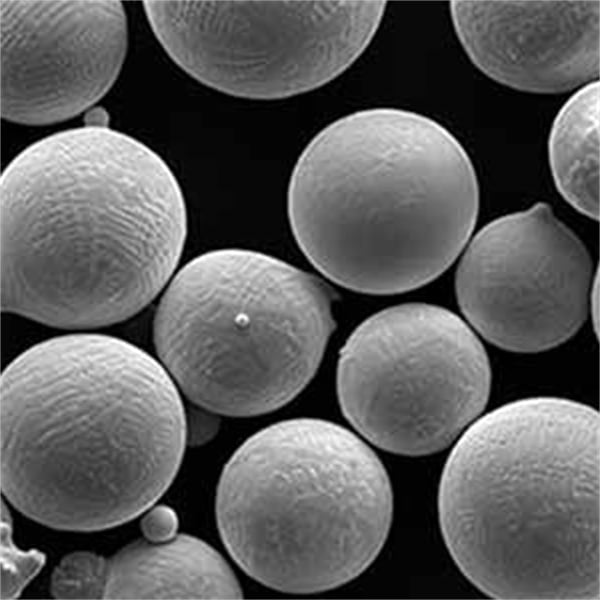
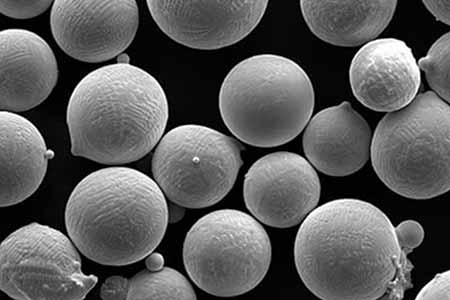
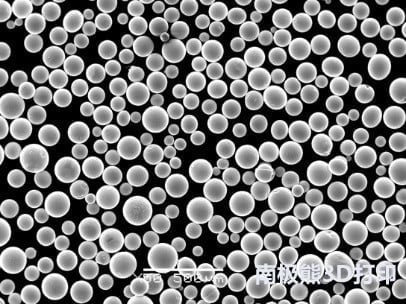
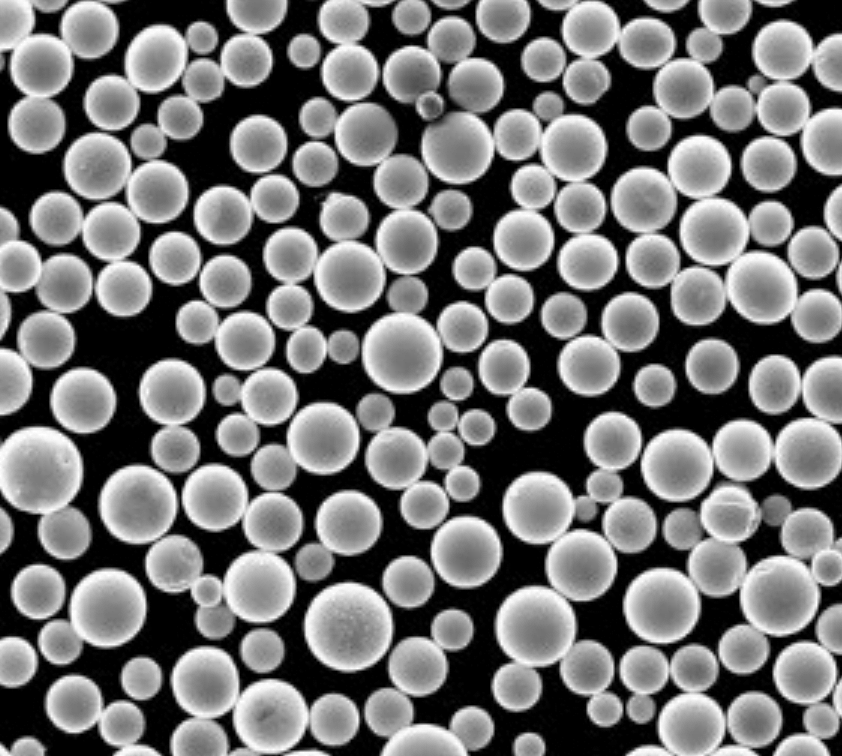
Avantages de la Moulage par injection de métal (MIM)
Pourquoi choisir le MIM plutôt que les méthodes traditionnelles d'usinage des métaux ? Il y a plusieurs avantages convaincants :
- Géométrie complexe : Le MIM permet de produire des formes complexes qui seraient difficiles, voire impossibles, à réaliser avec d'autres techniques de fabrication. Cette capacité réduit la nécessité d'opérations secondaires telles que l'usinage, qui peuvent être longues et coûteuses.
- Efficacité matérielle : Comme le MIM utilise des métaux finement pulvérisés, il permet une fabrication proche de la forme nette, ce qui minimise les pertes de matériaux par rapport à l'usinage traditionnel, qui implique souvent un enlèvement de matière important.
- Haute précision et cohérence : Le MIM produit des pièces avec des tolérances serrées et une qualité constante, ce qui en fait la solution idéale pour les applications où la précision est essentielle.
- Évolutivité : Le processus est hautement évolutif et permet la production de masse de pièces à un coût unitaire relativement faible, en particulier lorsqu'il s'agit de volumes importants.
- Variété de matériaux : Le MIM peut fonctionner avec une large gamme de métaux, y compris l'acier inoxydable, le titane et les alliages haute performance, ce qui offre une grande souplesse dans le choix des matériaux en fonction des besoins de l'application.
- Propriétés mécaniques : Les pièces MIM peuvent présenter des propriétés mécaniques comparables à celles obtenues par des méthodes de fabrication traditionnelles, telles que le moulage ou le forgeage, ce qui les rend adaptées à des applications exigeantes.
Avantages du moulage par injection de métal
Avantage | Description | Comparaison |
---|---|---|
Géométrie complexe | Capacité à produire des pièces complexes et détaillées | Mieux que le moulage et l'usinage pour les formes complexes |
Efficacité des matériaux | La fabrication de formes presque nettes minimise les déchets | Plus efficace que les méthodes soustractives |
Haute précision | Tolérances serrées et qualité constante | Comparable à l'usinage CNC |
Scalabilité | Adapté à la production en grande quantité | Plus rentable que les méthodes traditionnelles pour les grandes séries |
Variété de matériaux | Compatible avec une large gamme de métaux | Plus flexible que le moulage sous pression |
Propriétés mécaniques | Grande solidité, résistance à l'usure et autres propriétés souhaitables | Comparable aux pièces forgées ou moulées |
Applications du moulage par injection de métal (MIM)
Le MIM est utilisé dans diverses industries, grâce à sa capacité à produire de petites pièces complexes de manière efficace et rentable. Voici quelques-unes des principales applications :
- Industrie automobile : Les composants MIM sont utilisés dans les systèmes d'alimentation en carburant, les turbocompresseurs, les capteurs et diverses pièces de moteur. Le processus permet de créer des composants légers et très résistants qui contribuent à l'efficacité énergétique et aux performances.
- Industrie aérospatiale : Le MIM est utilisé pour fabriquer des pièces complexes et légères pour les moteurs d'avion, les systèmes de contrôle et les composants structurels. La capacité à produire des pièces de haute précision et d'excellentes propriétés mécaniques fait du MIM un outil de production de premier plan.
IM idéal pour les applications aérospatiales.
- Dispositifs médicaux : L'industrie médicale bénéficie de la capacité du MIM à produire des composants biocompatibles à géométrie complexe. Le MIM est utilisé pour la fabrication d'instruments chirurgicaux, d'implants orthopédiques et de dispositifs dentaires.
- Électronique : Le MIM est utilisé pour créer de petites pièces complexes pour les appareils électroniques, tels que des connecteurs, des boîtiers et des composants pour les téléphones mobiles et les ordinateurs portables. Ce procédé est bien adapté à la production en grande quantité de pièces présentant des tolérances serrées.
- Biens de consommation : Dans le secteur des biens de consommation, le MIM est utilisé pour produire des composants durables et de haute qualité pour des produits tels que les montres, les lunettes et les équipements sportifs.
- Défense : L'industrie de la défense utilise le MIM pour produire des composants légers, solides et durables pour les armes à feu, les munitions et d'autres équipements militaires.
Applications du moulage par injection de métal par l'industrie
Industrie | Applications clés | Exemples de composants MIM |
---|---|---|
Automobile | Pièces de moteur, capteurs, turbocompresseurs | Injecteurs de carburant, sièges de soupapes, composants de l'arbre à cames |
Aérospatial | Composants du moteur, pièces structurelles | Aubes de turbines, composants d'actionneurs, fixations |
Dispositifs médicaux | Instruments chirurgicaux, implants orthopédiques | Lames de bistouri, vis à os, brackets dentaires |
Électronique | Connecteurs, boîtiers, petits composants complexes | Connecteurs USB, boîtiers d'appareils photo, charnières d'ordinateurs portables |
Biens de consommation | Produits de consommation durables et de haute qualité | Etuis de montres, montures de lunettes, têtes de clubs de golf |
Défense | Équipement militaire, composants d'armes à feu | Éléments de la gâchette, pièces du chargeur, douilles de munitions |
Spécifications, tailles, qualités et normes dans le domaine du MIM
Les spécifications, les tailles, les qualités et les normes du moulage par injection de métal varient en fonction du matériau utilisé, de la complexité de la pièce et des exigences de l'application. Voici un résumé des spécifications les plus courantes :
- Acier inoxydable (316L, 17-4 PH) : Les tailles de grain typiques vont de 5 à 20 microns, avec des densités finales de pièces dépassant 95% de la densité théorique. Les normes comprennent la norme ASTM F2885 pour les pièces en acier inoxydable de qualité médicale.
- Alliages de titane (Ti-6Al-4V) : La taille des particules de poudre est généralement inférieure à 25 microns. Les pièces MIM fabriquées dans ce matériau sont conformes aux normes telles que ASTM F2885 et ISO 5832-3 pour les implants médicaux.
- Carbure de tungstène : La taille des particules de poudre varie de 0,5 à 10 microns. Les pièces finales peuvent atteindre une densité allant jusqu'à 99% de la densité théorique. Les normes comprennent la norme ISO 513 pour les outils de coupe.
- Acier à outils (M2, D2) : La taille des grains varie généralement de 10 à 40 microns, avec des densités frittées de l'ordre de 98% de la densité théorique. Les normes comprennent l'ASTM A681 pour les pièces en acier à outils.
Spécifications, tailles et normes pour les matériaux MIM courants
Matériau | Taille typique des particules | Densité finale | Normes pertinentes |
---|---|---|---|
Acier inoxydable 316L | 5-20 microns | >95% | ASTM F2885 pour les applications médicales |
Alliage de titane (Ti-6Al-4V) | <25 microns | >95% | ASTM F2885, ISO 5832-3 pour les implants médicaux |
Carbure de tungstène (WC-Co) | 0,5-10 microns | ~99% | ISO 513 pour les outils de coupe |
Acier à outils (M2, D2) | 10-40 microns | ~98% | ASTM A681 pour les pièces en acier à outils |
Fournisseurs et détails des prix
Il est essentiel de trouver le bon fournisseur de composants MIM pour garantir la qualité, la rentabilité et le respect des délais de livraison. Les prix des composants MIM peuvent varier considérablement en fonction du matériau, de la complexité, du volume et des exigences de traitement supplémentaires.
- GKN Powder Metallurgy (métallurgie des poudres) : GKN, l'un des principaux fournisseurs de poudres métalliques et de composants MIM, propose une large gamme de matériaux et de solutions personnalisées. Les prix sont généralement compris entre $0,10 et $10 par pièce, en fonction de la complexité et du volume.
- Parmaco Metal Injection Moulding : Spécialisé dans les composants MIM de haute précision, en particulier dans les secteurs médical, automobile et électronique. Les prix varient de $0,50 à $20 par pièce.
- Advanced Powder Products (APP) : Connue pour la production de pièces MIM complexes avec des tolérances serrées, APP dessert des industries telles que l'aérospatiale et la défense. Les prix varient mais commencent généralement autour de $1 par pièce.
Principaux fournisseurs et prix des composants MIM
Fournisseur | Spécialité | Prix typiques (par pièce) | Secteurs d'activité |
---|---|---|---|
GKN Métallurgie des poudres | Large gamme de matériaux et de composants MIM | $0.10 – $10 | Automobile, aérospatiale, industrie |
Parmaco Metal Injection Moulding | Composants de haute précision | $0.50 – $20 | Médical, automobile, électronique |
Advanced Powder Products (APP) | Pièces MIM complexes à tolérance serrée | A partir de $1 | Aérospatiale, défense, médecine |
Comparaison des avantages et des inconvénients du moulage par injection de métal
Comme tout processus de fabrication, le moulage par injection de métal présente un ensemble d'avantages et d'inconvénients. Les comprendre peut vous aider à déterminer si le MIM est le bon procédé pour votre application spécifique.
Avantages et inconvénients du moulage par injection de métal
Aspect | * Nécessaire pour les personnes qui ont des problèmes de mobilité * Peut être utilisé pour le transport de marchandises * Peut être utilisé pour les loisirs, comme le camping * Peut être utilisé pour explorer des zones reculées * Peut être utilisé pour les livraisons de nourriture * Peut être utilisé pour les services de messagerie * Peut être utilisé pour les services de sécurité * Peut être utilisé pour les services d'urgence * Peut être utilisé pour les opérations militaires Cons * Peut être cher à l'achat * Peut être cher à entretenir * Peut être difficile à conduire dans des espaces confinés * Peut être difficile à garer * Peut être bruyant * Peut être polluant | Inconvénients |
---|---|---|
Complexité | Peut produire des géométries complexes | Limité aux pièces de taille relativement petite |
Déchets matériels | Déchets minimes grâce à un traitement proche de la forme d'un filet | Coût élevé des matériaux pour certains métaux |
Volume de production | Économique pour la production en grande quantité | Moins rentable pour la production de faibles volumes |
Propriétés mécaniques | Haute résistance et bonnes propriétés mécaniques | Possibilité de rétrécissement pendant le frittage |
Variété de matériaux | Large gamme de métaux compatibles | Certains matériaux peuvent nécessiter des procédés de déliantage spécialisés |
Post-traitement | Permet de poursuivre l'usinage et la finition | Coûts supplémentaires pour le post-traitement |
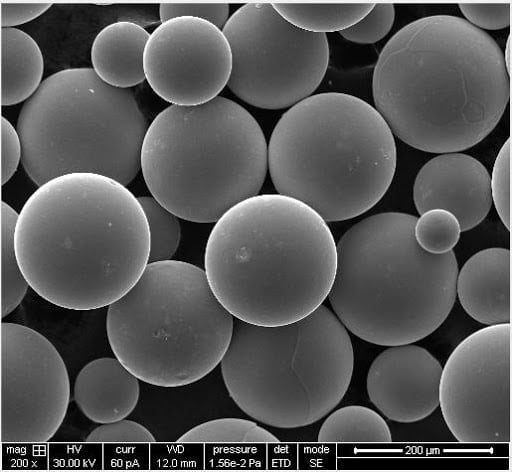
FAQ
Question | Réponse |
---|---|
Qu'est-ce que le moulage par injection de métal (MIM) ? | Le MIM est un procédé de fabrication qui associe des poudres métalliques à un liant pour produire des pièces métalliques complexes. |
Quelles sont les industries qui utilisent le plus la MIM ? | Les industries telles que l'automobile, l'aérospatiale, les appareils médicaux, l'électronique et la défense utilisent largement le MIM. |
Quels métaux peuvent être utilisés dans le MIM ? | Des métaux tels que l'acier inoxydable, le titane, le carbure de tungstène et les alliages à base de nickel sont couramment utilisés. |
Comment la MIM se compare-t-elle à l'usinage traditionnel ? | Le MIM est plus rentable pour les pièces complexes et de grand volume, tandis que l'usinage convient mieux aux pièces plus simples et de faible volume. |
Quelles sont les limites de la MIM ? | Le MIM est moins rentable pour la production de faibles volumes et présente des limites pour la production de très grandes pièces. |
Le MIM est-il respectueux de l'environnement ? | Le MIM produit moins de déchets que l'usinage traditionnel, ce qui en fait une option plus respectueuse de l'environnement. |
Quelle est la précision des pièces MIM ? | Les pièces MIM peuvent atteindre une grande précision avec des tolérances comparables à celles des pièces usinées par CNC. |
Quel est le délai de livraison habituel pour les composants MIM ? | Les délais de livraison peuvent varier de quelques semaines à plusieurs mois, en fonction de la complexité et du volume de la commande. |
Les pièces MIM peuvent-elles être personnalisées ? | Oui, le MIM permet une personnalisation importante en termes de forme, de matériau et de finition de surface. |
Comment le frittage affecte-t-il la pièce MIM finale ? | Le frittage densifie la pièce, réduisant la porosité et améliorant les propriétés mécaniques, mais il peut aussi provoquer un retrait. |
Conclusion
Moulage par injection de métal (MIM) est un processus de fabrication puissant qui comble le fossé entre le moulage par injection de plastique et les techniques traditionnelles de travail des métaux. Grâce à sa capacité à produire à grande échelle des pièces métalliques complexes et très résistantes, le MIM est une solution de choix pour les industries qui exigent précision, durabilité et efficacité. Que vous travailliez dans l'automobile, l'aérospatiale, la médecine ou toute autre industrie où des composants métalliques de haute performance sont essentiels, le MIM offre une solution polyvalente et rentable. Comprendre les matériaux, les étapes du processus, ainsi que les avantages et les limites du MIM vous aidera à prendre des décisions éclairées pour votre prochain projet.
À propos de 3DP mETAL
Catégorie de produits
CONTACTEZ-NOUS
Des questions ? Envoyez-nous un message maintenant ! Après avoir reçu votre message, nous traiterons votre demande avec toute une équipe.