Gas atomization is a fascinating and complex process crucial in the production of high-quality metal powders. If you’re diving into the world of metallurgy, 3D printing, or advanced manufacturing, understanding gas atomization is a must. Let’s embark on a journey through this intricate process, exploring its nuances, applications, and more.
Overview of Gas Atomization
Gas atomization is a technique used to create fine metal powders by disintegrating molten metal into droplets using a high-velocity gas stream. This method ensures uniform particle size, shape, and distribution, making it ideal for industries that require precision and consistency.
Key Details of Gas Atomization
- Process: High-velocity gas stream disintegrates molten metal.
- Products: Fine metal powders with uniform size and shape.
- Applications: Additive manufacturing, metallurgy, powder metallurgy, coatings.
How Gas Atomization Works
Gas atomization begins with melting the metal in a crucible. Once the metal reaches a molten state, it is forced through a nozzle. Here, a high-velocity gas stream (commonly nitrogen, argon, or helium) strikes the molten metal, breaking it into tiny droplets. These droplets solidify as they fall, forming fine metal powders.
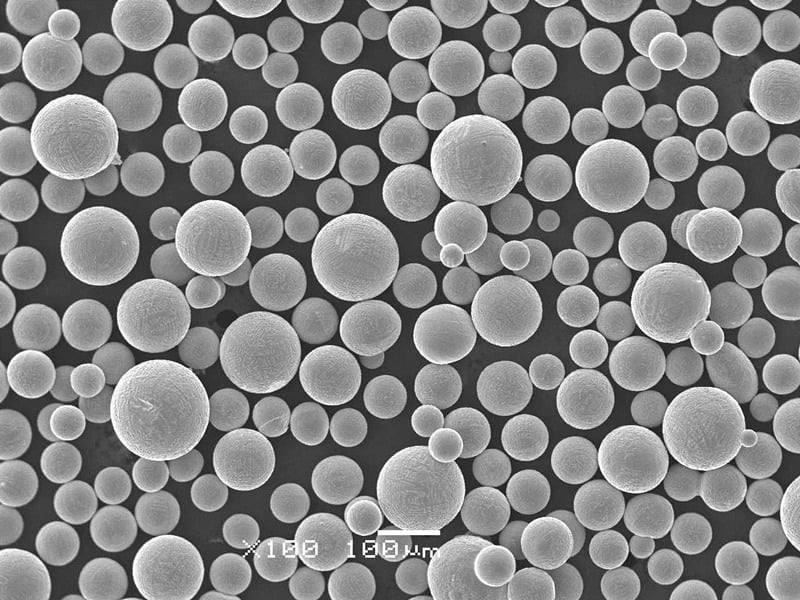
Types of Metal Powders Produced
Here’s a glimpse of some specific metal powders produced via gas atomization:
Metal Powder | Composition | Properties | Applications |
---|---|---|---|
Stainless Steel 316L | Fe, Cr, Ni, Mo | Corrosion resistance, strength | Medical implants, aerospace |
Inconel 718 | Ni, Cr, Fe, Mo | High temperature, strength | Aerospace, turbines |
Ti-6Al-4V | Ti, Al, V | Lightweight, strong | Aerospace, medical |
AlSi10Mg | Al, Si, Mg | Lightweight, thermal conductivity | Automotive, aerospace |
Cobalt Chrome | Co, Cr, Mo | Hardness, wear resistance | Dental, orthopedic |
Copper | Cu | Electrical conductivity, ductility | Electronics, electrical |
Tool Steel | Fe, C, Cr, Mo | Hardness, toughness | Cutting tools, molds |
Nickel 625 | Ni, Cr, Mo | Corrosion resistance, strength | Chemical, marine |
Bronze | Cu, Sn | Corrosion resistance, machinability | Bearings, bushings |
Stainless Steel 304 | Fe, Cr, Ni | Corrosion resistance, weldability | Construction, kitchenware |
Applications of Gas Atomization
Gas atomization’s ability to produce high-quality powders makes it indispensable in various fields. Here’s how it impacts different industries:
Additive Manufacturing
Additive manufacturing, commonly known as 3D printing, relies heavily on gas-atomized powders for producing precise and complex parts. The uniform particle size ensures smooth layering and high-quality prints.
Powder Metallurgy
In powder metallurgy, gas-atomized powders are compacted and sintered to create dense and robust components. This method is efficient for producing parts with intricate shapes and high strength.
Coatings
Gas-atomized powders are used in thermal spraying and other coating processes to enhance surface properties, such as wear resistance and corrosion protection.
Applications Overview
Application | Details |
---|---|
Additive Manufacturing | Precision parts, complex geometries, high strength |
Powder Metallurgy | Dense components, intricate shapes, high durability |
Coatings | Enhanced surface properties, wear resistance, corrosion protection |
Medical | Implants, prosthetics, biocompatibility |
Aerospace | Lightweight, high-strength parts, high temperature resistance |
Specifications of Metal Powders
When selecting metal powders, various specifications must be considered to ensure suitability for specific applications. These include particle size, shape, purity, and flowability.
Specifications Table
Metal Powder | Particle Size | Shape | Purity | Flowability |
---|---|---|---|---|
Stainless Steel 316L | 15-45 µm | Spherical | 99.9% | Excellent |
Inconel 718 | 15-53 µm | Spherical | 99.8% | Excellent |
Ti-6Al-4V | 20-45 µm | Spherical | 99.5% | Good |
AlSi10Mg | 20-60 µm | Spherical | 99.7% | Good |
Cobalt Chrome | 10-45 µm | Spherical | 99.8% | Excellent |
Copper | 10-60 µm | Spherical | 99.9% | Good |
Tool Steel | 15-53 µm | Spherical | 99.5% | Good |
Nickel 625 | 20-45 µm | Spherical | 99.8% | Excellent |
Bronze | 20-60 µm | Spherical | 99.7% | Good |
Stainless Steel 304 | 15-45 µm | Spherical | 99.9% | Excellent |
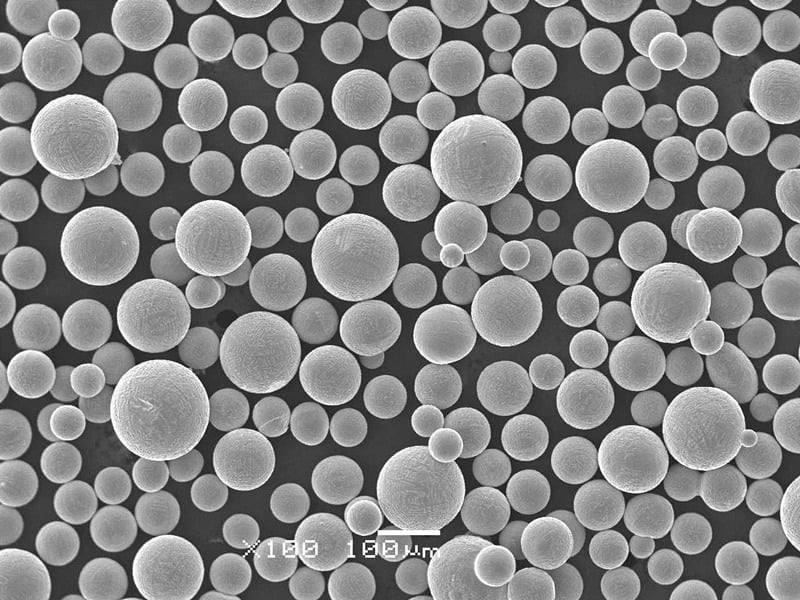
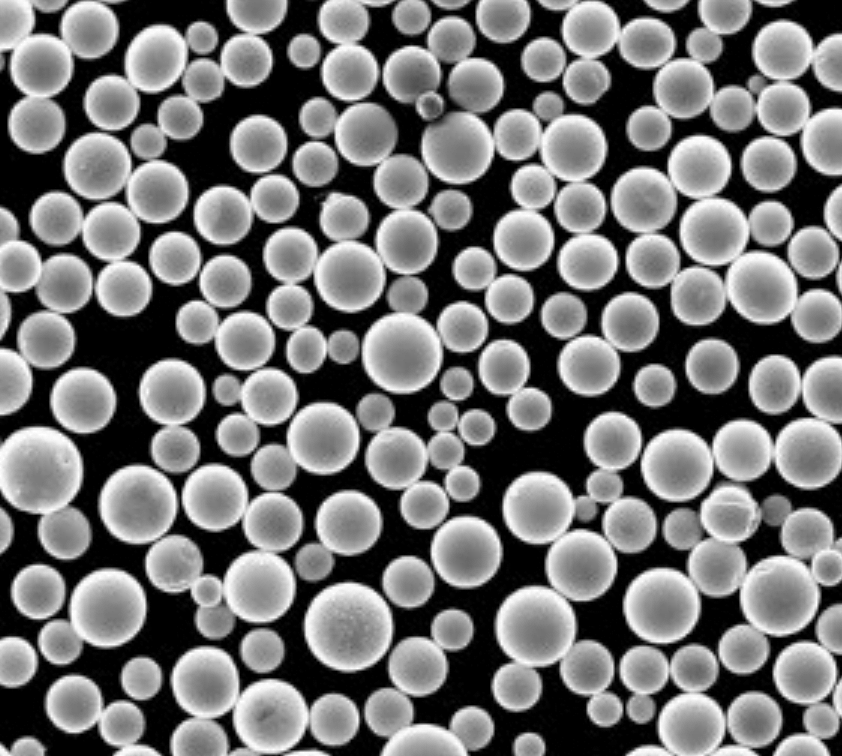
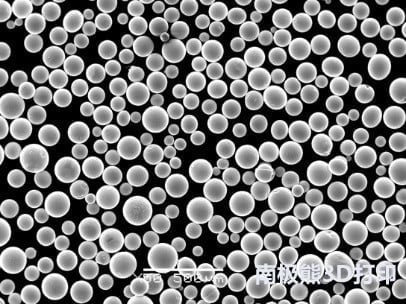
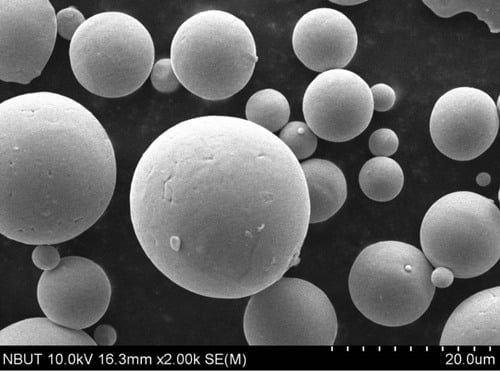
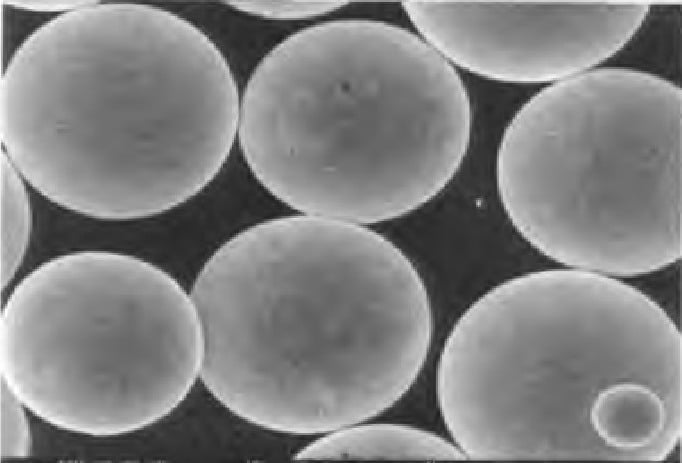
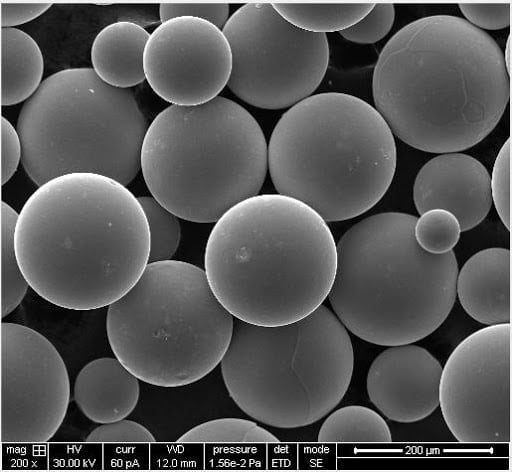
Suppliers and Pricing of Metal Powders
Numerous suppliers provide gas-atomized metal powders. Pricing can vary based on metal type, purity, and quantity.
Suppliers and Pricing Table
Supplier | Metal Powder | Price (per kg) | Quantity Available |
---|---|---|---|
Höganäs | Stainless Steel 316L | $120 | 100 kg |
Carpenter Additive | Inconel 718 | $200 | 50 kg |
Arcam AB | Ti-6Al-4V | $300 | 20 kg |
LPW Technology | AlSi10Mg | $150 | 100 kg |
Oerlikon Metco | Cobalt Chrome | $250 | 30 kg |
Praxair | Copper | $100 | 200 kg |
GKN Hoeganaes | Tool Steel | $180 | 50 kg |
Aubert & Duval | Nickel 625 | $220 | 40 kg |
Sandvik | Bronze | $90 | 150 kg |
Tekna | Stainless Steel 304 | $130 | 100 kg |
Advantages of Gas Atomization
Gas atomization offers numerous advantages, making it a preferred method for producing metal powders.
Advantages Overview
Advantage | Description |
---|---|
Uniform Particle Size | Ensures consistency in applications like 3D printing. |
High Purity | Minimizes contaminants, crucial for sensitive applications. |
Versatility | Can produce a wide range of metal powders. |
Efficiency | High production rates and minimal waste. |
Spherical Particles | Improves flowability and packing density. |
Disadvantages of Gas Atomization
However, gas atomization is not without its challenges and limitations.
Disadvantages Overview
Disadvantage | Description |
---|---|
Cost | High initial setup and operating costs. |
Complexity | Requires precise control and expertise. |
Energy Consumption | High energy usage due to the need for high-velocity gas. |
Equipment Wear | Nozzles and crucibles can wear out quickly. |
Comparing Gas Atomization with Other Methods
When compared to other powder production methods, gas atomization stands out in several ways.
Comparison Overview
Method | Gas Atomization | Water Atomization | Mechanical Alloying |
---|---|---|---|
Particle Size | Uniform, small | Larger, irregular | Variable |
Shape | Spherical | Irregular | Irregular |
Purity | High | Moderate | Variable |
Cost | High | Lower | High |
Applications | High-precision, advanced manufacturing | Less precise, bulk applications | Specialized alloys |
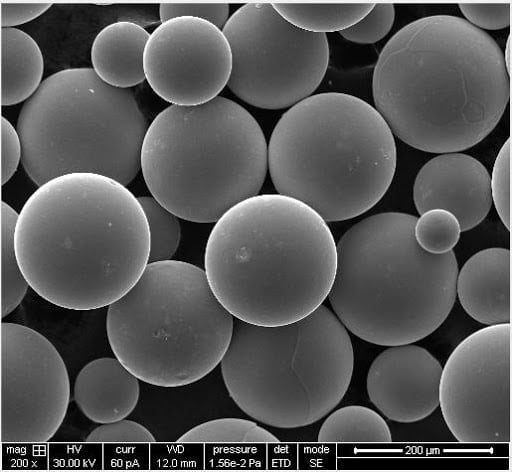
FAQ
Question | Answer |
---|---|
What is gas atomization? | A process to produce fine metal powders by disintegrating molten metal with a high-velocity gas stream. |
Why use gas atomization? | For producing high-quality, uniform metal powders essential for advanced manufacturing. |
What metals can be atomized? | Stainless steel, titanium, aluminum, nickel, and many more. |
What are the applications of gas-atomized powders? | 3D printing, powder metallurgy, coatings, medical implants, aerospace components. |
How does gas atomization compare to water atomization? | Gas atomization produces more uniform and spherical particles, but at a higher cost. |
Is gas atomization expensive? | Yes, due to high initial setup and operating costs. |
What gases are used in gas atomization? | Commonly nitrogen, argon, and helium. |
About 3DP mETAL
Product Category
CONTACT US
Any questions? Send us a message now! After receiving your message, we will process your request with a whole team.