Gas atomized powder is a crucial component in various industries, from aerospace to medical devices, offering unparalleled quality and performance. This article delves into the fascinating world of gas atomized powders, examining their properties, applications, and the specific metal powder models that set the standard in this field.
Overview of Gas Atomized Powder
Gas atomized powder is produced by disintegrating a molten metal stream into fine droplets using a high-pressure gas, resulting in a powder with a spherical shape and uniform particle size. This method ensures high purity and excellent flow characteristics, making it ideal for various applications, including additive manufacturing, thermal spray, and metal injection molding.
Types and Compositions of Gas Atomized Powders
Gas atomized powders can be made from a wide range of metals and alloys, each with unique properties tailored to specific applications. Here are some of the most common types:
Metal Powder Model | Composition | Key Properties |
---|---|---|
316L Stainless Steel | Fe, Cr, Ni, Mo | Corrosion resistance, high ductility, good weldability |
Inconel 625 | Ni, Cr, Mo, Nb | Oxidation resistance, high strength, excellent fatigue resistance |
Ti-6Al-4V | Ti, Al, V | High strength-to-weight ratio, biocompatibility, corrosion resistance |
AlSi10Mg | Al, Si, Mg | Lightweight, good thermal conductivity, excellent casting properties |
CuCrZr | Cu, Cr, Zr | High electrical and thermal conductivity, strength at elevated temperatures |
Maraging Steel | Fe, Ni, Co, Mo | Ultra-high strength, toughness, good weldability |
Cobalt Chrome | Co, Cr, Mo | High wear resistance, biocompatibility, strength at high temperatures |
Hastelloy X | Ni, Cr, Fe, Mo | Excellent oxidation resistance, strength at high temperatures |
Tool Steel | Fe, C, Cr, Mo, V | High hardness, wear resistance, toughness |
NiCrMo Alloy | Ni, Cr, Mo | Corrosion resistance, high strength, durability |
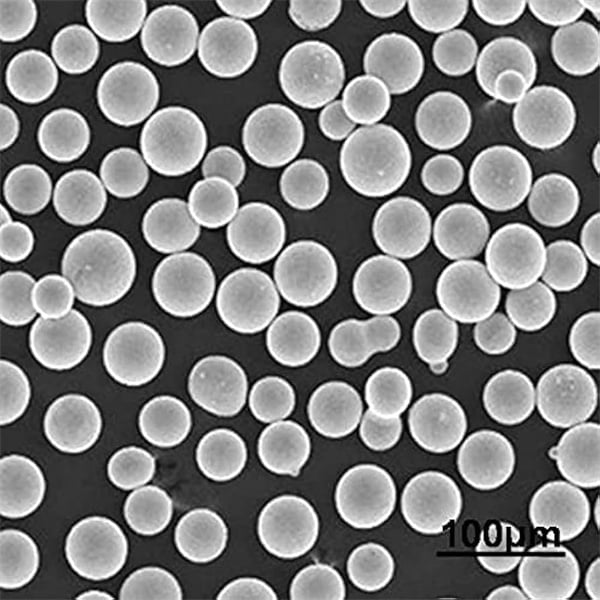
Properties and Characteristics
Gas atomized powders exhibit several desirable properties that make them suitable for various high-performance applications. Some of these properties include:
- Spherical Shape: Ensures high flowability and packing density, crucial for processes like 3D printing and powder metallurgy.
- Uniform Particle Size Distribution: Leads to consistent and predictable behavior in applications.
- High Purity: Minimizes impurities, resulting in superior mechanical and chemical properties.
- Excellent Alloy Homogeneity: Guarantees consistent material properties throughout the powder.
Applications of Gas Atomized Powder
Gas atomized powders are employed in numerous industries due to their versatile properties. Here are some key applications:
Application | Description |
---|---|
Additive Manufacturing | Used in 3D printing to produce complex, high-performance parts with precision and minimal waste |
Thermal Spraying | Applied as coatings to protect surfaces from wear, corrosion, and high temperatures |
Metal Injection Molding | Enables the production of small, intricate metal parts with high precision |
Hot Isostatic Pressing | Densifies metal powders to produce fully dense materials with superior mechanical properties |
Biomedical Implants | Utilized for producing biocompatible implants with complex geometries |
Aerospace Components | Essential for manufacturing lightweight, high-strength components for aircraft and spacecraft |
Automotive Parts | Used to produce durable and high-performance parts for vehicles |
Tooling | Applied in the production of high-hardness, wear-resistant tools and dies |
Energy Sector | Used in the production of components for power generation, including turbines and fuel cells |
Specifications, Sizes, Grades, and Standards
Understanding the specifications and standards for gas atomized powders is crucial for selecting the right material for your application. Here’s a breakdown:
Powder Model | Size Range (µm) | Grade | Standards |
---|---|---|---|
316L Stainless Steel | 15-45, 45-100 | AISI 316L | ASTM F138, ASTM F899 |
Inconel 625 | 15-53, 53-150 | AMS 5666, UNS N06625 | ASTM B443, AMS 5666 |
Ti-6Al-4V | 15-45, 45-105 | Grade 5 | ASTM F136, ASTM B348 |
AlSi10Mg | 20-63, 45-90 | AlSi10Mg | EN 1706, ASTM B85 |
CuCrZr | 10-45, 45-105 | C18150 | ASTM B936, UNS C18150 |
Maraging Steel | 15-45, 45-150 | 18Ni (300) | ASTM A538, AMS 6514 |
Cobalt Chrome | 15-45, 45-105 | CoCrMo | ASTM F75, ISO 5832-4 |
Hastelloy X | 15-53, 53-150 | UNS N06002 | ASTM B435, AMS 5754 |
Tool Steel | 15-45, 45-150 | D2, M2, T15 | ASTM A681, ISO 4957 |
NiCrMo Alloy | 15-53, 53-150 | Alloy 625 | ASTM B443, ASTM B446 |
Suppliers and Pricing Details
When it comes to sourcing gas atomized powders, several suppliers stand out for their quality and reliability. Here’s a comparative look:
Supplier | Powder Model | Price Range (per kg) | Additional Services |
---|---|---|---|
AP&C | Ti-6Al-4V, 316L | $250-$500 | Custom sizing, certification |
Carpenter Additive | Inconel 625, Hastelloy X | $300-$600 | Technical support, R&D collaboration |
Höganäs | AlSi10Mg, Tool Steel | $150-$400 | Application support, material testing |
Sandvik Osprey | Maraging Steel, Cobalt Chrome | $350-$700 | Bespoke alloy development, analysis |
GKN Hoeganaes | NiCrMo Alloy, CuCrZr | $200-$450 | Custom alloy production, consultation |
LPW Technology | Various | $200-$550 | Quality assurance, traceability |
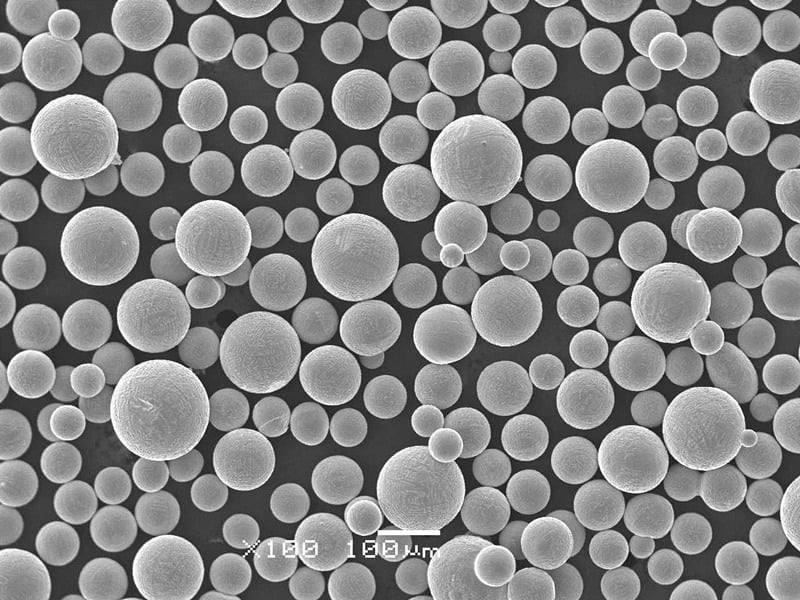
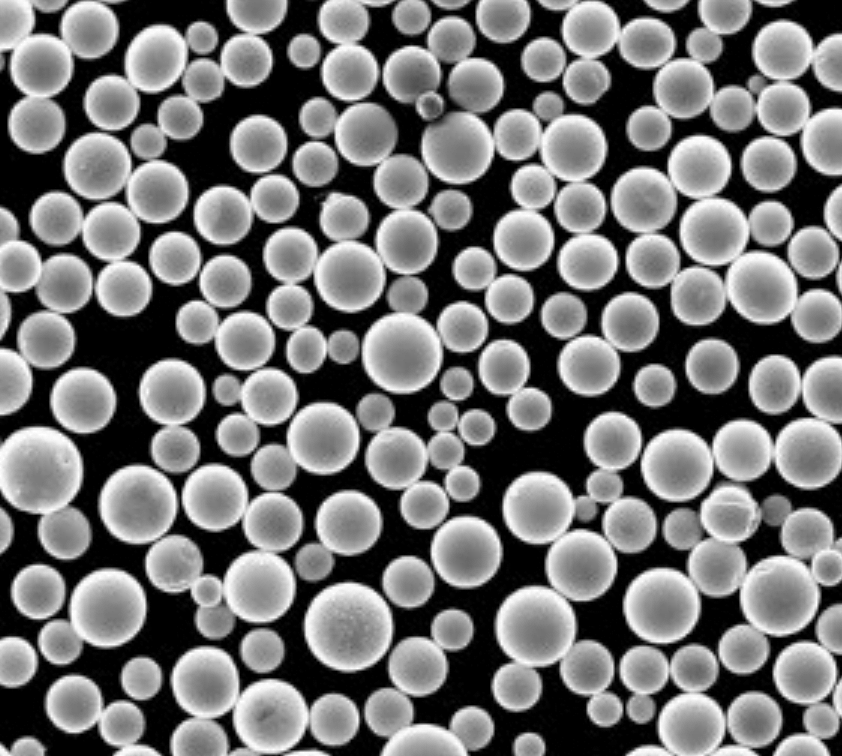
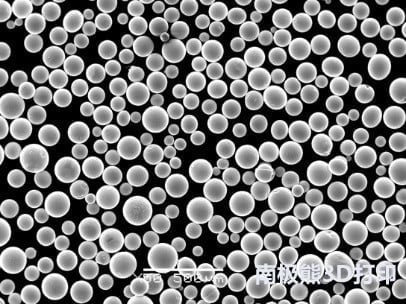
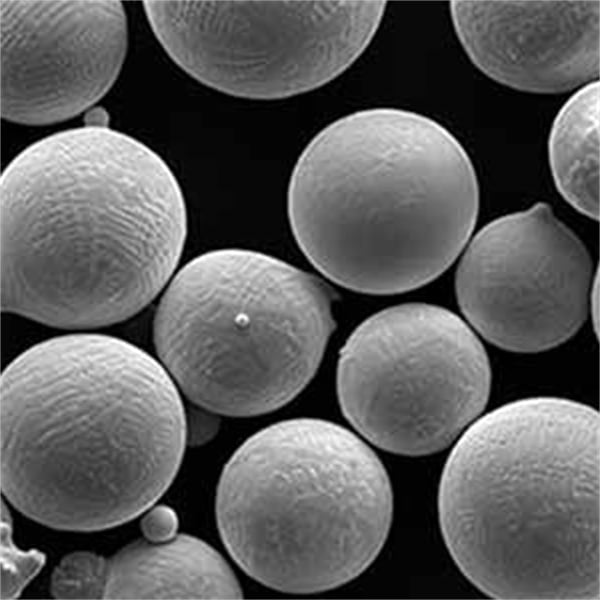
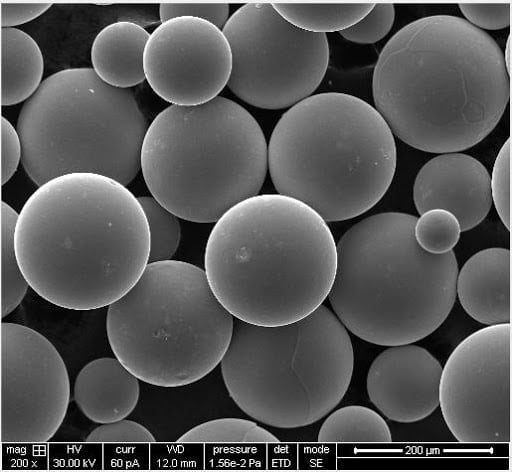
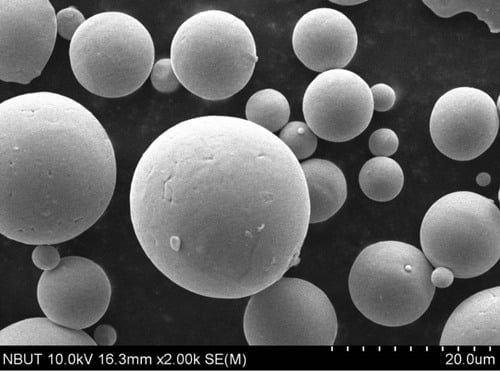
Aspect | Advantages | Limitations |
---|---|---|
Particle Shape | Spherical particles enhance flowability and packing density | Complex production process |
Purity | High purity reduces risk of defects and improves mechanical properties | Higher cost compared to other powder production methods |
Size Distribution | Uniform particle size ensures consistent application results | Limited size ranges depending on the production method |
Versatility | Applicable to a wide range of metals and alloys | Specific alloys may be challenging to produce |
Application Efficiency | Suitable for advanced manufacturing techniques like 3D printing | May require specific handling and storage conditions |
Mechanical Properties | Superior strength, ductility, and corrosion resistance | Initial investment in equipment and technology can be high |
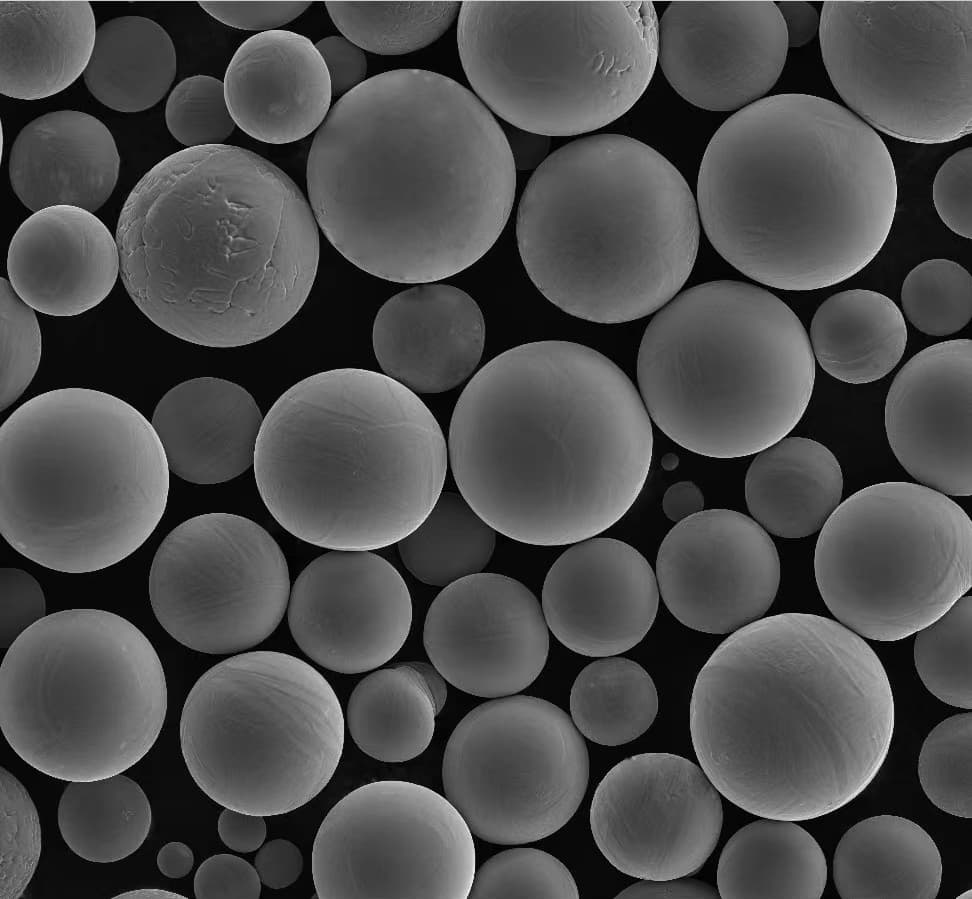
FAQ
Here are some common questions and answers about gas atomized powders to help you understand their usage and benefits better:
Question | Answer |
---|---|
What is gas atomized powder? | Gas atomized powder is a type of metal powder produced by disintegrating molten metal into fine droplets using high-pressure gas. |
What are the benefits of using gas atomized powders? | They offer high purity, excellent flowability, uniform particle size, and superior mechanical properties. |
Which industries use gas atomized powders? | Aerospace, automotive, biomedical, energy, and manufacturing industries commonly use these powders. |
How are gas atomized powders produced? | They are produced by melting metal and using high-pressure gas to break it into fine droplets that solidify into powder. |
What are some common applications of gas atomized powders? | 3D printing, thermal spraying, metal injection molding, hot isostatic pressing, and biomedical implants. |
Conclusion
Gas atomized powders are an essential component in modern manufacturing, offering unmatched quality and performance for a wide range of applications. From aerospace components to biomedical implants, these powders provide the reliability and precision needed in high-stakes industries. By understanding the properties, applications, and specific models available, you can make informed decisions to leverage the benefits of gas atomized powders in your projects. Whether you’re looking for superior corrosion resistance, high strength, or excellent flowability, there’s a gas atomized powder that fits your needs.
About 3DP mETAL
Product Category
CONTACT US
Any questions? Send us a message now! After receiving your message, we will process your request with a whole team.