Overview of Inconel 718
Inconel 718 is a superalloy renowned for its exceptional performance in high-stress, high-temperature environments. It’s a nickel-chromium alloy that’s designed to withstand extreme conditions, making it invaluable in industries like aerospace, oil and gas, and power generation. With its outstanding resistance to corrosion and oxidation, Inconel 718 is a top choice for critical applications.
But what makes Inconel 718 so special? Let’s dive deep into its composition, properties, and applications to understand why this material stands out in the world of high-performance alloys.
Key Details of Inconel 718:
- Composition: Nickel (50-55%), Chromium (17-21%), Iron (balance), plus Molybdenum, Columbium (Niobium), Titanium, and Aluminum.
- Properties: High tensile strength, creep resistance, and excellent weldability.
- Applications: Aerospace, nuclear reactors, gas turbines, and more.
- Characteristics: High fatigue resistance, excellent stress-corrosion cracking resistance, and good workability.
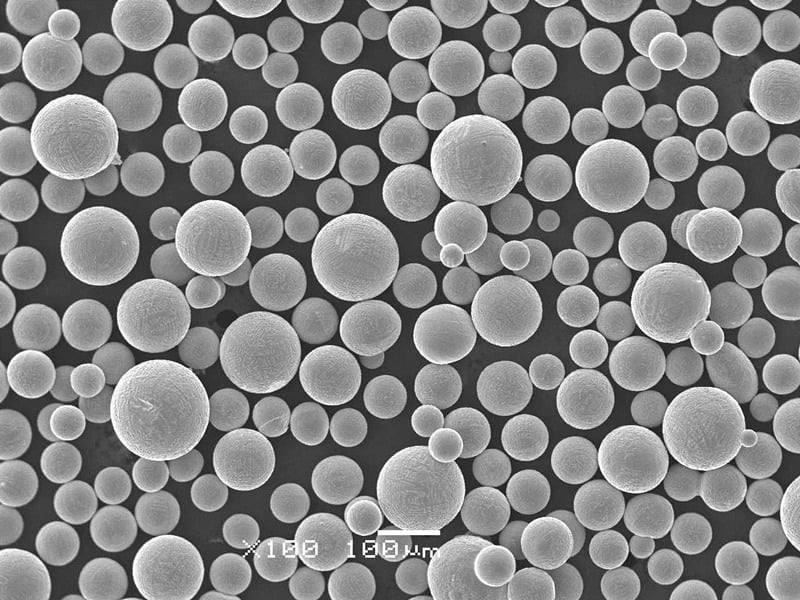
Composition of Inconel 718
Inconel 718’s remarkable properties stem from its unique composition. Here’s a detailed breakdown:
Element | Content (%) | Role |
---|---|---|
Nickel | 50-55 | Base metal, corrosion resistance |
Chromium | 17-21 | Oxidation resistance |
Iron | Balance | Structural stability |
Molybdenum | 2.8-3.3 | Strength and hardness |
Columbium (Niobium) | 4.75-5.5 | Strengthening |
Titanium | 0.65-1.15 | High-temperature strength |
Aluminum | 0.2-0.8 | Oxidation resistance |
Other elements | Minor amounts | Various enhancements |
Properties of Inconel 718
Property | Description |
---|---|
Tensile Strength | Up to 1,250 MPa (180,000 psi) |
Yield Strength | Approximately 1,030 MPa (150,000 psi) |
Creep Resistance | Excellent, maintains strength at high temperatures |
Hardness | High, typically around 330-370 HB |
Corrosion Resistance | Exceptional, especially in high-temperature environments |
Thermal Stability | Maintains properties at temperatures up to 700°C |
Weldability | Good, can be welded with standard techniques |
Applications of Inconel 718 Material
Inconel 718’s properties make it suitable for a wide range of demanding applications. Here are some key areas where this superalloy is utilized:
Industry | Application |
---|---|
Aerospace | Jet engines, rocket motors, and spacecraft |
Oil and Gas | Drilling equipment, valves, and pressure vessels |
Power Generation | Gas turbines, nuclear reactors |
Automotive | Turbocharger rotors, exhaust systems |
Chemical Processing | Heat exchangers, reactor cores |
Marine | Submarine components, offshore drilling rigs |
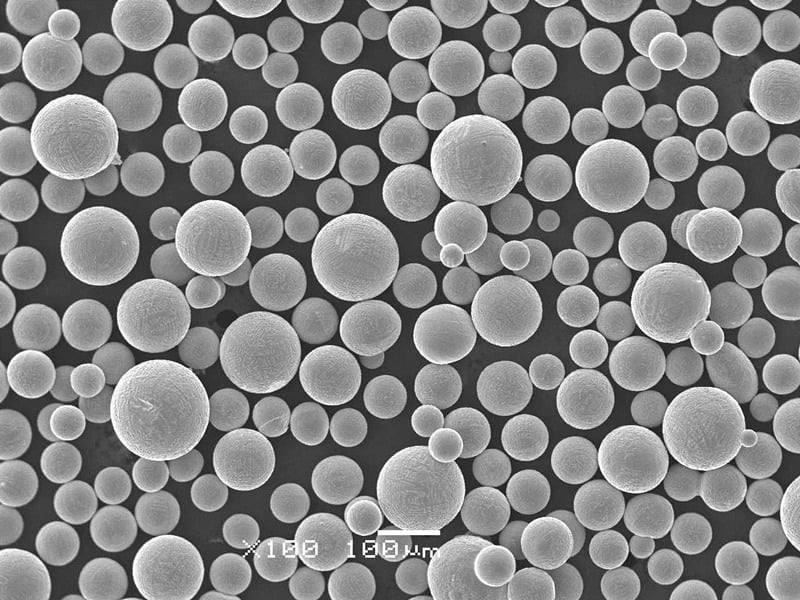
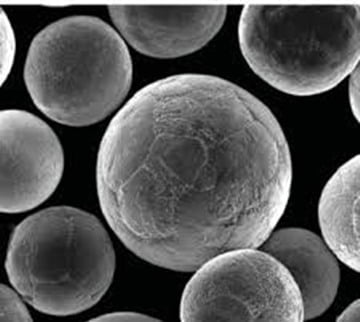
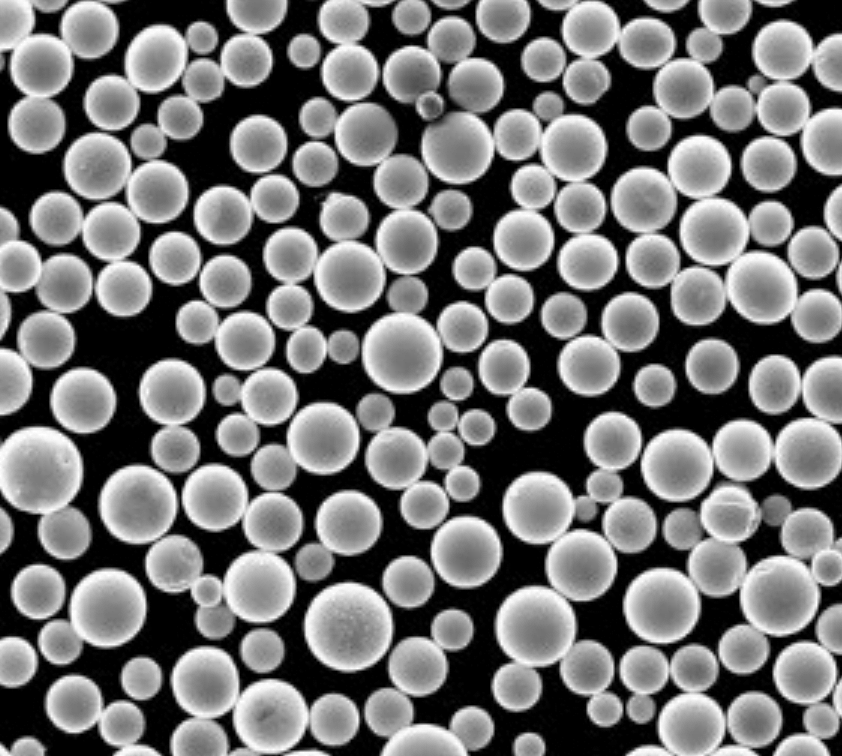
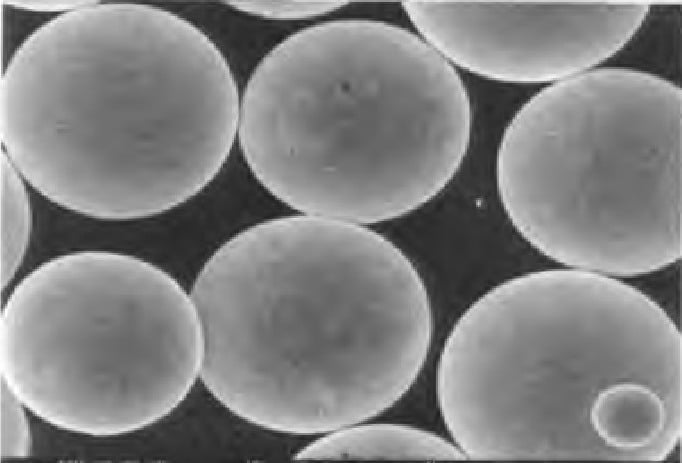
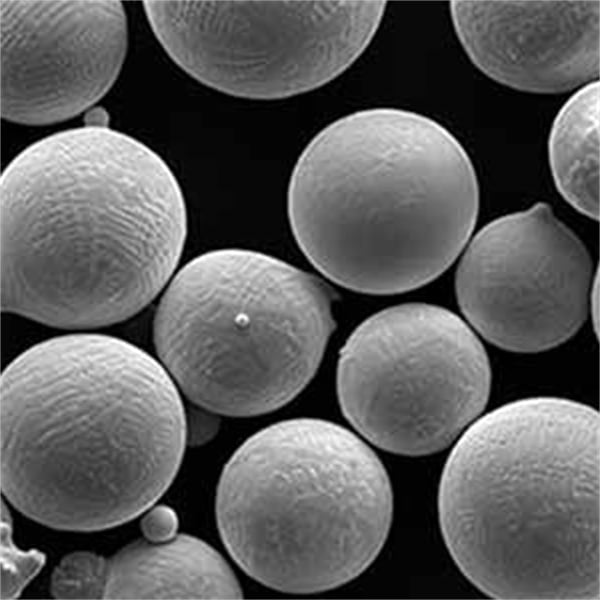
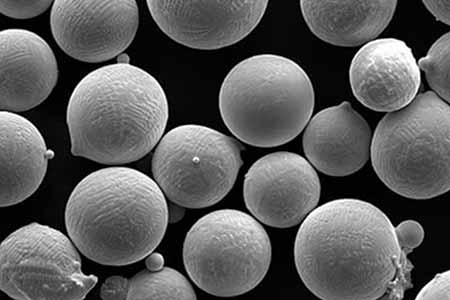
Specific Metal Powder Models of Inconel 718
Here’s a closer look at some specific metal powder models of Inconel 718, each tailored for different applications:
- Inconel 718 Plus: Enhanced version with improved tensile strength and creep resistance, ideal for high-temperature aerospace applications.
- Inconel 718 AQ: Designed for additive manufacturing with superior printability and material properties.
- Inconel 718 VIM/VAR: Produced through vacuum induction melting and vacuum arc remelting for applications requiring ultra-high purity.
- Inconel 718SPF: Super plastic forming grade for complex, high-strength parts.
- Inconel 718 Low Sulfur: Optimized for improved weldability and reduced risk of hot cracking.
- Inconel 718 Modified: Customized composition to enhance specific properties such as toughness or corrosion resistance.
- Inconel 718 DA: Direct aged version, offering high yield strength and hardness for specific industrial applications.
- Inconel 718 AM: Specifically developed for additive manufacturing processes like SLM and EBM.
- Inconel 718 HSC: High-strength, high-corrosion resistance variant for harsh environments.
- Inconel 718 HP: High-purity version for critical applications in the medical and aerospace sectors.
Advantages of Inconel 718 Material
Inconel 718 offers numerous advantages that make it a preferred choice in many industries:
- High Strength and Durability: With excellent tensile and yield strength, Inconel 718 maintains structural integrity under extreme stress.
- Corrosion and Oxidation Resistance: Resists corrosion in a wide range of environments, including high-temperature settings.
- Thermal Stability: Retains properties at elevated temperatures, essential for aerospace and power generation applications.
- Good Weldability: Can be welded without cracking, making it versatile for complex assemblies.
- Creep Resistance: Withstands long-term exposure to high temperatures and stress without deforming.
Disadvantages of Inconel 718 Material
Despite its many benefits, Inconel 718 also has some limitations:
- Cost: It is more expensive compared to other alloys, which can be a drawback for cost-sensitive projects.
- Machinability: While it is workable, machining Inconel 718 can be challenging and requires specialized equipment and techniques.
- Weight: Heavier than some alternative materials, which can be a disadvantage in weight-sensitive applications.
- Availability: Depending on the specific grade and form, availability might be limited, leading to longer lead times.
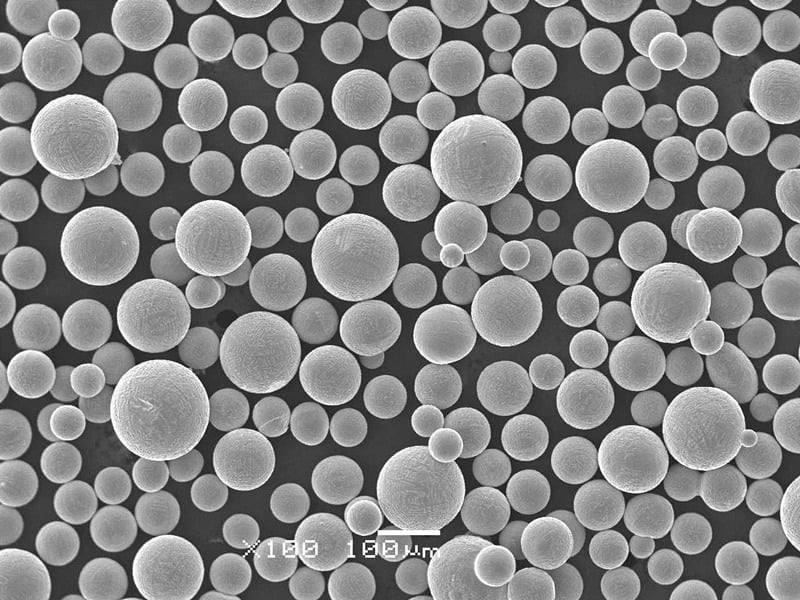
Comparison of Inconel 718 with Other Alloys
Property | Inconel 718 | Titanium Alloy (Ti-6Al-4V) | Stainless Steel (316L) |
---|---|---|---|
Tensile Strength | Up to 1,250 MPa | Up to 1,100 MPa | Up to 580 MPa |
Yield Strength | Approximately 1,030 MPa | Approximately 900 MPa | Approximately 290 MPa |
Corrosion Resistance | Excellent | Very good | Good |
Temperature Stability | Up to 700°C | Up to 400°C | Up to 870°C |
Weldability | Good | Moderate | Good |
Cost | High | High | Moderate |
Machinability | Moderate | Difficult | Easy |
Weight | Heavy | Light | Heavy |
Specifications, Sizes, Grades, and Standards
Inconel 718 is available in various specifications, sizes, and grades to suit different applications. Here’s a comprehensive overview:
Specifications and Standards
Standard | Description |
---|---|
ASTM B637 | Standard Specification for Precipitation-Hardening Nickel Alloy Bars, Forgings, and Forging Stock |
AMS 5662 | Aerospace Material Specification for Inconel 718 Bars, Forgings, and Rings |
AMS 5596 | Aerospace Material Specification for Inconel 718 Sheet, Strip, and Plate |
UNS N07718 | Unified Numbering System designation for Inconel 718 |
DIN 2.4668 | German Standard for Inconel 718 |
Sizes and Forms
Form | Sizes Available |
---|---|
Bar | 6 mm to 200 mm diameter |
Sheet/Plate | 0.25 mm to 100 mm thickness |
Wire | 0.1 mm to 10 mm diameter |
Tube | 1 mm to 100 mm diameter, various lengths |
Grades
Inconel 718 is available in different grades based on specific applications and processing methods:
Grade | Description |
---|---|
Standard Grade | General purpose, suitable for most applications |
High Purity | For critical applications requiring minimal impurities |
Additive Manufacturing Grade | Optimized for 3D printing and similar processes |
Direct Aged | Pre-aged for specific mechanical properties |
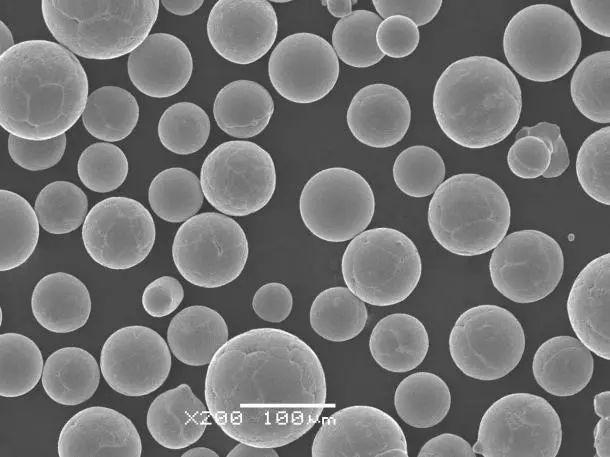
Suppliers and Pricing Details
Finding the right supplier is crucial for ensuring the quality and availability of Inconel 718. Here’s a list of some reputable suppliers and their pricing details:
Supplier | Location | Price Range (per kg) | Contact Details |
---|---|---|---|
Special Metals | USA | $40 – $60 | www.specialmetals.com |
ATI | USA | $45 – $65 | www.atimetals.com |
VDM Metals | Germany | $50 – $70 | www.vdm-metals.com |
Haynes International | USA | $42 – $68 | www.haynesintl.com |
ThyssenKrupp | Germany | $48 – $72 | www.thyssenkrupp.com |
Aperam | France | $47 – $69 | www.aperam.com |
Pros and Cons of Inconel 718
Understanding the advantages and limitations of Inconel 718 helps in making informed decisions for its use in various applications.
Advantages
- High Strength: Inconel 718 retains its strength under extreme conditions, which is critical for aerospace and industrial applications.
- Corrosion Resistance: The alloy’s resistance to corrosion and oxidation makes it suitable for harsh environments.
- Thermal Stability: Performs well at high temperatures, maintaining its mechanical properties.
- Weldability: Good weldability reduces complications during assembly.
Limitations
- Cost: Higher cost compared to other materials can be a drawback for budget-sensitive projects.
- Machinability: Requires specialized machining techniques, which can increase manufacturing time and costs.
- Weight: Heavier than some alternative materials, which might not be ideal for weight-sensitive applications.
Inconel 718 in Various Industries
Aerospace
Inconel 718 is a go-to material in the aerospace industry due to its high strength and ability to withstand extreme temperatures. It’s commonly used in jet engine components, turbine blades, and rocket motors. The alloy’s resistance to oxidation and thermal fatigue makes it ideal for these high-stress environments.
Oil and Gas
In the oil and gas sector, Inconel 718 is used for drilling equipment, wellhead components, and pressure vessels. Its excellent resistance to corrosion and high-temperature strength is crucial for equipment that operates in deep-sea and high-pressure conditions.
Power Generation
Gas turbines and nuclear reactors benefit from the use of Inconel 718 due to its ability to retain strength and resist oxidation at high temperatures. The alloy’s creep resistance is particularly valuable in these applications.
Automotive
Inconel 718 is used in high-performance automotive applications such as turbocharger rotors and exhaust systems. Its ability to withstand high temperatures and corrosive environments makes it a preferred choice for these demanding components.
Chemical Processing
The chemical industry utilizes Inconel 718 in heat exchangers and reactor cores, where resistance to corrosive chemicals and high temperatures is essential. The alloy’s durability and stability under such conditions ensure long service life and reliability.
Marine
In marine environments, Inconel 718 is used in submarine components and offshore drilling rigs. Its resistance to saltwater corrosion and high strength makes it suitable for these challenging applications.
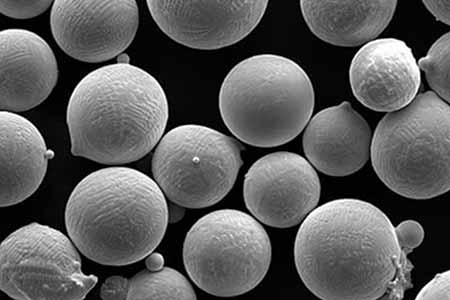
FAQs
Question | Answer |
---|---|
What is Inconel 718? | Inconel 718 is a nickel-chromium superalloy known for its high strength, corrosion resistance, and thermal stability. |
What are the main applications of Inconel 718? | It is used in aerospace, oil and gas, power generation, automotive, chemical processing, and marine industries. |
Why is Inconel 718 so expensive? | The cost is due to its complex manufacturing process and the high price of raw materials like nickel and chromium. |
Can Inconel 718 be welded? | Yes, Inconel 718 has good weldability and can be welded using standard techniques. |
What temperatures can Inconel 718 withstand? | Inconel 718 maintains its properties at temperatures up to 700°C (1292°F). |
Is Inconel 718 magnetic? | No, Inconel 718 is non-magnetic due to its nickel content. |
How does Inconel 718 compare to stainless steel? | Inconel 718 offers higher strength and better corrosion resistance compared to most stainless steels, but it is also more expensive and heavier. |
What are the limitations of Inconel 718? | The primary limitations are its high cost, challenging machinability, and heavy weight compared to some alternative materials. |
How is Inconel 718 manufactured? | It is produced through processes like vacuum induction melting (VIM) and vacuum arc remelting (VAR) to ensure high purity and performance. |
What forms does Inconel 718 come in? | Inconel 718 is available in various forms including bars, sheets, plates, wires, and tubes. |
Conclusion
Inconel 718 stands out as a high-performance superalloy that excels in demanding environments. Its unique combination of high strength, corrosion resistance, and thermal stability makes it indispensable in industries such as aerospace, oil and gas, power generation, and more. Despite its higher cost and challenging machinability, the benefits of Inconel 718 often outweigh these drawbacks, especially for critical applications where performance and reliability are paramount.
Understanding the specifics of Inconel 718, from its composition and properties to its applications and limitations, provides valuable insights for engineers, designers, and decision-makers. By leveraging the exceptional qualities of Inconel 718, industries can achieve new levels of performance and durability in their products and systems.
About 3DP mETAL
Product Category
CONTACT US
Any questions? Send us a message now! After receiving your message, we will process your request with a whole team.