Imagine a sculptor, not wielding a chisel and hammer, but wielding a high-powered jet of gas. Instead of chipping away at a block of stone, this sculptor disintegrates a stream of molten metal, transforming it into a cascade of tiny, individual particles. This is the essence of atomizzazione del metallo, a revolutionary process that breaks down bulk metals into fine metallic powders, unlocking a universe of possibilities in manufacturing and material science.
But why go through all this trouble to break down perfectly good metal? Buckle up, because the answer lies in the unique properties of metal powders and the doors they open for innovation.
the Advantages of Metal Atomization
Metal powders, unlike their solid counterparts, possess a remarkable set of advantages:
- Versatilità senza pari: Imagine metal that can be shaped like flour, molded like clay, and precisely controlled like a high-performance material. Metal powders offer this very versatility. They can be used in Additive Manufacturing (AM), also known as 3D printing, to create complex, near-net-shape components. They excel in Stampaggio a iniezione di metallo (MIM), allowing for the mass production of intricate metal parts. Even traditional techniques like Termo-spruzzatura benefit from metal powders, enabling the creation of wear-resistant coatings.
- Proprietà del materiale superiori: The rapid solidification that occurs during atomization creates unique microstructures within the metal particles. This can lead to improved strength, ductility, and corrosion resistance compared to conventionally manufactured metals. Imagine a lightweight material that’s stronger than steel – metal powders can make that a reality.
- Reduced Waste and Enhanced Efficiency: Traditional metal manufacturing often involves significant material loss through processes like machining. Metal atomization minimizes this waste by creating near-net-shape components directly from powder. This translates to cost savings, reduced environmental impact, and a more sustainable approach to metalworking.
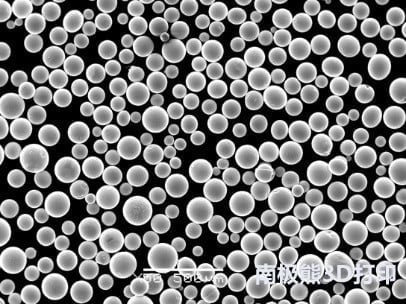
The Main Methods of Metal Atomization
Now that we understand the “why” behind metal atomization, let’s delve into the “how.” There are two main categories of atomization techniques: physical and chemical.
Common Physical Methods for Metal Atomization:
- Atomizzazione del gas: This method, like our sculptor with a gas jet, utilizes high-pressure inert gases like argon or nitrogen to break up a stream of molten metal. The resulting fine droplets rapidly solidify into spherical metal powders. Gas atomization is widely used for a broad range of metals, offering good control over particle size and morphology.
- Atomizzazione dell'acqua: Here, water replaces the gas as the atomizing force. A high-pressure water jet disintegrates the molten metal, creating a coarser powder compared to gas atomization. Water atomization is a cost-effective option for less critical applications, particularly for high-volume production.
Chemical Methods for Metal Atomization:
- Rapid Solidification (RS) Techniques: This group of methods involves injecting molten metal into a mold containing a reactive material. The rapid reaction between the metal and the mold material leads to the formation of highly refined and dispersed metal powders. These techniques offer superior control over microstructure and are often used for specialty alloys.
Choosing the Right Method: A Balancing Act
The selection of the ideal atomization method depends on several factors:
- Desired Powder Properties: The size, shape, and internal structure of the metal powder significantly impact its performance in downstream applications.
- Tipo di metallo: Different metals have varying melting points, viscosities, and reactivity, which influence the choice of the atomization method.
- Production Cost and Throughput: Gas atomization often offers finer control but can be more expensive compared to water atomization. Throughput (the amount of powder produced per unit time) also plays a role in selecting the most efficient method.
Beyond the Basics: Unveiling Specialized Techniques
The world of metal atomization extends beyond the core methods mentioned above. Here are some fascinating specialized techniques:
- Atomizzazione centrifuga: This method utilizes a high-speed rotating disc to break up molten metal into fine droplets. It’s particularly well-suited for producing spherical powders with a narrow size distribution.
- Vacuum Atomization: This technique eliminates the risk of oxidation by performing the atomization process in a vacuum chamber. It’s crucial for reactive metals like titanium and tantalum.
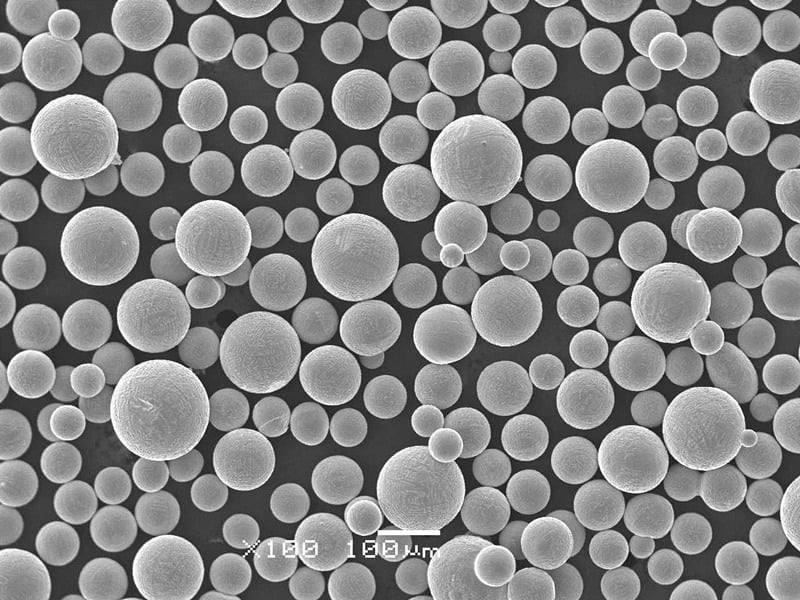
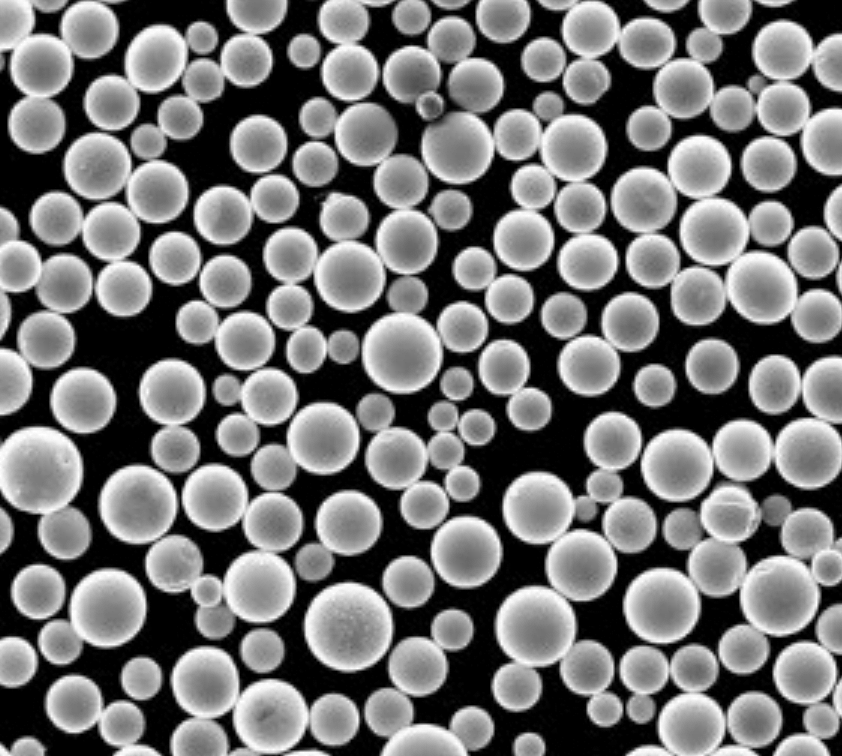
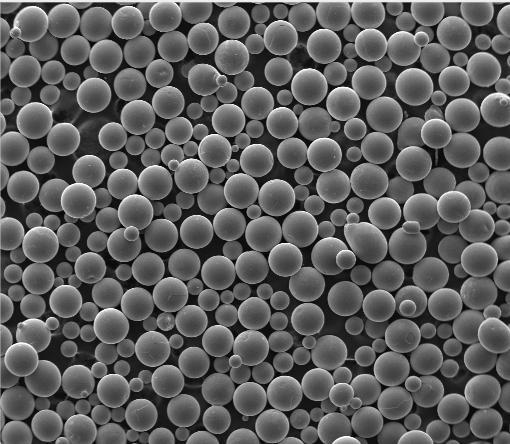
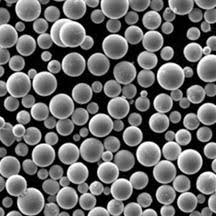
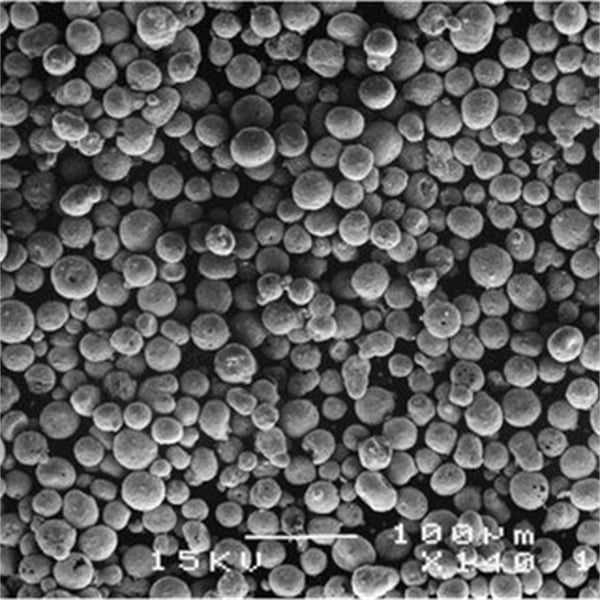
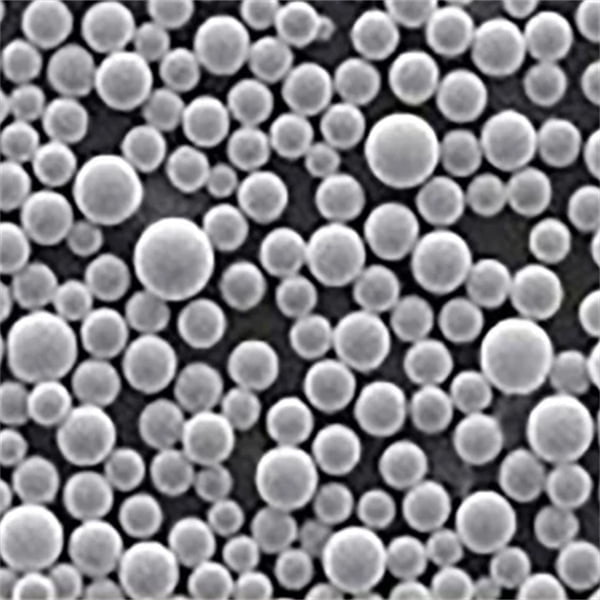
Shaping the Future of Manufacturing
As advancements continue in atomizzazione del metallo technology, we can expect even more exciting possibilities to emerge. Here are a few glimpses into the future:
- Production of Advanced Alloys: Metal atomization allows for the creation of novel alloys with superior properties, pushing the boundaries of what’s possible in material science.
- Personalization of Metal Components: The ability to precisely control powder characteristics through atomization opens doors for the customization of metal components for specific applications. Imagine components with tailored strength, weight, and heat resistance, designed exactly for their intended purpose.
- Integration with Advanced Manufacturing Techniques: Metal atomization acts as a powerful bridge between the world of powders and cutting-edge manufacturing processes like Additive Manufacturing (AM). As AM technology evolves, metal atomization will play a critical role in providing the high-quality, precisely engineered powders needed to unlock its full potential.
Where Do We See Metal Atomization in Action?
The applications of metal atomization span a vast array of industries, each benefiting from the unique properties of metal powders. Here are some prominent examples:
- Aerospaziale: The relentless pursuit of lightweight, high-strength materials in the aerospace industry makes metal atomization a perfect fit. Metal powders are used to create components for aircraft engines, airframes, and spacecraft, contributing to fuel efficiency and overall performance.
- Settore automobilistico: Metal atomization finds its place in the automotive industry as well. From lightweight components for electric vehicles to wear-resistant coatings for engine parts, metal powders are helping to improve fuel efficiency, reduce emissions, and enhance vehicle durability.
- Dispositivi medici: The biocompatible nature of certain metal powders allows them to be used in medical implants, such as artificial joints and dental prosthetics. Metal atomization enables the creation of these implants with tailored properties for better performance and biocompatibility within the human body.
- Elettronica di consumo: The intricate world of consumer electronics also benefits from metal atomization. Metal powders are used in the production of electronic components like heat sinks and EMI shielding, ensuring optimal performance and functionality of our everyday gadgets.
The Road Ahead: Challenges and Considerations
While metal atomization offers a treasure trove of benefits, there are challenges to consider:
- Cost Optimization: Developing and maintaining sophisticated atomization equipment can be expensive. Streamlining processes and finding cost-effective methods for specific applications remain ongoing endeavors.
- Impatto ambientale: The energy consumption associated with metal atomization necessitates continuous efforts towards improving efficiency and minimizing the environmental footprint.
- Powder Characterization and Control: Ensuring consistent and precise control over powder properties like size, shape, and flowability remains crucial for achieving optimal performance in downstream applications.
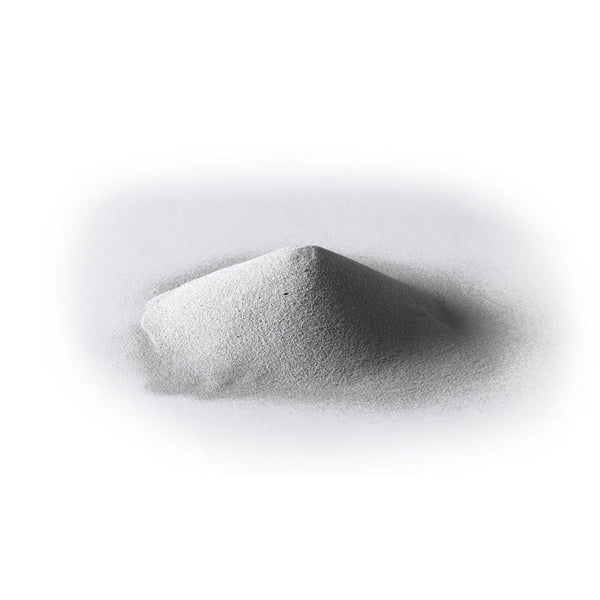
FAQ
Ecco una panoramica di alcune domande frequenti su atomizzazione del metallo, presentati in un formato tabellare chiaro e conciso:
Domanda | Risposta |
---|---|
Che cos'è l'atomizzazione dei metalli? | Metal atomization is a process that breaks down molten metal into fine metallic powders. |
What are the benefits of metal atomization? | Metal powders offer advantages like versatility, improved material properties, reduced waste, and enhanced efficiency. |
What are the main methods of metal atomization? | Physical methods (gas atomization, water atomization) and chemical methods (rapid solidification techniques) are the two main categories. |
What factors influence the choice of atomization method? | Desired powder properties, metal type, production cost, and throughput are key considerations. |
What are some specialized atomization techniques? | Centrifugal atomization and vacuum atomization offer unique advantages for specific applications. |
What are the future possibilities of metal atomization? | Advanced alloy production, personalized components, and integration with AM techniques are some exciting prospects. |
Where is metal atomization used? | Metal powders find applications in aerospace, automotive, medical devices, consumer electronics, and more. |
What are the challenges associated with metal atomization? | Cost optimization, environmental impact, and powder characterization control are ongoing areas of focus. |
In conclusione
Metal atomization stands as a testament to human ingenuity. By transforming bulk metals into a world of possibilities at the microscopic level, this technology paves the way for advancements across diverse industries. As research and development continue, metal atomization promises to be a driving force in shaping the future of manufacturing, innovation, and material science.
Informazioni su 3DP mETAL
Categoria di prodotto
CONTATTACI
Hai domande? Scrivici un messaggio ora! Dopo aver ricevuto il tuo messaggio, informeremo sull'elaborazione della tua richiesta a tutto il team.