Imagine crafting intricate components with exceptional strength, heat resistance, and corrosion defiance – all from a bed of fine powder. That’s the magic of high-performance metal powders, revolutionizing various industries with their unique properties and enabling the creation of game-changing parts. But what exactly are these wonder powders, and how do they transform metalworking? Buckle up, because we’re diving deep into the fascinating world of high-performance metal powders!
What are High-Performance Metal Powders?
High-performance metal powders are finely-grained metallic particles, meticulously crafted to possess superior mechanical properties compared to conventional metal powders. These exceptional powders are manufactured using various techniques like gas atomization or water atomization, resulting in consistent-sized, spherical particles with minimal impurities. This meticulous production process unlocks a treasure trove of advantages, making high-performance metal powders the material of choice for cutting-edge applications.
Key characteristics of high-performance metal powders:
- Forza eccezionale: Boasting superior tensile strength, yield strength, and fatigue resistance, these powders translate into components that can withstand immense physical stress. Think of them as the weightlifters of the metalworking world.
- Outstanding Heat Resistance: Unfazed by scorching temperatures, high-performance metal powders can handle extreme environments without succumbing to deformation or losing their integrity. Imagine jet engine components that perform flawlessly amidst fiery combustion.
- Maggiore resistenza alla corrosione: Highly resistant to rust, degradation, and chemical attacks, these powders are ideal for applications where environmental factors pose a constant threat. Picture marine components that perpetually battle the corrosive embrace of saltwater.
- Improved Flowability: The spherical shape and consistent size of these powders enable them to flow freely during additive manufacturing processes, ensuring smooth and efficient production. It’s like having perfectly round ball bearings for metal – minimal friction, maximum precision.
- Potenziale di leggerezza: Depending on the chosen metal, high-performance powders can offer weight reduction benefits compared to traditional metals. This translates to lighter, more fuel-efficient components in aerospace and automotive applications.
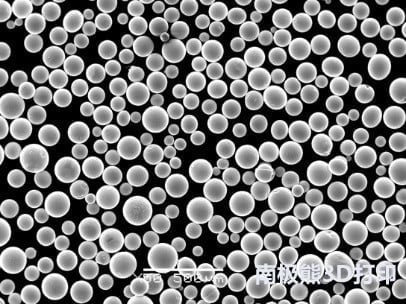
Specifico Polveri metalliche ad alte prestazioni
Now, let’s delve into the specific types of high-performance metal powders that are making waves across industries:
1. Nickel-based Alloy Powders:
- Inconel 625: An industry workhorse, Inconel 625 offers exceptional resistance to high temperatures, oxidation, and corrosion. It’s a popular choice for applications in gas turbines, heat exchangers, and chemical processing equipment.
- Inconel 718: This nickel-chromium alloy boasts high strength, good weldability, and excellent machinability. Think high-performance shafts, gears, and aerospace components that demand both robustness and intricate design.
2. Titanium-based Alloy Powders:
- Ti-6Al-4V (Grade 23): A dominant player in the titanium powder arena, Grade 23 offers a good balance of strength, ductility, and weight savings. It’s widely used in aerospace components, medical implants, and sporting goods seeking a blend of performance and weight reduction.
- Ti-6Al-4V (Grade 25): This variation boasts higher strength compared to Grade 23, making it ideal for applications demanding maximum structural integrity. Imagine stronger aircraft parts or medical implants that need to handle significant loads.
3. Stainless Steel Powders:
- 316L Stainless Steel: Offering excellent corrosion resistance and biocompatibility, 316L is a go-to choice for medical implants, chemical processing equipment, and marine applications.
- 17-4 PH Stainless Steel: Known for its high strength and good hardness after heat treatment, 17-4 PH is a versatile powder used in gears, shafts, and aerospace components requiring both durability and dimensional stability.
4. Aluminum Powders:
- AlSi10Mg: This aluminum-silicon-magnesium alloy powder offers a good balance of strength, ductility, and castability. It’s commonly used for lightweight prototypes, automotive components, and electronic enclosures.
- Scalmalloy: A unique aluminum-scandium alloy, Scalmalloy boasts exceptional strength-to-weight ratio and excellent fatigue resistance. Imagine groundbreaking advances in aerospace structures or high-performance bicycles where every ounce counts.
5. Refractory Metal Powders:
- Tungsten (W): Renowned for its incredibly high melting point and outstanding heat resistance, tungsten powder is a champion in high-temperature applications like furnace components, electrodes, and rocket engine nozzles.
- Molibdeno (Mo): Another high-temperature hero, molybdenum powder offers excellent strength and good electrical conductivity.
Applications of High-Performance Metal Powders
High-performance metal powders aren’t just a collection of fancy particles; they’re the building blocks for a revolution in various industries. Here’s a glimpse into the exciting applications where these wonder powders are flexing their muscles:
Fabbricazione additiva (AM): Also known as 3D printing, AM has become a playground for high-performance metal powders. Their exceptional flowability and precise particle size make them ideal for intricate layer-by-layer construction of complex components. Imagine creating jet engine parts with intricate cooling channels or lightweight medical implants with customized porosity for better bone ingrowth – all thanks to high-performance metal powders.
Stampaggio a iniezione di metallo (MIM): This cost-effective process utilizes high-performance metal powders mixed with a binder to create precise near-net-shape components. After shaping and debinding, the parts are sintered, resulting in intricate metal parts with good dimensional accuracy and complex geometries. Think of intricate gears, microfluidic devices, and small firearm components produced efficiently through MIM with high-performance metal powders.
Spruzzatura termica: This technique involves melting high-performance metal powders using a heat source like a plasma torch and then spraying them onto a substrate. This creates a protective coating that enhances the substrate’s properties, like wear resistance, corrosion resistance, or thermal resistance. Picture turbine blades shielded from extreme heat and wear, or oil drilling equipment fortified against harsh environments – all through the magic of thermal spraying with high-performance metal powders.
Cladding: This process involves bonding a layer of high-performance metal powder onto a base metal using techniques like welding or brazing. This creates a composite material with the desired properties of both the base metal and the cladding layer. Imagine pressure vessels with a corrosion-resistant inner layer made of high-performance metal powder cladding or nuclear reactor components shielded with a special cladding layer for enhanced safety.
Beyond these core applications, high-performance metal powders are constantly being explored for innovative uses in industries like:
- Aerospaziale: Lighter, stronger aircraft components for improved fuel efficiency and performance.
- Settore automobilistico: Weight reduction in car parts for better fuel economy and handling.
- Settore medico: Biocompatible implants with tailored properties for enhanced patient outcomes.
- Energia: Durable and high-temperature resistant components for power generation equipment.
- Elettronica: Heat sinks and other thermal management components for high-performance devices.
The potential applications of high-performance metal powders are truly boundless, and as technology continues to evolve, we can expect to see even more groundbreaking advancements in various sectors.
Vantaggi di Polveri metalliche ad alte prestazioni
There’s a reason why high-performance metal powders are creating a buzz in the manufacturing world. Let’s delve into the key advantages that make them so desirable:
- Libertà di progettazione senza pari: Unlike traditional subtractive manufacturing techniques, high-performance metal powders enable the creation of complex, near-net-shape components with intricate geometries. This opens doors for innovative designs that were previously impossible. Imagine designing a lightweight heat exchanger with internal channels that optimize heat transfer – a feat readily achievable with high-performance metal powders in AM.
- Proprietà del materiale superiori: As mentioned earlier, these powders boast exceptional strength, heat resistance, and corrosion resistance. This translates into components that can perform flawlessly in demanding environments, pushing the boundaries of what’s possible. Picture a jet engine component that endures scorching temperatures and intense pressure for extended periods, all thanks to the exceptional properties of high-performance metal powders.
- Weight Reduction: Certain high-performance metal powders, like titanium and aluminum alloys, offer significant weight savings compared to conventional metals. This is a game-changer for industries like aerospace and automotive, where every pound shaved off translates to improved fuel efficiency and performance. Imagine an aircraft with lighter, stronger components that require less fuel to fly further, all thanks to the magic of high-performance metal powders.
- Riduzione dei rifiuti: Unlike traditional manufacturing processes that generate significant scrap material, AM with high-performance metal powders minimizes waste. This translates to a more sustainable and environmentally friendly production process. Picture a future where intricate components are built layer-by-layer with minimal material wastage, a hallmark of high-performance metal powders in AM.
- Personalizzazione di massa: High-performance metal powders make it easier to produce customized components in small batches. This allows for rapid prototyping, faster product development cycles, and the creation of personalized medical implants tailored to individual patients. Imagine creating a custom-designed medical implant with biocompatible high-performance metal powder, perfectly matching a patient’s specific needs.
These advantages paint a compelling picture of why high-performance metal powders are revolutionizing the manufacturing landscape. As technology advances and production costs decrease, we can expect even wider adoption of these wonder powders across various industries.
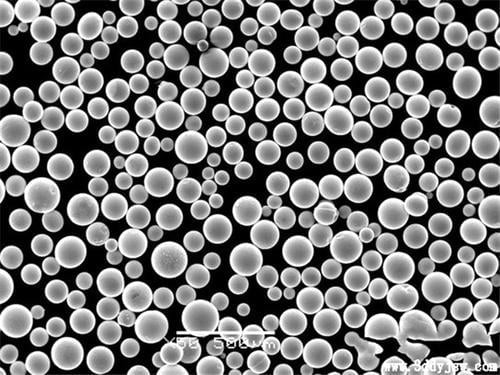
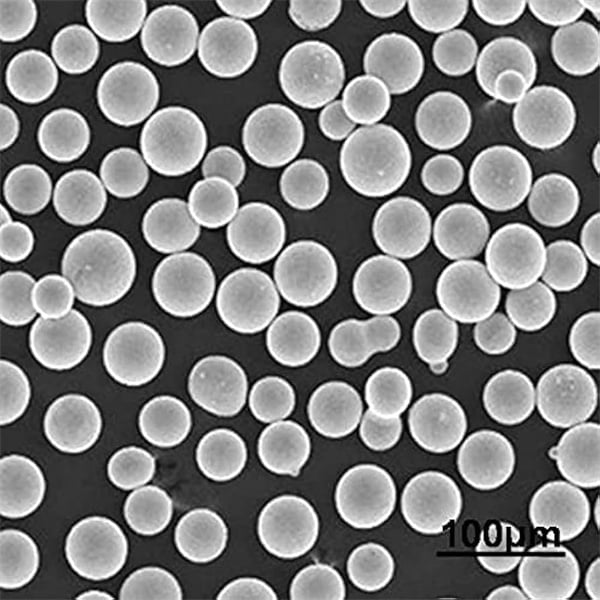
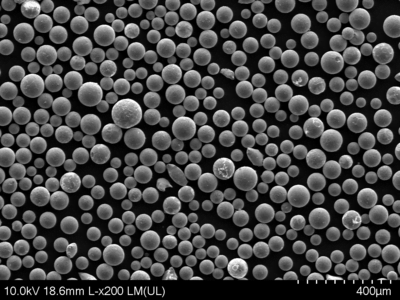
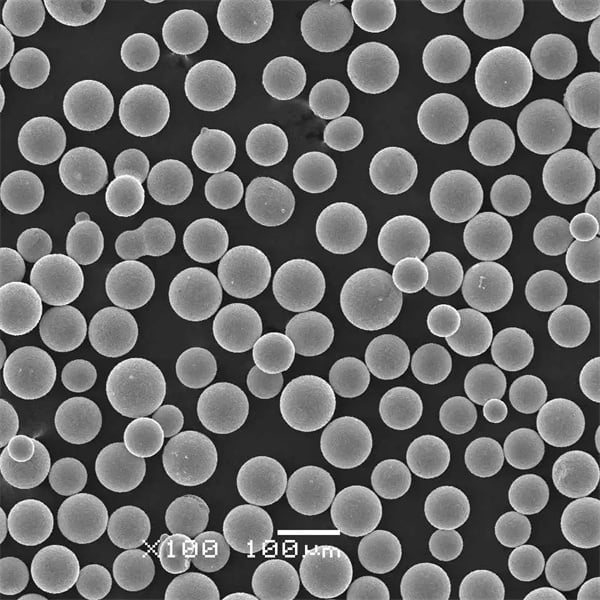
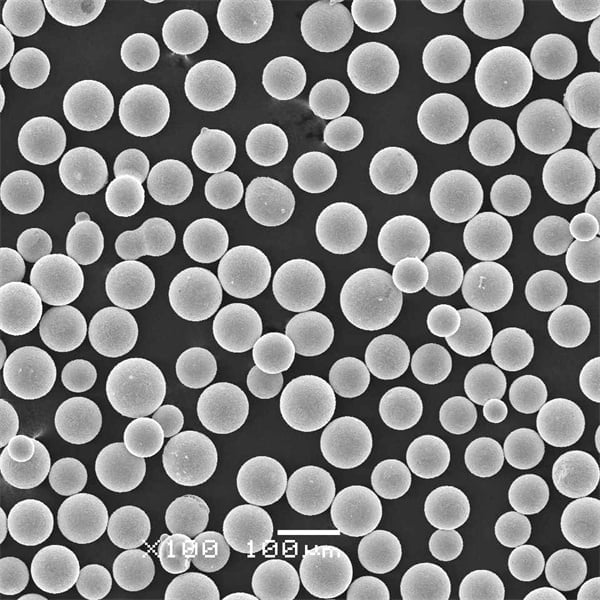
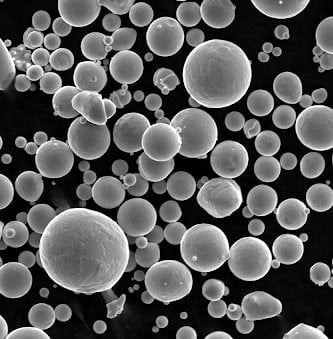
Svantaggi di Polveri metalliche ad alte prestazioni
While high-performance metal powders offer a plethora of advantages, it’s important to acknowledge the potential drawbacks associated with them:
- Costo elevato: Currently, high-performance metal powders can be significantly more expensive than conventional metal powders. This is due to the complex production processes involved and the relatively limited production volume. Imagine a scenario where a manufacturer needs to produce a large batch of components; the high cost of high-performance metal powders might make them a less viable option compared to traditional materials.
- Complessità del processo: Additive manufacturing processes utilizing high-performance metal powders can be intricate and require specialized equipment and expertise. This can pose a challenge for smaller companies or those without the necessary infrastructure in place. Think of a small machine shop; adopting high-performance metal powders in their workflow might require significant investment in new equipment and training for their staff.
- Selezione limitata di materiali: While the selection of high-performance metal powders is expanding, it’s still not as vast as that of conventional metals. This can restrict design options in certain applications where specific material properties are crucial. Imagine an engineer designing a high-pressure vessel; they might not find a readily available high-performance metal powder that perfectly meets all the pressure and corrosion resistance requirements.
- Rugosità superficiale: Components produced with high-performance metal powders through AM processes can sometimes exhibit a rougher surface finish compared to those made with traditional techniques. This might necessitate additional post-processing steps like machining or polishing, adding to the overall production time and cost. Picture a medical implant; a rough surface finish could potentially hinder its biocompatibility or functionality, requiring additional polishing steps before implantation.
- Quality Control Challenges: Ensuring consistent quality in high-performance metal powders and the final components can be more challenging compared to traditional manufacturing methods. This necessitates robust quality control procedures throughout the production process. Imagine a scenario where a batch of high-performance metal powder has slight inconsistencies; this could lead to variations in the final component’s properties, demanding stricter quality control measures.
Despite these limitations, the advantages of high-performance metal powders are undeniable. As production costs decrease, process knowledge expands, and material selection widens, we can expect these challenges to be gradually mitigated. Researchers and manufacturers are constantly innovating to overcome these limitations and unlock the full potential of high-performance metal powders.
Specifiche, dimensioni, gradi e standard
High-performance metal powders come in a variety of specifications, sizes, grades, and adhere to specific standards. Understanding these nuances is crucial for selecting the most suitable powder for a particular application. Here’s a breakdown of the key factors to consider:
Specifiche:
- Composizione chimica: The exact composition of the metal powder, including the main element and any alloying elements, significantly impacts its properties. For instance, the presence of chromium in Inconel 625 powder enhances its high-temperature oxidation resistance.
- Distribuzione granulometrica: The size and distribution of the metal powder particles significantly influence flowability, packing density, and the final component’s properties. A tighter particle size distribution ensures better packing density and potentially stronger components in AM processes.
- Morfologia: The shape of the metal powder particles also plays a role. Spherical particles typically offer better flowability and packing density compared to irregularly shaped particles.
Taglie:
High-performance metal powders are available in a range of sizes, typically measured in micrometers (µm). The choice of size depends on the specific application and the desired properties of the final component. For instance, finer powders might be preferred for intricate AM applications requiring high resolution, while coarser powders might be suitable for processes like thermal spraying.
Gradi:
Similar to conventional metals, high-performance metal powders come in various grades. These grades can define factors like oxygen content, impurity levels, or specific mechanical properties. The selection of the appropriate grade hinges on the intended application and the desired performance characteristics.
Standard:
Several international standards govern the production and quality of high-performance metal powders. These standards ensure consistency and quality across different manufacturers. Some prominent standards include ASTM International (ASTM) and the International Organization for Standardization (ISO). Following these standards helps ensure the quality and performance of the chosen high-performance metal powder.
Here’s a table summarizing the key considerations for specifications, sizes, grades, and standards:
Fattore | Descrizione | Esempio |
---|---|---|
Composizione chimica | The exact elements and their proportions in the metal powder. | Inconel 625 powder containing nickel, chromium, and other elements for high-temperature performance. |
Distribuzione granulometrica | The spread of particle sizes within the powder. | A narrow particle size distribution for better packing density in AM. |
Morfologia | The shape of the metal powder particles. | Sferica |
Fornitori e prezzi
Sourcing high-performance metal powders requires careful consideration of several factors, including supplier reputation, product quality, and pricing. Here’s a glimpse into the supplier landscape and pricing considerations:
Fornitori:
Several established and emerging players supply high-performance metal powders. Some prominent names include:
- AM powders: APEX Additive Technologies, Höganäs AB, Carpenter Additive Powder Products
- Metal Injection Molding (MIM) powders: Höganäs AB, Sandvik Hyperion, AMETEK Engineered Materials
- Thermal Spraying powders: Oerlikon Metco, Praxair Surface Technologies, SLM Solutions
Costi:
The pricing of high-performance metal powders can vary depending on several factors, including:
- Material: Exotic or rare earth metals will typically command a higher price compared to common metals.
- Caratteristiche della polvere: Finer powders, tighter size distributions, or higher purity grades will generally be more expensive.
- Volume: Larger quantities typically benefit from economies of scale and lower per-unit costs.
Here’s a table showcasing a range of high-performance metal powders, their typical sizes, and estimated pricing to provide a general sense of costs (please note that pricing can fluctuate based on market conditions and specific suppliers):
Polvere di metallo | Dimensioni (μm) | Estimated Price Range (per kg) |
---|---|---|
Inconel 625 | 15-45 | $200 – $400 |
Ti-6Al-4V (grado 23) | 45-100 | $100 – $250 |
Acciaio inox 316L | 15-45 | $50 – $100 |
AlSi10Mg | 25-75 | $20 – $40 |
Tungsteno (W) | 50-150 | $150 – $300 |
It’s crucial to remember that these are just estimated ranges, and actual pricing can vary based on the factors mentioned earlier. For accurate quotes, contacting potential suppliers directly is recommended.
Pro e contro di Polveri metalliche ad alte prestazioni
Pro:
- Libertà di progettazione senza pari: Enables creation of complex, near-net-shape components.
- Proprietà del materiale superiori: Exceptional strength, heat resistance, and corrosion resistance.
- Weight Reduction: Potential for lighter components in aerospace and automotive applications.
- Riduzione dei rifiuti: Minimizes waste compared to traditional subtractive manufacturing.
- Personalizzazione di massa: Facilitates production of customized components in small batches.
Contro:
- Costo elevato: Currently more expensive than conventional metal powders.
- Complessità del processo: Requires specialized equipment and expertise for AM processes.
- Selezione limitata di materiali: Selection is not as vast as conventional metals yet.
- Rugosità superficiale: Components might require additional post-processing for a smooth finish.
- Quality Control Challenges: Ensuring consistent quality requires robust procedures.
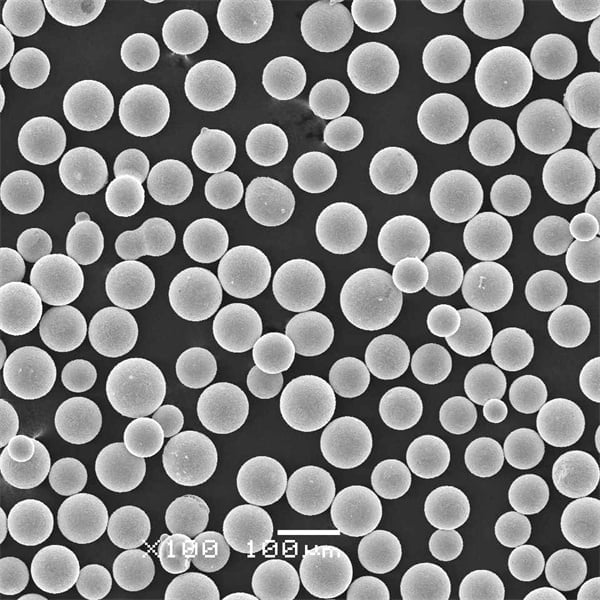
The Future of High-Performance Metal Powders
The future of high-performance metal powders is brimming with exciting possibilities. Here are some trends to watch out for:
- Reduced Production Costs: As production volumes increase and technology advances, we can expect the cost of high-performance metal powders to decrease, making them more accessible to a wider range of applications.
- Ampliamento della selezione dei materiali: Researchers are constantly developing new high-performance metal powder alloys with unique properties, catering to an even broader spectrum of applications.
- Advancements in AM Technology: Continued advancements in AM processes will unlock even greater design freedom and improve the efficiency of using high-performance metal powders.
- Produzione sostenibile: The minimal waste associated with AM using high-performance metal powders aligns well with the growing focus on sustainable manufacturing practices.
- Emerging Applications: We can expect to see high-performance metal powders explored in novel applications across various industries, further revolutionizing how we design and manufacture components.
High-performance metal powders are more than just a material; they’re a gateway to a future of innovation. As these wonder powders continue to evolve and become more accessible, we can expect to witness significant advancements across various sectors, from aerospace and automotive to medicine and energy. The possibilities are truly limitless!
FAQ
Q: What are the environmental benefits of using high-performance metal powders?
A: Compared to traditional manufacturing methods, AM using high-performance metal powders generates minimal waste. Additionally, the potential for weight reduction in components using these powders can lead to improved fuel efficiency in vehicles and aircraft, thereby reducing environmental impact.
Q: Are high-performance metal powders safe to handle?
A: The safety of handling high-performance metal powders depends on the specific material composition. Some metal powders, like nickel-based alloys, can be irritating to the skin and respiratory system. Here are some general safety precautions to consider:
- Dispositivi di protezione individuale (DPI): Always wear appropriate PPE like gloves, safety glasses, and a respirator when handling high-performance metal powders to minimize inhalation or skin contact.
- Ventilazione adeguata: Ensure adequate ventilation in the workspace to prevent dust accumulation.
- Good Hygiene Practices: Wash hands thoroughly after handling the powders and avoid eating or drinking in the work area.
- Safe Disposal: Follow recommended disposal procedures for the specific metal powder to avoid environmental contamination.
It’s crucial to consult the Safety Data Sheet (SDS) for the specific high-performance metal powder you’re working with to understand its unique hazards and proper handling procedures.
Q: Can high-performance metal powders be recycled?
A: Yes, high-performance metal powders can potentially be recycled using various techniques. Here are two common methods:
- Powder Recycling: Unoperated or recycled powder from AM processes can potentially be reused after proper sieving and analysis to ensure it meets quality specifications.
- Metal Reclamation: Components made from high-performance metal powders can potentially be recycled using traditional metal recycling techniques after their service life.
The feasibility of recycling high-performance metal powders depends on various factors like the specific material, contamination levels, and available recycling infrastructure. However, as sustainability becomes a growing priority, research and development in high-performance metal powder recycling are gaining momentum.
Q: What are some of the emerging applications for high-performance metal powders?
A: Beyond the established applications in aerospace, automotive, and medical sectors, high-performance metal powders are being explored in various innovative ways:
- Bioprinting: Researchers are investigating the use of biocompatible metal powders for 3D printing of human tissues and organs, potentially revolutionizing regenerative medicine.
- Elettronica: High-performance metal powders with unique electrical properties might be used to create novel electronic components with improved performance and miniaturization.
- Energy Storage: Metal powders are being explored for the development of next-generation battery technologies with enhanced energy density and efficiency.
- Costruzione: High-performance metal powders could potentially be used to create lightweight and strong building components for sustainable infrastructure projects.
These are just a few examples, and as research and development efforts continue, we can expect to see even more groundbreaking applications emerge for high-performance metal powders across various industries.
Informazioni su 3DP mETAL
Categoria di prodotto
CONTATTACI
Hai domande? Scrivici un messaggio ora! Dopo aver ricevuto il tuo messaggio, informeremo sull'elaborazione della tua richiesta a tutto il team.