Ever dreamt of building complex metal objects layer by layer, with unparalleled precision and material properties? Well, dream no more! Enter Electron Beam Melting (EBM), a revolutionary 3D printing technology that’s taking the manufacturing world by storm.
Imagine a high-powered electron beam, akin to a miniature sun, meticulously melting metal powder into a three-dimensional masterpiece. That’s the essence of EBM, offering a unique blend of design freedom, exceptional material strength, and near-net shape capabilities.
But before we delve deeper, let’s set the stage with a quick overview:
- What is EBM? EBM is an additive manufacturing process that uses a focused electron beam to melt metal powder bed-by-bed, building a 3D object from a digital design.
- What makes it special? EBM operates in a high vacuum, eliminating oxidation and ensuring exceptional part quality. It also excels at processing high-melting-point and reactive materials, pushing the boundaries of traditional manufacturing.
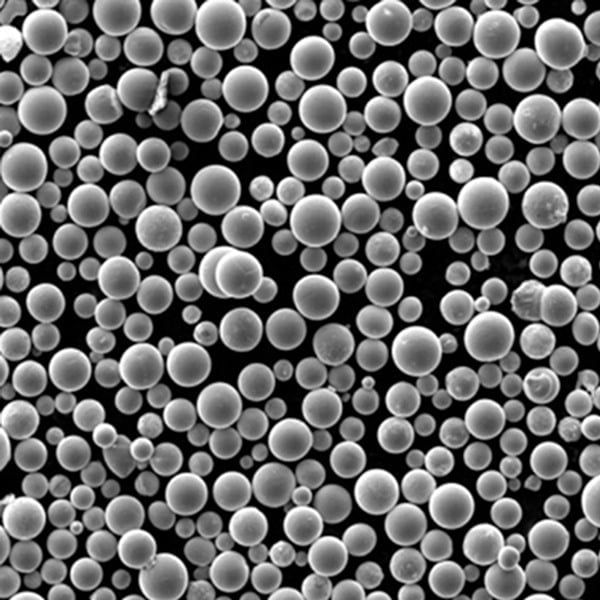
A Symphony of Metal Powders
The heart of the EBM process lies in the metal powders themselves. These finely-grained particles, each a tiny powerhouse of potential, come in a variety of flavors, offering a spectrum of properties for diverse applications. Let’s explore some of the most popular metal powders used in EBM:
Polvere di metallo | Composizione | Proprietà | APPLICAZIONI |
---|---|---|---|
Acciaio inox 316L | Fe (base), 16-18% Cr, 10-14% Ni, 2-3% Mo | Excellent corrosion resistance, high strength, biocompatible | Aerospace components, medical implants, chemical processing equipment |
Titanio Ti6Al4V | Ti (base), 6% Al, 4% V | Outstanding strength-to-weight ratio, good biocompatibility | Aerospace components, medical implants, sporting goods |
Inconel 625 | Ni (base), 20-24% Cr, 9% Fe, 5% Mo | Exceptional high-temperature performance, excellent corrosion resistance | Gas turbine components, heat exchangers, chemical processing equipment |
Cromo cobalto (CoCr) | Co (base), 27-30% Cr | Elevata resistenza all'usura, biocompatibile | Medical implants, dental prosthetics, cutting tools |
Molibdeno (Mo) | Mo (base) | High melting point, excellent thermal conductivity | High-temperature applications, molds, electrodes |
Tungsteno (W) | W (base) | Extremely high melting point, exceptional density | Ballistic armor, welding electrodes, radiation shielding |
Nichel (Ni) | Ni (base) | High ductility, good electrical conductivity | Electronic components, heat exchangers, brazing materials |
Rame (Cu) | Cu (base) | Eccellente conduttività termica ed elettrica | Heat sinks, electrical components, waveguides |
Beyond the Basics: Unveiling the Nuances of Metal Powders
Choosing the right metal powder for your EBM project is akin to selecting the perfect ingredients for a gourmet dish. Each powder boasts unique characteristics that influence the final product’s properties. Here’s a deeper dive into some key considerations:
- Distribuzione granulometrica: A balanced distribution of powder particle sizes ensures optimal packing density and promotes smooth melting during the EBM process. Imagine trying to build a sandcastle with only large pebbles – it wouldn’t hold its shape! The same principle applies to metal powders in EBM.
- Capacità di scorrimento Powders with good flowability enable a consistent and even deposition across the build platform, crucial for achieving precise geometries. Think of pouring sugar versus pouring flour – the sugar flows more readily, creating a smoother layer.
- Composizione chimica: Slight variations in the powder’s composition can significantly impact the final part’ s mechanical properties, such as strength, ductility, and corrosion resistance. Imagine baking a cake with too much sugar – it might be sweet, but the texture would be off!
- Morfologia della superficie: The shape and texture of the powder particles influence how well they pack together and interact with the electron beam. Think of building a house with smooth bricks versus jagged rocks – the smooth bricks create a stronger and more uniform structure.
A Spectrum of Applications: Where EBM Shines
The capabilities of EBM extend far beyond mere prototyping. This technology empowers manufacturers to create complex, high-performance metal parts for a wide range of industries:
- Aerospaziale: EBM excels at producing lightweight, high-strength components for aircraft and spacecraft, contributing to fuel efficiency and performance. Imagine creating a jet engine blade with intricate cooling channels – EBM makes it possible!
- Settore medico: EBM’s biocompatible metal powders pave the way for the creation of customized implants, such as hip replacements and dental prosthetics, that perfectly match a patient’s anatomy. Imagine a custom-made knee implant that integrates seamlessly with the bone, promoting faster healing and improved patient outcomes.
- Settore automobilistico: EBM is used to manufacture lightweight and high-strength components for race cars and performance vehicles, shaving off precious weight and enhancing overall performance. Imagine a car with pistons made from a special EBM-printed alloy, offering exceptional strength and reduced weight for a thrilling driving experience.
- Energia: EBM finds application in the production of complex components for gas turbines and other energy generation equipment, capable of withstanding extreme temperatures and pressures. Imagine turbine blades with intricate internal cooling channels, enabling more efficient energy conversion.
- Beni di consumo: The potential of EBM extends to the realm of high-end consumer goods, such as luxury watches and sporting equipment, offering unique design possibilities and exceptional material properties. Imagine a watch case with a complex, lattice-like structure, both lightweight and incredibly strong, thanks to EBM.
EBM vs. Other Metal Additive Manufacturing Processes
While EBM reigns supreme in specific areas, it’s essential to understand how it stacks up against other popular metal additive manufacturing (AM) techniques:
Processo | EBM | Fusione selettiva laser (SLM) | Binder Jetting (BJ) |
---|---|---|---|
Fonte di energia | Electron Beam | Laser Beam | Inkjet Printing Binder |
Ambiente sotto vuoto | Sì | Yes (Optional) | No |
Compatibilità dei materiali | High-melting point, reactive materials | Ampia gamma di metalli | Limited metal options |
Finitura superficiale | Eccellente | Bene | Rough (requires post-processing) |
Part Density | Near-net shape | Near-net shape | Lower density (requires infiltration) |
Strutture di supporto | Minimo | May be required | Necessary |
EBM emerges as a champion for high-performance metal parts, particularly for applications demanding exceptional material properties and intricate geometries. However, its reliance on a vacuum environment and compatibility with specific powders can make it a costlier option compared to SLM for certain applications. BJ offers a more budget-friendly alternative but often requires additional post-processing steps to achieve the desired density and surface finish.
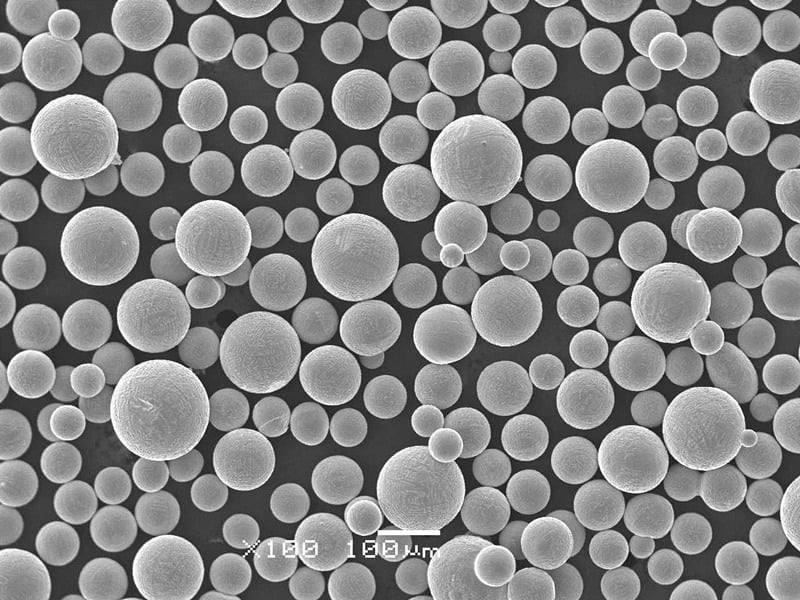
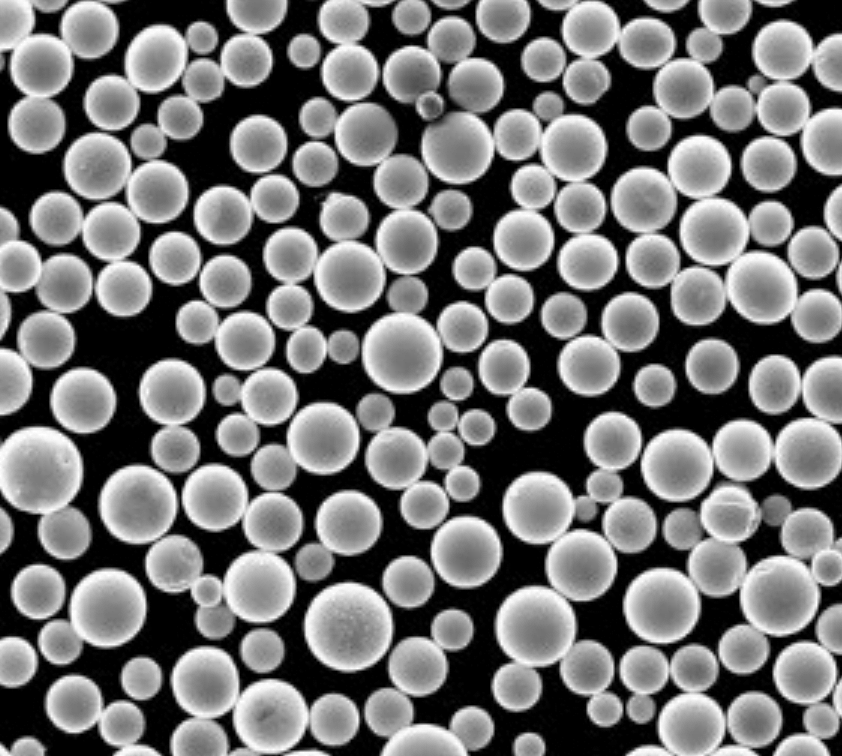
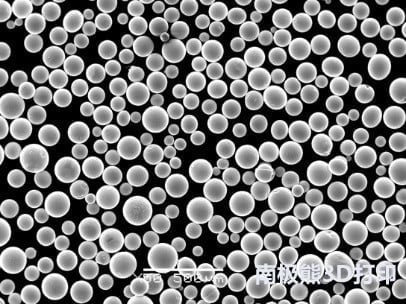
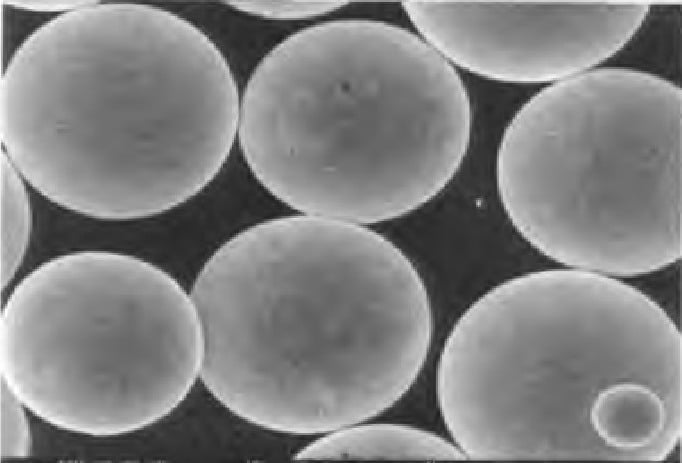
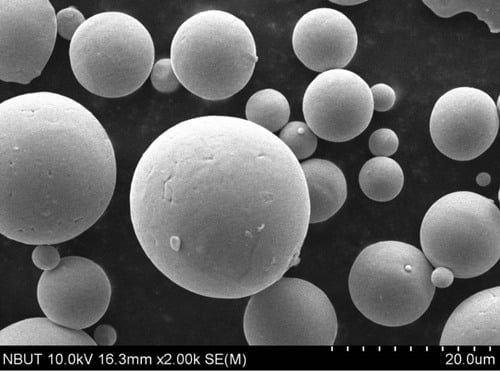
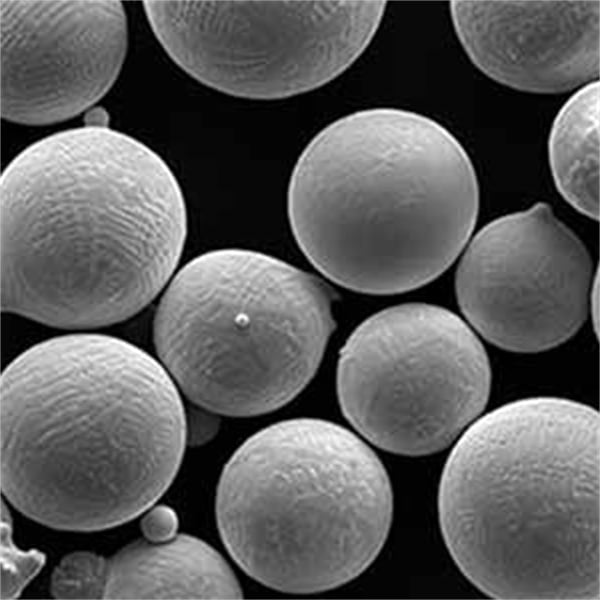
Il Vantaggios of EBM
Unveiling the Advantages of EBM:
- Proprietà eccezionali del materiale: EBM excels at producing parts boasting superior strength, high-temperature resistance, and excellent corrosion resistance, making it ideal for demanding applications. Imagine a rocket engine component that can withstand the scorching heat of combustion – EBM can deliver!
- Libertà di progettazione senza precedenti: EBM’s layer-by-layer approach unlocks the potential to create intricate geometries with internal channels, lattices, and other complex features that would be impossible with traditional manufacturing methods. Imagine a heat exchanger with a network of microchannels for optimal heat transfer – EBM makes it a reality!
- High-Vacuum Environment: The vacuum chamber in EBM eliminates the risk of oxidation, ensuring exceptional part quality and compatibility with reactive metals like titanium and tantalum. Imagine creating a medical implant that won’t corrode in the body – EBM provides the perfect solution!
- Near-Net Shape Manufacturing: EBM minimizes the need for extensive post-processing, reducing material waste and production time. Imagine creating a complex turbine blade with minimal machining requirements – that’s the power of EBM!
Acknowledging the Limitations of EBM:
- Costo: The complex setup and material requirements can make EBM a costlier option compared to some AM techniques. Imagine building a car – traditional manufacturing might be cheaper for mass production, while EBM could be ideal for creating a limited-edition, high-performance engine component.
- Velocità di costruzione: EBM has a slower build speed compared to some other AM processes. Imagine baking a cake – a conventional oven might be faster than a slow cooker, but the slow cooker can achieve a more even and consistent bake, similar to EBM’s focus on precision over speed.
- Selezione limitata di materiali: While EBM boasts compatibility with a wide range of metals, it might not be suitable for all materials, particularly those with low melting points. Imagine trying to 3D print a chocolate figurine with EBM – the chocolate would melt well before it could be built layer-by-layer!
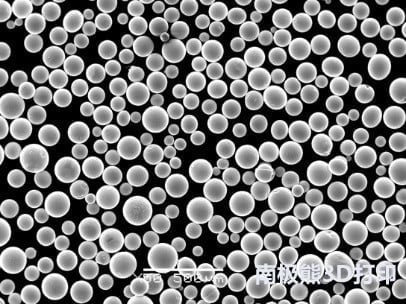
FAQ
Q: What are the limitations of EBM?
A: EBM can be a costlier option compared to some AM techniques, has a slower build speed, and might not be suitable for all materials, particularly those with low melting points.
Q: What types of metal powders can be used in EBM?
A: A wide range of metal powders can be used in EBM, including stainless steel, titanium alloys, Inconel, cobalt chrome, molybdenum, tungsten, nickel, and copper. The choice of powder depends on the desired properties of the final part.
Q: What are some of the applications of EBM?
A: EBM finds application in various industries, including aerospace, medical, automotive, energy, and consumer goods. It’s particularly well-suited for creating high-performance metal parts with intricate geometries and exceptional material properties.
Q: How does EBM compare to Selective Laser Melting (SLM)?
A: Both EBM and SLM are powder bed fusion AM processes, but they differ in energy source and vacuum environment. EBM uses an electron beam in a vacuum, while SLM uses a laser beam and can operate in a vacuum or inert gas atmosphere. EBM generally offers superior material properties and is better suited for reactive metals, while SLM might be a more cost-effective option for a wider range of materials.
Q: What is the future of EBM?
A: The future of EBM is bright! As technology advances, we can expect to see faster build speeds, lower costs, and the development of new metal powders that further expand the capabilities of this transformative technology. EBM is poised to play a significant role in the future of manufacturing, enabling the creation of complex, high-performance metal parts that were once unimaginable.
Informazioni su 3DP mETAL
Categoria di prodotto
CONTATTACI
Hai domande? Scrivici un messaggio ora! Dopo aver ricevuto il tuo messaggio, informeremo sull'elaborazione della tua richiesta a tutto il team.