Overview of High Performance Metal Powders
Metal powders are revolutionizing the landscape of advanced manufacturing, providing unparalleled performance, versatility, and efficiency. High performance metal powders are engineered for superior properties, making them essential in industries such as aerospace, automotive, medical, and electronics. These powders are used in various applications including additive manufacturing (3D printing), powder metallurgy, and coating processes.
In this comprehensive guide, we will delve into the world of high performance metal powders, exploring their types, compositions, properties, and applications. We will also compare different metal powder models, provide insights into their specifications, and examine their advantages and limitations. Our goal is to provide a detailed, engaging, and SEO-optimized resource that helps you understand and leverage the potential of high performance metal powders.
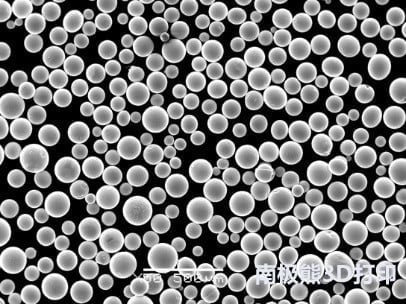
Composition of High Performance Metal Powders
Understanding the composition of high performance metal powders is crucial, as it directly influences their properties and applications. These powders are typically made from a variety of metals and alloys, each offering unique characteristics.
Table: Types and Compositions of High Performance Metal Powders
Metal Powder Model | Composition | Key Elements |
---|---|---|
Stainless Steel 316L | Fe, Cr, Ni, Mo | Chromium, Nickel, Molybdenum |
Titanium Alloy (Ti-6Al-4V) | Ti, Al, V | Titanium, Aluminum, Vanadium |
Inconel 718 | Ni, Cr, Fe, Nb, Mo | Nickel, Chromium, Iron, Niobium, Molybdenum |
Aluminum Alloy (AlSi10Mg) | Al, Si, Mg | Aluminum, Silicon, Magnesium |
Copper (Cu-ETP) | Cu | Copper |
Tool Steel (M2) | Fe, W, Mo, Cr, V, C | Tungsten, Molybdenum, Chromium, Vanadium, Carbon |
Cobalt-Chrome (CoCrMo) | Co, Cr, Mo | Cobalt, Chromium, Molybdenum |
Maraging Steel (18Ni300) | Fe, Ni, Co, Mo, Ti | Nickel, Cobalt, Molybdenum, Titanium |
Nickel Alloy (Ni625) | Ni, Cr, Mo, Nb | Nickel, Chromium, Molybdenum, Niobium |
Tungsten Carbide (WC) | W, C | Tungsten, Carbon |
Key Takeaways:
- Stainless Steel 316L: Known for its corrosion resistance, this powder is ideal for marine and medical applications.
- Titanium Alloy (Ti-6Al-4V): Lightweight yet strong, perfect for aerospace and medical implants.
- Inconel 718: High strength and resistance to extreme temperatures, used in aerospace and gas turbines.
- Aluminum Alloy (AlSi10Mg): Lightweight with good mechanical properties, suitable for automotive and aerospace.
- Copper (Cu-ETP): Excellent electrical and thermal conductivity, used in electronics and heat exchangers.
- Tool Steel (M2): High hardness and wear resistance, ideal for cutting tools.
- Cobalt-Chrome (CoCrMo): Biocompatible and wear-resistant, used in medical implants and dental prosthetics.
- Maraging Steel (18Ni300): High strength and toughness, used in tooling and high-performance engineering.
- Nickel Alloy (Ni625): Corrosion and oxidation-resistant, used in chemical processing and marine applications.
- Tungsten Carbide (WC): Extremely hard, used in cutting and mining tools.
Characteristics of High Performance Metal Powders
The unique characteristics of high performance metal powders make them suitable for a wide range of applications. Key characteristics include particle size distribution, purity, and flowability, which affect the powder’s performance in various processes.
Table: Properties and Characteristics of High Performance Metal Powders
Property | Description |
---|---|
Particle Size Distribution | Uniform particle size ensures consistent performance and quality. |
Purity | High purity levels reduce defects and enhance material properties. |
Flowability | Good flowability is essential for processes like 3D printing and powder metallurgy. |
Density | Influences the strength and structural integrity of the final product. |
Oxidation Resistance | Prevents degradation in high-temperature environments. |
Mechanical Strength | Determines the durability and load-bearing capacity of the material. |
Thermal Conductivity | Important for applications requiring heat dissipation. |
Electrical Conductivity | Crucial for electronic components and conductive materials. |
Key Takeaways:
- Particle Size Distribution: Ensures even distribution during manufacturing, resulting in consistent product quality.
- Purity: High purity metals are essential for achieving the desired mechanical and physical properties.
- Flowability: Critical for ensuring smooth operation in additive manufacturing and other powder-based processes.
- Density: Affects the overall strength and application suitability of the metal part.
- Oxidation Resistance: Protects against environmental degradation, extending the lifespan of components.
- Mechanical Strength: Key for structural applications, determining how much load a material can bear.
- Thermal Conductivity: Essential for managing heat in high-performance applications.
- Electrical Conductivity: Important for the performance of electronic and electrical components.
Advantages of High Performance Metal Powders
High performance metal powders offer numerous advantages that make them indispensable in modern manufacturing. These advantages include enhanced mechanical properties, versatility in applications, and improved production efficiency.
Table: Advantages of High Performance Metal Powders
Advantage | Description |
---|---|
Superior Mechanical Properties | High strength, hardness, and durability for demanding applications. |
Versatility | Suitable for a wide range of industries including aerospace, automotive, and medical. |
Efficiency | Enables rapid production and reduces material waste. |
Customization | Allows for tailored properties to meet specific application requirements. |
Lightweight | Reduces overall weight without compromising strength, crucial for aerospace and automotive industries. |
Corrosion Resistance | Enhances lifespan and performance in harsh environments. |
High Temperature Resistance | Suitable for applications exposed to extreme temperatures. |
Biocompatibility | Safe for medical applications such as implants and prosthetics. |
Complex Geometries | Enables the creation of intricate designs that are difficult with traditional methods. |
Sustainability | Reduces waste and energy consumption, contributing to greener manufacturing processes. |
Key Takeaways:
- Superior Mechanical Properties: Ensures components can withstand high stress and operational demands.
- Versatility: Makes high performance metal powders a go-to solution across multiple industries.
- Efficiency: Reduces production time and costs, making manufacturing more economical.
- Customization: Provides the ability to engineer materials with specific properties for specialized applications.
- Lightweight: Essential for reducing fuel consumption in aerospace and automotive applications.
- Corrosion Resistance: Important for extending the service life of components in corrosive environments.
- High Temperature Resistance: Allows use in high-stress environments such as turbines and engines.
- Biocompatibility: Critical for ensuring safety and compatibility in medical devices.
- Complex Geometries: Facilitates the production of complex parts, opening new possibilities in design and engineering.
- Sustainability: Supports environmentally friendly manufacturing practices.
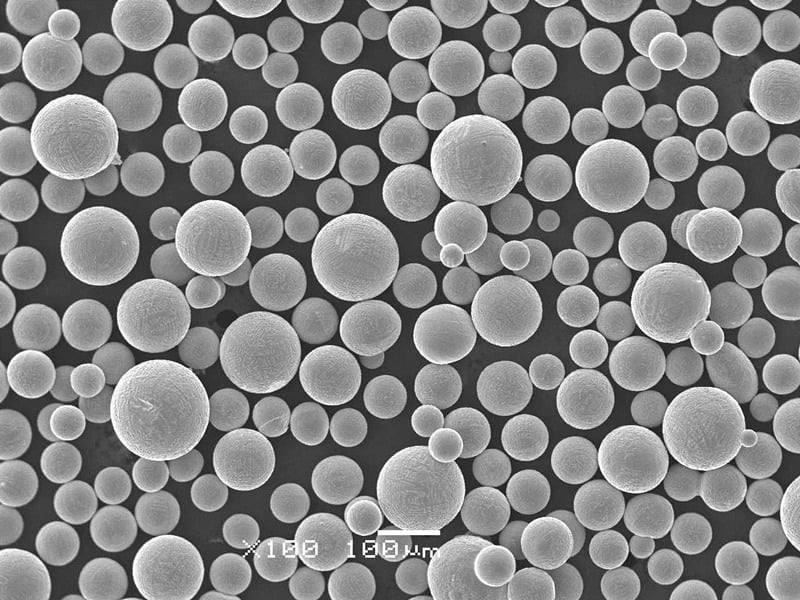
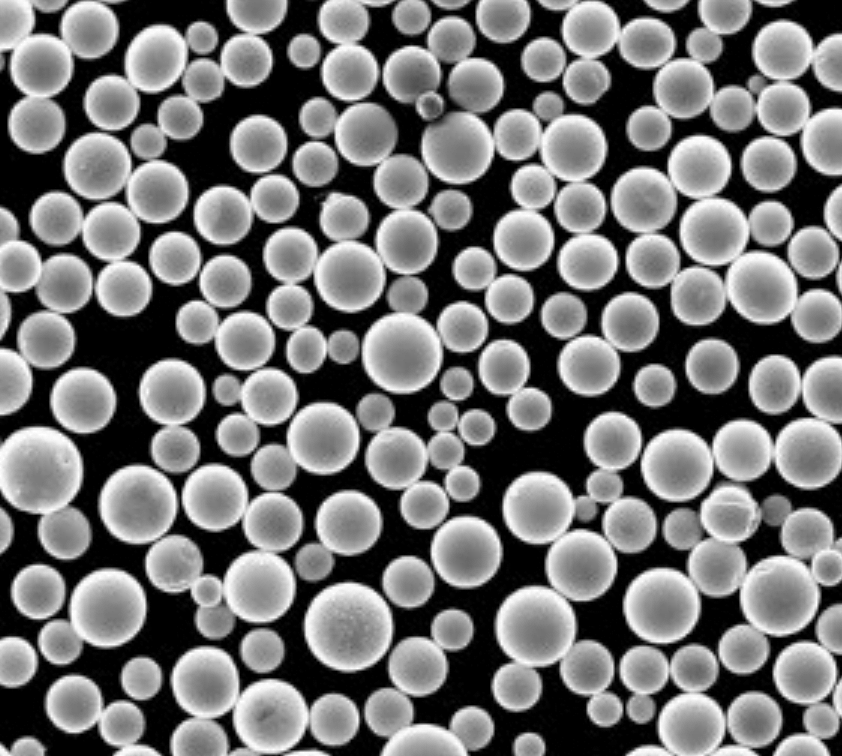
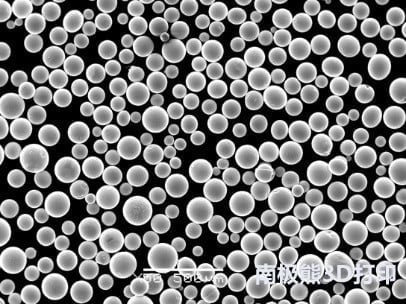
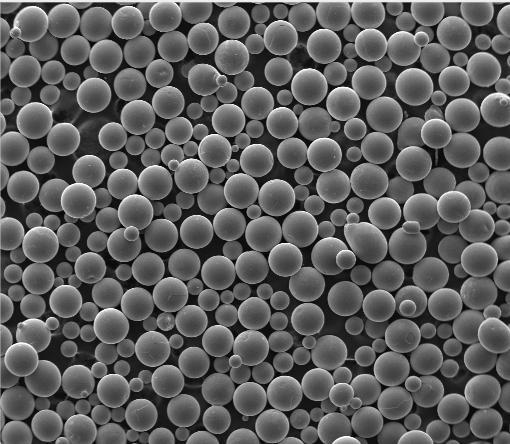
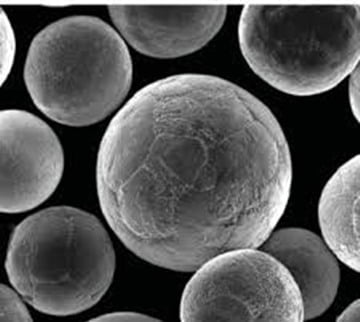
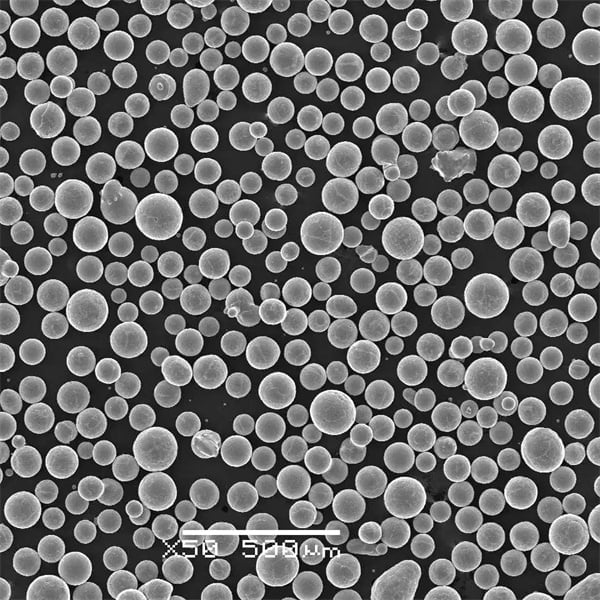
Applications of High Performance Metal Powders
High performance metal powders are used in a variety of applications, each leveraging their unique properties to enhance product performance and efficiency. These applications span multiple industries, highlighting the versatility of these materials.
Table: Applications of High Performance Metal Powders
Industry | Application | Description |
---|---|---|
Aerospace | Turbine Blades, Structural Components | High strength and lightweight properties are crucial. |
Automotive | Engine Parts, Lightweight Components | Enhances fuel efficiency and performance. |
Medical | Implants, Prosthetics, Surgical Instruments | Biocompatibility and precision are key. |
Electronics | Conductive Components, Heat Sinks | High electrical and thermal conductivity. |
Energy | Wind Turbine Components, Fuel Cells | Durability and efficiency in energy generation and storage. |
Tooling | Cutting Tools, Molds, Dies | High hardness and wear resistance for extended tool life. |
Defense | Armor, Weapon Components | High strength and lightweight for tactical advantages. |
Jewelry | Custom Designs, Intricate Details | Allows for creative and complex designs. |
Construction | Structural Parts, Fasteners | Strength and durability for building and infrastructure. |
Aviation | Engine Components, Structural Parts | High performance and reliability are essential. |
Key Takeaways:
- Aerospace: High performance metal powders are used in critical components where weight and strength are paramount.
- Automotive: These powders help reduce vehicle weight, improving fuel efficiency and performance.
Medical: Biocompatible metal powders are ideal for creating safe and durable implants and surgical tools.
Electronics: High thermal and electrical conductivity make these powders perfect for electronic components.
- Energy: Durability and efficiency are critical for components in renewable energy systems.
- Tooling: High hardness and wear resistance are essential for manufacturing tools that last longer.
- Defense: Lightweight and strong materials provide tactical advantages in defense applications.
- Jewelry: The ability to create intricate and custom designs makes these powders popular in the jewelry industry.
- Construction: Strength and durability are key for building and infrastructure components.
- Aviation: High performance metal powders ensure reliability and performance in critical aviation components.
Specifications and Standards for High Performance Metal Powders
When selecting high performance metal powders, understanding their specifications and standards is crucial. These specifications ensure that the powders meet the necessary quality and performance requirements for their intended applications.
Table: Specifications, Sizes, Grades, and Standards
Metal Powder Model | Specifications | Sizes | Grades | Standards |
---|---|---|---|---|
Stainless Steel 316L | ASTM A276, ASTM F138 | 15-45 µm | 316L | ISO 5832-1, ASTM F138 |
Titanium Alloy (Ti-6Al-4V) | ASTM F136, ASTM B348 | 20-60 µm | Grade 5 | ISO 5832-3, ASTM F136 |
Inconel 718 | AMS 5662, AMS 5663 | 15-53 µm | 718 | AMS 5662, AMS 5663 |
Aluminum Alloy (AlSi10Mg) | ASTM B928, ASTM B209 | 20-63 µm | AlSi10Mg | ASTM B209, ISO 3522 |
Copper (Cu-ETP) | ASTM B187, ASTM B152 | 10-45 µm | Cu-ETP | ASTM B187, ASTM B152 |
Tool Steel (M2) | ASTM A600, ASTM B243 | 10-50 µm | M2 | ASTM A600, ASTM B243 |
Cobalt-Chrome (CoCrMo) | ASTM F75, ASTM F799 | 15-53 µm | CoCrMo | ASTM F75, ISO 5832-4 |
Maraging Steel (18Ni300) | ASTM A538, AMS 6514 | 10-45 µm | 18Ni300 | AMS 6514, ASTM A538 |
Nickel Alloy (Ni625) | ASTM B443, AMS 5599 | 15-63 µm | 625 | ASTM B443, AMS 5599 |
Tungsten Carbide (WC) | ISO 9001, ASTM B777 | 1-30 µm | WC | ISO 9001, ASTM B777 |
Key Takeaways:
- Stainless Steel 316L: Used for its corrosion resistance, common in medical and marine applications.
- Titanium Alloy (Ti-6Al-4V): Favored in aerospace and medical implants for its strength and biocompatibility.
- Inconel 718: Utilized in high-temperature environments, particularly in aerospace and turbine industries.
- Aluminum Alloy (AlSi10Mg): Popular in automotive and aerospace for its lightweight properties.
- Copper (Cu-ETP): Essential in electronics for its excellent conductivity.
- Tool Steel (M2): Ideal for cutting tools due to its hardness and wear resistance.
- Cobalt-Chrome (CoCrMo): Common in medical implants for its biocompatibility.
- Maraging Steel (18Ni300): Used in high-stress engineering applications for its strength.
- Nickel Alloy (Ni625): Preferred for its corrosion resistance in marine and chemical environments.
- Tungsten Carbide (WC): Known for its extreme hardness, used in cutting and mining tools.
Comparing High Performance Metal Powders
Choosing the right metal powder depends on various factors such as mechanical properties, cost, and application requirements. Here, we compare different high performance metal powders to help you make an informed decision.
Table: Comparison of High Performance Metal Powders
Metal Powder Model | Strength | Cost | Corrosion Resistance | Thermal Conductivity | Electrical Conductivity |
---|---|---|---|---|---|
Stainless Steel 316L | High | Moderate | Excellent | Moderate | Low |
Titanium Alloy (Ti-6Al-4V) | Very High | High | Good | Low | Low |
Inconel 718 | Very High | Very High | Excellent | Moderate | Low |
Aluminum Alloy (AlSi10Mg) | Moderate | Low | Moderate | High | High |
Copper (Cu-ETP) | Moderate | Low | Poor | High | Very High |
Tool Steel (M2) | Very High | Moderate | Moderate | Low | Low |
Cobalt-Chrome (CoCrMo) | High | High | Excellent | Low | Low |
Maraging Steel (18Ni300) | Very High | High | Moderate | Low | Low |
Nickel Alloy (Ni625) | High | Very High | Excellent | Moderate | Low |
Tungsten Carbide (WC) | Extremely High | High | Poor | Low | Low |
Key Takeaways:
- Stainless Steel 316L: Balances strength and corrosion resistance, suitable for a wide range of applications.
- Titanium Alloy (Ti-6Al-4V): Offers the highest strength but at a higher cost, ideal for critical applications.
- Inconel 718: Provides superior strength and corrosion resistance, best for extreme environments.
- Aluminum Alloy (AlSi10Mg): Lightweight and cost-effective, great for automotive and aerospace.
- Copper (Cu-ETP): Best electrical and thermal conductivity, though less corrosion-resistant.
- Tool Steel (M2): Exceptional hardness and wear resistance, perfect for cutting tools.
- Cobalt-Chrome (CoCrMo): Excellent for medical applications due to biocompatibility and wear resistance.
- Maraging Steel (18Ni300): Offers high strength and toughness, suitable for engineering applications.
- Nickel Alloy (Ni625): Excellent for corrosion resistance, used in marine and chemical industries.
- Tungsten Carbide (WC): Provides extreme hardness, used in cutting and mining tools.
Suppliers and Pricing of High Performance Metal Powders
Knowing where to source high performance metal powders and understanding their pricing can help in planning and budgeting for your projects.
Table: Suppliers and Pricing Details
Supplier | Metal Powder Model | Price (per kg) | Availability |
---|---|---|---|
Sandvik | Stainless Steel 316L | $80 | High |
Carpenter Technology | Titanium Alloy (Ti-6Al-4V) | $150 | Moderate |
Höganäs | Inconel 718 | $200 | High |
LPW Technology | Aluminum Alloy (AlSi10Mg) | $50 | High |
Kymera International | Copper (Cu-ETP) | $30 | High |
Arcam AB | Tool Steel (M2) | $90 | Moderate |
HC Starck | Cobalt-Chrome (CoCrMo) | $180 | Moderate |
Aubert & Duval | Maraging Steel (18Ni300) | $160 | High |
VSMPO-AVISMA | Nickel Alloy (Ni625) | $220 | High |
Global Tungsten & Powders | Tungsten Carbide (WC) | $100 | High |
Key Takeaways:
- Sandvik: Reliable supplier of stainless steel powders with high availability.
- Carpenter Technology: Offers titanium alloys at a premium price, with moderate availability.
- Höganäs: Supplies Inconel powders, ideal for high-temperature applications.
- LPW Technology: Affordable aluminum alloy powders, widely available.
- Kymera International: Provides cost-effective copper powders.
- Arcam AB: Offers tool steel powders with moderate availability.
- HC Starck: Supplies high-quality cobalt-chrome powders.
- Aubert & Duval: Reliable source for maraging steel powders.
- VSMPO-AVISMA: Premium supplier of nickel alloys.
- Global Tungsten & Powders: Provides tungsten carbide powders, essential for cutting tools.
Pros and Cons of High Performance Metal Powders
High performance metal powders offer a mix of advantages and limitations. Understanding these can help you make informed decisions based on your specific needs and applications.
Table: Pros and Cons of High Performance Metal Powders
Pros | Cons |
---|---|
High Strength | Cost: Can be expensive depending on the metal. |
Versatility | Availability: Some powders have limited suppliers. |
Customization | Processing Complexity: Requires specialized equipment. |
Corrosion Resistance | Oxidation: Some powders are prone to oxidation. |
Lightweight | Density: Not all powders are lightweight. |
High Temperature Resistance | Thermal Conductivity: Varies by metal type. |
Biocompatibility | Electrical Conductivity: Not all powders are conductive. |
Complex Geometries | Material Waste: Potential for waste in some processes. |
Sustainability | Production Time: Can be longer for complex parts. |
Key Takeaways:
- High Strength: Essential for demanding applications, but can increase costs.
- Versatility: Suitable for multiple industries, though availability can vary.
- Customization: Offers tailored properties, but may require advanced processing techniques.
- Corrosion Resistance: Extends component lifespan, though some powders are more prone to oxidation.
- Lightweight: Important for reducing weight, but not all powders offer this benefit.
- High Temperature Resistance: Crucial for high-stress environments, though thermal conductivity varies.
- Biocompatibility: Ideal for medical applications, though not all powders are suitable for electrical uses.
- Complex Geometries: Enables innovative designs, but can result in material waste.
- Sustainability: Supports green manufacturing, though production times can be longer for intricate parts.
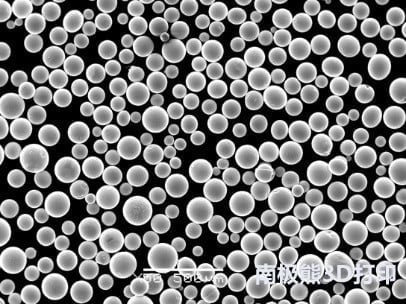
FAQs
Table: Frequently Asked Questions
Question | Answer |
---|---|
What are high performance metal powders? | They are finely powdered metals engineered for superior mechanical properties and versatility. |
What industries use high performance metal powders? | Aerospace, automotive, medical, electronics, energy, tooling, defense, jewelry, construction, and aviation. |
How are high performance metal powders made? | Through processes like atomization, mechanical alloying, and chemical reduction. |
What are the benefits of using high performance metal powders? | Superior strength, versatility, efficiency, customization, and sustainability. |
Can high performance metal powders be recycled? | Yes, they can be recycled, reducing material waste and supporting sustainable practices. |
Are high performance metal powders expensive? | Costs vary by metal type and supplier, but they can be more expensive due to their advanced properties. |
How do you select the right metal powder? | Consider application requirements, mechanical properties, cost, and supplier availability. |
What is the role of particle size in metal powders? | It affects the powder’s flowability, packing density, and overall performance in manufacturing processes. |
Are there any safety concerns with metal powders? | Yes, handling and processing require safety measures to prevent inhalation and combustion risks. |
What is additive manufacturing with metal powders? | A process that builds 3D objects layer by layer using metal powders, commonly known as 3D printing. |
About 3DP mETAL
Product Category
CONTACT US
Any questions? Send us a message now! After receiving your message, we will process your request with a whole team.