Imagine a world where intricate, near-net-shape metal components can be mass-produced with high precision and intricate details. This isn’t science fiction; it’s the reality of Metal Injection Molding (MIM), a revolutionary manufacturing process that relies on a secret weapon: Polvere di metallo MIM.
But what exactly is MIM metal powder, and how does it transform tiny particles into complex metal parts? Buckle up, because we’re diving deep into the fascinating world of MIM powders, exploring their types, properties, applications, and the intricate dance they perform to create the metal components that power our everyday lives.
the Composition and Properties of MIM Metal Powder
MIM metal powders are finely-ground metallic particles, typically ranging from 5 to 100 microns in size (that’s about 5-100 times thinner than a human hair!). These microscopic marvels come in various compositions, each tailored for specific applications. Here’s a peek into the most common types of MIM metal powders:
Common MIM Metal Powder Compositions
Metallo/lega | Descrizione |
---|---|
Acciaio inossidabile (316L) | The most widely used MIM powder, known for its excellent corrosion resistance, high strength, and biocompatibility. |
Low-Alloy Steel | Offers a balance of affordability and good mechanical properties, making it ideal for high-volume applications. |
Acciaio per utensili | Boasts exceptional wear resistance, perfect for components that need to endure friction and abrasion. |
Superleghe a base di nichel | High-performance alloys known for their ability to withstand extreme temperatures and harsh environments. |
Leghe di titanio | Lightweight yet incredibly strong, titanium alloys are popular in aerospace and medical applications. |
Leghe di rame | Excellent thermal and electrical conductivity make copper alloys ideal for heat sinks and electrical components. |
Leghe di alluminio | Lightweight and readily machinable, aluminum alloys offer a cost-effective option for various applications. |
Kovar | A unique alloy with a thermal expansion coefficient that closely matches glass, making it ideal for glass-to-metal seals. |
Invar | Known for its incredibly low thermal expansion coefficient, Invar is used in precision instruments and components that need to maintain dimensional stability across temperature changes. |
Carburo di tungsteno | Exceptionally hard and wear-resistant, tungsten carbide is perfect for cutting tools and components that experience high levels of abrasion. |
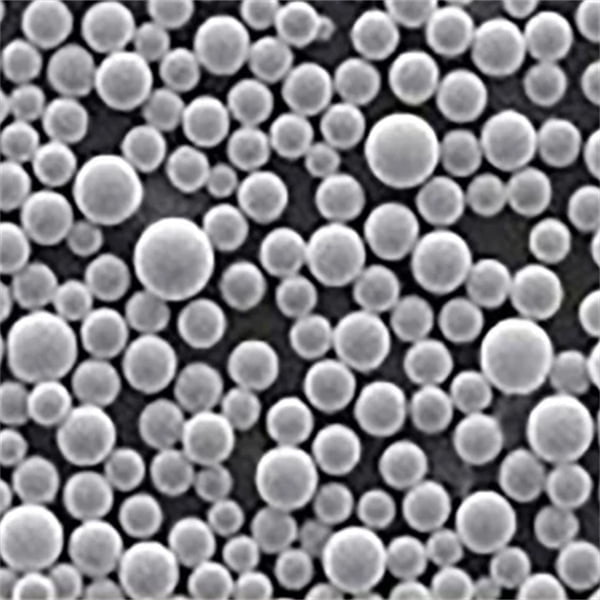
Proprietà di Polvere di metallo MIM
Beyond composition, several key properties define the performance and suitability of MIM metal powder for different applications. These include:
- Dimensione e distribuzione delle particelle: Particle size and its even distribution significantly impact the final part’s density, surface finish, and mechanical properties. Finer powders generally produce denser parts with smoother finishes but might be more challenging to process.
- Capacità di scorrimento The powder’s ability to flow freely is crucial for even distribution during the injection molding process. Good flowability ensures consistent part quality and minimizes processing defects.
- Sinterizzazione: This refers to the powder’s ability to bond together during the sintering stage, forming a strong, cohesive metal part. Sinterability is heavily influenced by particle size, morphology, and composition.
- Composizione chimica: The specific elements present in the powder determine the final part’s mechanical properties, corrosion resistance, and other performance characteristics.
Choosing the right MIM metal powder is like selecting the perfect ingredients for a recipe. By understanding the composition and properties of various powders, manufacturers can optimize the manufacturing process and achieve the desired characteristics in the final metal component.
Applicazioni della polvere di metallo MIM
MIM metal powder isn’t just a collection of tiny particles; it’s the foundation for a vast array of complex and intricate metal components. Here’s a glimpse into some of the most common applications of MIM metal powder:
Applicazioni della polvere di metallo MIM
Industria | Esempi |
---|---|
Elettronica di consumo | Gears, housings, connectors, heat sinks, RF components |
Automotive | Engine components, fuel system parts, transmission components, gears, locks |
Dispositivi medici | Surgical instruments, dental implants, bone screws, biocompatible components |
Aerospaziale e difesa | Aircraft engine components, weapon parts, guidance systems, high-performance components |
Telecomunicazioni | Connectors, RF components, housings for electronic devices |
Macchinari industriali | Gears, sprockets, valves, wear-resistant components |
Articoli sportivi | Bicycle components, firearm parts, fishing reel components |
The beauty of MIM lies in its ability to produce intricate shapes with tight tolerances, making it ideal for applications where complex geometries and high precision are essential. Unlike traditional machining processes that remove material to create a desired shape, MIM builds parts layer by layer, offering exceptional design freedom and the ability to create features that would be incredibly difficult or impossible to machine.
Let’s delve deeper into some specific examples:
- Gears: MIM metal powder is a game-changer for gear manufacturing. It allows for the production of intricate gear shapes with high precision and excellent wear resistance. Compared to traditional gear manufacturing methods like hobbing or broaching, MIM offers several advantages. Firstly, MIM can produce gears with complex geometries, such as internal gears or gears with variable tooth profiles. Secondly, MIM gears boast near-net shapes, minimizing the need for post-processing and reducing material waste. Finally, MIM gears can be produced with a wide range of materials, including high-strength steels and wear-resistant alloys, making them ideal for demanding applications.
- Dispositivi medici: The biocompatible nature of certain MIM metal powders makes them a perfect fit for the medical device industry. MIM technology allows for the creation of intricate surgical instruments, dental implants, and bone screws with exceptional strength, corrosion resistance, and smooth surface finishes. Compared to traditional methods like casting or forging, MIM offers several advantages for medical devices. Firstly, MIM produces parts with high precision and tight tolerances, crucial for the proper functioning of medical implants. Secondly, MIM allows for the creation of complex geometries, enabling the design of innovative and minimally invasive surgical tools. Finally, MIM ensures consistent material properties throughout the part, critical for the safety and reliability of medical devices.
- Elettronica di consumo: The world of consumer electronics relies heavily on intricate and miniaturized components. MIM metal powder excels in this arena, enabling the production of gears, housings, connectors, heat sinks, and RF components with exceptional detail and tight tolerances. Compared to traditional methods like stamping or plastic injection molding, MIM offers several advantages. Firstly, MIM allows for the creation of metallic components with superior strength and thermal conductivity, essential for high-performance electronics. Secondly, MIM enables the production of complex shapes and features that would be difficult or impossible to achieve with other methods. Finally, MIM ensures consistent part quality and dimensional accuracy, crucial for reliable electronic devices.
These are just a few examples of the vast potential of MIM metal powder. As technology continues to evolve, we can expect to see even more innovative applications emerge, pushing the boundaries of what’s possible in the world of metal manufacturing.
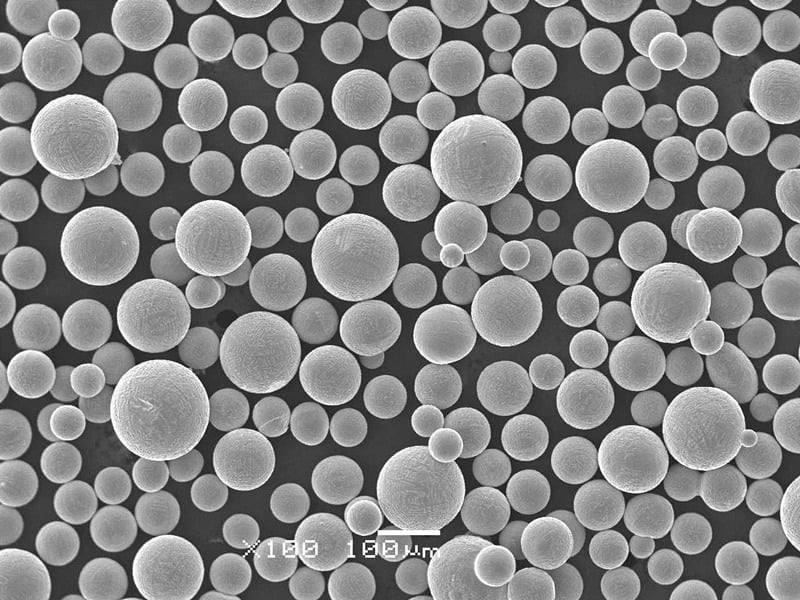
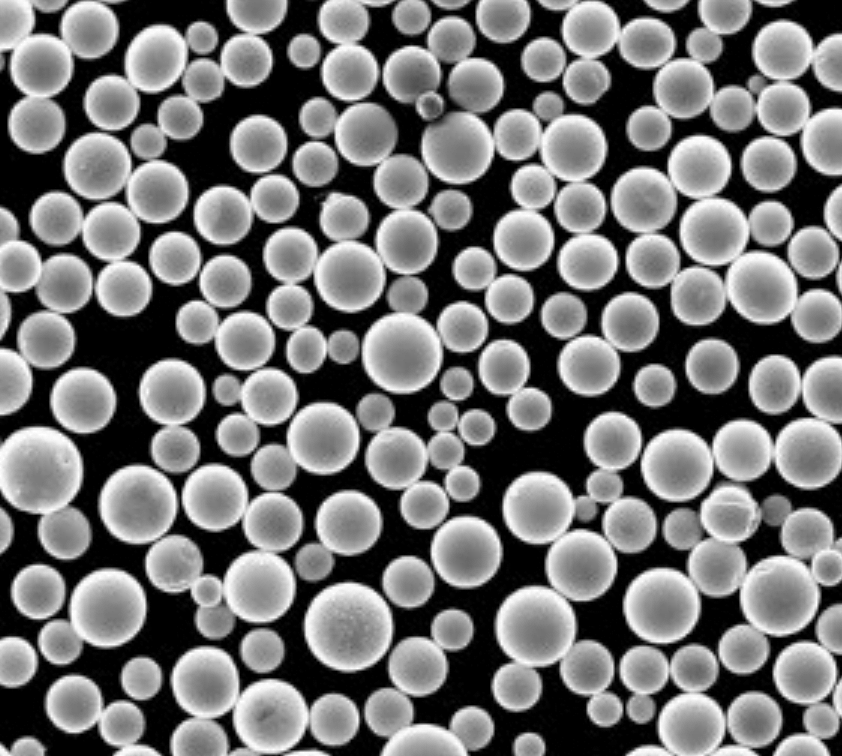
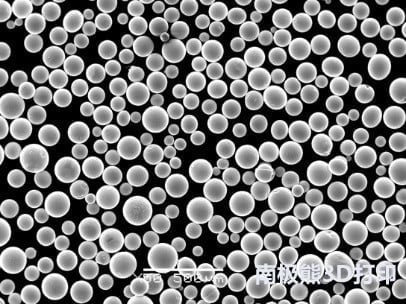
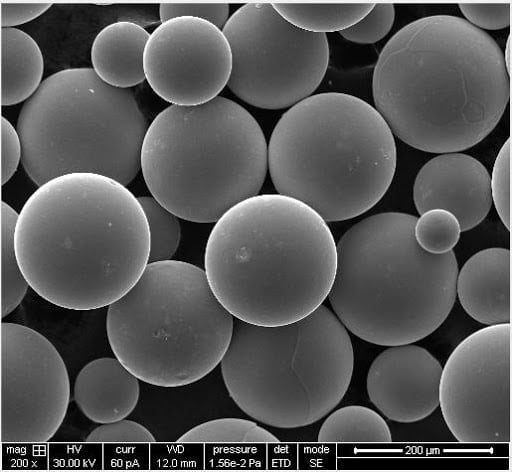
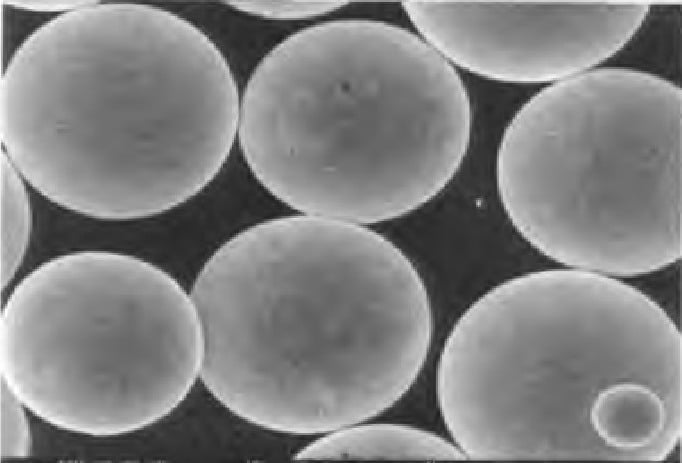
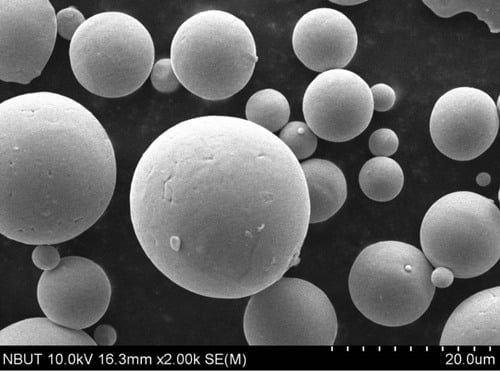
Sizes, Grades, and Standards
When it comes to MIM metal powder, choosing the right material goes beyond just composition. Several factors come into play, including particle size, grade, and adherence to specific standards. Let’s explore these aspects in more detail:
MIM Metal Powder Specifications
Fattore | Descrizione |
---|---|
Dimensione particellare: | As mentioned earlier, particle size plays a crucial role in the final part’s properties. Finer powders generally produce denser parts with smoother finishes but can be more challenging to process. Coarser powders offer better flowability but might result in parts with lower density and higher surface roughness. |
Grado: | Similar to other materials, MIM metal powder comes in various grades, each with specific chemical compositions and mechanical properties. The choice of grade depends on the desired performance characteristics of the final part. For instance, a component requiring high strength might utilize a higher-grade powder with a higher alloy content. |
Standard: | Several industry standards govern the production and properties of MIM metal powders. These standards ensure consistent quality and performance across different suppliers. Common standards include ASTM International (ASTM) and the American Society for Testing and Materials (AMPM). |
Examples of MIM Metal Powder Specifications:
Here’s a table showcasing some examples of commercially available MIM metal powders with their specifications:
In polvere | Composizione | Dimensione delle particelle (µm) | Grado | Standard |
---|---|---|---|---|
Acciaio inox 316L | Fe-16Cr-10Ni-2Mo | 10-20 | Standard | ASTM B930 |
Low Alloy Steel | Fe-1%Mn-0.2%Mo | 15-30 | Grado A | Standard MPIF 35 |
Acciaio per utensili | Fe-4%Cr-1%Mo-1%V | 20-40 | High Carbon | ASTM A29 |
Pro e contro di Polvere di metallo MIM
MIM metal powder offers a compelling solution for manufacturing complex and intricate metal components. However, like any technology, it has its own set of advantages and disadvantages. Understanding these factors is essential for determining if MIM is the right fit for your specific application.
Advantages of MIM Metal Powder
- Produzione a forma di quasi rete: MIM allows for the production of parts with minimal post-processing requirements. This translates to reduced material waste, lower production costs, and faster turnaround times compared to traditional machining processes.
- Libertà di progettazione: MIM offers exceptional design flexibility, enabling the creation of intricate shapes and features that would be difficult or impossible to achieve with other methods. This opens doors for innovative product designs and enhanced functionality.
- High Precision and Tight Tolerances: MIM parts are known for their exceptional dimensional accuracy and consistent quality. This is crucial for applications where precise tolerances are essential, such as in medical devices and aerospace components.
- Wide Range of Materials: MIM can be used with a vast array of metal powders, including stainless steels, tool steels, nickel-based alloys, and even exotic materials like tungsten carbide. This versatility allows for the selection of the optimal material for each specific application.
- Mass Production Capabilities: MIM is a well-suited technology for high-volume production runs. The consistency and repeatability of the process ensure high-quality parts at scale.
- Migliori proprietà meccaniche: The sintering process in MIM strengthens the powder particles, resulting in metal parts with excellent mechanical properties, including strength, hardness, and wear resistance.
Disadvantages of MIM Metal Powder
- High Initial Investment: The equipment and setup costs associated with MIM can be significant. This might be a barrier for smaller companies or those with limited production volumes.
- Complessità del processo: MIM involves several intricate stages, each requiring careful control and monitoring. This complexity necessitates skilled personnel and a deep understanding of the process to ensure consistent quality.
- Limitazioni materiali: While MIM offers a wide range of materials, some metals might not be compatible with the process due to their high melting points or reactivity.
- Surface Finish Limitations: MIM parts might have a slightly rougher surface finish compared to machined components. However, post-processing techniques can improve the surface finish if necessary.
- Limitazioni delle dimensioni dei pezzi: There are limitations on the size of parts that can be produced using MIM. MIM is best suited for smaller, intricate components.
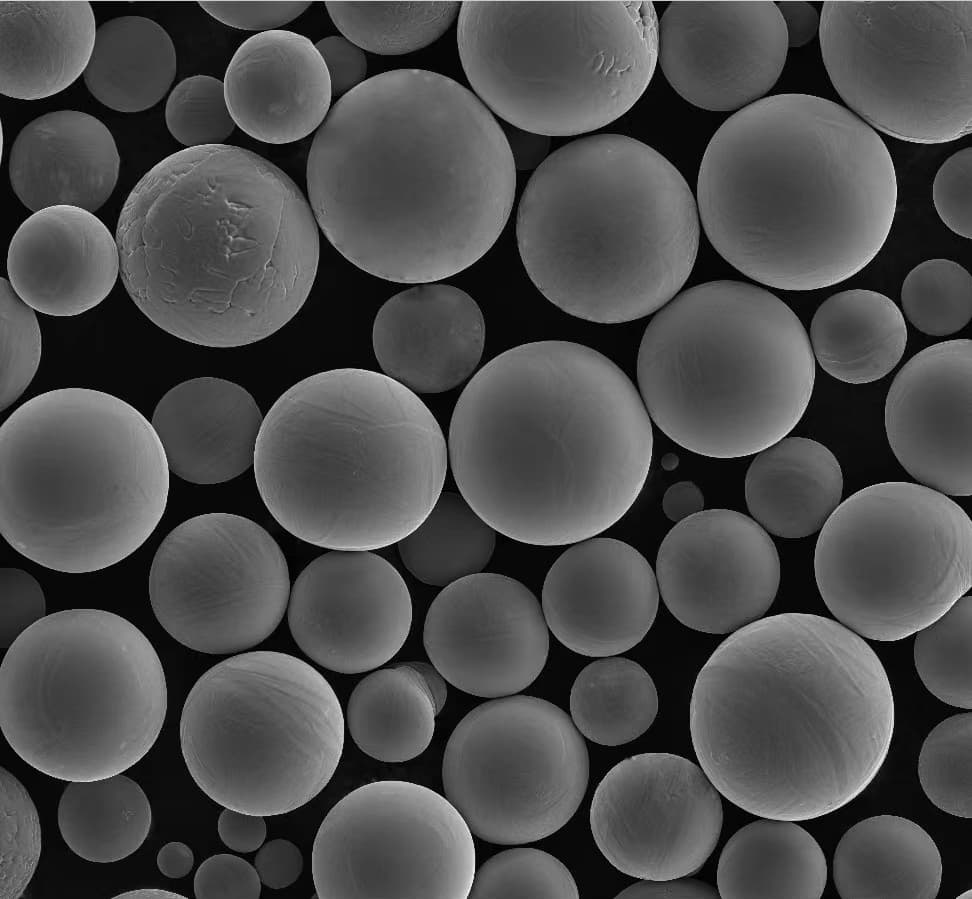
Choosing Between MIM and Other Manufacturing Processes
The decision to utilize MIM metal powder depends on various factors, including the complexity of the part, desired production volume, required tolerances, material selection, and budget constraints. Here’s a brief comparison of MIM with some alternative manufacturing processes:
- Lavorazione: MIM offers advantages for complex shapes and near-net-shape production compared to traditional machining. However, machining might be more cost-effective for simpler parts or lower production volumes.
- Casting: Casting can be a good option for high-volume production of simpler shapes. However, MIM provides greater design freedom and tighter tolerances.
- Metal Additive Manufacturing (3D Printing): Both MIM and 3D printing offer design freedom and can produce complex shapes. However, MIM is generally faster and more cost-effective for high-volume production, while 3D printing might be better suited for prototypes or low-volume applications.
By carefully considering the advantages and limitations of Polvere di metallo MIM and comparing it to alternative processes, manufacturers can make an informed decision about the most suitable technology for their specific needs.
FAQ
Here are some of the most commonly asked questions regarding MIM metal powder, presented in a clear and concise question-and-answer format:
Domanda | Risposta |
---|---|
What is MIM metal powder? | MIM metal powder is a collection of finely-ground metallic particles used in the Metal Injection Molding (MIM) process to create complex and intricate metal components. |
What are the benefits of using MIM metal powder? | MIM metal powder offers several advantages, including near-net-shape manufacturing, design freedom, high precision, a wide range of materials, mass production capabilities, and improved mechanical properties. |
Are there any limitations to using MIM metal powder? | Yes, MIM has some limitations, such as high initial investment costs, process complexity, material limitations, surface finish limitations, and part size limitations. |
What are some common applications of MIM metal powder? | MIM metal powder is used in various industries, including consumer electronics, automotive, medical devices, aerospace & defense, telecommunications, industrial machinery, and sporting goods. |
How does MIM metal powder compare to other manufacturing processes? | MIM offers advantages over traditional machining for complex shapes and near-net-shape production. It provides greater |
Informazioni su 3DP mETAL
Categoria di prodotto
CONTATTACI
Hai domande? Scrivici un messaggio ora! Dopo aver ricevuto il tuo messaggio, informeremo sull'elaborazione della tua richiesta a tutto il team.