Imagine building intricate metal parts layer by layer, with exceptional strength and versatility. That’s the magic of low-alloy steel powders, a revolutionary material taking the world of additive manufacturing (AM) by storm. But what exactly are these fine, metallic grains, and how do they transform into high-performance components? Buckle up, because we’re diving deep into the fascinating world of low-alloy steel powders!
An Overview: Unveiling the Powerhouse Material
Low-alloy steel powders are finely ground iron-based materials with small, carefully measured additions of elements like chromium, manganese, molybdenum, nickel, silicon, and carbon. These alloying elements play a crucial role in fine-tuning the mechanical properties of the final product. Compared to traditional wrought steels, low-alloy steel powders offer several advantages:
- Libertà di progettazione: AM allows for intricate geometries that would be impossible with conventional techniques. Think of lightweight components with internal channels or complex lattice structures – low-alloy steel powders make these dreams a reality.
- Produzione a forma di quasi rete: This fancy term means minimal material waste. With AM, you build the part layer by layer, using only the necessary amount of powder.
- Forza superiore: Low-alloy steel powders can be processed to achieve excellent strength-to-weight ratios, making them ideal for applications demanding high performance.
But before we delve into the nitty-gritty of specific powders, let’s explore their key characteristics through a handy table:
Caratteristica | Descrizione |
---|---|
Composizione | Iron base with controlled additions of alloying elements like chromium, manganese, molybdenum, nickel, silicon, and carbon |
Forma delle particelle | Typically spherical for optimal flowability and packing density during AM processes |
Dimensione particellare | Ranging from 10 to 150 microns, depending on the specific application and AM technique |
Densità | Close to the density of wrought steel (around 7.8 g/cm³), ensuring minimal shrinkage during AM |
Let’s face it, choosing the right low-alloy steel powder is like picking the perfect ingredients for a delicious meal. Each element plays a specific role, and the final properties depend on the precise recipe.
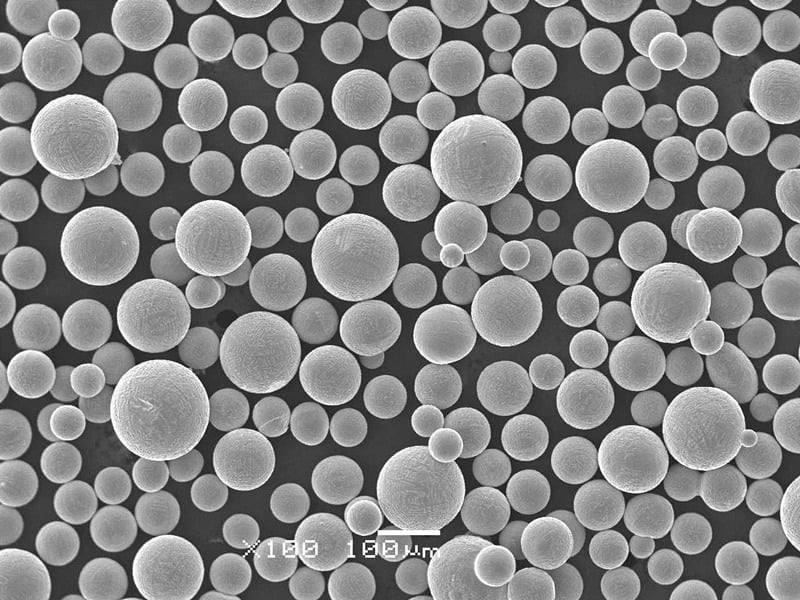
Exploring Popular Low-Alloy Steel Powder Modelli
Now that we understand the fundamentals, let’s explore some of the most popular low-alloy steel powder models in the market:
- SAE 15CrNi6-4 (AISI 9310): This chromium-nickel-molybdenum alloy is a versatile workhorse, offering excellent hardenability and good toughness. It’s a popular choice for gears, shafts, and other high-stress components.
- AISI 4140: This chromium-molybdenum alloy boasts good strength, wear resistance, and fatigue strength. It’s commonly used in the aerospace industry for landing gear components and engine parts.
- 20MnCr5: This manganese-chromium alloy is known for its high strength, ductility, and excellent wear resistance. It’s a cost-effective option for automotive prototypes and functional parts.
- ASTM A276 Grade 4140: This standardized version of AISI 4140 ensures consistent quality and properties, making it ideal for critical applications where reliability is paramount.
- Osprey® 42CrMo4 (AISI 4140): This gas-atomized powder from Sandvik offers exceptional flowability and packing density, leading to high-quality AM builds with minimal porosity.
- GLM® (Gas-Atomized Low-Manganese Steel): This low-manganese alternative from Höganäs minimizes the risk of hydrogen cracking during AM, making it suitable for thick-walled parts.
- EM100 (HP): This high-performance powder from Carpenter Additive Manufacturing boasts superior strength and toughness, making it ideal for demanding applications like tooling and aerospace components.
- AM304L: This nitrogen-alloyed version of 304 stainless steel offers improved printability and corrosion resistance, making it a valuable option for applications requiring both strength and resistance to harsh environments.
- 17-4 PH: This precipitation-hardening stainless steel powder provides exceptional strength and good corrosion resistance while remaining relatively easy to print. It’s a popular choice for medical instruments and high-performance marine components.
- Polveri di acciaio Maraging: These high-nickel alloys offer exceptional strength and ductility after heat treatment, making them ideal for aerospace components and applications requiring high strength-to-weight ratios.
Applicationsof Low-Alloy Steel Powders
The potential applications of low-alloy steel powders are as vast as human imagination. Here are some key areas where these versatile materials are making a significant impact:
- Aerospaziale: Low-alloy steel powders are lightweight yet incredibly strong, making them ideal for aircraft components like landing gear, engine mounts, and structural parts. Their ability to achieve complex geometries also allows for weight optimization, a critical factor in fuel efficiency.
- Settore automobilistico: From intricate gears and shafts to lightweight suspension components, low-alloy steel powders are revolutionizing the automotive industry. The ability to produce near-net-shape parts minimizes waste and reduces production costs. Additionally, their high strength-to-weight ratio contributes to improved fuel economy.
- Dispositivi medici: The biocompatible nature of certain low-alloy steel powders, like 316L stainless steel, makes them valuable for creating medical implants and surgical instruments. Their excellent strength and corrosion resistance ensure long-lasting performance in the human body.
- Utensili e stampi: Low-alloy steel powders can be used to create complex molds and tooling inserts with intricate channels and cooling features, leading to faster production cycles and improved part quality. Additionally, their high wear resistance makes them ideal for demanding applications.
- Settore energetico: From components in oil and gas exploration to parts for wind turbines and power generation plants, low-alloy steel powders offer the perfect blend of strength, durability, and affordability for the energy sector.
Beyond these core applications, low-alloy steel powders are finding their way into various other industries, including:
- Consumer goods (e.g., sporting equipment, bicycles)
- Robotics (e.g., manipulator arms, grippers)
- Defense (e.g., firearm components, protective gear)
- Architecture and construction (e.g., lightweight structural elements, customized brackets)
As AM technology continues to evolve, we can expect even more innovative applications for low-alloy steel powders. The possibilities are truly limitless!
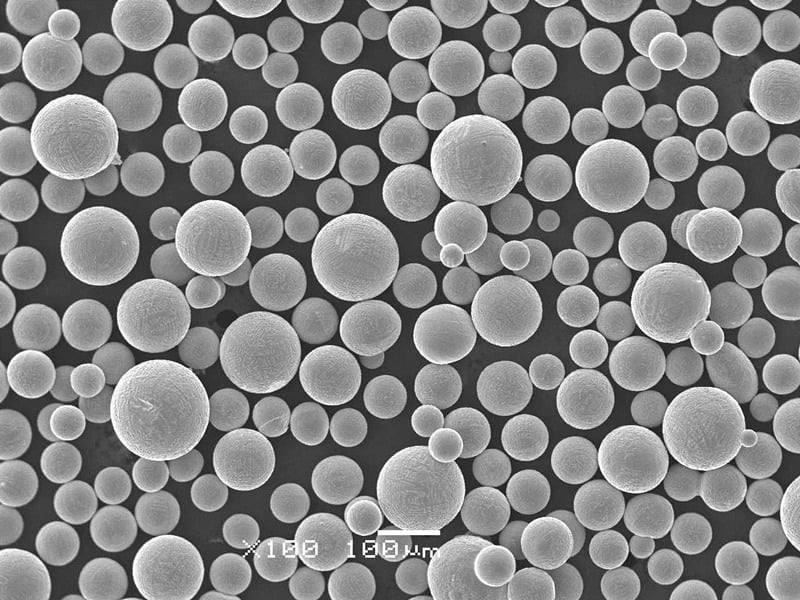
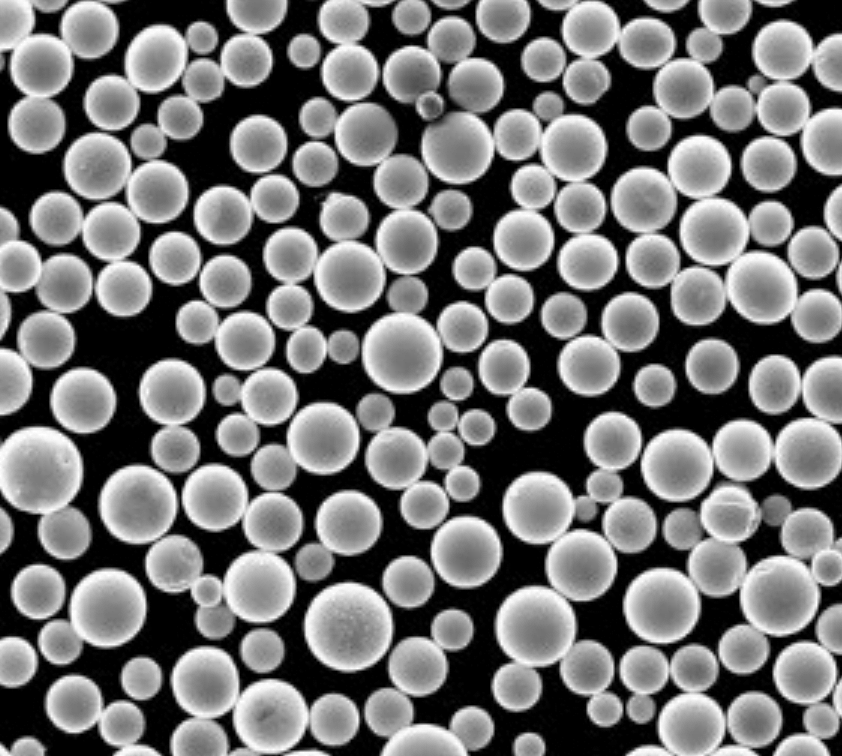
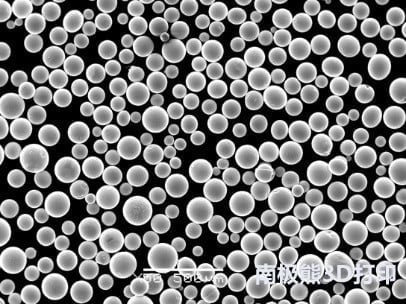
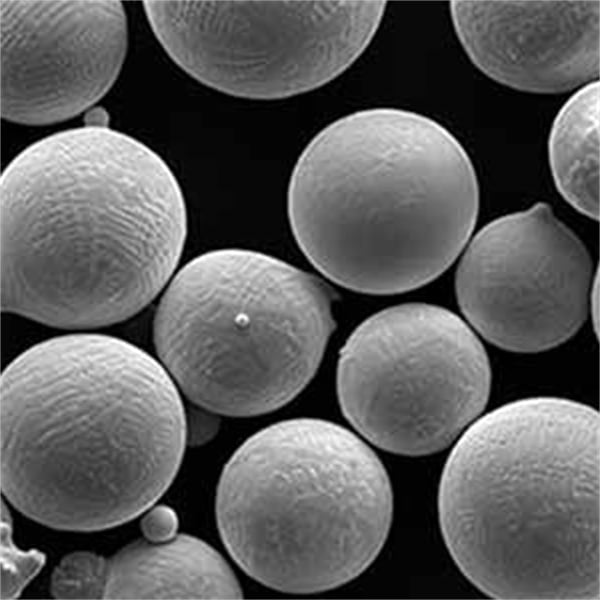
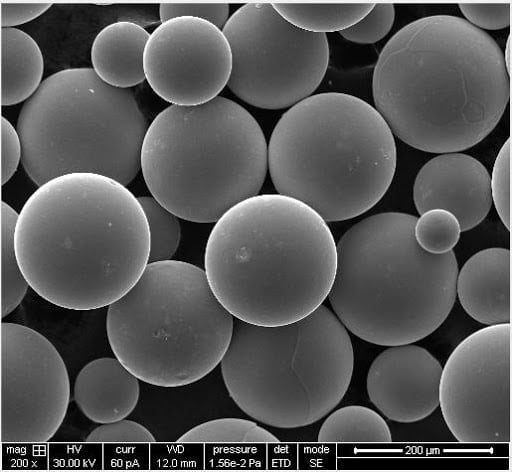
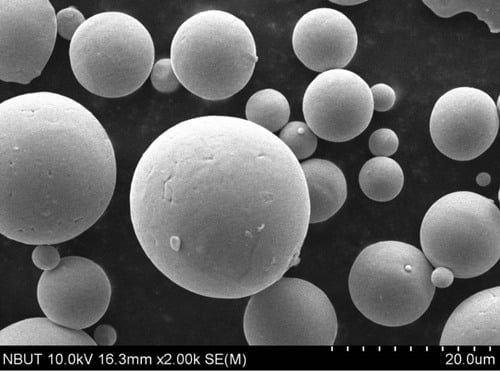
Specifications & Considerations
Selecting the ideal low-alloy steel powder for your project requires careful consideration of several factors:
Key Considerations:
- Proprietà desiderate: What properties are crucial for your application? Do you need high strength, wear resistance, fatigue strength, or a combination of these?
- Processo AM: Different AM techniques have varying requirements for powder characteristics like particle size and flowability.
- Part Geometry: Complex geometries might necessitate finer powders for better resolution, while simpler shapes can utilize larger particles.
- Post-elaborazione: Some powders might require heat treatment or other post-processing steps to achieve the desired properties.
Here’s a table to help you navigate the world of polvere di acciaio a bassa lega specifications:
Specificazione | Descrizione | Importanza |
---|---|---|
Composizione chimica | The specific percentages of iron and alloying elements | Determines the final mechanical properties of the printed part |
Distribuzione granulometrica | The range of particle sizes within the powder | Affects flowability, packing density, and surface finish of the printed part |
Densità apparente | The bulk density of the powder | Influences the amount of powder required to build a part |
Flussibilita | The ease with which the powder flows | Crucial for consistent feeding during the AM process |
Sfericità | The shape of the powder particles (ideally spherical) | Affects packing density and minimizes porosity in the printed part |
Remember, consulting with a qualified AM service provider can be invaluable in selecting the optimal low-alloy steel powder for your specific needs.
Advantages & Limitations
Advantages of Low-Alloy Steel Powders:
- Libertà di progettazione: Unleash your creativity with complex geometries and internal features.
- Produzione a forma di quasi rete: Minimize waste and optimize material utilization.
- Forza superiore: Achieve excellent strength-to-weight ratios for lightweight, high-performance parts.
- Efficienza del materiale: Utilize only the necessary amount of material for each part.
- Broad Range of Properties: Tailor properties by selecting the appropriate powder and heat treatment.
Limitations of Low-Alloy Steel Powders:
- Costo: Low-alloy steel powders can be more expensive than traditional wrought steels, especially for high-volume production.
- Finitura superficiale: AM processes might result in a rougher surface finish compared to conventional techniques, potentially requiring additional post-processing.
- Limitazioni delle dimensioni di costruzione: Current AM machines have limitations on build volume, restricting the size of parts that can be produced.
- Requisiti di post-elaborazione: Some powders might require heat treatment or hot isostatic pressing (HIP) for optimal performance.
The key takeaway? Low-alloy steel powders offer a powerful combination of design freedom, material efficiency, and superior strength. However, it’s crucial to consider the cost implications, potential surface finish limitations, and build size restrictions before diving into this exciting technology.
Here’s a table summarizing the key advantages and limitations of low-alloy steel powders:
Vantaggio | Descrizione | Limitazione | Descrizione |
---|---|---|---|
Libertà di progettazione | Create intricate geometries and internal features | Costi | Low-alloy steel powders can be more expensive than traditional steels |
Near-Net-Shape Manufacturing | Minimize waste and optimize material utilization | Finitura superficiale | AM processes might require additional post-processing for a smooth finish |
Superior Strength | Achieve excellent strength-to-weight ratios | Limitazioni delle dimensioni di costruzione | Current AM machines have limitations on the size of parts that can be produced |
Efficienza del materiale | Utilize only the necessary amount of material for each part | Requisiti di post-elaborazione | Some powders might require heat treatment or HIP for optimal performance |
Broad Range of Properties | Tailor properties by selecting the appropriate powder and heat treatment |
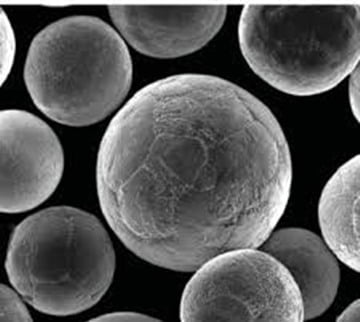
Suppliers & Pricing
The world of low-alloy steel powder suppliers is constantly evolving. Here are some of the leading players:
- Höganäs: A global leader in metal powders, offering a wide range of low-alloy steel powders for various AM applications.
- APM Materials: Specializes in high-performance metal powders, including gas-atomized low-alloy steel powders for demanding applications.
- Carpenter Additive Manufacturing: Provides a variety of high-performance metal powders, including low-alloy steel options with superior strength and toughness.
- Sandvik: Offers Osprey® branded metal powders, including gas-atomized low-alloy steel powders renowned for their excellent flowability and packing density.
- GKN Powder Metallurgy: A leading manufacturer of metal powders, including low-alloy steel powders specifically designed for additive manufacturing processes.
Pricing for low-alloy steel powders can vary depending on several factors:
- Specific powder type (alloy composition): More complex alloys with higher performance characteristics typically come at a premium.
- Dimensione e distribuzione delle particelle: Finer powders with tighter size distribution tend to be more expensive.
- Quantità: Bulk purchases often offer significant cost savings compared to smaller orders.
It’s essential to get quotes from multiple suppliers to compare pricing and ensure you’re getting the best value for your project.
FAQ
1. What are the advantages of using low-alloy steel powders compared to traditional wrought steels?
Low-alloy steel powders offer several advantages, including:
- Libertà di progettazione: Create complex geometries and internal features impossible with traditional techniques.
- Near-net-shape manufacturing: Minimize waste and optimize material utilization.
- Superior strength-to-weight ratio: Achieve lightweight, high-performance parts.
- Broad range of properties: Tailor properties by selecting the appropriate powder and heat treatment.
2. What are the limitations of using low-alloy steel powders?
There are some limitations to consider:
- Costo: Low-alloy steel powders can be more expensive than traditional steels, especially for high-volume production.
- Finitura superficiale: AM processes might require additional post-processing for a smooth finish.
- Limitazioni delle dimensioni di costruzione: Current AM machines have limitations on the size of parts that can be produced.
- Requisiti di post-elaborazione: Some powders might require heat treatment or HIP for optimal performance.
3. What are some of the typical applications for low-alloy steel powders?
Low-alloy steel powders are used in various industries, including:
- Aerospace (landing gear, engine mounts, structural parts)
- Automotive (gears, shafts, suspension components)
- Medical devices (implants, surgical instruments)
- Tooling and molds (complex molds, tooling inserts)
- Energy sector (oil & gas exploration, wind turbine components)
4. How do I choose the right low-alloy steel powder for my project?
Selecting the ideal powder requires considering several factors:
- Desired properties: What properties are crucial for your application (strength, wear resistance, etc.)?
- AM process: Different AM techniques have varying requirements for powder characteristics.
- Part geometry: Complex geometries might necessitate finer powders.
- Post-elaborazione: Some powders might require heat treatment or other post-processing steps.
Consulting with a qualified AM service provider can be invaluable in selecting the optimal powder for your needs.
Informazioni su 3DP mETAL
Categoria di prodotto
CONTATTACI
Hai domande? Scrivici un messaggio ora! Dopo aver ricevuto il tuo messaggio, informeremo sull'elaborazione della tua richiesta a tutto il team.