Imaginez un processus de fabrication qui associe la liberté de conception complexe du moulage par injection de plastique à la solidité et à la durabilité inégalées du métal. C'est la magie de Technologie MIMUn changement dans le monde de l'usinage des métaux.
Cet article plonge dans le monde fascinant de la technologie MIM, dont il explore les subtilités, les applications, les avantages et les aspects à prendre en compte. Alors, attachez votre ceinture et préparez-vous à découvrir une technologie qui repousse les limites du possible dans la fabrication des métaux.
Le processus MIM
Le principe du MIM est d'une simplicité déconcertante. Voici un aperçu des étapes à suivre :
- Centrale à poudre : Le voyage commence par un métal finement pulvérisé, semblable à une poussière métallique. Cette poudre peut être composée de différents métaux, dont l'acier, l'acier inoxydable, le titane et même des alliages exotiques.
- Collage du liant : Imaginez que vous mélangiez la poudre de métal avec un agent liant spécial, comme une colle qui maintient le tout ensemble. Ce mélange, appelé "feedstock", devient le matériau moulable pour l'étape suivante.
- Intuition d'injection : La matière première est ensuite injectée sous haute pression dans une cavité de moule conçue avec précision. C'est un peu comme si l'on pressait de la pâte à modeler dans un emporte-pièce, mais avec des machines beaucoup plus sophistiquées.
- La mise en forme : Une fois injecté, le produit de départ prend la forme de la cavité du moule, formant un composant de forme quasi-nette. Cette forme quasi-nette fait référence à une pièce qui nécessite un post-traitement minimal pour atteindre ses dimensions finales.
- Reliure Buh-Bye : L'étape suivante consiste à éliminer le liant par un processus de déliantage thermique. Il peut s'agir de techniques telles que l'extraction par solvant ou la dégradation thermique, qui consistent essentiellement à vaporiser le liant et à laisser le squelette métallique.
- Surcharge de force : L'étape finale est un processus de frittage à haute température. Ici, les particules de métal deviennent chaudes et chaudes, fusionnent et densifient le composant. La résistance et l'intégrité structurelle de la pièce s'en trouvent considérablement renforcées.
Imaginez le MIM comme un origami métallique sophistiqué, pliant méticuleusement de la poudre de métal en des formes complexes d'une résistance impressionnante.
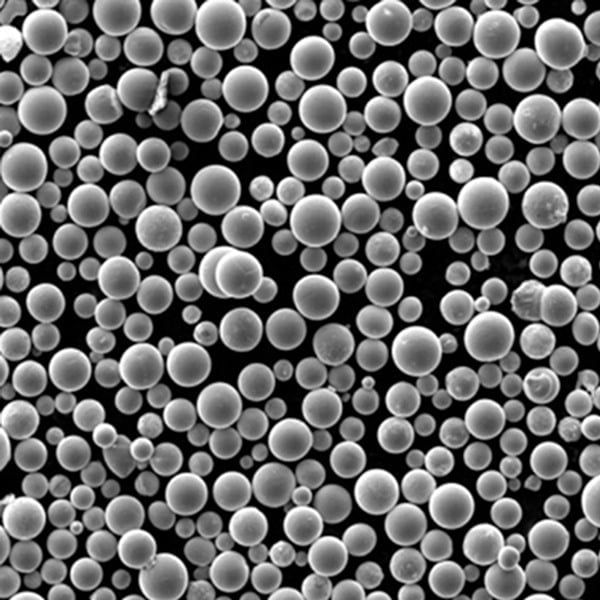
Les avantages de la Technologie MIM
La technologie MIM présente un ensemble d'avantages convaincants qui en font un choix privilégié pour diverses applications de fabrication. Examinons-en les principaux avantages :
- Polyvalence de la conception : Contrairement aux méthodes traditionnelles d'usinage des métaux, telles que le moulage ou l'usinage, le MIM offre une liberté de conception exceptionnelle. Géométries complexes, détails compliqués et parois minces : le MIM gère tout cela avec facilité. Imaginez la fabrication d'engrenages aux dents minuscules ou d'instruments médicaux complexes aux caractéristiques délicates - le MIM rend cela possible.
- Volume élevé, haute précision : Le MIM se distingue dans les productions en grande série. La possibilité de créer des formes presque nettes minimise la nécessité d'un post-traitement approfondi, ce qui permet d'accélérer les cycles de production et de réaliser des économies. En outre, le MIM garantit une précision dimensionnelle exceptionnelle, cruciale pour les composants nécessitant des tolérances précises.
- Matériau Marvel : Le MIM offre la possibilité de travailler avec une large gamme de poudres métalliques. Cela permet de fabriquer des composants à partir d'aciers à haute résistance, d'alliages résistants à la corrosion ou même de matériaux légers comme le titane.
- Considérations relatives aux coûts : Si les coûts d'installation initiaux du MIM peuvent être plus élevés, les capacités de production en grande série et le post-traitement minimal se traduisent par des économies significatives à long terme. Le MIM est donc une option convaincante pour la production en série de pièces métalliques complexes.
- Ne pas gaspiller, ne pas vouloir : Le MIM est un procédé relativement respectueux de l'environnement par rapport aux méthodes traditionnelles. L'approche de la forme proche du filet minimise les déchets de matériaux, et le processus de déliantage contrôlé permet de récupérer et de réutiliser les liants dans certains cas.
La technologie MIM est un champion bien équilibré, qui offre une grande souplesse de conception, une fabrication de haute précision, une grande polyvalence des matériaux et un bon rapport coût-efficacité, tout en minimisant l'impact sur l'environnement.
Les applications de la Technologie MIM
La technologie MIM trouve des applications dans un large éventail d'industries, du monde complexe des dispositifs médicaux à celui, colossal, des composants automobiles. En voici quelques exemples marquants :
- Merveilles médicales : Le MIM joue un rôle crucial dans la fabrication d'implants médicaux complexes tels que les prothèses articulaires, les prothèses dentaires et les instruments chirurgicaux. La capacité de créer des formes complexes avec des matériaux biocompatibles fait du MIM la solution idéale pour ces applications exigeantes.
- Avantage automobile : L'industrie automobile utilise la MIM pour la fabrication de divers composants tels que les engrenages, les pignons et les pièces du système d'alimentation en carburant. Les capacités de production en grande quantité de la MIM et son aptitude à créer des formes quasi nettes avec des tolérances serrées en font un outil parfaitement adapté à l'univers rapide de l'automobile.
- Symphonie de l'électronique grand public : Qu'il s'agisse de minuscules composants de téléphones portables ou de pièces complexes de vêtements, le MIM contribue à la miniaturisation et à la fonctionnalité de l'électronique grand public. Sa capacité à produire des formes complexes avec une grande précision s'adapte parfaitement au monde des gadgets, qui ne cesse de se réduire.
- Ascendance aérospatiale : L'industrie aérospatiale exige des composants à la fois légers et robustes. Le MIM relève le défi en permettant la création de pièces complexes à partir d'alliages à haute résistance et à faible poids comme le titane. Cela se traduit par une réduction de la consommation de carburant et une amélioration des performances des avions et des engins spatiaux.
- Finesse des armes à feu : Le MIM joue un rôle dans l'industrie des armes à feu pour la fabrication de composants complexes tels que les gâchettes, les marteaux et les dispositifs de sécurité. Sa capacité à produire des formes presque nettes avec une grande précision et une résistance exceptionnelle le rend adapté à ces applications exigeantes.
Au-delà de ces exemples marquants, la technologie MIM a le potentiel de révolutionner plusieurs autres industries. À mesure que la technologie mûrit et que les coûts deviennent plus compétitifs, on peut s'attendre à ce que les applications de la MIM se développent dans des domaines tels que :
- Infrastructures énergétiques : Fabrication de composants complexes pour les pompes, les vannes et d'autres pièces critiques dans les systèmes de production et de distribution d'énergie.
- Télécommunications : Création de composants miniaturisés et de haute précision pour des équipements de télécommunication complexes.
- Articles de sport : Fabrication de composants légers et durables pour les bicyclettes, les clubs de golf et d'autres équipements sportifs.
Les possibilités offertes par la technologie MIM sont vraiment vastes et son impact sur les différentes industries ne fera que croître dans les années à venir.
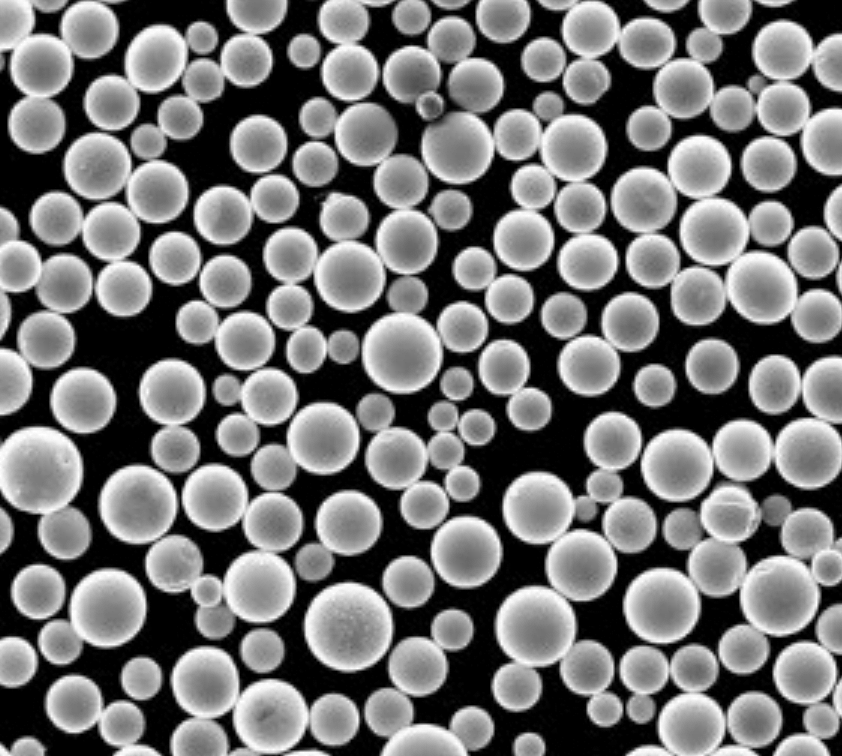
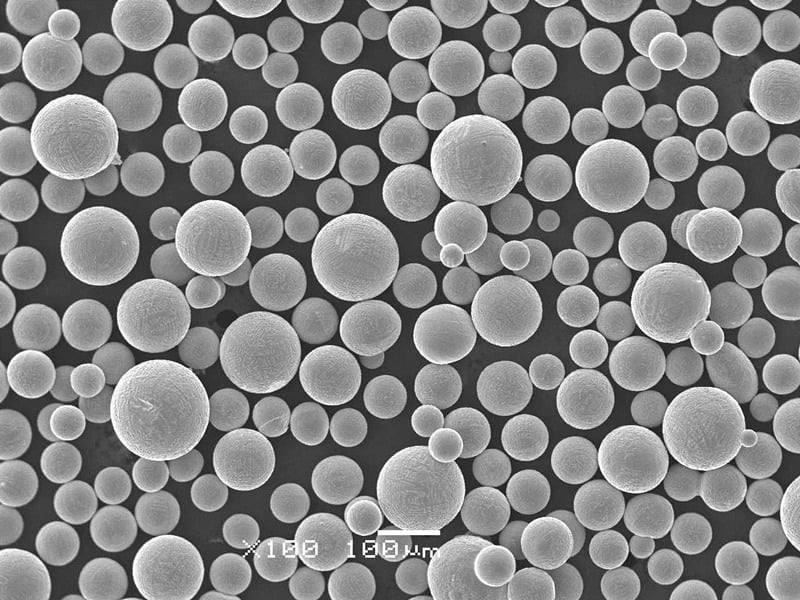
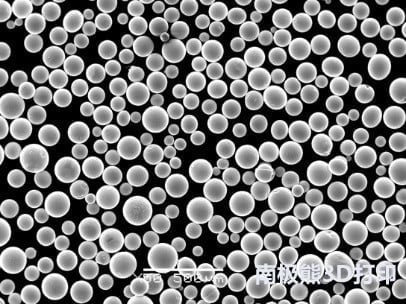
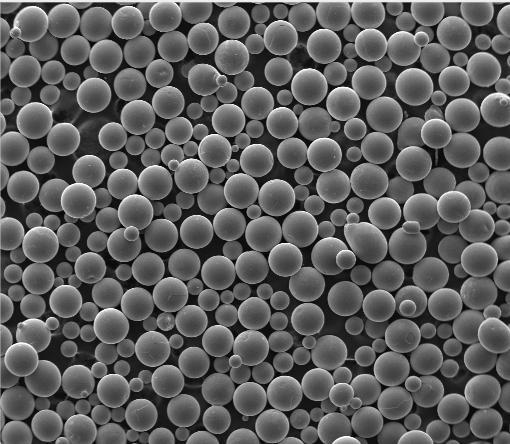
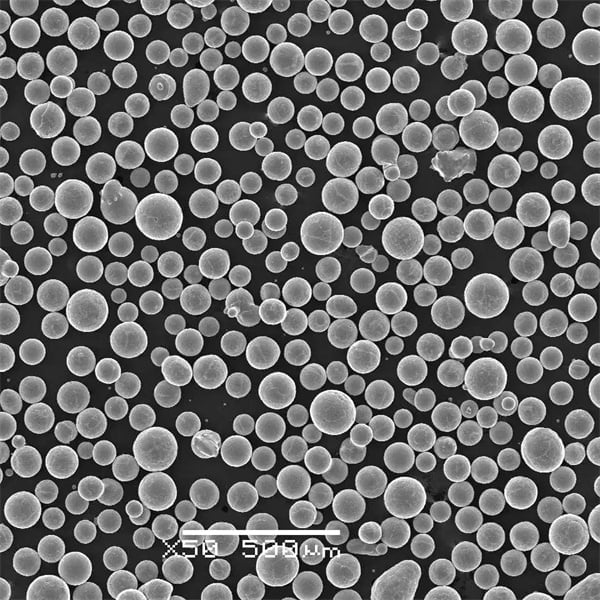
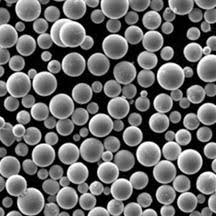
Les caractéristiques de la technologie d'atomisation
Maintenant que nous avons exploré la magie du MIM, approfondissons un aspect crucial : la technologie d'atomisation. Ce processus est responsable de la création des poudres métalliques fines qui constituent la base du MIM. Voici une présentation des deux principales techniques d'atomisation :
- Atomisation par gaz : Imaginez que du métal en fusion soit projeté à travers une buse à haute pression, le brisant en minuscules gouttelettes qui se solidifient dans l'air sous la forme d'une fine poudre de métal. C'est l'essence même de l'atomisation gazeuse. Il s'agit d'une technique polyvalente qui convient à une large gamme de métaux et d'alliages.
- Atomisation de l'eau : Cette méthode utilise un jet d'eau à grande vitesse pour fragmenter le métal en fusion en fines particules. La pulvérisation d'eau est particulièrement adaptée à la production de poudres métalliques sphériques et est souvent utilisée pour des matériaux spécifiques tels que l'acier inoxydable.
Le choix de la technique d'atomisation dépend de plusieurs facteurs, notamment des caractéristiques souhaitées de la poudre, du type de métal traité et des considérations de coût.
Voici un tableau résumant les principales caractéristiques de chaque technique d'atomisation :
Fonctionnalité | Atomisation par gaz | Pulvérisation d'eau |
---|---|---|
Processus | Métal en fusion poussé à travers une buse à haute pression | Métal en fusion fragmenté par un jet d'eau à grande vitesse |
Morphologie des poudres | Formes généralement irrégulières | Généralement plus sphérique |
Adéquation du métal | Large gamme de métaux et d'alliages | Principalement adapté à des matériaux spécifiques tels que l'acier inoxydable |
Coût | Coût généralement plus élevé | Coût inférieur à celui de l'atomisation au gaz |
Il est important de noter que ce tableau fournit une comparaison générale et qu'il peut y avoir un certain chevauchement des capacités en fonction de la technologie spécifique et des paramètres du processus.
Considérations et limites de la Technologie MIM
Bien que la MIM offre un ensemble d'avantages convaincants, il est essentiel d'en comprendre les limites et les considérations avant de s'y plonger la tête la première. Voici quelques points clés à garder à l'esprit :
- Contraintes liées à la taille des pièces : Le MIM est le mieux adapté à la production de composants de taille relativement petite à moyenne. Les limites proviennent de facteurs tels que les capacités de remplissage des moules et le risque de fissuration interne au cours des étapes de déliantage et de frittage.
- Finition de la surface : Bien que le MIM puisse produire de bons états de surface, il n'est peut-être pas idéal pour les applications nécessitant une douceur exceptionnelle. Dans ce cas, des étapes de post-traitement supplémentaires, telles que le polissage ou l'usinage, peuvent s'avérer nécessaires.
- Sélection des matériaux : Tous les métaux ne sont pas facilement compatibles avec le MIM. Des facteurs tels que le point de fusion et le comportement au frittage jouent un rôle crucial. Les métaux réfractaires dont le point de fusion est extrêmement élevé peuvent ne pas convenir au MIM en raison des limitations des températures de traitement.
- Conception pour le MIM : Pour profiter pleinement des avantages du MIM, il est essentiel de concevoir des composants spécifiquement adaptés au processus. Cela implique de prendre en compte des facteurs tels que l'épaisseur des parois, les angles de dépouille et le potentiel de contraintes internes pendant le traitement.
En comprenant ces considérations et ces limites, les fabricants peuvent décider en toute connaissance de cause si le MIM est adapté à leur application spécifique.
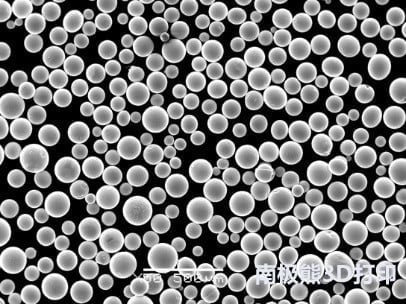
FAQ
Voici une section qui répond aux questions les plus fréquemment posées sur les sujets suivants Technologie MIMLes résultats sont présentés sous forme de tableaux clairs et concis :
Question | Réponse |
---|---|
Quels sont les avantages de la technologie MIM ? | Souplesse de conception, production en grande quantité, polyvalence des matériaux, rentabilité et minimisation des déchets. |
Quelles sont les applications de la technologie MIM ? | Dispositifs médicaux, composants automobiles, électronique grand public, pièces pour l'aérospatiale, composants pour armes à feu, etc. |
Quels sont les différents types de techniques d'atomisation utilisés dans le MIM ? | Pulvérisation de gaz et pulvérisation d'eau. |
Quelles sont les limites de la technologie MIM ? | Les contraintes de taille, les limites de la finition de surface, les considérations relatives à la sélection des matériaux et la nécessité de concevoir selon les principes de la MIM. |
Le MIM est-il un procédé respectueux de l'environnement ? | Le MIM est relativement respectueux de l'environnement par rapport aux méthodes traditionnelles d'usinage des métaux en raison du peu de déchets de matériaux et de la possibilité de réutiliser les liants. |
Quelles sont les perspectives d'avenir de la technologie MIM ? | La technologie MIM devrait connaître une croissance et une adoption continues dans divers secteurs en raison de ses avantages et de ses progrès constants. |
Comment le MIM se compare-t-il à d'autres procédés de transformation des métaux tels que l'usinage ou le moulage ? | Par rapport à l'usinage, le MIM offre une plus grande liberté de conception et des formes presque nettes. Si le moulage permet de produire des formes complexes, le MIM se distingue souvent par une plus grande précision et de meilleures propriétés des matériaux. |
Quels sont les défis associés à la technologie MIM ? | Développer des méthodes rentables pour traiter une gamme plus large de métaux et d'alliages, et faire progresser les techniques de déliantage afin de minimiser les risques de défauts. |
À propos de 3DP mETAL
Catégorie de produits
CONTACTEZ-NOUS
Des questions ? Envoyez-nous un message maintenant ! Après avoir reçu votre message, nous traiterons votre demande avec toute une équipe.