CuSnTi powder, also known as copper-tin-titanium powder, is a metal alloy powder gaining significant traction in the realm of Powder Metallurgy (PM). Imagine tiny, potent warriors made of copper, tin, and titanium, ready to be pressed and sintered into formidable metal parts. That’s the essence of CuSnTi powder – a potent combination offering a unique blend of properties for PM applications.
This article delves deep into the world of CuSnTi power, exploring its composition, properties, applications, advantages, limitations, and various available models. Buckle up, as we embark on a journey to understand this powerful PM material!
la composizione di CuSnTi Powder
CuSnTi powder, as the name suggests, is a composite metal powder consisting primarily of copper (Cu), tin (Sn), and titanium (Ti). The exact proportions of these elements can vary depending on the desired final properties of the part being manufactured. Here’s a breakdown of the key players:
- Rame (Cu): The dominant element, often constituting around 80-90% of the composition. Copper provides excellent thermal and electrical conductivity, making CuSnTi powder well-suited for applications like heat sinks and electrical components.
- Tin (Sn): Typically present in a range of 6-10%. Tin acts as a sintering aid, lowering the sintering temperature required to form strong bonds between the powder particles. This translates to energy savings during the PM process.
- Titanio (Ti): The “secret weapon” of CuSnTi powder, usually present in quantities of 0.5-2%. Titanium boasts superior strength and enhances the mechanical properties of the final part, making it ideal for applications demanding high strength-to-weight ratios.
Additionally, some CuSnTi powder formulations might include trace amounts of other elements like nickel (Ni) or chromium (Cr) to further fine-tune specific properties like corrosion resistance or wear resistance.
By carefully manipulating the ratios of these elements, manufacturers can tailor CuSnTi powder to meet the specific needs of a vast array of PM applications.
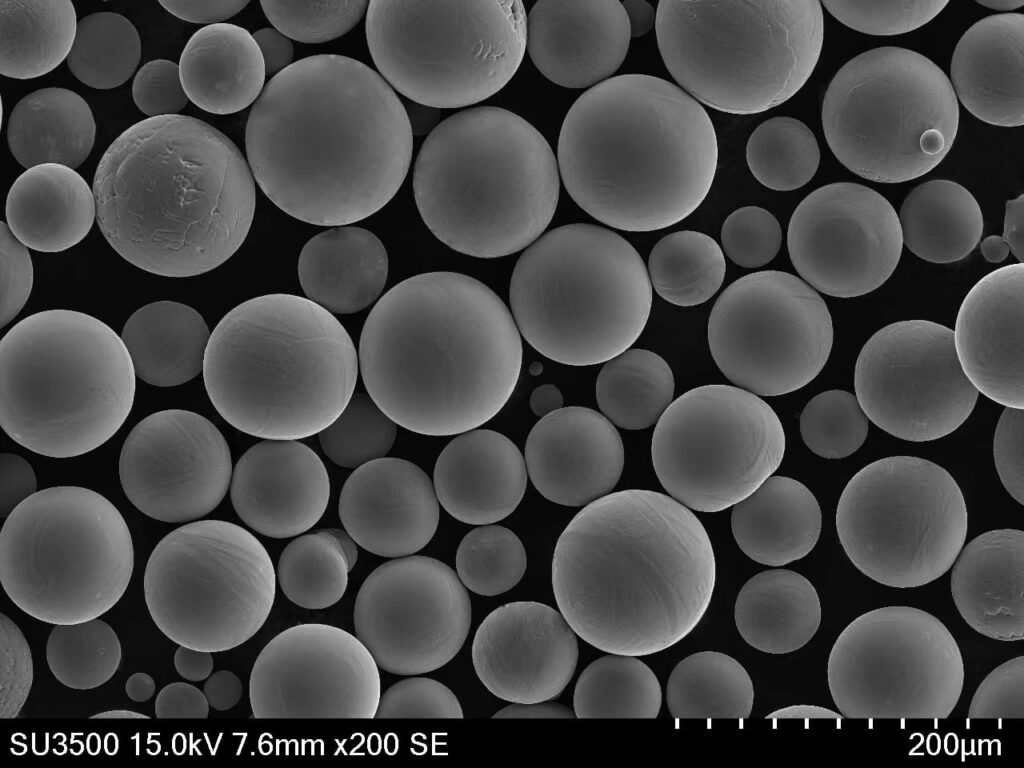
the Superpowers of CuSnTi Powder
Now that we’ve met the team players, let’s explore the superpowers CuSnTi powder possesses:
- Alta resistenza: The presence of titanium significantly boosts the strength of CuSnTi PM parts compared to pure copper parts. Imagine replacing a flimsy copper pipe with a robust CuSnTi counterpart – that’s the kind of strength enhancement we’re talking about.
- Eccellente conduttività: Copper, the dominant element, ensures CuSnTi powder retains a good degree of thermal and electrical conductivity. This makes it a valuable material for applications requiring efficient heat dissipation or electrical conduction.
- Improved Sinterability: The addition of tin as a sintering aid lowers the sintering temperature required to create strong bonds between the powder particles. Think of it as a magic ingredient that allows the powder to “fuse” more easily during the PM process, saving energy and production time.
- Resistenza alla corrosione: Depending on the specific composition, some CuSnTi formulations can exhibit enhanced resistance to corrosion compared to pure copper. Consider it a protective shield against environmental elements that might otherwise degrade the material.
- Buona lavorabilità: CuSnTi PM parts often demonstrate good machinability, allowing for post-processing and shaping as needed. This flexibility ensures the final product can be customized to meet specific design requirements.
It’s important to remember that the specific properties of CuSnTi powder can vary depending on the exact composition and processing parameters. However, the qualities mentioned above highlight the potential of this versatile material for various PM applications.
Applications of CuSnTi Powder
CuSnTi powder finds application in a diverse range of industries, thanks to its unique blend of properties. Here are some prominent examples:
- Industria automobilistica: CuSnTi powder shines in the automotive sector, used to manufacture components like bushings, connectors, and heat sinks due to its strength, conductivity, and good machinability. Imagine lightweight, robust engine components that efficiently dissipate heat – that’s the power of CuSnTi at play.
- Electronics Industry: The combination of conductivity and sinterability makes CuSnTi powder a valuable material for electronic components like lead frames and connectors. Think of tiny, reliable connectors that efficiently conduct electricity within your favorite gadgets – that’s CuSnTi doing its job.
- Industria aerospaziale: The need for high strength-to-weight ratio materials makes CuSnTi powder a potential candidate for specific aerospace applications. Imagine lightweight yet robust components in aircraft that can withstand demanding operational environments – that’s the potential of CuSnTi in action.
- Beni di consumo: The good machinability and potential for a polished appearance make CuSnTi powder a possibility for specific consumer goods applications. Imagine sleek, functional components in everyday items with a touch of strength – that’s CuSnTi’s versatility on display.
It’s important to note that CuSnTi powder is a relatively new player in the PM arena, and its applications are still under development. However, ongoing research and innovation are continuously expanding its reach across various industries.
Exploring Specific CuSnTi Powder Models
Now that we’ve explored the general properties and applications of CuSnTi powder, let’s delve deeper and meet some of the key players in the field. Here’s a breakdown of ten prominent CuSnTi powder models, highlighting their unique characteristics:
Nome del modello | Composizione (wt%) | Proprietà chiave | APPLICAZIONI |
---|---|---|---|
Höganäs AM [AMPC040] | Cu-8.0Sn-1.0Ti | High strength, good conductivity, excellent machinability | Automotive bushings, connectors, heat sinks |
Ametek [Scoville SC-75] | Cu-9.0Sn-1.5Ti | Improved corrosion resistance, good sinterability | Electronic connectors, lead frames |
Carpenter Additive [Carpenter Incus] | Cu-8.5Sn-1.0Ti-0.5Ni | Enhanced strength and wear resistance | Aerospace components (potential) |
AP&C [ὅ (Ohm) CuSnTi] | Cu-8.0Sn-2.0Ti | Elevato rapporto resistenza-peso | Aerospace components (potential) |
GKN Hoeganaes [AMPC030] | Cu-6.0Sn-1.0Ti | Excellent machinability, good conductivity | Consumer goods components (potential) |
Merck [EMD Millipore CuSnTi] | Cu-8.5Sn-1.0Ti | Elevata conducibilità termica | Heat sinks, electronics components |
Lehmann & Voss [Levo CuSnTi] | Cu-7.5Sn-1.5Ti | Improved corrosion resistance, good sinterability | Fluid handling components (potential) |
Sasol [Catamold CuSnTi] | Cu-9.0Sn-1.0Ti | Good balance of strength and conductivity | Electrical connectors, automotive components |
LP Powder [AM CuSnTi] | Cu-8.0Sn-1.0Ti-0.25Cr | Maggiore resistenza all'ossidazione | High-temperature applications (potential) |
Höganäs [AMPC050] | Cu-10.0Sn-0.5Ti | Very good sinterability | Applications requiring low-cost, fast production |
Please note that this table is not exhaustive, and there are many other CuSnTi powder models available from various manufacturers. The specific properties and applications can vary depending on the manufacturer’s formulation and processing techniques.
When choosing a CuSnTi powder model, it’s crucial to consider the desired final properties of the PM part and consult with the material supplier for specific recommendations.
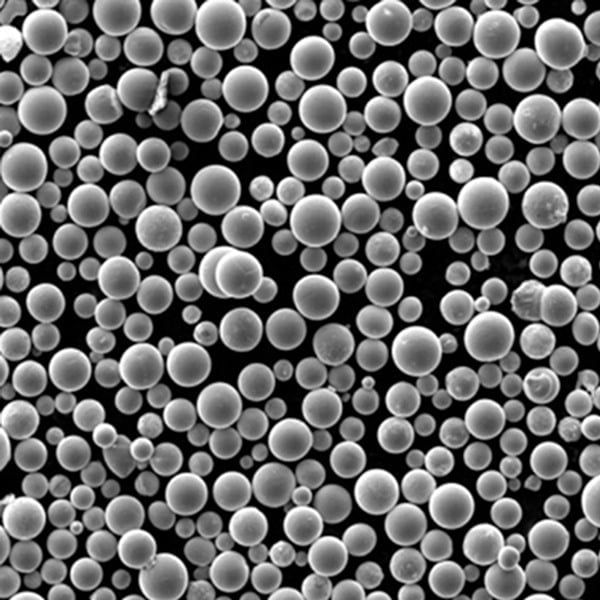
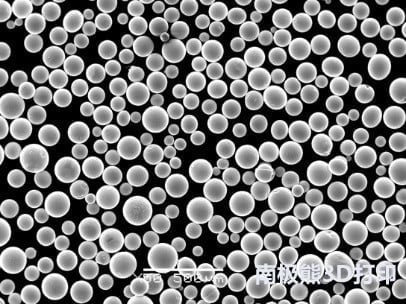
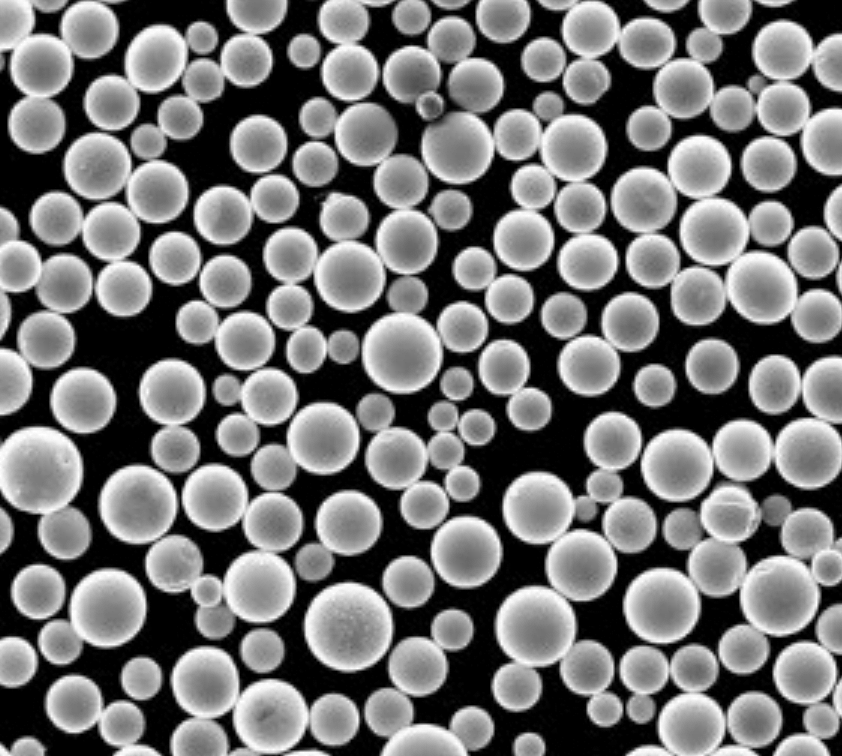
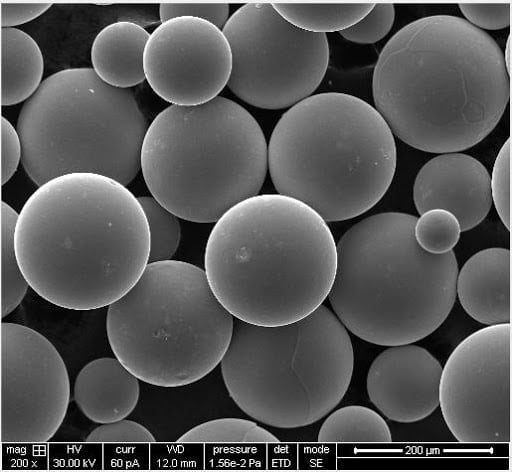
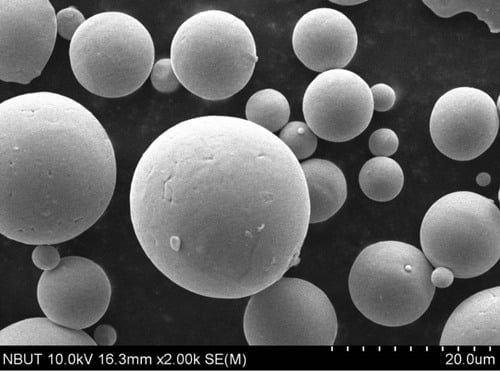
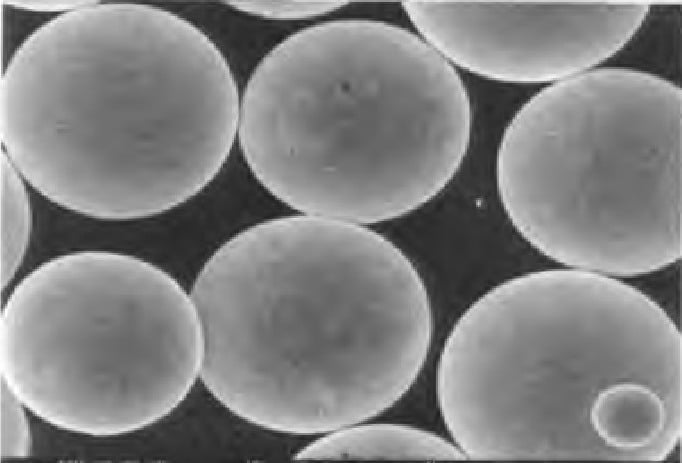
Vantaggi e limiti di CuSnTi Powder
Like any material, CuSnTi powder comes with its own set of advantages and limitations. Let’s weigh the pros and cons to understand its true potential:
Vantaggi:
- Alta resistenza: The presence of titanium significantly enhances the strength of CuSnTi PM parts compared to pure copper.
- Eccellente conduttività: Copper, the dominant element, ensures CuSnTi powder retains a good degree of thermal and electrical conductivity.
- Improved Sinterability: The addition of tin lowers the sintering temperature, leading to energy savings and faster production times.
- Resistenza alla corrosione: Depending on the composition, some CuSnTi formulations offer enhanced resistance to corrosion compared to pure copper.
- Buona lavorabilità: CuSnTi PM parts often demonstrate good machinability, allowing for post-processing and shaping as needed.
Limitazioni:
- Costo: CuSnTi powder can be more expensive than pure copper powder due to the addition of titanium.
- Oxidation: At high temperatures, CuSnTi can be susceptible to oxidation, requiring specific processing techniques or additional alloying elements for mitigation.
- Disponibilità limitata: Compared to some more widely used PM materials, CuSnTi powder might have limited availability from certain suppliers.
- Relatively New Material: Being a newer player in the PM arena, CuSnTi powder might require further research and development to fully optimize its properties and applications.
By carefully considering these advantages and limitations, engineers and manufacturers can determine if CuSnTi powder is the right fit for their specific PM application.
Here’s an analogy: Imagine CuSnTi powder as a highly skilled warrior. It possesses exceptional strength and agility (high strength and good conductivity), but requires specialized training and equipment (potentially higher cost and specific processing techniques) to unleash its full potential. Additionally, the warrior might be relatively new to the battlefield (limited availability and a newer material), requiring some experience to truly master combat (further research and development).
Specifiche, dimensioni, gradi e standard
For those delving deeper into the technical aspects of CuSnTi powder, here’s a breakdown of key specifications, sizes, grades, and relevant standards:
Specifiche:
- Distribuzione granulometrica: The size and distribution of CuSnTi powder particles significantly impact the final properties of the PM part. Typically, CuSnTi powder is available in a range of particle sizes, from a few microns to several hundred microns. Finer particle sizes can lead to higher density and improved mechanical properties, but might also affect flowability during processing.
- Apparente densità: This refers to the bulk density of the CuSnTi powder, which influences the amount of powder needed to fill a mold during the PM process.
- Capacità di scorrimento The ease with which the powder flows is crucial for efficient processing. Powders with good flowability ensure consistent filling of molds and minimize production issues.
Sizes & Grades:
- CuSnTi powder is typically available in a range of standard particle sizes, catering to different PM applications. Common size ranges include:
- < 10 microns (very fine)
- 10-45 microns (fine)
- 45-100 microns (medium)
- 100-250 microns (coarse)
- Some manufacturers might offer CuSnTi powder in specific grades with tailored properties for particular applications.
Standard:
- Several industry standards govern the specifications and testing methods for CuSnTi powder. These standards ensure consistency and quality between different manufacturers. Some relevant standards include:
- ASTM B930 – Standard Specification for Copper-Tin Alloys in Wrought Forms
- MPIF Standard 35 – Standard Test Methods for Metal Powders and Feedstocks
It’s important to consult with the CuSnTi powder supplier for specific technical data and ensure the material meets the required standards for your intended application.
CuSnTi Powder vs. Alternatives
CuSnTi powder isn’t the only contender in the PM arena. Here’s a comparison with some commonly used alternatives to understand its relative strengths and weaknesses:
Caratteristica | CuSnTi Powder | Polvere di bronzo | Polvere di ferro |
---|---|---|---|
Forza | Elevato | Moderato | Elevato |
Conduttività | Excellent (thermal & electrical) | Good (electrical) | Scarso |
Sinterabilità | Bene | Eccellente | Bene |
Resistenza alla corrosione | Can be improved (depending on composition) | Moderato | Scarso |
Costi | Più alto | Inferiore | Inferiore |
Bronze powder offers good sinterability and can be a cost-effective alternative for applications where high strength isn’t a primary concern. However, its conductivity is lower compared to CuSnTi powder.
Iron powder boasts high strength but lacks the good conductivity of CuSnTi powder. Additionally, iron powder is susceptible to corrosion, making it unsuitable for applications requiring good corrosion resistance.
The choice between CuSnTi powder and these alternatives depends on the specific needs of the PM application. If high strength, good conductivity, and decent sinterability are paramount, CuSnTi powder emerges as a compelling option.
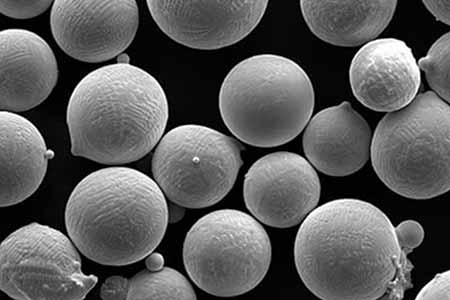
FAQ
Q: Is CuSnTi powder safe to use?
A: CuSnTi powder itself is generally considered safe to handle with proper precautions. However, as with any metal powder, inhalation should be avoided. Always follow recommended safety practices when handling CuSnTi powder, including wearing appropriate personal protective equipment (PPE) such as gloves, safety glasses, and dust masks.
Q: How is CuSnTi powder recycled?
A: CuSnTi powder scrap from the PM process can potentially be recycled and reused depending on the specific composition and contamination levels. Consult with your CuSnTi powder supplier for specific recycling recommendations.
Q: What are the future prospects of CuSnTi powder?
A: With ongoing research and development, CuSnTi powder holds promise for even wider adoption in various PM applications. Potential areas of exploration include further optimization of properties for specific applications, development of new CuSnTi powder formulations with enhanced characteristics, and exploring cost-reduction strategies to make CuSnTi powder more competitive in the PM market.
Q: Where can I buy CuSnTi powder?
A: Several reputable metal powder suppliers offer CuSnTi powder. Here are some resources to get you started:
Informazioni su 3DP mETAL
Categoria di prodotto
CONTATTACI
Hai domande? Scrivici un messaggio ora! Dopo aver ricevuto il tuo messaggio, informeremo sull'elaborazione della tua richiesta a tutto il team.