Have you ever dreamt of building something layer by layer, with molten metal as your paint and a robotic arm as your brush? Well, Deposizione diretta di energia (DED) makes this science fiction a reality. DED is a revolutionary 3D printing process that’s transforming manufacturing, allowing us to create complex metal structures with unmatched precision and flexibility.
This article delves into the fascinating world of DED, exploring its core principles, the advantages it offers over traditional methods, and the diverse applications it’s finding across various industries.
The Basic Principle of Directed Energy Deposition (DED)
Imagine a high-powered laser beam, like a supercharged version of a laser pointer, focused on a specific spot. Now, picture a metal wire or powder being continuously fed through a nozzle right next to the laser beam. As the laser beam hits the metal feedstock, it melts it instantly. This molten metal is then meticulously deposited onto a platform, layer by layer, following a digital blueprint. With each layer solidifying rapidly, the desired 3D structure takes shape.
Here’s a breakdown of the key components involved in DED:
- Fonte di energia: Lasers, electron beams, and plasma arcs are the most common energy sources used in DED. Each offers unique advantages and considerations, depending on the desired material and application.
- Feedstock Material: DED can handle a wide variety of metal alloys, including titanium, steel, aluminum, and nickel superalloys. The choice of material depends on the desired properties of the final product, such as strength, weight, and corrosion resistance.
- Delivery System: The nozzle plays a crucial role, guiding the feedstock material into the path of the energy source and ensuring precise deposition.
- Computer Control: The entire DED process is meticulously controlled by computer software. This software translates the 3D design file into a series of instructions, dictating the movement of the robotic arm, the energy source output, and the feedstock flow rate.
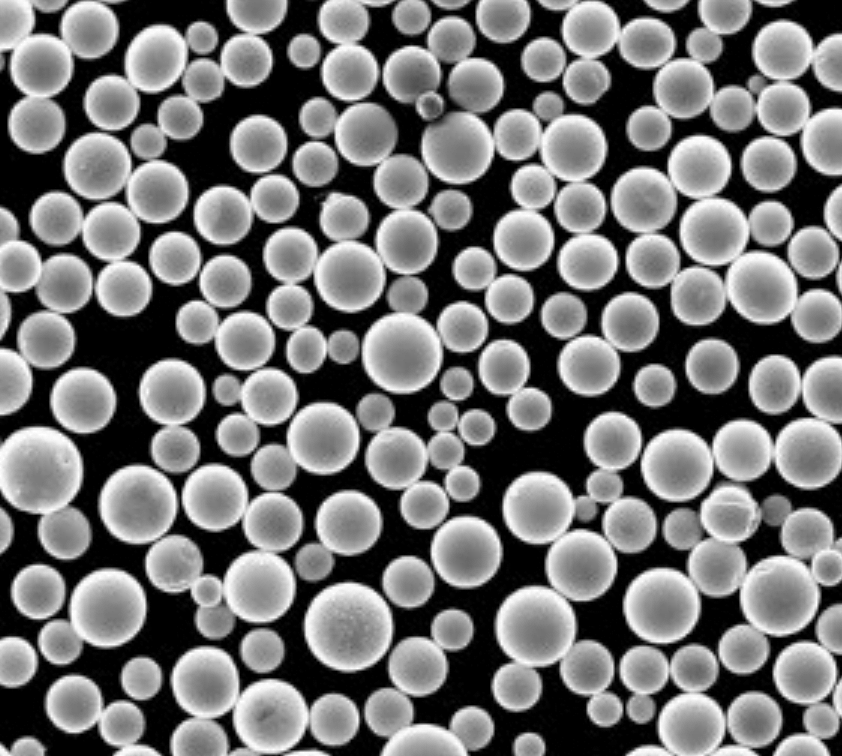
Advantages of Directed Energy Deposition (DED)
DED offers a compelling set of advantages compared to traditional manufacturing methods like machining and casting. Let’s explore some of the key benefits:
- Libertà di progettazione: Unlike subtractive techniques like machining, DED is additive. This means you’re not limited by the initial shape of a raw material block. DED allows you to create complex geometries with internal features and intricate details that would be impossible or highly expensive to achieve with traditional methods.
- Efficienza del materiale: DED boasts exceptional material efficiency. With precise deposition, there’s minimal waste compared to subtractive techniques that generate significant scrap metal. This translates to cost savings and a more environmentally friendly process.
- Strutture leggere: DED excels at creating lightweight yet strong structures. By strategically designing hollow internal features, DED parts can achieve exceptional strength-to-weight ratios, making them ideal for applications like aerospace and transportation.
- Prototipazione rapida: DED allows for rapid creation of functional prototypes directly from digital models. This eliminates the need for lengthy tooling processes, accelerating the design and development cycle.
- Produzione a forma di quasi rete: DED can produce parts very close to their final dimensions, minimizing the need for extensive post-processing steps like machining. This translates to faster production times and lower overall costs.
- Repair and Restoration: DED’s ability to precisely deposit material makes it ideal for repairing damaged metal components. This extends the lifespan of existing equipment and reduces the need for complete replacements.
Applications of Directed Energy Deposition (DED)
DED’s versatility is truly remarkable. Here’s a glimpse into some of the exciting applications across different industries:
- Aerospaziale: DED is being used to create lightweight and high-strength components for aircraft, such as brackets, wing ribs, and engine parts. This technology is helping to optimize fuel efficiency and performance in the aerospace industry.
- Settore automobilistico: DED is finding applications in creating custom parts for racing vehicles and for repairing damaged components in high-performance cars.
- Settore medico: DED is revolutionizing the medical field by enabling the creation of custom prosthetics and implants that are perfectly tailored to individual patients.
- Petrolio e gas: DED is used for repairing and cladding critical components in the oil and gas industry, extending their service life and enhancing their resistance to harsh environments.
- Utensili: DED can be used to create complex molds and dies with conformal cooling channels, improving efficiency and production speed in various manufacturing processes.
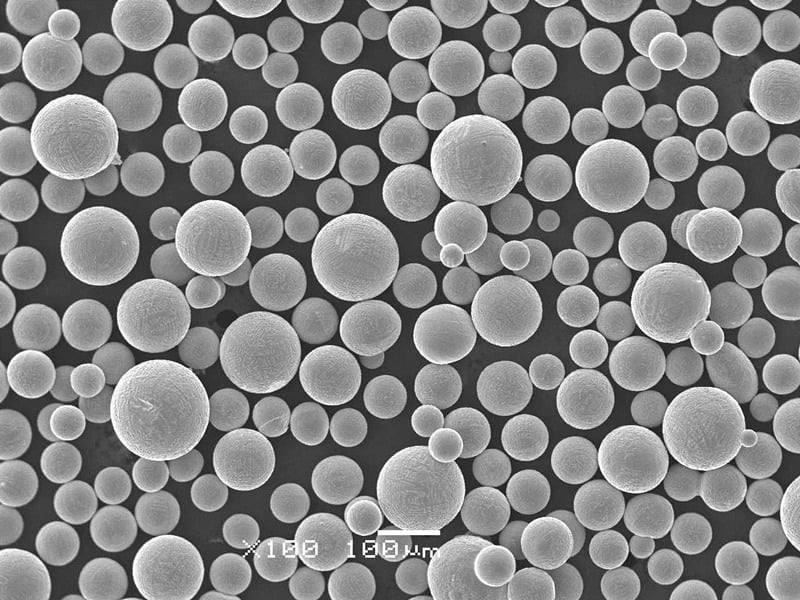
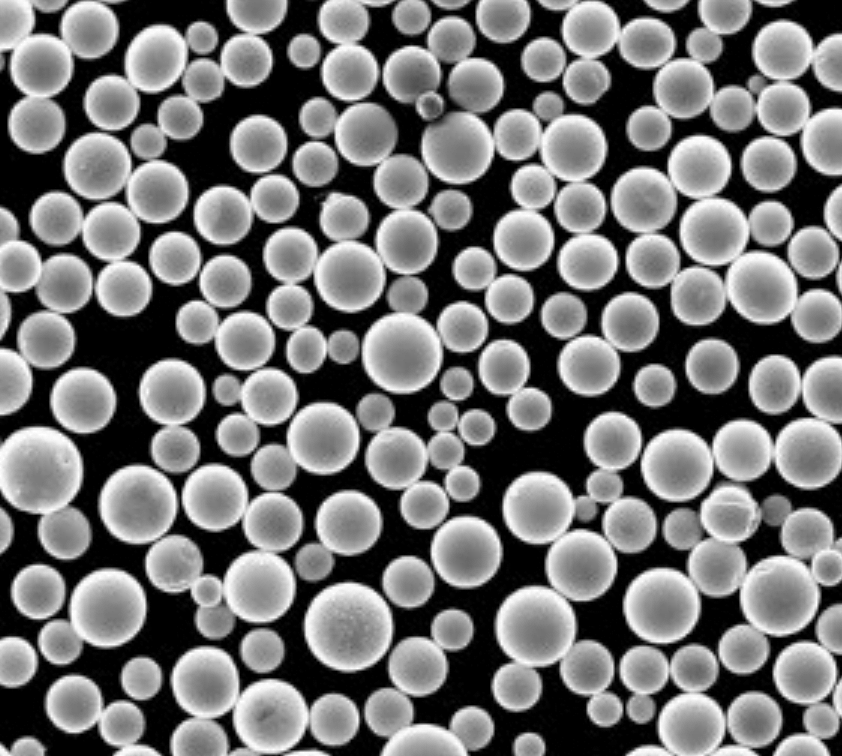
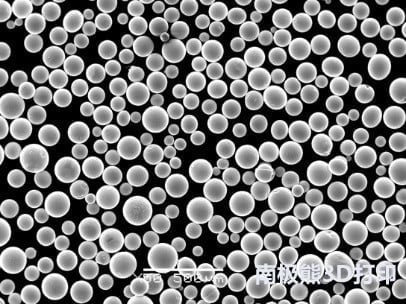
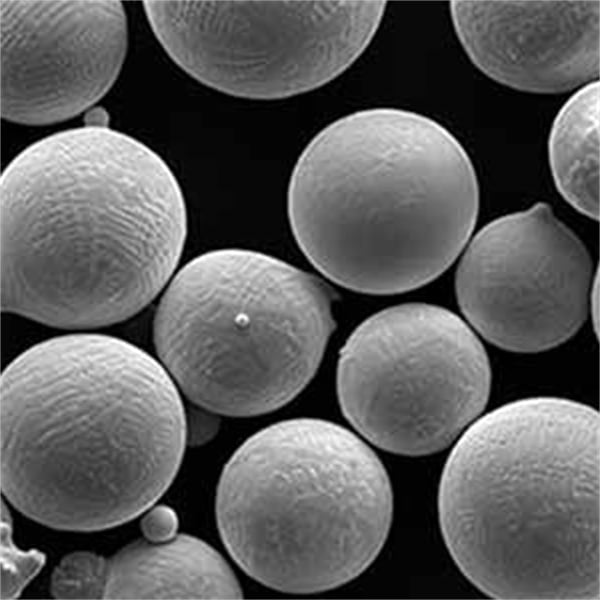
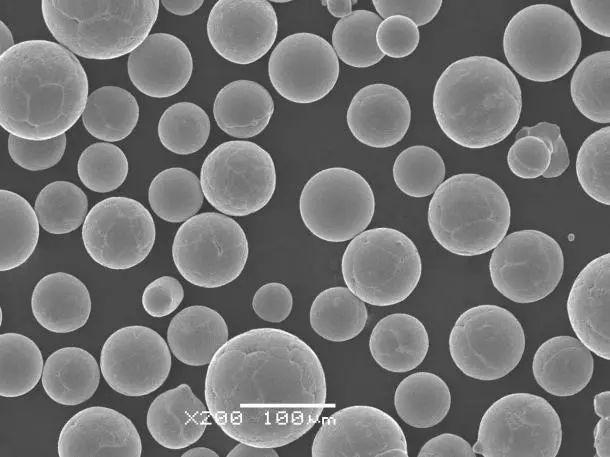
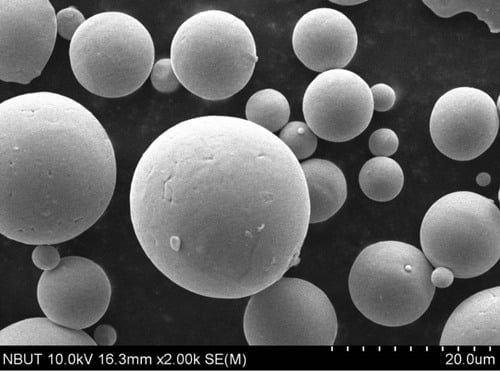
Considerations for DED
While DED offers numerous benefits, it’s essential to consider some key factors before diving into this technology.
Costo: DED machines can be expensive compared to traditional manufacturing equipment. However, the cost savings on material efficiency, design freedom, and reduced post-processing can make DED a compelling choice in the long run, especially for high-value, complex parts.
Material Properties and Considerations in DED
DED’s ability to work with a wide range of metals is a significant advantage. However, it’s crucial to understand how the DED process can affect the material properties of the final product compared to traditional methods. Here are some key considerations:
- Grain Structure: The rapid melting and solidification of metal in DED can result in a finer grain structure compared to cast or wrought metals. This finer grain structure can improve the mechanical properties like strength and ductility of the DED part. However, it can also make the material more susceptible to stress cracking in certain applications.
- Sollecitazione residua: The DED process involves localized heating and cooling, which can introduce residual stress within the part. Uncontrolled residual stress can lead to warping and distortion. DED processes often incorporate post-deposition heat treatments to manage residual stress and optimize the final properties of the part.
- Finitura superficiale: The surface finish of a DED part depends on several factors, including the energy source, feedstock material, and deposition parameters. DED parts can have a slightly rougher surface finish compared to machined parts. However, post-processing techniques like machining or polishing can be used to achieve a smoother surface finish if required by the application.
Different DED Techniques and their Applications
While the core principle of DED remains the same, there are several variations in the technology depending on the energy source used. Here’s a breakdown of the three main DED techniques:
- Laser DED (L-DED):
- Utilizes a high-powered laser beam as the energy source.
- Offers excellent control and precision, making it suitable for creating intricate geometries and features.
- Well-suited for applications requiring high-quality surface finishes, such as medical implants and aerospace components.
- Compared to other DED techniques, L-DED can be limited in deposition rate and may not be ideal for large-scale applications.
- Electron Beam DED (EB-DED):
- Employs a focused electron beam within a vacuum chamber for melting the feedstock material.
- Offers deeper penetration and higher deposition rates compared to L-DED.
- This makes EB-DED a good choice for creating thick-walled structures and repairing large components.
- However, the vacuum chamber requirement adds complexity and cost to the EB-DED process.
- Plasma Arc DED (PA-DED):
- Utilizes a high-temperature plasma arc as the energy source.
- Offers the fastest deposition rates among DED techniques, making it suitable for large-scale, high-throughput applications.
- PA-DED can also handle a wider range of metal feedstocks compared to L-DED and EB-DED.
- However, PA-DED can have a broader heat zone compared to other DED techniques, leading to a rougher surface finish and potentially larger grain size in the deposited material.
The Future of Directed Energy Deposition
DED is still a relatively young technology with immense potential for growth and innovation. Here are some exciting trends shaping the future of DED:
- Multi-Material DED: Researchers are exploring ways to combine different DED techniques or even integrate DED with other additive manufacturing processes to create multi-material parts with tailored properties in different regions. Imagine a lightweight aerospace component with a high-strength core and a corrosion-resistant outer layer – all fabricated in a single DED process.
- Hybrid DED Processes: The integration of DED with in-situ machining or monitoring technologies holds significant promise. Real-time process control and adaptive manufacturing capabilities would enable DED to produce high-quality parts with even greater precision and efficiency.
- Standardization and Qualification: As DED adoption grows, establishing standardized processes and qualification procedures will be crucial. This will ensure the reliability and repeatability of DED parts for critical applications in industries like aerospace and medical.
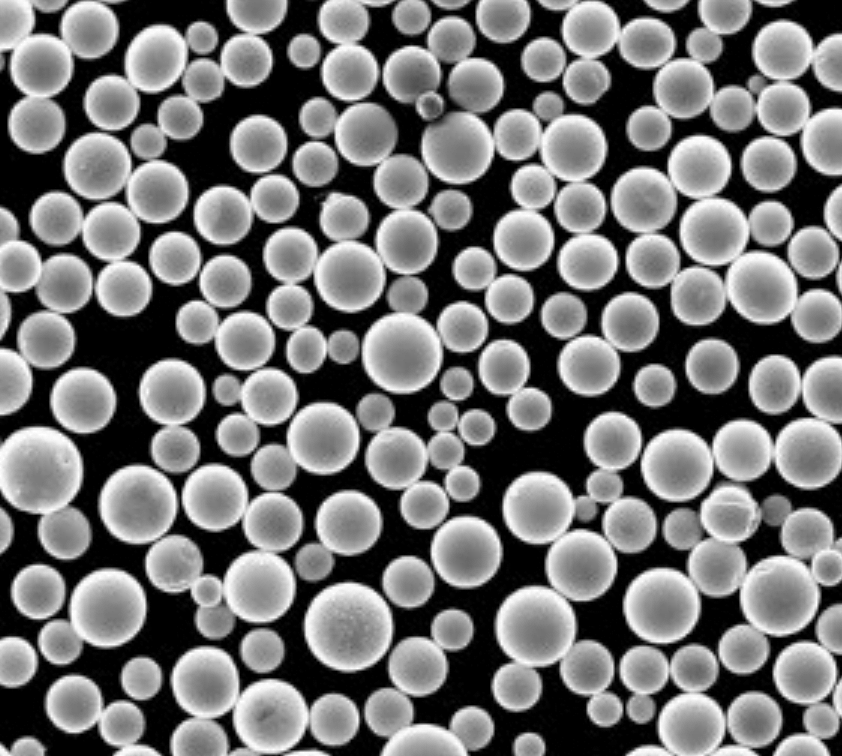
FAQ
Domanda | Risposta |
---|---|
What are the benefits of DED over traditional manufacturing methods? | DED offers design freedom, material efficiency, ability to create lightweight structures, rapid prototyping, near-net-shape manufacturing, and repair capabilities. |
What are some of the applications of DED? | DED is used in aerospace, automotive, medical, oil & gas, and tooling industries. |
What factors need to be considered when using DED? | Cost, material properties (grain structure, residual stress, surface finish), and choice of DED technique (Laser, Electron Beam, Plasma Arc) are important considerations. |
Informazioni su 3DP mETAL
Categoria di prodotto
CONTATTACI
Hai domande? Scrivici un messaggio ora! Dopo aver ricevuto il tuo messaggio, informeremo sull'elaborazione della tua richiesta a tutto il team.