Iron alloy powders are the unsung heroes of the metalworking world. These tiny, metallic marvels are much more than just crushed-up bits of iron. They are meticulously crafted materials with unique properties that come together to form the backbone of countless industries.
Imagine a world without gears, bearings, cutting tools, and even complex machine parts. That’s the reality we might face without iron alloy powders. These versatile materials have revolutionized manufacturing, allowing us to create intricate shapes and components with exceptional precision and efficiency.
But before we delve into the exciting world of iron alloy powders, let’s take a step back and understand what they truly are.
What are Iron Alloy Powders?
Iron alloy powders are finely divided metallic particles consisting primarily of iron, but often blended with other elements like nickel, chromium, molybdenum, and copper. Think of them as microscopic building blocks for metal components. These powders are produced through various techniques, such as water atomization and gas atomization, which involve transforming molten metal into a fine mist that rapidly solidifies into tiny spheres.
The beauty of iron alloy powders lies in their tailorability. By adjusting the composition, particle size, and processing techniques, manufacturers can create powders with a wide range of properties, making them suitable for a vast array of applications.
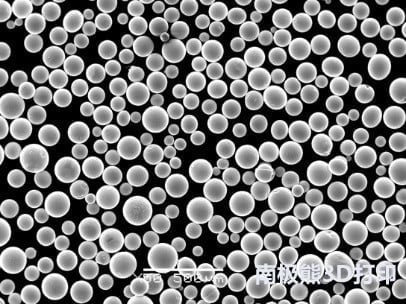
Different Iron Alloy Powder Types
The world of iron alloy powders is a diverse one, with each type offering distinct advantages. Let’s explore some of the most common models and their unique characteristics:
Berperan sebagai penerjemah dan penyempurna,Terjemahkan teks berikut ke dalam bahasa ID: Model | Komposisi | Properti | APLIKASI |
---|---|---|---|
Low-Alloy Steel Powders | Fe (Iron) + Small amounts of C (Carbon), Mn (Manganese), Cu (Copper) | High compressibility, good machinability | Gears, bearings, structural components |
Nickel Steel Powders | Fe (Iron) + Ni (Nickel) | High strength, good ductility, wear resistance | Gears, shafts, cutting tools |
Bubuk Baja Tahan Karat | Fe (Iron) + Cr (Chromium), Ni (Nickel) | Ketahanan korosi yang sangat baik, kekuatan tinggi | Medical implants, fasteners, pump components |
Nickel-Chromium Powders | Fe (Iron) + Ni (Nickel) + Cr (Chromium) | High-temperature oxidation resistance, good strength | Furnace components, heat exchangers |
Molybdenum Steel Powders | Fe (Iron) + Mo (Molybdenum) | Improved hardenability, good toughness | High-strength fasteners, cutting tools |
Copper Steel Powders | Fe (Iron) + Cu (Copper) | Enhanced machinability, improved conductivity | Electrical components, automotive parts |
High-Carbon Steel Powders | Fe (Iron) + Higher C (Carbon) content | Ketahanan aus yang sangat baik, kekerasan tinggi | Alat pemotong, pelat aus |
Tool Steel Powders | Fe (Iron) + Alloying elements like W (Tungsten), Cr (Chromium), V (Vanadium) | Exceptional hardness, wear resistance | High-performance cutting tools, dies |
Soft Magnetic Powders | Fe (Iron) + Si (Silicon) | Permeabilitas magnetik tinggi, koersivitas rendah | Electrical transformers, magnetic cores |
Invar Powders | Fe (Iron) + Ni (Nickel) | Low thermal expansion coefficient | Precision instruments, optical components |
Breaking it Down:
- Low-alloy steel powders are the workhorses of the industry, offering a good balance of cost, formability, and machinability. They are ideal for creating gears, bearings, and various structural components.
- Nickel steel powders step up the game with their enhanced strength and wear resistance. Gears, shafts, and cutting tools benefit greatly from these properties.
- Stainless steel powders bring corrosion resistance to the forefront, making them perfect for medical implants, fasteners, and pump components where hygiene and durability are paramount.
- Nickel-chromium powders are the heat shields of the powder world, offering exceptional resistance to high-temperature oxidation. They find their place in furnace components and heat exchangers.
- Molybdenum steel powders are the tough guys, boasting improved hardenability and toughness. They are the go-to choice for high-strength fasteners and cutting tools.
This list just scratches the surface of the vast array of iron alloy powders available. But it gives you a glimpse into the possibilities these versatile materials offer.
Aplikasi dari Bubuk Paduan Besi
Iron alloy powders have revolutionized manufacturing by enabling the creation of complex and intricate components through a process called powder metallurgy (PM). In PM, the powders are compacted into the desired shape and then sintered, which involves heating them to a high temperature below the melting point to promote bonding between the particles.
Here’s a closer look at some of the key applications of iron alloy powders, showcasing their diverse capabilities:
- Industri Otomotif: From intricate gears and bearings in transmissions to durable components in braking systems, iron alloy powders play a crucial role in keeping vehicles running smoothly. Their ability to be shaped into complex geometries makes them ideal for these applications.
- Advantage: Compared to traditional machining methods, iron alloy powders offer near-net-shape manufacturing, which minimizes material waste and production time.
- Disadvantage: Certain high-performance automotive components might require materials produced through traditional casting or forging techniques for ultimate strength.
- Industri Kedirgantaraan: The relentless pursuit of lightweight yet robust materials makes iron alloy powders a valuable asset in the aerospace industry. They are used in components like landing gear parts and lightweight structural components.
- Advantage: The ability to control the density of iron alloy powders allows for the creation of lightweight yet strong components, crucial for fuel efficiency in aircrafts.
- Disadvantage: Strict performance requirements in the aerospace industry might necessitate additional processes like heat treatment to achieve the desired mechanical properties.
- Elektronik Konsumen: The ubiquitous presence of electronics in our daily lives owes a debt to iron alloy powders. They are used in a wide range of components, from gears and bearings in miniature motors to electromagnetic components.
- Advantage: The high precision achievable with powder metallurgy using iron alloy powders allows for the creation of intricate and miniaturized components essential for modern electronics.
- Disadvantage: Certain electronic components might require specific properties like high electrical conductivity, which might be better achieved with alternative materials like copper or aluminum.
- Peralatan Medis: The world of medical devices relies heavily on the biocompatibility and corrosion resistance offered by certain iron alloy powders. They are used in implants like joint replacements and surgical instruments.
- Advantage: Specific stainless steel iron alloy powders offer excellent biocompatibility, minimizing the risk of rejection by the human body.
- Disadvantage: Strict regulations and biocompatibility testing are crucial for iron alloy powders used in medical devices.
- Alat Pemotong: The quest for ever-sharper and more durable cutting tools is where iron alloy powders truly excel. High-carbon and tool steel powders are used to create drill bits, milling cutters, and other cutting tools.
- Advantage: The ability to control the microstructure of iron alloy powders during the manufacturing process allows for the creation of exceptionally hard and wear-resistant cutting tools.
- Disadvantage: The cost of high-performance tool steel powders can be higher compared to some conventional tool steels.
These are just a few examples of the vast potential of iron alloy powders. Their versatility extends to countless other applications, making them a cornerstone of modern manufacturing.
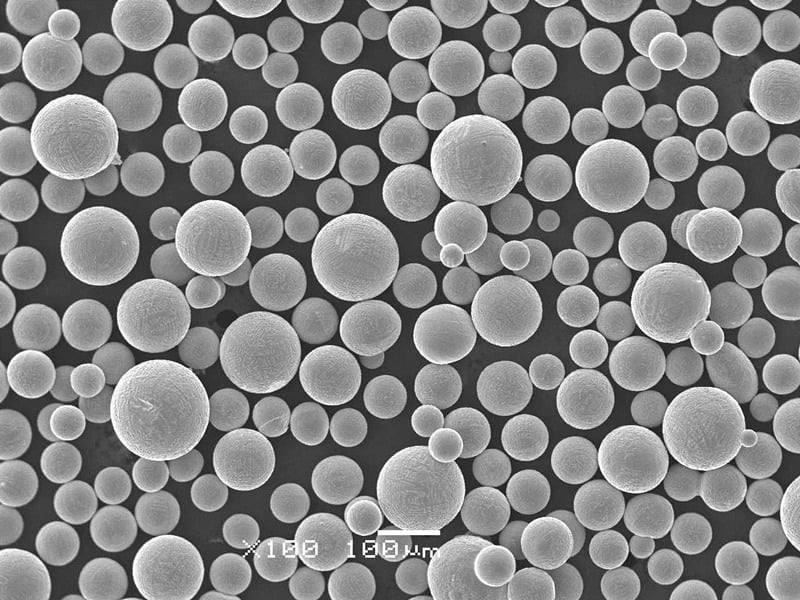
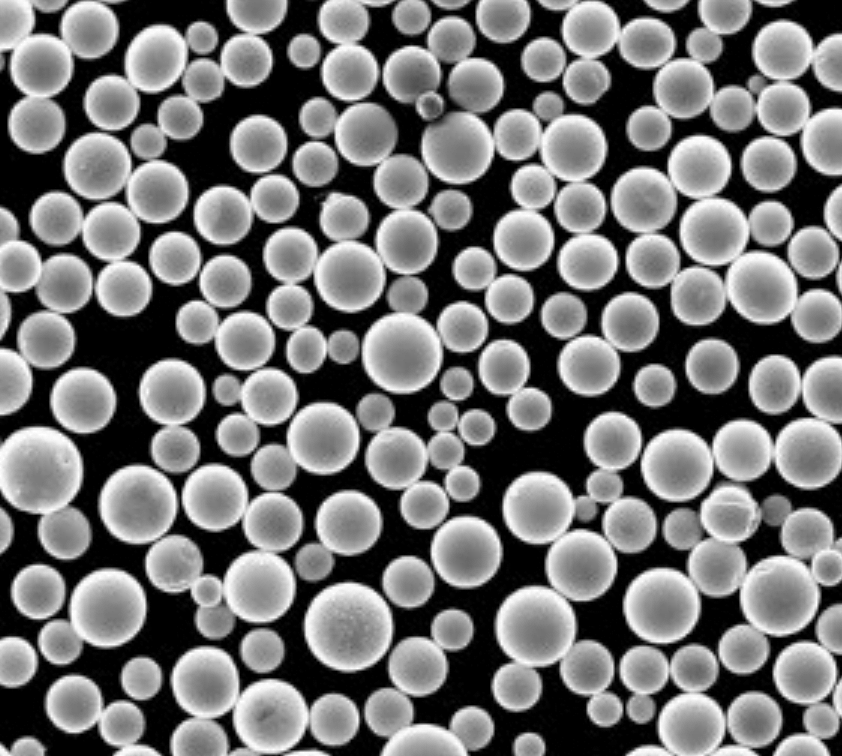
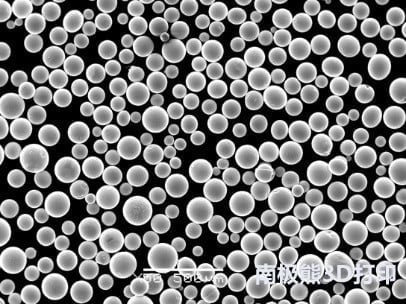
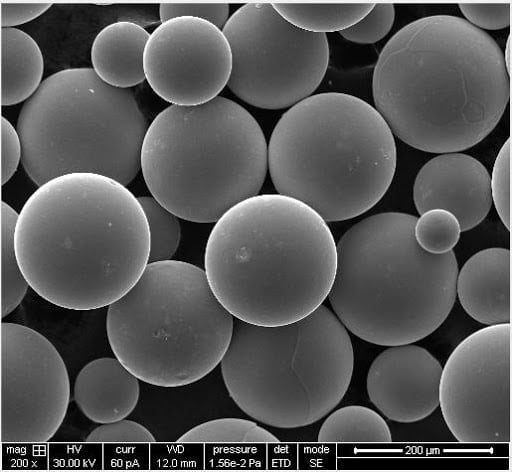
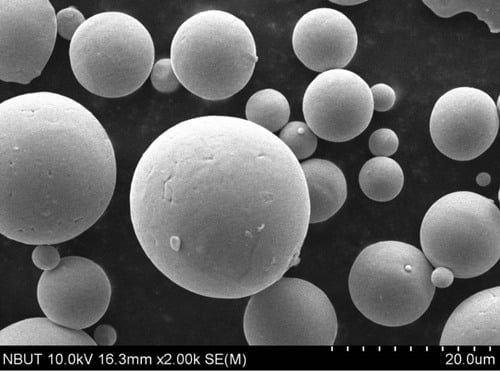
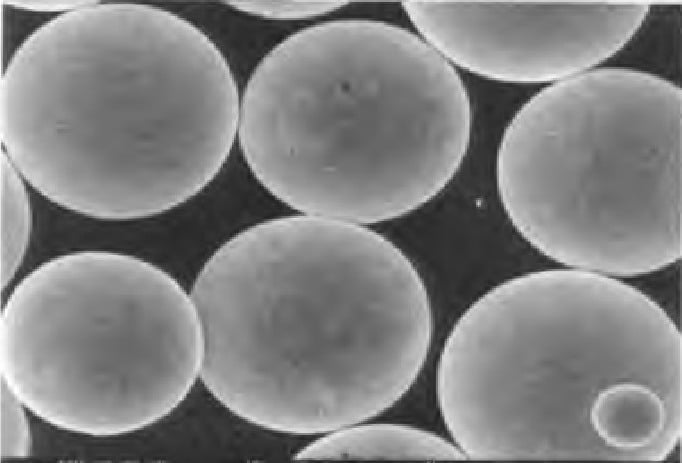
Spesifikasi, Ukuran, Kelas, dan Standar
Iron alloy powders come in a variety of specifications, sizes, grades, and adhere to different standards depending on their intended application. Here’s a breakdown to help you navigate this world:
Property | Deskripsi | Contoh |
---|---|---|
Ukuran partikel | The size of individual powder particles, measured in microns (µm). | Fine powders (<25 µm) for high density components, coarser powders (>100 µm) for filters. |
Kepadatan Semu | The bulk density of the powder, measured in grams per cubic centimeter (g/cm³). | Varies depending on particle size and shape, typically between 2-7 g/cm³. |
Aliran | The ease with which the powder flows. | Affects handling and processing. Improved flowability is desired for efficient production. |
Komposisi Kimia | The specific percentages of various elements present in the alloy. | Precise control ensures desired properties. Example: 316L stainless steel powder with specific Cr and Ni content for optimal corrosion resistance. |
Standar: Iron alloy powders adhere to various industry standards set by organizations like the Metal Powder Industries Federation (MPIF) and the American Society for Testing and Materials (ASTM). These standards define specific requirements for chemical composition, particle size distribution, and other properties to ensure consistent performance.
Size and Grade Considerations: The choice of particle size and grade depends on the desired application. For instance, finer powders are preferred for creating high-density components through powder metallurgy, while coarser powders might be suitable for applications like additive manufacturing. Similarly, the specific grade of iron alloy powder, such as a low-alloy steel or a high-nickel steel, will be chosen based on the required mechanical properties like strength, wear resistance, or corrosion resistance.
the Pros and Cons of Iron Alloy Powders
Iron alloy powders, like any material, come with their own set of advantages and disadvantages. Here’s a closer look to help you decide if they are the right fit for your application:
Keuntungan:
- Manufaktur Bentuk Hampir Bersih: Iron alloy powders allow for the creation of components with minimal material waste. This translates to cost savings, reduced environmental impact, and faster production times compared to traditional machining methods.
- Fleksibilitas Desain: The ability to create complex geometries through powder metallurgy opens doors for innovative designs that might be difficult or impossible to achieve with conventional manufacturing techniques.
- Keserbagunaan Material: The vast array of iron alloy powder compositions allows for tailoring properties to meet specific application needs. From high strength and wear resistance to exceptional corrosion resistance, there’s an iron alloy powder for nearly every requirement.
- Potensi Produksi Massal: Powder metallurgy processes using iron alloy powders are well-suited for high-volume production, ensuring consistency and repeatability in the manufactured components.
- Efisiensi Material: Iron alloy powders can be recycled and reused, minimizing waste and promoting sustainable manufacturing practices.
Kekurangan:
- Biaya Material: Certain high-performance iron alloy powders can be more expensive compared to some bulk metals. However, the near-net-shape manufacturing advantage and reduced waste can offset this cost in some applications.
- Process Limitations: Powder metallurgy processes might not be suitable for all component sizes or geometries. Very large or complex components might be better suited for traditional techniques like casting or forging.
- Persyaratan Pasca-Pemrosesan: Depending on the desired properties, iron alloy powders might require additional post-processing steps like sintering or heat treatment, adding to the overall production time and cost.
- Anisotropy: The directional nature of the powder compaction process can lead to anisotropic properties in the final component, meaning the mechanical properties might vary depending on the direction of testing.
Membuat Keputusan yang Tepat:
Understanding these advantages and disadvantages is crucial for making informed decisions about incorporating iron alloy powders into your manufacturing process. Consider the specific requirements of your application, such as the desired shape, material properties, production volume, and cost constraints. Weighing the pros and cons alongside alternative materials and manufacturing techniques will help you determine if iron alloy powders are the ideal choice for your project.
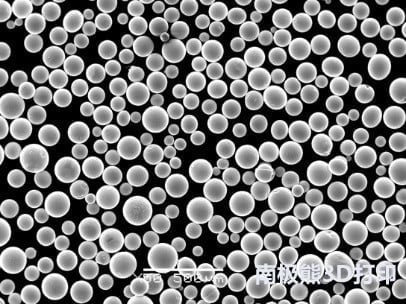
Pertanyaan yang Sering Diajukan (FAQ)
Here are some frequently asked questions (FAQs) about iron alloy powders to provide further insights:
Q: What are the different methods for producing iron alloy powders?
A: There are several methods for producing iron alloy powders, including:
- Atomisasi Air: Molten metal is dispersed into a stream of high-pressure water, creating rapidly solidified spherical particles.
- Atomisasi Gas: Molten metal is atomized using an inert gas like nitrogen or argon, resulting in finer and more uniform powder particles compared to water atomization.
- Electrolytic Atomization: An electric current is used to break down the molten metal into fine particles, offering good control over particle size and morphology.
Q: How are iron alloy powders stored and handled?
A: Iron alloy powders are typically hygroscopic, meaning they readily absorb moisture from the environment. Therefore, they need to be stored in dry conditions, often with sealed containers or desiccants, to prevent moisture absorption and oxidation. Special handling procedures might be required depending on the specific powder composition to ensure safety and prevent contamination.
Q: Are there any safety hazards associated with iron alloy powders?
A: Iron alloy powders can pose some safety hazards, such as inhalation risks during handling and processing. Proper ventilation and personal protective equipment (PPE) are essential to minimize exposure. Additionally, some iron alloy powders might contain elements with specific safety considerations, requiring adherence to appropriate safety data sheets (SDS).
Q: What are the future trends in iron alloy powder technology?
A: The future of iron alloy powders is bright. There’s ongoing research and development in areas like:
- Development of new alloy compositions: Tailoring iron alloy powders with even more specific properties for demanding applications.
- Additive manufacturing advancements: Utilizing iron alloy powders in additive manufacturing techniques like 3D printing for even greater design freedom and customization.
- Sustainability improvements: Developing more efficient and environmentally friendly processes for iron alloy powder production.
By addressing these aspects, iron alloy powders are poised to play an even more significant role in shaping the future of metal manufacturing.
Tentang LOGAM 3DP
Kategori Produk
HUBUNGI KAMI
Ada pertanyaan? Kirim pesan sekarang! Setelah menerima pesan Anda, kami akan memproses permintaan Anda bersama seluruh tim.