Introduction
Imagine a material so strong it can handle the intense heat of a jet engine, yet so resistant to corrosion it can withstand the harsh environment of a chemical processing plant. That’s the magic of Inconel 718 powder, a superhero in the world of metal alloys. But what exactly is it, and why is it causing such a stir in the manufacturing industry? Buckle up, because we’re about to delve into the fascinating world of Inconel 718 powder, exploring its properties, applications, and the specific models that make it all possible.
What is Inconel 718 Powder?
At its core, Inconel 718 powder is a finely-ground version of Inconel 718, a high-performance nickel-chromium superalloy. Think of it like taking a bar of super strong steel and grinding it down into tiny particles. These particles, typically ranging in size from 15 to 150 micrometers (that’s incredibly small, about the width of a human hair!), are specifically designed for a revolutionary manufacturing technique called additive manufacturing, also known as 3D printing.
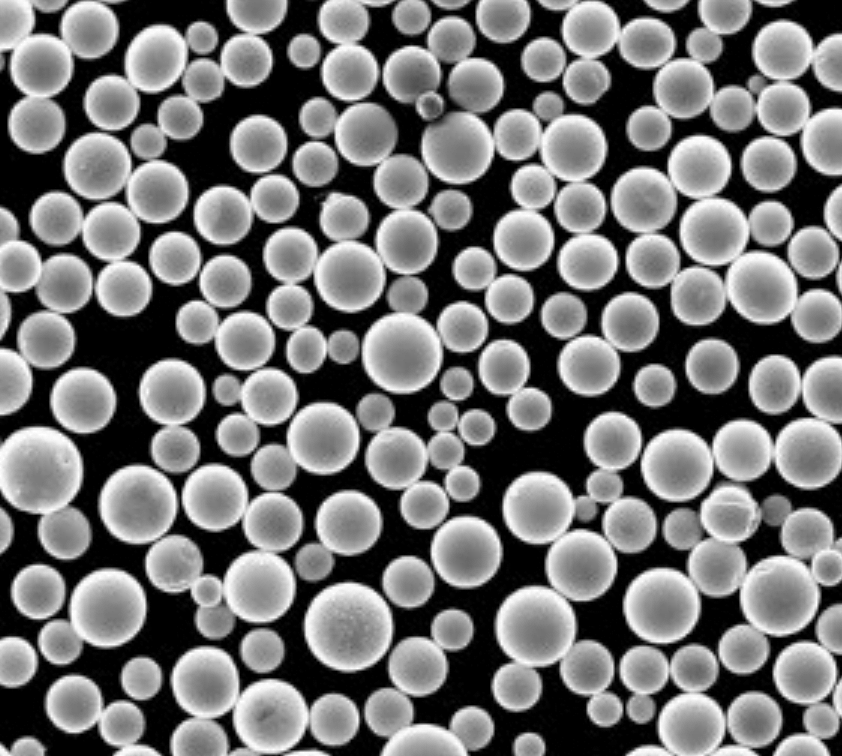
Key Properties of Inconel 718 Powder
(Table: Key Properties of Inconel 718 Powder)
Property | Description |
---|---|
High Strength | Inconel 718 powder boasts exceptional tensile strength, meaning it can resist pulling forces without breaking. This makes it ideal for components that experience significant stress, like turbine blades in aircraft engines. |
Excellent Corrosion Resistance | Even the most acidic or caustic environments can’t faze Inconel 718 powder. This resistance to rust and degradation makes it perfect for applications in chemical processing plants, marine environments, and oil and gas production. |
Superior Heat Resistance | Imagine a material that can shrug off scorching temperatures exceeding 1300°F (705°C). That’s the heat resistance of Inconel 718 powder, making it a prime candidate for parts exposed to extreme heat, like combustors and heat exchangers. |
Weldability | Unlike some finicky materials, Inconel 718 powder welds beautifully. This allows for the creation of complex and intricate structures using 3D printing technology. |
Age Hardenability | This unique property allows Inconel 718 powder to be further strengthened through a heat treatment process. This additional boost in strength makes it even more suitable for demanding applications. |
the Applications of Inconel 718 Powder
(Table: Applications of Inconel 718 Powder)
Industry | Application Examples |
---|---|
Aerospace | Turbine blades, combustor liners, landing gear components, rocket engine parts |
Oil & Gas | Downhole tools, wellhead components, valves |
Chemical Processing | Reactors, heat exchangers, pumps, valves |
Power Generation | Gas turbine components, heat exchangers |
Medical | Prosthetic implants, surgical instruments |
Specific Metal Powder Models
With the vast potential of Inconel 718 powder, it’s no surprise that there are various models available, each with slight variations in properties and specifications. Here’s a closer look at ten prominent models:
- AMCP AM 718: This water-atomized powder offers excellent flowability and packing density, making it ideal for complex 3D printing applications.
- Höganäs AM Hyperion® 718: This gas-atomized powder boasts superior strength and high-temperature capabilities, perfect for demanding aerospace components.
- SLM Solutions® Inconel 718: Optimized for laser beam melting (LBM) 3D printing, this powder delivers exceptional surface quality and dimensional accuracy.
- EOS GmbH Inconel 718 Powder: Tailored for the EOS additive manufacturing systems, this powder ensures consistent performance and reliable printability.
- Carpenter Additive AM 718: Produced by a renowned steel manufacturer, this powder offers high quality and consistency, making it a trusted choice for critical applications.
- Elementum Specialty Materials IN718: This water-atomized powder prioritizes affordability while maintaining good mechanical properties.
- Special Metals Corporation Osprey® 718: This gas-atomized powder is known for its exceptional cleanliness and low oxygen content, leading to superior weldability.
- Kennametal AM718: This powder offers a good balance between cost and performance, making it a versatile option for various applications.
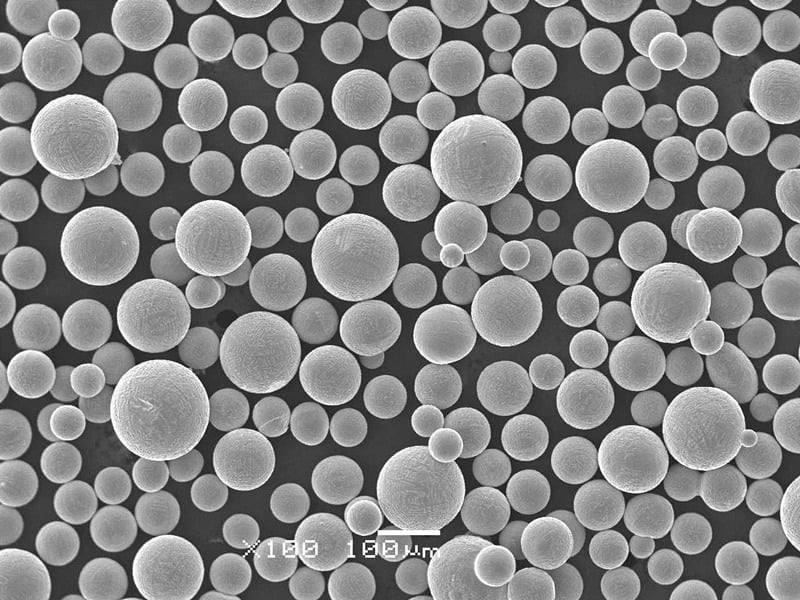
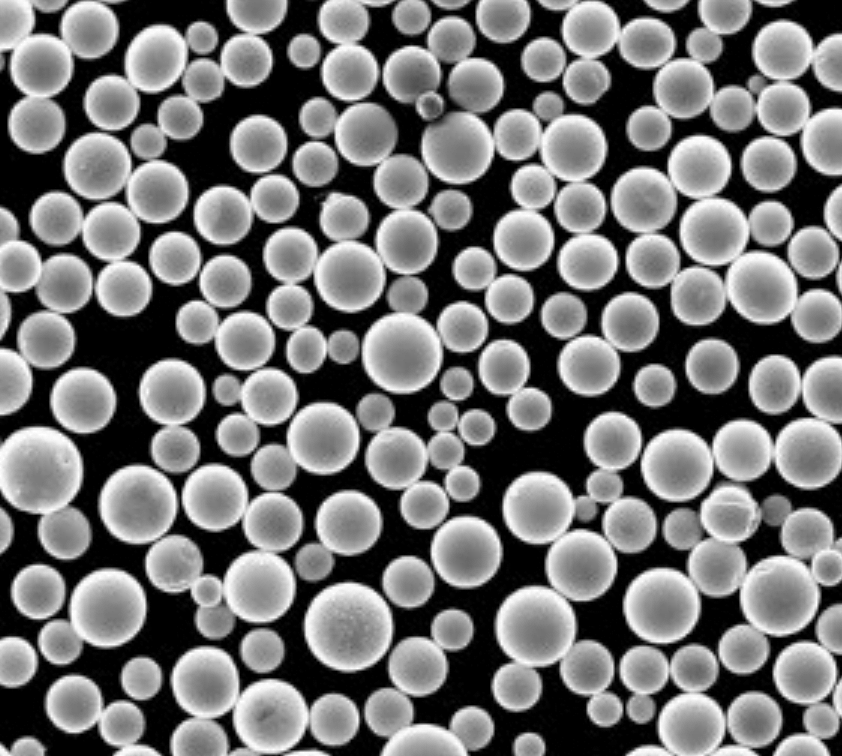
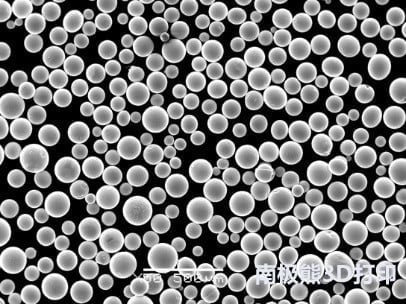
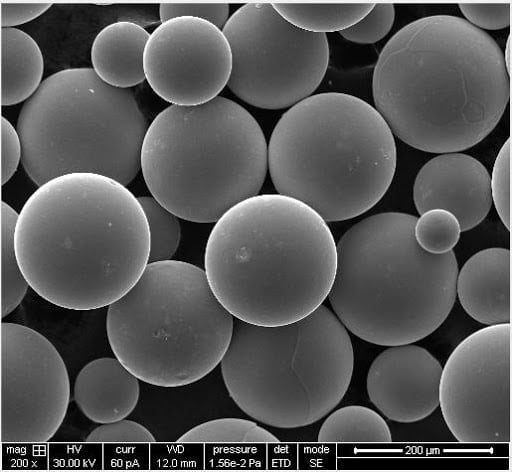
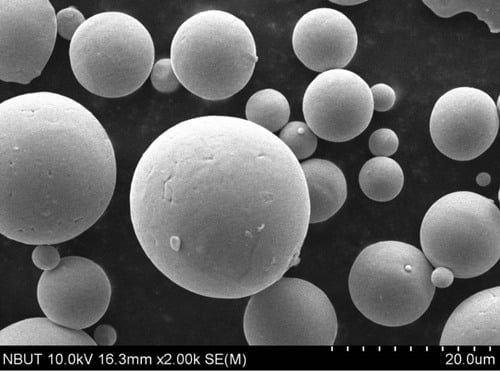
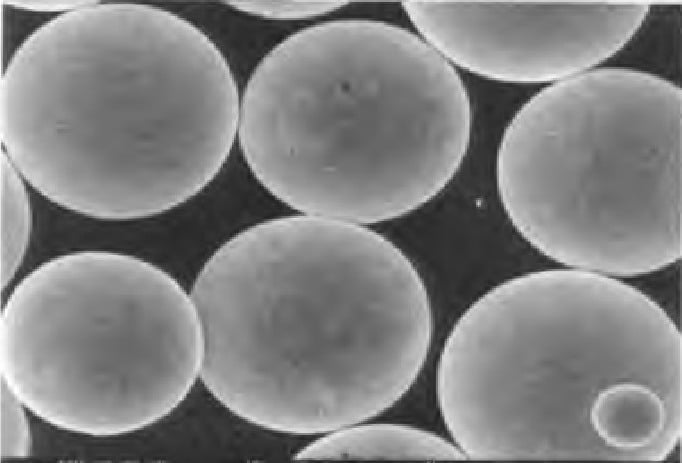
Inconel 718 Powder
Advantages and Disadvantages of Inconel 718 Powder
(Table: Advantages and Disadvantages of Inconel 718 Powder)
Advantage | Description | Disadvantage | Description |
---|---|---|---|
Exceptional Mechanical Properties | The combination of high strength, excellent corrosion resistance, and superior heat resistance makes Inconel 718 powder a top contender for demanding applications. | High Cost | Compared to traditional manufacturing methods, Inconel 718 powder can be more expensive due to the material cost and the specialized 3D printing equipment required. |
Design Freedom | Additive manufacturing allows for the creation of complex geometries and intricate designs that might be impossible with conventional techniques. | Process Complexity | 3D printing with Inconel 718 powder requires a high level of expertise and careful process control to ensure successful part production. |
Lightweighting Potential | The ability to create intricate lattice structures with 3D printing can significantly reduce the weight of components made from Inconel 718 powder, which is crucial in applications like aerospace. | Limited Material Availability | While Inconel 718 powder is becoming increasingly available, it might not be as readily accessible as some other metal powders. |
Reduced Material Waste | Unlike subtractive manufacturing techniques that generate significant scrap, 3D printing with Inconel 718 powder minimizes material waste, promoting sustainability. | Surface Roughness | Parts printed with Inconel 718 powder might require additional post-processing to achieve a desired surface finish. |
Specifications, Sizes, Grades, and Standards
(Table: Specifications, Sizes, Grades, and Standards of Inconel 718 Powder)
Property | Description |
---|---|
Chemical Composition | Typically consists of Nickel (Ni) as the base element, with significant amounts of Chromium (Cr), Iron (Fe), Niobium (Nb), Molybdenum (Mo), and other trace elements. The exact composition can vary slightly depending on the specific model. |
Particle Size | Ranges from 15 to 150 micrometers, with different size distributions available depending on the desired application and 3D printing technology. |
Grades | Inconel 718 powder is typically available in a single grade, conforming to the UNS N07718 or AMS 5662 specifications. |
Standards | Conforms to various industry standards, including ASTM International (ASTM) specifications and Aerospace Material Specifications (AMS). |
Suppliers and Pricing
(Table: Suppliers and Pricing of Inconel 718 Powder)
Supplier | Description | Pricing |
---|---|---|
AMCP Powder | A leading manufacturer of metal powders, offering AMCP AM 718 with competitive pricing. | Pricing varies depending on quantity and particle size. Generally starts around $100 per kilogram and can go up for finer grades. |
Höganäs AB | Renowned for their high-quality metal powders, Höganäs offers AM Hyperion® 718 at a premium price due to its exceptional properties. | Expect to pay a higher price point compared to standard models, potentially exceeding $200 per kilogram. |
SLM Solutions GmbH | Provides Inconel 718 powder specifically optimized for their 3D printing systems, potentially at a higher cost than generic models. | Pricing might be influenced by compatibility with specific SLM Solutions machines. |
EOS GmbH | Offers a range of metal powders, including Inconel 718 powder tailored for their EOS additive manufacturing systems. Pricing might vary depending on the chosen EOS platform. |
It’s important to note that pricing for Inconel 718 powder can fluctuate based on market conditions, order quantity, and specific supplier quotes. Always consult with potential suppliers for the most up-to-date pricing information.
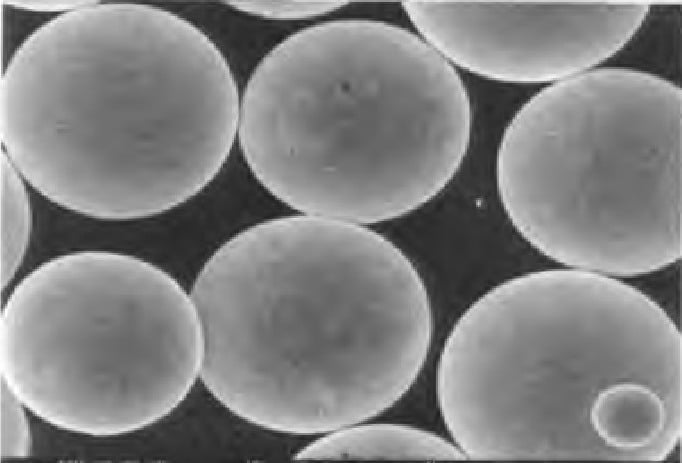
FAQ
Q: What are the benefits of using Inconel 718 powder compared to traditional manufacturing methods?
A: Inconel 718 powder offers several advantages, including design freedom for complex geometries, lightweighting potential, and reduced material waste. Additionally, 3D printing allows for faster prototyping and production compared to traditional techniques.
Q: Are there any limitations to using Inconel 718 powder?
A: The primary limitations include the higher cost compared to traditional methods, the complexity of the 3D printing process, and the limited availability of Inconel 718 powder compared to some other materials.
Q: What are the key properties of Inconel 718 powder?
- High Strength: Can resist pulling forces without breaking, making it ideal for components under significant stress.
- Excellent Corrosion Resistance: Withstands harsh environments like chemical processing plants and marine settings.
- Superior Heat Resistance: Can handle scorching temperatures exceeding 1300°F (705°C), perfect for parts exposed to extreme heat.
- Weldability: Allows for the creation of intricate structures through 3D printing and easy joining with other components.
- Age Hardenability: Can be further strengthened through a heat treatment process for even more demanding applications.
Q: What are some applications of Inconel 718 powder?
- Aerospace: Turbine blades, combustor liners, landing gear components, rocket engine parts.
- Oil & Gas: Downhole tools, wellhead components, valves.
- Chemical Processing: Reactors, heat exchangers, pumps, valves.
- Power Generation: Gas turbine components, heat exchangers.
- Medical: Prosthetic implants, surgical instruments (limited use due to biocompatibility considerations).
Q: What are the advantages and disadvantages of using Inconel 718 powder?
Advantages:
- Exceptional mechanical properties (strength, corrosion resistance, heat resistance)
- Design freedom for complex geometries and lightweighting potential
- Reduced material waste compared to traditional manufacturing
Disadvantages:
- High cost compared to traditional methods
- Process complexity of 3D printing requires expertise and control
- Limited material availability compared to some other metal powders
- Surface roughness might require additional post-processing
Q: What are some things to consider when choosing an Inconel 718 powder supplier?
- Pricing: Prices can vary depending on quantity, particle size, and supplier.
- Availability: Not all suppliers may carry Inconel 718 powder readily.
- Compatibility: If using a specific 3D printing system, ensure the powder is optimized for that machine.
- Reputation: Choose a reputable supplier with a history of high-quality metal powders.
Q: What is the future outlook for Inconel 718 powder?
The future looks promising with potential advancements in:
- New alloys: Development of even better performing nickel-based superalloy powders.
- Reduced powder costs: Economies of scale could lead to lower material costs.
- Improved printability: Faster printing speeds and better control over the 3D printing process.
About 3DP mETAL
Product Category
CONTACT US
Any questions? Send us a message now! After receiving your message, we will process your request with a whole team.