When it comes to advanced manufacturing, Hot Isostatic Pressing (HIP) metal powders stand out as game-changers. If you’re diving into the world of HIP metal powders, you’re in for a treat. In this guide, we’ll walk you through everything you need to know about HIP metal powders, from what they are to their applications, advantages, and even specific models. So, grab a cup of coffee, and let’s explore the fascinating world of HIP metal powders together!
Overview of HIP Metal Powders
HIP, or Hot Isostatic Pressing, is a manufacturing process that uses high temperature and high pressure to improve the properties and performance of metal powders. This process results in materials with superior density, mechanical properties, and uniformity. HIP metal powders are crucial in industries like aerospace, medical, automotive, and more, where high performance and reliability are essential.
What Makes HIP Metal Powders Special?
HIP metal powders are known for their ability to create parts with minimal porosity and high structural integrity. This means stronger, more durable components that can withstand harsh conditions. The HIP process also allows for the production of complex shapes and designs that would be challenging or impossible to achieve through traditional manufacturing methods.
Key Benefits of HIP Metal Powders:
- Enhanced Strength and Durability: The HIP process eliminates internal voids, resulting in materials with superior mechanical properties.
- Improved Fatigue Resistance: Components made from HIP metal powders can endure repetitive stress without failure.
- Uniform Properties: The process ensures consistent material properties throughout the component.
- Complex Geometries: HIP allows for the production of intricate designs that meet specific application requirements.
- Cost-Effective: Reduces material waste and post-processing steps, leading to cost savings in the long run.
Now, let’s delve into the specifics of different HIP metal powder models and their applications.
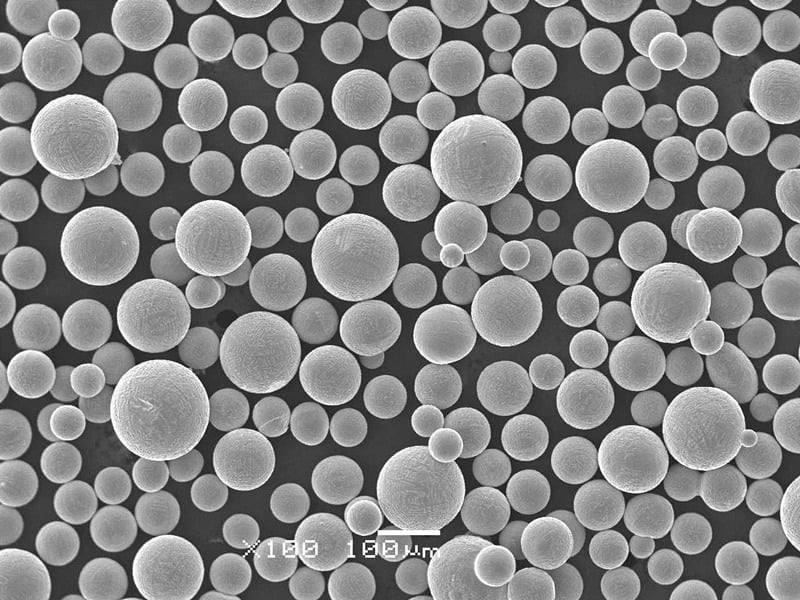
Types and Descriptions of HIP Metal Powders
Below is a detailed table showcasing various HIP metal powder models, their composition, properties, and characteristics.
Model | Composition | Properties | Characteristics |
---|---|---|---|
Ti-6Al-4V | Titanium, Aluminum, Vanadium | High strength, lightweight, excellent corrosion resistance | Widely used in aerospace and medical implants |
Inconel 718 | Nickel, Chromium, Iron | High temperature strength, corrosion resistance | Ideal for gas turbine engines and other high-temperature applications |
316L SS | Stainless Steel | Excellent corrosion resistance, good weldability | Common in medical devices and marine applications |
CoCrMo | Cobalt, Chromium, Molybdenum | High wear resistance, biocompatible | Perfect for orthopedic implants and dental devices |
AlSi10Mg | Aluminum, Silicon, Magnesium | High strength-to-weight ratio, good thermal conductivity | Used in lightweight structural components |
Maraging Steel | Nickel, Molybdenum, Cobalt | Ultra-high strength, toughness | Favored in tooling and aerospace sectors |
17-4 PH SS | Stainless Steel | High strength, hardness, corrosion resistance | Utilized in aerospace, chemical, and petrochemical industries |
Hastelloy X | Nickel, Molybdenum, Chromium | High temperature strength, oxidation resistance | Suitable for jet engine components and chemical processing |
CuCrZr | Copper, Chromium, Zirconium | High thermal and electrical conductivity, strength | Used in electrical contacts and heat exchangers |
Tungsten Carbide | Tungsten, Carbon | Extreme hardness, wear resistance | Ideal for cutting tools and wear-resistant components |
Applications of HIP Metal Powders
HIP metal powders find applications across various industries due to their unique properties and advantages. Here’s a comprehensive table highlighting the key applications.
Industry | Applications | Key Benefits |
---|---|---|
Aerospace | Turbine blades, engine components, structural parts | High strength-to-weight ratio, fatigue resistance |
Medical | Implants, surgical instruments | Biocompatibility, corrosion resistance |
Automotive | Engine parts, transmission components | Durability, wear resistance |
Oil & Gas | Drilling equipment, valves, fittings | Corrosion resistance, high strength |
Tooling | Dies, molds, cutting tools | Hardness, wear resistance |
Energy | Heat exchangers, electrical contacts | Thermal conductivity, strength |
Defense | Armor, weapons components | Toughness, high performance |
Electronics | Conductive components, connectors | Electrical conductivity, thermal management |
Marine | Propellers, pumps, marine hardware | Corrosion resistance, durability |
Chemical | Reactor components, processing equipment | Chemical resistance, high temperature performance |
Specifications, Sizes, Grades, Standards
To help you choose the right HIP metal powder for your application, here’s a detailed table outlining their specifications, sizes, grades, and standards.
Model | Specifications | Sizes (µm) | Grades | Standards |
---|---|---|---|---|
Ti-6Al-4V | ASTM F2924 | 15-45, 45-105 | Grade 23 | ASTM, ISO |
Inconel 718 | AMS 5662, ASTM B637 | 15-45, 45-105 | – | AMS, ASTM |
316L SS | ASTM F138, F139 | 15-45, 45-105 | – | ASTM, ISO |
CoCrMo | ASTM F75 | 15-45, 45-105 | – | ASTM, ISO |
AlSi10Mg | – | 15-45, 45-105 | – | – |
Maraging Steel | ASTM A579, A646 | 15-45, 45-105 | Grade 250 | ASTM, AMS |
17-4 PH SS | AMS 5643, ASTM A693 | 15-45, 45-105 | – | AMS, ASTM |
Hastelloy X | ASTM B572 | 15-45, 45-105 | – | ASTM, AMS |
CuCrZr | – | 15-45, 45-105 | – | – |
Tungsten Carbide | ISO 9001 | 15-45, 45-105 | – | ISO, ASTM |
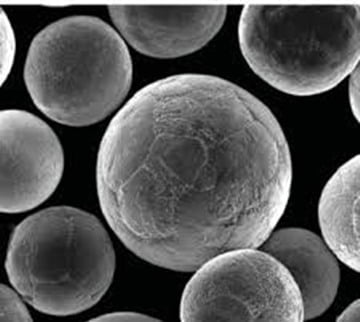
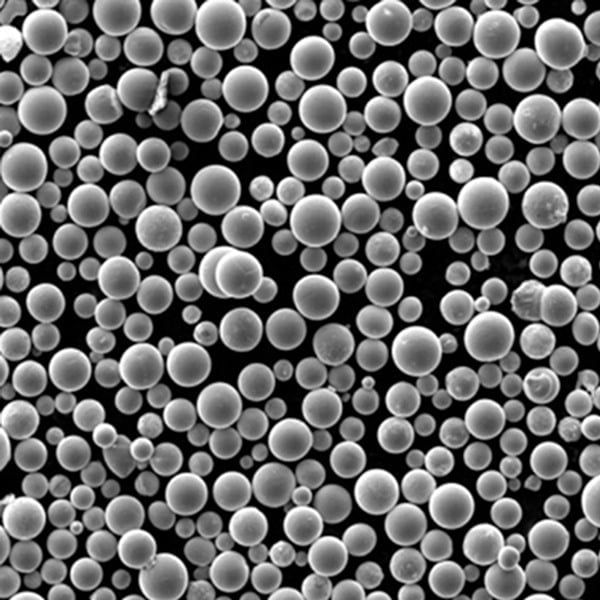
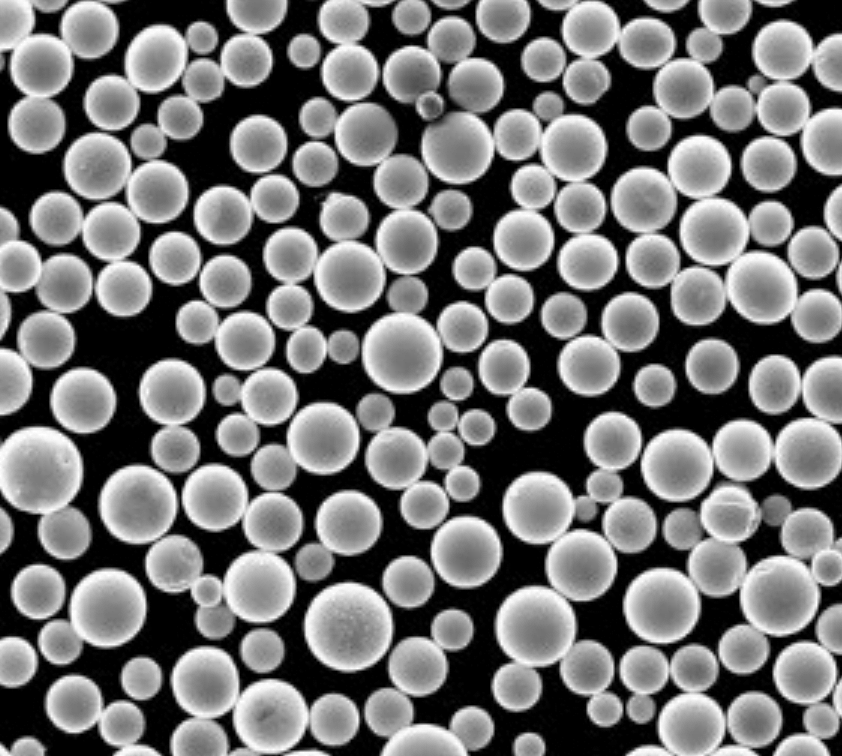
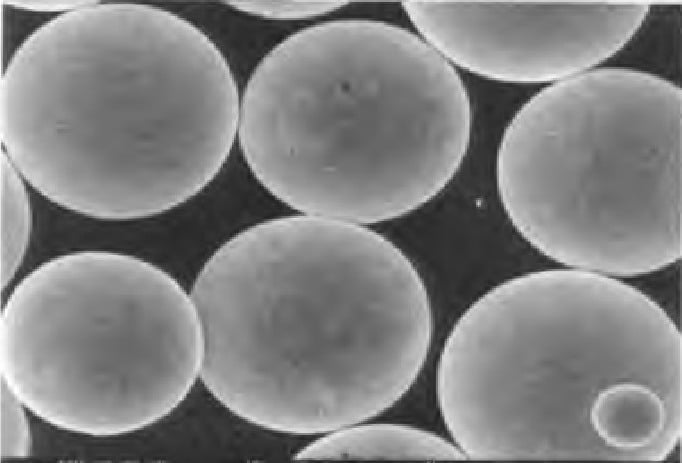
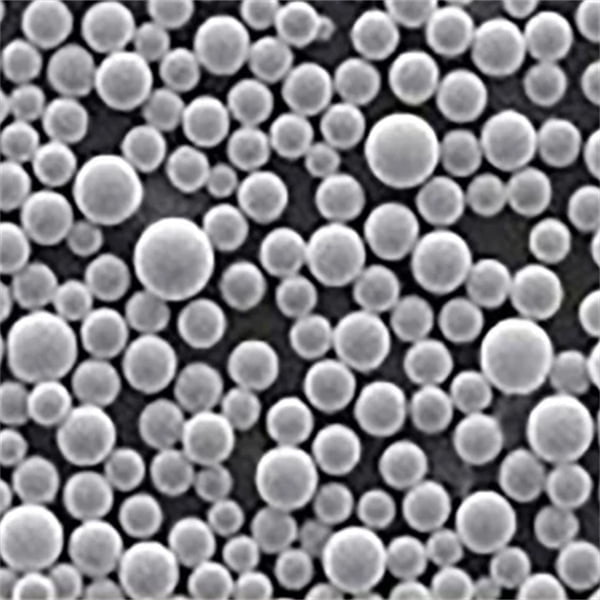
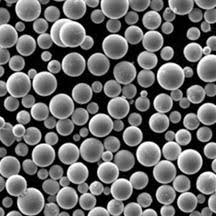
Suppliers and Pricing Details
Finding the right supplier is crucial for sourcing high-quality HIP metal powders. Here’s a table listing some reputable suppliers along with pricing details.
Supplier | Location | Key Products | Price Range ($/kg) |
---|---|---|---|
Carpenter Technology | USA | Ti-6Al-4V, 17-4 PH SS | 100-300 |
Höganäs AB | Sweden | Inconel 718, Maraging Steel | 150-400 |
Sandvik Materials Technology | Sweden | Hastelloy X, CoCrMo | 200-500 |
GKN Additive | Global | AlSi10Mg, 316L SS | 50-200 |
Kennametal | USA | Tungsten Carbide, CuCrZr | 300-700 |
Arcam AB | Sweden | Ti-6Al-4V, Inconel 718 | 150-400 |
AP&C | Canada | Ti-6Al-4V, Hastelloy X | 200-500 |
Praxair Surface Technologies | USA | 17-4 PH SS, CoCrMo | 100-350 |
LPW Technology | UK | Inconel 718, AlSi10Mg | 120-300 |
EOS GmbH | Germany | Various HIP powders | 100-400 |
Pros and Cons of HIP Metal Powders
Understanding the advantages and limitations of HIP metal powders is essential for making informed decisions. Here’s a detailed comparison:
Pros | Cons |
---|---|
Enhanced Mechanical Properties: Superior strength, hardness, and fatigue resistance | High Cost: HIP processing can be expensive compared to traditional methods |
Reduced Porosity: Minimizes internal voids, leading to higher density materials | Complex Process: Requires precise control of temperature and pressure |
Improved Uniformity: Consistent material properties throughout the component | Equipment Investment: Requires specialized equipment and facilities |
Design Flexibility: Allows for the production of complex shapes and geometries | Longer Lead Times: The process can be time-consuming |
Material Efficiency: Reduces waste and post-processing needs | Limited Material Availability: Not all materials are suitable for HIP |
Enhanced Wear and Corrosion Resistance: Ideal for harsh environments | Knowledge and Expertise: Requires skilled operators and engineers |
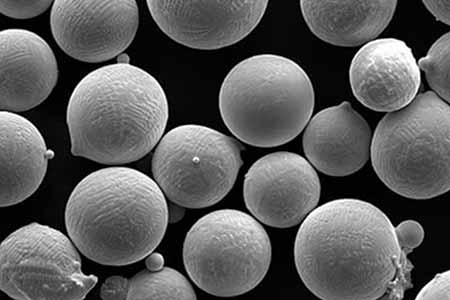
FAQ
To make things easier, here are some common questions about HIP metal powders answered in a straightforward manner.
Question | Answer |
---|---|
What is HIP? | HIP stands for Hot Isostatic Pressing, a process using high temperature and pressure to enhance material properties. |
What are the benefits of HIP metal powders? | They offer superior strength, durability, uniformity, and the ability to create complex shapes. |
Which industries use HIP metal powders? | Aerospace, medical, automotive, oil & gas, tooling, energy, defense, electronics, marine, and chemical industries. |
Are HIP metal powders expensive? | They can be more expensive due to the processing costs but offer long-term benefits and cost savings in certain applications. |
Can HIP be used for all metals? | Not all metals are suitable for HIP; it works best with specific alloys that benefit from the process. |
What sizes are available for HIP metal powders? | Sizes typically range from 15-105 micrometers, depending on the application requirements. |
How do I choose the right HIP metal powder? | Consider the application, required properties, and compatibility with HIP processing. |
Are there environmental benefits to using HIP metal powders? | Yes, they reduce waste and material usage, contributing to more sustainable manufacturing practices. |
Can HIP metal powders be recycled? | Yes, many HIP metal powders can be recycled, though the process and feasibility depend on the specific material. |
Where can I buy HIP metal powders? | From reputable suppliers like Carpenter Technology, Höganäs AB, Sandvik Materials Technology, and others listed above. |
Conclusion
HIP metal powders are revolutionizing manufacturing by offering superior material properties, design flexibility, and cost efficiency. Whether you’re in aerospace, medical, automotive, or any other industry that demands high-performance materials, HIP metal powders provide a compelling solution. From their unique benefits to detailed specifications and applications, this guide covers everything you need to know about HIP metal powders. So, go ahead and explore the possibilities – the future of manufacturing is here, and it’s powered by HIP metal powders!
About 3DP mETAL
Product Category
CONTACT US
Any questions? Send us a message now! After receiving your message, we will process your request with a whole team.