Imagine crafting complex metal parts with laser precision, layer by layer, building intricate designs that were once impossible. This isn’t science fiction; it’s the reality of Selective Laser Melting (Halo), a revolutionary 3D printing technology that’s transforming the way we manufacture metal components.
SLM, also known as Direct Metal Laser Sintering, opens a treasure trove of possibilities for designers, engineers, and manufacturers alike. But before we delve into its applications and benefits, let’s unpack the core concept.
What is SLM?
Think of SLM as a sophisticated 3D printer for metals. A high-powered laser beam acts as the sculptor, meticulously melting a bed of fine metal powder according to a pre-designed digital blueprint. Layer by layer, the laser fuses the powder particles together, solidifying the desired shape. This intricate dance continues until the entire 3D object is complete.
Here’s a breakdown of the magic behind SLM:
- Persiapan Serbuk: The journey begins with a bed of meticulously crafted metal powder. These powders boast exceptional flowability and particle size distribution for optimal laser interaction during the printing process.
- Peleburan Laser: With laser precision, the machine melts specific areas of the powder bed, fusing the particles together based on the digital design.
- Lapis demi lapis: A new layer of powder is deposited, and the laser continues its dance, meticulously building the object one layer at a time.
- Penghapusan Dukungan: Once the printing process is complete, the finished part is removed from the build chamber. Support structures, essential for complex geometries, may need to be removed using specialized techniques.
- Pemrosesan Lanjutan: Depending on the application and desired finish, the final part might undergo additional processes like heat treatment or surface finishing.
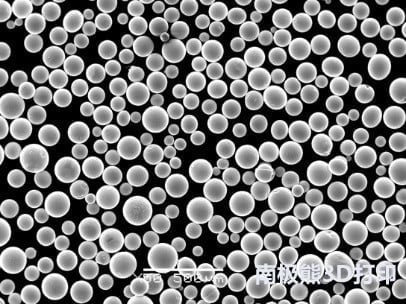
Choosing the Right Tool for the Job
Just like an artist needs the perfect brush for their masterpiece, SLM relies on a diverse range of metal powders to create exceptional parts. Here are some of the most commonly used metal powders in SLM, each with its unique properties:
Bubuk Logam | Komposisi | Properti | APLIKASI |
---|---|---|---|
Baja Tahan Karat 316L | Fe (basa), 16-18% Cr, 10-14% Ni, 2-3% Mo | Ketahanan korosi yang sangat baik, kekuatan tinggi, biokompatibel | Komponen kedirgantaraan, implan medis, peralatan pemrosesan bahan kimia |
Baja Tahan Karat 17-4 PH | Fe (base), 16-18% Cr, 3-5% Ni, 4 Cu | High strength, good corrosion resistance, age-hardenable | Gears, shafts, molds, fasteners |
Inconel 625 | Ni (base), 20-25% Cr, 9% Fe, 5% Mo | Exceptional high-temperature strength, excellent corrosion resistance | Gas turbine components, rocket engines, heat exchangers |
Titanium 6Al-4V (Ti64) | Ti (dasar), 6% Al, 4% V | High strength-to-weight ratio, good biocompatibility | Aircraft components, orthopedic implants, sporting goods |
Aluminium AlSi10Mg | Al (base), 10-13% Si, 0.3-0.6% Mg | Ringan, kemampuan cor yang baik, rasio kekuatan-terhadap-berat yang tinggi | Automotive parts, aerospace components, heat sinks |
Tembaga Cu | 100% Cu | Konduktivitas termal dan kelistrikan yang sangat baik | Heat exchangers, electrical components, waveguides |
Nikel Ni | 100% Ni | Ketahanan korosi yang tinggi, keuletan yang baik | Chemical processing equipment, electronics components, electrodes |
Cobalt-Chrome CoCr | Co (base), 20-30% Cr | Ketahanan aus yang tinggi, biokompatibel | Dental implants, orthopedic implants, cutting tools |
Baja Perkakas | Varies depending on type | Kekerasan tinggi, ketahanan aus | Molding tools, cutting tools, dies |
Inconel 718 | Ni (base), 17-21% Cr, 5-9% Fe, ~Nb + Ta | Excellent high-temperature strength, good corrosion resistance | Aerospace components, turbine blades, nuclear reactors |
This list represents just a glimpse into the vast array of metal powders available for SLM. With continuous advancements in materials science, we can expect even more specialized powders to emerge, pushing the boundaries of what’s possible.
Aplikasi dari Halo Across Industries
SLM’s ability to create complex geometries with high precision opens doors to a wide range of applications. Here are some prominent examples of how this revolutionary technology is transforming various industries:
1. Aerospace & Defense:
- Meringankan beban: SLM allows for the creation of intricate, lightweight components for aircraft, reducing fuel consumption and increasing flight range. Imagine intricate lattice structures within wings or control surfaces, impossible with traditional manufacturing, yet achievable with SLM.
- Suku Cadang Berkinerja Tinggi: Jet engines and other critical components require materials that can withstand extreme temperatures and stresses. SLM enables the creation of parts from high-performance alloys like Inconel 625, offering exceptional strength and heat resistance.
- Kustomisasi: SLM empowers the creation of customized components for specific applications, like personalized flight control systems or custom-designed rocket engine parts.
2. Automotive:
- Performance Parts: SLM is making its mark in the high-performance automotive sector. Think of lightweight yet strong components like pistons or intricate cooling systems for racing engines, pushing the boundaries of performance.
- Prototyping & Design Freedom: The ability to rapidly iterate on designs with SLM allows car manufacturers to bring innovative concepts to life quickly. Imagine testing intricate designs for new fuel injection systems or complex aerodynamic components before committing to mass production.
- Meringankan beban: Similar to the aerospace industry, SLM allows for the creation of lightweight car parts, improving fuel efficiency and overall vehicle performance.
3. Medical & Dental:
- Customized Implants: SLM is revolutionizing the field of prosthetics and implants. Surgeons can now create customized implants that perfectly match a patient’s anatomy, leading to faster recovery times and improved patient outcomes.
- Biocompatible Materials: Certain metal powders used in SLM, like Titanium 6Al-4V (Ti64), are biocompatible, meaning they can be safely implanted in the human body. This opens doors for the creation of life-changing implants like hip replacements or dental implants.
- Complex Designs: SLM enables the creation of intricate medical devices with complex geometries, like intricate lattice structures in prosthetics that mimic natural bone growth or porous structures in implants that promote bone ingrowth.
4. Consumer Goods:
- Customization & Design Freedom: SLM allows for the creation of personalized consumer goods, like custom-designed jewelry or intricate watch components. Imagine creating a unique ring with a complex design or a personalized sports watch with lightweight, high-strength components.
- Limited-Edition Products: SLM’s ability to produce small batches efficiently opens doors for the creation of limited-edition consumer goods, adding a touch of exclusivity and collectability.
- Functional Components: SLM isn’t just about aesthetics; it can also create functional components for consumer products. Think of lightweight, high-performance heat sinks for laptops or intricate components for high-end bicycles.
These are just a few examples of how SLM is transforming various industries. As the technology matures and the cost becomes more accessible, we can expect even more innovative applications to emerge, blurring the lines between imagination and reality.
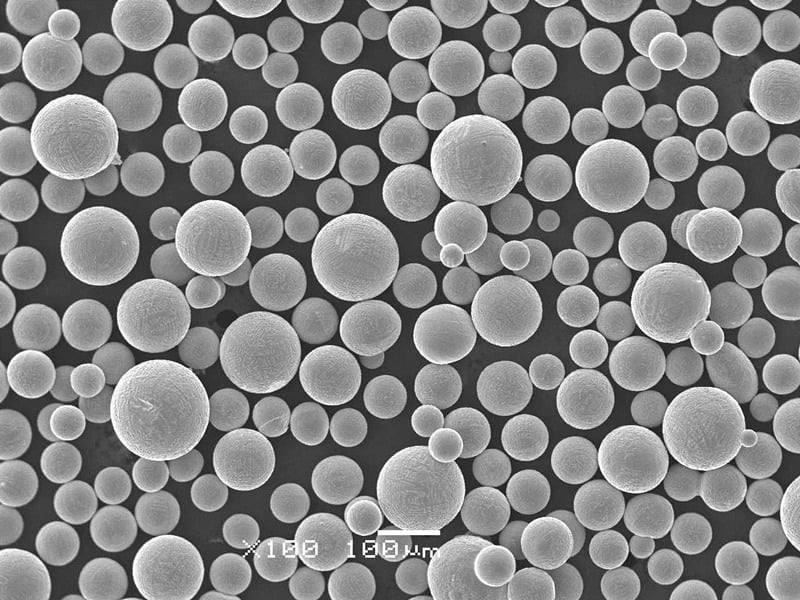
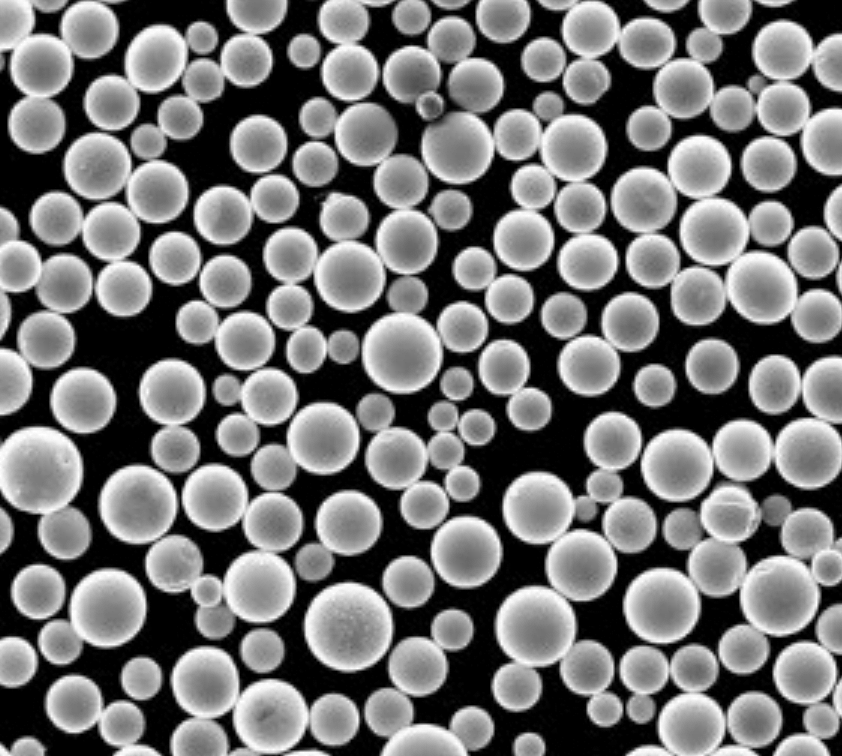
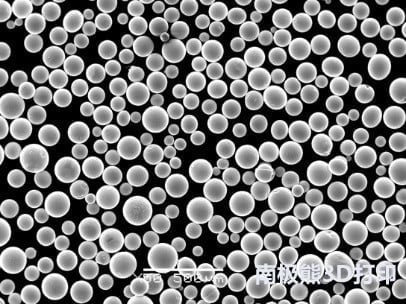
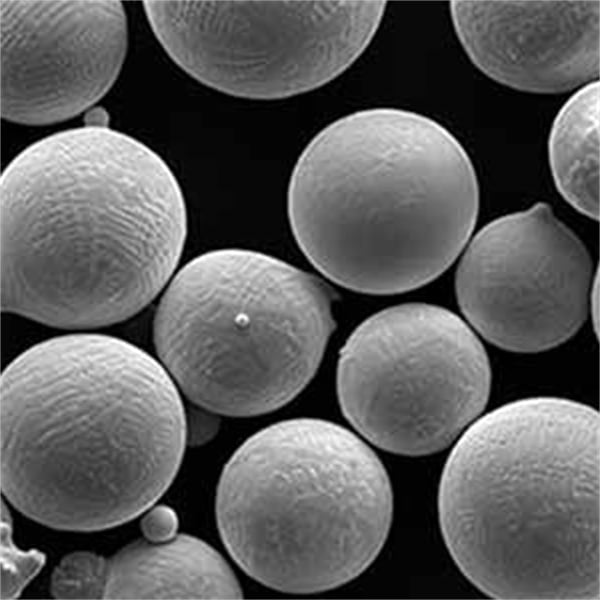
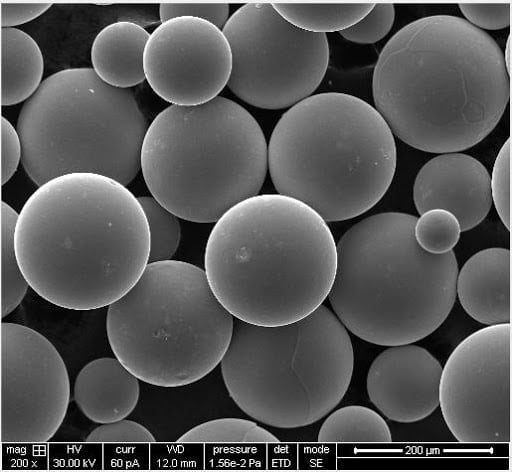
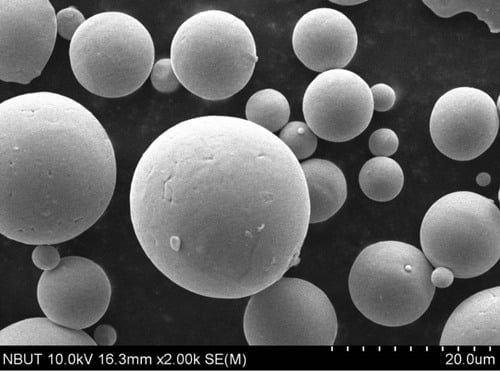
Keuntungan dari Halo
SLM offers a plethora of advantages over traditional metal manufacturing techniques like casting, machining, and forging. Here’s a closer look:
- Kebebasan Desain: SLM allows for the creation of complex geometries that are simply impossible with traditional methods. Think of intricate internal channels within a part or lattice structures for lightweighting, pushing the boundaries of design possibilities.
- Meringankan beban: By creating parts with intricate structures, SLM enables the creation of lightweight components while maintaining high strength. This is particularly beneficial in industries like aerospace and automotive, where weight reduction is paramount.
- Pembuatan Prototipe Cepat: Compared to traditional methods, SLM allows for the rapid creation of prototypes, accelerating the design and development process. This allows for faster iteration and quicker time-to-market for new products.
- Mengurangi Limbah: Traditional manufacturing techniques often generate significant waste material. SLM, on the other hand, utilizes a powder-based approach, minimizing material waste and promoting a more sustainable production process.
- Kustomisasi Massal: SLM’s ability to produce small batches efficiently opens doors for mass customization, allowing for the creation of personalized products or components tailored to specific needs.
Limitations and Challenges of SLM
While SLM offers a compelling array of benefits, it’s important to acknowledge the limitations and challenges associated with this technology:
- Biaya: Currently, SLM machines and metal powders can be expensive compared to traditional manufacturing methods. This can be a barrier to entry for smaller companies or for applications where cost is a major concern.
- Permukaan akhir: SLM-produced parts can have a rough surface finish compared to traditionally machined parts. While post-processing techniques can improve the surface finish, it can add to the overall production cost.
- Batasan Ukuran Bangunan: The build size of SLM machines is currently limited compared to some traditional techniques. This can restrict the creation of very large metal parts.
- Properti Material: The properties of SLM-produced parts can differ slightly from traditionally manufactured parts due to the unique solidification process involved. Extensive testing and qualification may be required for critical applications.
- Struktur Pendukung: Creating complex geometries with SLM often requires the use of support structures. These supports need to be removed after printing, which can be a time-consuming and potentially delicate process.
- Pemilihan Material yang terbatas: While the range of metal powders available for SLM is growing, it’s still not as vast as the materials that can be processed using traditional methods.
Choosing Between SLM and Traditional Techniques
The decision to use SLM or a traditional manufacturing technique depends on several factors, including:
- Kompleksitas bagian: If the part requires a complex geometry that’s difficult or impossible to achieve with traditional methods, then SLM might be the better choice.
- Volume produksi: For high-volume production runs, traditional methods might still be more cost-effective. SLM shines in low-volume or customized production scenarios.
- Sifat material: Consider the required properties of the final part. If the application demands specific mechanical properties that might be affected by the SLM process, traditional techniques might be preferred.
- Biaya: While SLM offers several advantages, the cost of the machines, materials, and post-processing needs to be factored into the equation.
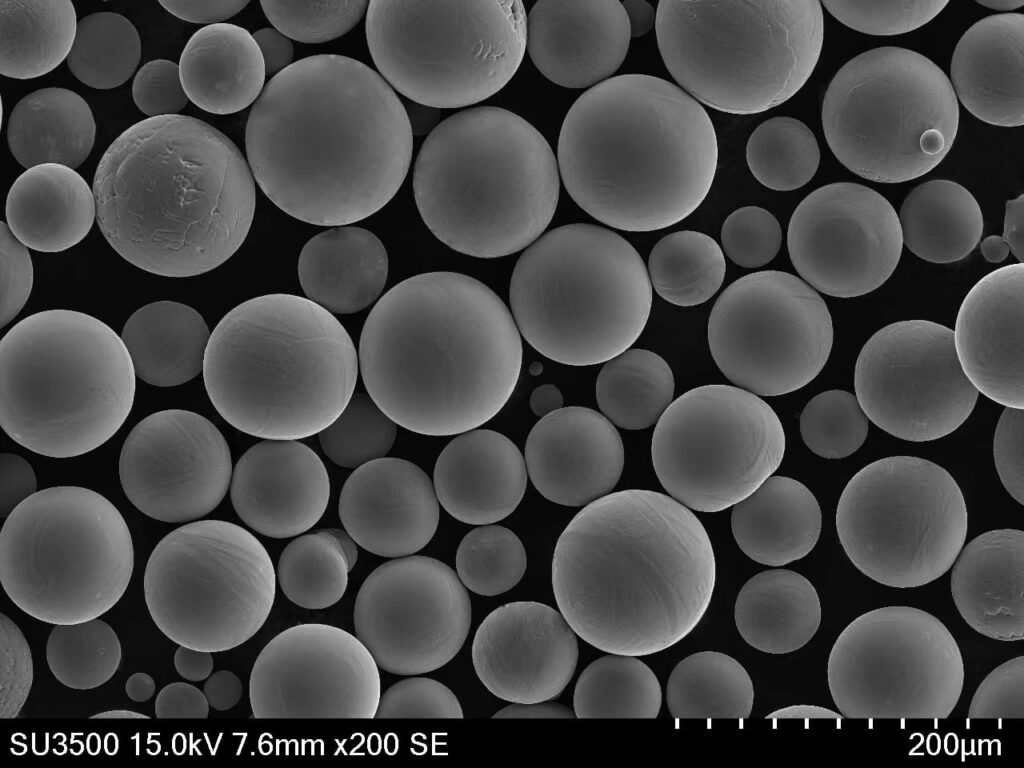
The Future of SLM and Metal 3D Printing
SLM is a rapidly evolving technology with immense potential to revolutionize metal manufacturing. Here’s a glimpse into what the future holds:
- Mengurangi Biaya: As the technology matures and adoption increases, we can expect the cost of SLM machines and metal powders to decrease, making it more accessible to a wider range of applications.
- Material Tingkat Lanjut: Pengembangan serbuk logam yang baru dan lebih baik dengan sifat yang disempurnakan akan semakin memperluas kemampuan SLM. Bayangkan material dengan rasio kekuatan-terhadap-berat yang lebih baik atau performa suhu tinggi yang unggul.
- Ukuran Bangunan yang Lebih Besar: Kemajuan dalam teknologi mesin diharapkan akan mengarah pada pengembangan mesin SLM dengan volume rakitan yang lebih besar, sehingga memungkinkan pembuatan komponen logam yang lebih besar dan lebih kompleks.
- Integrasi dengan Teknologi Lain: Di masa depan, SLM mungkin akan diintegrasikan dengan teknologi manufaktur aditif lainnya, seperti pencetakan multi-bahan, untuk menciptakan komponen logam yang lebih fungsional dan kompleks.
- Keberlanjutan: Seiring dengan meningkatnya kekhawatiran tentang konsumsi sumber daya dan dampak lingkungan, HaloKemampuannya untuk meminimalkan limbah material dan memungkinkan produksi sesuai permintaan memposisikannya sebagai solusi manufaktur logam yang lebih berkelanjutan.
FAQ
T: Apa saja manfaat SLM dibandingkan teknik manufaktur logam tradisional?
J: SLM menawarkan beberapa keuntungan, termasuk kebebasan desain, bobot yang ringan, pembuatan prototipe yang cepat, mengurangi limbah, dan kustomisasi massal.
T: Apa saja keterbatasan SLM?
J: Keterbatasan saat ini termasuk biaya tinggi, potensi tantangan penyelesaian permukaan, keterbatasan ukuran bangunan, pertimbangan seputar sifat material, struktur pendukung, dan pemilihan material yang terbatas dibandingkan dengan metode tradisional.
T: Kapan SLM merupakan pilihan yang tepat untuk aplikasi tertentu?
J: Memilih antara SLM dan teknik tradisional bergantung pada faktor-faktor seperti kompleksitas komponen, volume produksi, sifat material yang diperlukan, dan pertimbangan biaya.
T: Bagaimana masa depan SLM di masa depan?
J: Masa depan cerah untuk SLM, dengan kemajuan yang diantisipasi dalam pengurangan biaya, pengembangan material, ukuran rakitan yang lebih besar, integrasi dengan teknologi lain, dan fokus yang semakin besar pada keberlanjutan.
Tentang LOGAM 3DP
Kategori Produk
HUBUNGI KAMI
Ada pertanyaan? Kirim pesan sekarang! Setelah menerima pesan Anda, kami akan memproses permintaan Anda bersama seluruh tim.