Imagine a 3D printer that bypasses the mess of powders and the intense heat of lasers. Instead, it uses droplets of molten metal, fired with pinpoint precision, to build complex objects layer by layer. This isn’t science fiction; it’s the innovative world of Pengaliran Logam Cair (LMJ), an additive manufacturing (AM) technique poised to revolutionize metal fabrication.
But how exactly does LMJ work? What are its advantages and limitations? And where is this technology headed? Buckle up, because we’re diving deep into the fascinating world of LMJ!
How Does Liquid Metal Jetting Work?
Think of LMJ as a high-tech inkjet printer for metals. Here’s a breakdown of the process:
- Melted Metal on Demand: The core of LMJ is a reservoir containing a metal alloy heated to its liquid state. This molten metal is the “ink” that will build the 3D object.
- Precise Delivery System: A specialized print head houses a tiny nozzle that precisely controls the flow of molten metal. Imagine this nozzle as a microscopic conductor’s baton, directing the metal droplets with incredible accuracy.
- Droplet Dance: Using piezoelectric actuators (think tiny electric buzzers), the print head generates pressure pulses, ejecting minuscule droplets of molten metal at high speeds. These droplets travel through a jet stream towards the build platform.
- Membangun Blok demi Blok: As the metal droplets hit the build platform, they rapidly cool and solidify, bonding with each other and the previous layer. This process continues layer by layer, meticulously building the desired 3D object.
- Shaping Up: The print head strategically deposits the droplets based on a digital design file. This allows for the creation of intricate geometries and internal features that would be difficult, if not impossible, with traditional manufacturing methods.
LMJ is a marvel of engineering, offering a unique approach to metal 3D printing. But what makes it stand out from the crowd?
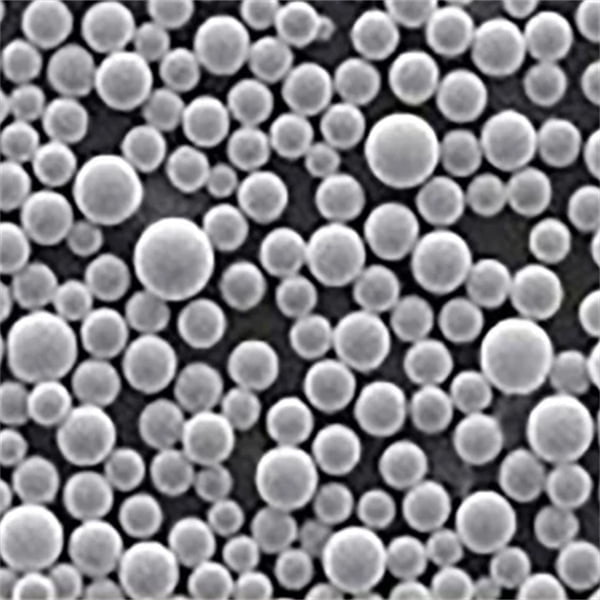
Keuntungan dari Pengaliran Logam Cair (LMJ)
LMJ boasts several advantages that make it a game-changer in the world of metal AM:
- Superior Resolution: Since LMJ works with tiny droplets, it can achieve exceptional resolution compared to powder-based methods. This allows for the creation of highly detailed features and smooth surface finishes, making it ideal for applications like microfluidics and heat exchangers.
- Efisiensi Material: Unlike powder-based AM, LMJ utilizes nearly 100% of the metal feedstock. There’s minimal waste, making it a more sustainable and cost-effective option in the long run.
- Reduced Processing: LMJ parts often require minimal post-processing compared to powder-based methods. This translates to faster turnaround times and lower overall production costs.
- Broader Material Palette: LMJ can work with a wider range of metals and alloys compared to laser-based techniques. This opens doors for applications requiring specific material properties like high strength, heat resistance, or biocompatibility.
- Safety First: Since LMJ eliminates the need for metal powders, it minimizes the risk of inhalation and explosion hazards associated with powder handling. This creates a safer work environment for operators.
LMJ sounds like a dream come true, but are there any limitations to consider?
Limitations of Liquid Metal Jetting (LMJ)
While LMJ offers a compelling set of advantages, it’s important to acknowledge its current limitations:
- Membangun Kecepatan: Compared to powder-bed fusion methods, LMJ can be slower, especially for larger parts. This is because each layer is meticulously built with tiny droplets.
- Properti Material: While the material palette is expanding, LMJ may not yet support all the exotic alloys used in traditional metalworking.
- Technology Maturation: LMJ is a relatively new technology compared to other AM techniques. This means the technology and equipment are still under development, potentially leading to higher upfront costs.
Despite these limitations, LMJ is rapidly evolving, and its potential applications are vast.
The Application of Pengaliran Logam Cair (LMJ)
LMJ’s unique capabilities make it suitable for a diverse range of industries, including:
- Kedirgantaraan & Pertahanan: The high strength-to-weight ratio and design freedom of LMJ make it ideal for lightweight aircraft components, heat exchangers in rockets, and even custom. LMJ could revolutionize the production of custom defense equipment like heat sinks for electronics in harsh environments.
- Otomotif: LMJ can be used to create lightweight and complex internal engine components, leading to increased fuel efficiency and performance. Imagine intricate cooling channels or high-precision pistons crafted with LMJ!
- Peralatan Medis: The biocompatibility of certain LMJ alloys makes them suitable for creating customized prosthetic limbs, dental implants, and even microfluidic devices used in medical diagnostics.
- Elektronik: The ability to print intricate features with high conductivity makes LMJ ideal for producing miniaturized electronic components like heat sinks for high-performance chips or waveguides for advanced optical systems.
- Barang Konsumsi: The potential for LMJ extends beyond industrial applications. Imagine customized jewelry printed with LMJ, or high-performance heat spreaders for your gaming laptop!
The possibilities with LMJ are truly exciting. But what does the future hold for this innovative technology?
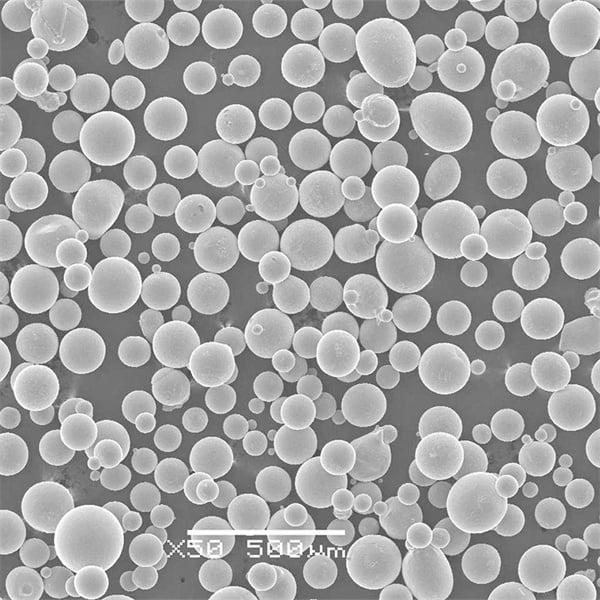
Future Development of Pengaliran Logam Cair (LMJ)
LMJ is still in its early stages of development, but significant advancements are happening:
- Faster Build Speeds: Researchers are working on improving droplet generation and deposition techniques to increase printing speeds. This will make LMJ more competitive for larger-scale production.
- Material Expansion: The range of printable alloys is constantly expanding. This will unlock new applications and broader adoption of LMJ across various industries.
- Pengurangan Biaya: As the technology matures, LMJ equipment is expected to become more affordable, making it accessible to a wider range of manufacturers.
- Pencetakan Multi-Material: The future might see LMJ capable of printing objects using multiple metals within a single build. This would allow for the creation of parts with graded properties or combined functionalities.
With continued research and development, LMJ has the potential to become a mainstream metal AM technology, transforming how we design and manufacture complex metal parts.
FAQ
Q: How does LMJ compare to other metal 3D printing methods?
A: LMJ offers several advantages over other methods:
- Compared to powder-bed fusion: LMJ boasts superior resolution, minimal waste, and a wider material palette. However, it can be slower for large parts.
- Compared to directed energy deposition (DED): LMJ offers better resolution and potentially safer operation due to the absence of metal powders. DED, however, might be faster for large-scale depositions.
Q: What are the typical materials used in LMJ?
A: Common LMJ materials include aluminum, stainless steel, titanium, and nickel alloys. The range of printable materials is constantly expanding.
Q: What are the size limitations of LMJ printed parts?
A: Current LMJ systems can print parts ranging from millimeters to a few hundred millimeters in size. The maximum build size is expected to increase as technology develops.
Q: Is LMJ a suitable option for mass production?
A: While LMJ isn’t there yet, advancements in build speed and affordability could make it a viable option for mass production in the future, particularly for high-value, complex metal components.
Q: Where can I learn more about LMJ?
A: Several resources offer in-depth information about LMJ, including research papers, industry publications, and websites of LMJ technology developers and machine manufacturers.
Tentang LOGAM 3DP
Kategori Produk
HUBUNGI KAMI
Ada pertanyaan? Kirim pesan sekarang! Setelah menerima pesan Anda, kami akan memproses permintaan Anda bersama seluruh tim.