Imagine a world where car manufacturing transcends the limitations of traditional assembly lines. A world where vehicles are not just built, but intelligently designed and constructed based on specific needs. This transformative vision is precisely what the Sistema di produzione adattativo divergente (DAPS) promises.
DAPS is a revolutionary concept spearheaded by Divergent Technologies, a company determined to reshape the future of manufacturing. It’s not just a new machine; it’s an entire ecosystem – a software-hardware marriage that reimagines the design, engineering, and assembly processes from the ground up.
But how exactly does DAPS work? Buckle up, gearheads, because we’re about to delve into the fascinating world of this industry-disrupting technology.
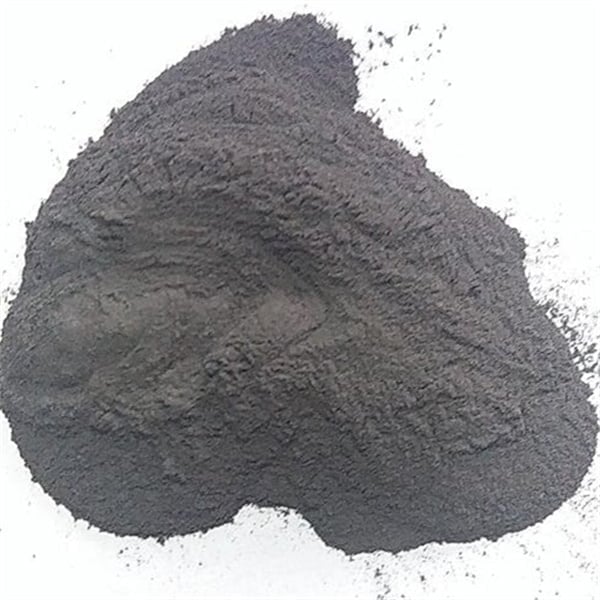
the Power of Sistema di produzione adattativo divergente (DAPS)
DAPS operates on a core principle: data-driven design and production. It seamlessly integrates several key components:
- AI-powered Generative Design: Imagine a design team on steroids. DAPS utilizes cutting-edge generative design software that acts as a digital architect. You feed in the desired functionalities and performance parameters – think lightweight yet high-strength car chassis. The software then analyzes a vast database of materials and structures, employing artificial intelligence to create an optimized design that perfectly meets your specifications. This eliminates the need for traditional, time-consuming design iterations.
- Novel Material Development: DAPS isn’t limited to existing materials. It paves the way for the exploration and creation of entirely new materials with superior properties. This opens doors for lighter, stronger, and even more environmentally friendly vehicles.
- Metal Additive Manufacturing (AM): Think 3D printing on an industrial scale. DAPS leverages metal AM to transform digital designs into physical reality. Laser beams precisely melt metal powders, layer by layer, to build complex structures with minimal waste. This allows for intricate designs that would be impossible with traditional manufacturing techniques.
- Automated Fixtureless Assembly: Say goodbye to the clunky assembly lines of yesteryear. DAPS employs a unique automated system that eliminates the need for traditional fixtures. Robots equipped with advanced vision systems can meticulously assemble components, ensuring precision and efficiency.
In essence, DAPS functions as a cohesive unit, transforming the entire production process from conception to completion. It’s a one-stop shop for intelligent and sustainable manufacturing.
Usable Metal Powders in DAPS
Now, let’s delve deeper into the heart of DAPS – the metal powders used to build these groundbreaking structures. The choice of metal powder significantly impacts the final product’s properties. Here’s a glimpse into some of the most commonly used metal powders within the DAPS ecosystem:
Polvere di metallo | Composizione | Proprietà | Caratteristiche | Applications in DAPS |
---|---|---|---|---|
Aluminum Alloys (AA2024, AA6061, etc.) | Aluminum with various alloying elements like copper, magnesium, and silicon | Lightweight, good corrosion resistance, high strength-to-weight ratio | Excellent for weight reduction in car components like frames and body panels | Offers a good balance of strength, weight, and affordability for various DAPS applications. However, strength can be lower compared to some other options. |
Titanium Alloys (Ti-6Al-4V, etc.) | Titanium with Aluminum and Vanadium | Elevato rapporto forza-peso, eccellente resistenza alla corrosione | Known for their exceptional strength and durability, ideal for high-performance components | Perfect for applications demanding exceptional strength and weight reduction, such as suspension components and safety cages. However, titanium powders can be more expensive compared to aluminum. |
Stainless Steel Powders (316L, 17-4PH, etc.) | Iron, Chromium, Nickel, with varying additional elements | High strength, good corrosion resistance, biocompatible | Offer a combination of strength, corrosion resistance, and biocompatibility | Valuable for components requiring strength and resistance to harsh environments, like exhaust systems and some medical implants used in DAPS-manufactured vehicles. |
Inconel Powders (IN625, etc.) | Nickel-Chromium alloy with various additions | High strength, excellent heat resistance, good corrosion resistance | Renowned for their ability to withstand extreme temperatures | Ideal for components exposed to high heat, such as engine parts and exhaust manifolds. However, Inconel powders are typically more expensive than other options. |
Leghe di nichel | Primarily Nickel with various alloying elements | High strength, excellent heat resistance, good corrosion resistance | Offer a range of properties depending on the specific alloy composition | Useful for applications requiring a combination of strength, heat resistance, and corrosion resistance, such as in high-performance engines and exhaust systems. |
Copper Alloys (CuSn4, etc.) | Copper with various alloying elements like tin, zinc, and nickel | High electrical conductivity, good heat conductivity, improved machinability | Offer superior electrical conductivity compared to pure copper | Invaluable for electrical components within DAPS-manufactured vehicles, such as wiring harnesses and busbars. However, the presence of tin can slightly reduce pure copper’s thermal conductivity. |
Tool Steels | Various alloy compositions based on iron, chromium, tungsten, and molybdenum | Very high strength, good wear resistance | Renowned for their ability to retain their hardness at high temperatures | Ideal for tooling used within the DAPS system itself, such as cutting tools and dies for metal AM processes. |
Magnesium Alloys | Magnesium with various alloying elements like aluminum, manganese, and zinc | Extremely lightweight, good strength-to-weight ratio | The lightest of all commonly used metal powders | Used for applications where weight reduction is paramount, such as in non-structural components within DAPS vehicles. However, magnesium can be susceptible to corrosion and requires careful handling. |
Cobalt Chrome Alloys (CoCr) | Cobalt and Chromium | High strength, excellent wear resistance, biocompatible | A popular choice for medical implants due to their biocompatibility | Can be utilized for components requiring a combination of strength, wear resistance, and biocompatibility, potentially for prosthetics or custom-designed medical devices integrated into DAPS vehicles. |
Refractory Metal Alloys | Primarily based on Tungsten, Molybdenum, or Tantalum | Extremely high melting points, good high-temperature strength | Can withstand incredibly high temperatures | Ideal for components exposed to extreme heat, such as parts within high-performance engines or rocket propulsion systems developed using DAPS. However, refractory metal powders are often very expensive and challenging to process. |
Important Note: This table presents a selection of some of the most common metal powders used within the DAPS ecosystem. As DAPS technology evolves, the range of compatible metal powders is constantly expanding. Additionally, researchers are actively exploring novel metal powder compositions with unique properties tailored for specific DAPS applications.
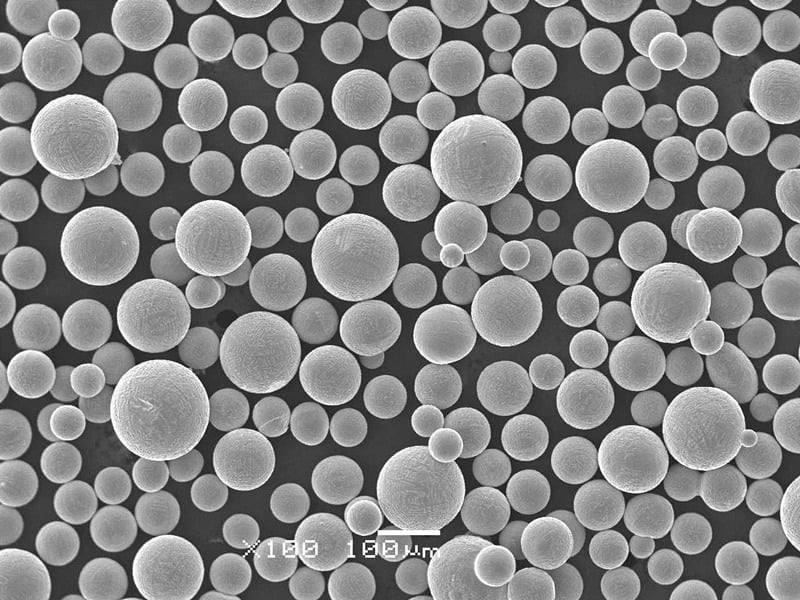
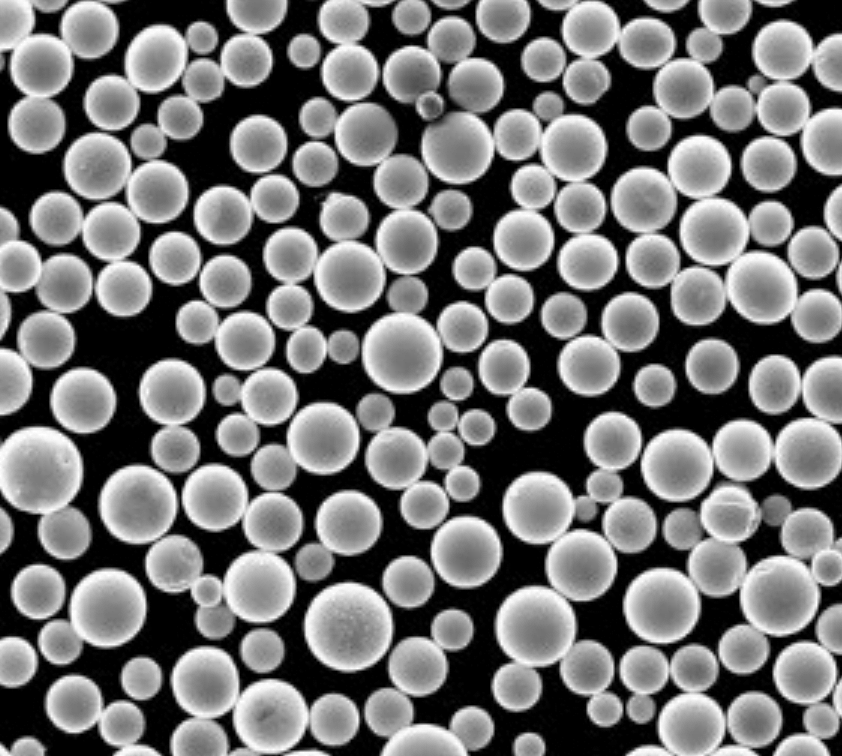
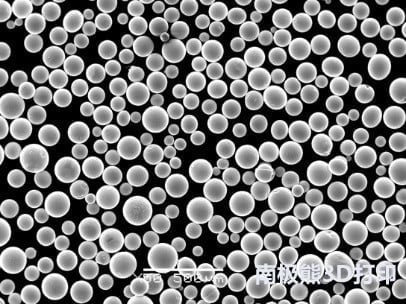
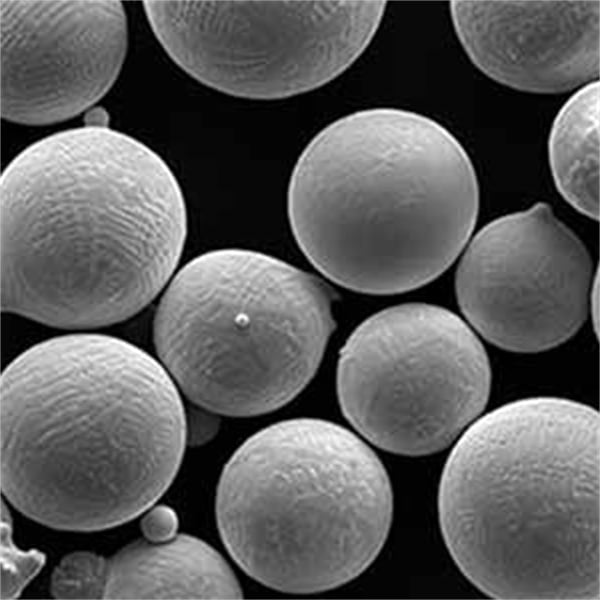
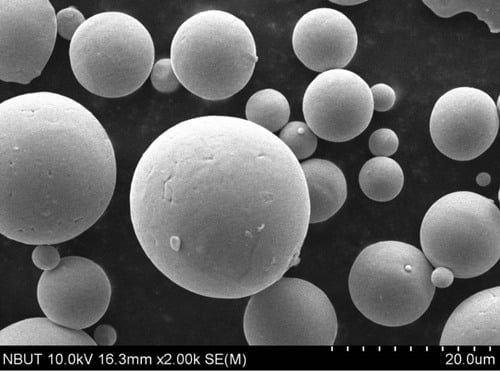
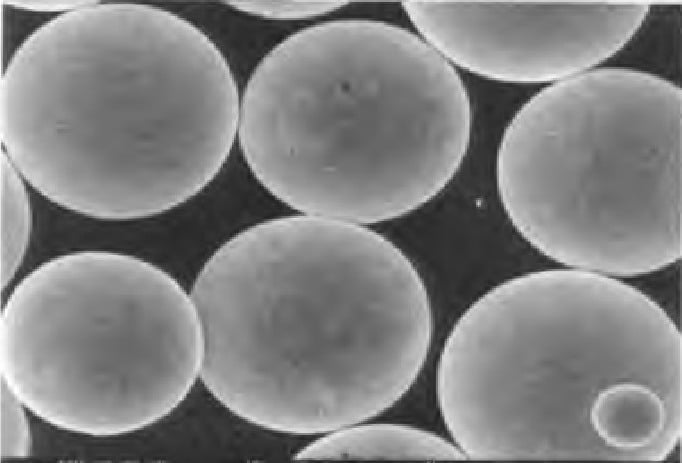
Selecting the Right Metal Powder
As you can see, the choice of metal powder in DAPS is crucial. It significantly impacts the final product’s weight, strength, heat resistance, corrosion resistance, and even biocompatibility. Here are some key factors to consider when selecting a metal powder for your DAPS project:
- Proprietà desiderate: What are the primary functionalities and performance requirements of the component you’re building? Does it need to be incredibly lightweight, withstand extreme temperatures, or resist corrosion? Identifying the essential properties will guide your metal powder selection.
- Strength vs. Weight: DAPS excels at creating lightweight yet strong structures. However, there’s always a trade-off. For instance, aluminum alloys offer a good balance, but titanium provides superior strength at the cost of increased weight.
- Heat Resistance: For components exposed to high temperatures, like engine parts, heat-resistant powders like Inconel become the clear choice.
- Resistenza alla corrosione: If the component will be exposed to harsh environments, stainless steel or copper alloys with improved corrosion resistance might be preferable.
- Biocompatibilità: For components intended for medical applications within DAPS vehicles, biocompatible materials like cobalt chrome alloys become a necessity.
- Costo: Metal powders can vary significantly in price. Consider the project’s budget and whether a slightly more expensive powder with superior properties justifies the cost increase.
Remember: DAPS allows for the exploration of entirely new materials. Don’t be afraid to push the boundaries and explore unconventional metal powder combinations to achieve groundbreaking results in your DAPS creations.
Advantages and Limitations of DAPS
DAPS boasts a compelling array of advantages that are revolutionizing the manufacturing landscape:
- Libertà di progettazione senza pari: DAPS empowers the creation of complex, lightweight structures that would be impossible with traditional manufacturing techniques. This opens doors for entirely new design possibilities and enhanced vehicle performance.
- Riduzione dei rifiuti: Metal AM, a core component of DAPS, is known for minimal material waste. DAPS takes this a step further by optimizing designs to minimize material usage from the very beginning.
- Personalizzazione di massa: DAPS readily adapts to produce customized vehicles or components tailored to specific needs. This allows for the creation of personalized experiences and potentially even on-demand manufacturing.
- Faster Time to Market: The streamlined design and production process of DAPS can significantly reduce the time it takes to bring a new product to market.
- Produzione sostenibile: DAPS’ focus on material optimization and reduced waste contributes to a more sustainable manufacturing approach.
- High Initial Investment: The DAPS system itself requires a significant upfront investment in hardware and software. This can be a barrier for smaller manufacturers or those just starting out.
- Selezione limitata di materiali: While DAPS is constantly expanding its compatible metal powder library, the selection is still not as vast as traditional manufacturing methods. This may limit the design possibilities for certain applications.
- Sfide di elaborazione: Metal AM, a core technology within DAPS, can be more complex and time-consuming compared to traditional techniques like casting or forging. This can impact production speed, especially for large-scale projects.
- Controllo qualità: Metal AM processes require stringent quality control measures to ensure the structural integrity of the final product. This can add complexity to the production process.
- Skilled Workforce: Implementing DAPS effectively necessitates a workforce with specialized skills in areas like generative design, metal AM, and automated systems.
Making the Call: Is DAPS Right for You?
DAPS presents a revolutionary approach to manufacturing, but it’s not a one-size-fits-all solution. Here are some questions to consider before diving into the DAPS world:
- Volume di produzione: If you require high-volume production runs, traditional methods might still be more efficient. DAPS shines in creating customized or low-volume, high-performance products.
- Bilancio: The upfront investment in DAPS technology can be significant. Carefully evaluate your budget and long-term goals to determine if DAPS offers a cost-effective solution for your needs.
- Product Complexity: DAPS excels at creating intricate, lightweight structures. If your product design demands such features, DAPS could be a perfect fit.
- Sustainability Goals: If reducing waste and adopting a more sustainable manufacturing approach are priorities, DAPS aligns perfectly with those objectives.
The Future of DAPS
DAPS represents a significant leap forward in the manufacturing industry. Its potential to create lighter, stronger, and more sustainable products is undeniable. As the technology matures, we can expect to see:
- Wider Material Selection: The range of compatible metal powders will continue to expand, opening doors for an even greater variety of DAPS applications.
- Faster Processing Speeds: Advancements in metal AM technology will lead to faster production times, making DAPS even more competitive for larger-scale projects.
- Costi ridotti: As DAPS technology becomes more widespread, the associated costs are likely to decrease, making it accessible to a broader range of manufacturers.
- Integration with AI and Robotics: DAPS will likely become even more intelligent, leveraging advanced AI and robotics for further optimization of design, production, and quality control processes.
- Revolutionizing Industries: The impact of DAPS won’t be limited to the automotive industry. We can expect to see its influence extend to aerospace, medical devices, and other sectors that demand high-performance, lightweight components.
In conclusion, DAPS is not just a new manufacturing system; it’s a paradigm shift. It empowers the creation of a new generation of products that are not only functional but also intelligent and sustainable. As DAPS continues to evolve, it has the potential to reshape the very foundation of how we design, build, and interact with the world around us.
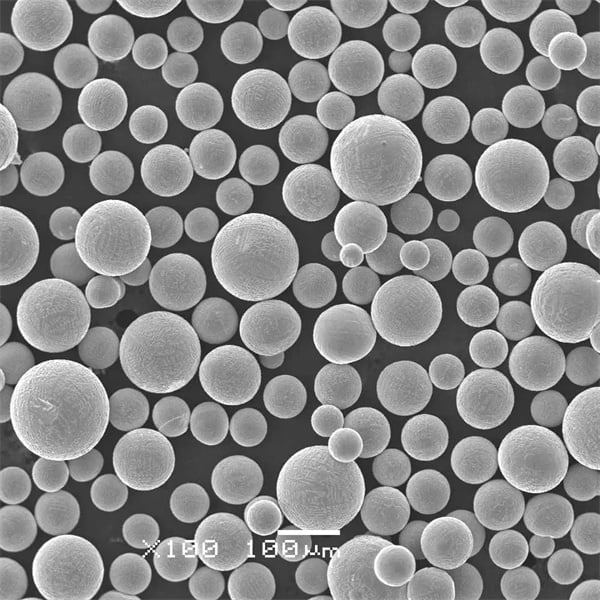
FAQ
Here are some of the most frequently asked questions regarding DAPS:
Domanda | Risposta |
---|---|
What are the main components of DAPS? | DAPS integrates AI-powered generative design, novel material development, metal additive manufacturing (AM), and automated fixtureless assembly. |
What are the benefits of using DAPS? | DAPS offers unmatched design freedom, reduced waste, mass customization potential, faster time to market, and a more sustainable manufacturing approach. |
What are the limitations of DAPS? | High initial investment, limited material selection compared to traditional methods, processing challenges inherent to metal AM, and the need for a skilled workforce are some of the current limitations. |
Is DAPS right for me? | Consider your production volume, budget, product complexity, and sustainability goals to determine if DAPS aligns with your needs. |
What is the future of DAPS? | We can expect a wider range of compatible metal powders, faster processing speeds, reduced costs, deeper integration with AI and robotics, and broader industry applications. |
Informazioni su 3DP mETAL
Categoria di prodotto
CONTATTACI
Hai domande? Scrivici un messaggio ora! Dopo aver ricevuto il tuo messaggio, informeremo sull'elaborazione della tua richiesta a tutto il team.