Imagine crafting complex metal parts layer by layer, not with glue and plastic, but with the focused power of electrons. That’s the magic of Electron Beam Melting (EBM), a revolutionary 3D printing technology that’s transforming the way we manufacture intricate components. But how exactly does EBM work? What kind of metal parts can it create? And is it the right fit for your next project? Buckle up, because we’re diving deep into the world of EBM, unraveling its secrets and exploring its potential.
A Symphony of Electrons and Metal Powder
EBM operates in a realm of high vacuum and intense heat. Here’s a breakdown of the key steps involved:
- Setting the Stage: The EBM chamber is evacuated to near-perfect vacuum, removing any air molecules that could interfere with the melting process. This pristine environment ensures clean welds and minimizes oxidation.
- Kekuatan Bubuk: A thin layer of metal powder, meticulously chosen for its properties, is spread across the build platform. Think of it as a bed of tiny, metallic grains waiting to be sculpted.
- Electron Beam: The Sculpting Tool: An electron gun fires a highly focused beam of electrons. Imagine a miniature, supercharged spotlight. This beam scans across the powder bed, precisely melting the desired areas according to the digital design.
- Membangun Blok demi Blok: As the electron beam melts the powder, it fuses the particles together, forming a solid layer. The build platform then lowers slightly, and a fresh layer of powder is deposited. This meticulous dance of melting and layering continues until the entire part is complete.
- Unearthing the Treasure: Once the build is finished, the chamber is brought back to atmospheric pressure. The completed part is then removed from the surrounding unmelted powder, a process called de-powdering. This metallic marvel is then ready for post-processing steps like support removal and surface finishing.
Think of EBM as a sophisticated 3D printing chef. The metal powder is the key ingredient, the electron beam is the heat source, and the build chamber is the kitchen. Each layer meticulously added creates a complex dish, in this case, a high-performance metal component.
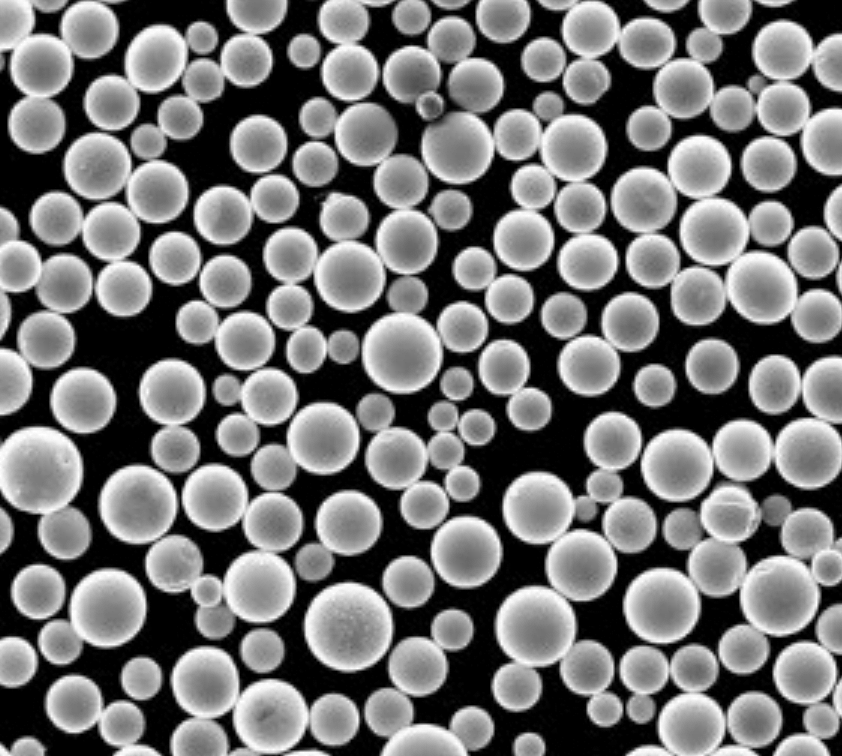
Metal Powders for EBM
The success of EBM hinges on the specific metal powder used. Different powders offer unique properties, making them ideal for diverse applications. Here are 10 noteworthy metal powders for EBM, along with their characteristics:
Bahan | Deskripsi |
---|---|
Titanium Ti-6Al-4V (Grade 23) | The workhorse of EBM powders, offering excellent strength-to-weight ratio, biocompatibility, and corrosion resistance. Widely used in aerospace, medical implants, and motorsport components. |
Inconel 625 | A high-performance nickel-chromium alloy renowned for its exceptional resistance to heat, corrosion, and oxidation. Ideal for parts operating in harsh environments like jet engines and chemical processing equipment. |
Baja Tahan Karat 316L | A versatile stainless steel powder known for its good corrosion resistance and biocompatibility. Used in medical devices, fluid handling components, and general-purpose parts. |
CoCrMo (Cobalt-Chrome-Molybdenum) | A biocompatible alloy favored in the medical device industry due to its excellent wear resistance and resistance to body fluids. Common in hip and knee replacements. |
Aluminium AlSi10Mg | An aluminum alloy offering a good balance of strength, weight, and castability. Used in automotive and aerospace applications where weight reduction is crucial. |
Tembaga | Pure copper powder enables the creation of highly conductive parts for electrical applications like heat sinks and busbars. However, special considerations are needed due to copper’s high thermal conductivity. |
Wolfram | Renowned for its extreme heat resistance, tungsten powder finds applications in furnaces, rocket engine components, and other high-temperature environments. |
Menikahi Baja | A family of high-strength, low-alloy steels known for their exceptional toughness and dimensional stability. Used in aerospace components and tooling applications. |
Nikel | Pure nickel powder offers good corrosion resistance and electrical conductivity. Used in electronic components and applications requiring high electrical performance. |
Tantalum | A versatile material with exceptional biocompatibility, high melting point, and good corrosion resistance. Used in medical implants, capacitors, and other specialized applications. |
Choosing the right metal powder is like selecting the perfect spice for a dish. Each powder offers a unique flavor of properties, and the ideal choice depends on the specific requirements of the final component.
Applications Bringing Metal 3D Printing to Life
EBM’s ability to create complex, high-performance metal parts unlocks a world of possibilities across various industries. Here are some key application areas where EBM thrives:
- Dirgantara: Weight reduction is paramount in aircraft design. EBM allows for the creation of lightweight, high-strength components like brackets, housings, and even engine parts using materials like titanium and aluminum alloys. This translates to increased fuel efficiency and improved aircraft performance.
- Implan Medis: EBM’s biocompatible powders like titanium and cobalt-chrome are ideal for manufacturing customized implants like hip and knee replacements. These implants offer excellent wear resistance, osseointegration (bone bonding), and long-term functionality, improving patient outcomes.
- Olahraga motor: The relentless pursuit of speed and performance in motorsports finds a perfect partner in EBM. Complex, lightweight components like gear housings, suspension parts, and even engine components can be created using high-strength materials like titanium and Inconel. This translates to significant weight reduction and improved vehicle performance.
- Sektor Energi: EBM enables the creation of intricate components for turbines, heat exchangers, and other equipment operating in harsh environments. Materials like Inconel 625 offer exceptional resistance to heat, corrosion, and oxidation, ensuring the longevity and reliability of these critical parts.
- Pertahanan dan Keamanan: EBM’s ability to manufacture complex, high-strength components makes it valuable for the defense industry. Components like weapon parts, armor components, and even custom tools can be created using materials known for their outstanding strength and durability.
- Perkakas: EBM-produced tools boast exceptional wear resistance and dimensional stability, making them ideal for applications like injection molding tools and metal forming dies. Maraging steel powders are particularly well-suited for these applications due to their high toughness and ability to maintain precise shapes under pressure.
These are just a few examples, and the potential applications of EBM continue to expand as the technology matures. As new materials and design techniques emerge, EBM is poised to revolutionize the way we manufacture complex, high-performance metal parts across various industries.
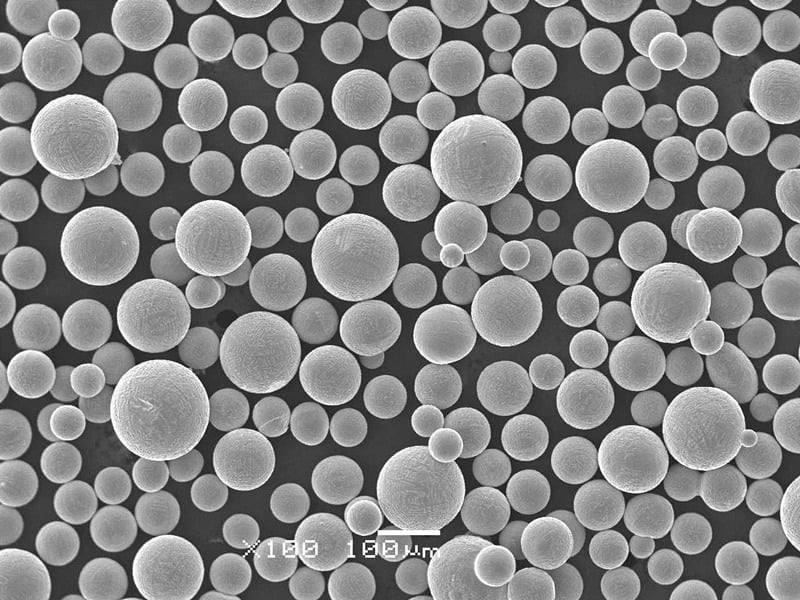
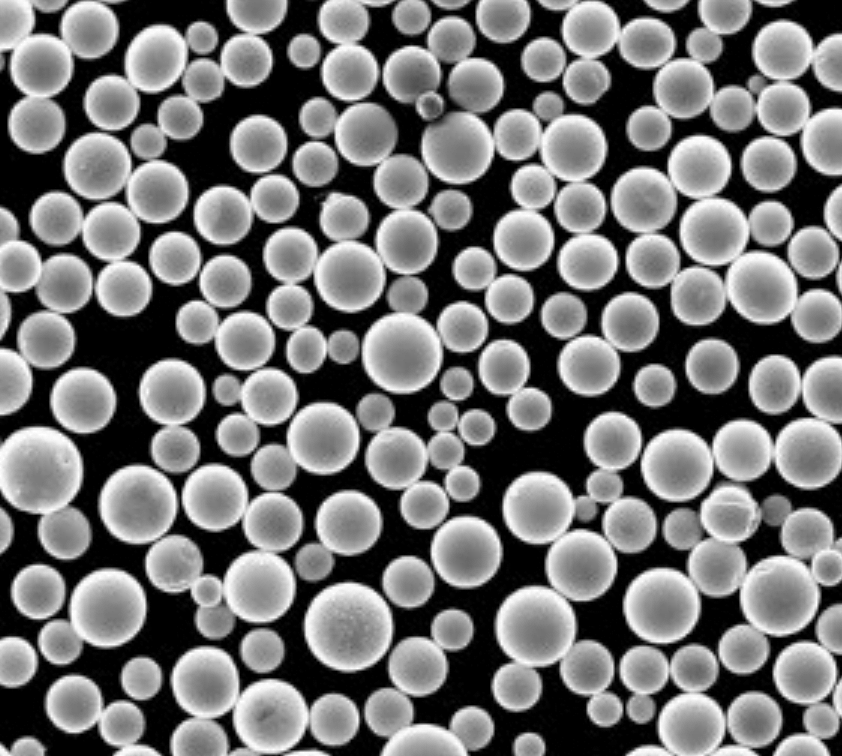
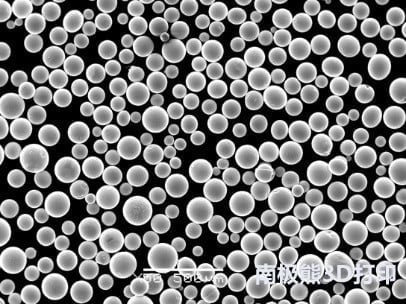
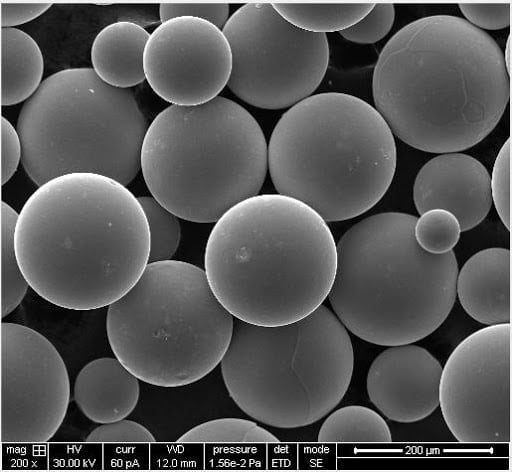
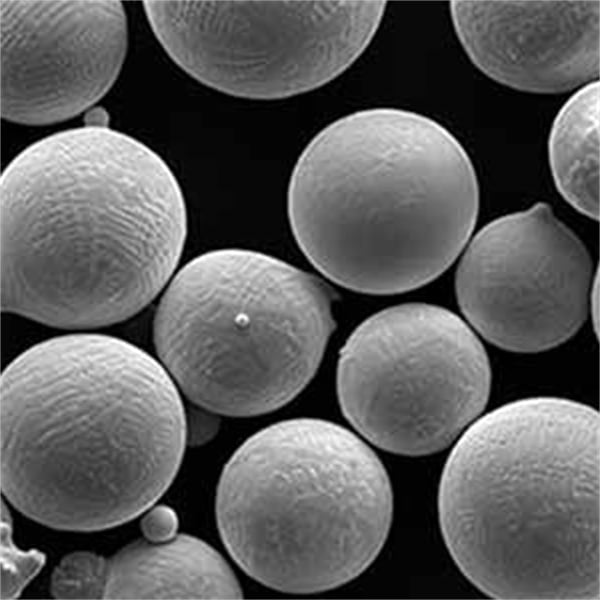
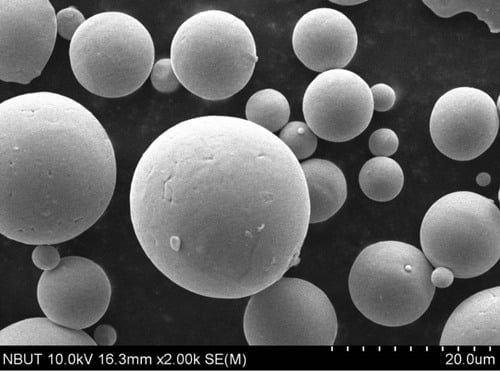
Keuntungan dan Keterbatasan
EBM offers a unique set of advantages that make it a compelling choice for specific applications. However, it also comes with limitations that need to be considered. Let’s delve into both sides of the coin:
Advantages of EBM:
- High-Quality Parts: EBM produces near-net-shape components with excellent mechanical properties, including high strength, good fatigue resistance, and superior surface finishes. This translates to parts that can withstand demanding environments and perform reliably for extended periods.
- Kebebasan Desain: EBM allows for the creation of complex geometries with internal channels, lattices, and other intricate features that would be impossible with traditional manufacturing techniques. This design freedom opens doors for innovative and lightweight parts with improved functionality.
- Keserbagunaan Material: EBM can work with a wide range of metal powders, including reactive metals like titanium and refractory metals like tungsten. This versatility allows for the creation of parts with specific properties tailored to the application.
- Vacuum Environment: The high-vacuum environment minimizes oxidation and contamination during the melting process, leading to cleaner welds and improved material properties compared to laser-based powder bed fusion techniques.
Keterbatasan EBM:
- Membangun Kecepatan: Compared to other metal 3D printing technologies like Selective Laser Melting (SLM), EBM is generally slower. This is because the electron beam needs to travel through a vacuum, adding processing time.
- Kekasaran Permukaan: EBM parts can have a slightly rougher surface finish compared to SLM parts. However, post-processing techniques like machining and polishing can help achieve a smoother finish if required.
- Material Costs: Metal powders for EBM can be more expensive than some materials used in other metal 3D printing processes. This can impact the overall cost of the finished part.
- Struktur Pendukung: EBM requires intricate support structures to prevent warping and distortion during the build process. Removal of these supports can be a time-consuming and potentially delicate task.
Choosing EBM involves carefully weighing the advantages against the limitations. For applications where high-quality, complex metal parts are needed, and the potential benefits outweigh the slower build speed and higher material costs, EBM can be the perfect solution.
EBM vs. Other Metal 3D Printing Techniques
EBM isn’t the only contender in the metal 3D printing arena. Here’s a quick comparison of EBM with two other popular technologies:
EBM vs. Selective Laser Melting (SLM):
- Heat Source: EBM uses a focused electron beam, while SLM uses a laser beam.
- Membangun Kecepatan: EBM is generally slower than SLM.
- Permukaan akhir: EBM parts can have a slightly rougher surface finish compared to SLM parts. However, both technologies can achieve good surface quality with proper post-processing.
- Kompatibilitas Material: EBM offers better compatibility with reactive metals like titanium due to the high-vacuum environment.
- Aplikasi: Both EBM and SLM are suitable for high-performance metal parts. However, EBM might be preferred for applications requiring biocompatible materials or intricate internal features.
EBM vs. Binder Jetting (BJ):
- Proses: EBM melts metal powder layer-by-layer, while BJ binds metal powder particles with a liquid binder before infiltration with a sintering agent.
- Material Range: EBM offers a wider range of metal materials, including reactive and refractory metals. BJ is typically limited to ferrous materials like steel.
- Part Strength: EBM-produced parts generally have higher strength due to the melting process compared to BJ parts, which rely on sintering.
- Biaya: BJ is generally faster and more cost-effective than EBM. However, EBM parts offer superior mechanical properties for demanding applications.
Ultimately, the choice between EBM, SLM, and BJ depends on the specific needs of the project. Consider factors like the desired material properties, part complexity, required build speed, and budget constraints when making your decision.
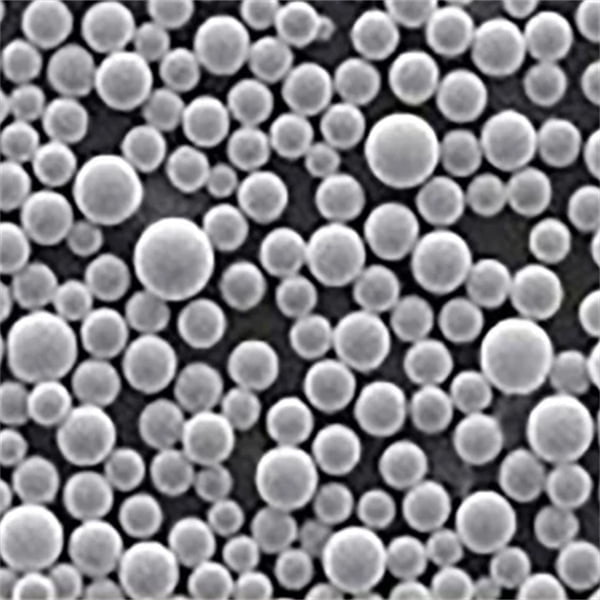
Pertanyaan yang Sering Diajukan (FAQ)
Here are some frequently asked questions about EBM, answered in a clear and concise format:
Pertanyaan | Jawaban |
---|---|
What is the difference between EBM and SLM? | Both EBM and SLM are metal 3D printing technologies that use a laser or electron beam to melt metal powder layer-by-layer to create a 3D object. However, EBM uses an electron beam in a vacuum environment, while SLM uses a laser beam in an inert gas atmosphere. This difference leads to variations in build speed, surface finish, and material compatibility. |
What are the advantages of EBM? | EBM offers several advantages, including the ability to produce high-quality parts with excellent mechanical properties, design freedom for complex geometries, material versatility for a wide range of metals, and a clean vacuum environment for minimal oxidation. |
What are the limitations of EBM? | EBM has limitations such as slower build speed compared to some other metal 3D printing technologies, slightly rougher surface finish in some cases, potentially higher material costs, and the need for intricate support structures. |
What materials can be used with EBM? | EBM can work with a wide variety of metal powders, including titanium alloys, nickel alloys, stainless steel, cobalt-chrome, aluminum alloys, copper, tungsten, and more. |
What are some applications of EBM? | EBM is used in various industries to create complex, high-performance metal parts. Some common applications include aerospace components, medical implants, motorsports parts, energy sector components, defense and security components, and tooling. |
Is EBM right for my project? | EBM can be a great choice for projects requiring high-quality, complex metal parts with excellent mechanical properties. However, factors like build speed, budget constraints, and desired material properties need to be considered when making the decision. |
Tentang LOGAM 3DP
Kategori Produk
HUBUNGI KAMI
Ada pertanyaan? Kirim pesan sekarang! Setelah menerima pesan Anda, kami akan memproses permintaan Anda bersama seluruh tim.