Inconel 718 powder, a name that conjures images of immense strength and unwavering resilience, is a superhero in the world of advanced materials. But what exactly is this wonder material, and why is it causing such a stir in the manufacturing industry? Buckle up, because we’re about to embark on a journey to uncover the secrets of Inconel 718 powder, exploring its composition, properties, applications, and the very specific reasons why it stands out from the crowd.
Composition and Properties of Inconel 718 Powder
At its core, Inconel 718 powder is a nickel-chromium superalloy, a fancy way of saying it’s a metal alloy primarily composed of nickel and chromium, with other elements strategically added to create a powerhouse of properties. Imagine it like a superhero team – nickel is the leader, providing overall strength, while chromium acts as the shield, offering exceptional resistance to corrosion and high temperatures. But that’s not all! Other teammates like molybdenum, niobium, and titanium join the party, each contributing unique abilities like high creep resistance and exceptional weldability.
Here’s a table summarizing the key aspects of Inconel 718 powder:
Property | Description |
---|---|
Composition | Primarily Nickel (Ni), Chromium (Cr), with additions of Molybdenum (Mo), Niobium (Nb), Titanium (Ti), and others |
Form | Fine, spherical metal powder |
Color | Silvery-gray |
Density | Around 8.2 g/cm³ |
Melting Point | Approximately 1300°C (2372°F) |
Key Strengths | High strength, excellent corrosion resistance, resistance to high temperatures, good weldability |
Let’s delve deeper into these properties:
- High Strength: Imagine a material that can withstand immense pressure and force without breaking a sweat. That’s Inconel 718 powder. Its high strength makes it ideal for applications where structural integrity is paramount, like aerospace components and downhole oil drilling equipment.
- Exceptional Corrosion Resistance: Saltwater, harsh chemicals – no problem for Inconel 718 powder. Its exceptional resistance to corrosion ensures components can function flawlessly in demanding environments, like marine applications and chemical processing equipment.
- Resistance to High Temperatures: Think of a material that can shrug off scorching heat like it’s a gentle breeze. Inconel 718 powder maintains its strength and structural integrity at high temperatures, making it perfect for applications like jet engine parts and heat exchangers.
- Good Weldability: Seamless integration is crucial for complex components. Inconel 718 powder exhibits good weldability, allowing for the creation of strong, reliable joints between different parts.
These properties, combined with its versatility in forming intricate shapes, make Inconel 718 powder a highly sought-after material for various demanding applications.
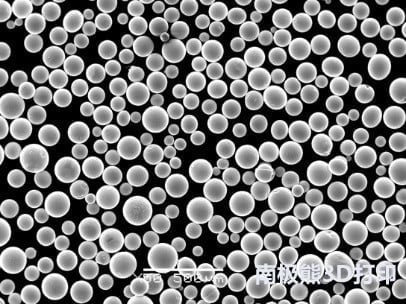
Applications of Inconel 718 Powder
The exceptional properties of Inconel 718 powder translate into a vast array of applications across diverse industries. Here’s a glimpse into where this wonder material shines:
Industry | Applications |
---|---|
Aerospace | Turbine blades, rocket engine components, landing gear components |
Oil & Gas | Downhole drilling equipment, wellhead components |
Chemical Processing | Reactors, heat exchangers, valves |
Power Generation | Gas turbine components, heat exchangers |
Marine | Propeller shafts, rudders, valves |
Medical | Implants, surgical instruments |
Let’s explore some of these applications in more detail:
- Aerospace: Soaring through the skies requires materials that can handle extreme temperatures and stresses. Inconel 718 powder is a key player in aerospace, used in turbine blades that propel jet engines and rocket engine components that withstand the fiery wrath of combustion.
- Oil & Gas: Venturing deep below the Earth’s surface demands equipment that can withstand immense pressure and harsh environments. Inconel 718 powder is perfectly suited for downhole drilling equipment and wellhead components, ensuring safe and reliable extraction of oil and gas.
- Chemical Processing: Chemical reactions can be brutal on materials. That’s where Inconel 718 powder steps in. Its exceptional corrosion resistance makes it ideal for reactors, heat exchangers, and valves used in the chemical processing industry.
Specific Metal Powder Models of Inconel 718
The realm of Inconel 718 powder isn’t a one-size-fits-all situation. Several manufacturers offer distinct models, each with slight variations in composition and properties tailored for specific applications. Here are ten noteworthy models to consider:
- AMPO® Nickel Alloy 718: This offering from Höganäs, a leading metal powder producer, boasts excellent flowability and packing density, making it ideal for Additive Manufacturing (AM) processes like laser sintering.
- EOS NickelAlloy IN718: Developed by EOS GmbH, a renowned AM technology provider, this model is specifically optimized for their laser sintering systems, ensuring high-quality parts with consistent properties.
- SLM® Solutions Nickel 718: This model from SLM Solutions, another major player in the AM arena, is designed for their selective laser melting (SLM) machines, delivering exceptional mechanical properties for demanding applications.
- Waterbury® IN718: Carpenter Additive Division’s Waterbury® IN718 caters to various AM processes, offering a good balance of strength, ductility, and printability.
- Pramco® IN718: Pramet offers Pramco® IN718, known for its consistent particle size distribution and high tap density, leading to improved powder bed packing and printability.
- Special Metals Corporation IN718: This model from Special Metals Corporation prioritizes high performance, delivering excellent strength and high-temperature capabilities for critical applications.
- Arcam® AM718: This offering from Arcam AB, a prominent AM equipment manufacturer, is specifically formulated for their electron beam melting (EBM) machines, resulting in dense, near-net-shape components with superior mechanical properties.
- LPW® IN718: LPW Technology’s LPW® IN718 is optimized for their laser powder bed fusion (LPBF) systems, ensuring high build rates and excellent mechanical properties for aerospace and other demanding applications.
- GE Additive IN718: This model from GE Additive, a leader in the AM industry, caters to various AM processes, offering a balance of properties for a wide range of applications. 1 0. ADDISIVE Industries IN718: ADDISIVE Industries’ IN718 is formulated for their metal additive manufacturing systems, known for its good flowability and packing density, leading to improved powder bed characteristics.
Choosing the Right Model:
Selecting the most suitable Inconel 718 powder model depends on several factors, including:
- Specific application: The desired properties like strength, corrosion resistance, and printability will guide your choice.
- AM process: Different AM technologies have varying powder requirements. Ensure compatibility between the model and your chosen AM system.
- Manufacturer reputation: Consider the manufacturer’s experience and expertise in metal powder production.
It’s crucial to consult with material suppliers and AM equipment manufacturers to determine the optimal Inconel 718 powder model for your specific needs.
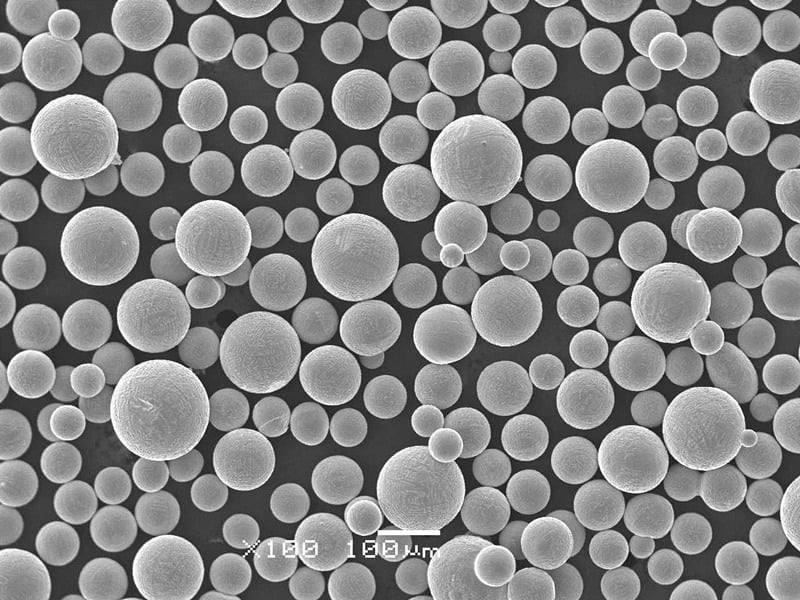
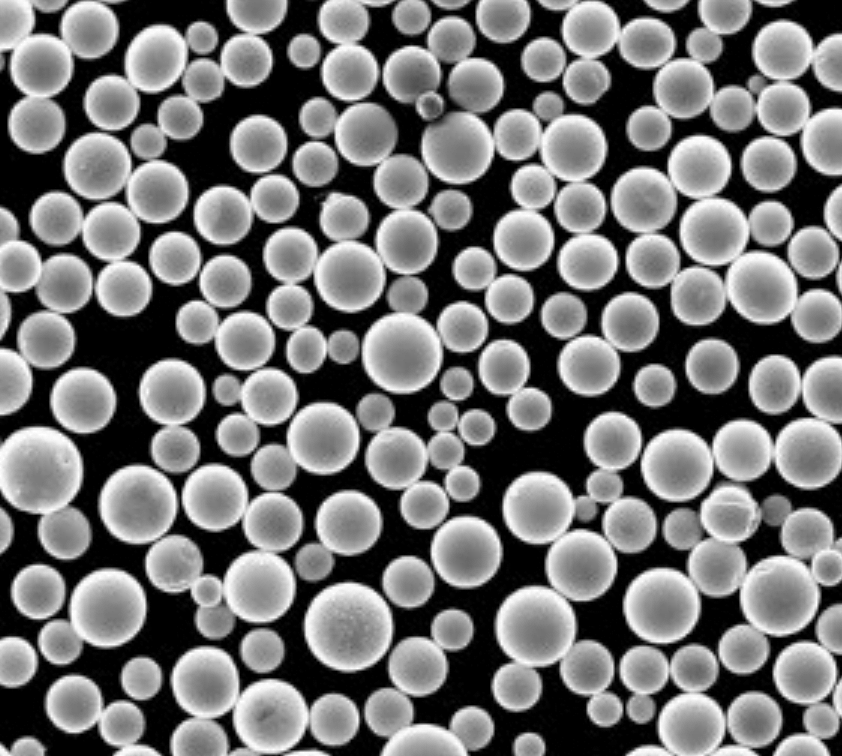
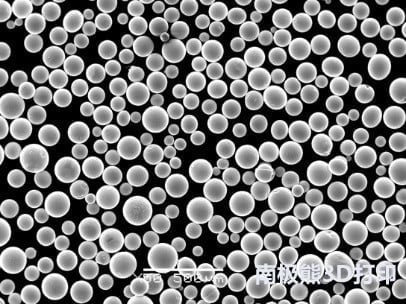
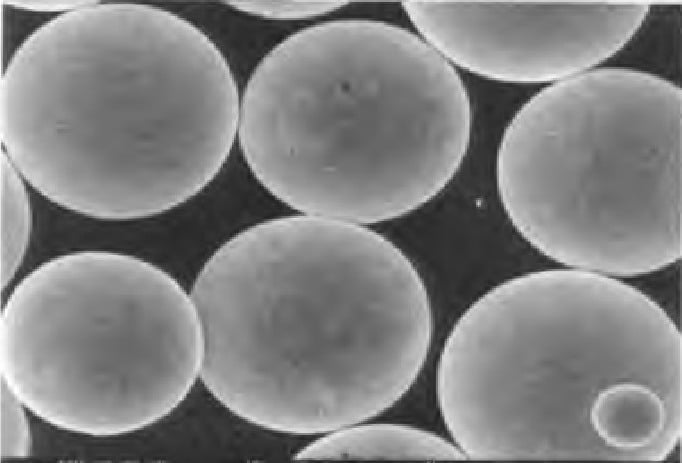
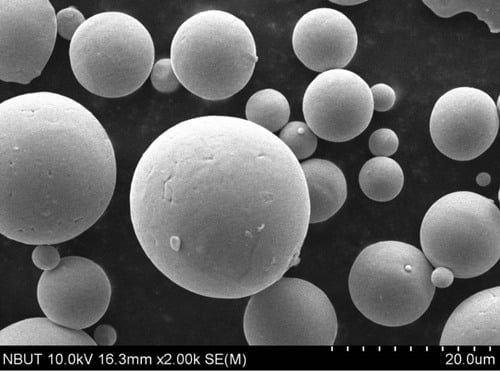
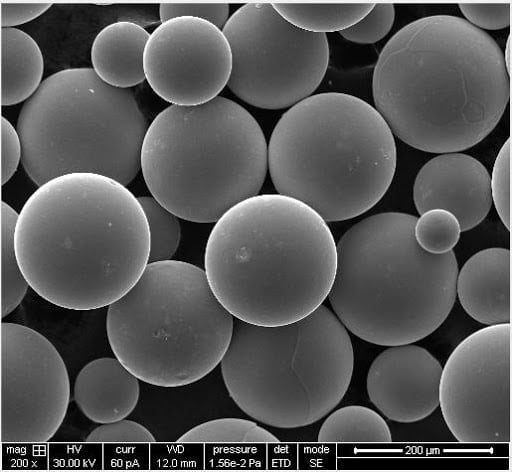
Advantages and Limitations of Inconel 718 Powder
While Inconel 718 powder boasts an impressive array of advantages, it’s essential to acknowledge its limitations to make an informed decision. Here’s a balanced perspective:
Advantages:
- Exceptional Properties: The combination of high strength, excellent corrosion resistance, high-temperature capabilities, and good weldability makes it a go-to material for demanding applications.
- Design Flexibility: AM processes utilizing Inconel 718 powder enable the creation of intricate shapes and complex geometries, previously impossible with traditional manufacturing methods.
- Reduced Waste: Compared to conventional manufacturing techniques, AM with Inconel 718 powder minimizes material waste, promoting sustainability.
- Lightweighting Potential: AM allows for the creation of lightweight components with high strength-to-weight ratios, crucial in sectors like aerospace.
Limitations:
- Cost: Inconel 718 powder itself and the AM processes involved can be expensive compared to traditional manufacturing methods.
- Surface Finish: AM-produced parts using Inconel 718 powder may require post-processing for a desired surface finish.
- Build Time: Depending on the part complexity and size, AM processes with Inconel 718 powder can have longer build times compared to some conventional techniques.
- Limited Availability: While the availability of Inconel 718 powder is increasing, it might not be readily available in all regions or through all suppliers compared to more common metal powders.
- Process Expertise: Successful utilization of Inconel 718 powder in AM requires skilled operators and in-depth process knowledge.
Making an Informed Choice:
Despite the limitations, the advantages of Inconel 718 powder are undeniable. By carefully considering the application requirements, weighing the pros and cons, and collaborating with qualified suppliers and AM professionals, you can leverage the true potential of this remarkable material.
Specifications, Sizes, Grades, and Standards
When working with Inconel 718 powder, understanding the available specifications, sizes, grades, and relevant standards is essential. Here’s a breakdown to guide you:
Specifications:
Inconel 718 powder typically adheres to specifications outlined by organizations like ASTM International (ASTM) or AMS International (AMS). These specifications define the chemical composition, mechanical properties, and powder characteristics like particle size distribution and flowability. Some common specifications for Inconel 718 powder include ASTM B166 and AMS 5662.
Sizes:
Inconel 718 powder comes in various particle sizes, typically ranging from 15 to 150 microns. The chosen size depends on the specific AM process and desired part properties. Finer powders generally produce smoother surface finishes, while coarser powders may offer better flowability.
Grades:
There can be slight variations in the composition of Inconel 718 powder, leading to different grades. These variations may involve adjustments to specific elements like niobium or titanium content, tailored for optimizing certain properties. Consulting with material suppliers about the available grades and their suitability for your application is crucial.
Standards:
Several industry standards govern the production, quality control, and testing of Inconel 718 powder. These standards ensure consistency and reliability in the material. Some relevant standards include ASTM F3054 and ISO 5793.
Understanding these factors allows for precise communication with suppliers and facilitates the selection of Inconel 718 powder that perfectly aligns with your project requirements.
Suppliers and Pricing
The cost of Inconel 718 powder can vary depending on several factors, including:
- Supplier: Different suppliers may have varying pricing structures based on their production costs and market dynamics.
- Quantity: Generally, bulk purchases offer lower per-unit costs compared to smaller quantities.
- Specific Model: As discussed earlier, different models from various manufacturers might have slight price variations.
Here’s a table outlining a general range for Inconel 718 powder pricing, keeping in mind the aforementioned factors can cause fluctuations:
Quantity | Estimated Price Range (per kilogram) |
---|---|
Small quantities (less than 10 kg) | $200 – $400 |
Larger quantities (over 10 kg) | $150 – $300 |
Supplier Selection:
When choosing a supplier for Inconel 718 powder, consider these aspects:
- Reputation: Look for a reputable supplier with a proven track record of providing high-quality metal powders.
- Experience: Choose a supplier with experience in Inconel 718 powder and a good understanding of AM processes.
- Technical Support: Ensure the supplier offers technical support to assist you in selecting the most suitable powder for your application.
- Pricing: While cost is a factor, prioritize quality and reliable supply over chasing the absolute lowest price.
By carefully evaluating these points, you can select a supplier that provides high-quality Inconel 718 powder at a fair price, setting your project up for success.
Remember, the cost of Inconel 718 powder is just one aspect to consider. The overall project economics will also factor in the AM process costs, post-processing requirements, and the value proposition of the final component.
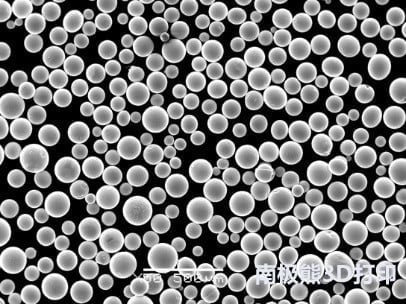
Advantages vs. Disadvantages
Here’s a table summarizing the key advantages and limitations of Inconel 718 powder to help you make an informed decision:
Advantages | Disadvantages |
---|---|
Exceptional combination of high strength, corrosion resistance, high-temperature capabilities, and good weldability | Higher cost compared to traditional manufacturing methods |
Design flexibility for creating intricate shapes and complex geometries | May require post-processing for a desired surface finish |
Reduced waste compared to conventional manufacturing techniques | Build time can be longer for complex parts compared to some traditional methods |
Lightweighting potential for applications like aerospace | Limited availability in all regions or through all suppliers compared to more common metal powders |
Enables the creation of near-net-shape components | Requires skilled operators and in-depth process knowledge for successful utilization |
The Verdict: A Material with Immense Potential
While Inconel 718 powder has limitations, its advantages are undeniable. For applications demanding exceptional properties, intricate designs, and lightweighting potential, Inconel 718 powder shines. However, the cost factor and process requirements necessitate careful consideration.
Here’s an analogy to solidify this concept: Imagine Inconel 718 powder as a high-performance sports car. It offers incredible speed, handling, and performance (like the exceptional properties), but it comes with a higher price tag and requires a skilled driver to handle its potential (like the cost and process expertise). For everyday commutes, a reliable sedan might suffice. But for pushing the boundaries of performance, the sports car is the clear choice.
The decision to utilize Inconel 718 powder hinges on your specific project requirements and priorities. By weighing the pros and cons, and carefully considering the application needs, you can determine if this remarkable material is the perfect fit for your project.
FAQ
Here are some frequently asked questions regarding Inconel 718 powder, answered in a clear and concise manner:
Q: What are some alternative materials to Inconel 718 powder?
A: Several alternative materials offer similar properties, including other nickel-based superalloys like Inconel 625 or Haynes 282. The choice depends on the specific application requirements and desired balance of properties.
Q: Can Inconel 718 powder be recycled?
A: Yes, Inconel 718 powder can be recycled to a certain extent, although the process might involve additional steps compared to virgin powder. Recycling can help reduce costs and minimize environmental impact.
Q: What are the typical applications for Inconel 718 parts produced via AM?
A: AM-produced Inconel 718 parts find applications in various sectors, including aerospace components (turbine blades, landing gear), downhole oil and gas equipment, chemical processing equipment (reactors, heat exchangers), and implant devices in the medical field.
Q: How strong is Inconel 718 powder compared to other metal powders?
A: Inconel 718 powder boasts exceptional strength, superior to many commonly used metal powders like stainless steel or aluminum. This high strength makes it ideal for applications requiring exceptional load-bearing capabilities.
Q: What are the future prospects for Inconel 718 powder?
A: The future of Inconel 718 powder looks bright. Advancements in AM technology and continuous research are expected to improve printability, potentially leading to faster build times and reduced costs. This could further expand the range of applications where Inconel 718 powder proves to be the ideal material choice.
About 3DP mETAL
Product Category
CONTACT US
Any questions? Send us a message now! After receiving your message, we will process your request with a whole team.